Week 10

Moulding And Casting
This weeek Professor Neil gives an idea about moulding and casting.The assignment in this week is to Design and build a mold also need to cast it.Moulding is a process of manufacturing by shaping liquid.Casting is a manufacturing process in which a liquid material is usually poured into a mold, which contains a hollow cavity of the desired shape, and then allowed to solidify.
Before starting to design my mold for this week assignment, I spent a lot of time thinking about what I would have wanted to machine. I had a lot of ideas in mind but those were too complicated to me because of risk behind all the equipments
So I decided to make a star shape for molding and casting.As I am a 10 year old student actually my instructor did all the experiments for me because all the materials I used aree too hot to handle .
Steps for making mold
1.Design the mold.Here I decided to make a star shape. I designed in rhino.
Mill the desing in the wax block.
picture of wax block
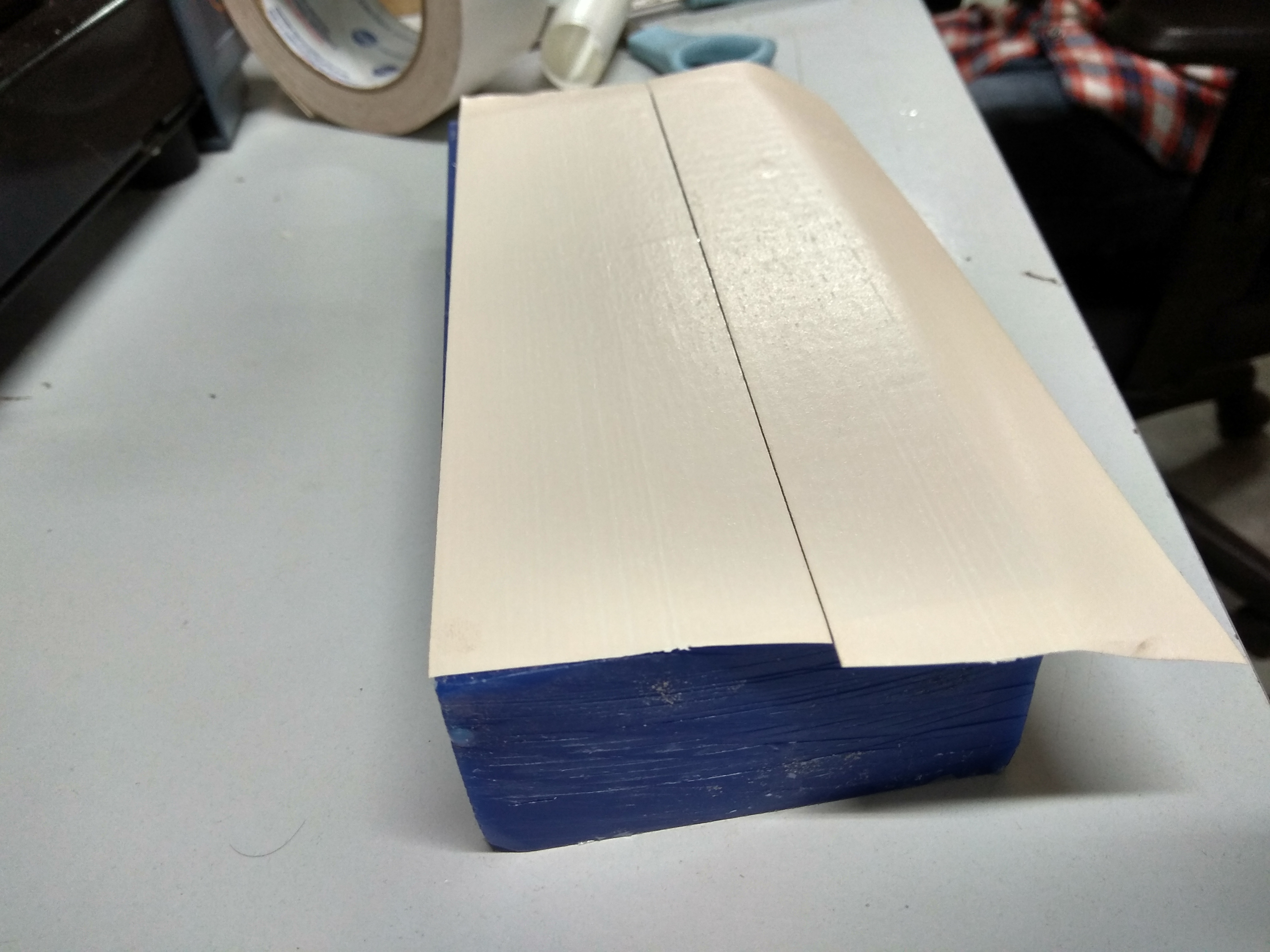
design in fab modules and milling it
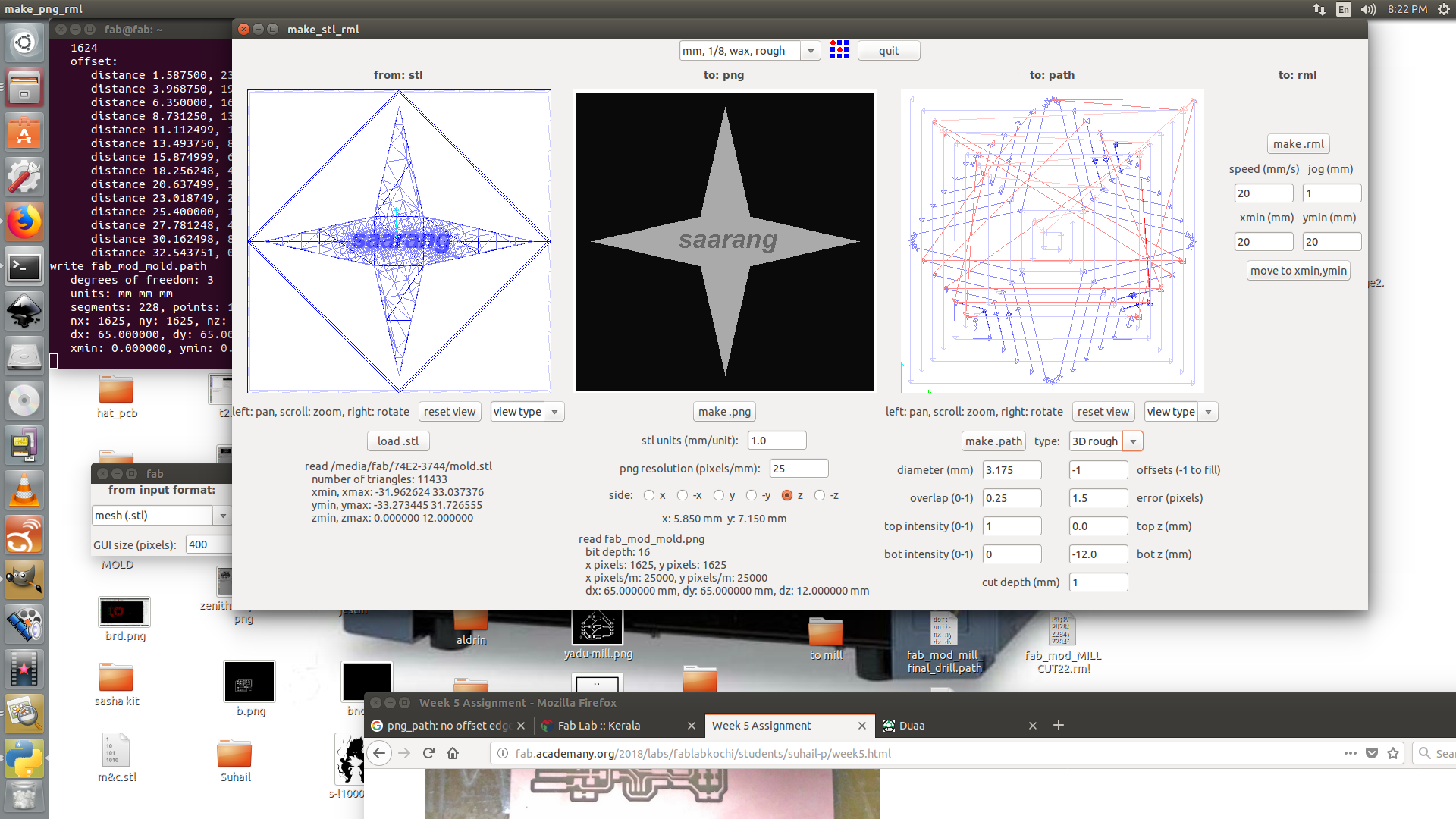
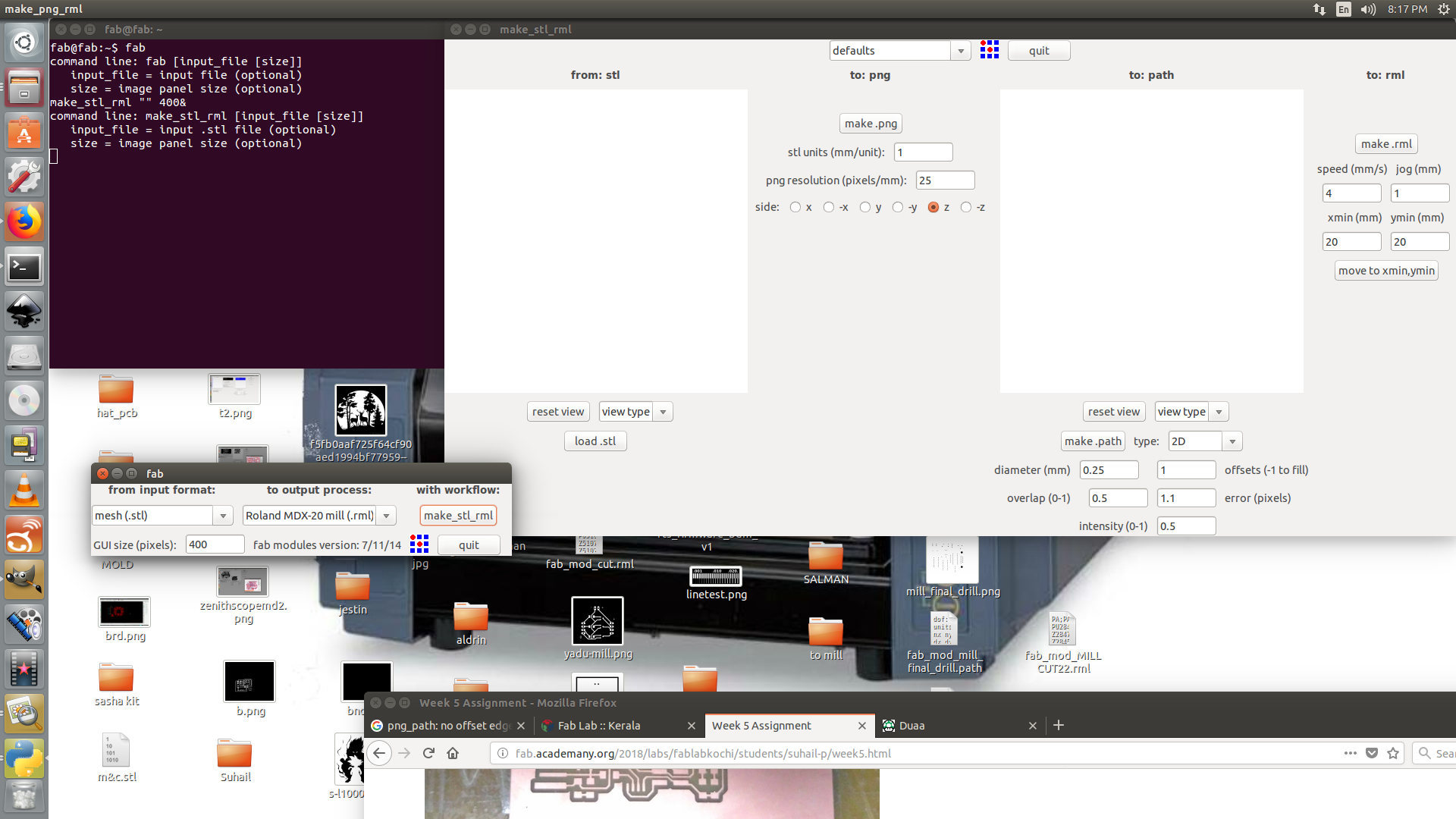
milling the disign in wax block
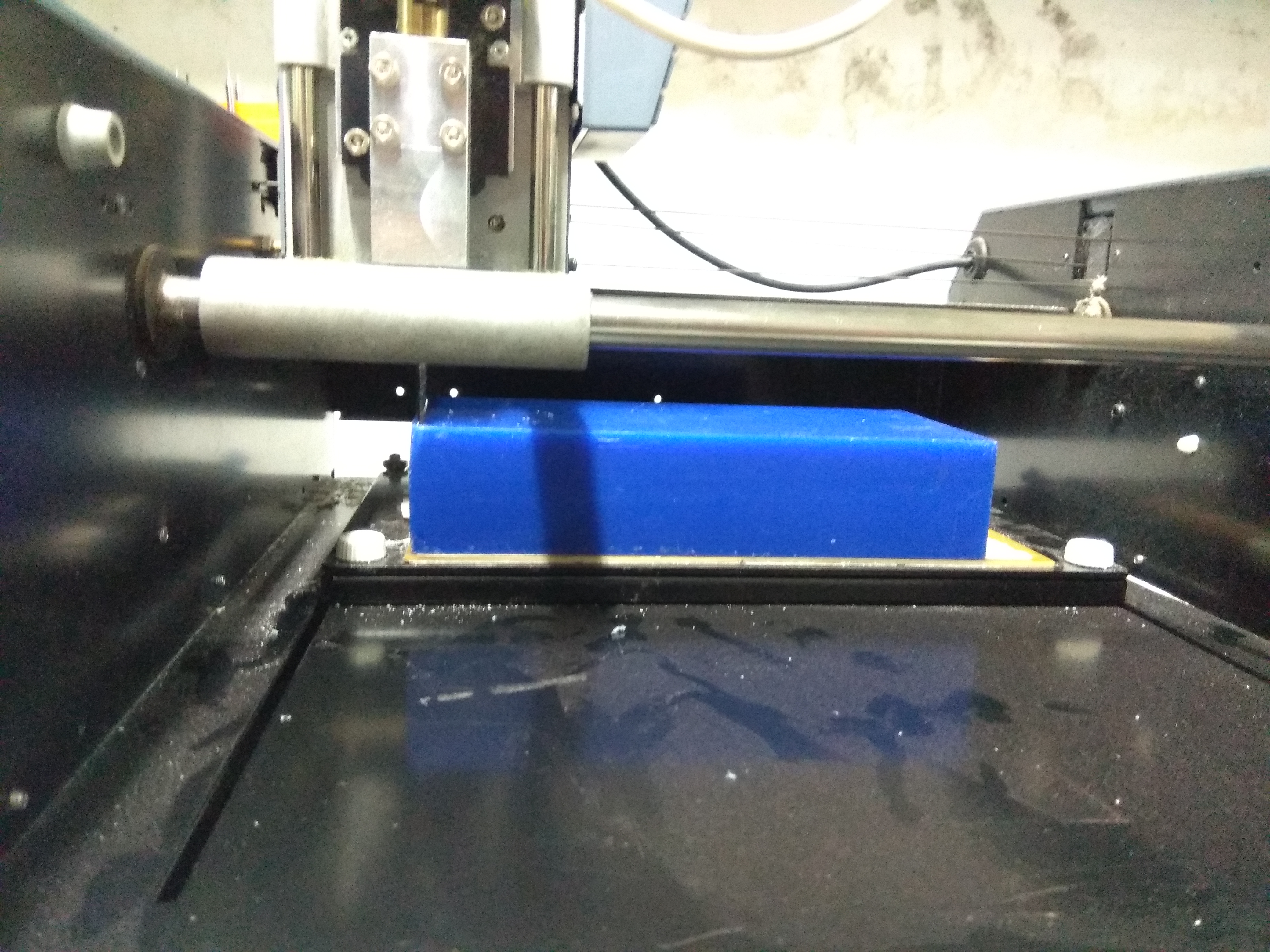
In my design actually I engraved my name also .But unfortunately my finished cut was not proper.so my name was not clear.
moulding
Next step is to make mold.For this I choosed Smooth on Liquid Rubber.
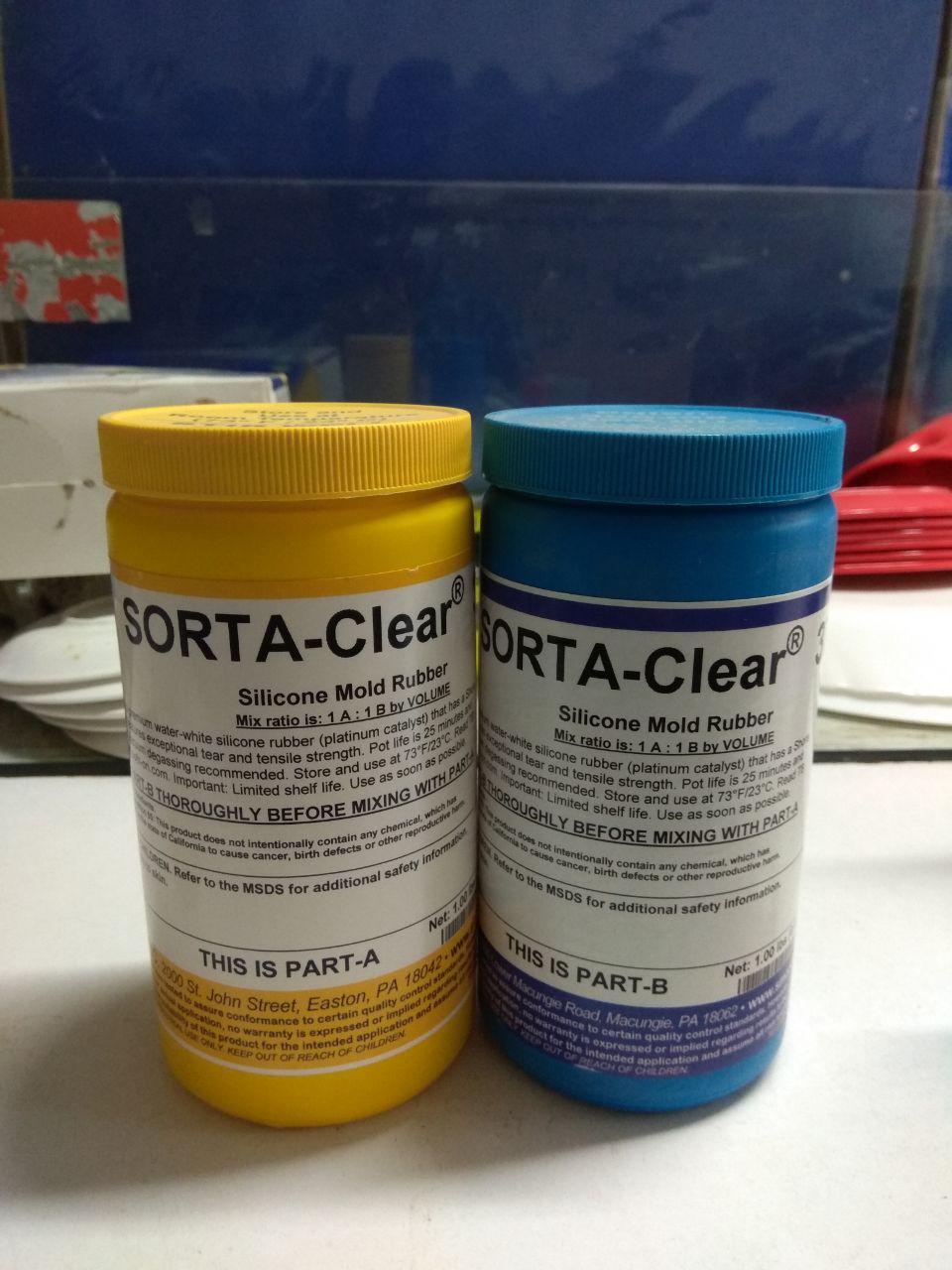
First we have to know the volume of the mold.I followed the instructions from Smooth-On. They can be found here.For this I take some water poured it into the mold.The compound had to be mixed in the ratio 3/100. After that take Part A and Part B in the same amount and mix them. I stirred it for five minute and poured it into the wax block and I waited for 6 hrs to get the mold.
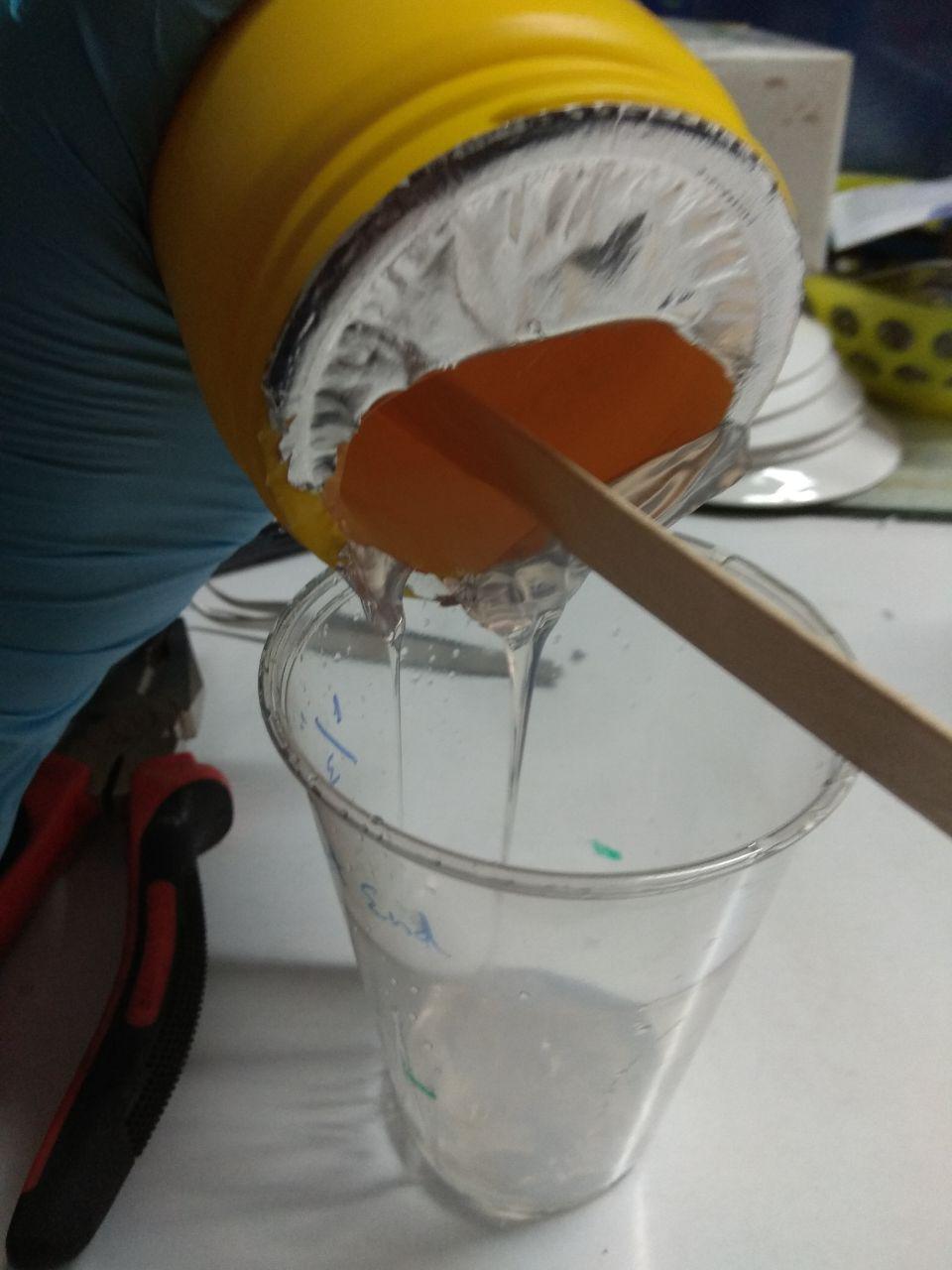
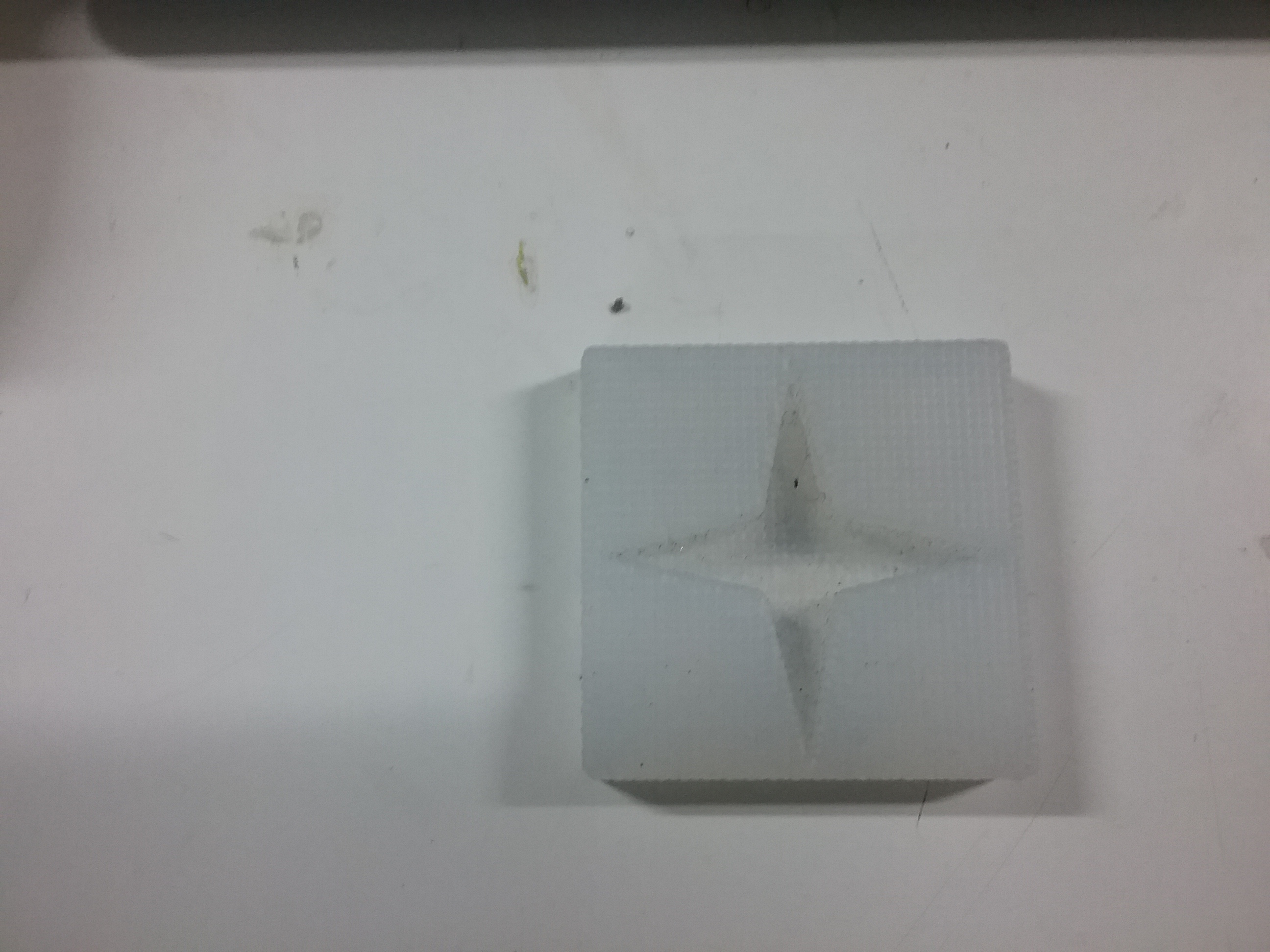
casting
Casting is a manufacturing process in which a liquid material is usually poured into a mold, which contains a hollow cavity of the desired shape, and then allowed to solidify. The solidified part is also known as a casting, which is ejected or broken out of the mold to complete the process. Casting materials are usually metals or various cold setting materials that cure after mixing two or more components together; examples are epoxy, concrete, plaster and clay.Casting is most often used for making complex shapes that would be otherwise difficult or uneconomical to make by other methods.
I used bismuth for casing the mold. The fact that bismuth and many of its alloys expand slightly when they solidify make them ideal for this purpose.it;'scompounds are used in cosmetics, medicines, and in medical procedures. As the toxicity of lead has become more apparent in recent years, alloy uses for bismuth metal as a replacement for lead have become an increasing part of bismuth's commercial importance.
As it is too hot to handle we should take safety measures
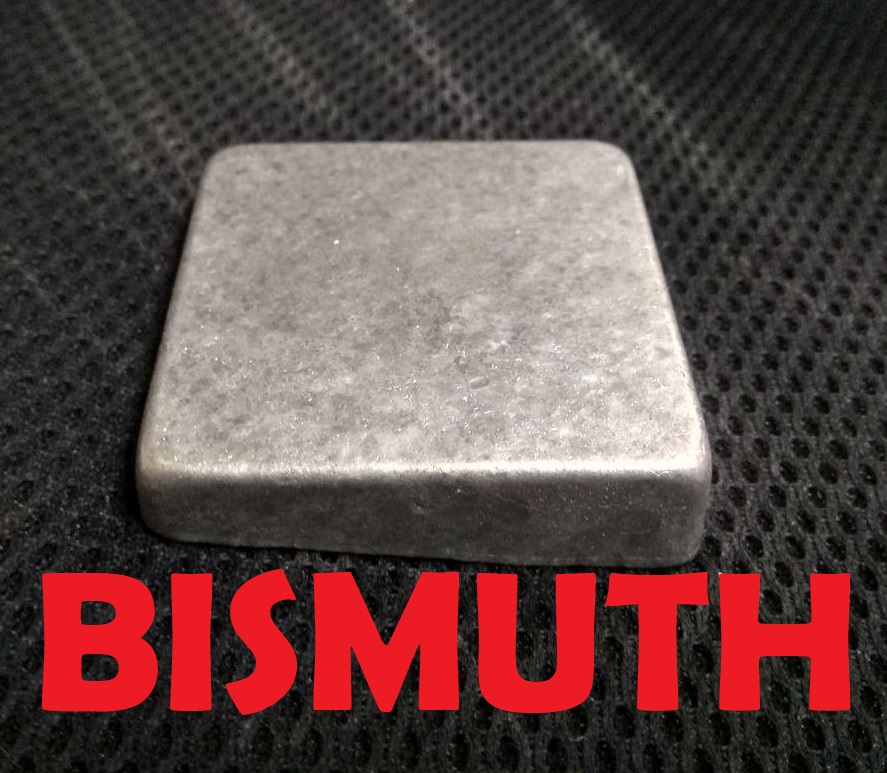
First melt the bismuth in furnace.We are using Vulcan Muffle Furnace in the lab.Bismuth piece was put into the furnace and heated at 400 degrees.After melting the liquid bismuth is poured into the mold and wait for 1 hr and then got the result.
My instructors helped in all my way because I am handling with very high temperature.
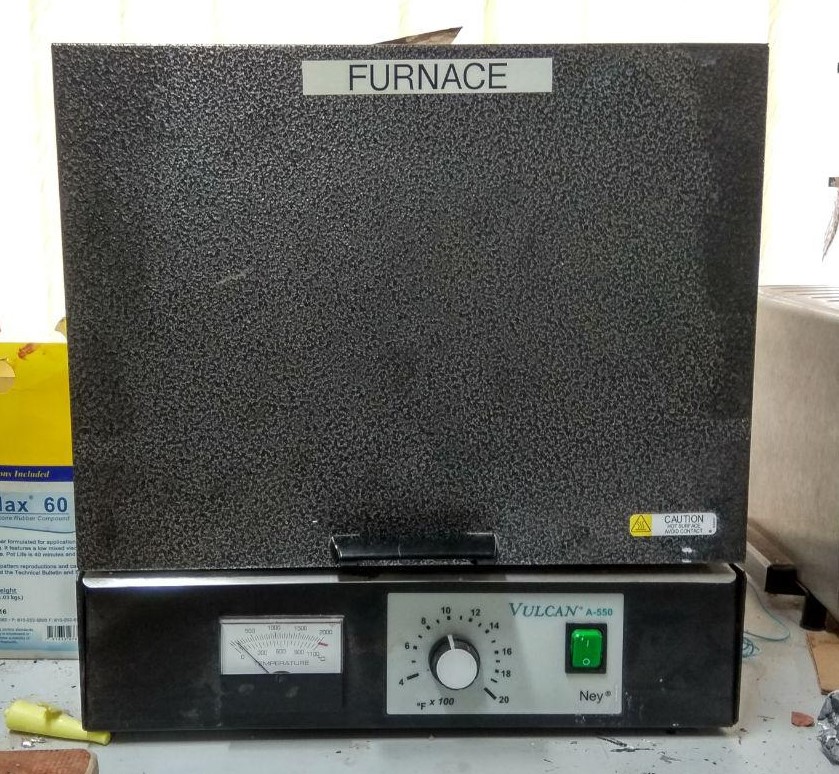
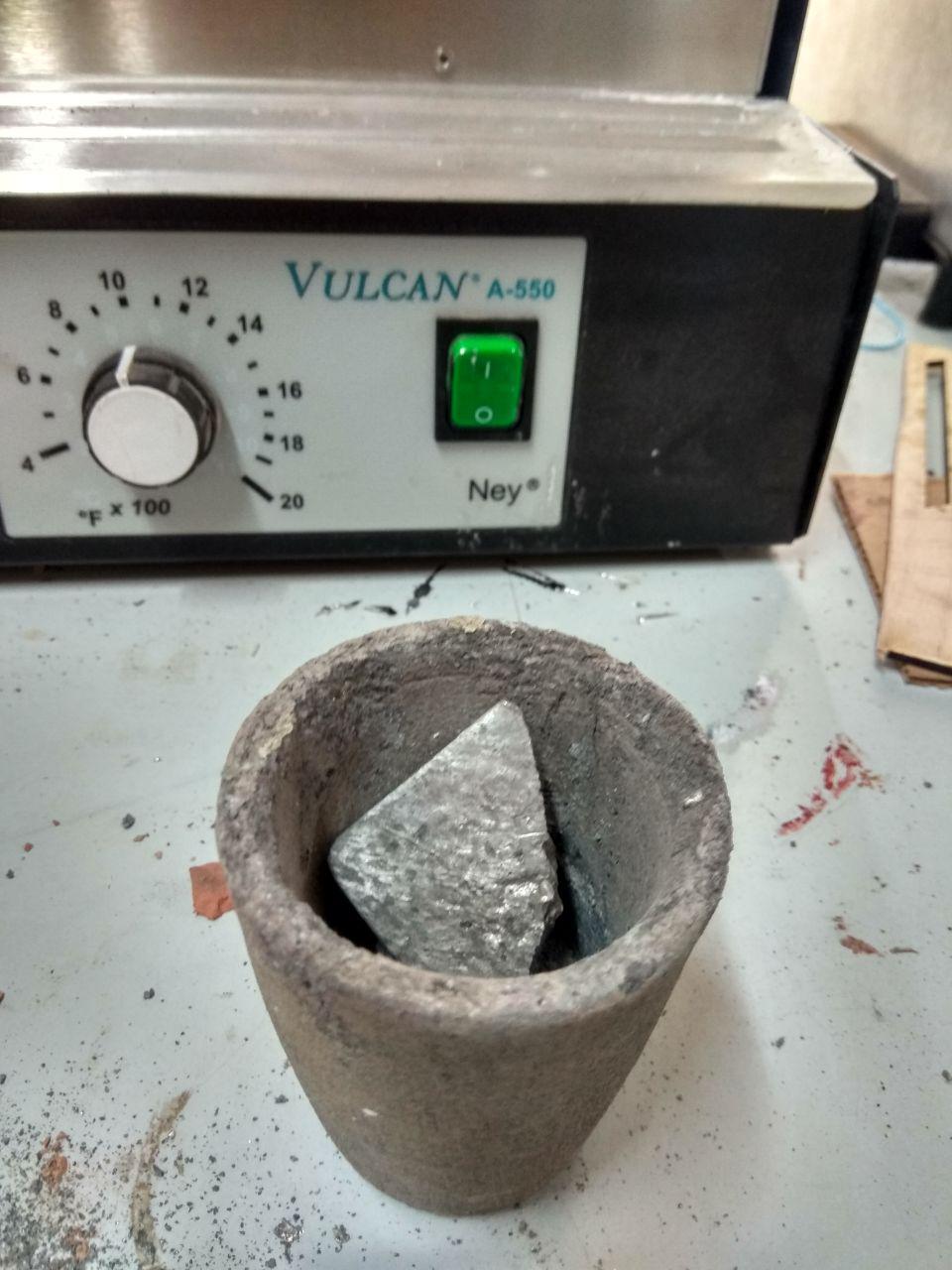
final output
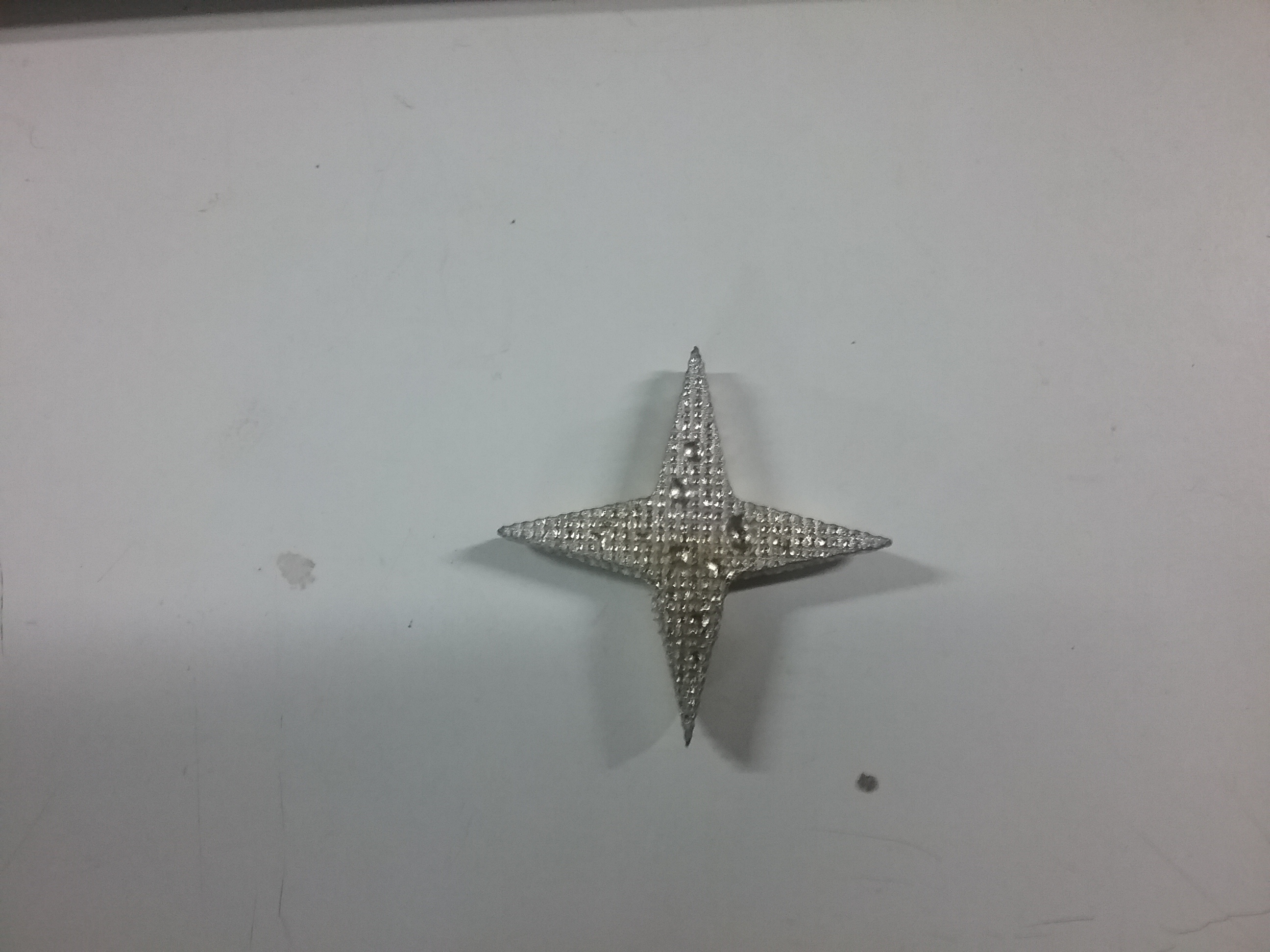
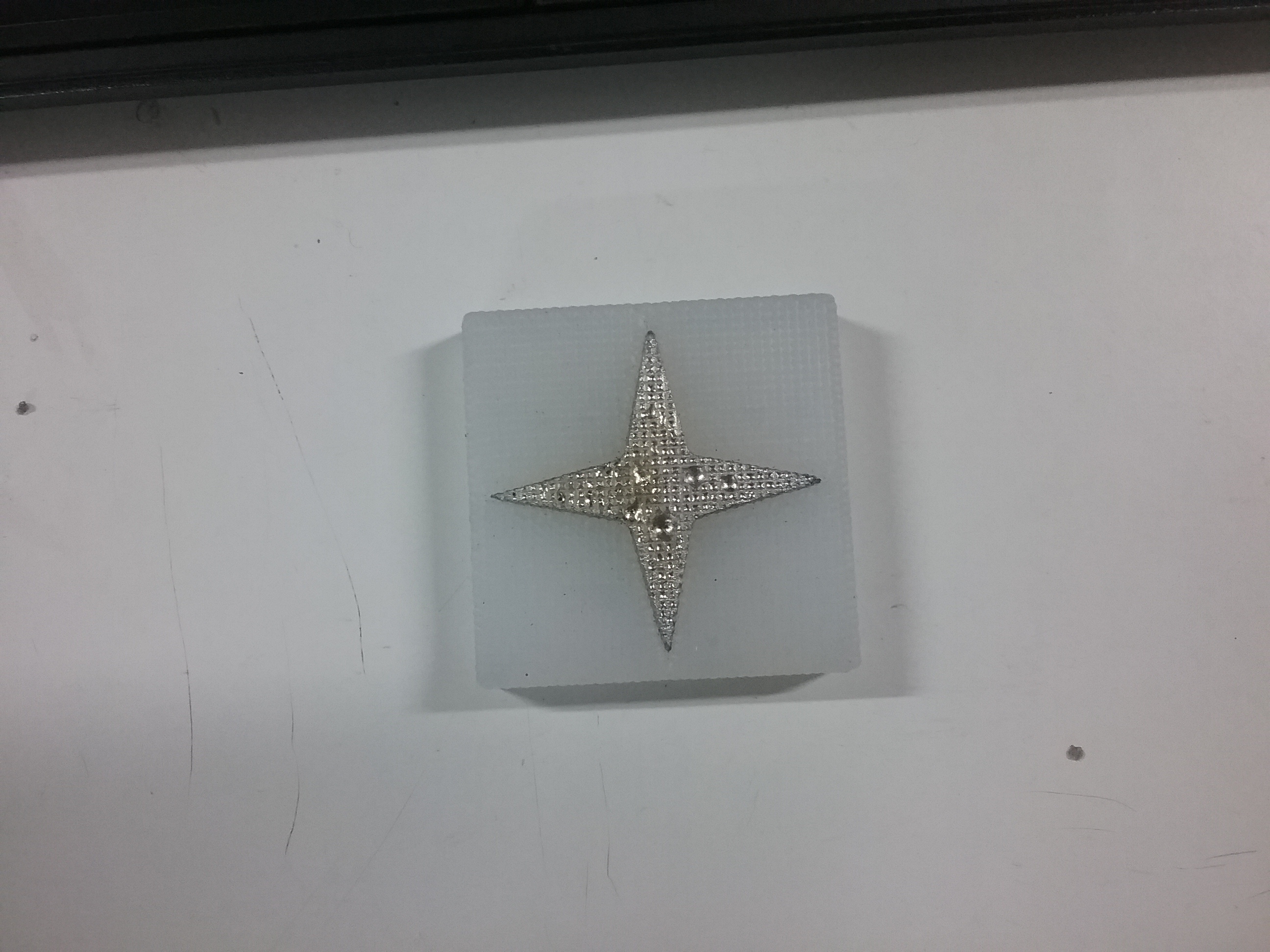