Composites (Page 2 of 2)
Continue from Composites Write up - Part 1
Step 5: The Real Deal, casting the Composites Stool
I could see most people were having 2 problems making the composites
1) the model doesn't come away from the composite so that's why I used a layer of epoxy,
5 layers of wax and Vaseline on the model.
2) cling film with pin holes punched through it has been used as a perforated film
between the outer layer of the material (exterior of the final composite) and the breather
layer. From what I can tell people can't remove the cling film from the composite though.
So I decided to use grease proof paper with holes punched into it instead.
The epoxy resin was Gurit's SP115 which gave me 30 minutes working time.
The ratio was mixed in 3:1 if measuring by weight.
I used 501 of resin with 167 of hardener which was perfect for the amount of material I used.
I used
- 2 full layers of burlap and then 1 layer of burlap that was cut into strips and laid across the body.
All soaked in epoxy.
- the final layer is cotton fabric with a pattern for the outside to have a different aesthetic.
This wasn't soaked in epoxy because there was enough to come through the other layers
and soak into this layer. I tested this with a practice run before.
Order of materials/layers:
- mold (with 1 layer of epxoy,
- 5 layers of wax & 1 layer of Vaseline)
- Burlap (soaked in epoxy)
- Strips of Burlap & laid in different directions on the mold (soaked in epoxy)
- Burlap (soaked in epoxy) Aesthetic cotton fabric (not soaked in epoxy)
- Greaseproof paper (with holes made it with a scalpel)
- 4 layers of Burlap as a Breather Layer (some people use a towel)
- Vacuum Bag

Step 6: Getting the mold out of the composite
The greaseproof paper with hole it it worked really well and came off very easily.
I thought I might have more luck getting the mold out of the compsite because I had added epoxy,
5 layers of wax and vaseline to the model. It was still quiet a fight to get the mold out though.
Strangely parts of the model came out ok. Another reason I think it was hard to get the model out was
because the model was made up of 3 layers of foam. Even though the layers were relatively secured together
epoxy got in between the layers of foam. This meant the composites then had epoxy undercut in it, going into the
model.
The Final Piece
A little bit too low and the surface finish isn't perfect but it's strong and well able to hold my weight.
Reflections on Composites Project
Problems:
- Burlap material was far too thick and stiff to wrap onto the shape. It was also very difficult to get the layers of material to lie over each other securely because of its stiffness. I've used glass before and it is far easier to overlay layers of glass and get them to take the shape of the mold.
- Couldn't get the mold out of the composite in one piece. I can see one reason for this. Because it was a 3 part mold the epoxy got in between the layers of foam which made it hard to get out of the composite. The mold was coated in 5 layers of wax and 1 layer of Vaseline. The strange thing is parts of the mold didn't get stuck to the composites and other parts did get stuck. The flat surface at the back didn't get stuck to the composite but a lot of the rest of it did.
- The final layer that wasn't soaked in epoxy should have soaked up epoxy for the layers underneath. Most of it did but some of it didn't and is just material without any epoxy. So in future I would stick to the norm and soak this layer in epoxy as well.
What did work well
- using the greaseproof paper with holes in it worked well as a perforated film between the composite layers and breather material. It came away very easily from the composite. It was probably the easiest thing about the process.
Things I'd change if I was doing this again.
- I'd look up more patterns and how to cut the material in the best way to be laid and wrapped onto to the shape.
- Try a shape with less sharp angles as the material doesn't easily wrap around them. I guess this is why most people do a bowl or sphere of some kind.
- I would use material that is much thinner and less stiff so I can really get it to form onto the shape of the mold, like glass.
- If I was using foam again I'd try using packaging tape on it or more layers of epxoy resin on the foam before coating it in wax. I'd also use a lot more Vaseline on the mold before casting. These steps should help get the mold out of the composite afterwards.
- A 2 part mold would have been better to have pressure on the material from both the top and bottom.
Download All Files
Download the STL files for the 3D model of the stool
here
Download the FNC files for milling out the model here
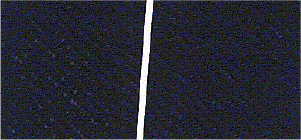
Week 11, Apr 3