Group Assignment
Group Assignment- Review the safety data sheets for each of your molding and casting materials
- Make and compare test casts with each of them
- Compare printing vs milling molds
Individual Assignment
- Design a mold around the process you'll be using
- Produce the mold with a smooth surface finish that does not show the production process
- Use the mold to cast parts
Hero Shot
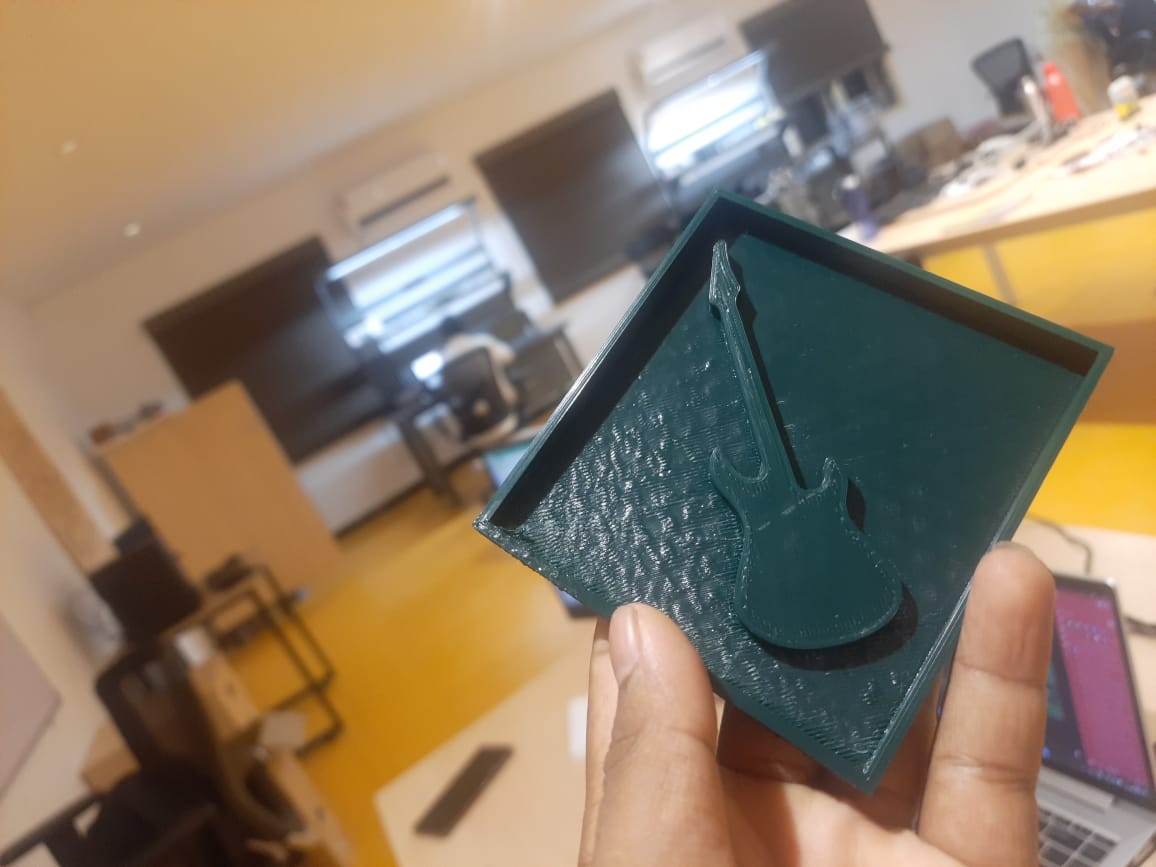
Designing the Mold
Molding and Casting – Mold Design and Preparation
For my molding and casting assignment, I designed a 3D mold specifically tailored to the casting material and process I intended to use. I selected a guitar-shaped model—a simple yet detailed part—to demonstrate the fidelity of the mold and the surface quality of the final cast. The model was created using SolidWorks, considering essential mold design principles such as undercuts, draft angles, and parting lines to enable easy and damage-free demolding.
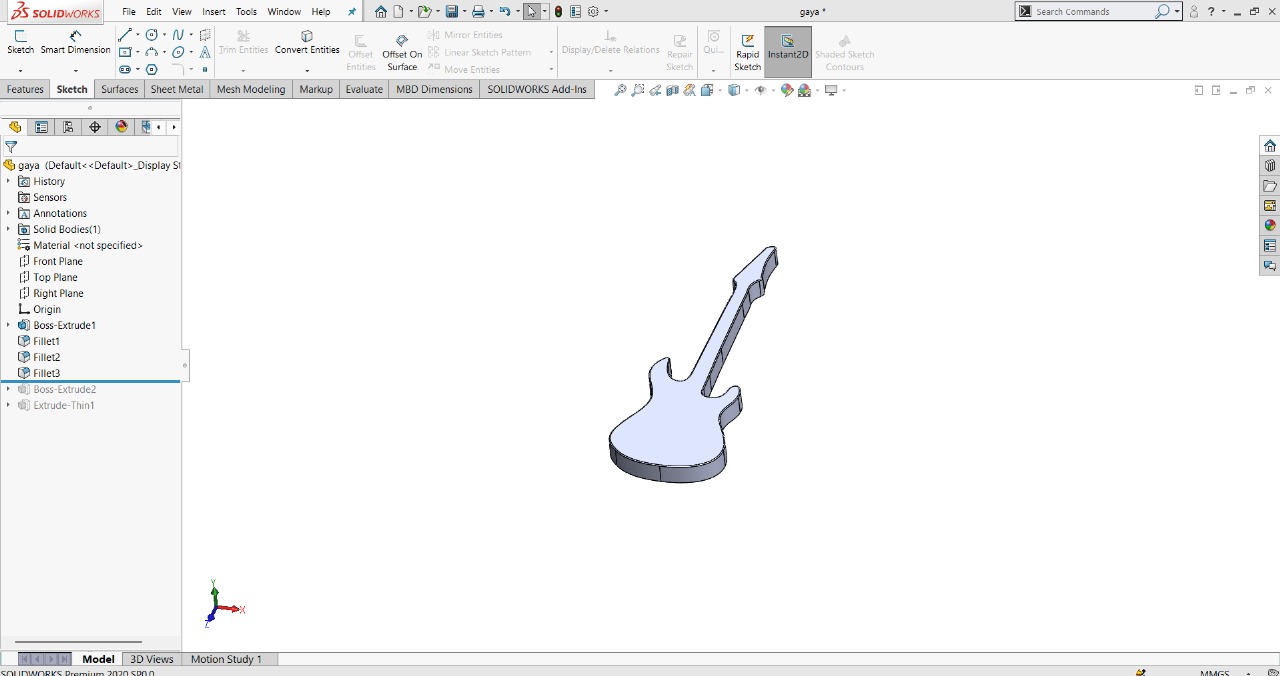
To streamline the process, I chose a single-part mold design, allowing for straightforward removal of the cast without requiring a complex multi-part setup. The mold incorporates a base plate .the guitar is fixed directly in the center of the base plate. Its dimensions were optimized to fit within the build volume of theFDM 3D printer used for fabrication.
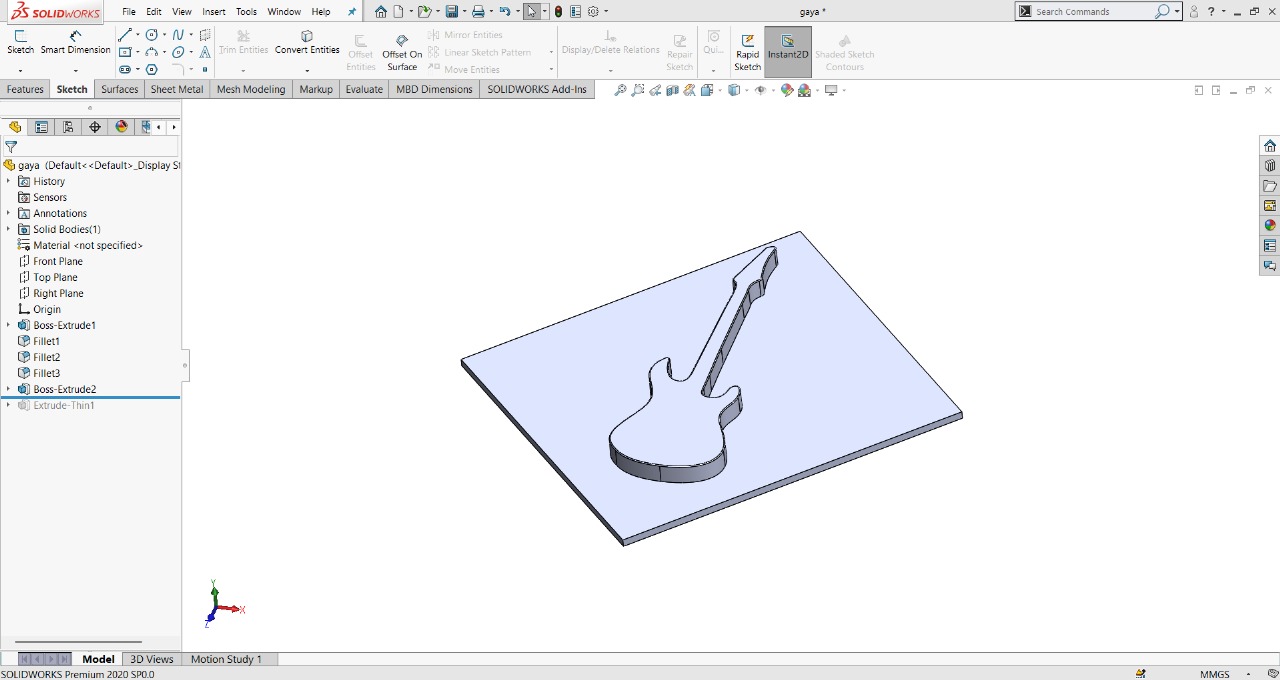
The mold was specifically designed to be 3D printed using an FDM printer. To achieve a smooth surface finish, I optimized the layer height and carefully selected the print orientation to minimize visible layer lines on the critical mold surfaces. The design avoided steep overhangs to reduce the need for support structures, thereby minimizing post-processing. Additionally, I maintained uniform wall thickness throughout the mold to prevent deformation or shrinkage during the casting process.
In the guitar and base plate design, the corners on all four sides were extruded slightly above the top surface of the guitar model. These raised walls serve as a containment boundary to hold the silicone in place while it cures, preventing leakage and helping achieve the desired mold depth and detail.
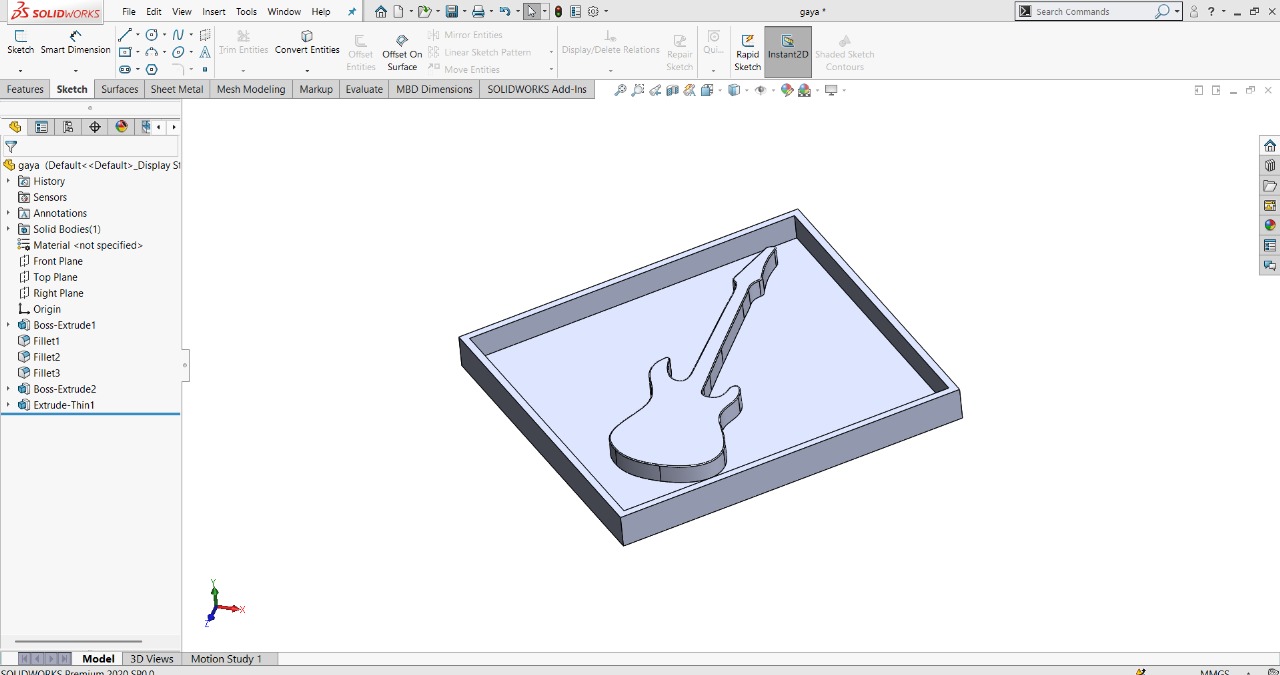
Types of Molding and Casting and Their Benefits
Type | Description | Benefits |
---|---|---|
3D Printed Molding | Using 3D printed parts directly as molds or masters for casting. | Rapid prototyping, customizable, low-cost tooling, ideal for short runs. |
Silicone Molding | Liquid silicone poured over a master (e.g., 3D print) to create a flexible mold. | Captures fine details, reusable, easy demolding, suits complex geometries. |
Resin Casting | Pouring resin into molds (often silicone) to form solid parts. | Smooth finish, accurate, ideal for decorative or functional parts. |
Injection Molding | Molten plastic injected into a metal mold under pressure. | High-speed production, durable parts, excellent surface finish. |
Compression Molding | Material is placed in a heated mold and compressed into shape. | Strong parts, good for composites, lower tooling cost than injection molding. |
Blow Molding | Air blown into heated plastic in a mold to form hollow shapes. | High-volume production of bottles and containers, cost-effective. |
Thermoforming | Heated plastic sheets are vacuum-formed over a mold. | Fast, inexpensive, ideal for packaging and enclosures. |
Plaster Molding | Plaster is used as the mold material, often for ceramics or metal prototypes. | Cheap, good detail, suitable for low-volume or artistic parts. |
Lost-Wax Casting | Wax model is encased in ceramic, melted out, then filled with molten material. | High detail, great for jewelry, precise metal casting. |
I am selecting a 3D printed relief guitar model as the master for silicone rubber molding and resin casting. This model features a shallow raised outline of a guitar—including the body, neck, and headstock—on a flat base. Its low-profile design ensures easy silicone flow, smooth demolding, and accurate resin replication.
Review of Safety Data Sheets (SDS)
As part of our group assignment, we carefully reviewed the Safety Data Sheets (SDS) for each of the molding and casting materials we planned to use. The primary materials included:
- RTV Silicone Rubber: Safe to use with proper ventilation; avoid skin and eye contact.
- Epoxy Resin: Requires gloves and mask; can cause skin irritation and respiratory issues if inhaled.
- Polyurethane Resin: Must be handled with care; reacts with moisture and requires use in a dry, well-ventilated area.
- Plaster of Paris: Safe in dry form, but can generate heat when curing; use gloves to prevent skin burns.
Test Casting and Comparison
We created small test casts using each material to compare their properties and casting quality. Below are our observations:
Material | Surface Finish | Cure Time | Flexibility | Detail Reproduction |
---|---|---|---|---|
RTV Silicone | Smooth and flexible | 4–6 hours | High | Excellent |
Epoxy Resin | Glossy and hard | 12–24 hours | Low | Very Good |
Polyurethane | Matte finish | 15–30 minutes | Medium | Good |
Plaster of Paris | Chalky, brittle | 30–60 minutes | Very Low | Moderate |
These tests helped us determine which materials are most suitable for different use cases—epoxy for rigid, clear parts; silicone for molds; and plaster for quick, low-cost prototyping.
3D guitar relief model Design and Creation of 3D Mold
The 3D guitar relief model was designed in SolidWorks with a clean, smooth outline, featuring only the overall shape of the guitar including the body, neck, and headstock. A flat rectangular base was created and the guitar shape was sketched on its surface using spline and arc tools. The shape was then extruded by 1.5 mm to form a shallow relief, ideal for easy silicone molding. Gentle fillets were added to avoid sharp edges and ensure smooth demolding. The final model is optimized for PLA 3D printing on FDM printers like the Flashforge Creator 3 Pro and resin casting application
The mold cavity was 3d print in PLA dark green color filament using a 3D Printer machine. I used Mods for this task and generated the toolpath.
Machine Settings Used:
- Material: PLA (Dark Green Color Filament)
- Printer Model: Flashforge Creator 3 Pro
- Nozzle Temperature: 200–210 °C
- Bed Temperature: 50–60 °C
- Print Speed: 50–60 mm/s
- Layer Height: 0.2 mm
- Infill Density: 20%
- Cooling Fan: On (100% after the first few layers)
- Build Plate Adhesion: Skirt or Brim (recommended for better adhesion)
- Support Material: Enabled (if overhangs are present)
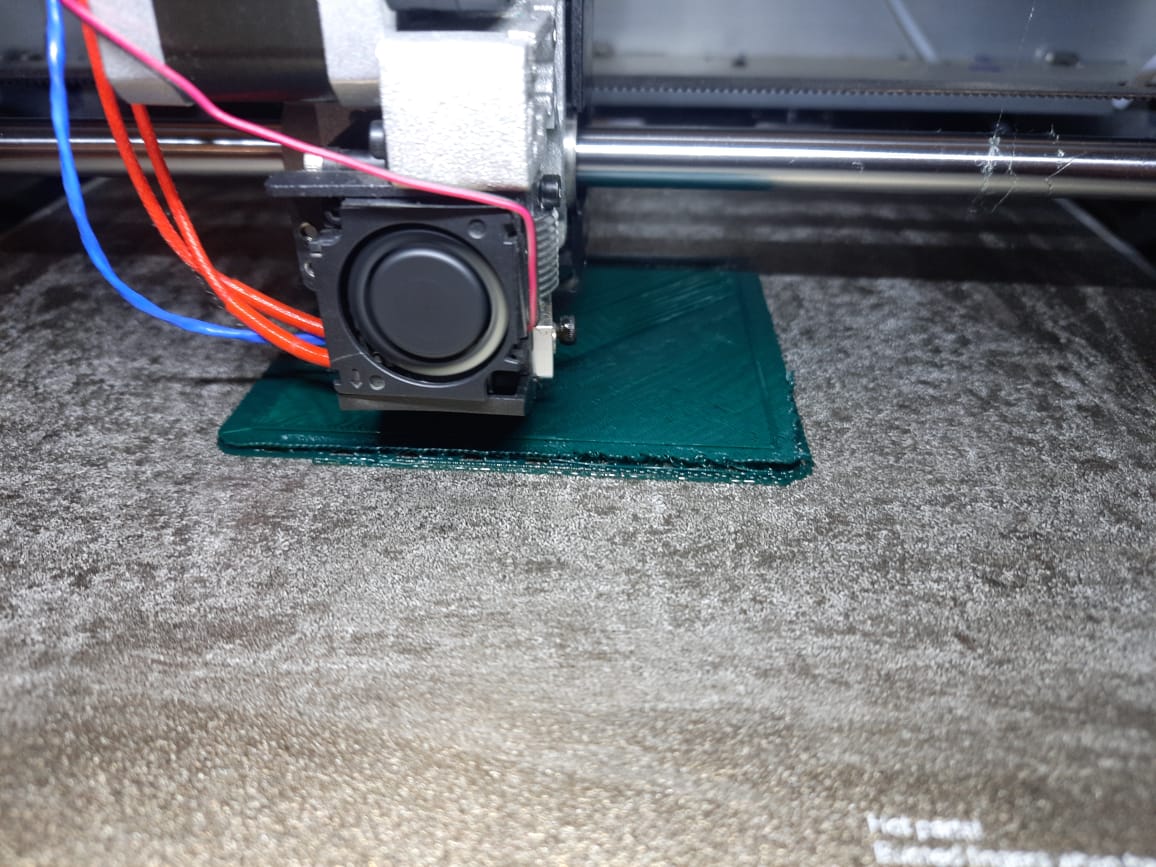
Ensuring a Smooth Surface Finish
To ensure a smooth surface finish after 3D printing using only isopropyl alcohol (IPA) wipes, gently clean the printed part with a lint-free IPA wipe to remove dust, oils, and loose particles. This method is especially effective for enhancing the appearance of PLA and smoothing minor surface inconsistencies without affecting the part’s geometry. Wiping with IPA can slightly soften the outer layer, blending small ridges and improving the overall sheen. Repeat the wiping process evenly across the surface for a consistent finish. While it won’t eliminate layer lines completely, it provides a cleaner, more polished look with minimal effort.
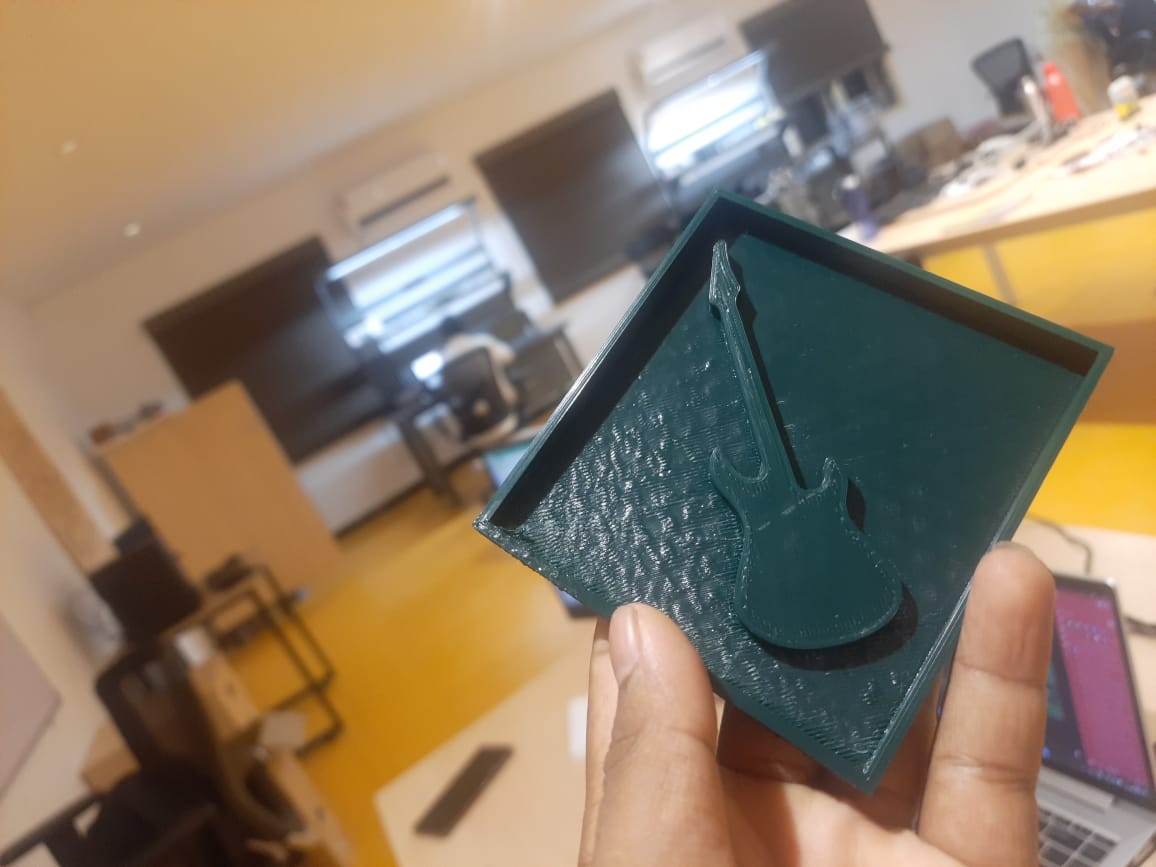
Safe Molding and Casting Process
Safety was a top priority throughout the molding and casting process. Before starting, I reviewed the Safety Data Sheets (SDS) of all materials used, including RTV silicone rubber for mold making and epoxy resin for casting. Proper ventilation, personal protective equipment (PPE), and workspace cleanliness were strictly followed.
Safety Measures Followed:
- Gloves: Nitrile gloves were used to prevent direct skin contact with chemicals.
- Face Mask: A protective mask was worn to avoid inhalation of any fumes during resin mixing and pouring.
- Ventilation: Work was done in a well-ventilated area with windows open and a fan running
- Protective Clothing: An apron was used to avoid spills on clothes.
- Labeling and Storage: All chemical containers were clearly labeled and stored safely after use.
Mold Making Process:
The mold-making process using Siloczest two-part liquid silicone rubber begins by preparing the model and securing it in a mold box. Siloczest has a mixing ratio of 1:50, meaning for every 1 kg of base silicone, 50 grams of catalyst (hardener) is added. Carefully measure both components by weight for accuracy. Mix thoroughly for 3–5 minutes to ensure uniform blending without introducing air bubbles. Pour the silicone slowly from one corner to allow it to flow naturally over the model, reducing trapped air. Allow it to cure as per the manufacturer’s instructions. Once cured, gently demold to reveal a flexible, detailed mold.
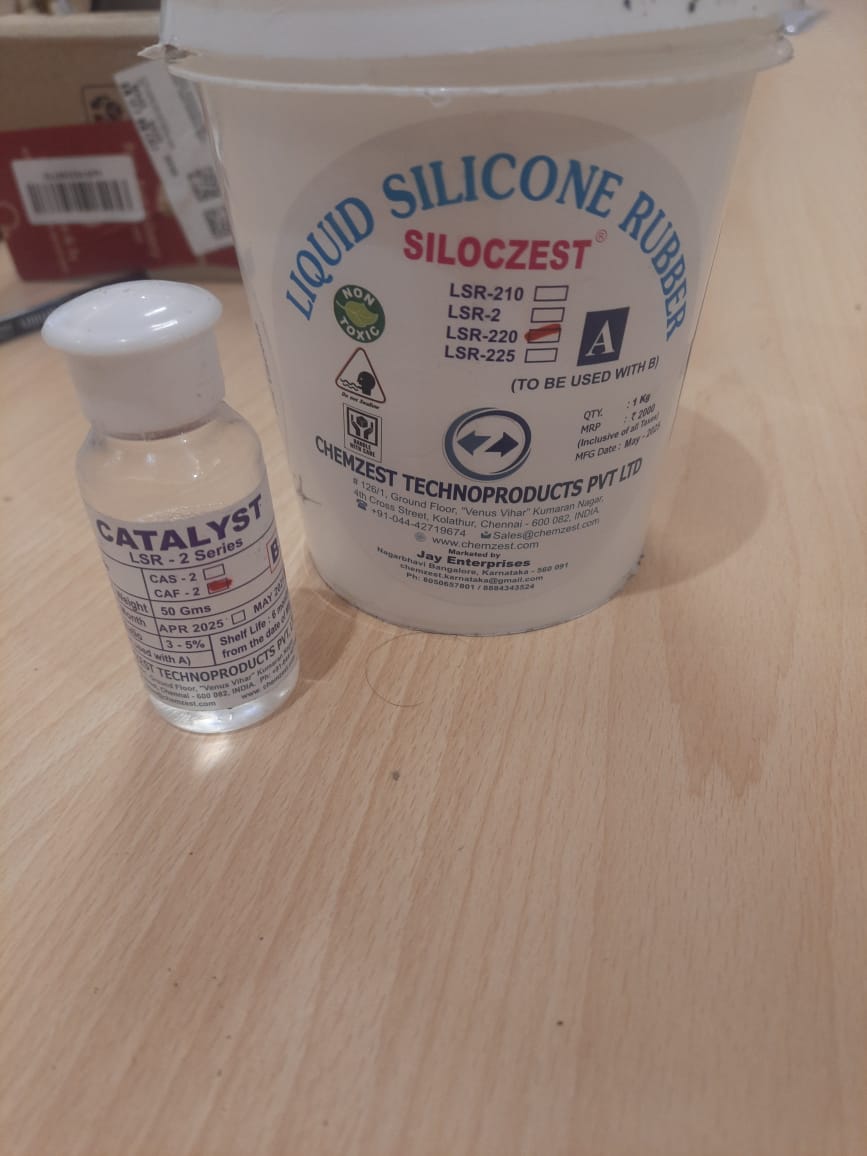
I poured the RTV silicone rubber into a transparent plastic container and measured the total weight as 100 grams. While pouring, I took extra care to avoid spilling, as the silicone is very sticky and difficult to remove once it comes into contact with skin or clothing. Wearing gloves and working on a covered surface helped ensure safety and cleanliness. The thick, viscous nature of the silicone made it important to pour slowly and steadily. I also kept tissues and isopropyl alcohol nearby for quick cleanup in case of accidental drips. The process was completed smoothly without any spills.
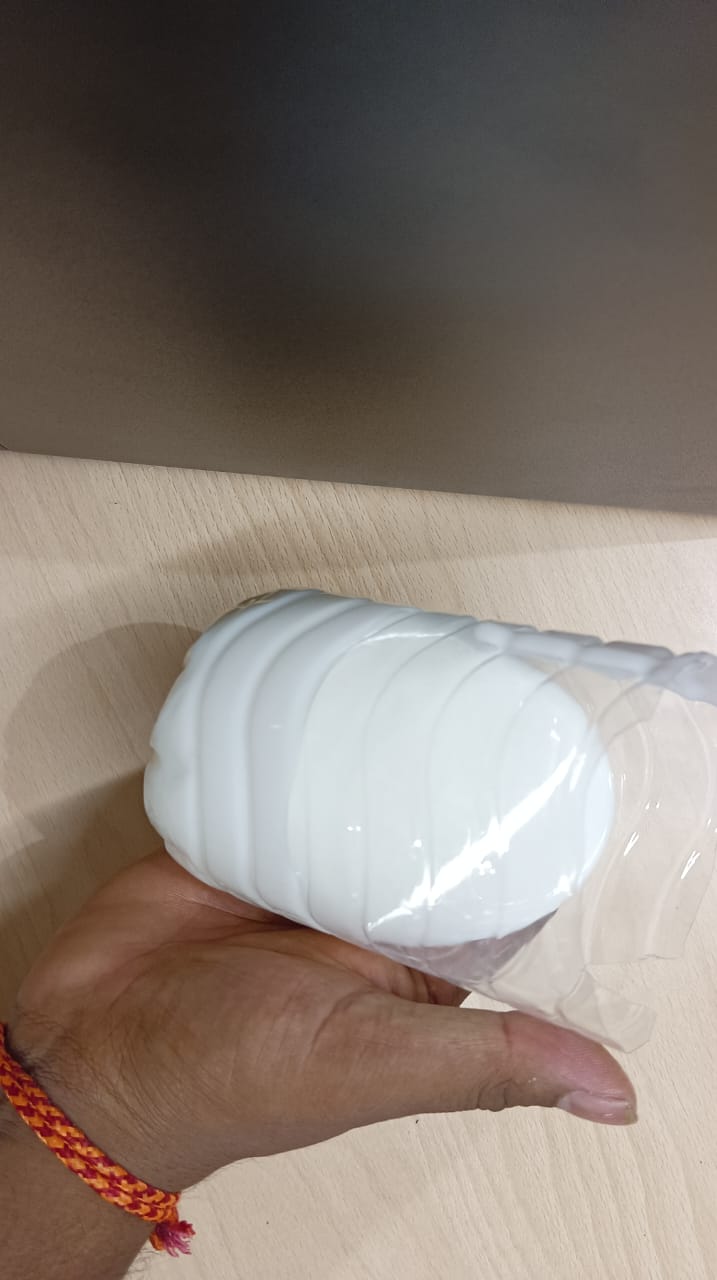
I poured 5% catalyst into 100 grams of silicone rubber, measuring 5 grams of catalyst precisely. The catalyst was added to the base silicone in a clean mixing container. I used a smooth stirring stick and mixed the components thoroughly for about 2–3 minutes. Care was taken to ensure even mixing without creating excessive air bubbles, as proper blending is essential for consistent curing and mold strength.
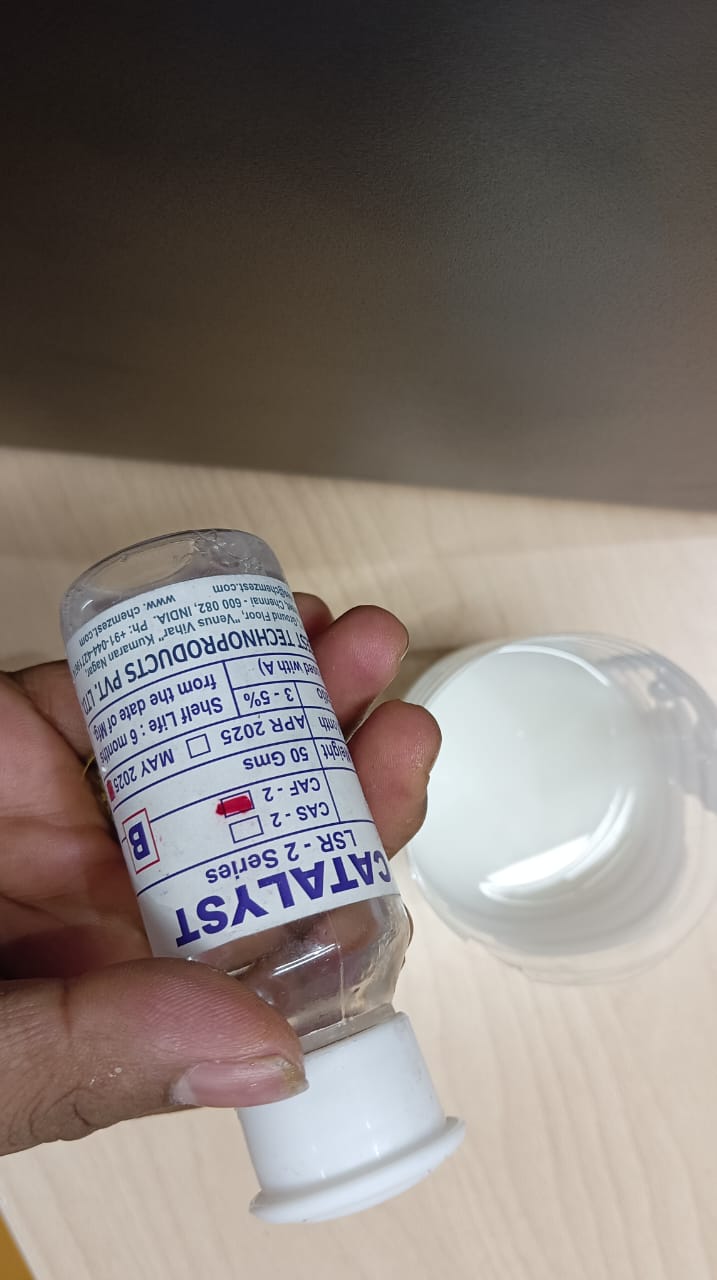
After mixing, I noticed many bubbles in the silicone rubber despite mixing slowly. Pouring directly would ruin the surface finish, so I used a round brush to gently paint the silicone onto the mold. Whenever I saw bubbles, I carefully removed them to ensure a smooth, detailed surface finish.
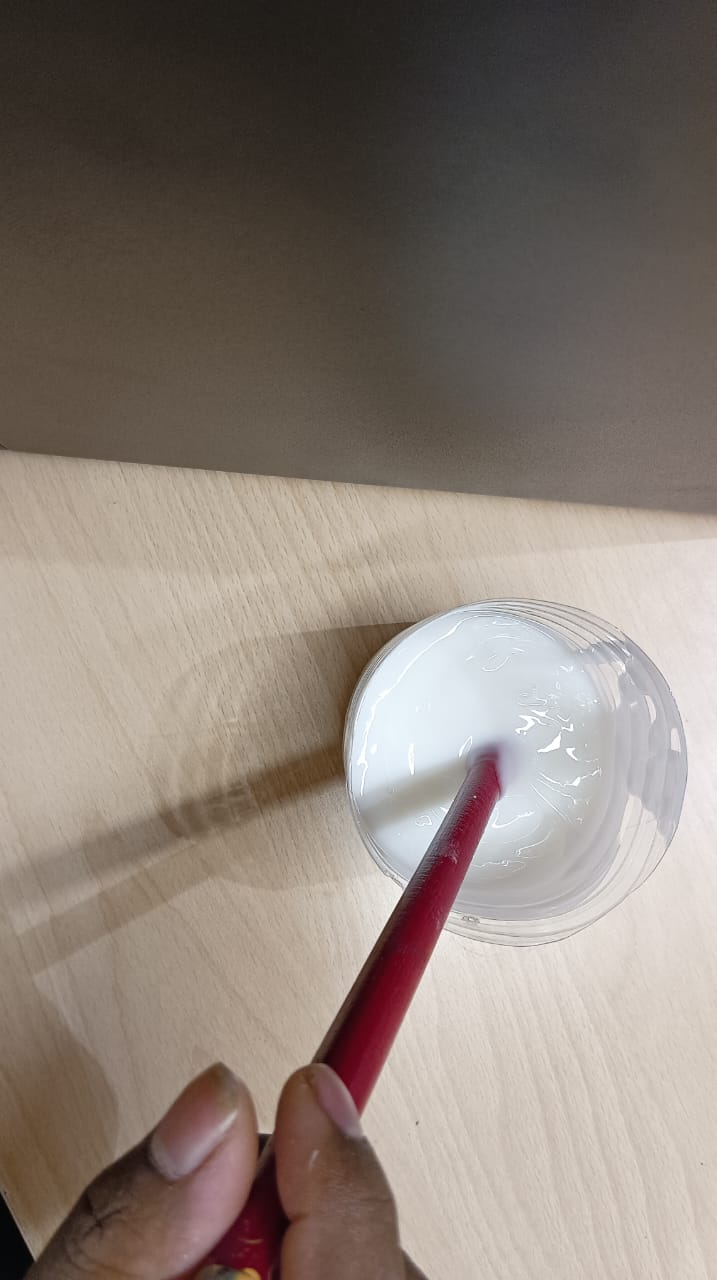
Brushing the first layer helped the silicone settle into fine textures and corners. After this initial coating, I poured the remaining mixed silicone rubber from one corner of the mold box, allowing it to flow slowly and evenly across the surface. This technique reduced the risk of air entrapment. I continued pouring until the entire area was filled, then left the mold to cure undisturbed for best results.
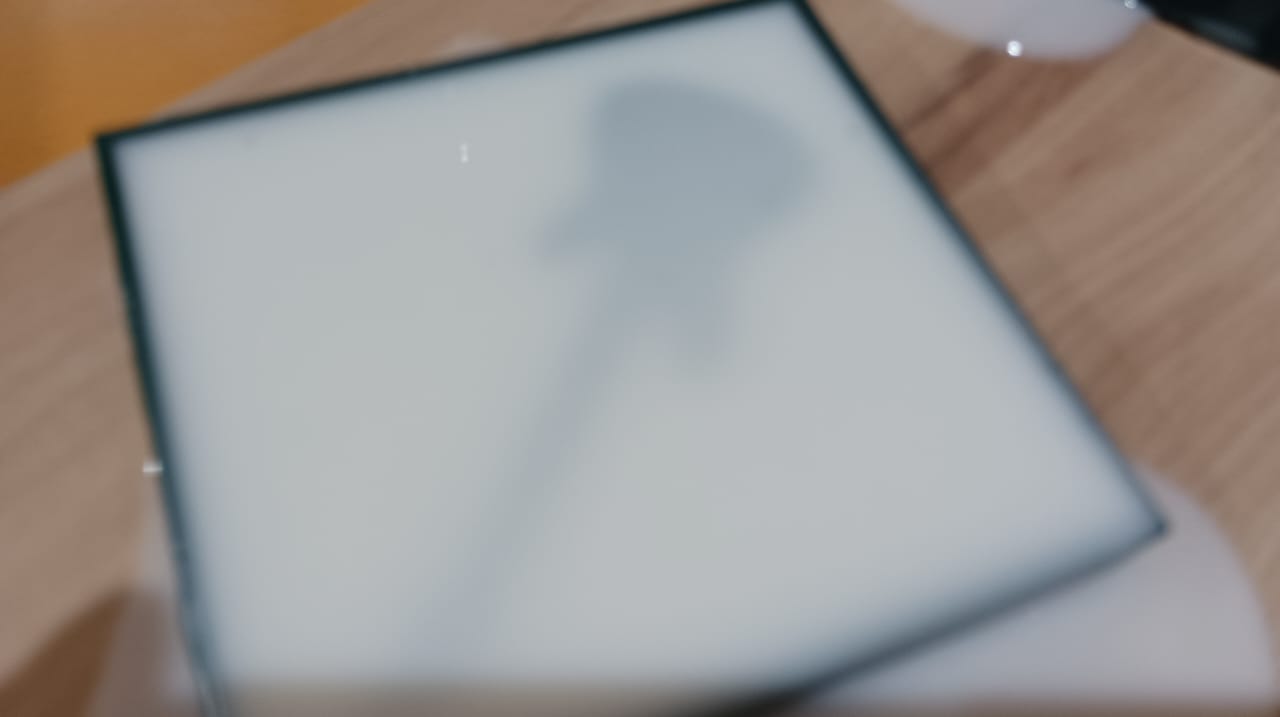
Here is the output of silicone mold
I let the silicone mold fully cure overnight, which was longer than the 8-hour curing time recommended by the manufacturer. I checked the top surface with my hand to confirm it was completely cured. Then, I carefully removed the mold and cleaned the cavity using soap oil and water . After cleaning, I wiped the silicone rubber mold with a clean cotton cloth. Now, the mold is ready for casting.
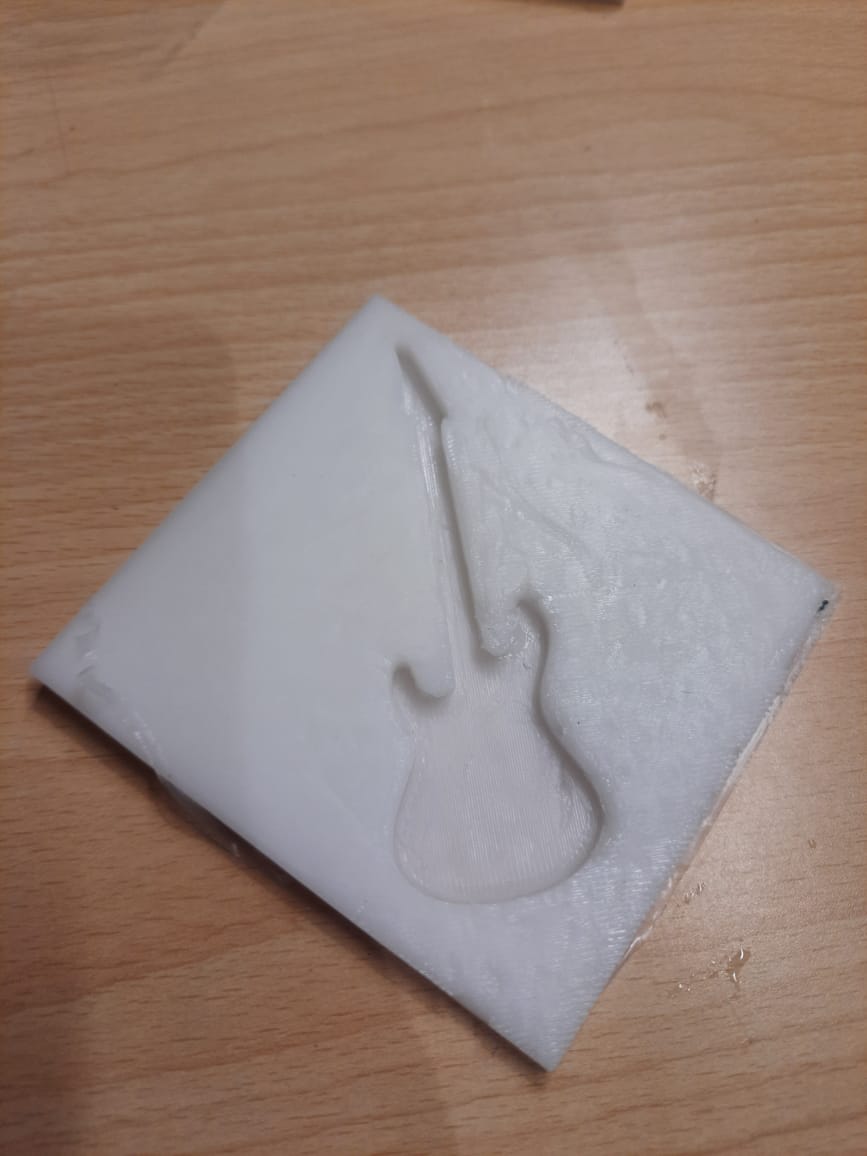
Resin Casting Process:
I am using an all-purpose resin art kit with a 2:1 mixing ratio, meaning two parts epoxy resin to one part hardener. The total kit includes 500 grams of epoxy resin and 250 grams of hardener, designed for accurate mixing and strong bonding. Once mixed, the resin has a thermosetting working time of 45 minutes, allowing enough time for pouring and leveling. After application, the mixture begins to cure and fully hardens within 24 hours. Once cured, it becomes as hard as stone, making it ideal for casting, coating, and decorative work with a durable and glossy finish.
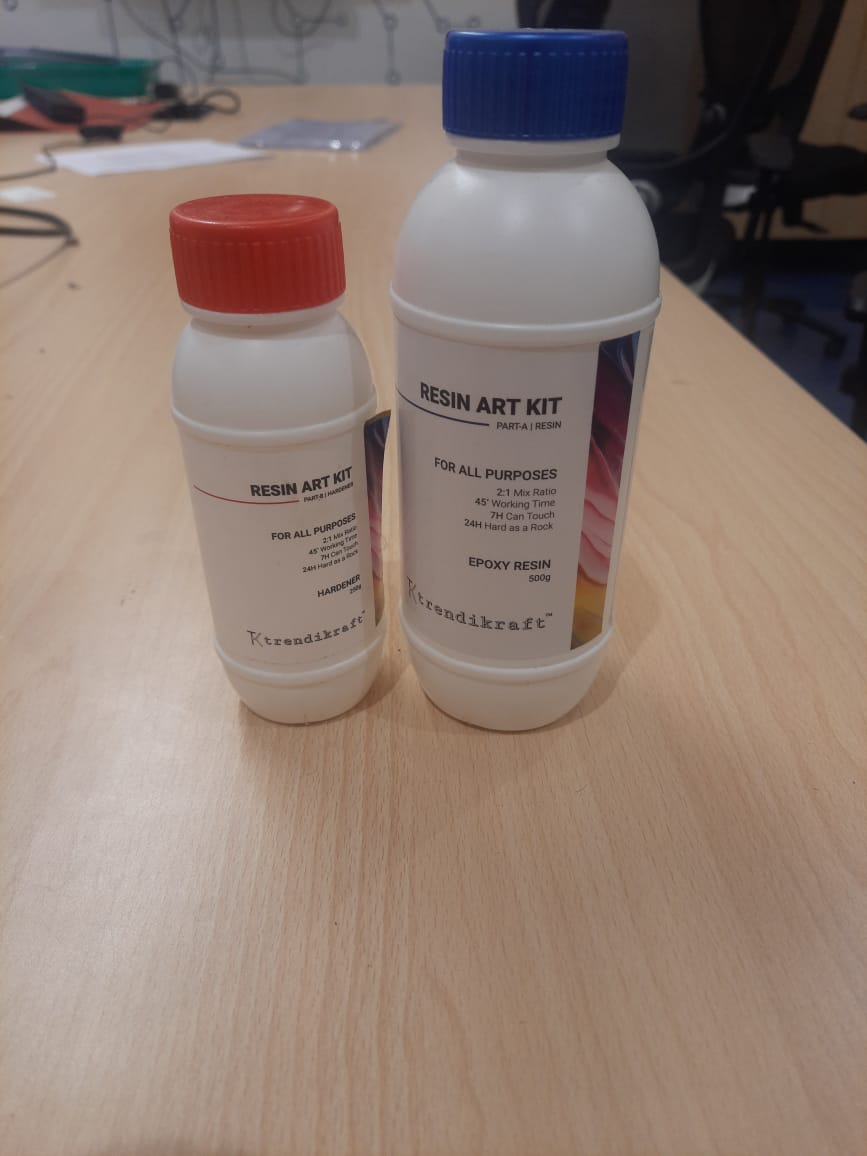
Next, I measured and poured 30 grams of resin using a weighing scale to begin the casting process for my guitar model. Following the 2:1 mixing ratio, I added 20 grams of epoxy resin and 10 grams of hardener into a clean mixing cup.
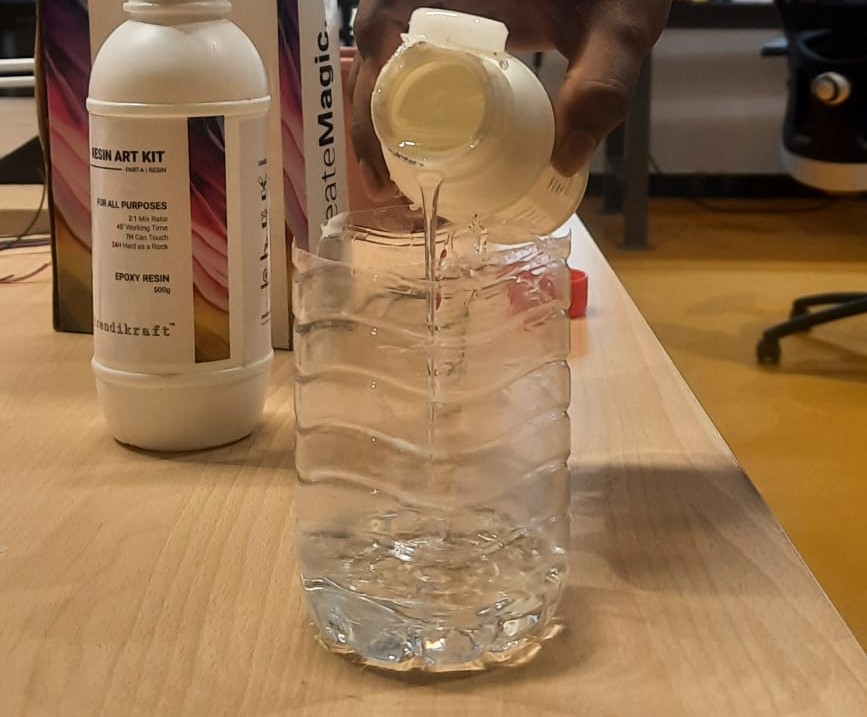
I used a digital weighing scale to accurately measure the two parts of the resin mixture, ensuring the correct 2:1 ratio of epoxy resin to hardener. Precise measurement is crucial to achieve proper curing and to avoid issues like tackiness or incomplete hardening. First, I placed a clean cup on the scale and tared it to zero. Then, I poured 20 grams of epoxy resin followed by 10 grams of hardener. I carefully monitored the weight to maintain exact proportions. This accurate mixing process ensures the final casting will be strong, fully cured, and have a smooth, glossy finish.
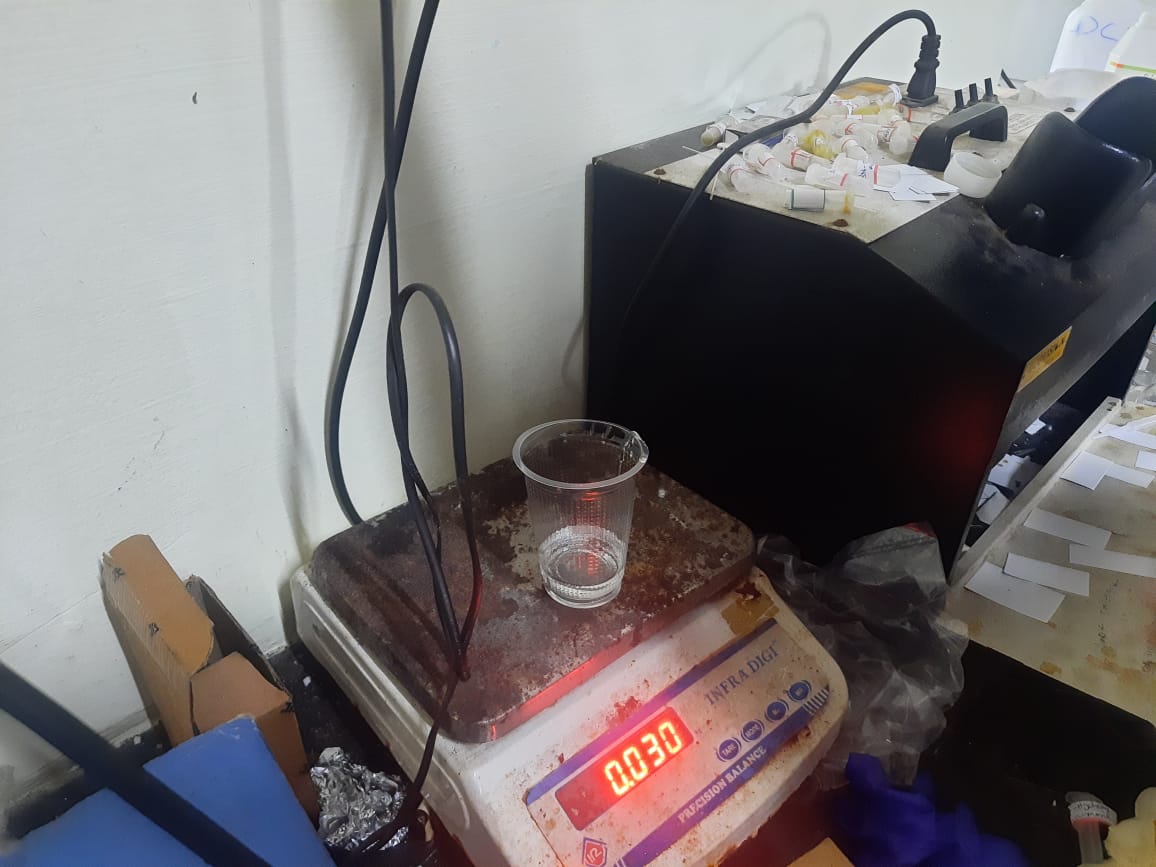
I mixed the two components slowly and thoroughly for a few minutes to ensure a uniform blend and minimize the formation of air bubbles. The mixture was then ready for pouring into the prepared silicone mold for casting.
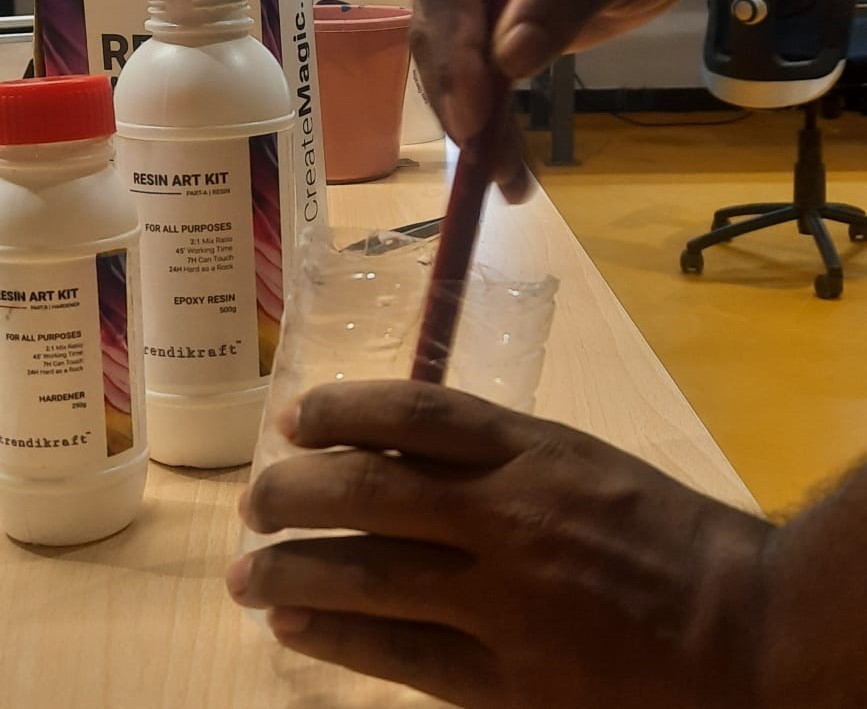
After thoroughly mixing the resin and hardener in the correct 2:1 ratio, I slowly poured the mixture into the silicone rubber mold of the guitar model. I began pouring from one corner to allow the resin to flow naturally and fill all the intricate details of the mold, reducing the chances of air bubble formation. To ensure an even spread, I gently tilted the mold and tapped the sides to release any trapped air. The resin leveled smoothly due to its self-leveling properties. I then left the mold undisturbed, allowing the resin to settle and begin the curing process.
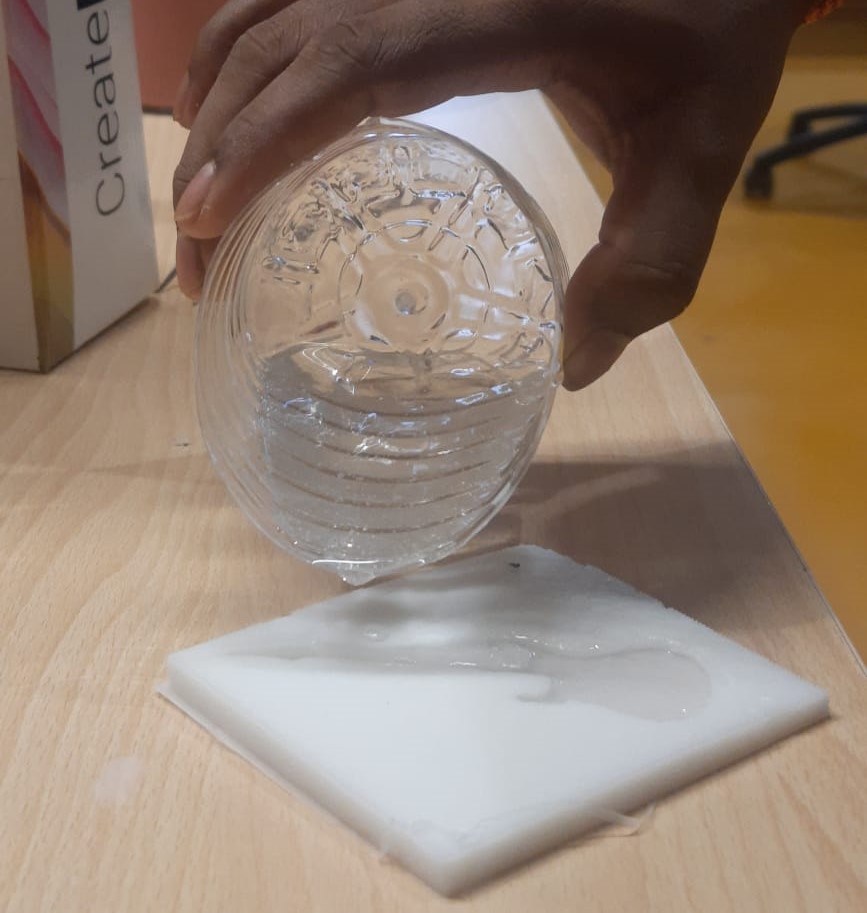
Though the resin is clear and gives a glass-like finish, I decided to embed female header pins, commonly used in electronics, into the casting. This adds a unique aesthetic and functional element to the design, making the piece both visually interesting and potentially interactive for future electronic integration or decoration.
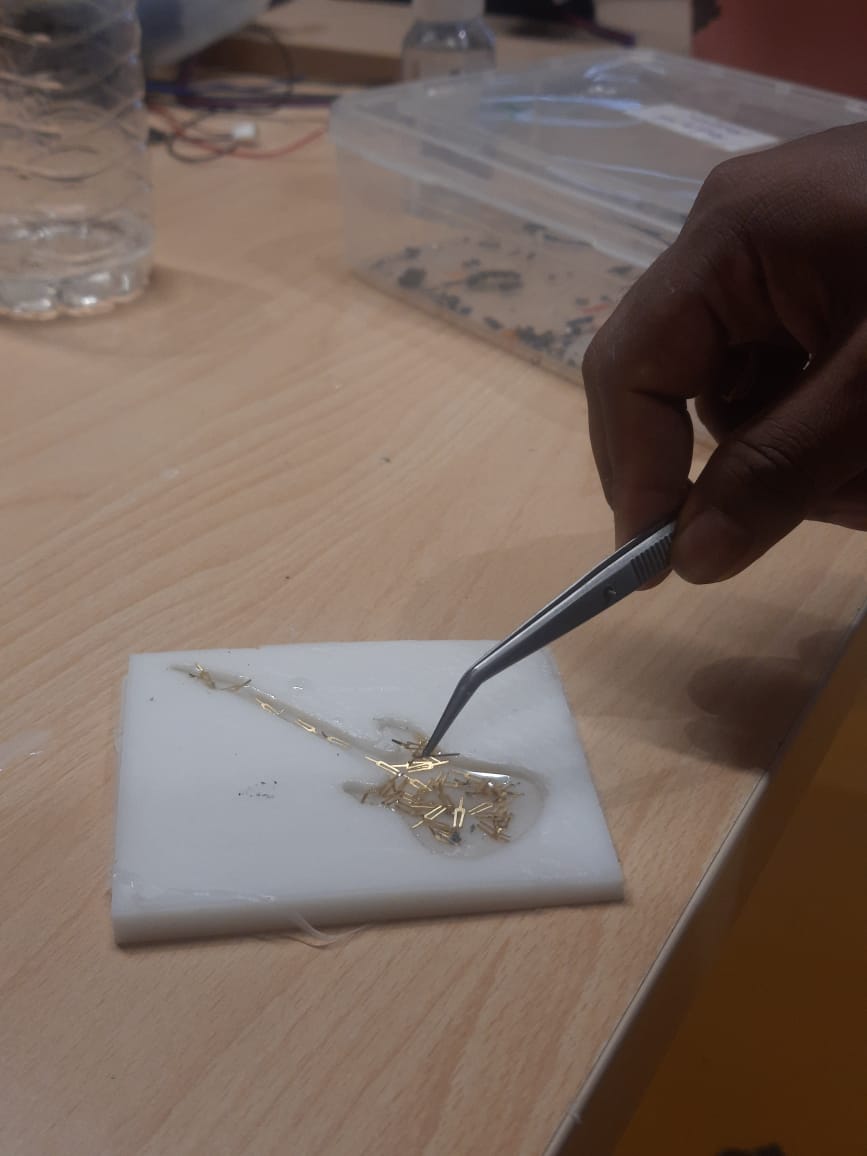
I carefully added the female header pins into the resin using a small picker tool. This allowed me to place them precisely in the desired position without disturbing the surface or creating air bubbles. Gentle handling ensured they stayed aligned and fully embedded as the resin began to cure.
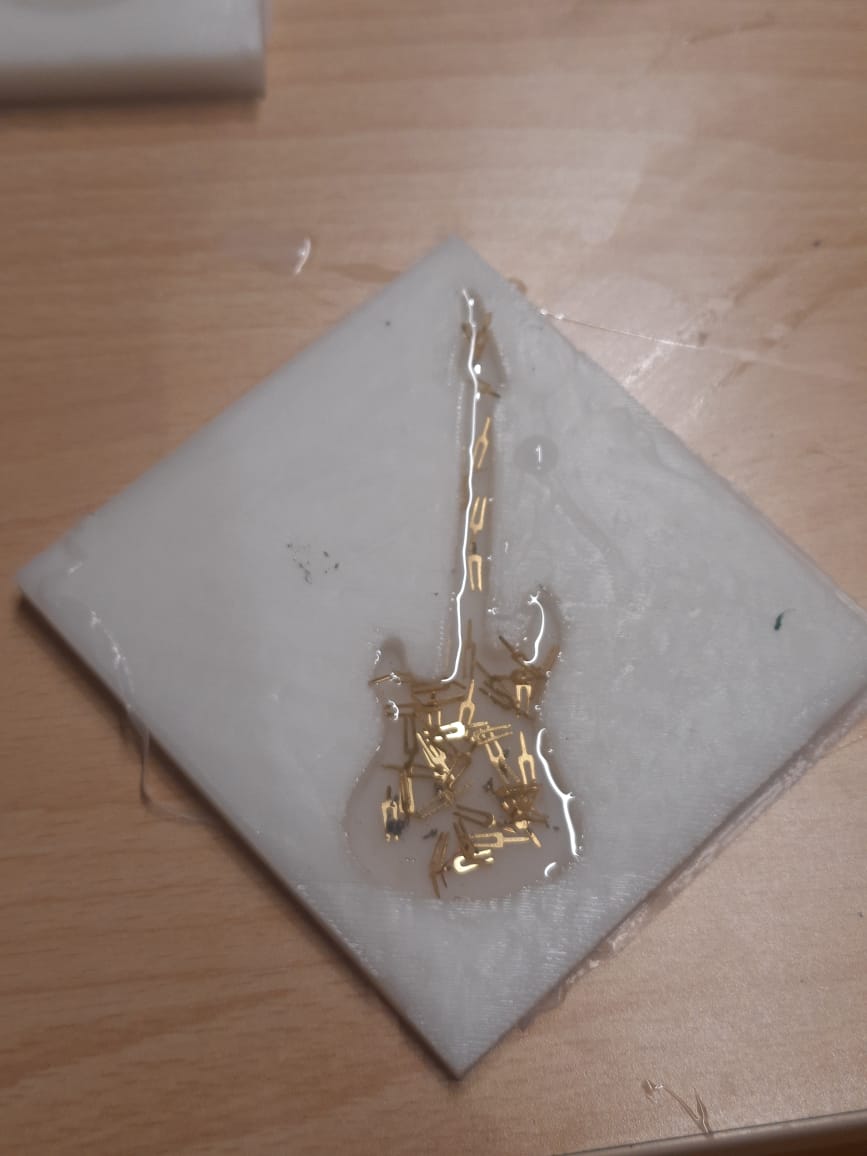
Final OutPut
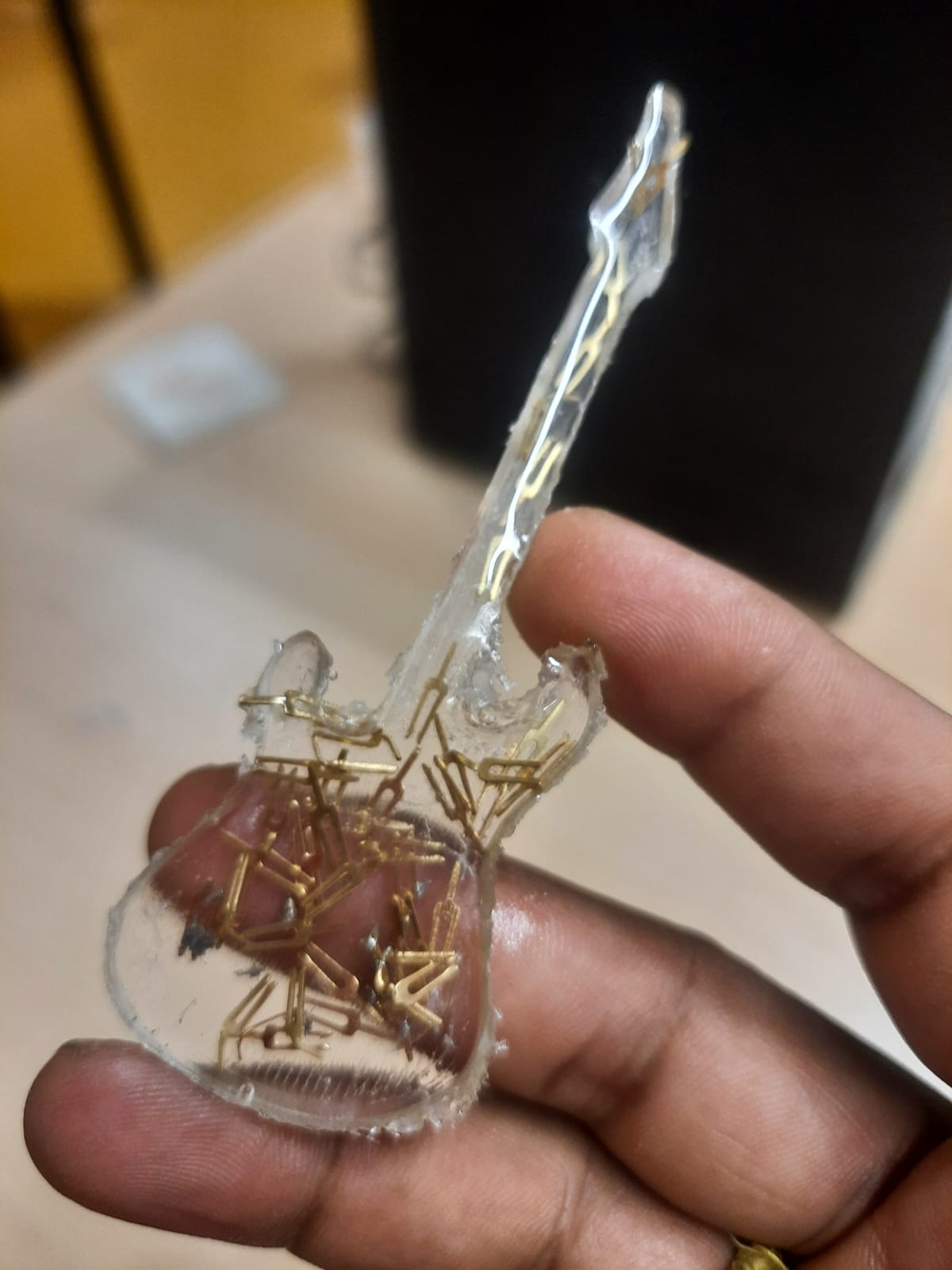
Problems Faced and How I Fixed Them
Air Bubbles in the Mold
While pouring the RTV silicone into the wax mold, I noticed the formation of air bubbles, especially around detailed areas. These bubbles caused defects in the mold surface.
Solution-Manual Technique to Avoid Air Bubbles Without Vacuum Degassing
Since a vacuum degassing machine was not available, I followed a manual technique to minimize air bubbles during silicone mold making. I started by using a small round brush to gently paint a thin layer of silicone directly onto the surface of the mold. This helped push silicone into fine details and prevented air from being trapped in corners and small features.
I carefully ensured there were no gaps while brushing the first layer. Once the surface was fully coated, I slowly poured the remaining mixed silicone over the mold from a height in a thin stream. This method reduces air entrapment during pouring and allows bubbles to rise naturally before curing.
This brushing and pouring technique proved effective in capturing fine details and minimizing surface defects in the final mold, especially in the absence of a vacuum chamber.