Vinyl Cutter
Summary
In this documentation, I detail the process of using the Roland GS-24 vinyl cutter in the lab. I began by researching the machine and learning how to operate it through online resources and tutorials. Using Inkscape, I designed a simple street sign, utilizing various shape tools, alignment techniques, and grouping functions to create a clean vector design.
After preparing the vinyl cutter by calibrating the blade and loading the material, I used CutStudio to convert and send the file for cutting. Once cut, I transferred the vinyl using duct tape or transfer tape to ensure proper alignment. Additionally, I experimented with a multi-layered stop sign, cutting separate layers for different colors and using a laser cutter to create a precise backing. This experience reinforced the importance of calibration, design preparation, and transfer techniques for achieving high-quality vinyl stickers.
Work Process Detail
Using the Roland GS-24 Vinyl Cutter – Step-by-Step Guide
1. Understanding the Machine
- The vinyl cutter available in the lab is a Roland GS-24.
- To learn how to use it, I researched online and found two helpful YouTube videos:
- Video 1: How to operate the Roland GS-24 machine.
- Video 2: How to use CutStudio, the software that controls the machine.
- After watching and understanding both videos, I proceeded to create a test design.
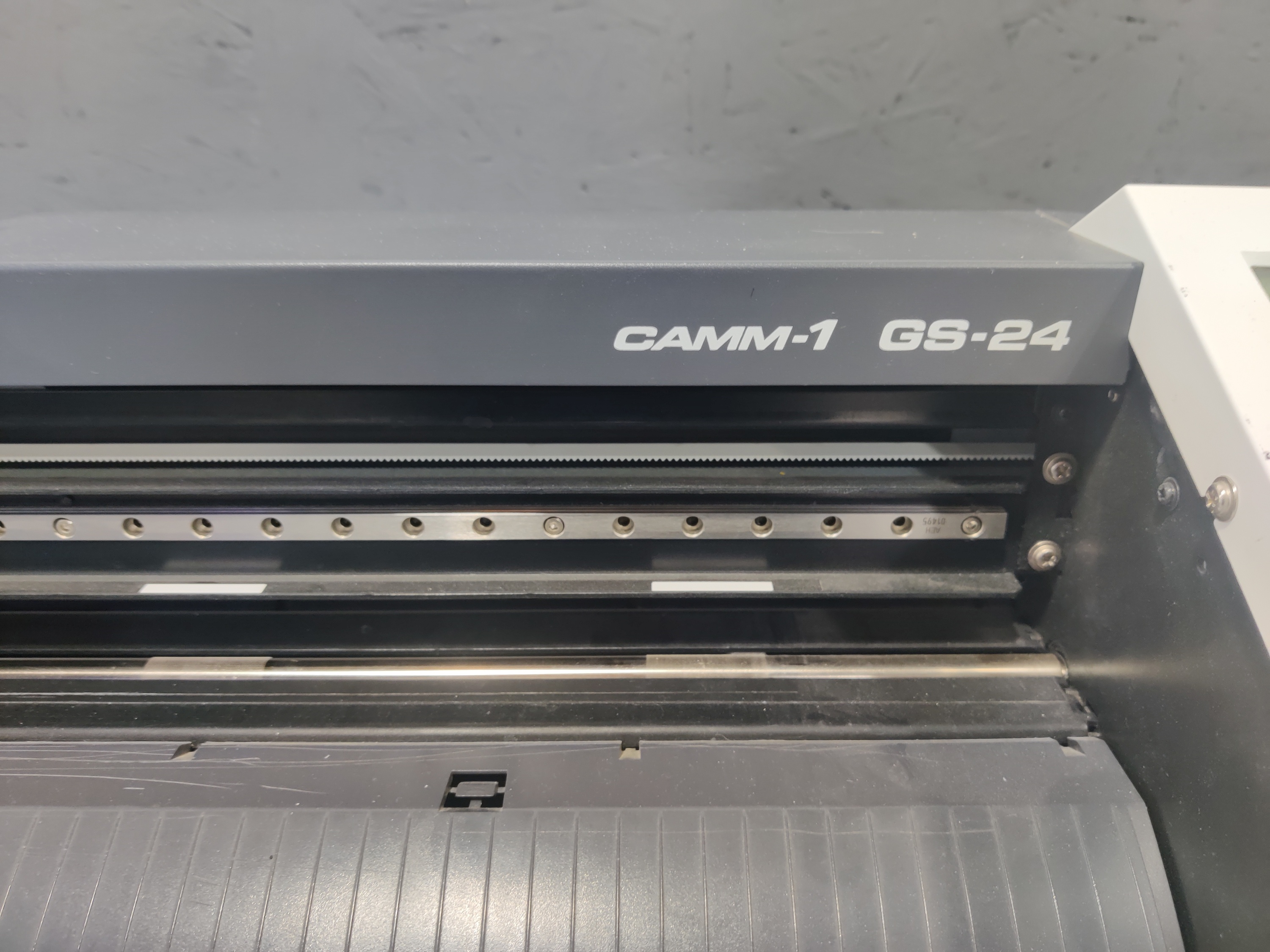
2. Designing a Vinyl Sticker in Inkscape
Creating a Simple Street Sign
- Open Inkscape and create a new document.
- Draw an ellipse (circle) using the Ellipse Tool.
- Hold CTRL + SHIFT to resize while keeping it centered.
- Duplicate the ellipse by right-clicking → Duplicate (instead of CTRL+C, CTRL+V).
- This keeps the new shape aligned to the center of the original.
- Resize the duplicate to be slightly larger or smaller as needed.
- Change the color of each shape using the Fill & Stroke panel.
- Add a rectangle (for text or symbols) and place it in the center using the Align Tool.
- Use the Shape Builder Tool to merge all elements into a single shape.
- Group the design (right-click → Group) to keep everything together.
- Repeat the process for additional signs, including my final project logo.
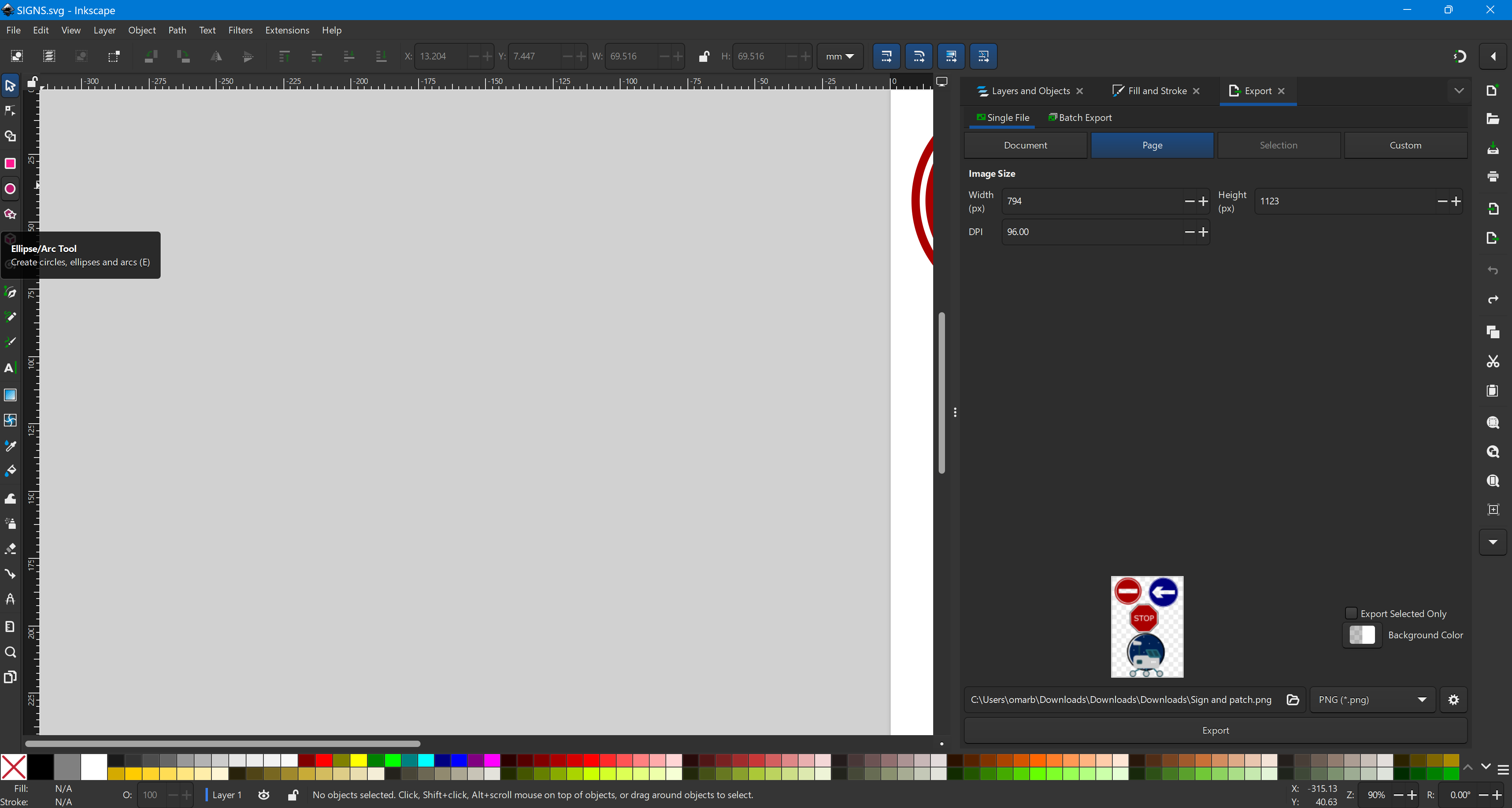

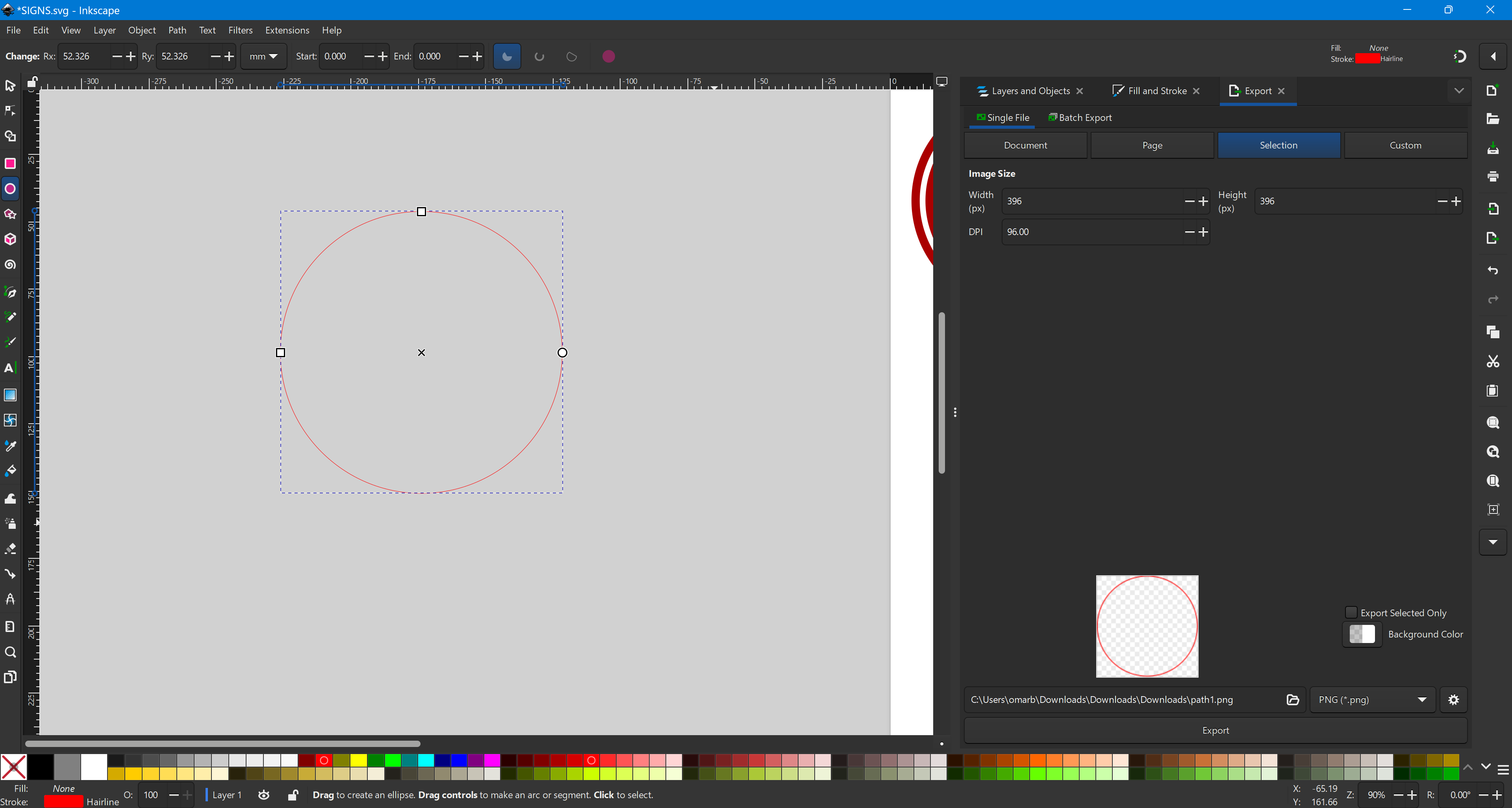
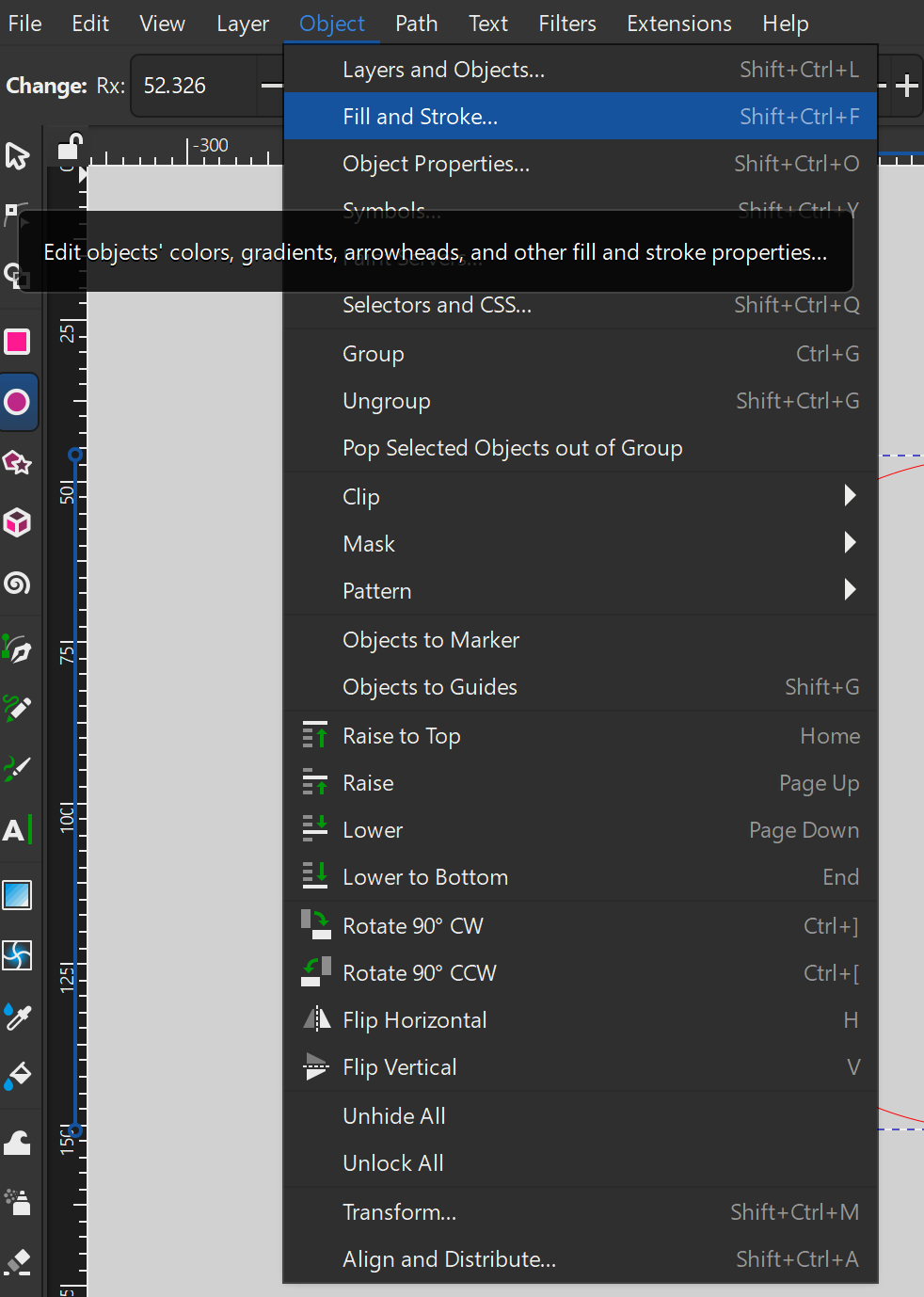
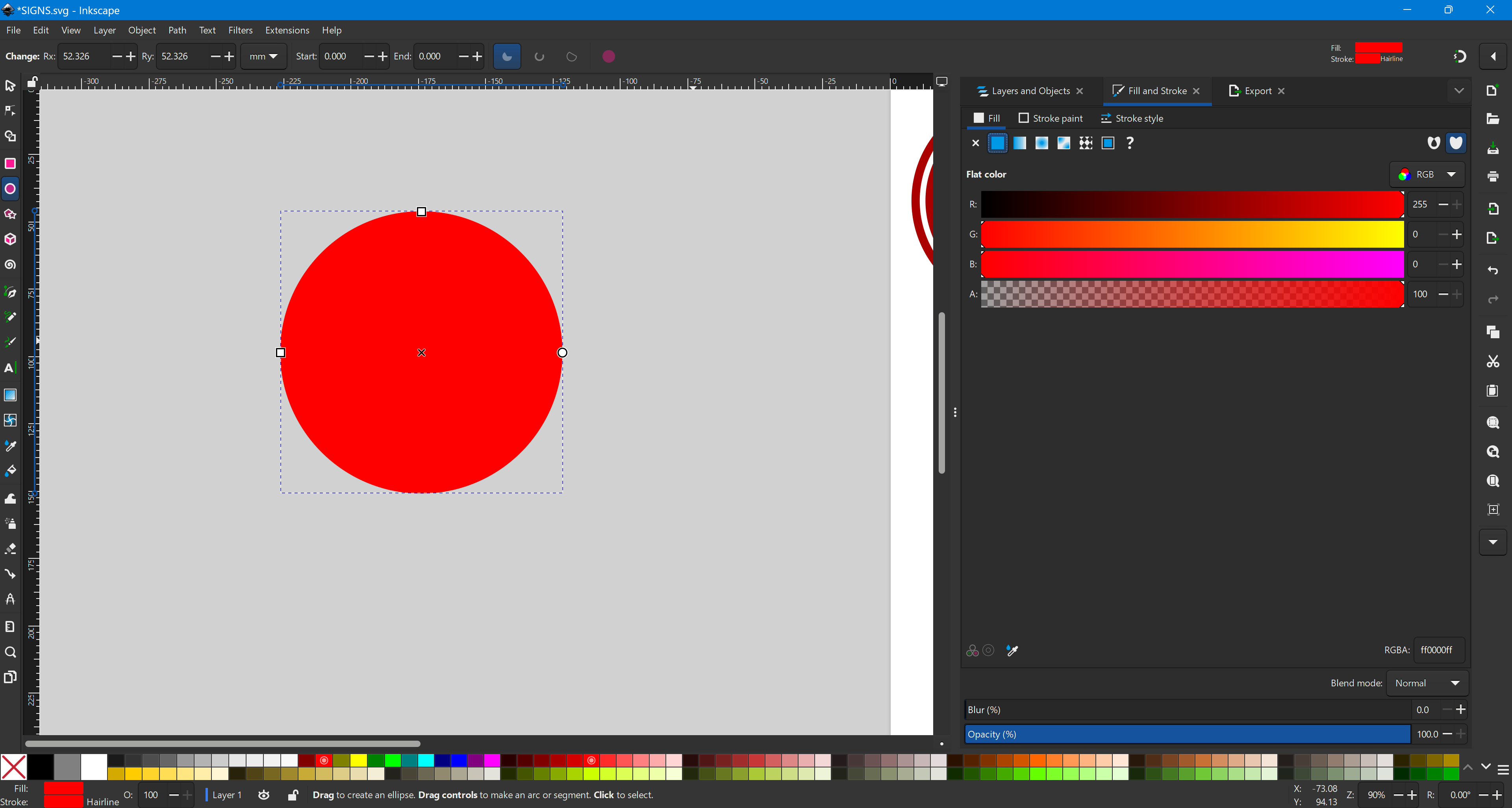
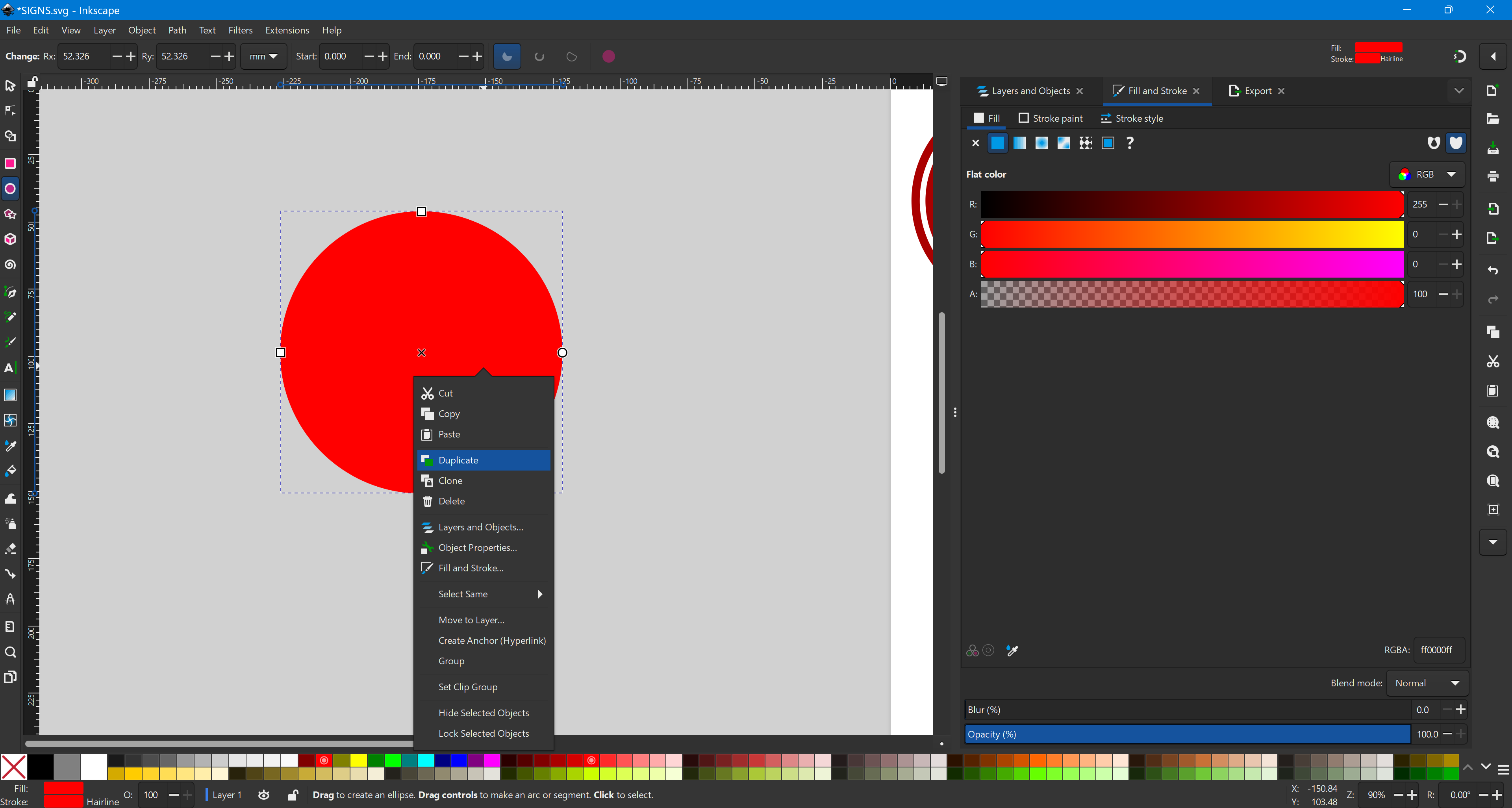
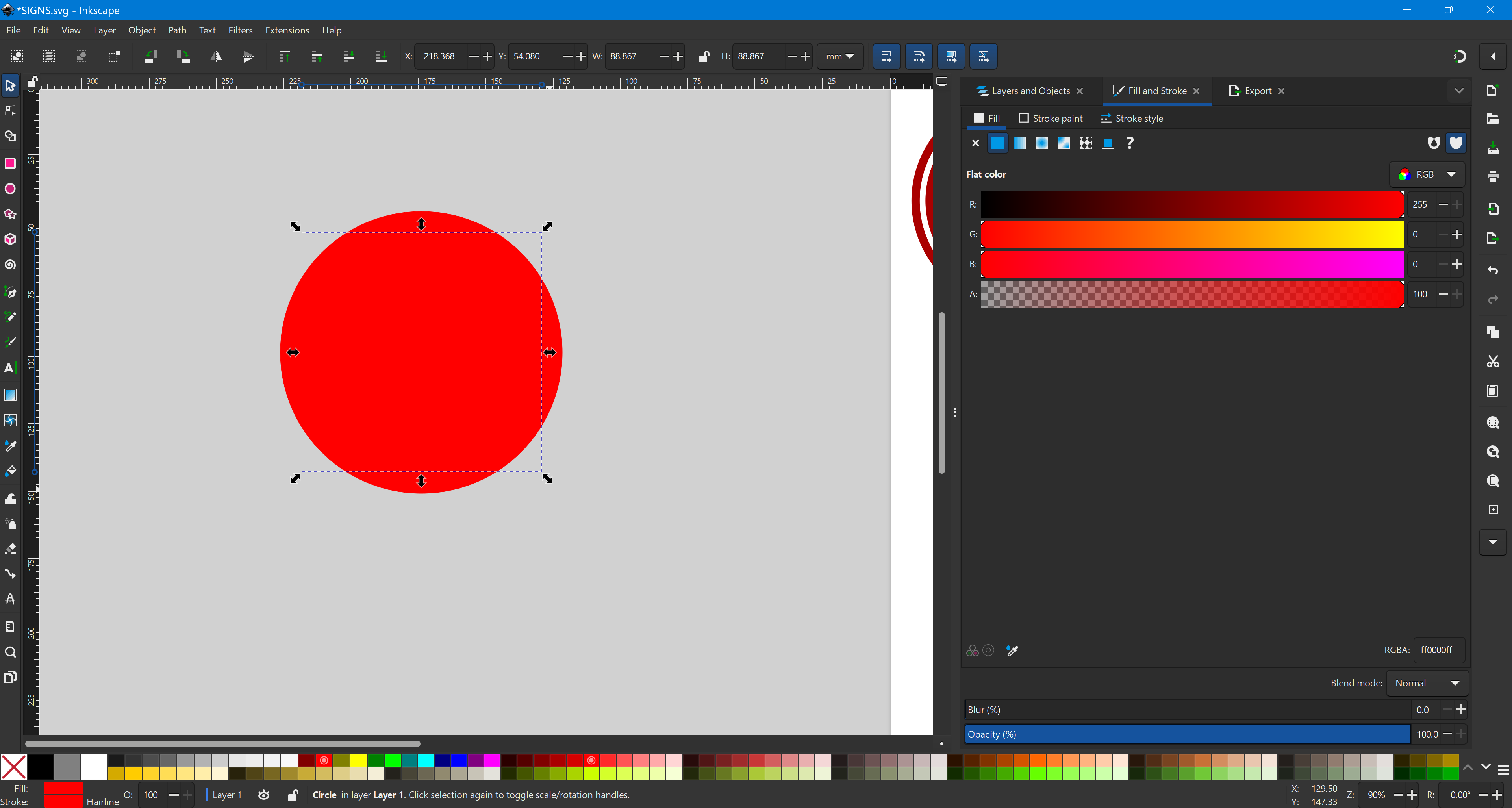
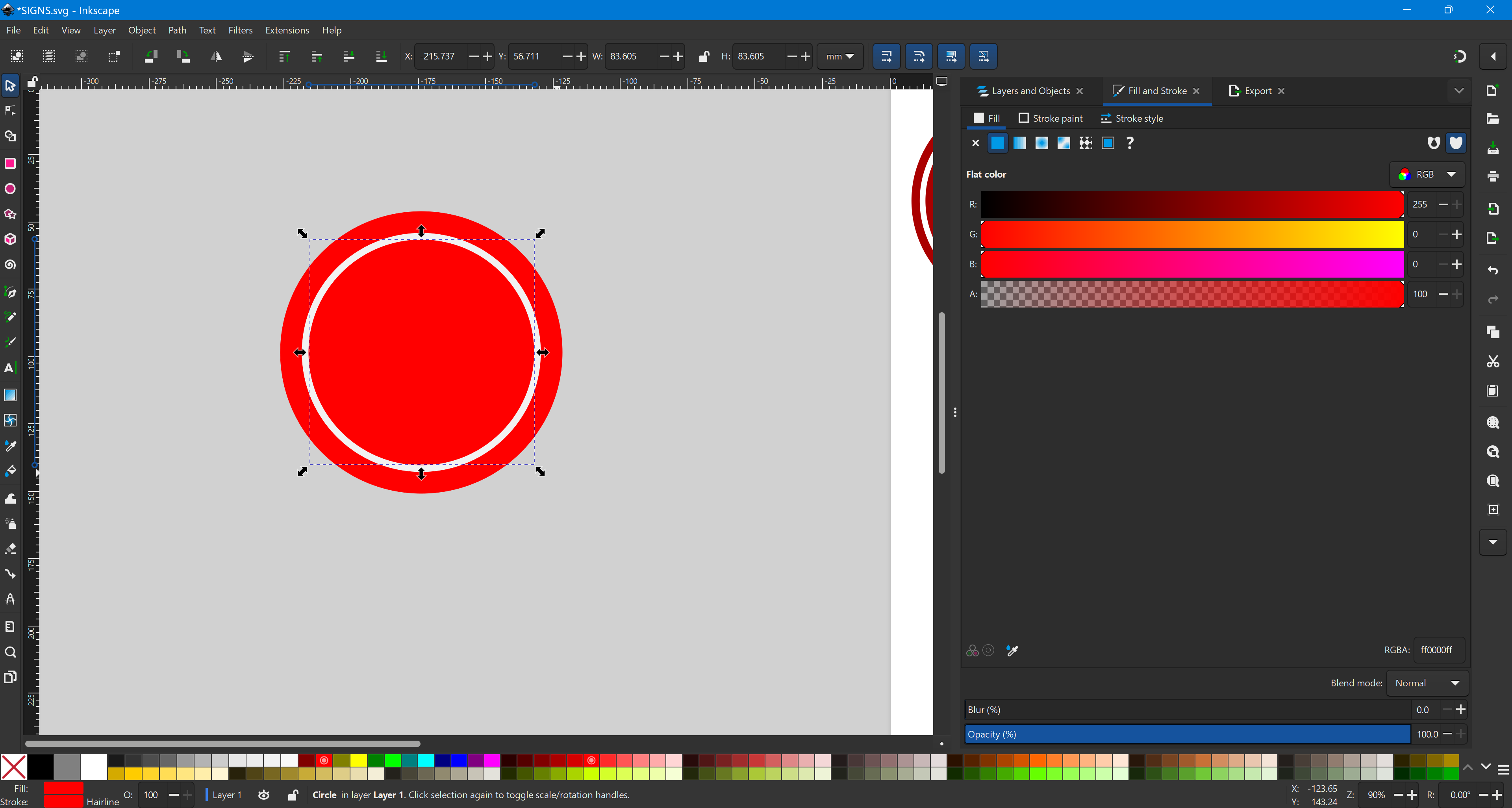
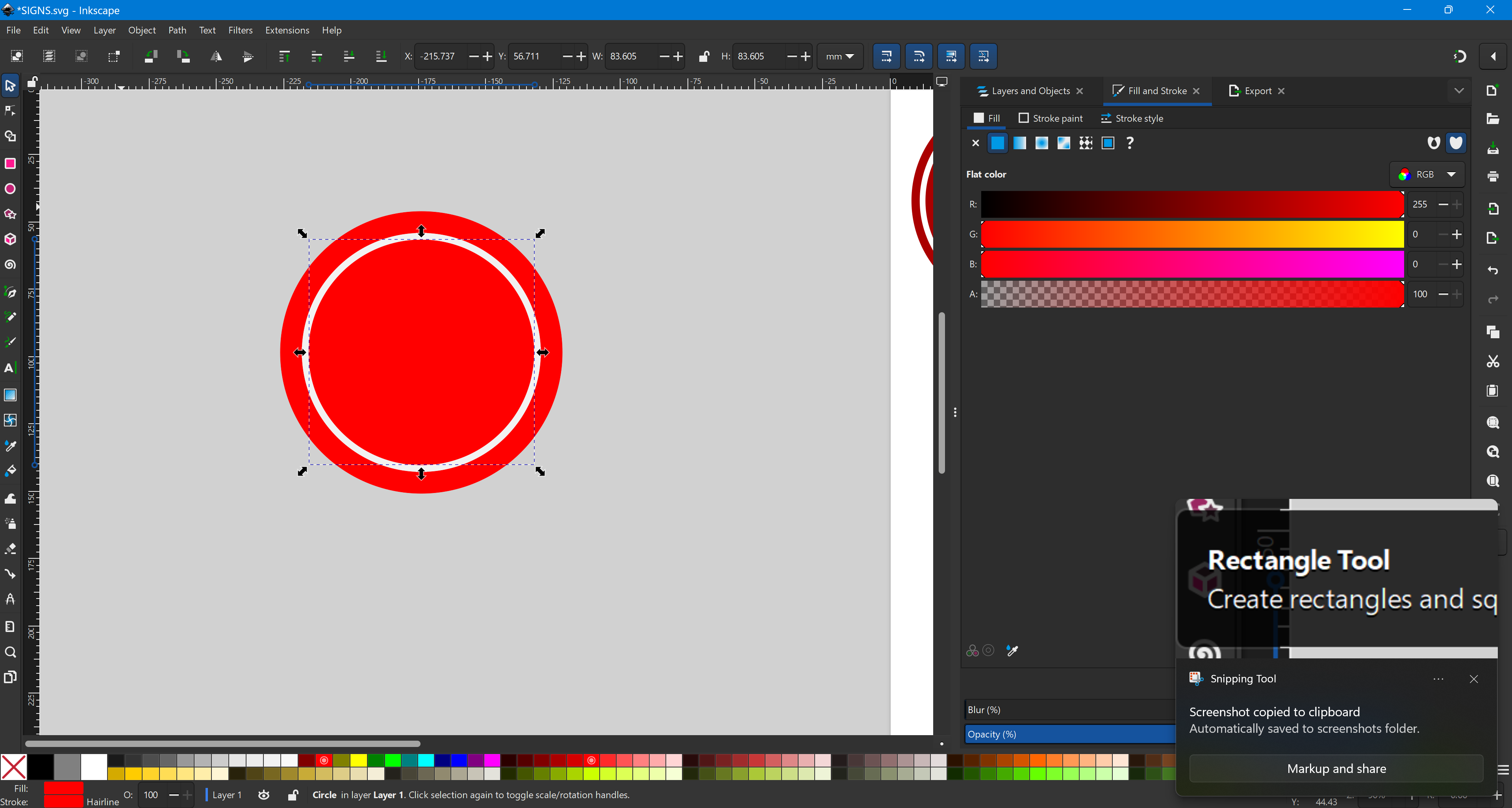
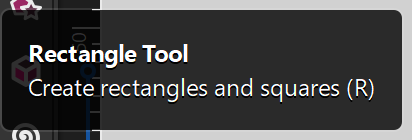
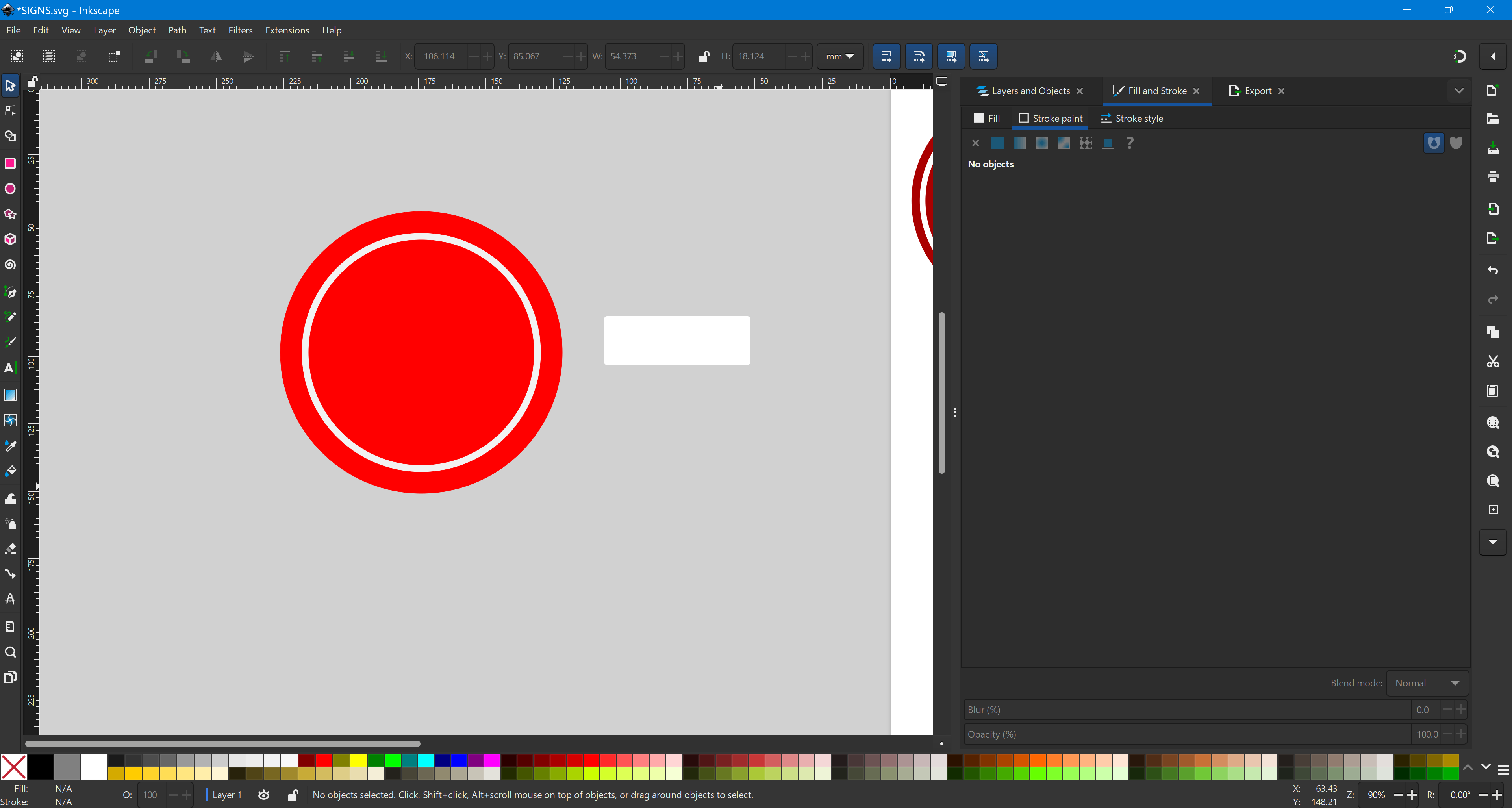
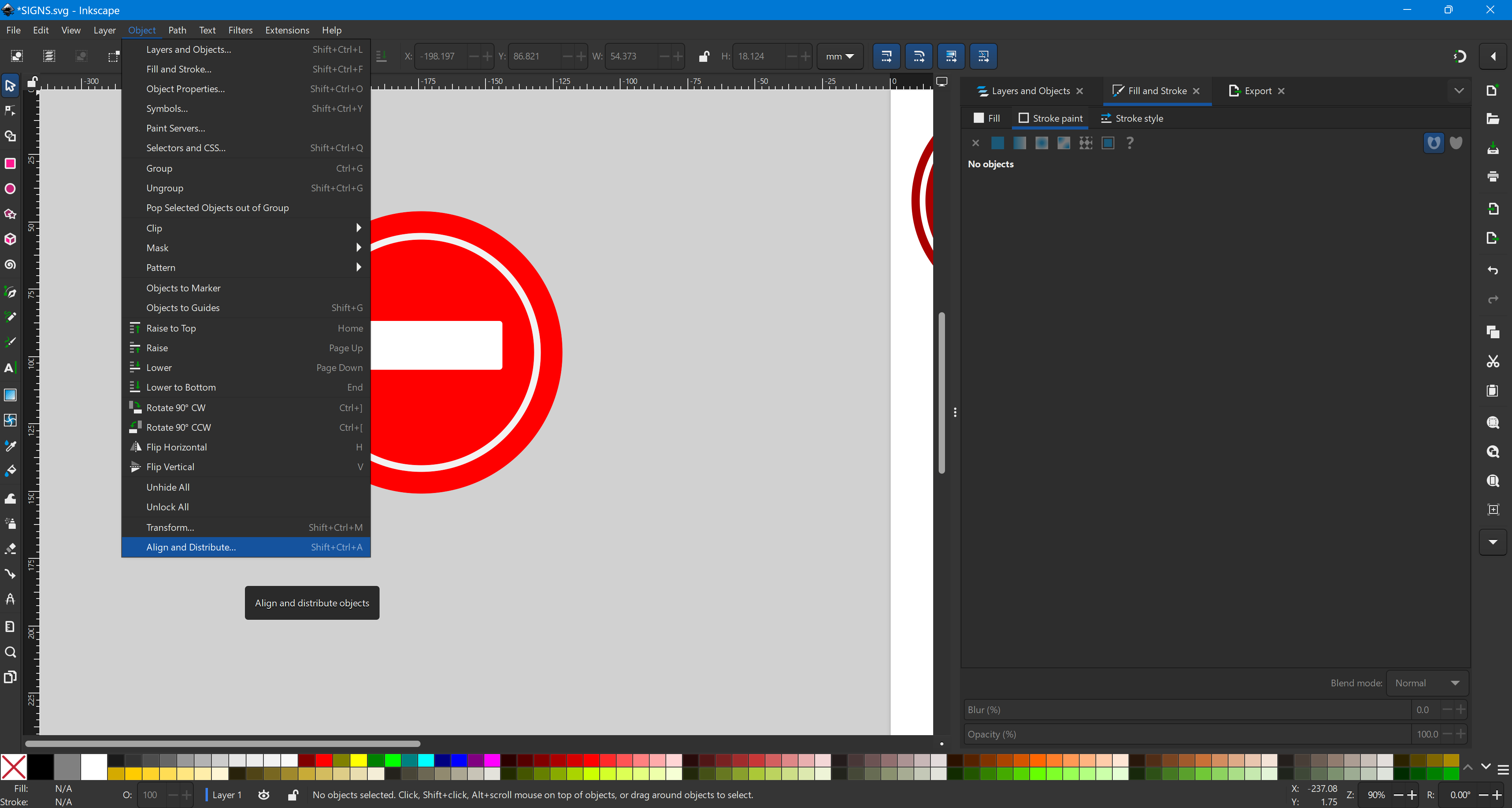
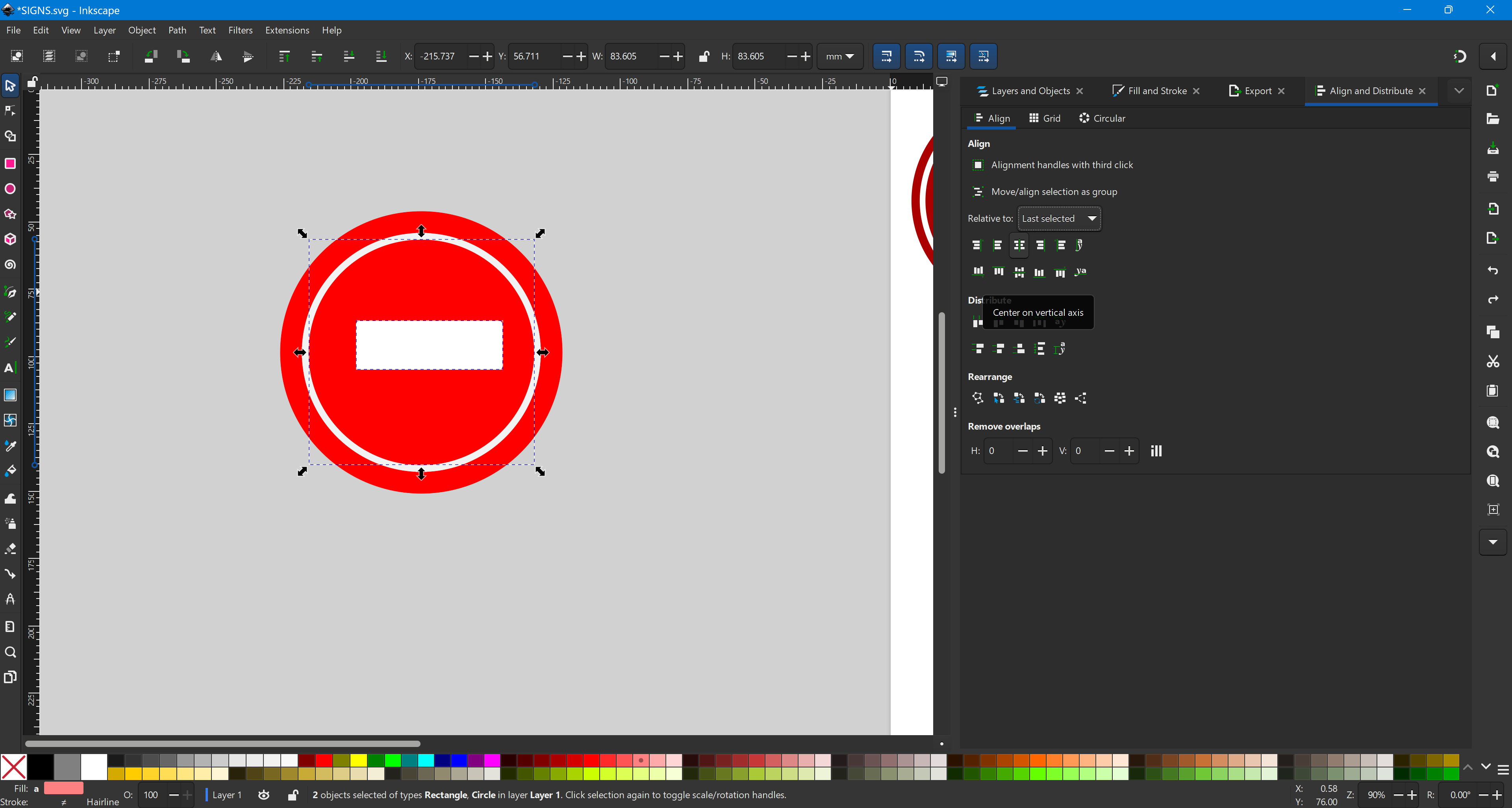
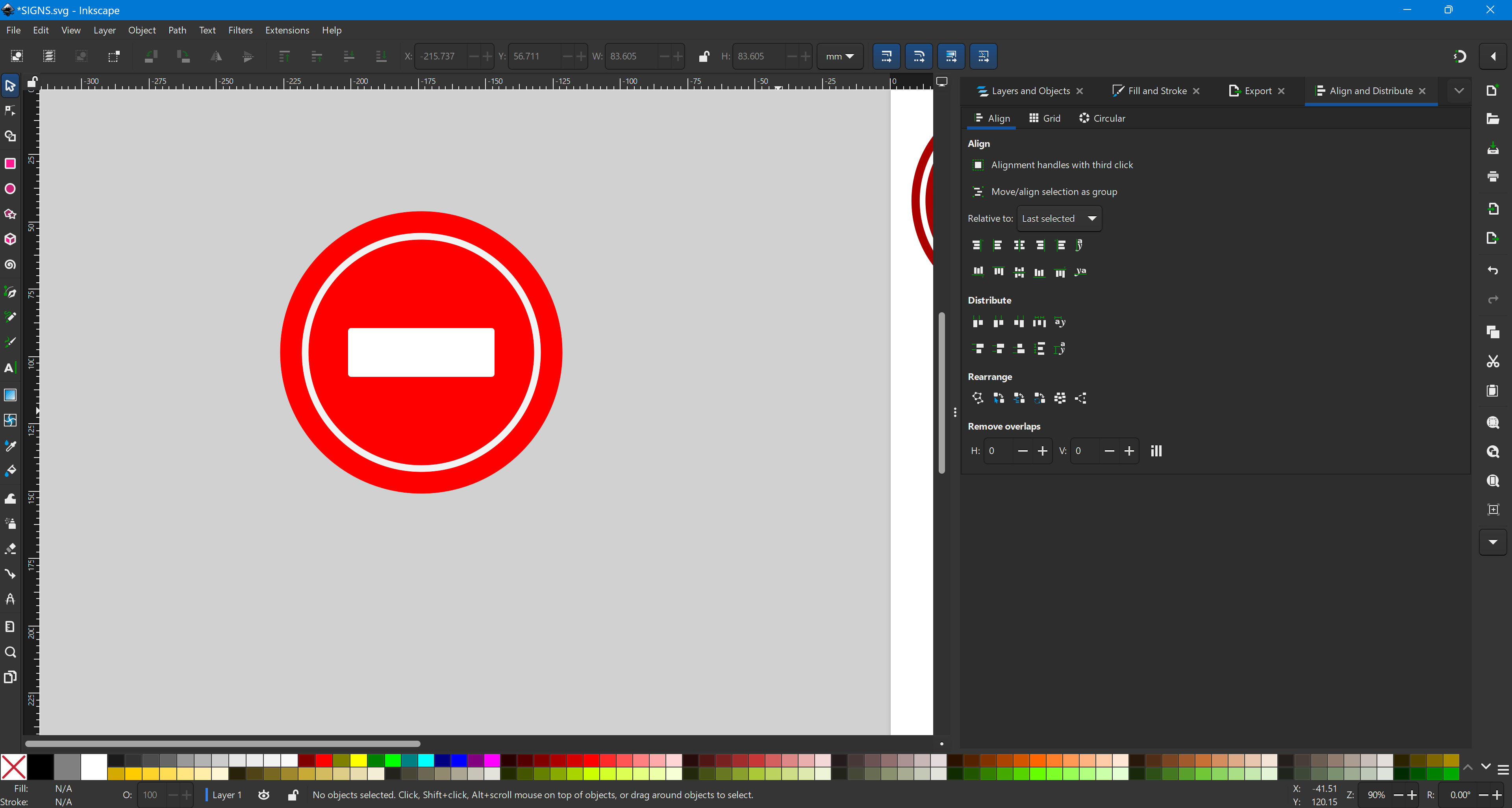
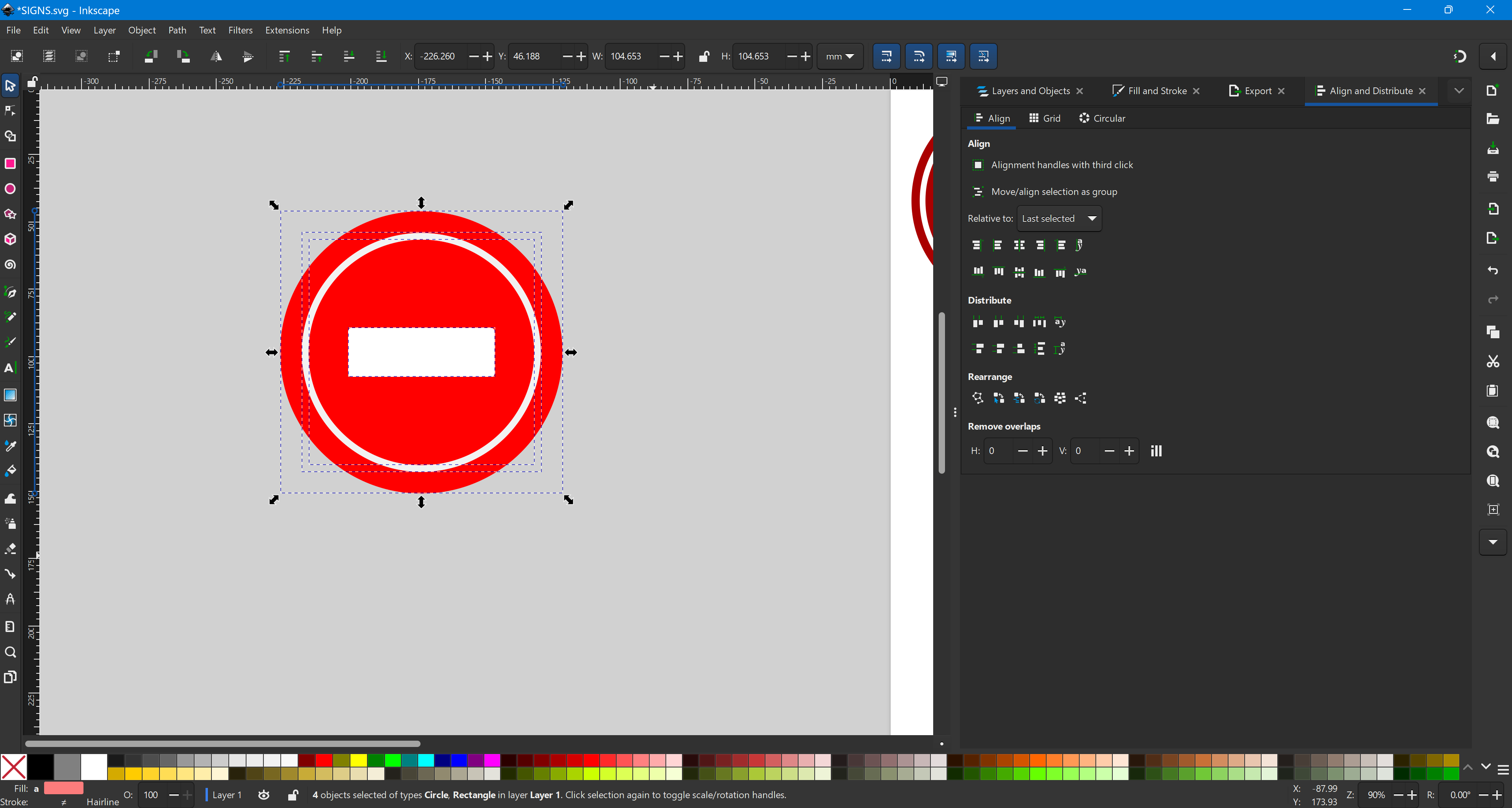
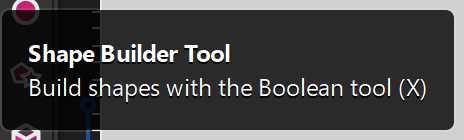
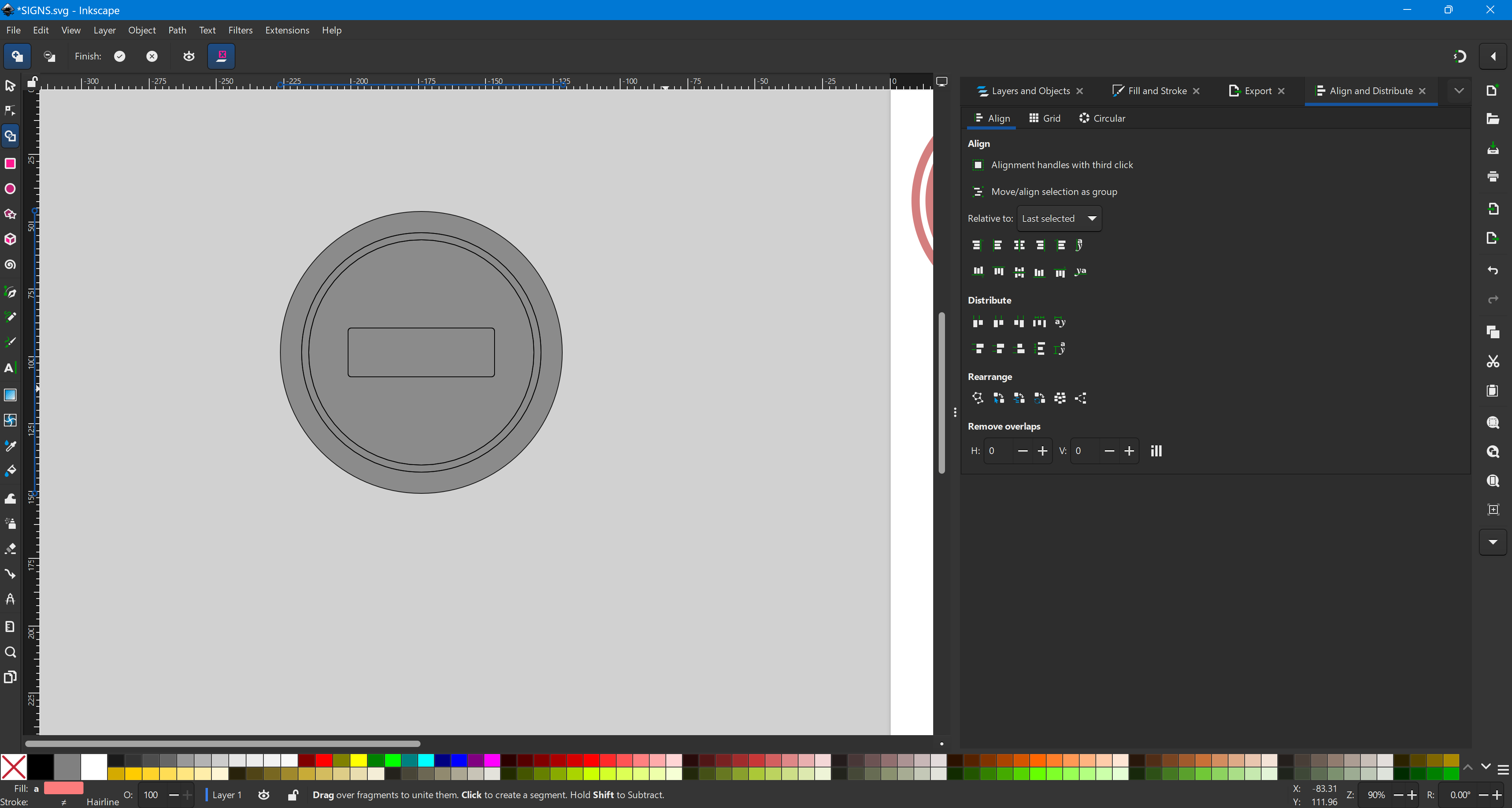
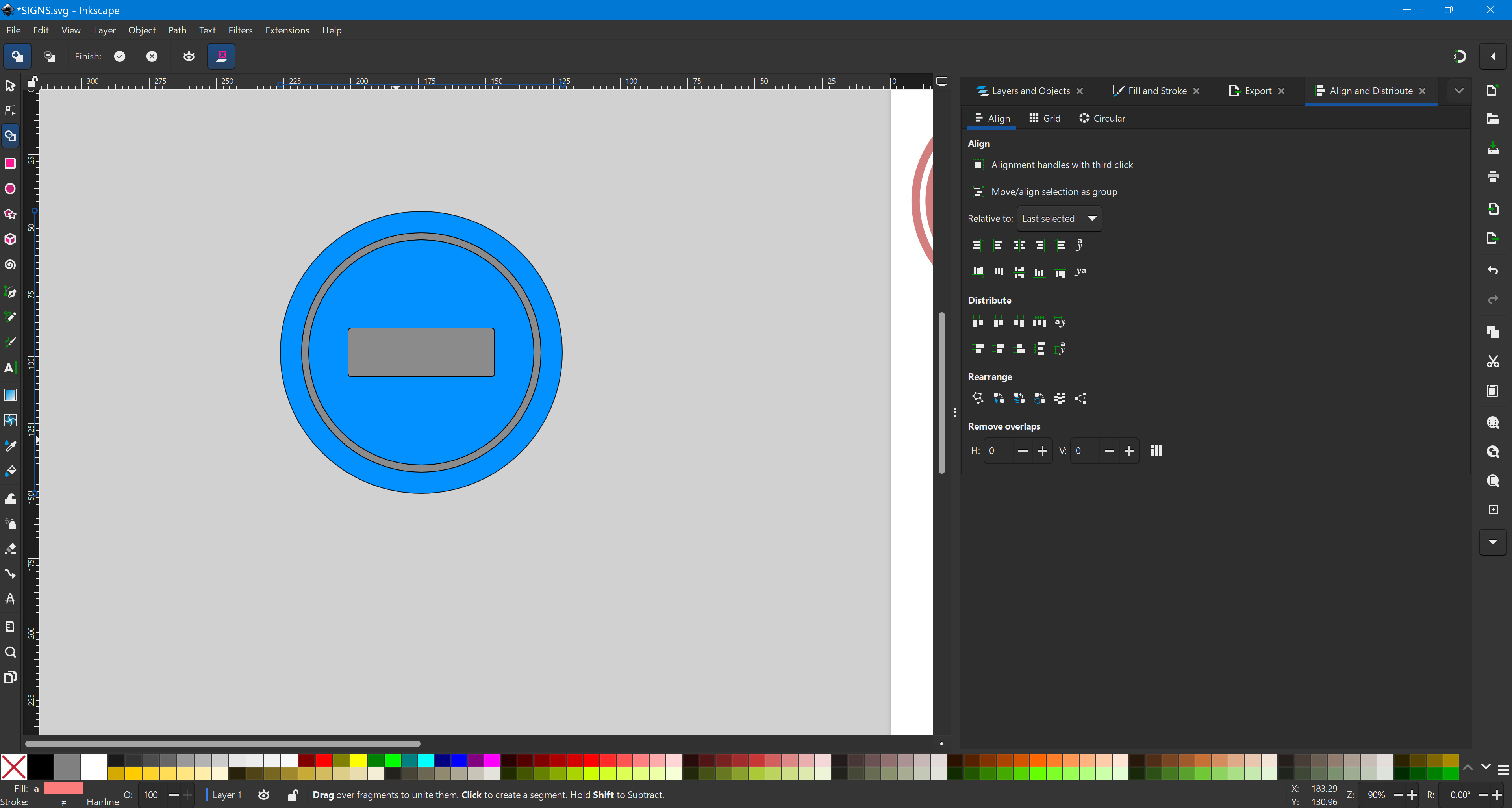
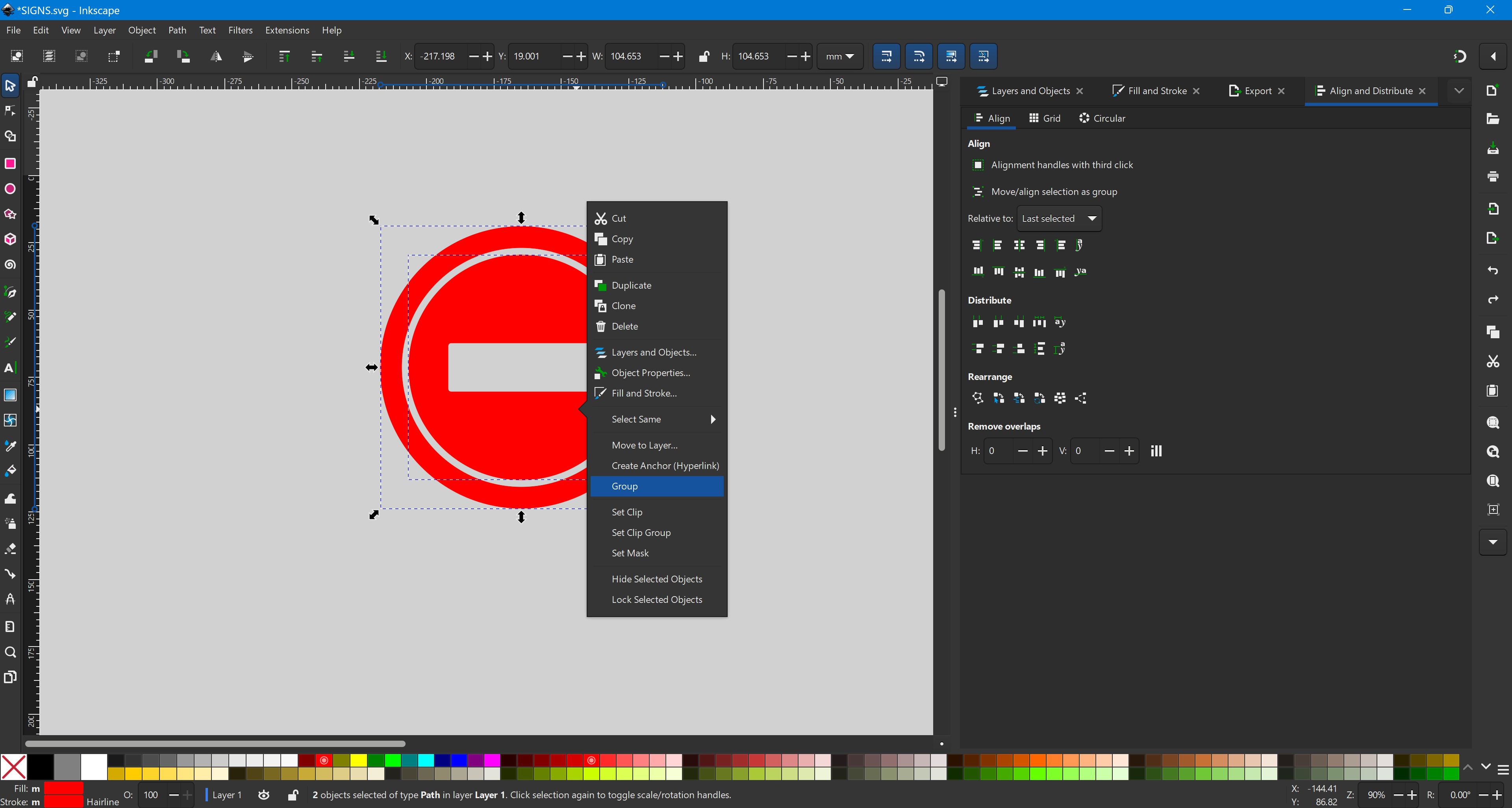
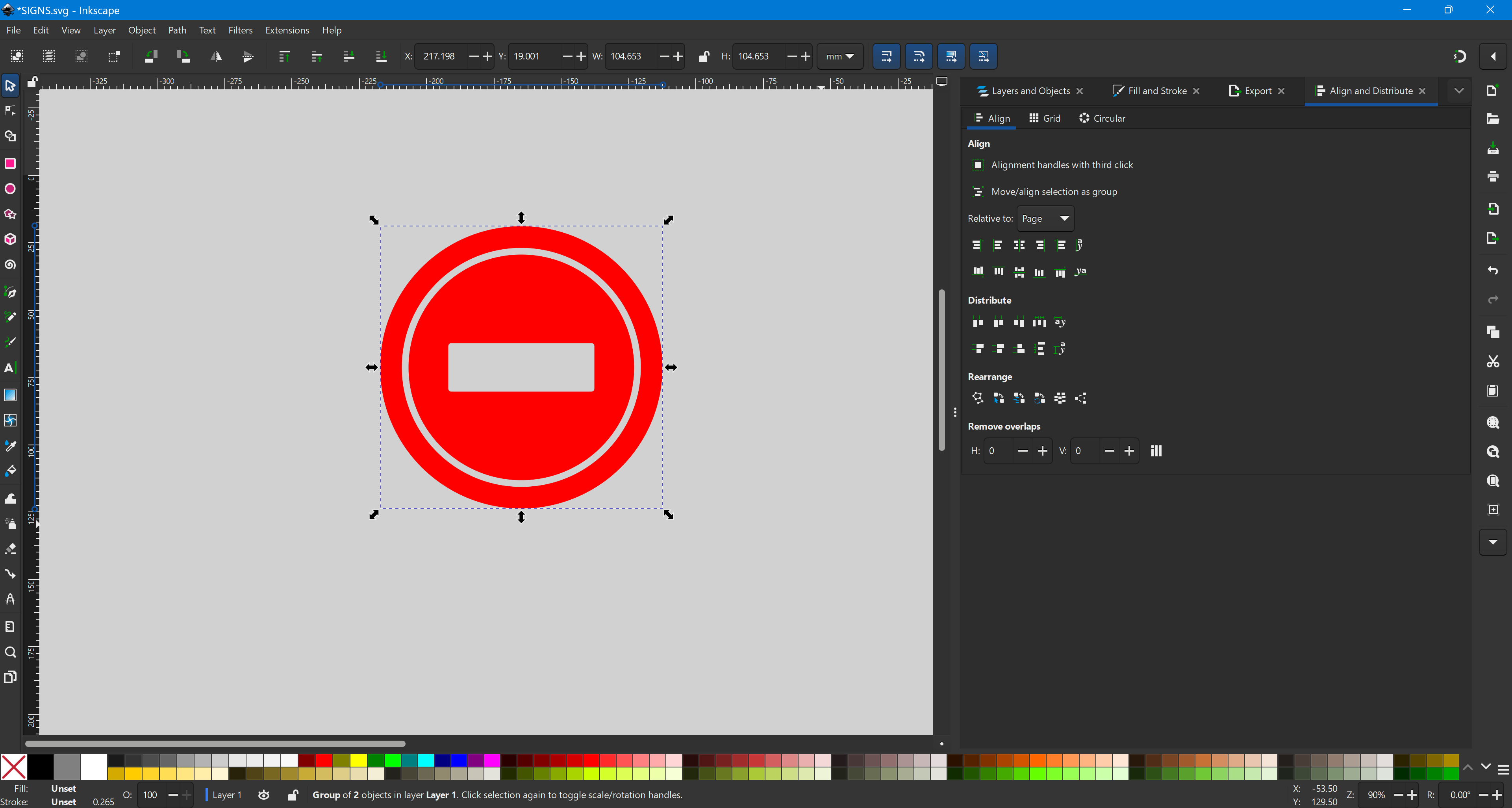
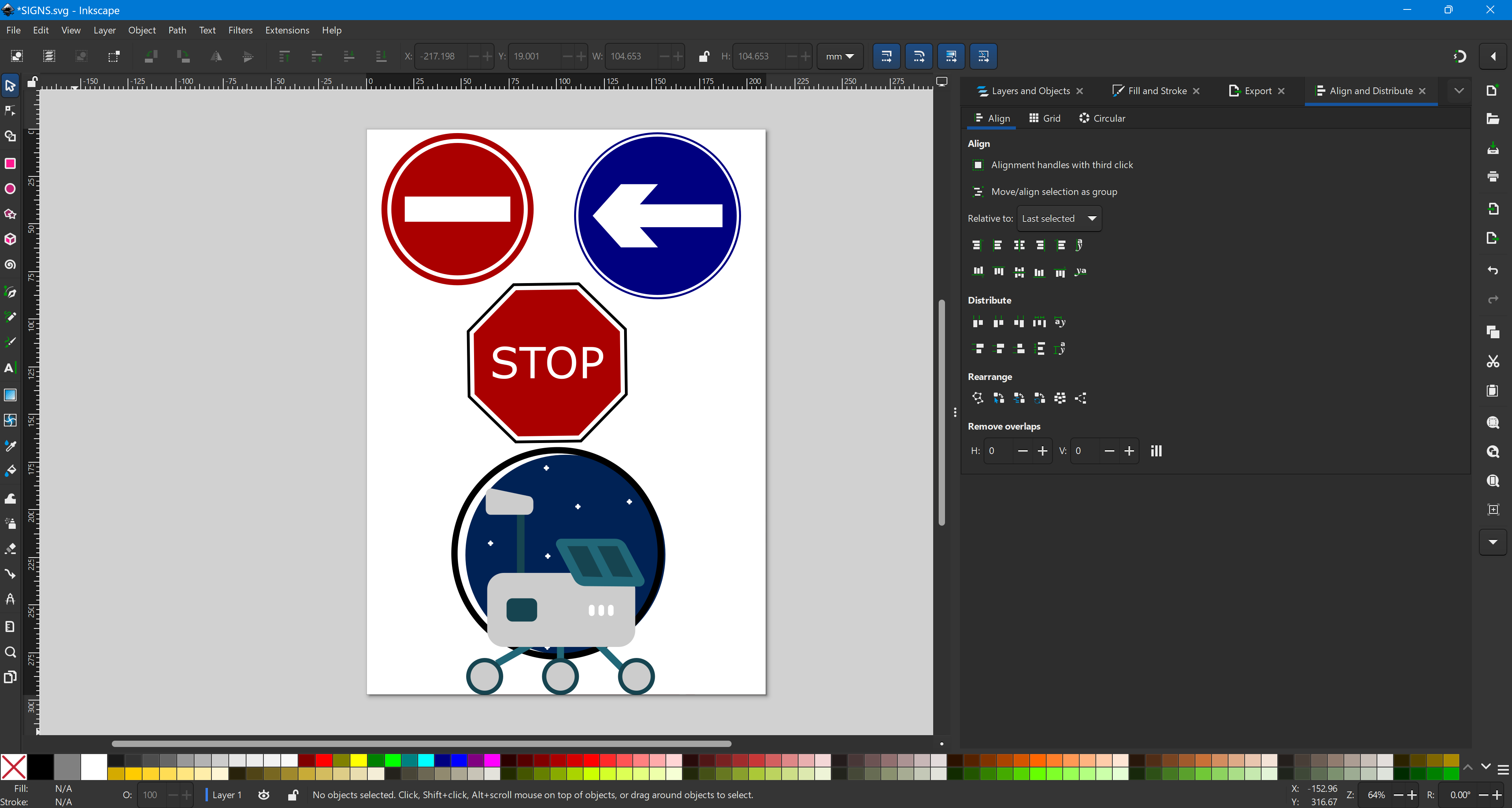
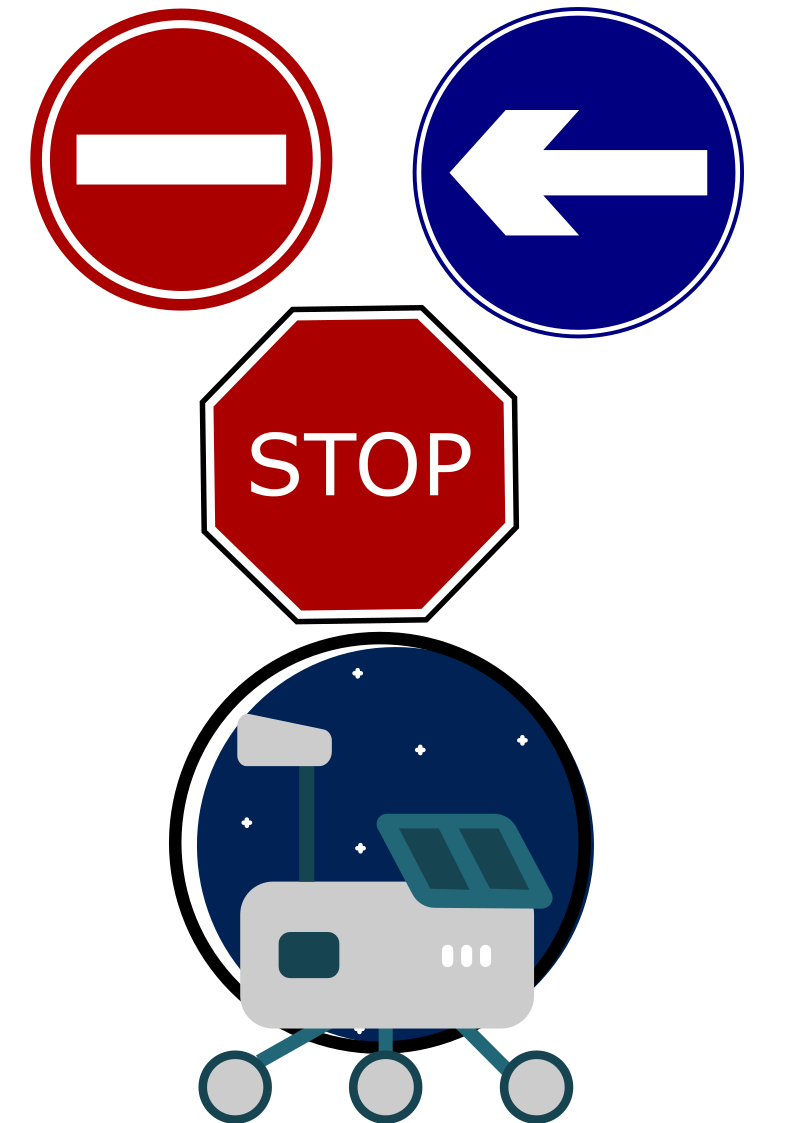
3. Preparing the Vinyl Cutter
- Check machine calibration:
- Disassemble the knife (blade) and adjust its height to match the vinyl thickness.
- Load the vinyl roll into the cutter, ensuring it is properly aligned.
- Use CutStudio to prepare the design for cutting:
- Convert the SVG file into cutting lines.
- Send the file to the vinyl cutter.
- Start the cutting process step by step as shown in the instructional videos.
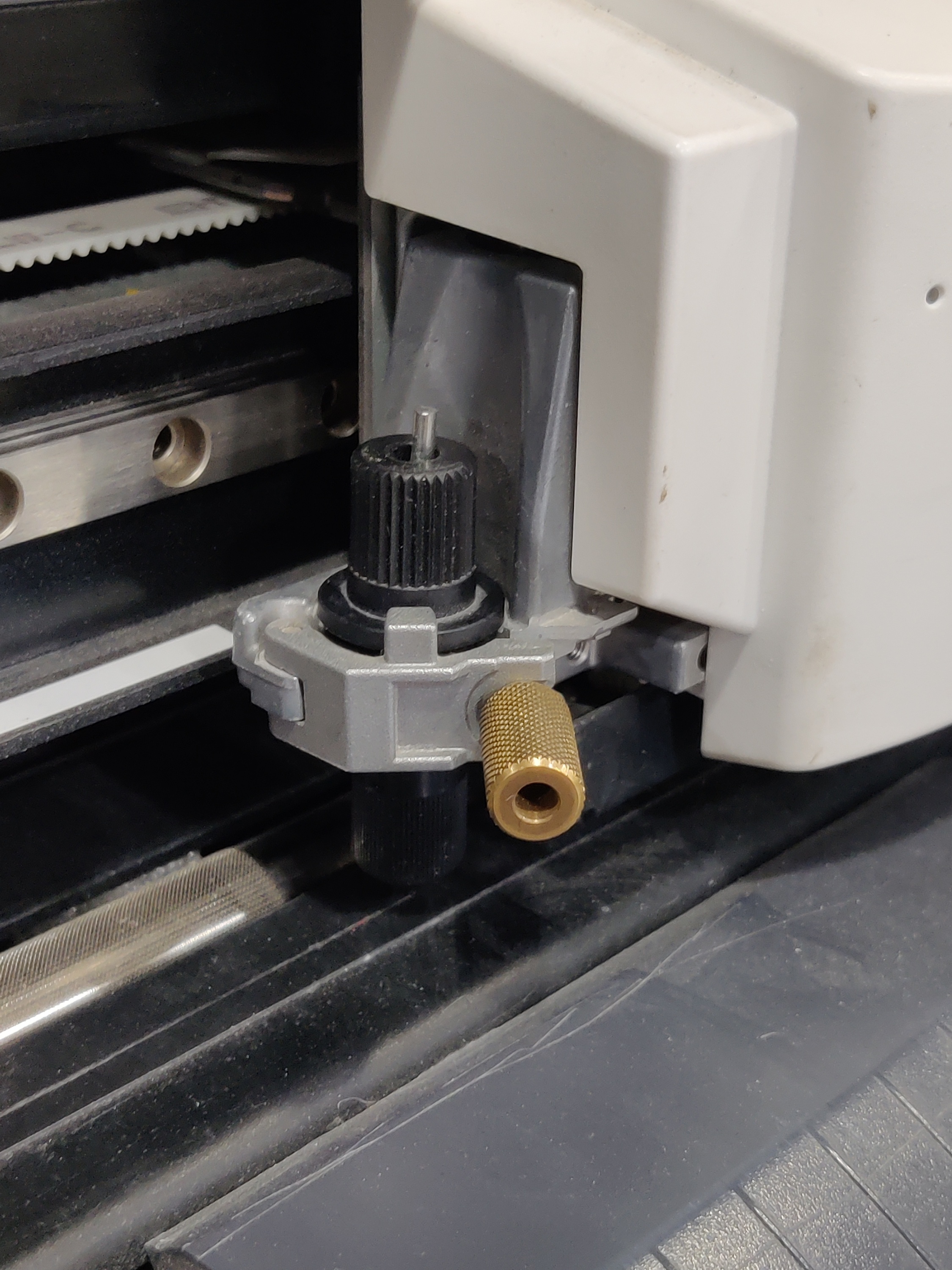
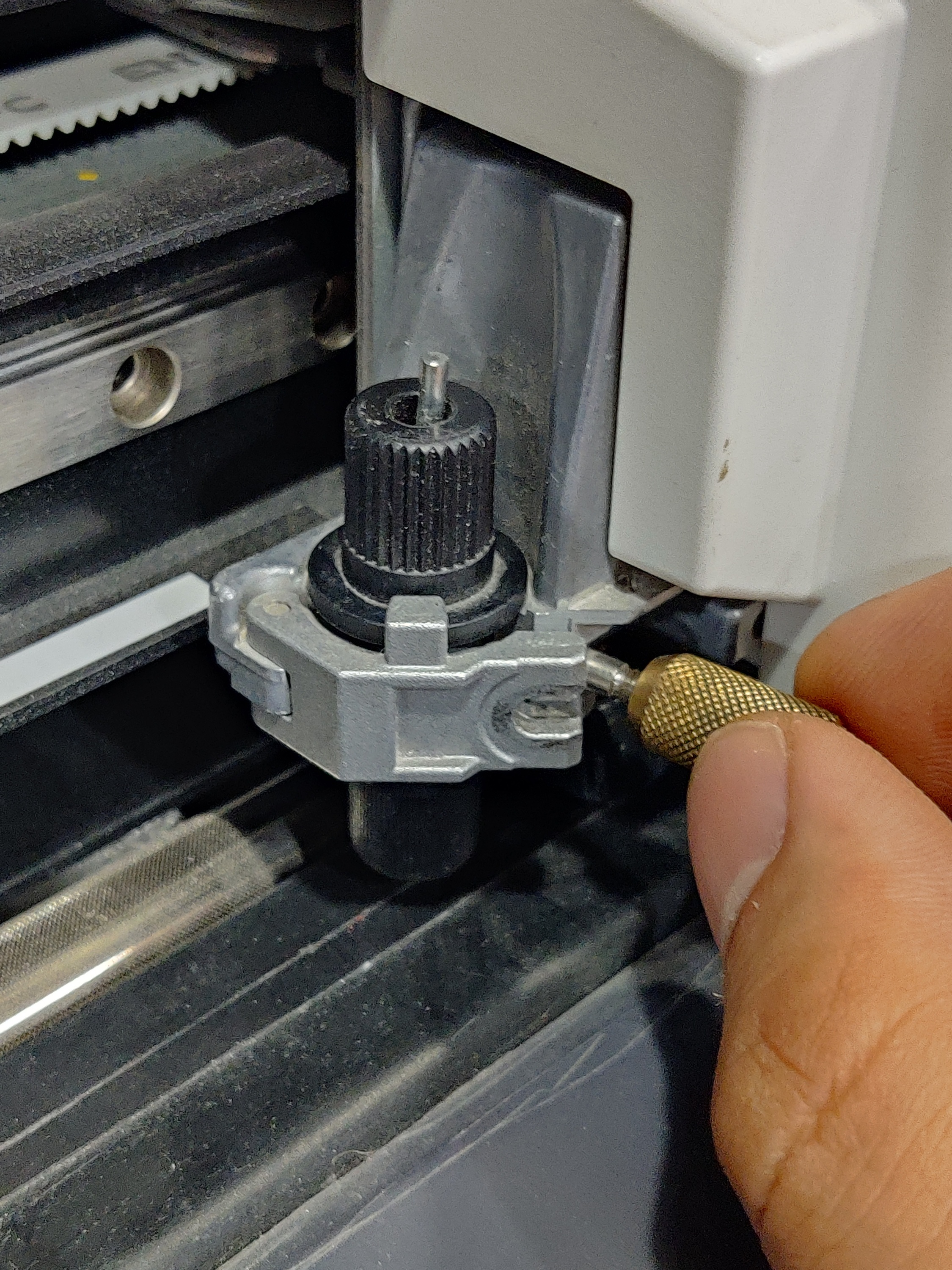
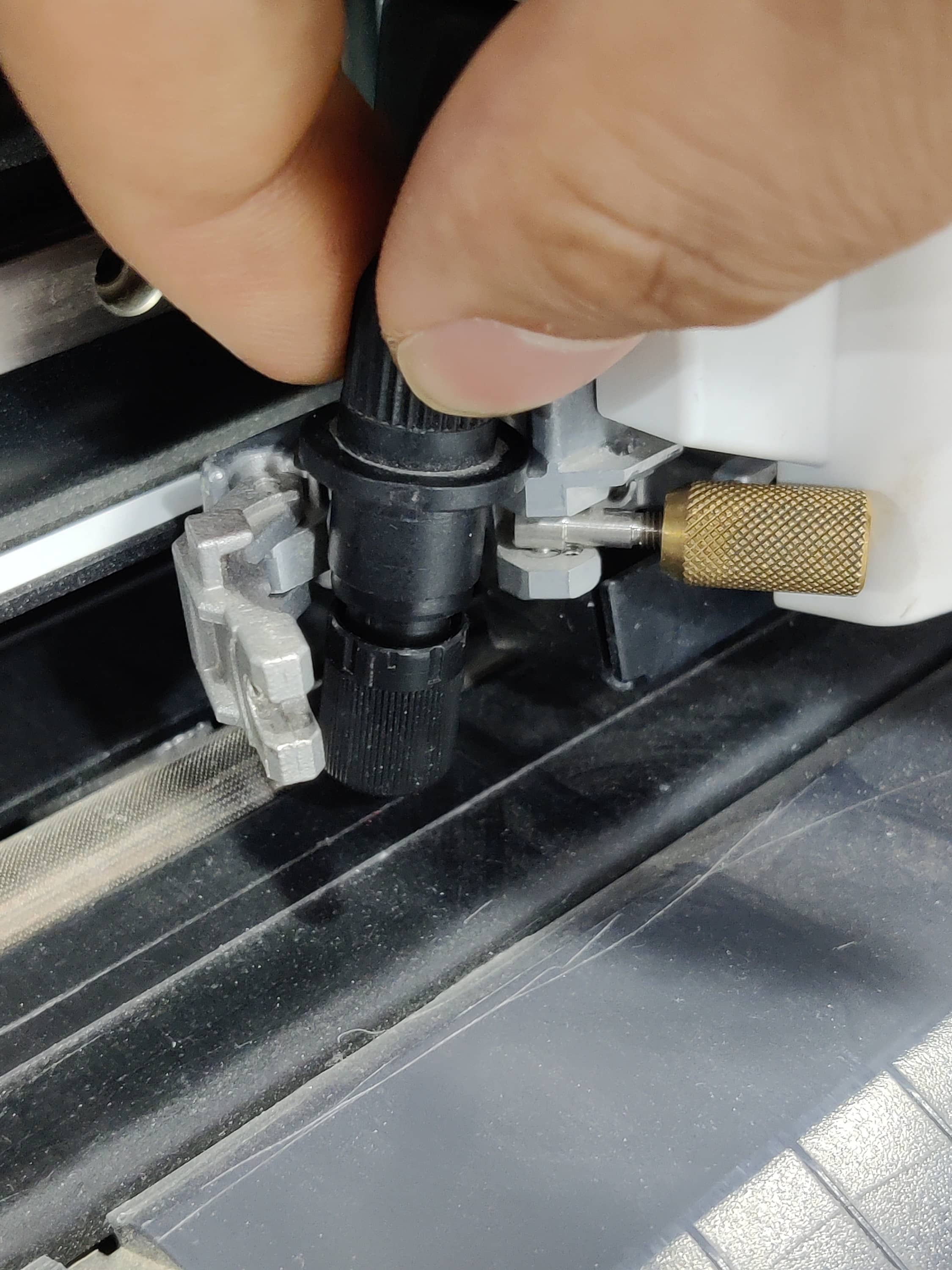
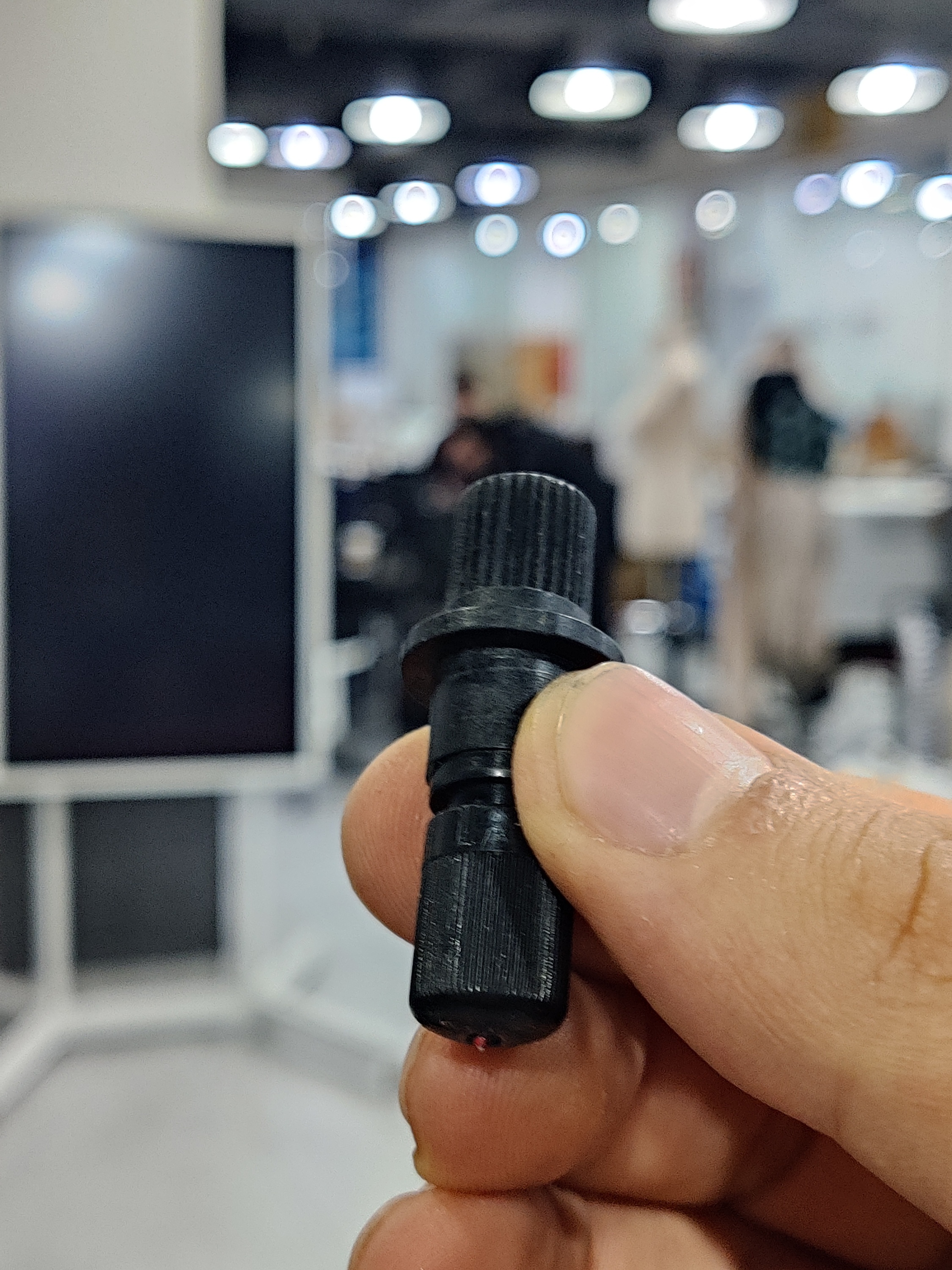
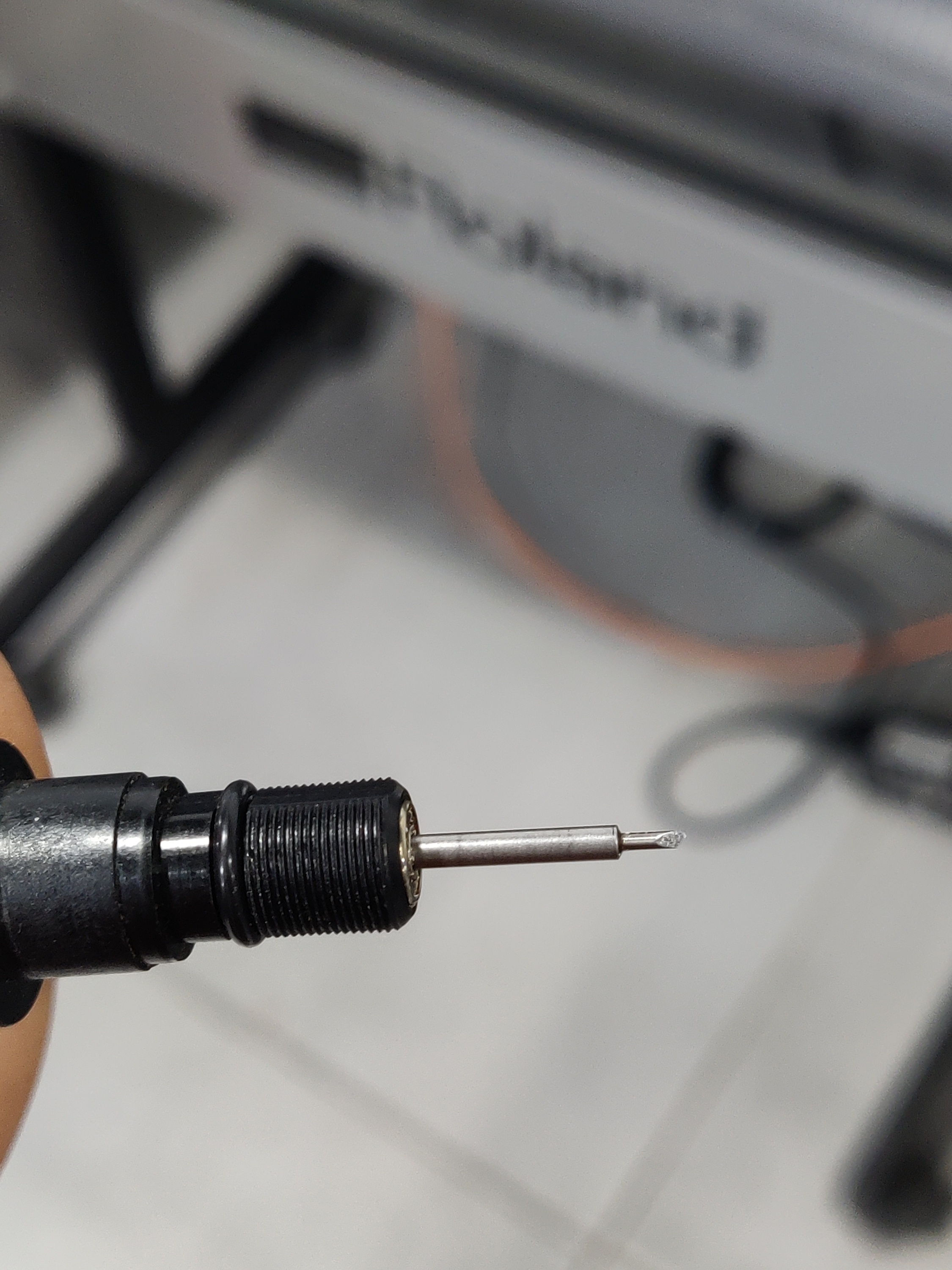
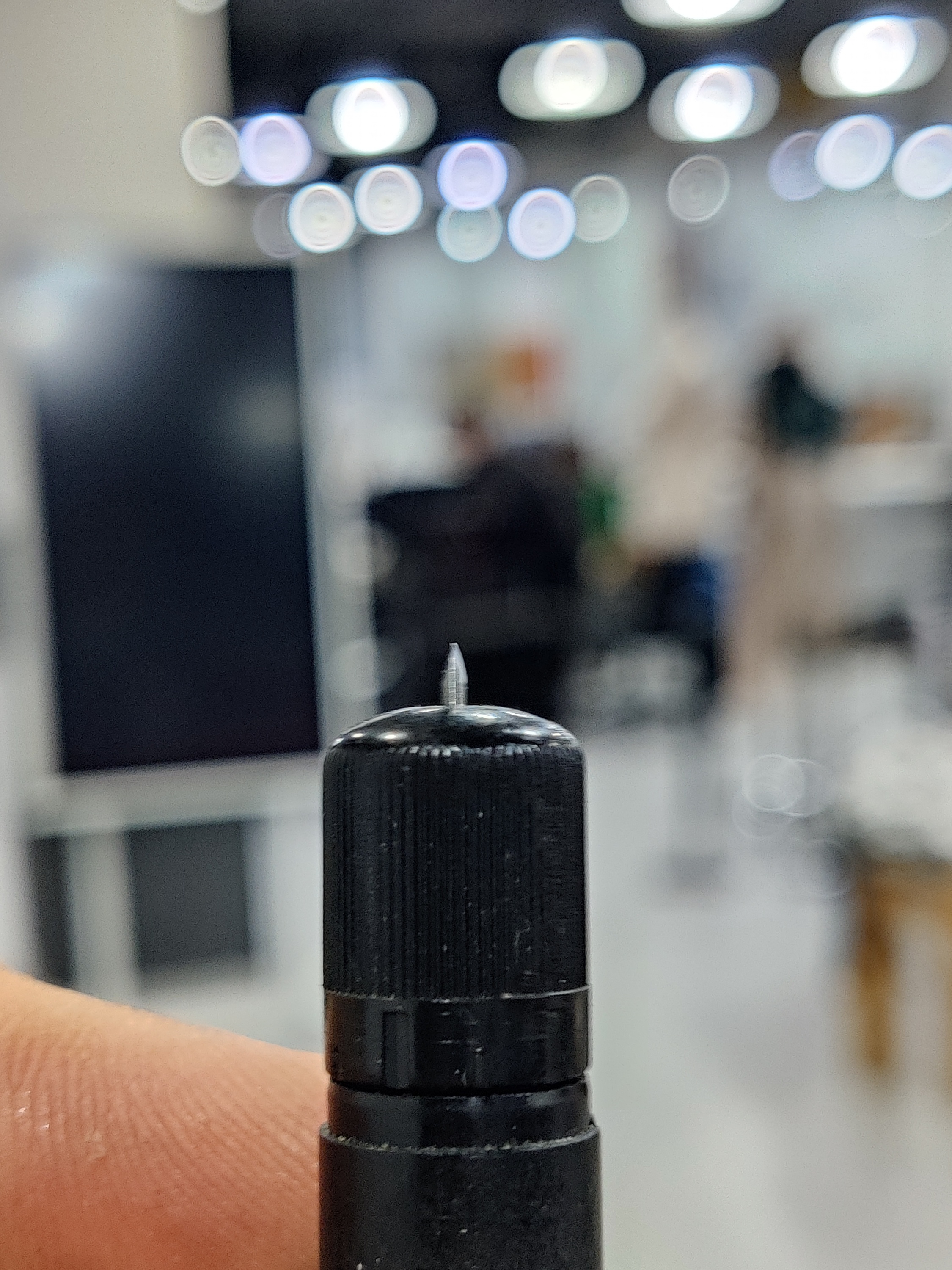
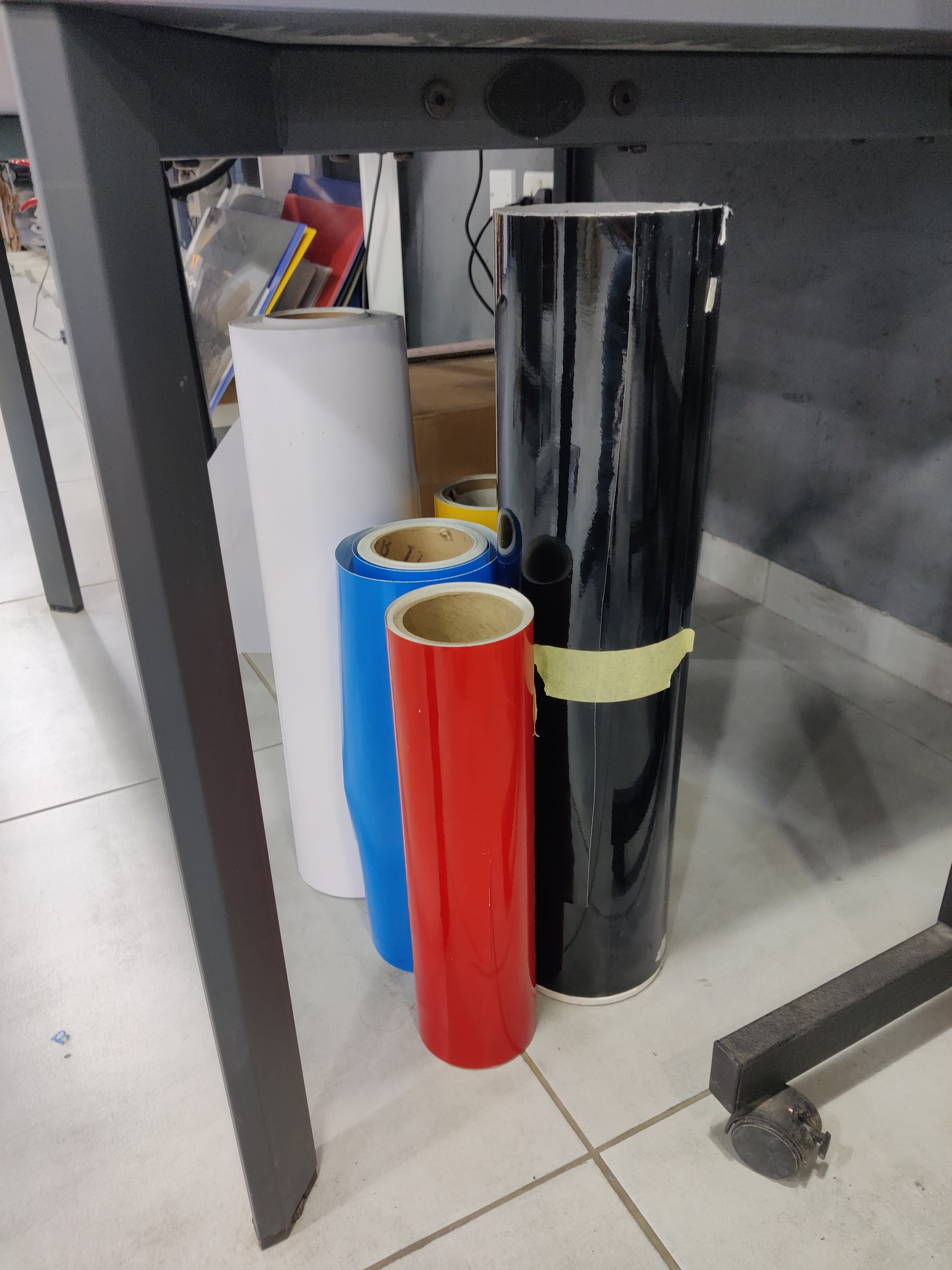
- Export Design from Inkscape
- After designing your artwork in Inkscape, export it as an SVG file.
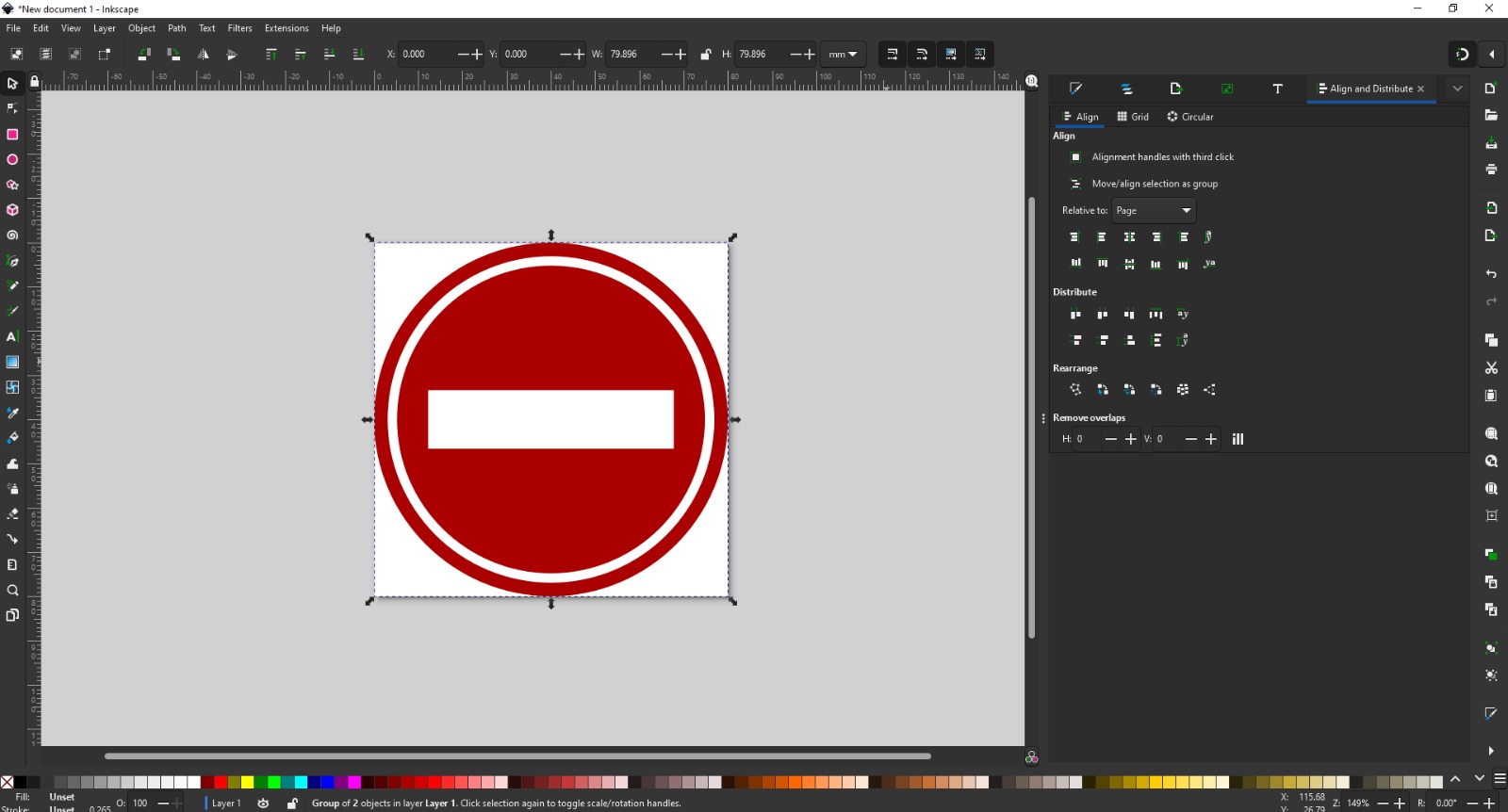
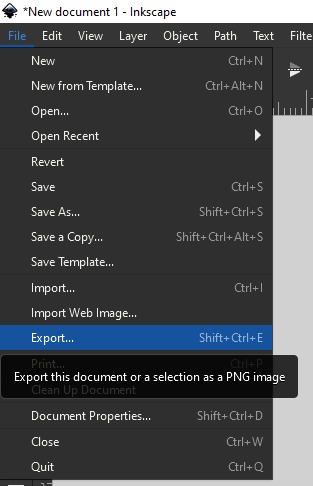
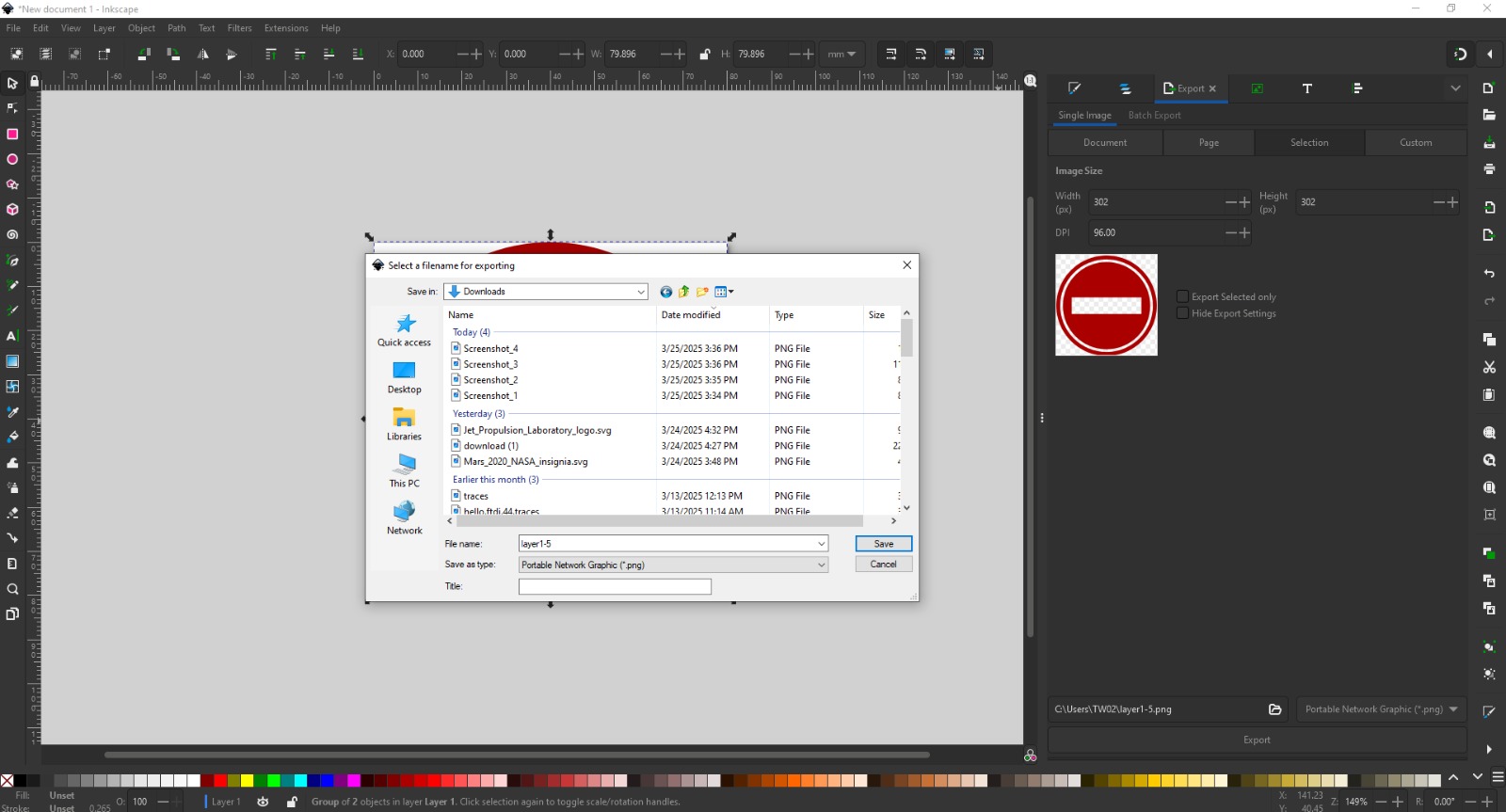
- Open CutStudio Software
- Launch Roland CutStudio on your computer.
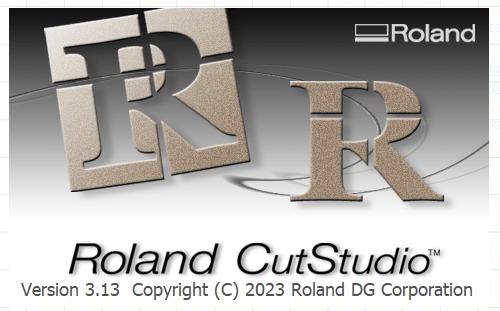
- Import the SVG File
- Right-click inside the workspace and select Import.
- Choose your exported SVG file.
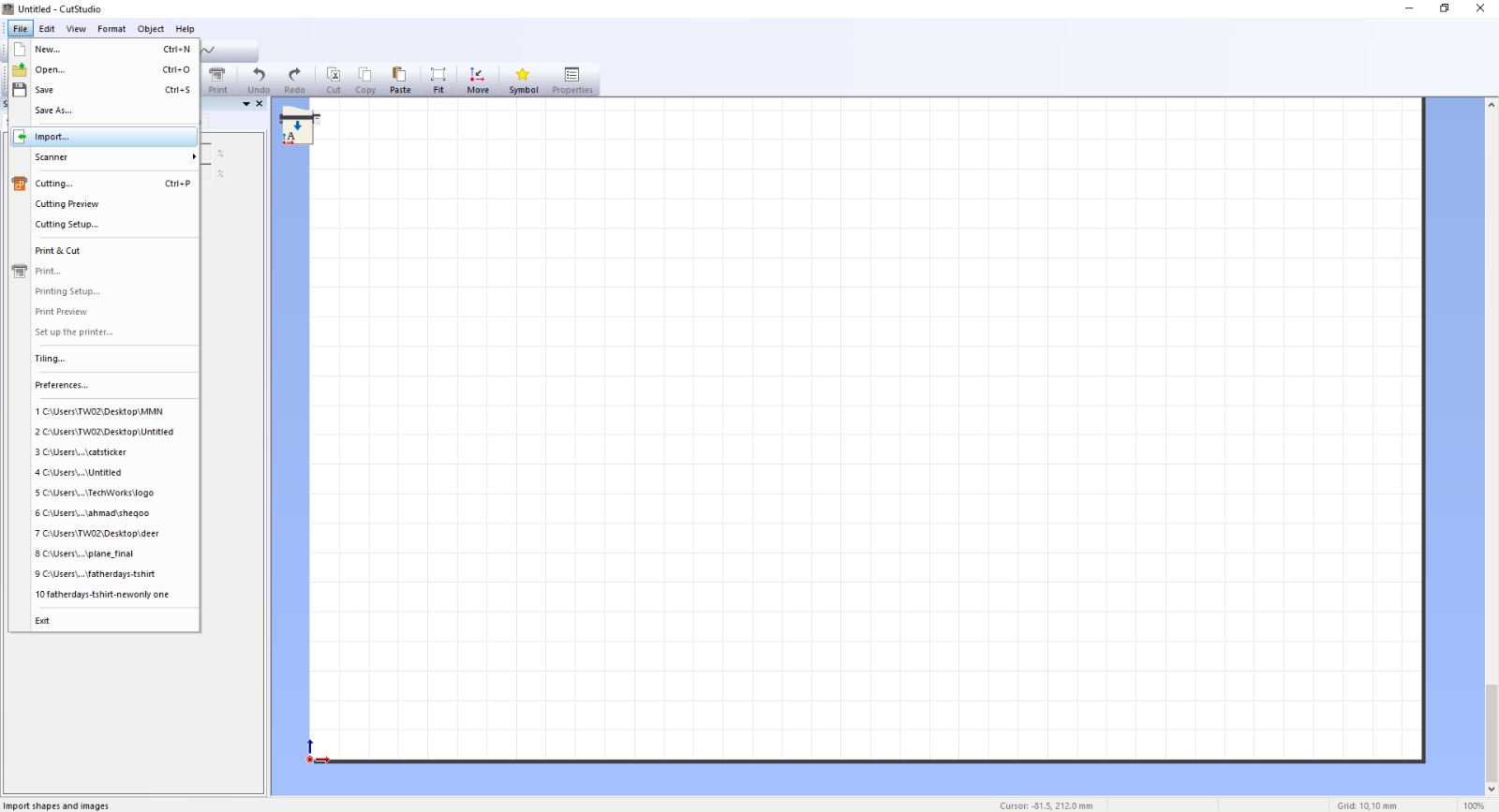
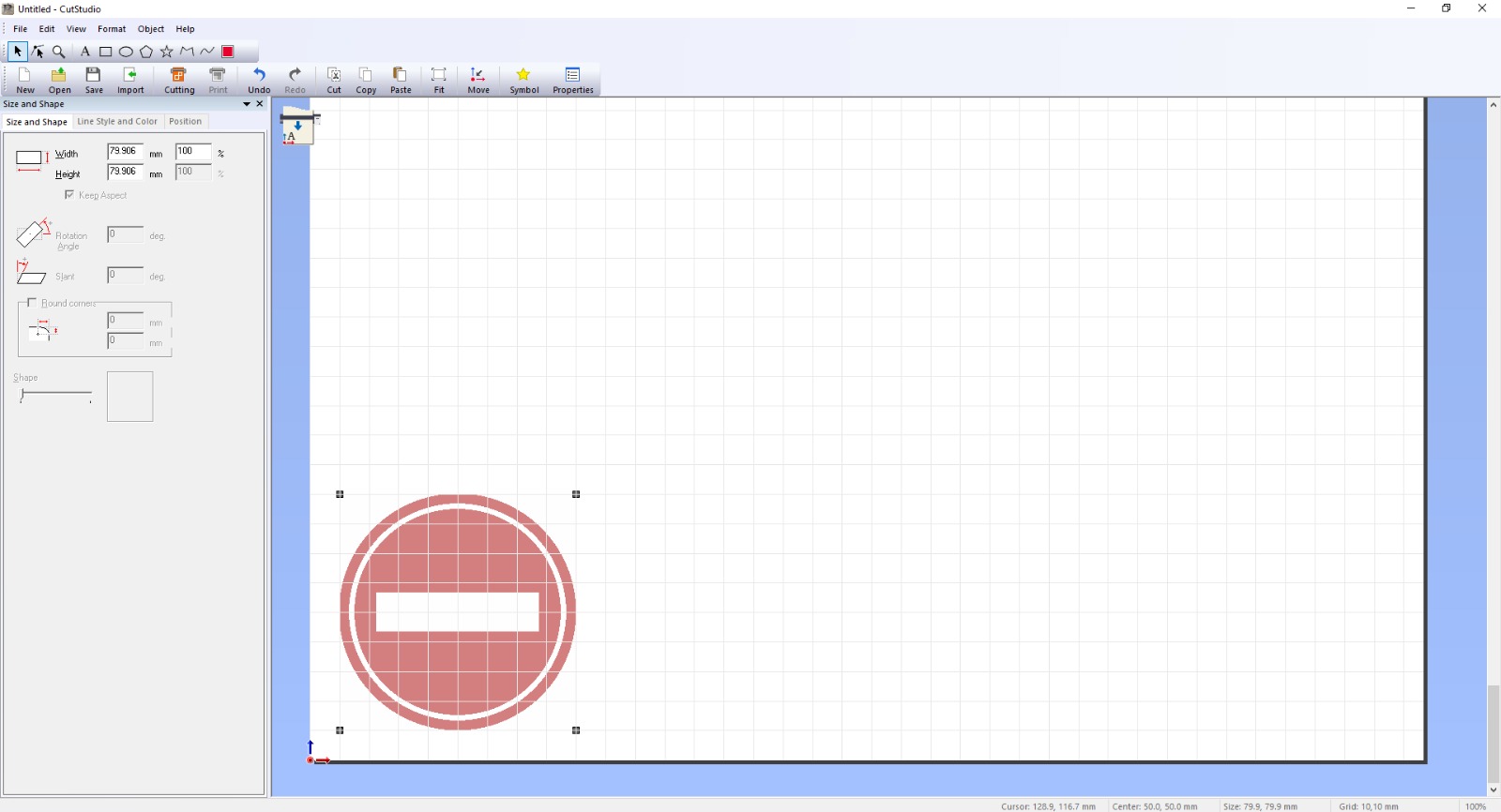
- Outline the Image
- After importing, right-click on the image and choose Image Outline (this converts your design into cuttable paths).
- Trace the Outline
- In the image outline settings:
- Adjust the alignment and image density if necessary.
- Confirm to generate the traced outlines.
- In the image outline settings:
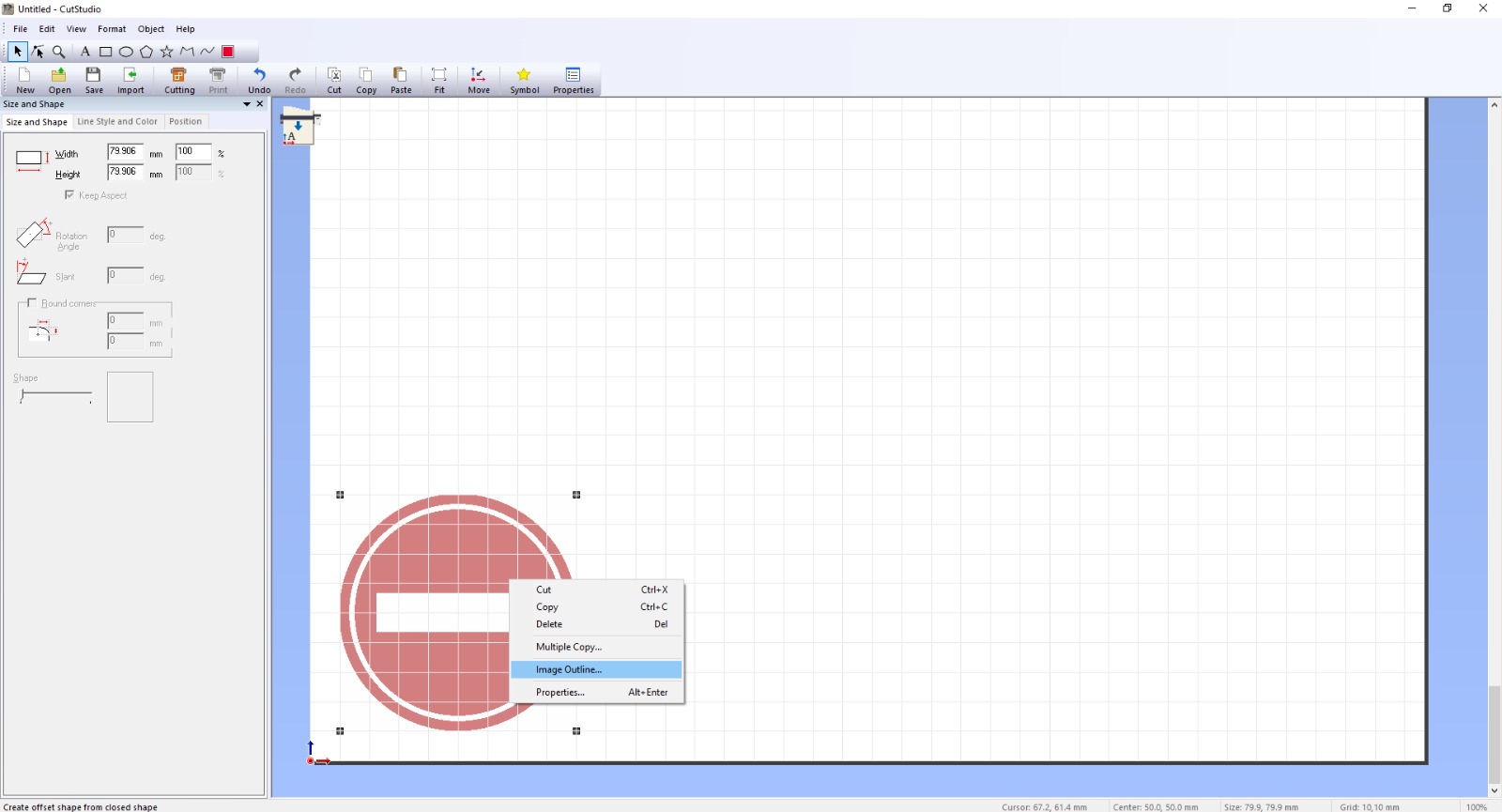
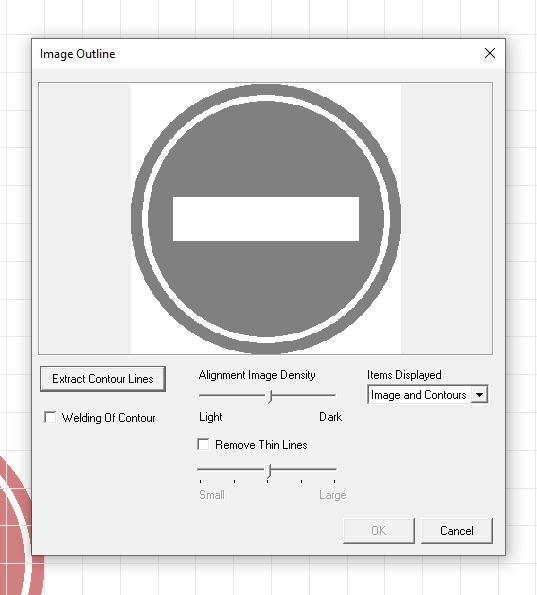
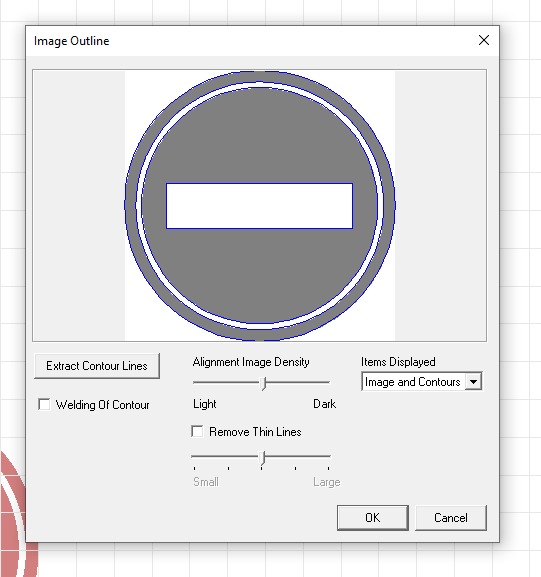
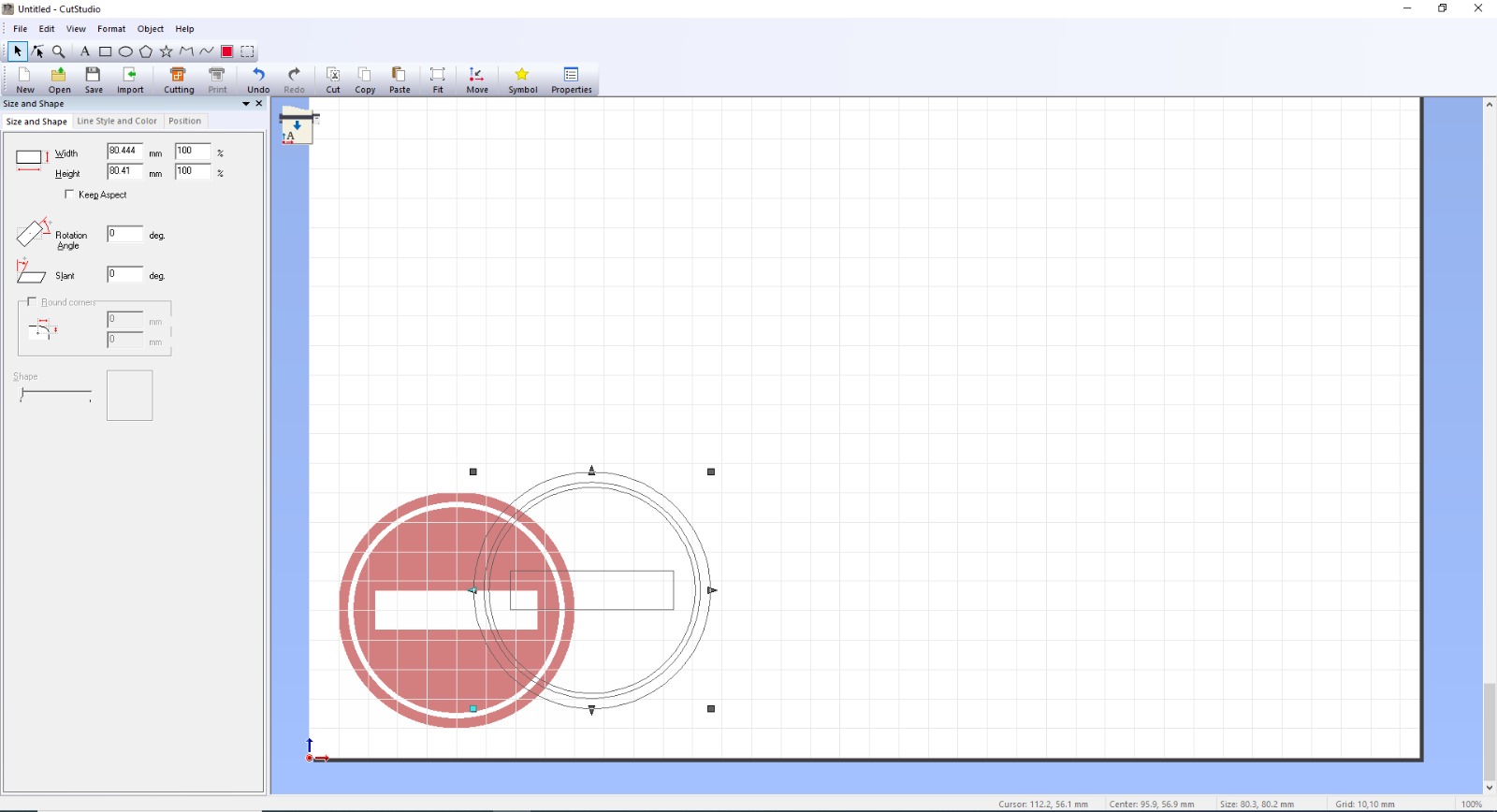
- Adjust Media Settings
- Go to File > Cutting Setup or toolbar settings.
- Select Get from Machine to fetch the correct media size (width and length).
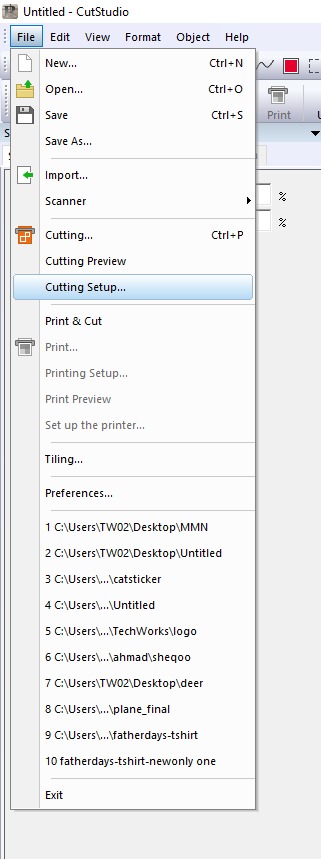
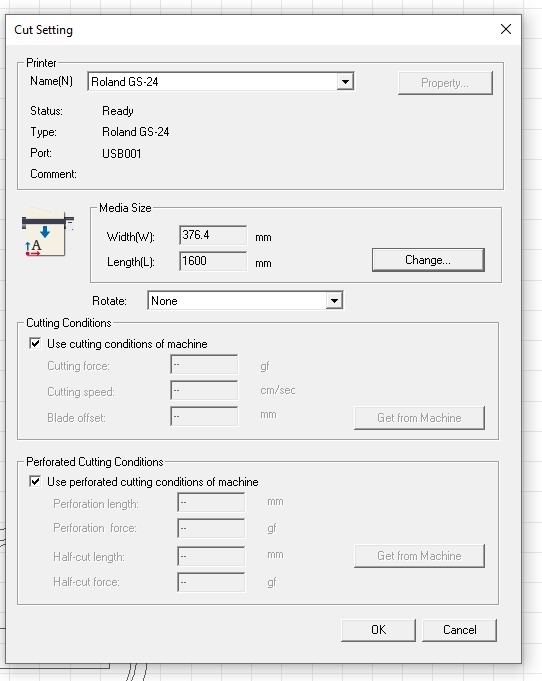
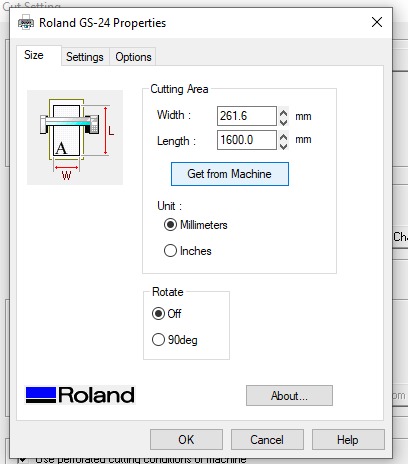
- Send to Cut
- Once your layout is ready and aligned within the media size, click Cutting in the toolbar.
- Confirm settings and start the cutting process.

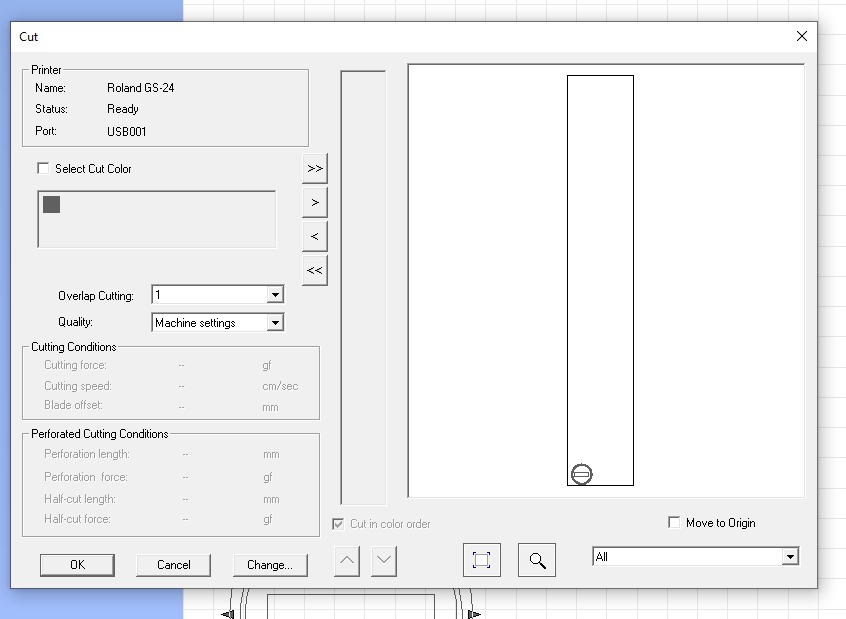
4. Transferring the Vinyl Design
- Use duct tape or transfer tape to lift the vinyl design while keeping it aligned.
- Carefully apply the sticker to the final surface to prevent air bubbles or misalignment.
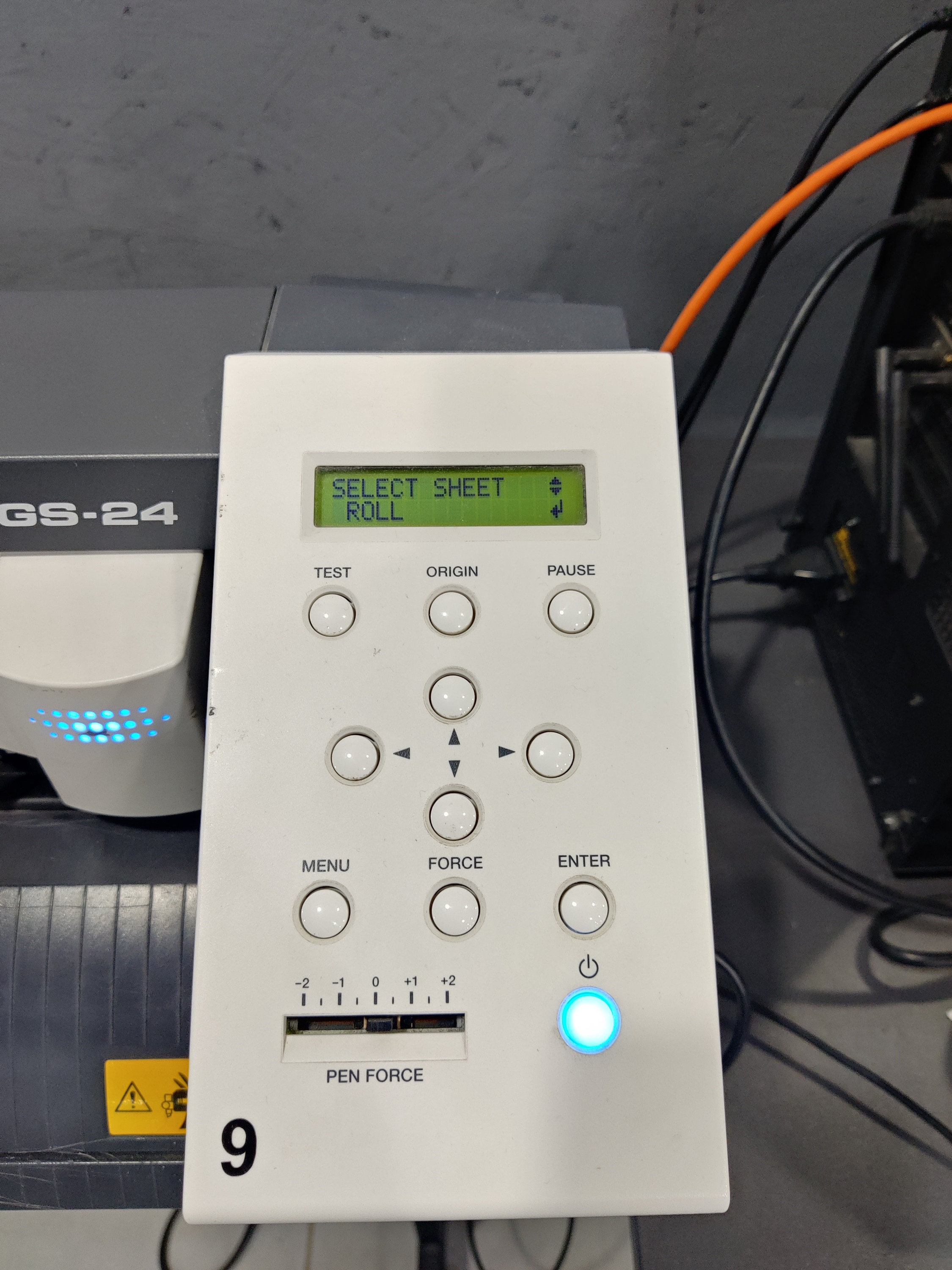
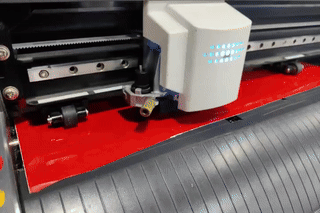
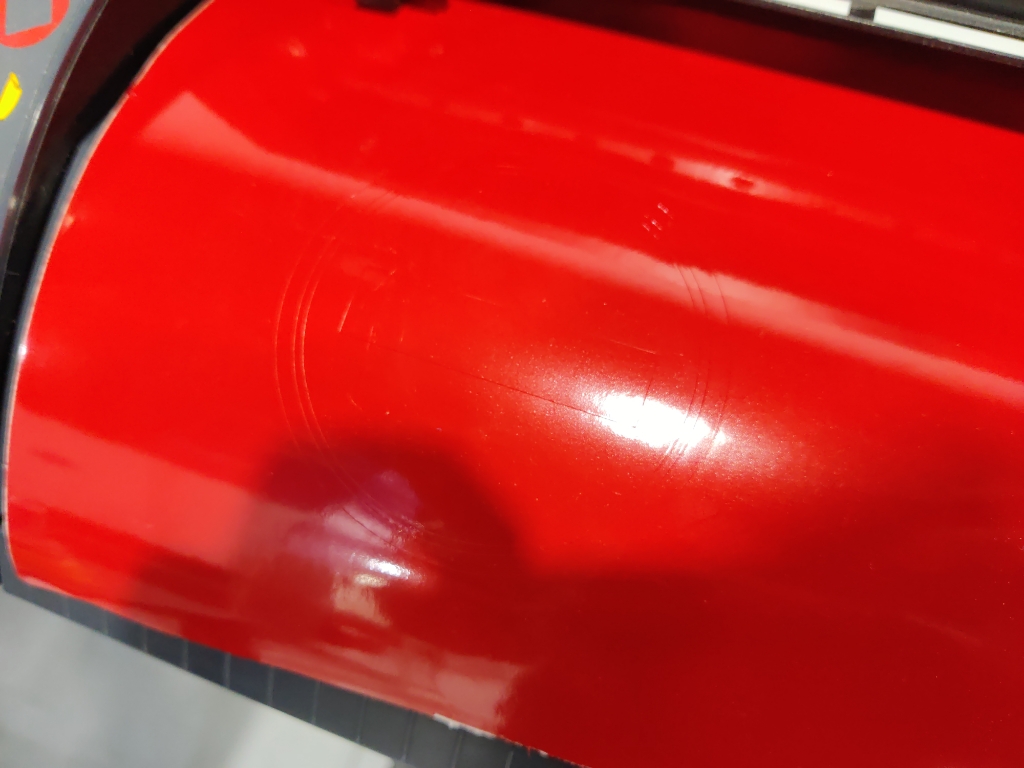
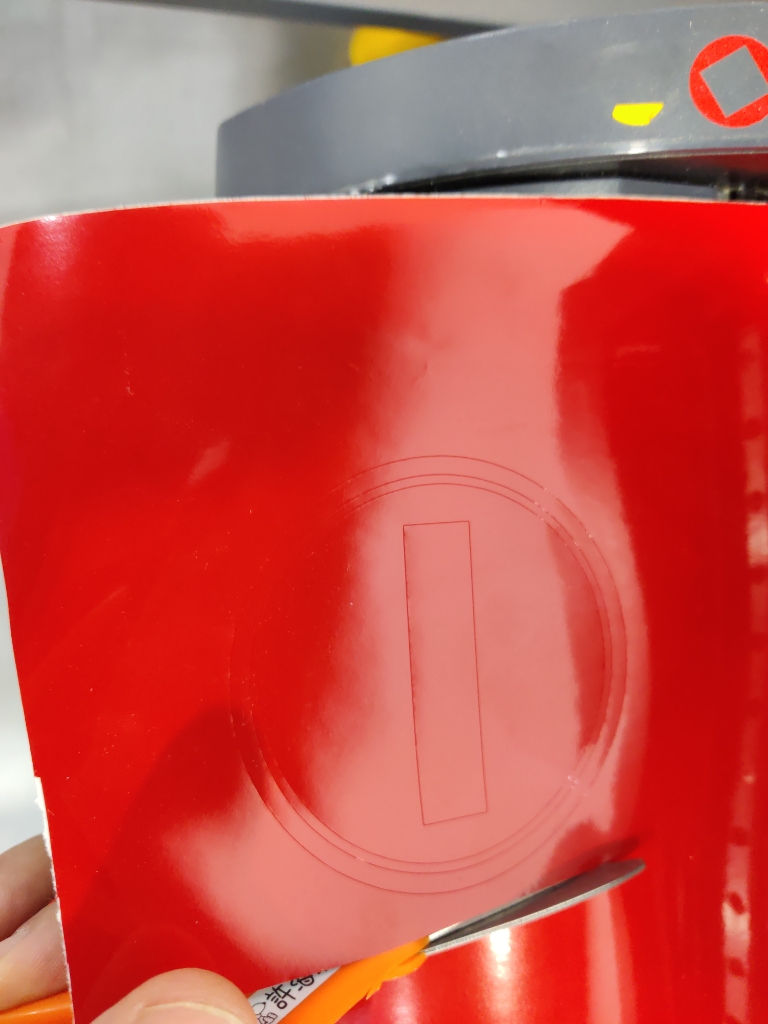
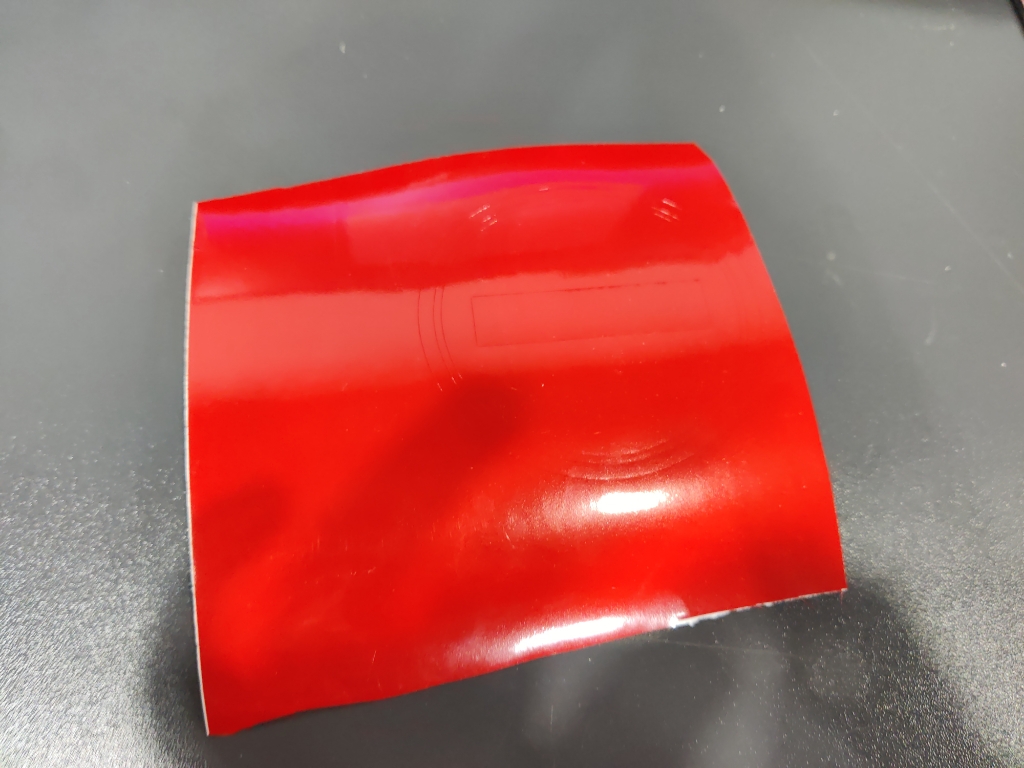
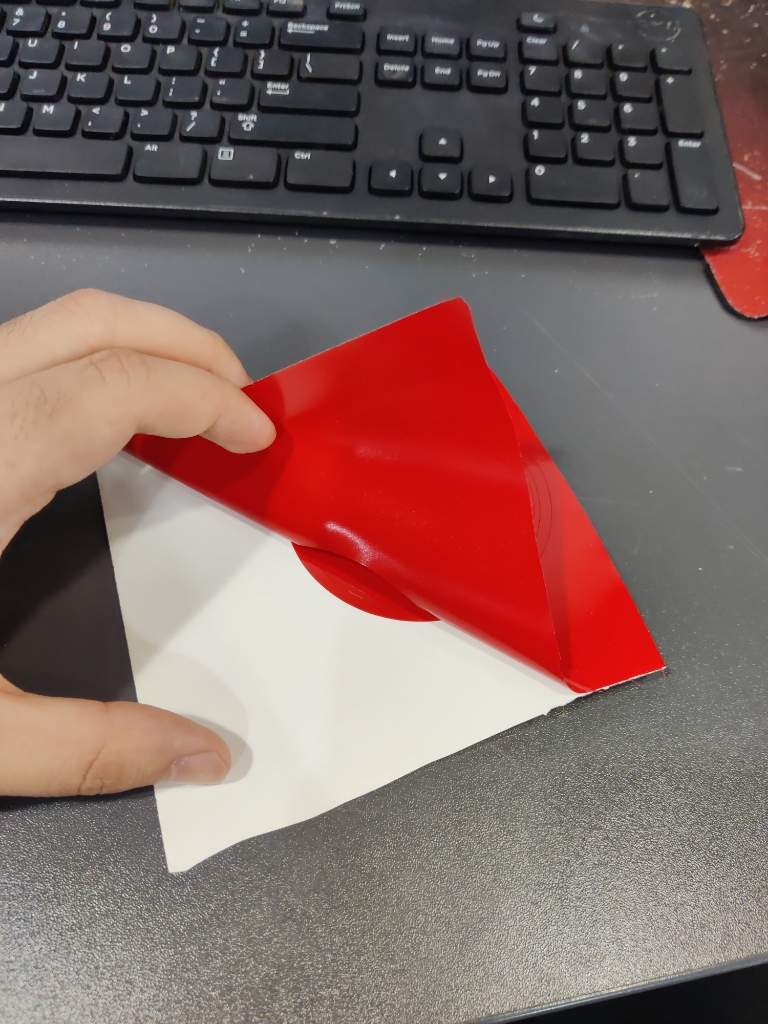
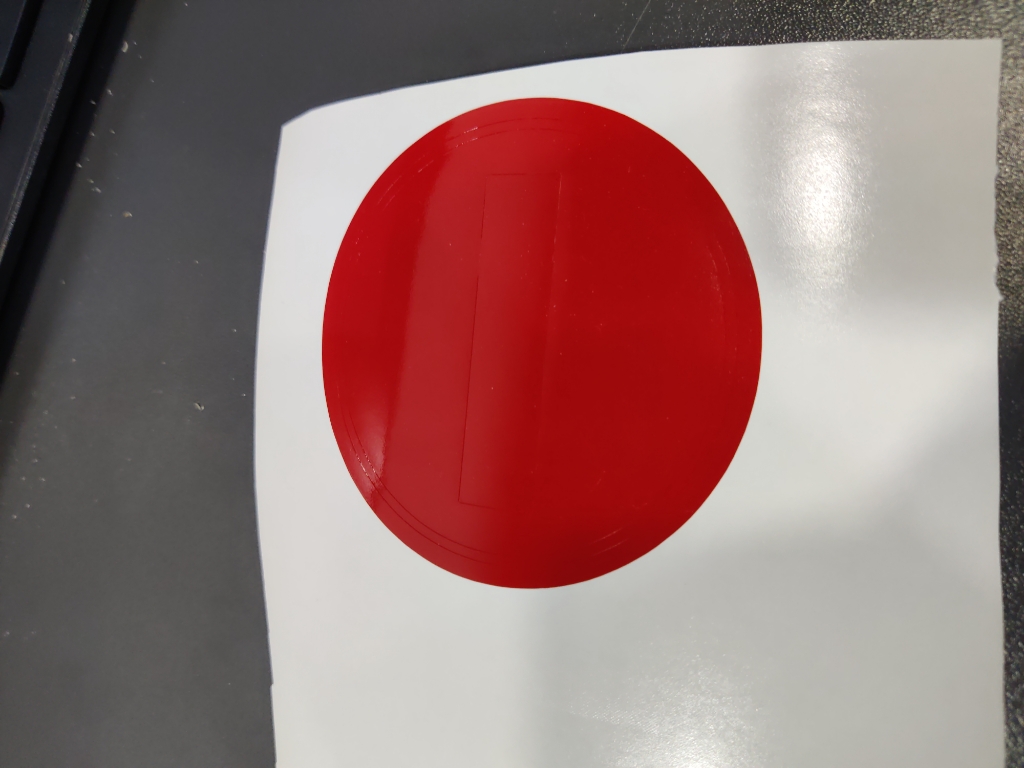
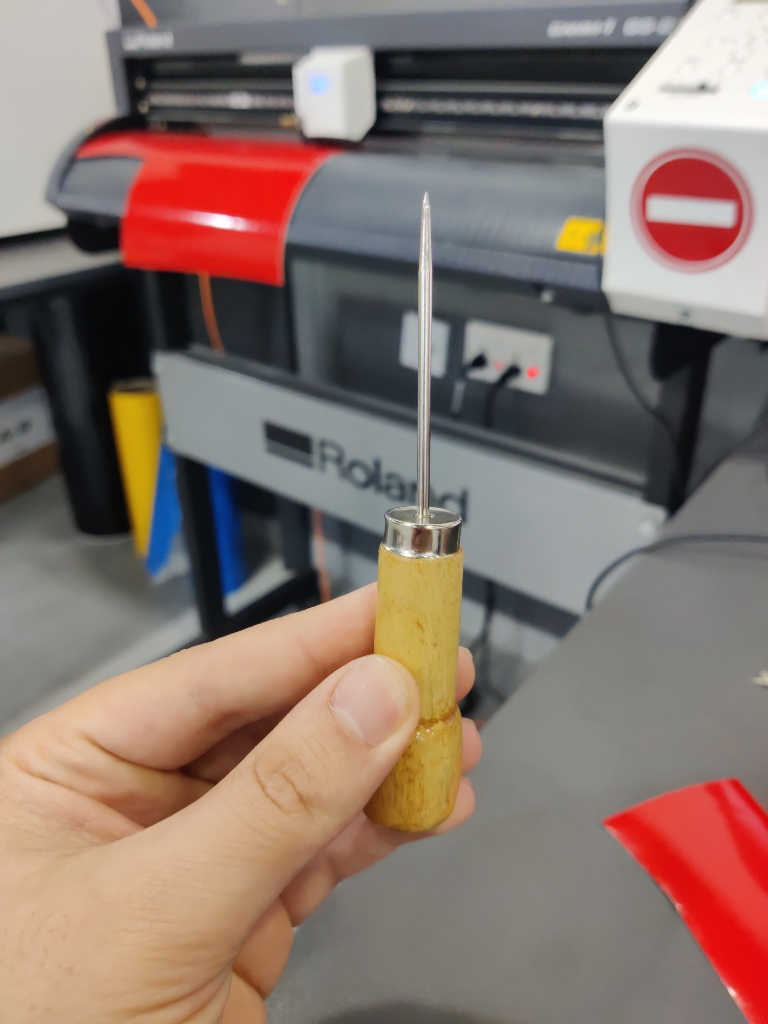
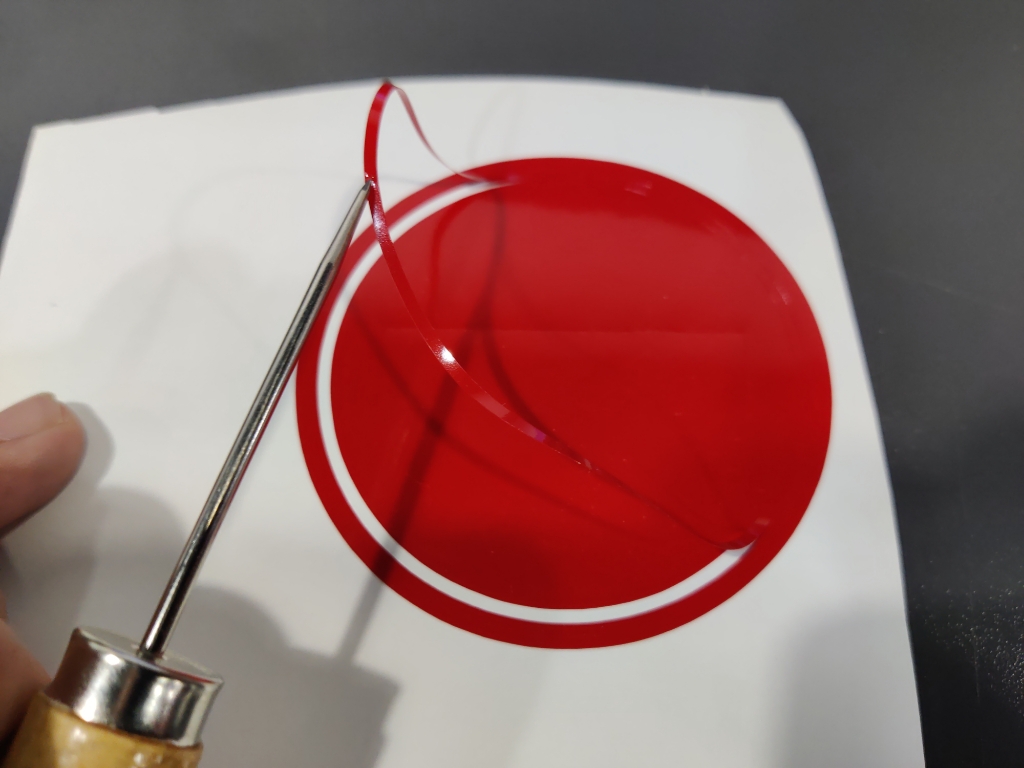
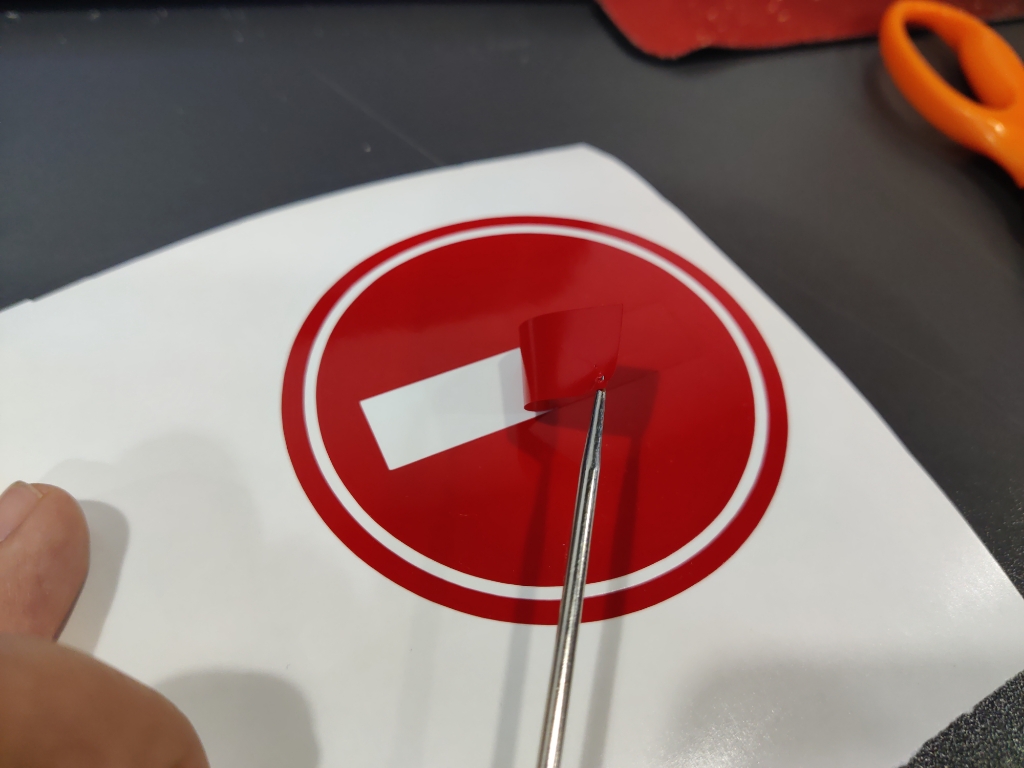
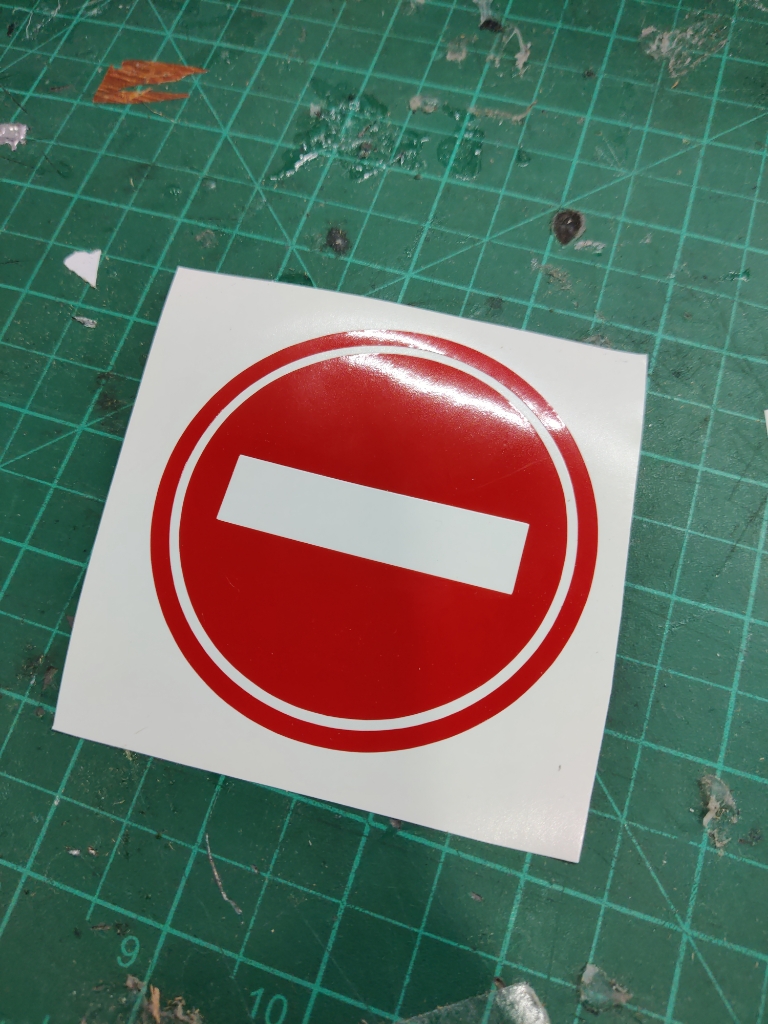
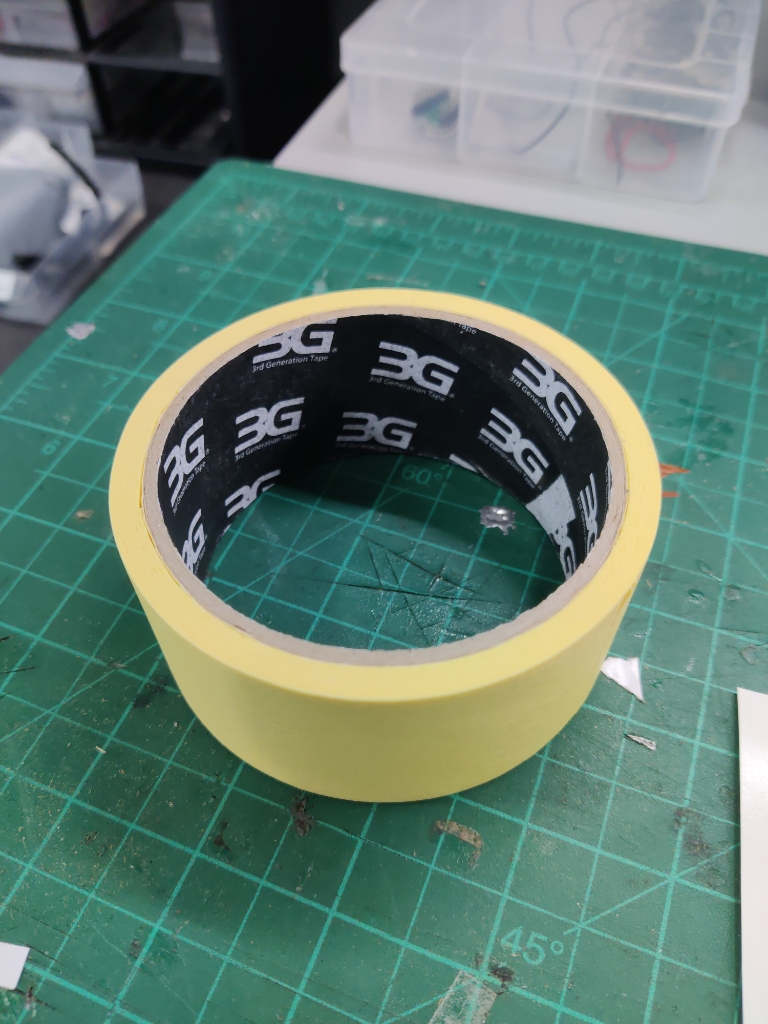
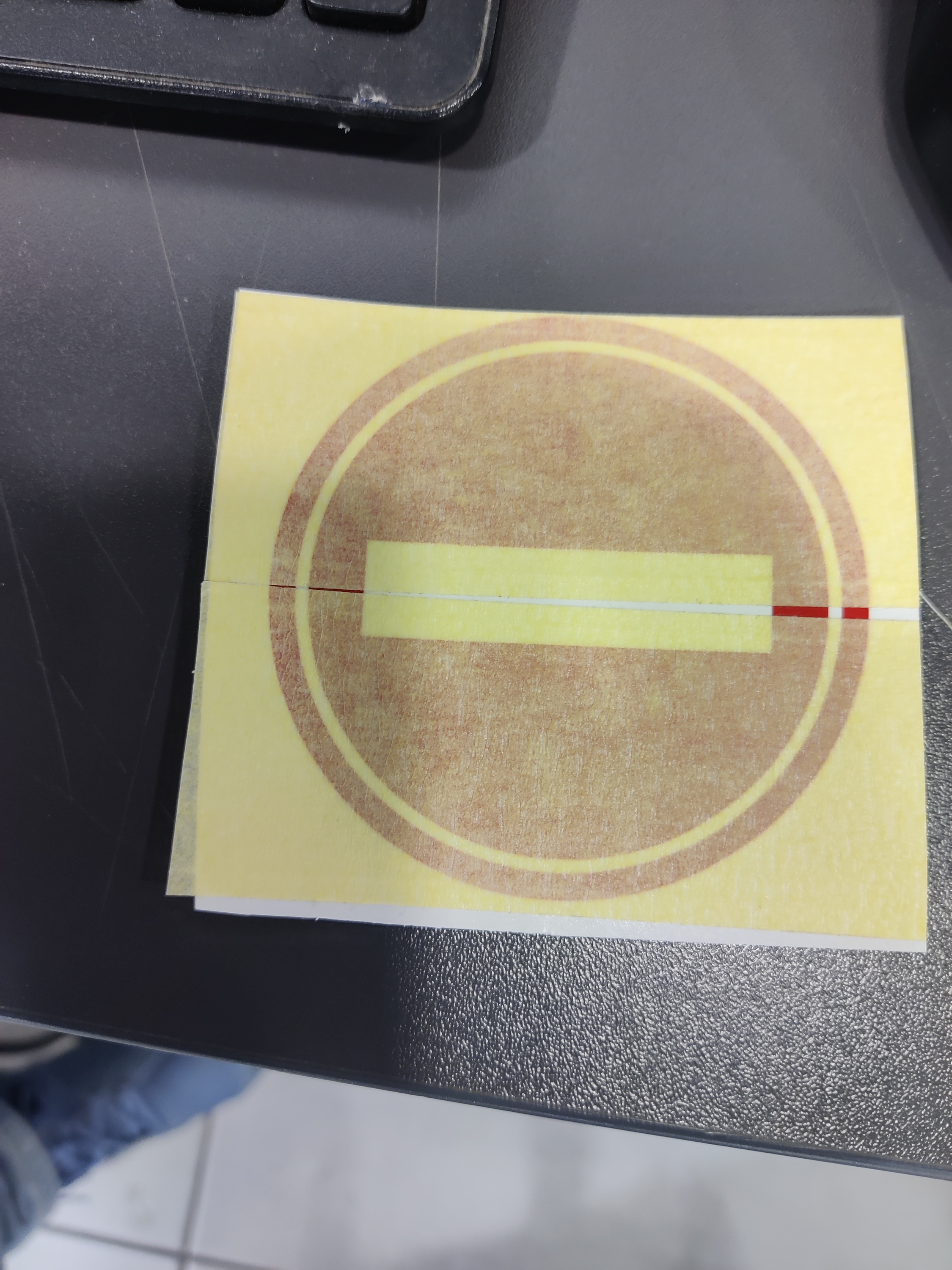

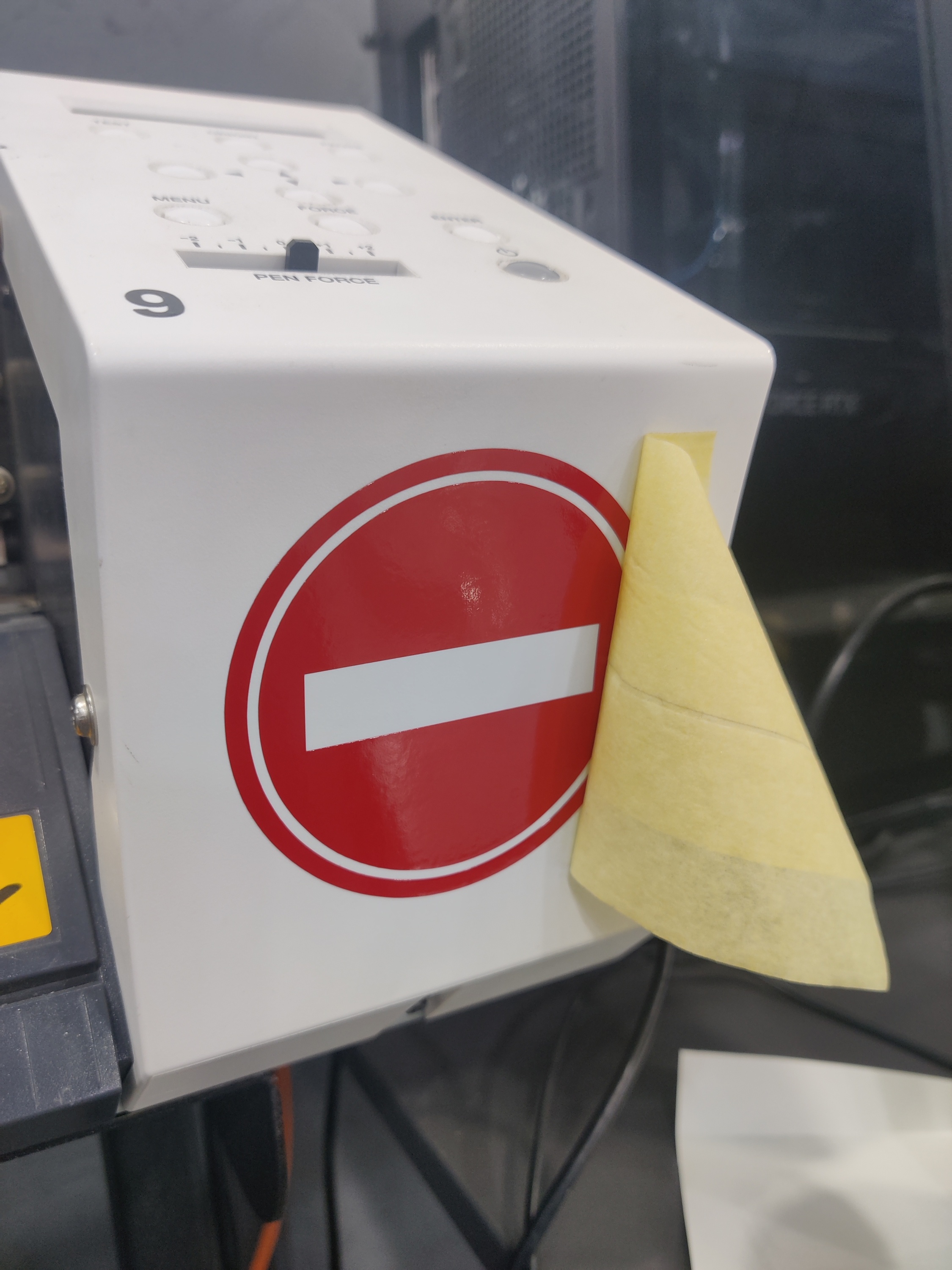
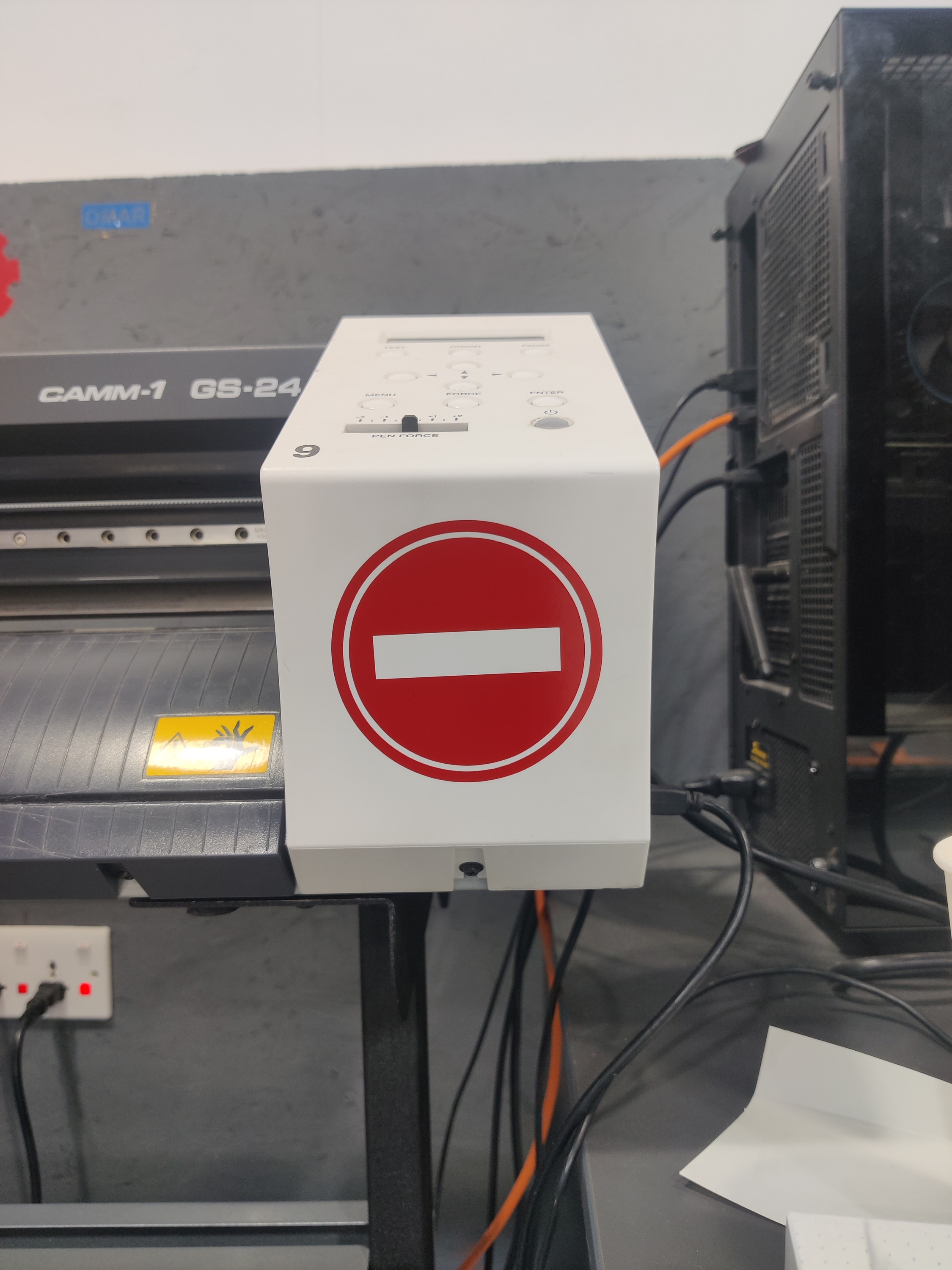
5. Creating a Stop Sign (Multi-Layered Design)
- Unlike the first single-color design, the stop sign required multiple layers.
- I repeated the same steps but cut separate layers for each color.
- After aligning the layers using transfer tape, I cut the final sign shape using a laser cutter.
- Finally, I stuck the vinyl sticker onto the laser-cut base for a clean finish.
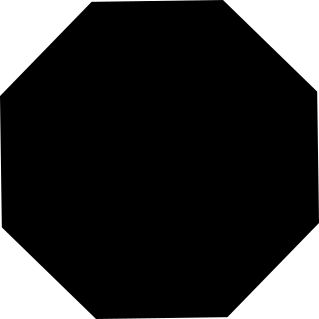
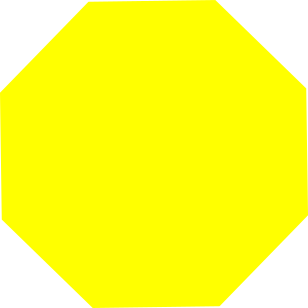
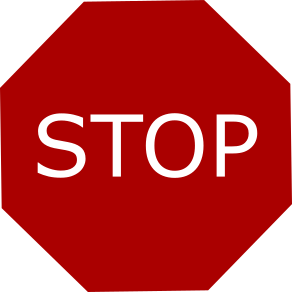
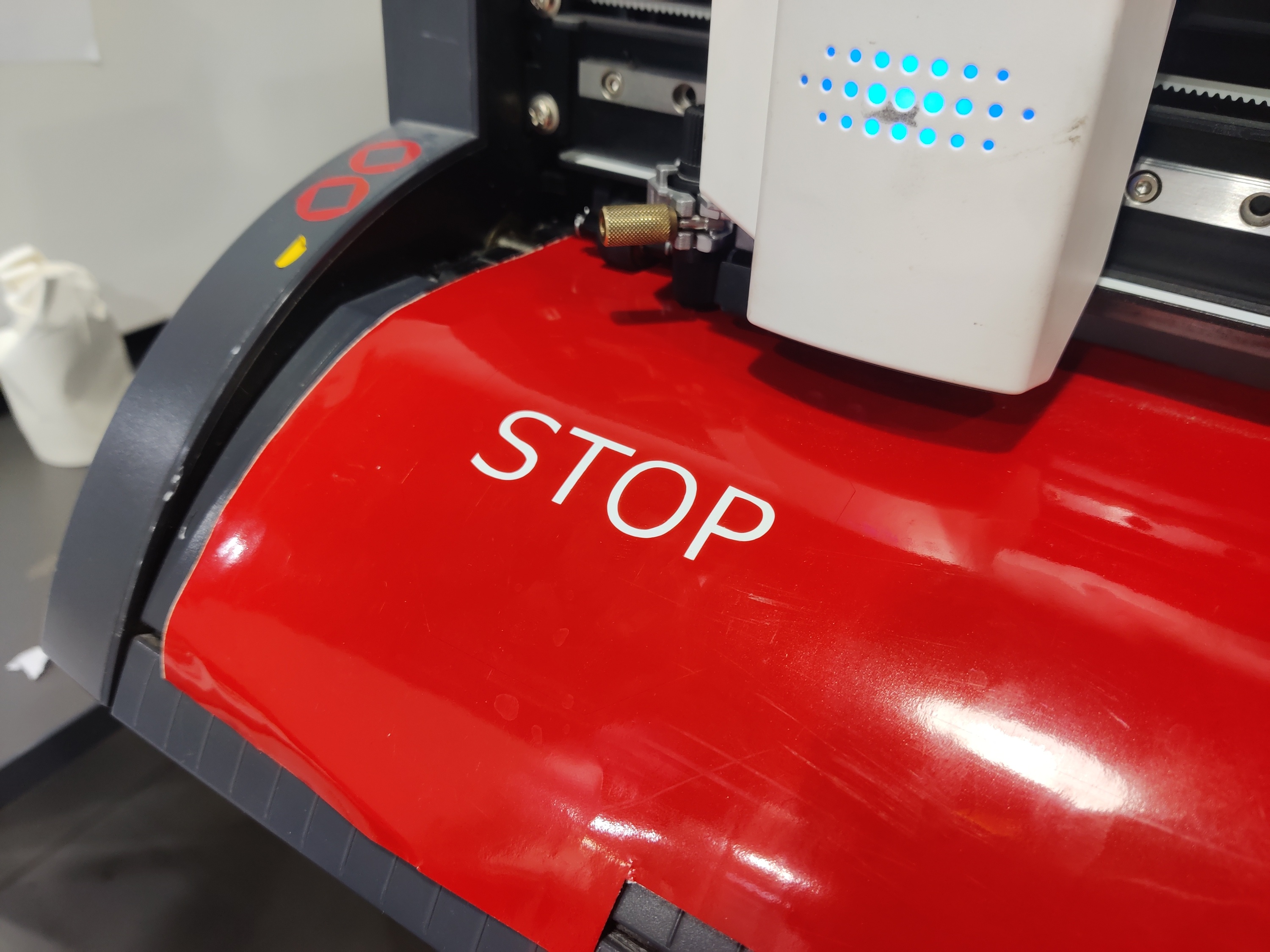
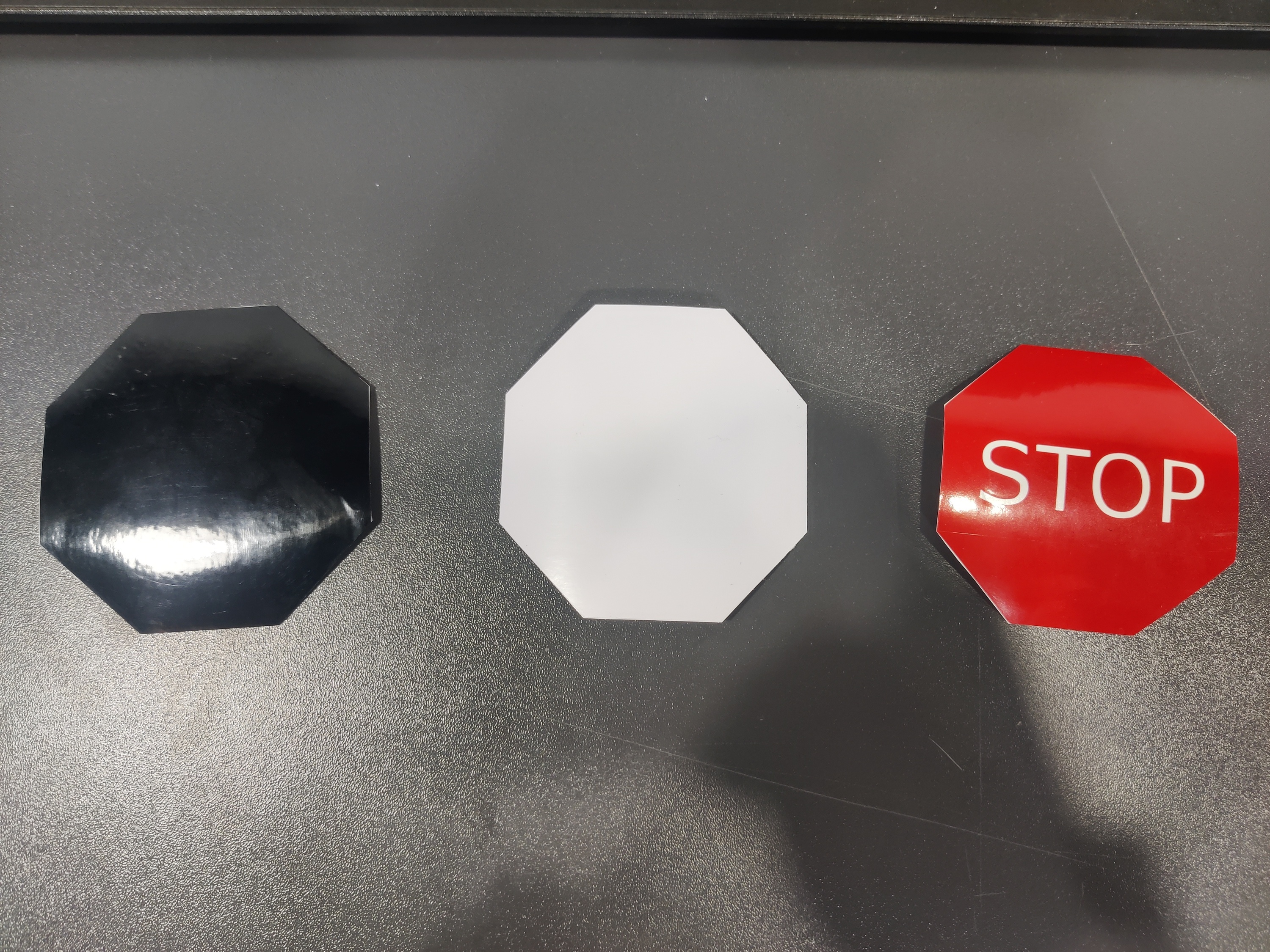
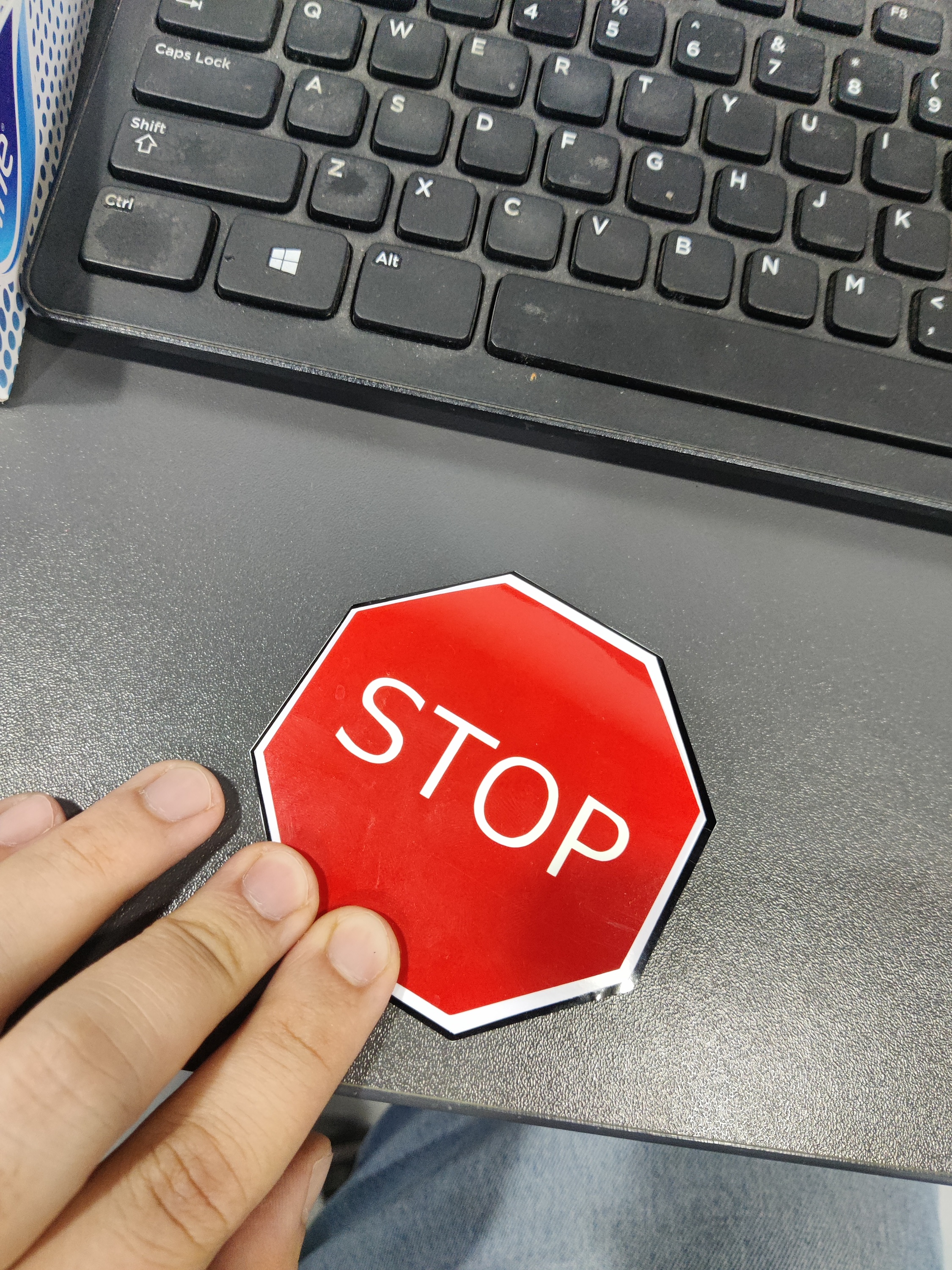
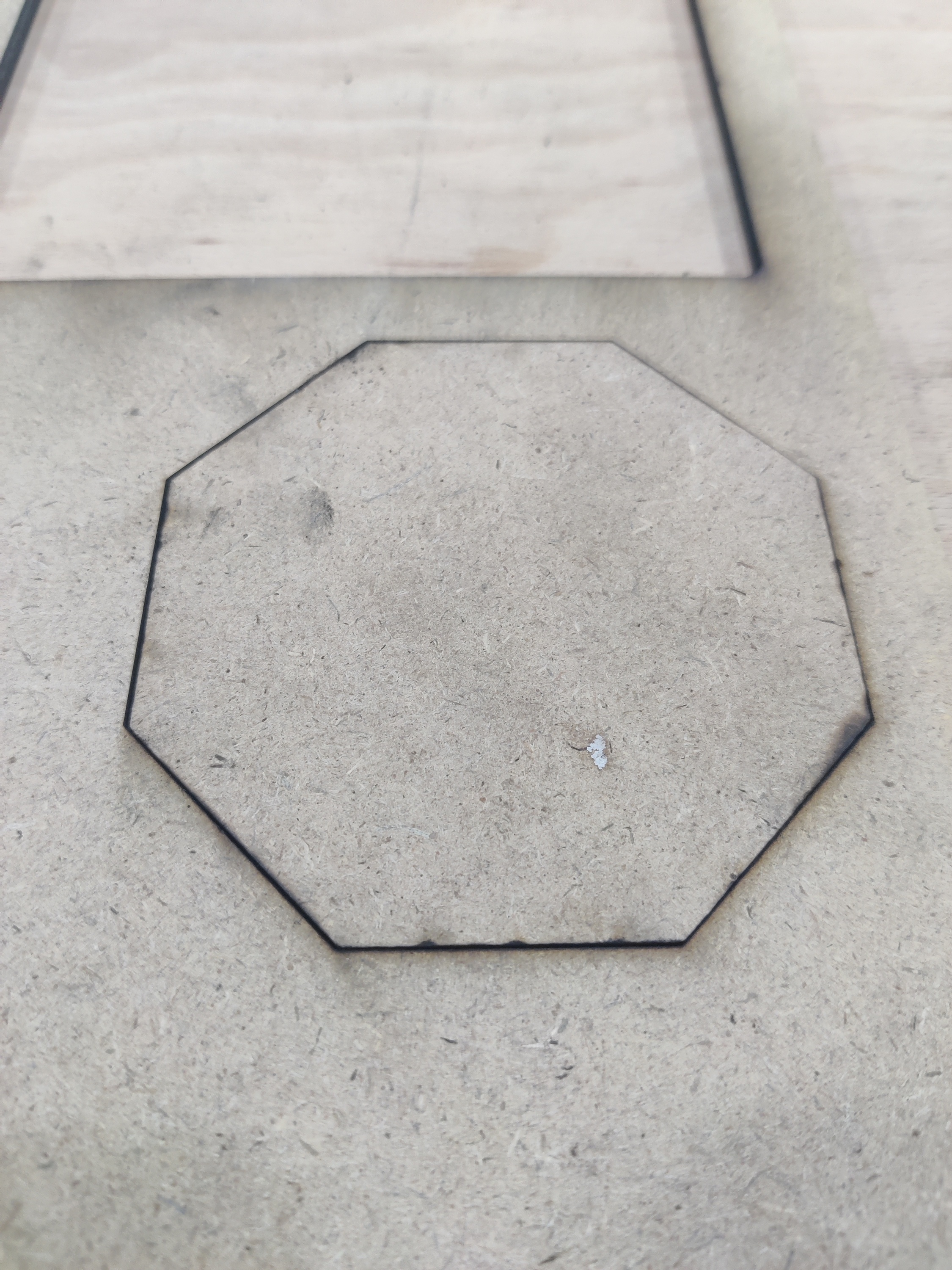
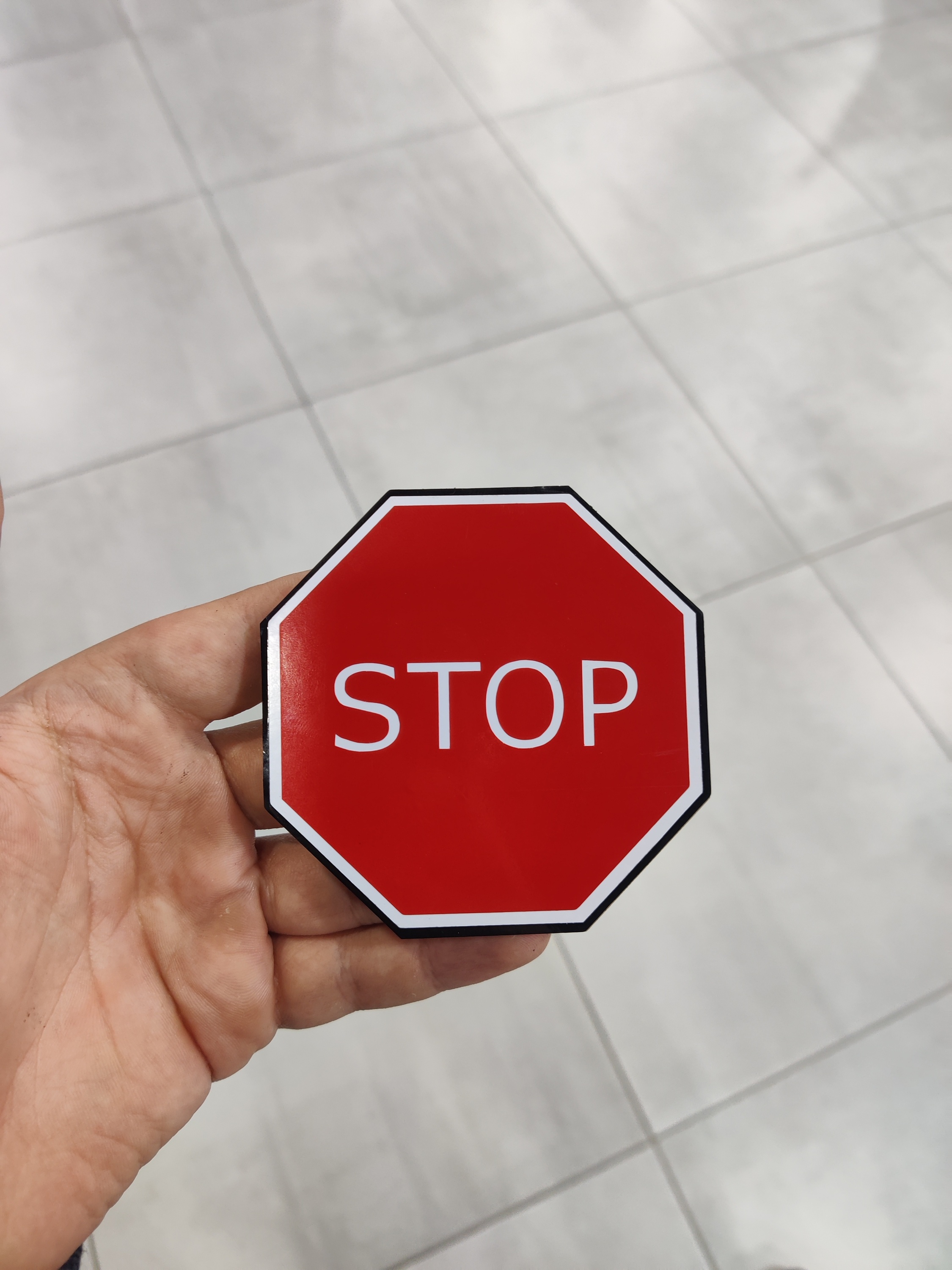
Learning Outcome
Through this experiment, I gained hands-on experience with the vinyl cutter, a powerful tool for creating stickers, logos, and layered designs. I learned the importance of calibrating the knife to ensure clean cuts and precise results. Additionally, I explored its applications in various industries, including custom t-shirt printing, signage, paper cutting, and even origami prototyping like making valley folds. This process also helped me understand layer-by-layer design techniques, improving my skills in alignment, vector preparation, and working with multi-layered graphics.