Vacuum Forming Machine
Hero Shot
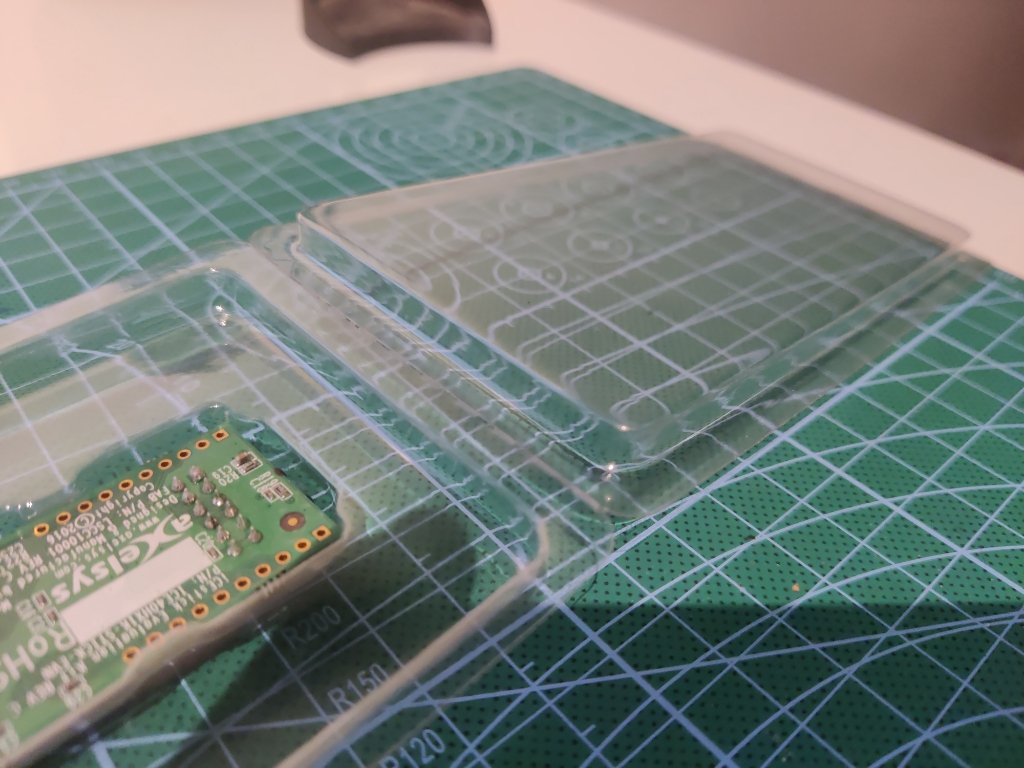
You might be wondering why I’m shifting from embedded programming to a vacuum forming machine—it seems like an odd transition, right? But here’s what happened: while working on my last board, the ICE40 FPGA, I started thinking about how the packaging for these chips was made. Curious, I asked my instructor, who explained that this type of packaging is created using a vacuum forming machine. Intrigued, I decided to explore it further. I gathered some raw materials and tested the process, considering how I could use it to create future product packaging for my own projects.
Summary
This week, I had extra time to explore the Formech 508DT Vacuum Forming Machine. I started by reading the official documentation from the company and learning about its features, setup, and operating procedures. I then tested the machine to understand its functionality and workflow. This documentation outlines my experience with setup, operation, and key takeaways from working with the vacuum forming process.
Work Process Detail
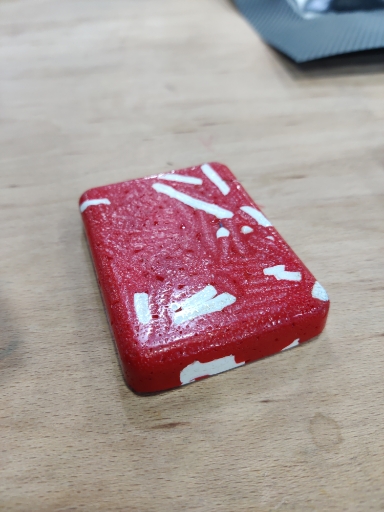
1. Understanding the Formech 508DT Machine
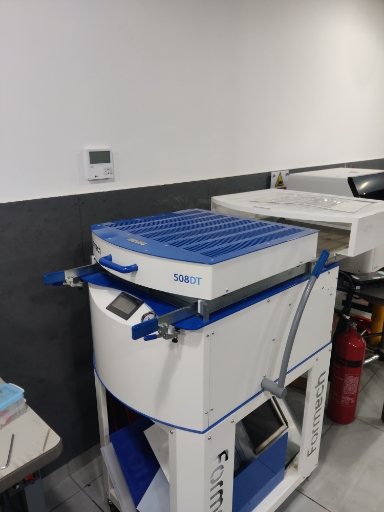
Before operating the Formech 508DT, I reviewed the official manual to understand its capabilities and specifications.
Key Features of the Formech 508DT:
✅ Forming Area: 482mm x 432mm (19" x 17")
✅ Max Depth of Draw: 185mm (7.3")
✅ Max Material Thickness: 6mm (0.25")
✅ Quartz Heating System: Provides fast and even heating.
✅ Four Heating Zones: Allows independent control for precise forming.
✅ HMI Touchscreen Interface: Offers easy operation and saved program functions.
✅ Vacuum System: Uses a dry-running diaphragm vacuum pump for forming plastic sheets.
This machine is designed for prototyping, small-scale production, and educational purposes, making it ideal for experimenting with different materials.
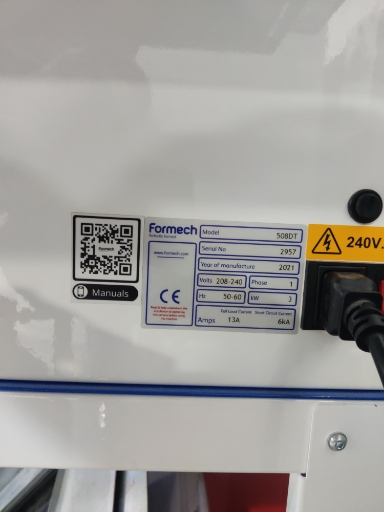
2. Setting Up and Operating the Machine
Following the company's documentation, I performed a general test of the vacuum forming process.
🛠️ Setup Process:
✅ Placed the machine on a stable surface with adequate ventilation.
✅ Connected the power supply and ensured proper earthing.
✅ Checked the clamping frame and vacuum seals for proper alignment.
✅ Loaded a plastic sheet into the machine.
🔹 Operating the Vacuum Former:
1️⃣ Powered on the machine using the HMI touchscreen interface.
2️⃣ Preheated the quartz heating elements, adjusting heating zones based on material thickness.
3️⃣ Moved the heater forward to soften the plastic sheet.
4️⃣ Monitored the plastic softening point (when it started sagging slightly).
5️⃣ Engaged the vacuum system to form the plastic sheet over the mold.
6️⃣ Allowed the formed plastic to cool before releasing the vacuum.
7️⃣ Removed the final formed part for inspection.
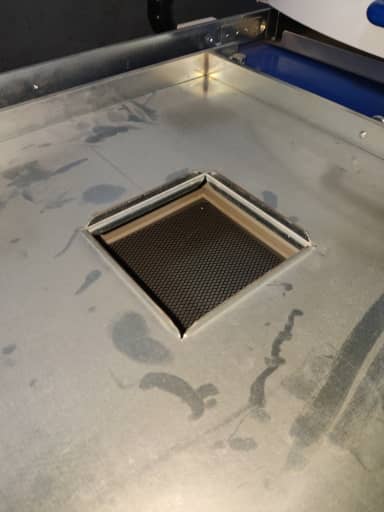
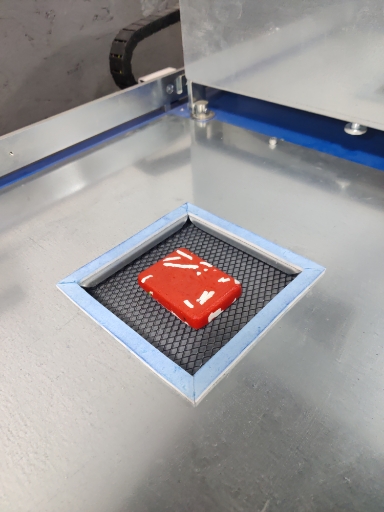
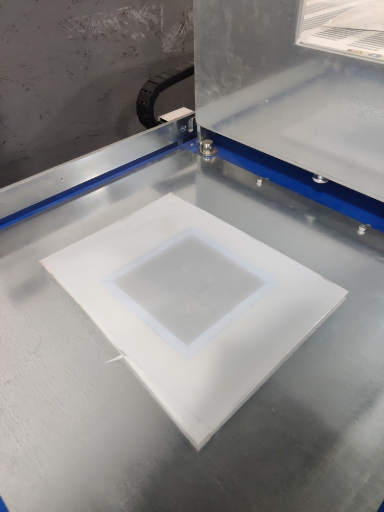
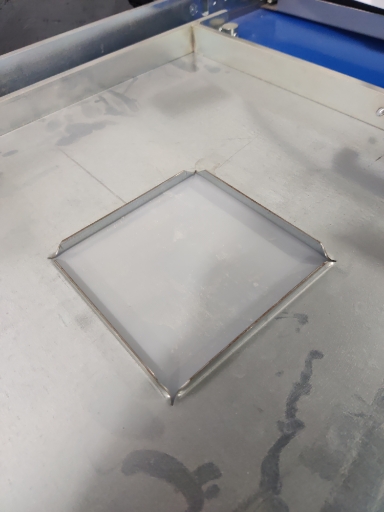
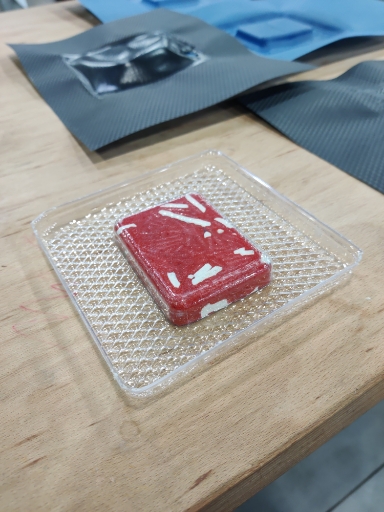
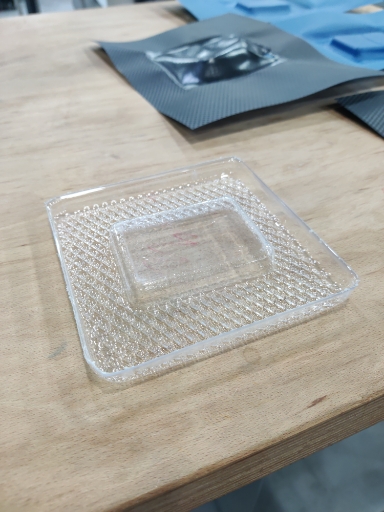
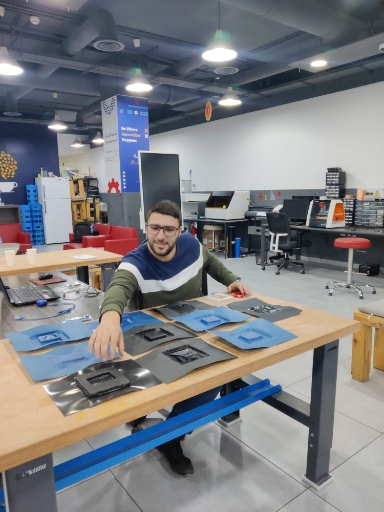
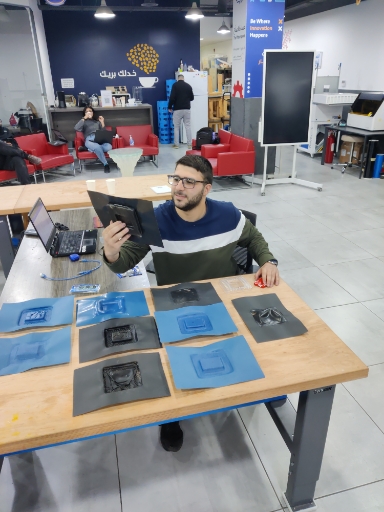
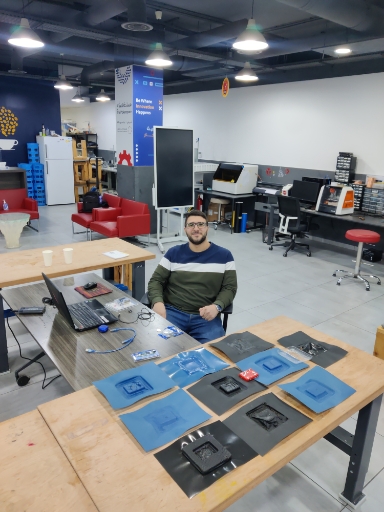
✅ Tested different heat settings and forming times to observe variations in results.
Learning Outcome
sing the Formech 508DT gave me hands-on experience in vacuum forming, an essential process in rapid prototyping and manufacturing. I learned how material thickness, heat distribution, and vacuum timing affect the final formed shape. Additionally, working with the HMI control system provided insight into automated machine control and preset configurations for repeatable results.This experience will help me apply vacuum forming techniques to prototyping projects, custom enclosures, and product design, integrating it with my knowledge of CNC, laser cutting, and 3D printing for multi-process manufacturing workflows. 🚀