Probe Digital / Analog Device
Summary
During the Input Devices week, our group explored various sensors and how to read their outputs using an oscilloscope and a microcontroller. We selected multiple sensors and used an Arduino board as the primary controller. We began with an infrared speed sensor, which we used to calculate the RPM of a motor. By attaching a disk with specific hole patterns to a shaft, the sensor could detect interruptions in light and output a square wave signal. We verified this signal using both the oscilloscope and the Arduino serial plotter.
Next, we tested a thermal temperature sensor based on an NTC thermistor. We applied heat using a soldering station and observed real-time temperature changes through the serial plotter. Lastly, we worked with a rotary encoder, which includes two Hall effect sensors (A and B) to determine rotational directionâclockwise or counterclockwise. This sensor's signals were also verified using both oscilloscope and software tools.
The group assignment
Page :
Work Process Detail
We used the Arduino Plotter and an Oscilloscope to plot the output.
1. Infrared Speed Sensor¶
The Infrared Speed Sensor Module is an IR counter that has an IR transmitter and receiver. If any obstacle is placed between these sensors, a signal is sent to the microcontroller. The module can be used in association with a microcontroller for motor speed detection, pulse count, position limit, etc.
How it works
When operating, the infrared light-emitting diode continuously emits infrared light (invisible light), and the phototransistor will conduct if it receives it.

We connected the sensor to the Arduino and plotted the output. When thereâs no object between the photodiode and phototransistor, the output is zero, and if thereâs an object, the output is one.
Arduino Code
#define Sensor A1
void setup() {
// put your setup code here, to run once:
Serial.begin(9600);
pinMode(Sensor,INPUT);
}
void loop() {
// put your main code here, to run repeatedly:
int SensorRead = digitalRead (Sensor);
Serial.println (SensorRead);
delay(100);
}
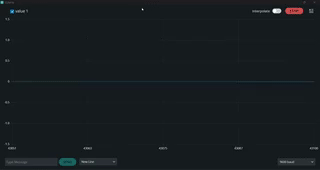
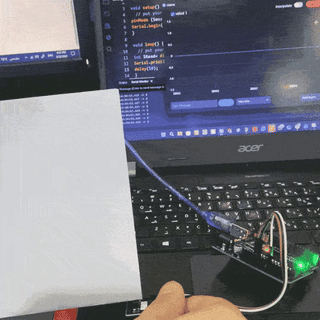
2. Thermistor Thermal Temperature Sensor¶
The Thermistor Temperature Sensor consists of an NTC (Negative Temperature Coefficient) thermistor, which measures temperature variations. This module provides both digital and analog outputs. An NTC thermistor is a variable resistor whose resistance decreases as temperature increases. The sensorâs sensitivity can be adjusted using the onboard potentiometer.

Arduino Code
#define Sensor A1
void setup() {
// put your setup code here, to run once:
Serial.begin(9600);
pinMode(Sensor,INPUT);
}
void loop() {
// put your main code here, to run repeatedly:
int SensorRead = analogRead (Sensor);
Serial.println (SensorRead);
delay(100);
}
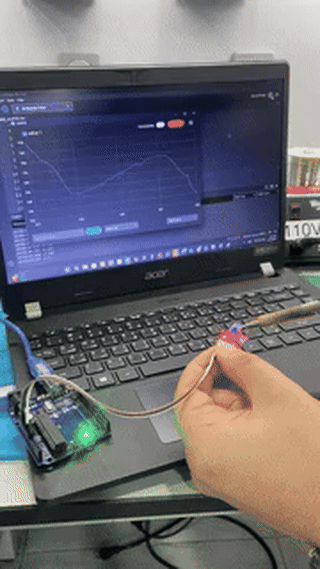
3. Rotary Encoder¶
A Rotary Encoder is a position sensor used to determine the angular position of a rotating shaft. It generates an electrical signalâeither analog or digitalâbased on rotational movement.

How It Works When the disk rotates step by step, pins A and B make contact with the common pin, generating two square wave output signals.
Any of the two outputs can be used to determine the rotational position by counting pulses. However, to determine the direction of rotation, both signals must be considered simultaneously. By counting each step where the signal transitions from High to Low or Low to High, we can determine whether the signals have opposite values and thus identify the rotation direction.

Arduino Code
#define Sensor 3
void setup() {
// put your setup code here, to run once:
Serial.begin(9600);
pinMode(Sensor,INPUT);
}
void loop() {
// put your main code here, to run repeatedly:
int SensorRead = digitalRead (Sensor);
Serial.println (SensorRead);
delay(100);
}
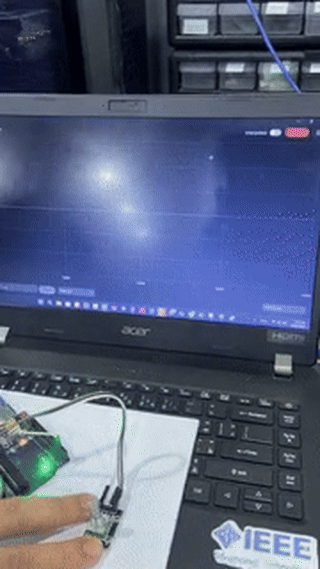
Learning Outcome
Through this weekâs assignment, I learned how to work with various input devices and interpret their signals. I gained a deeper understanding of how input data is captured and processed to influence system behavior. This knowledge is critical in designing any interactive system, as input devices are the foundation for generating responsive outputs. The range and potential of sensors are vast, and understanding how to choose and apply them effectively is key to successful prototyping and development.