Week 18
Assignment: Applications and Implications, Project Development
Individual assignment
- What will it do?
- Who has done what beforehand?
- What will you design?
- What materials and components will be used?
- Where will they come from?
- How much will they cost?
- What parts and systems will be made?
- What processes will be used?
- What questions need to be answered?
- How will it be evaluated?
- What tasks have been completed?
- What tasks remain?
- What has worked? What hasn't?
- What questions need to be resolved?
- What will happen when?
- What have you learned?
Scope of the Project
Onion Storage Climate Monitor & Controller
Scope Statement
Build a portable, autonomous monitoring and control system that:
Measures temperature and humidity inside traditional onion storage cabins.
Automatically actuates a fan or heater via relay to maintain optimal conditions (e.g. 25‑30 °C, 65‑75 % RH).
Logs data locally and optionally sends alerts to a mobile app/web dashboard.
Operates on battery or mains supply, capable of ~12 hours runtime if battery-powered.
Designed for makers, allowing full replication using accessible materials and digital fabrication.
In Scope:
System design: electronic sensing, relay control, microcontroller programming.
Enclosure: 2D/3D design and fabrication (laser/CNC + 3D-print).
Power system: battery management or mains + basic charging/regulation.
UI/Interfacing: onboard or app-level monitoring (e.g., via Wi‑Fi or BLE).
Testing: lab performance testing and field validation in actual onion storage.
Out of Scope (for now):
Cloud dashboard with user accounts.
Extra sensors (CO₂, gas, etc.).
Mass manufacturing or IP certification.
Project Plan: Schedule & BOM
A. Schedule Overview
Week 1: Finalize scope, complete this plan + BOM
Week 5: 2D/3D enclosure design; order parts
Week 8: Design & board mill PCB + initial firmware (sensing + logging)
Week 10: Integrate relay control and power circuit; build enclosure
Week 16: Electronics assembly & full system integration
Week 17: Iterative testing (temp control threshold tuning)
Week 18: Field test in storage environment
Week 19: Finalize documentation, website updates, prepare video demo
Track Progress with a Project Tracker
Here's a progress tracker you can maintain (e.g., in your GitHub or sheet):
Task | Status | Target Date | Notes |
---|---|---|---|
Define scope & scope statement | ✅ Done | Week 1 | Completed above |
Draw enclosure in 2D & 3D (CAD) | ✅ Done | Week 5 | CAD files completed and approved |
Order/mill PCB & components | ✅ Done | Week 6 | All components received |
Write/flash firmware (sensing + logs) | ✅ Done | Week 11 | Firmware tested and uploaded |
Integrate relay & power circuit | ✅ Done | Week 15 | Circuit integration completed |
Print & assemble enclosure | ✅ Done | Week 16 | Enclosure printed and assembled |
Full electronics assembly | ✅ Done | Week 17 | All electronics assembled and tested |
Integration & system testing | ✅ Done | Week 18 | System calibrated and validated |
Field testing (onion cabin) | ✅ Done | Week 19 | Field tests completed successfully |
Final documentation & demo | ✅ Done | Week 20 | Documentation complete, demo ready |
What will it do?
This project aims to build a functional storage monitoring device which is used for traditional onion storage cabin. It will allow farmers to monitor the condition of their stored onion. The primary goal is reduce the onion wastage while storing the onions for more than three months. The product can control external fan or heating machine to control the temperature of the environment.
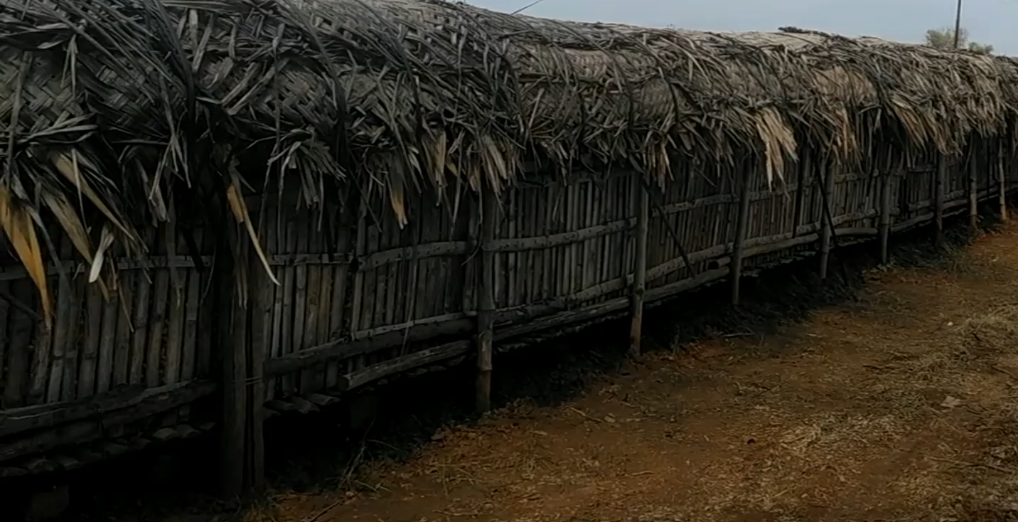
Who's done what beforehand?
Many hobbyists, educators, and even some professional designers have built prototypes for temperature controlling devices and storage monitor devices.
Online Videos and Documentation Links
S. No. | Resource Link | Type |
---|---|---|
1 | YouTube Video Tutorial | Video |
2 | YouTube Project Demo | Video |
3 | Temperature & Humidity Monitoring using NodeMCU | Tutorial |
4 | ESP8266 Temperature Monitoring - Instructables | Guide |
5 | IoT Temperature System - Medium | Article |
Commercially available products
1) Crodeon's Reporter
Crodeon's Reporter is a plug-and-play sensor module designed for remote monitoring of agricultural storage conditions. It measures temperature and humidity inside onion piles and integrates with a cloud dashboard accessible via smartphones or computers.
Learn More: https://www.crodeon.com/
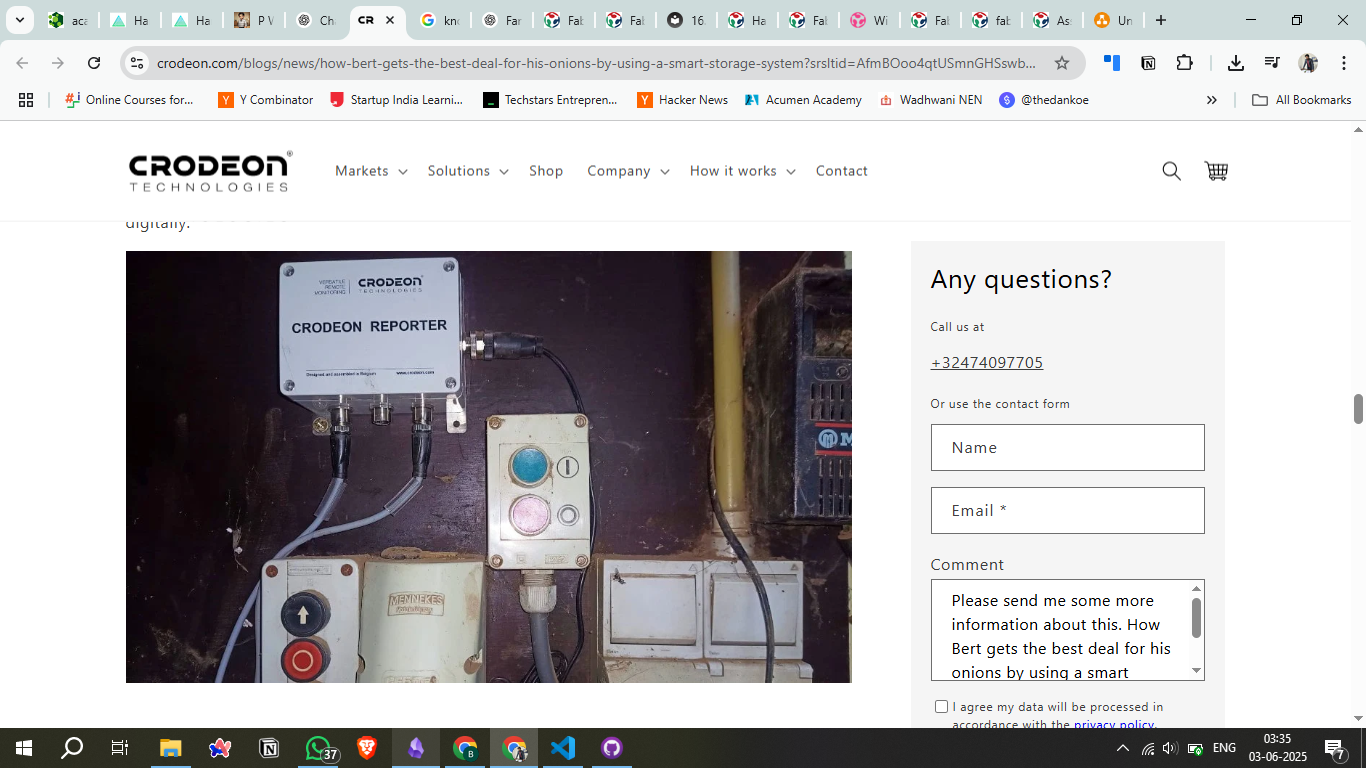
2) IVI's Imperium Control Panel
IVI's Imperium control panel allows precise control over airflow, humidity, and other storage parameters. It includes an app for off-site monitoring and control, making it easier to maintain optimal storage conditions.
Learn More: https://ivi-air.com/
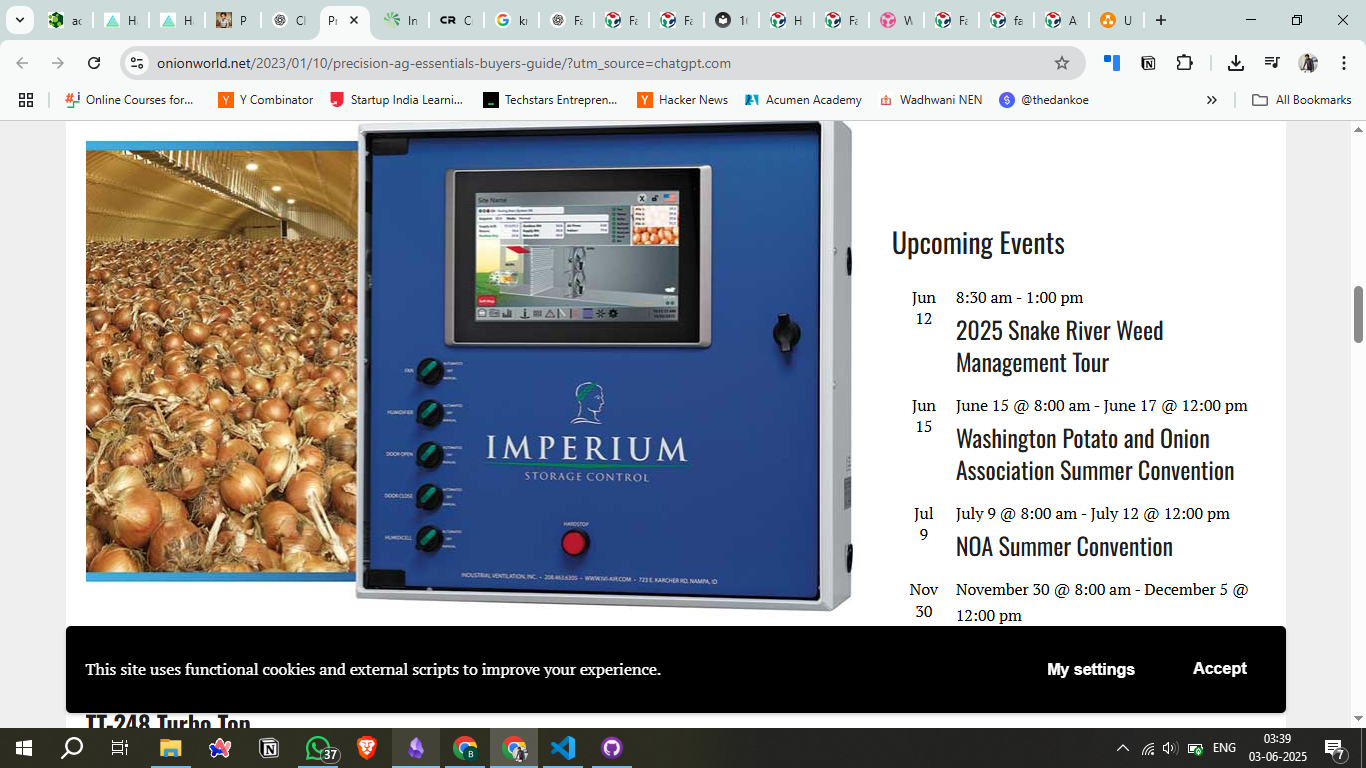
What source will you use?
As mentioned above my source of inspiration is from instructables and other online resources from the internet.
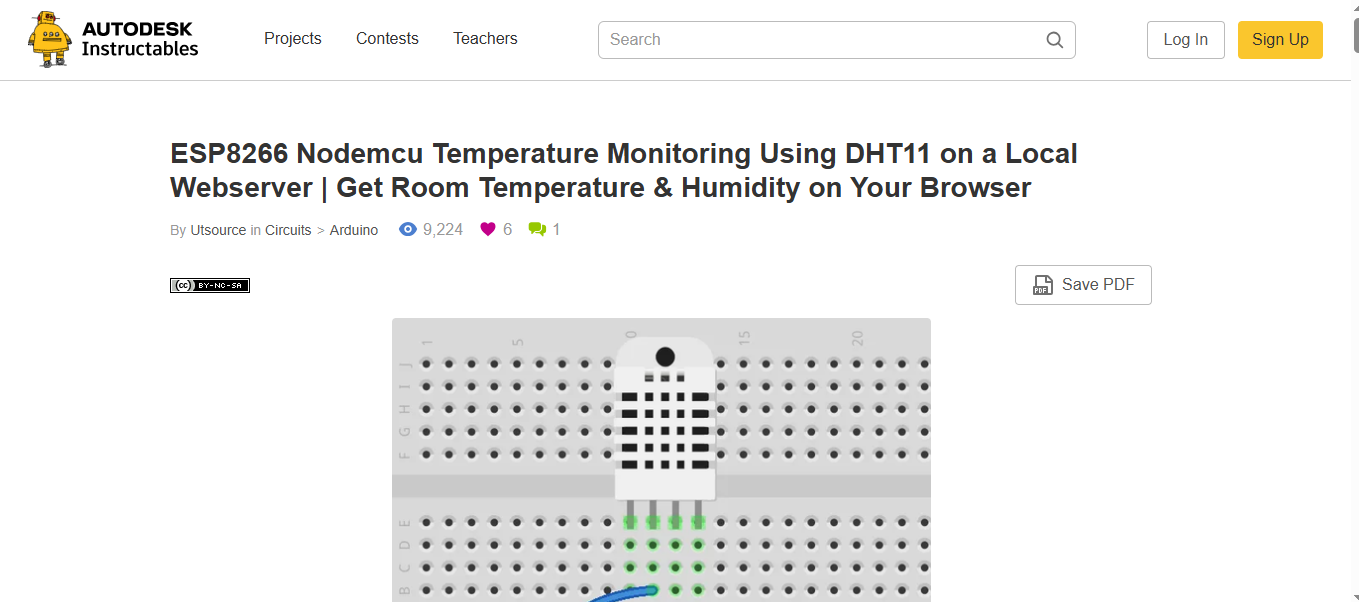
What will you design?
In this product development simple techniques are used in such a way any body can download and recreate the onion temperature monitoring device using digital fabrication techniques. The system is divided into three sub-systems:
- Temperature sensor
- Relay control
- Mobile control
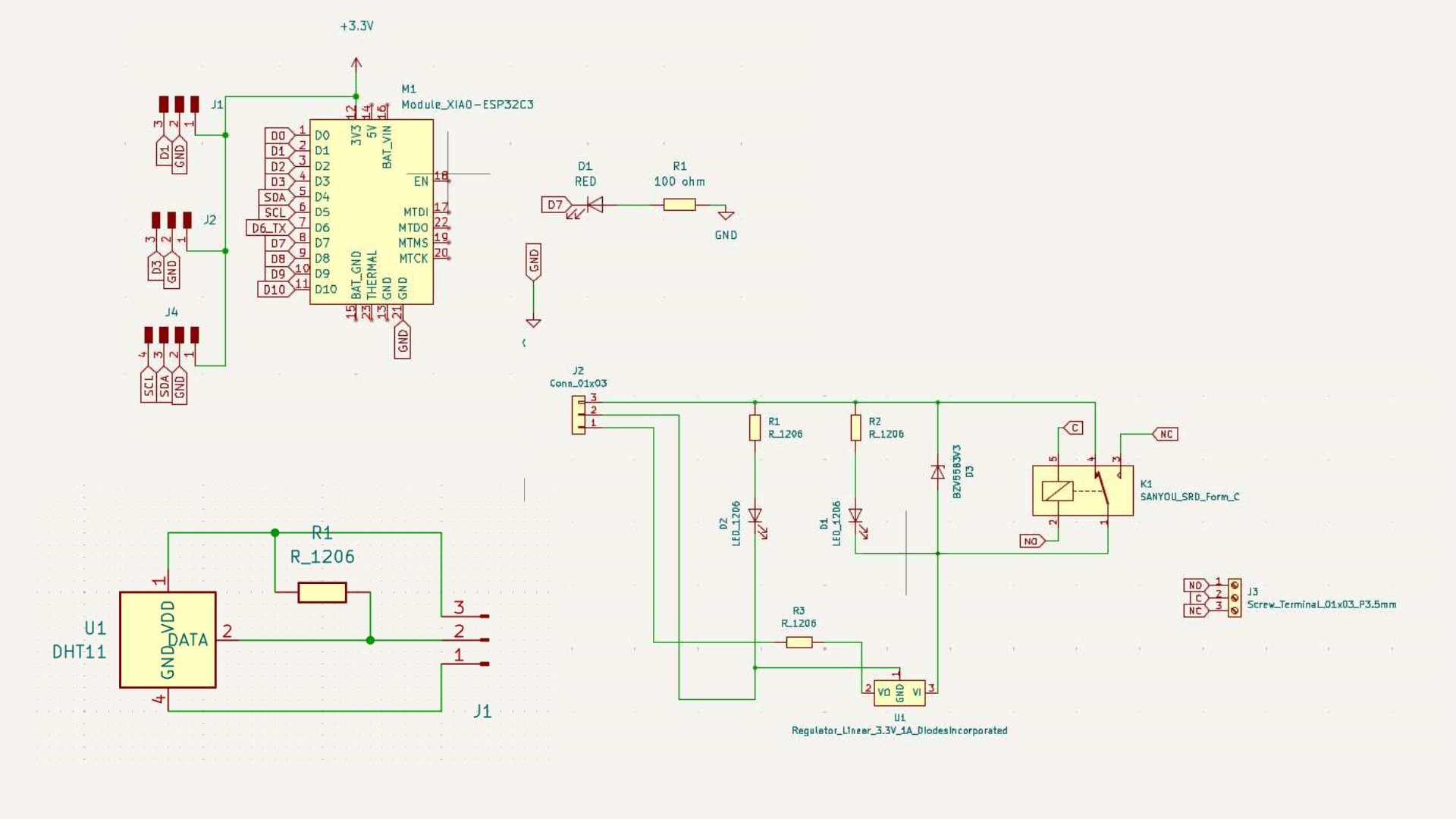
What materials and components will be used?
Component | Quantity | Purpose |
---|---|---|
ESP8266 or XIAO ESP32 | 1 | Main controller |
DHT11/DHT22 | 1 | Temperature & humidity sensing |
Relay Module | 1 | To control heater/fan |
Battery (18650 or LiPo) | 1 | Portable power supply |
PCB/Perfboard | 1 | Circuit prototyping |
Enclosure (Acrylic/PLA) | 1 | Housing |
Where will it come from?
In this design, we tried to be very minimalistic so that the model can be recreated anywhere with common, locally available materials. Major components are available from the lab inventory and local electronics stores.
How much will they cost?
Item | Estimated Cost (INR) |
---|---|
ESP32/NodeMCU/XIAO w/ Wi‑Fi | 500 |
DHT22 Temp & Humidity Sensor | 150 |
5 V Relay Module | 100 |
18650 Li-Ion + holder | 300 |
5 V Regulator (LM2596) | 80 |
PCB board (epoxy) | 100 |
PLA filament (≈100 g) | 250 |
Wires, connectors, solder | 150 |
Total | ~1630 INR |
What processes will be used?
- 2D Design (CAD): For the enclosure panels using Solidworks
- 3D Design (CAD): For 3D-printed parts and assembly visualization using Solidworks
- 3D Printing (FDM): For manufacturing custom plastic parts
- CNC Milling: For creating the custom PCB
- Electronics Soldering: For assembling the PCB and connecting components
- Assembly: Mechanical assembly of the enclosure, fan, and electronics
- Programming (Embedded C/Arduino): For controlling the microcontroller, fan, and reading sensors
- Testing and Iteration: Repeated testing of airflow, visualization, and any measurement systems, followed by design adjustments
What parts and systems will be made?
- Parts are 3D printed using FDM 3D printer - Flash Forge and Creality
- PCB is milled using the Wegster PCB milling machine
What questions need to be answered?
- What is the optimal range of temperature and humidity for the application (e.g., poultry)?
- How to minimize power consumption for battery-powered operation?
- How to make the system robust against dust/moisture in rural settings?
- What level of precision is required for temperature/humidity?
- Can this system scale or be modular for future upgrades?
What tasks have been completed?
- Initial research: Explored existing wind tunnel designs, fan types, and airflow visualization methods
- Conceptual design sketching: Brainstormed various layouts and component placements
- Gathering of initial requirements: Defined the scale of cars, desired functionalities, and budget constraints
- Initial material sourcing ideas: Identified potential suppliers for key components
What questions need to be resolved?
- Optimal thresholds: What is the ideal temperature range for poultry at different growth stages in Indian winter conditions?
- Power consumption: How can I optimize the system to work efficiently on battery power for extended periods (e.g., overnight)?
- Heater safety: Is the heating pad safe for continuous use in enclosed areas? How can I ensure it doesn't overheat?
- Durability: Can the enclosure and components withstand harsh rural environments (dust, moisture, animal proximity)?
- Expandability: Can the current design support multiple sensor nodes or remote wireless communication in future versions?
- Cost trade-offs: What is the best balance between affordability and durability for mass deployment?
What will happen when?
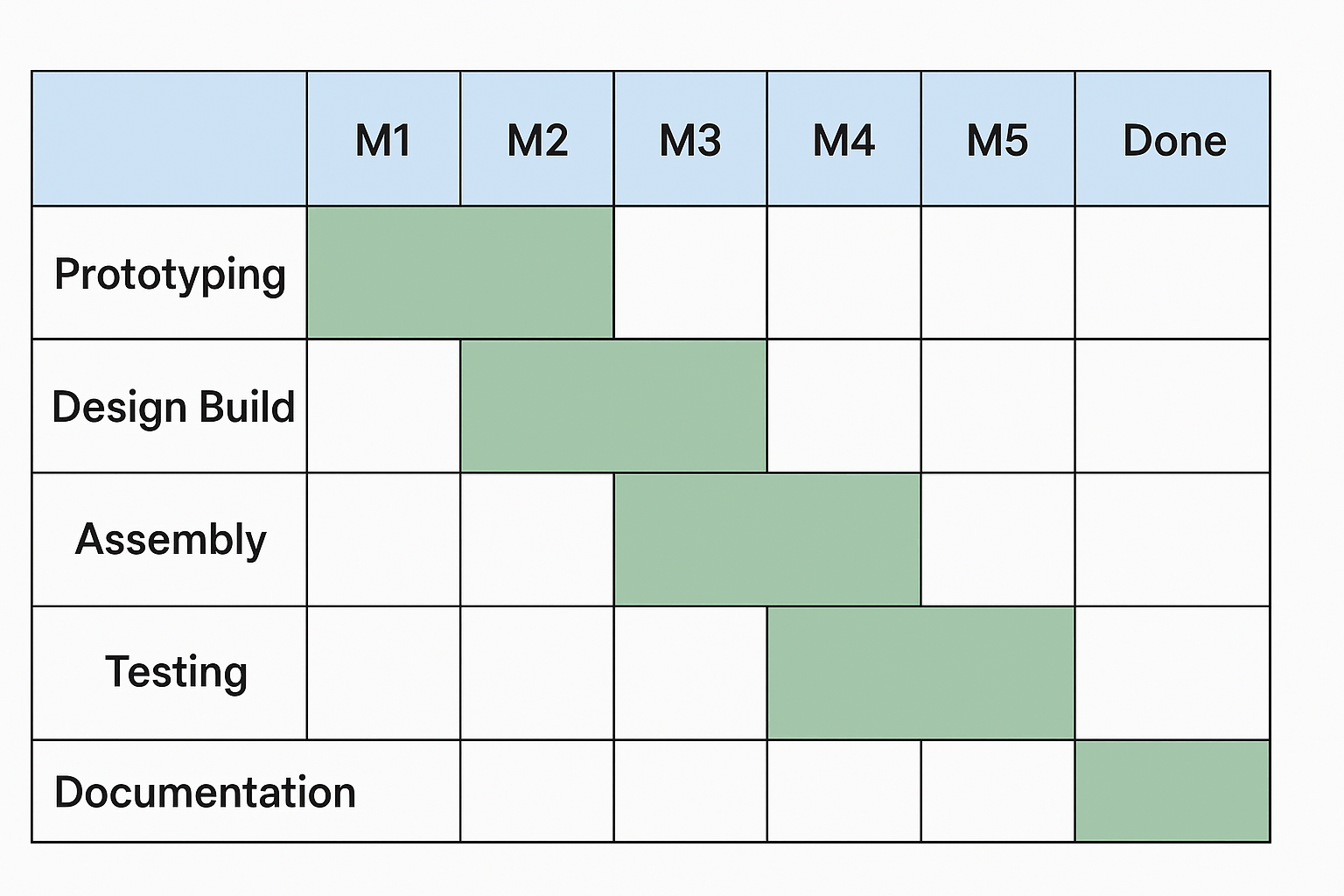
What have you learned?
- I learned how to combine electronics, design, and fabrication into a functional embedded system.
- Understood the importance of designing for real-world environments, especially in rural applications.
- Gained experience with low-power microcontrollers, sensor integration, and actuator control using relays.
- Learned how to apply iterative development—testing small modules before integrating the full system.
- Realized the need for user-friendly, maintainable solutions when designing for non-technical users.
- Developed skills in project planning, documentation, and troubleshooting at the system level.
Prototype
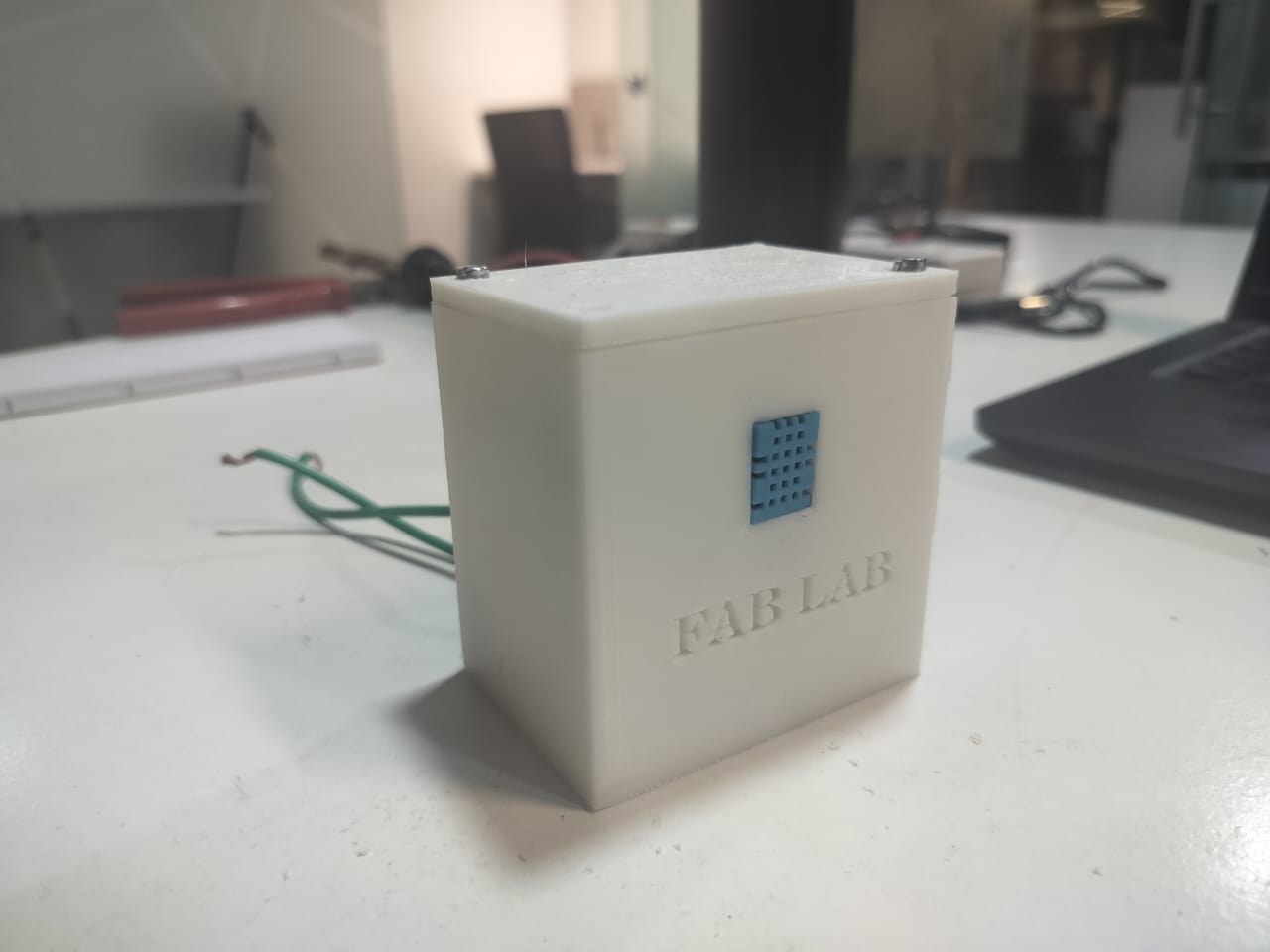
Table of Contents
- Assignment
- What will it do?
- Who's done what beforehand?
- Commercially Available Products
- What source will you use?
- What will you design?
- Materials & Components
- Where will it come from?
- Cost Breakdown
- Processes Used
- Parts & Systems Made
- Questions to Answer
- Completed Tasks
- Questions to Resolve
- What will happen when?
- What have you learned?
- Prototype