Week 3: Computer-Controlled Cutting
Group Assignment (link):
do your lab's safety training characterize your lasercutter's focus, power, speed, rate, kerf, joint clearance and types
Individual Assignment:
1) cut something on the vinylcutter 2) design, lasercut, and document a parametric construction kit, accounting for the lasercutter kerf, which can be assembled in multiple ways
Triangular-based Platonic Solids:
In the Kochi lab is a parametric construction kit for a dodecahedron, the best of all the platonic solids.
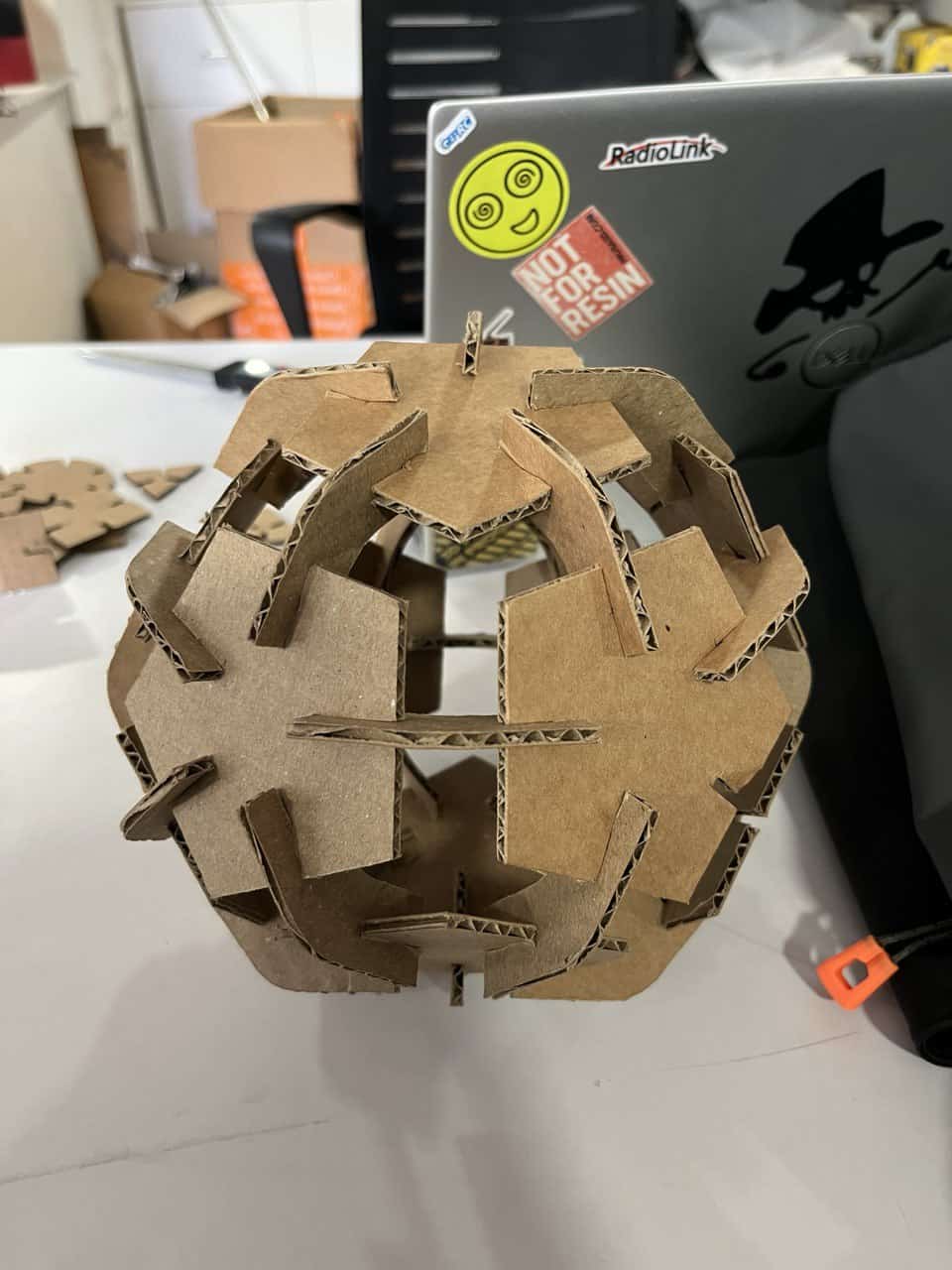
However, 3 of the 5 platonic solids are made from equilateral triangles, so obviously a good option will be to make a construction kit for the triangular faced platonic solids.
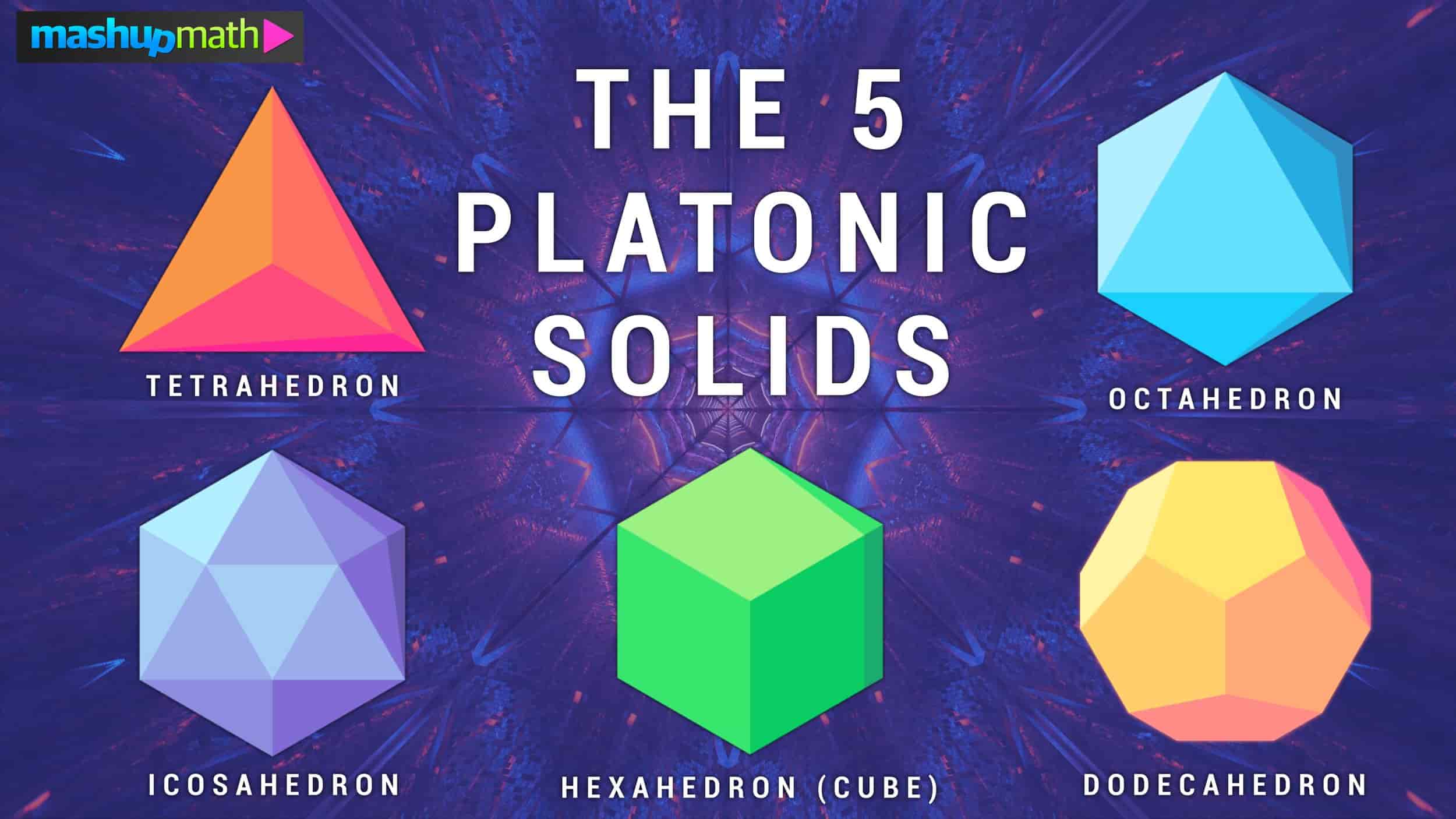
KERF
Kerf is a new and important concept - it refers to the laser beam width. Generally speaking it is the width of material that is destroyed by the cutting instrument. When we are cutting something with the laser, it is burning material. So if we cut out a square from a shape, and try to fit it back in, it will not fit tightly. Of course! because the material around the square has been burned. Here is the square which I cut with instructor Saheen:
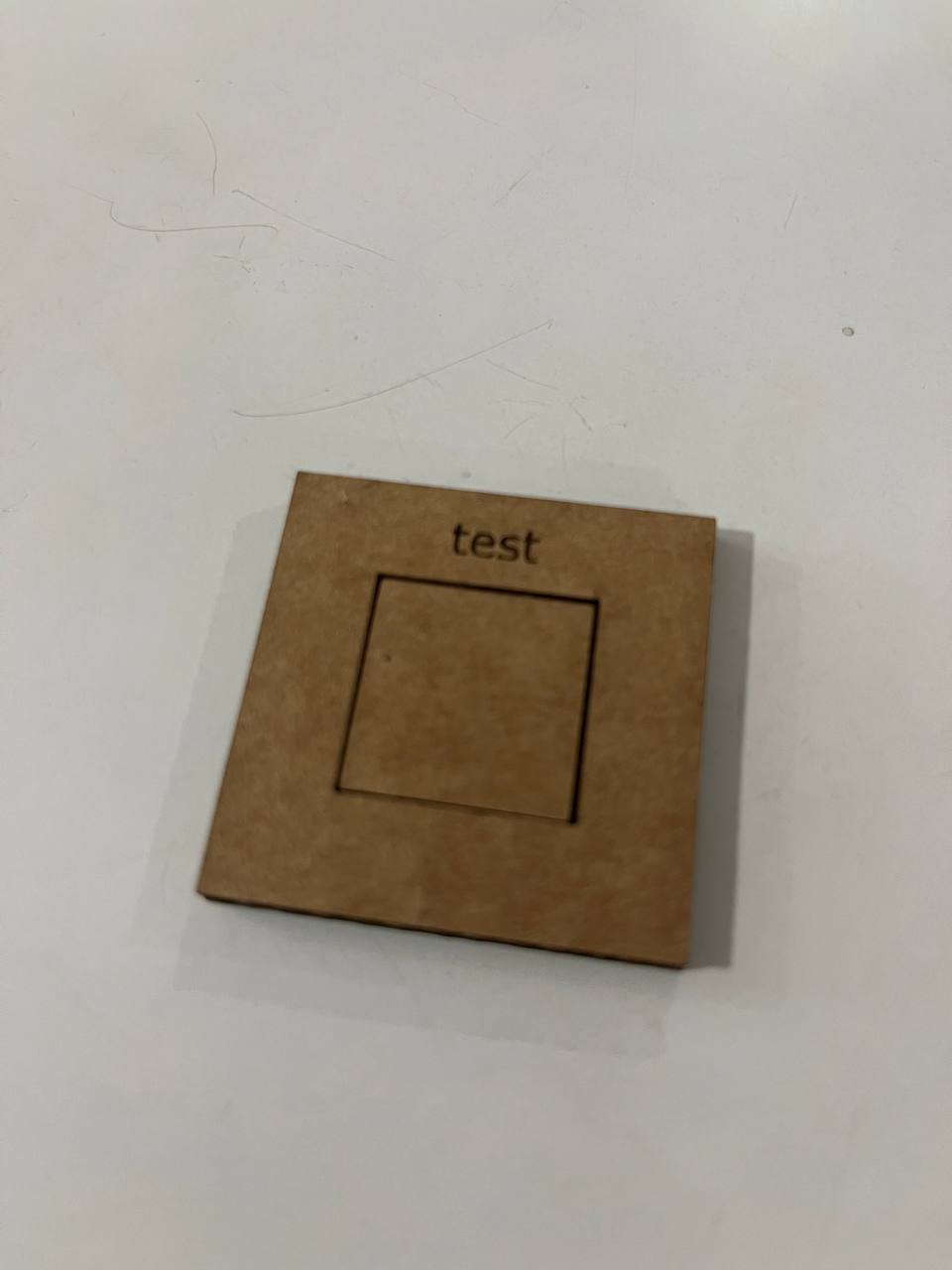
Using calipers, measure both the inside and the outside of the square.
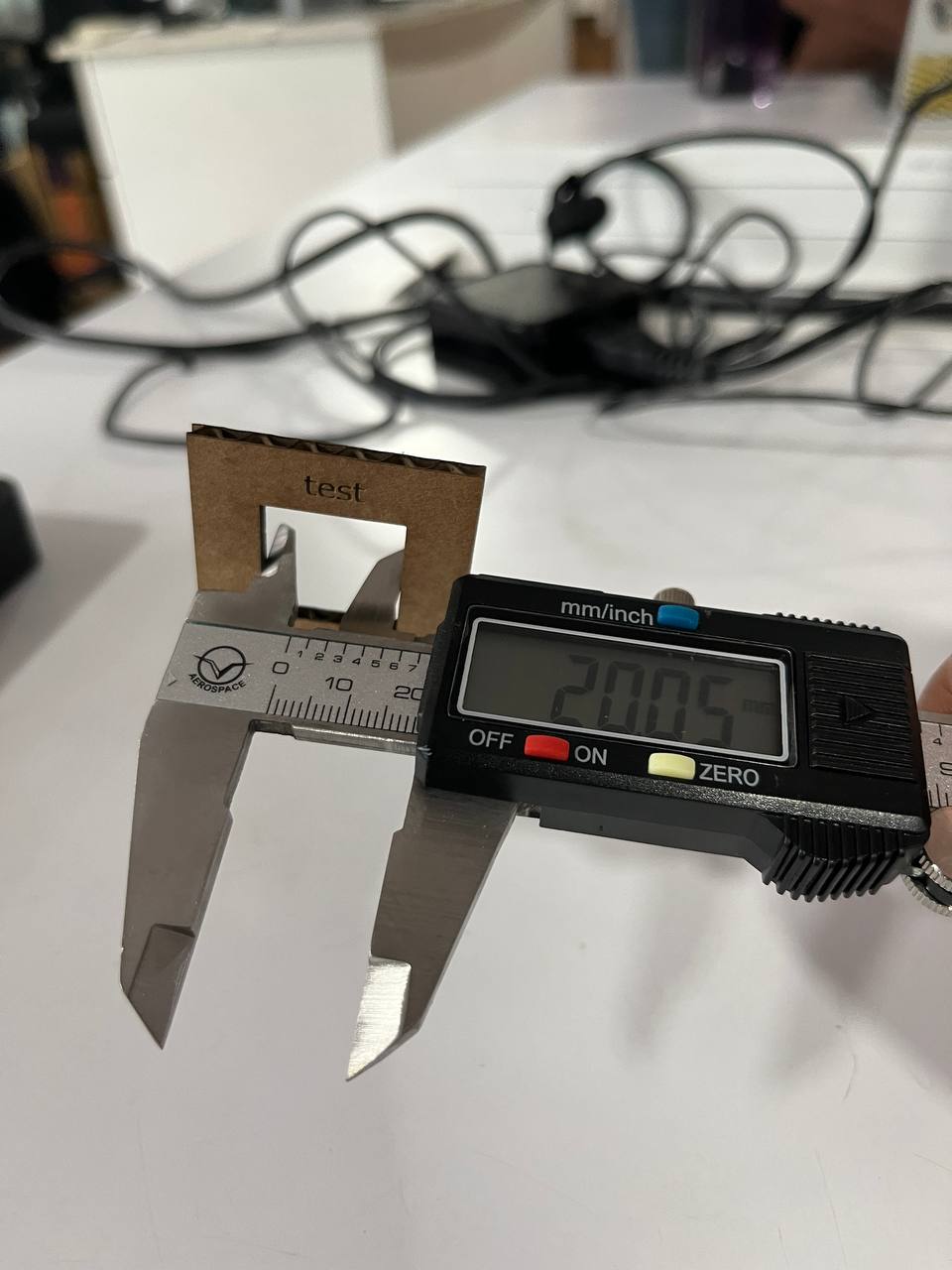
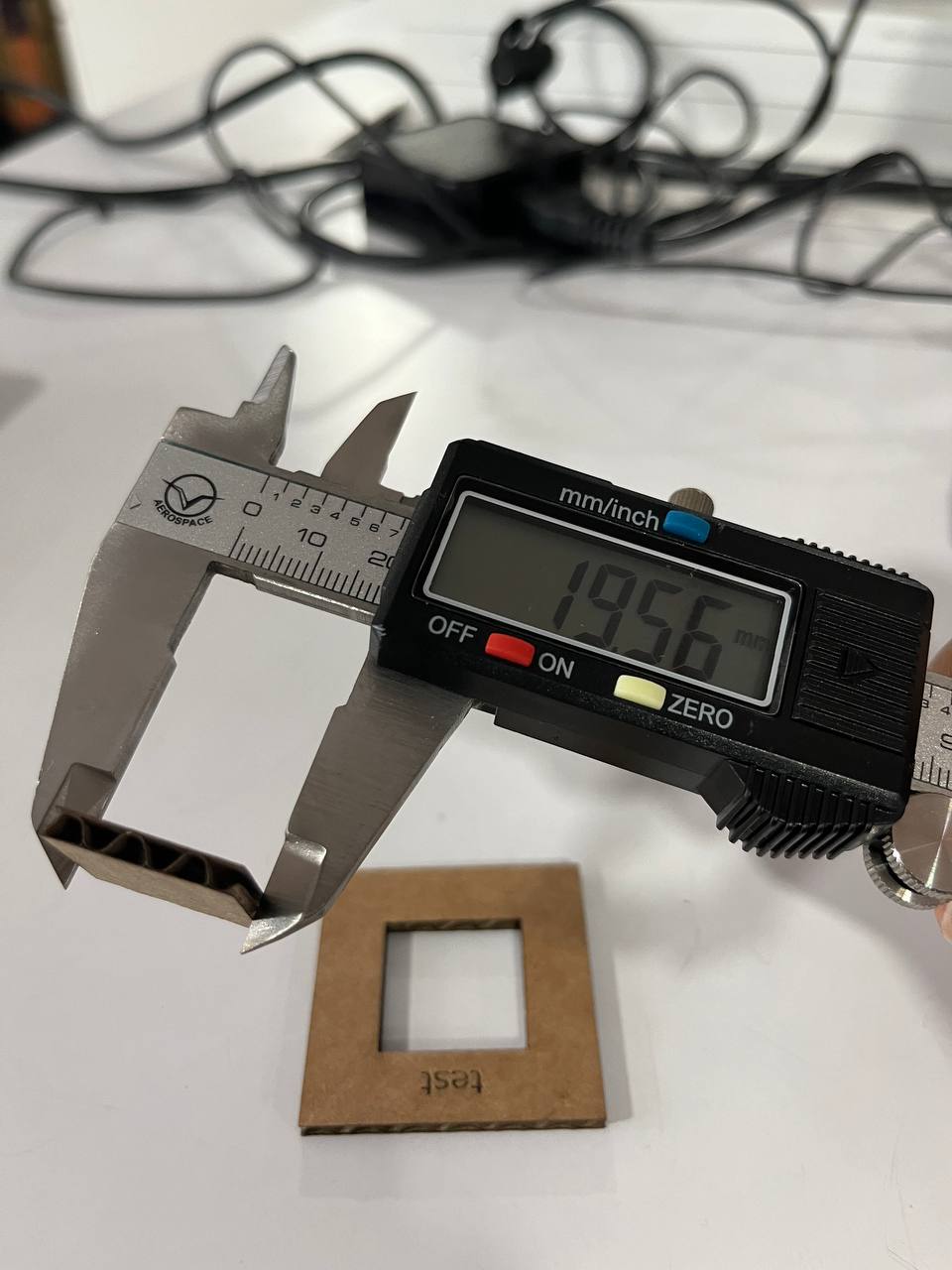
In our case the kerf is (20.05-19.56)/2=0.49/2=0.245. Here we divide by 2 to find the kerf since there are 2 cuts. Hence when we print we will offset by kerf/2=0.12mm. Then the square will fit securely.
Designing in Fusion 360
After using FreeCAD and enjoying it, I was peer-pressured into using Fusion 360. Sad. So the first part of making the parametric kit was in Fusion 360. It involved:
- Sketching the entire triangle and connectors with constraints
- Extruding and adding the chamfer
- Added the parameters
- Projecting the sketch onto a face, and exporting the sketch as a .dxf file
Creating a parametric design is very important. Here we have the designs for triangle and connectors:
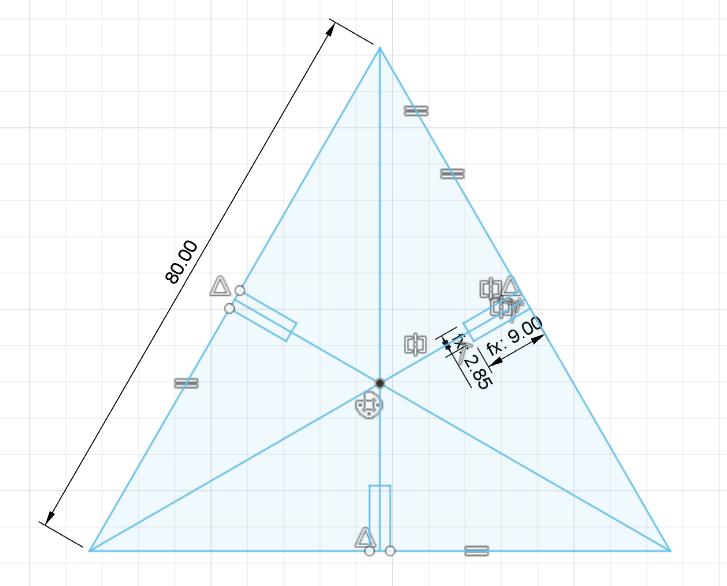
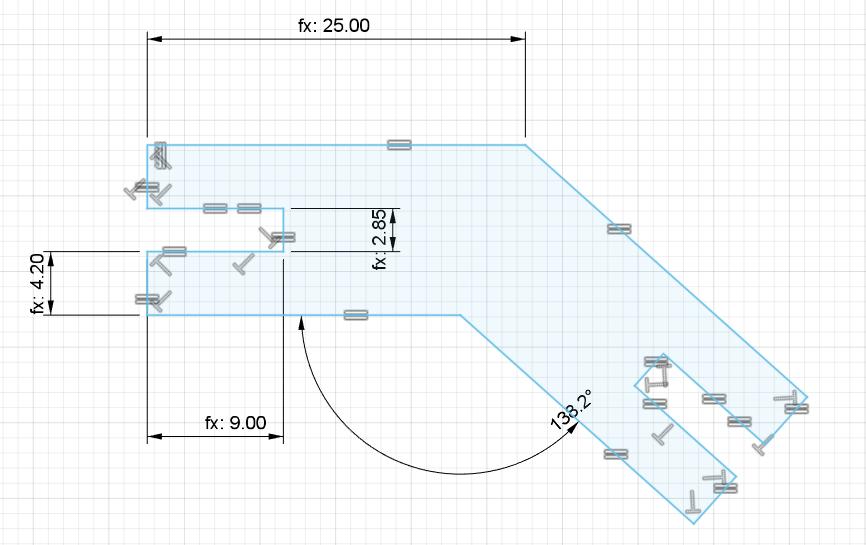
For context, the values for material thickness, kerf and compression were found by testing on the cardbaord using caliper.
The following parameters were used: (parameters can be found from the modify section of sketch menu.)
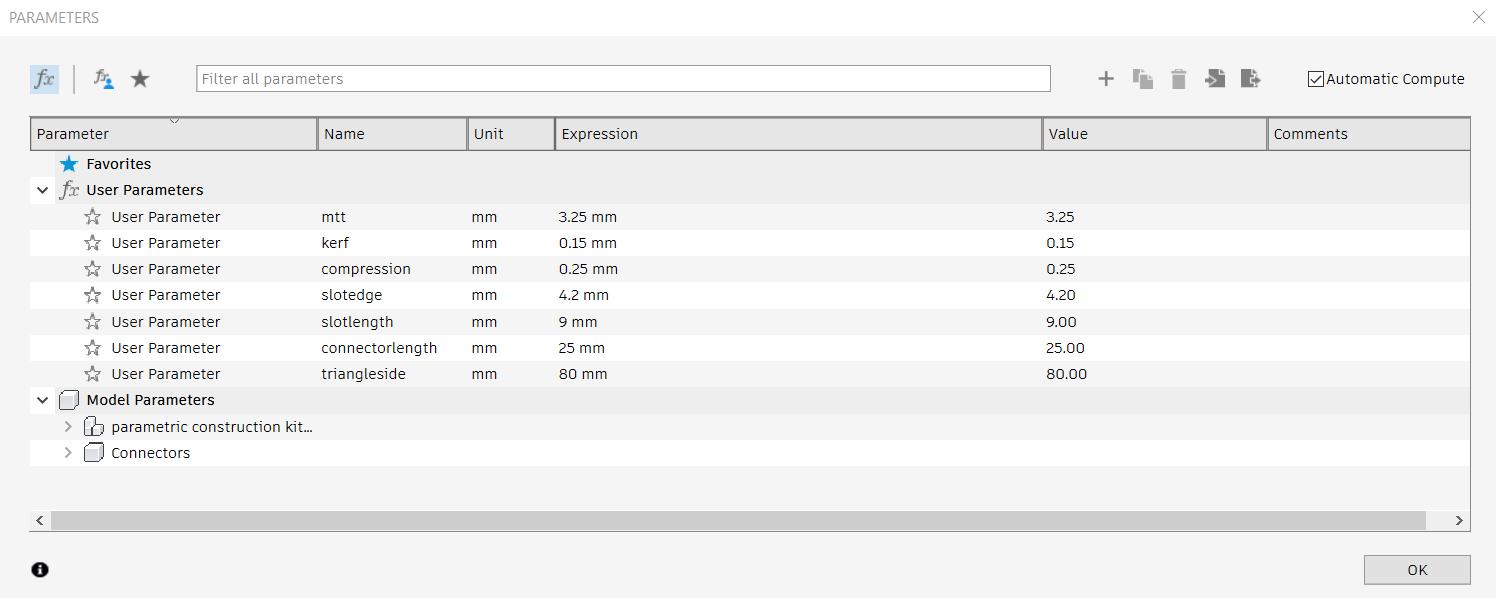
Cutting with Trotec
In the lab there is a nice laser-cutter. It is called Trotec and so this is what we will use. On the left is the exhaust system and on the right is the computer which is connected and has the appropriate software for cutting.

The power and controls are there. Important is to calibrate each time by pressing the two buttons on the right. But the laser cannot be at the edge to calibrate, bring it towards the middle somewhere.
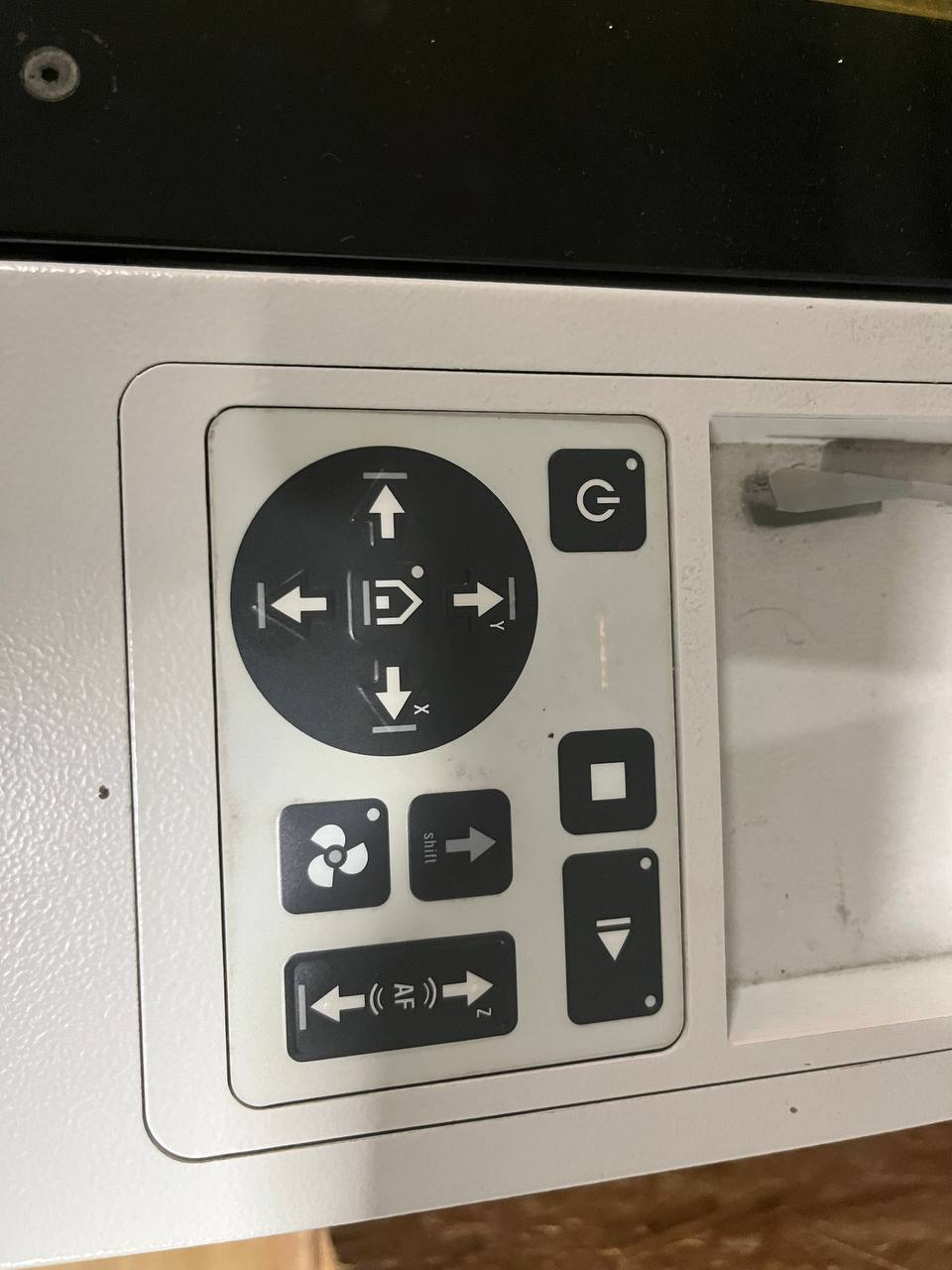
On the adjacent computer is software called "TROTEC Job Control", and is used to adjust settings like power and speed. These are recommended settings of power at 90 and speed at about 1.3 - for cardboard. Of course the power and speed will differ depending on the material used.
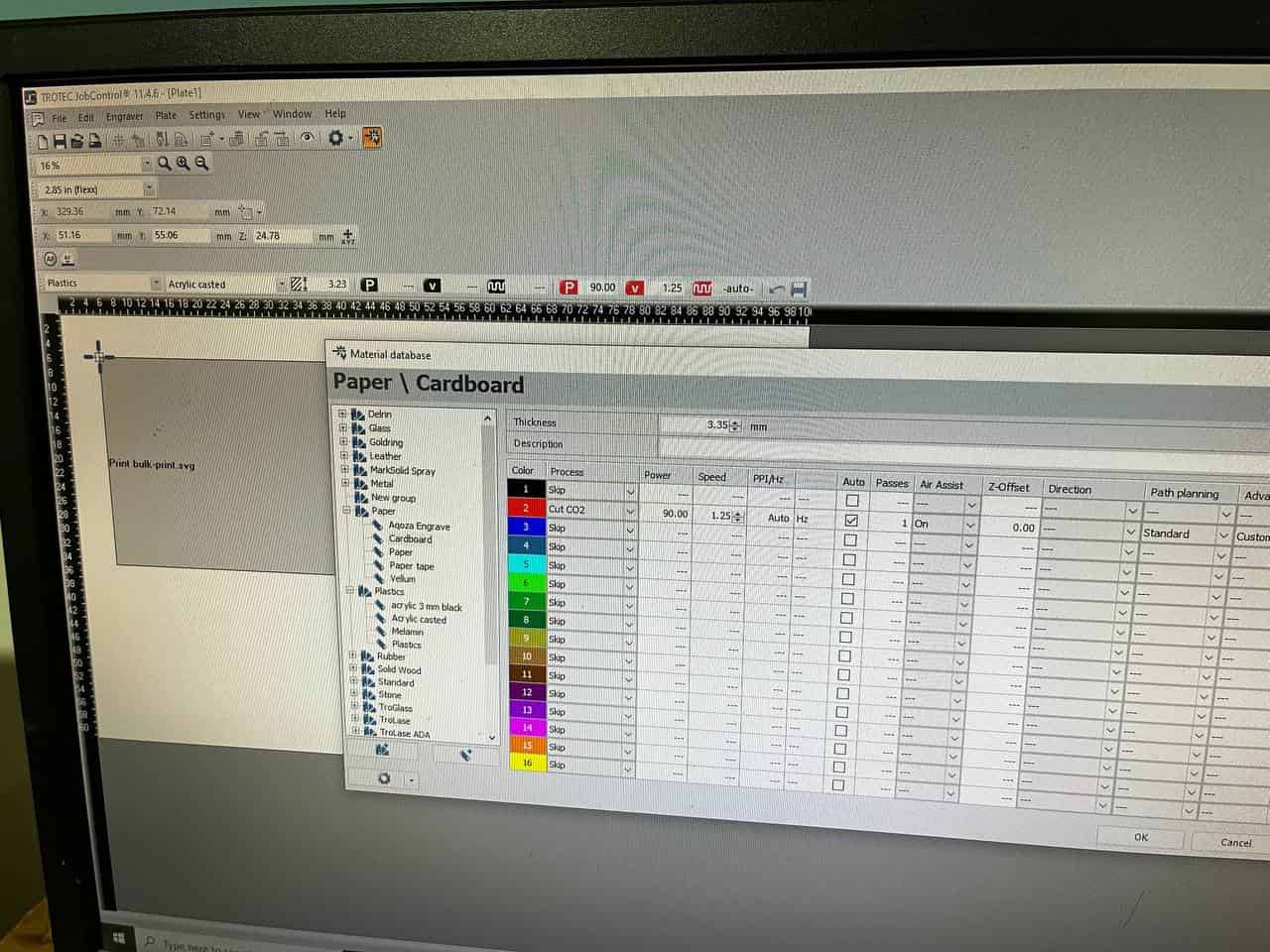
When we put the cardboard in, we must calibrate to the edges and hold it down with tape.
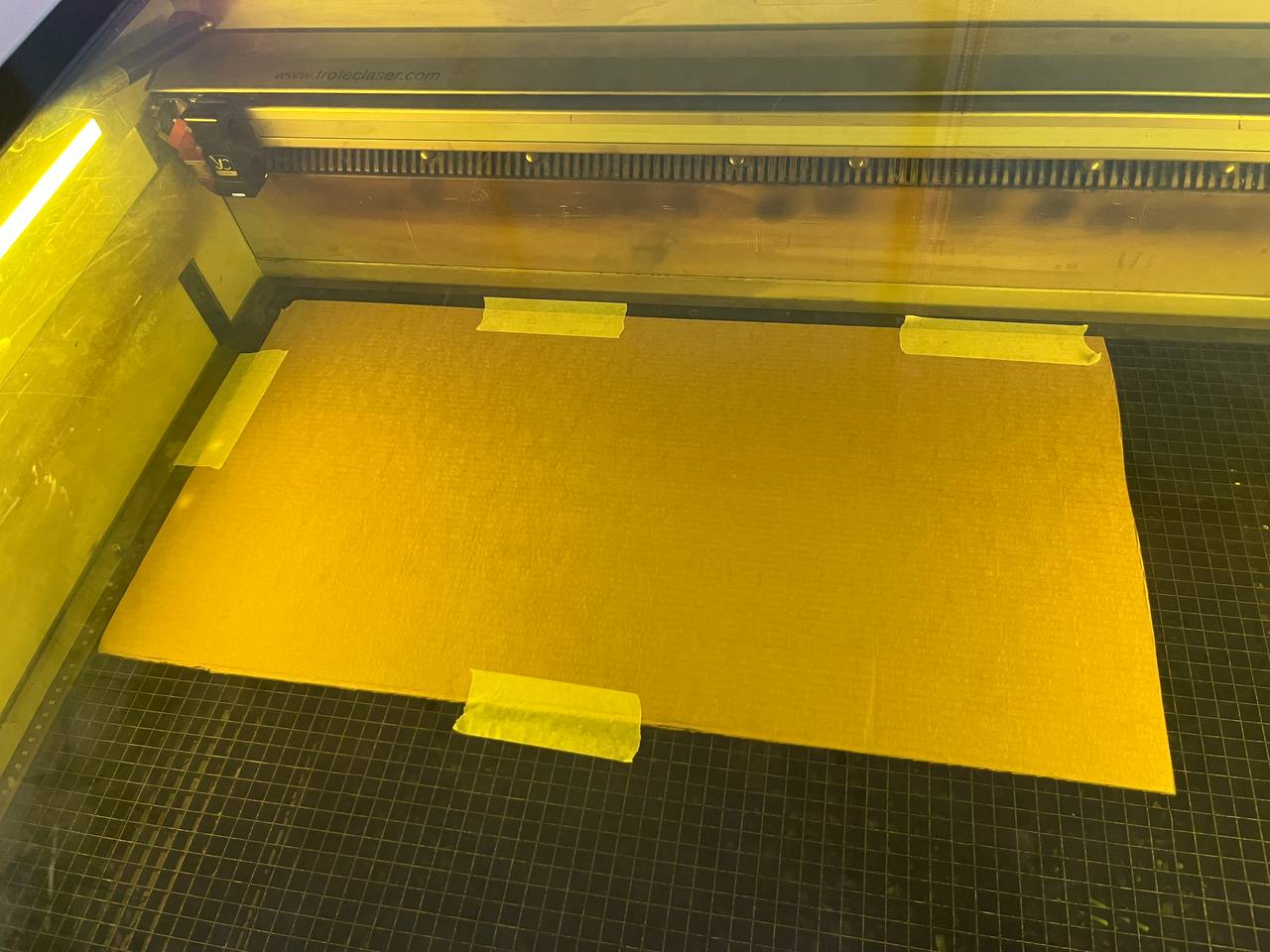
To start cutting our project we simply go to "print" from within Inkscape. Then in TROTEC we place the file onto the "cutting board". It automatically shows the size. Then click "ready".
First we wanted to cut a few of the objects as a test.
Here's the test file in Inkscape:
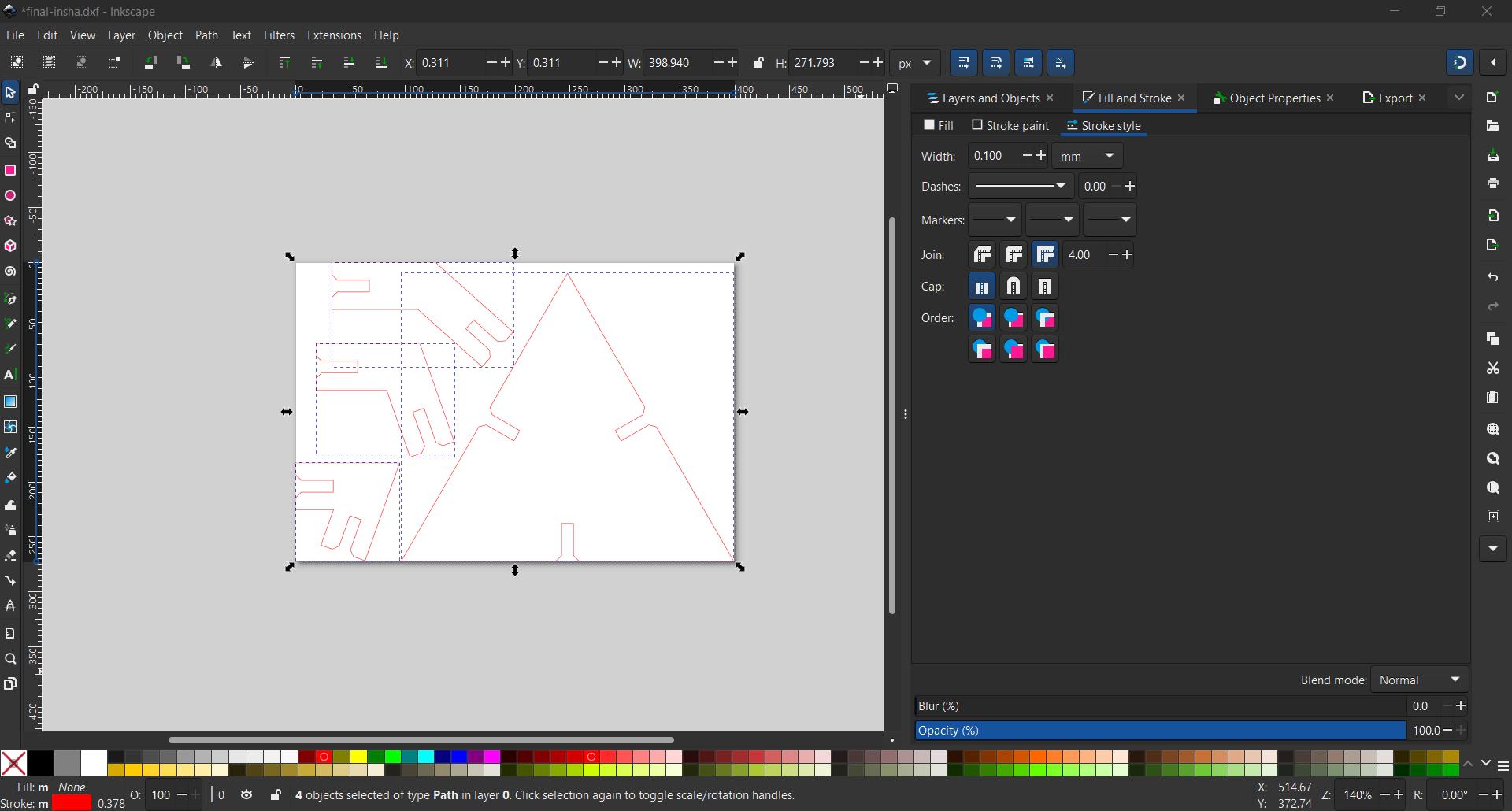
And here we are cutting the test file:
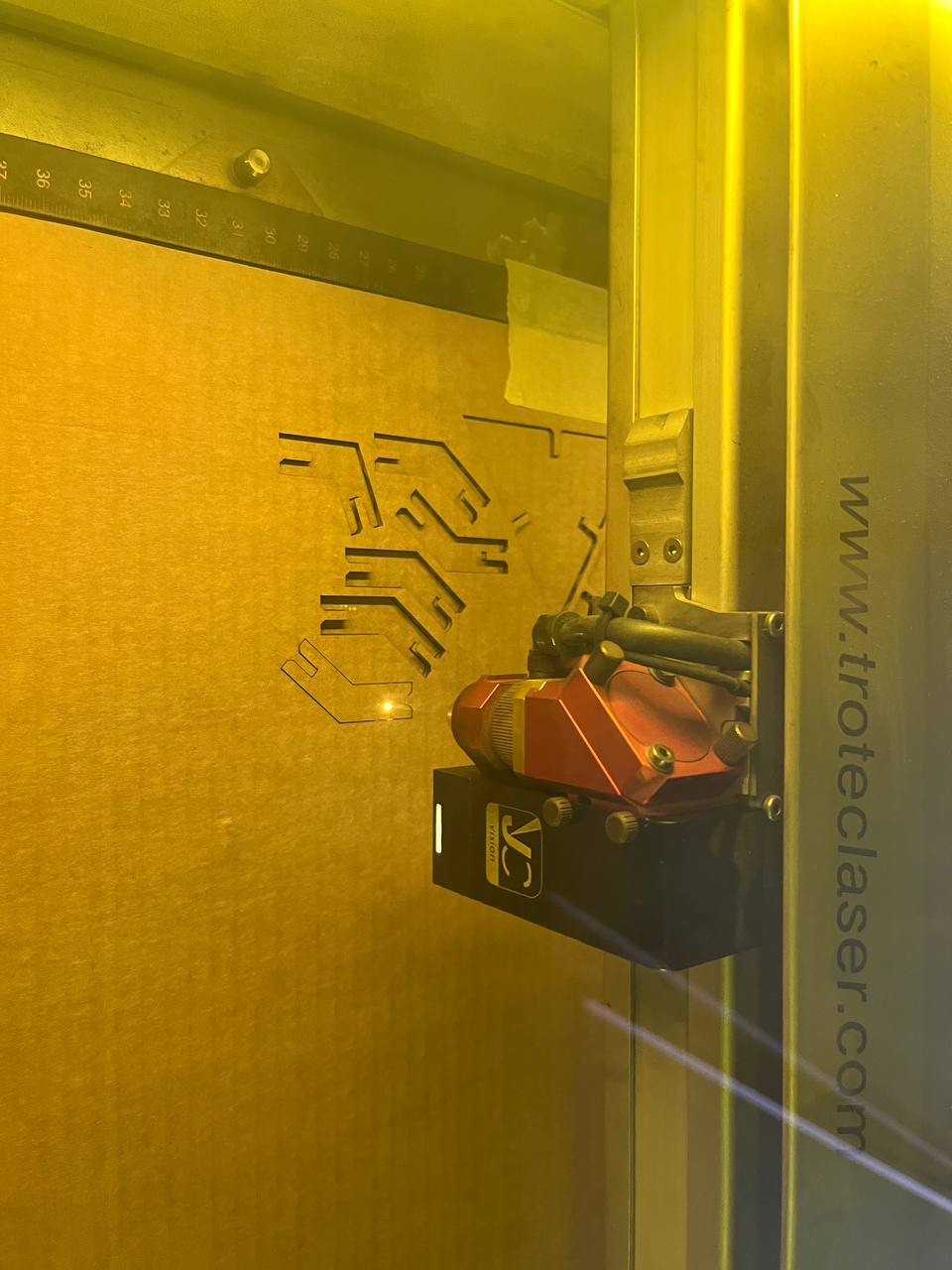
It was good, but needed to be adjusted for both the kerf and cardboard compression. However, it was very helpful to have parameters, and we could quickly change the appropriate values; the changes were automatically implemented both on the triangle and the connectors.
Nesting/Arranging
The final step is to print the whole kit! For this we need to make copies and arrange them: Fortunately there is an arrange function in Fusion 360. This is known as "nesting".
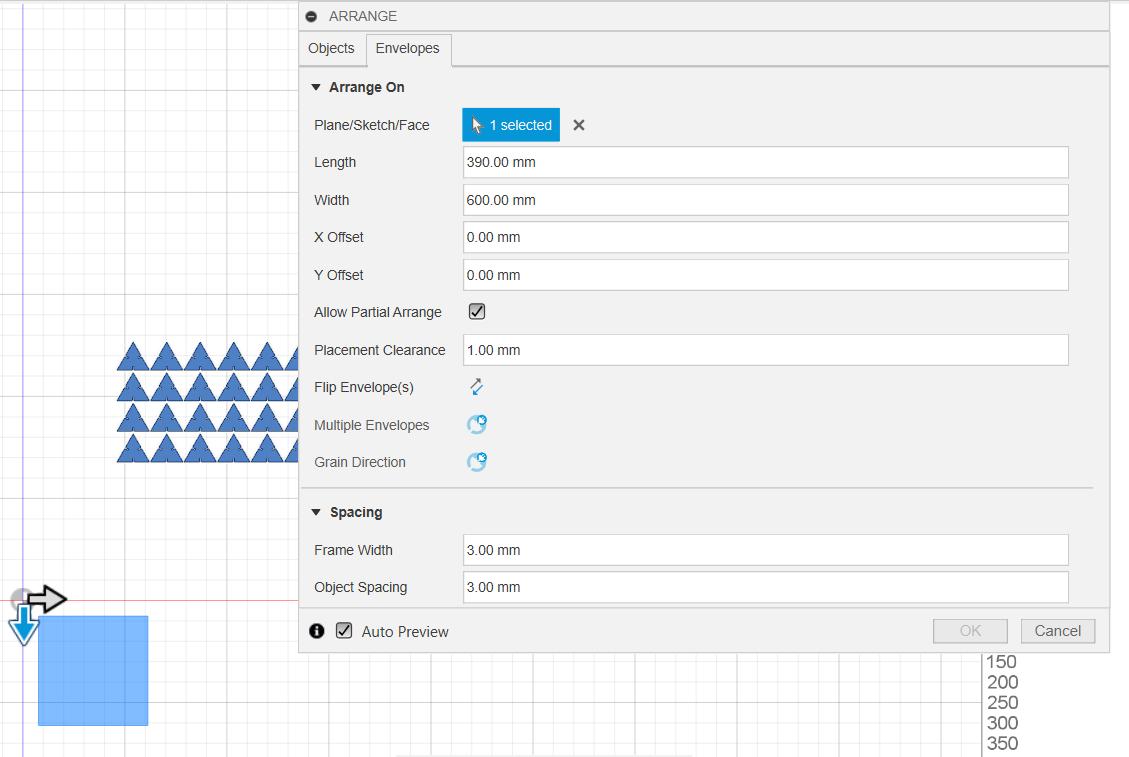
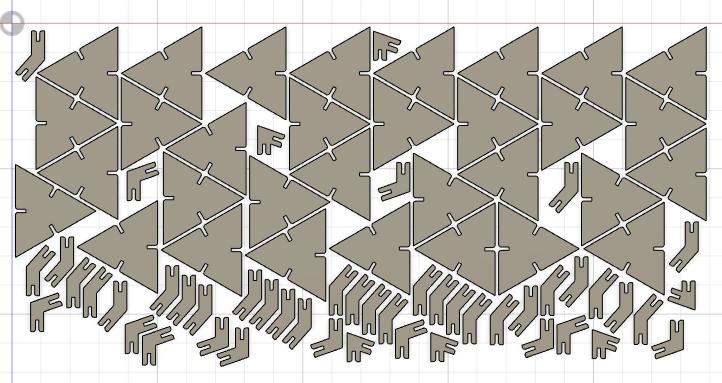
From Fusion we should then prepare the whole construction kit in Inkscape to send to the laser-cutter
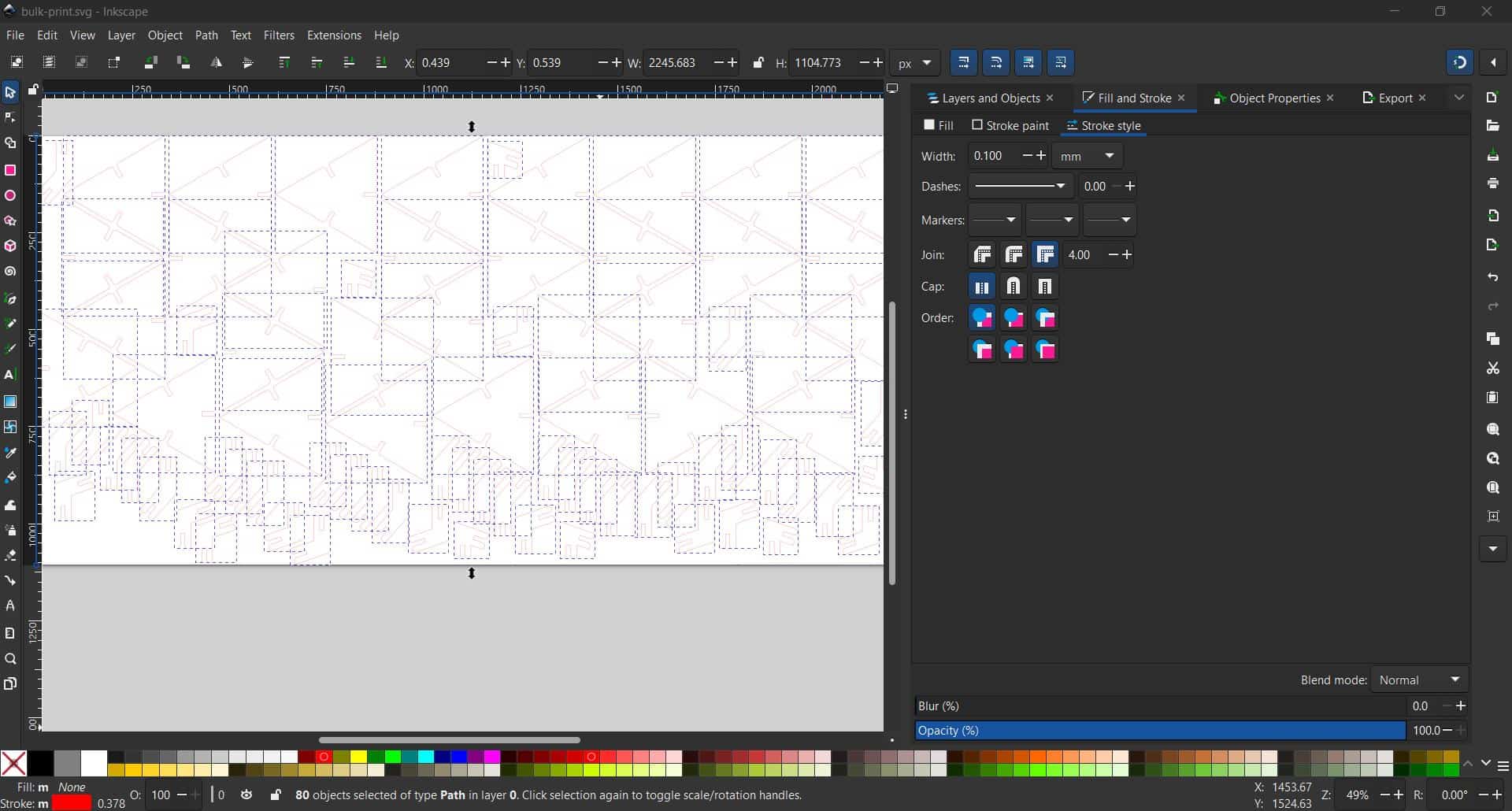
Preparing the file using Inkscape
Here are some additional notes in this regard as the process was new to us. It's an important process to note as we cannot immediately send the file from Fusion to the laser cutter. Here are the steps to take for future reference.
- export the file from Fusion in .dxf format.
- open the .dxf file in Inkscape, fitting the size (shortcut: Ctrl+Shift+R)
- in Inkscape, we set the stroke to red color of thickness 0.1 mm (and remove any fill).
- export the file from inkscape as .svg (shortcut: Ctrl+Shift+E)
- send the file from our computer to the laser cutter terminal using "send-anywhere" or similar
Cutting in Bulk:
Now it's time to print the entire parametric Kit! Here it is nearly done. Just took about 3 minutes:
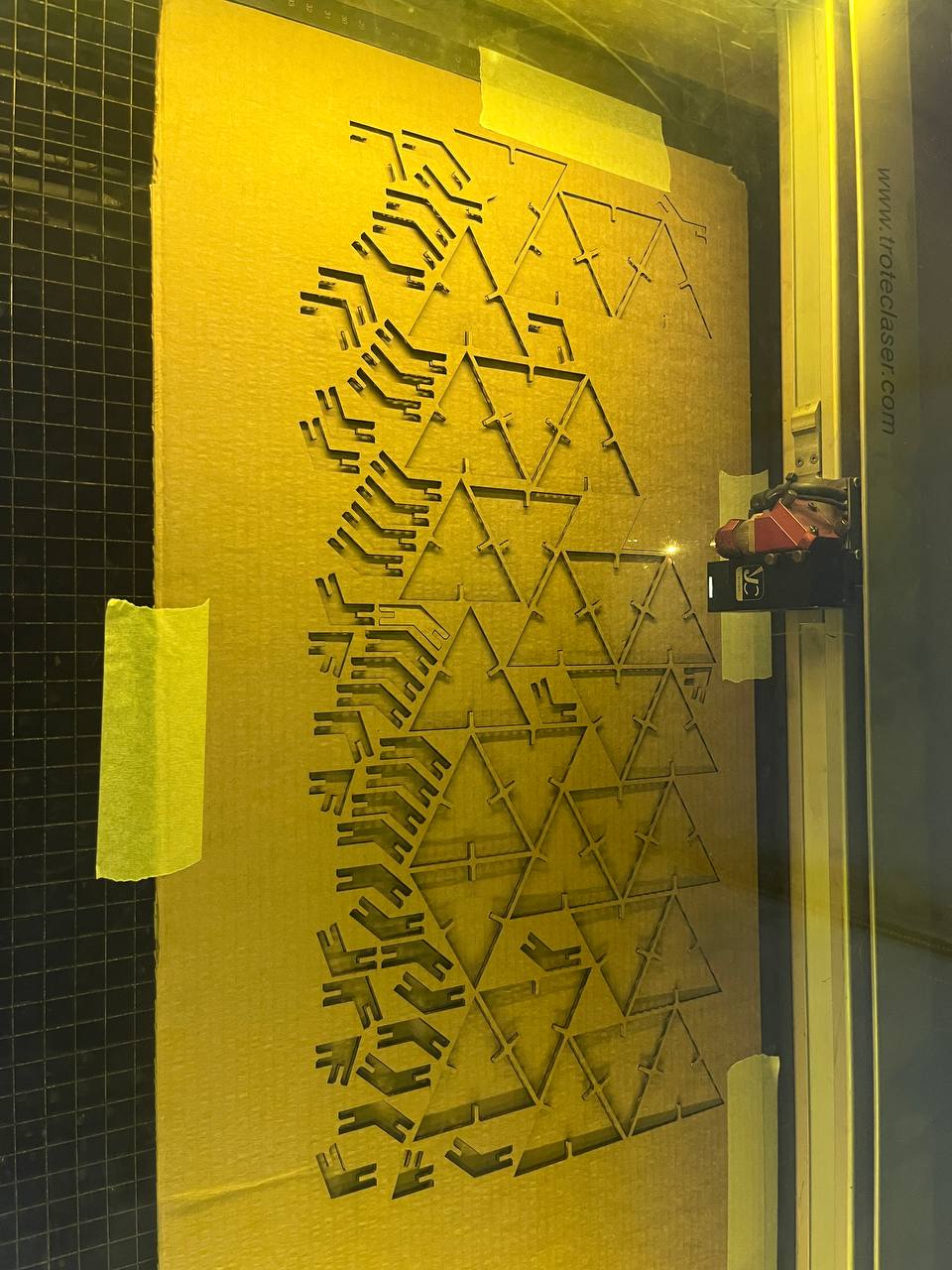
Note that the pieces have been cut cleanly and fallen out (appropriate speed and power settings)
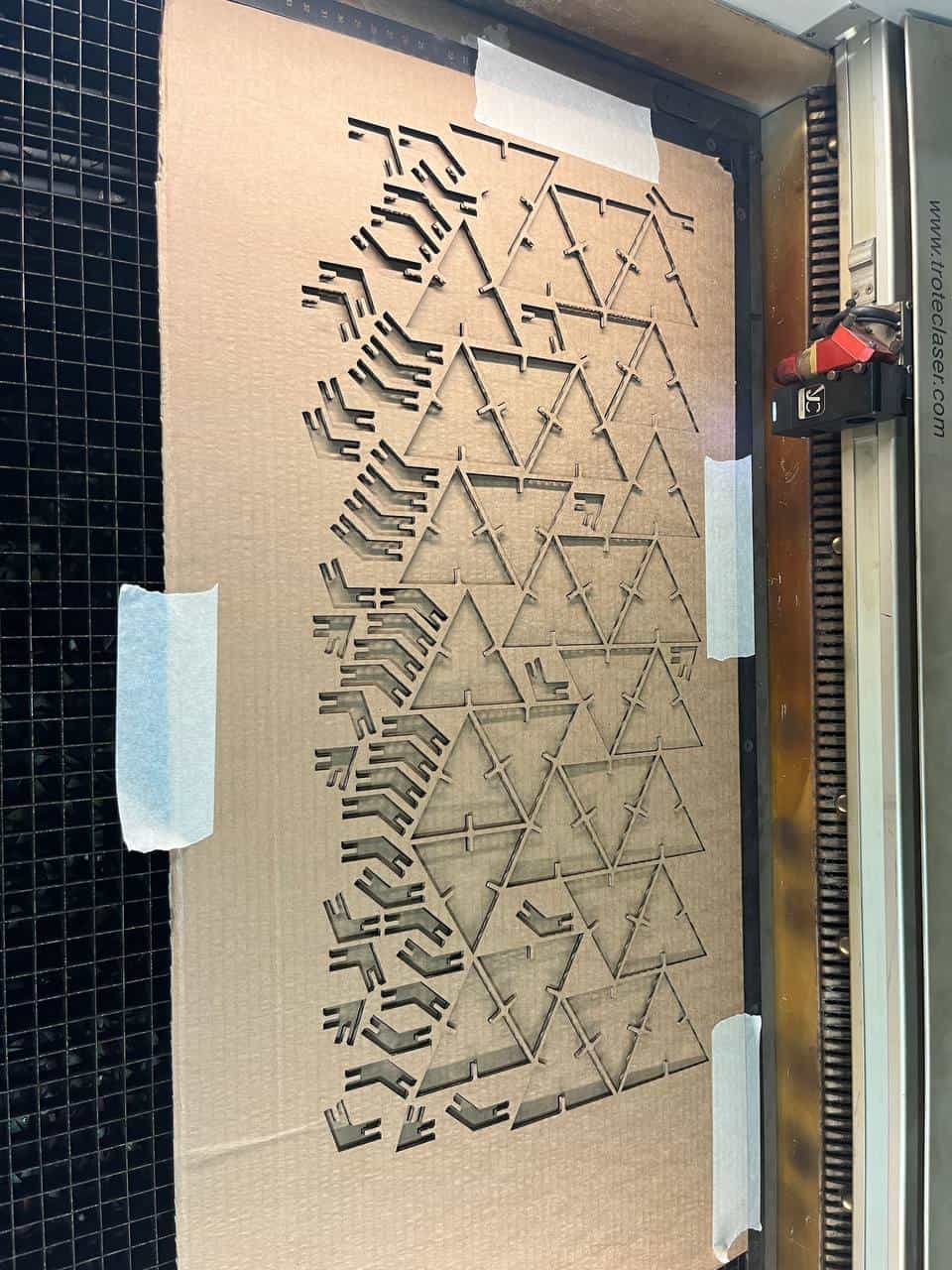
Here is the kit of construction pieces:
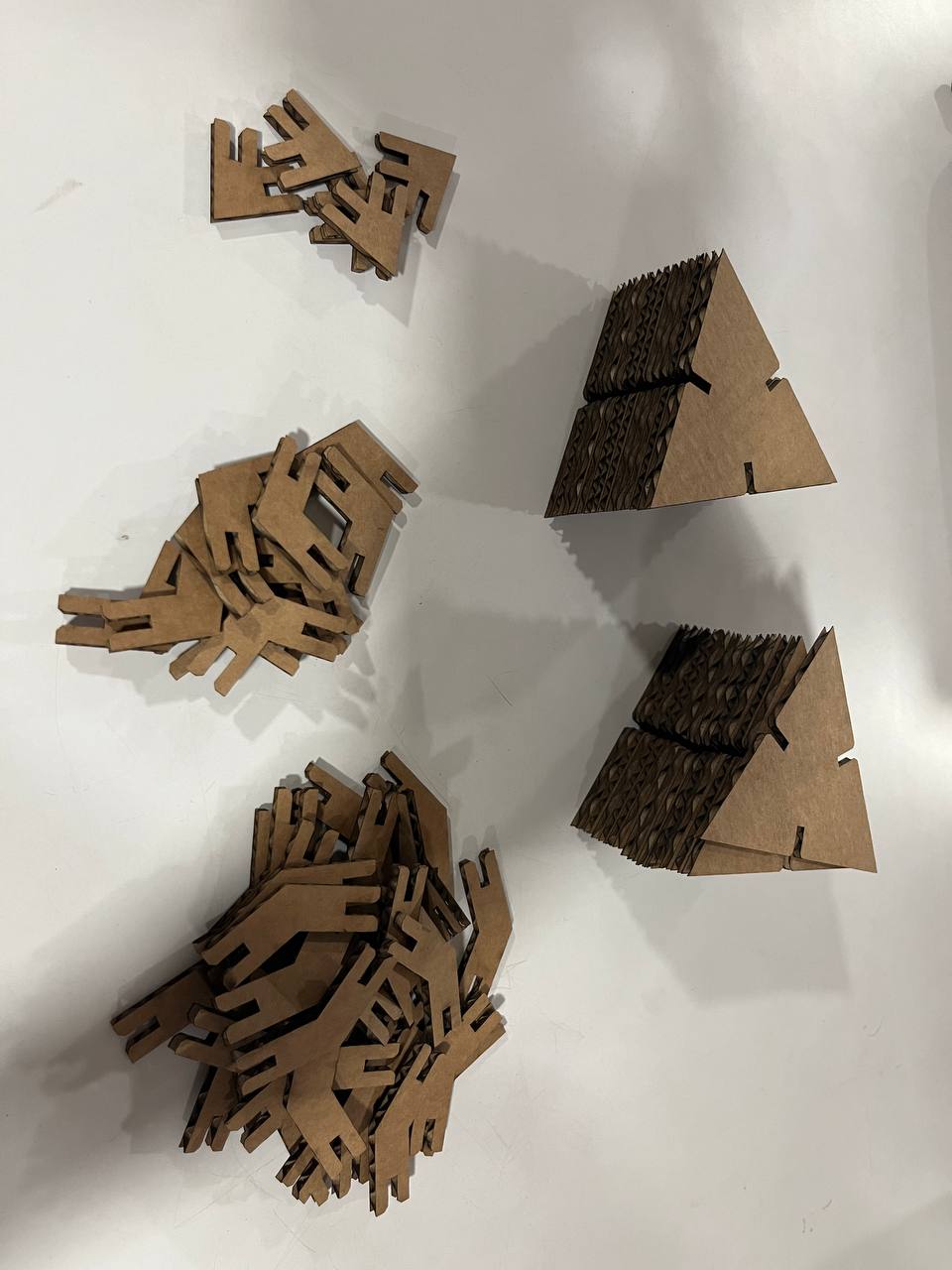
And here is the assembled triangular faced platonic solids - "Hero" shot.
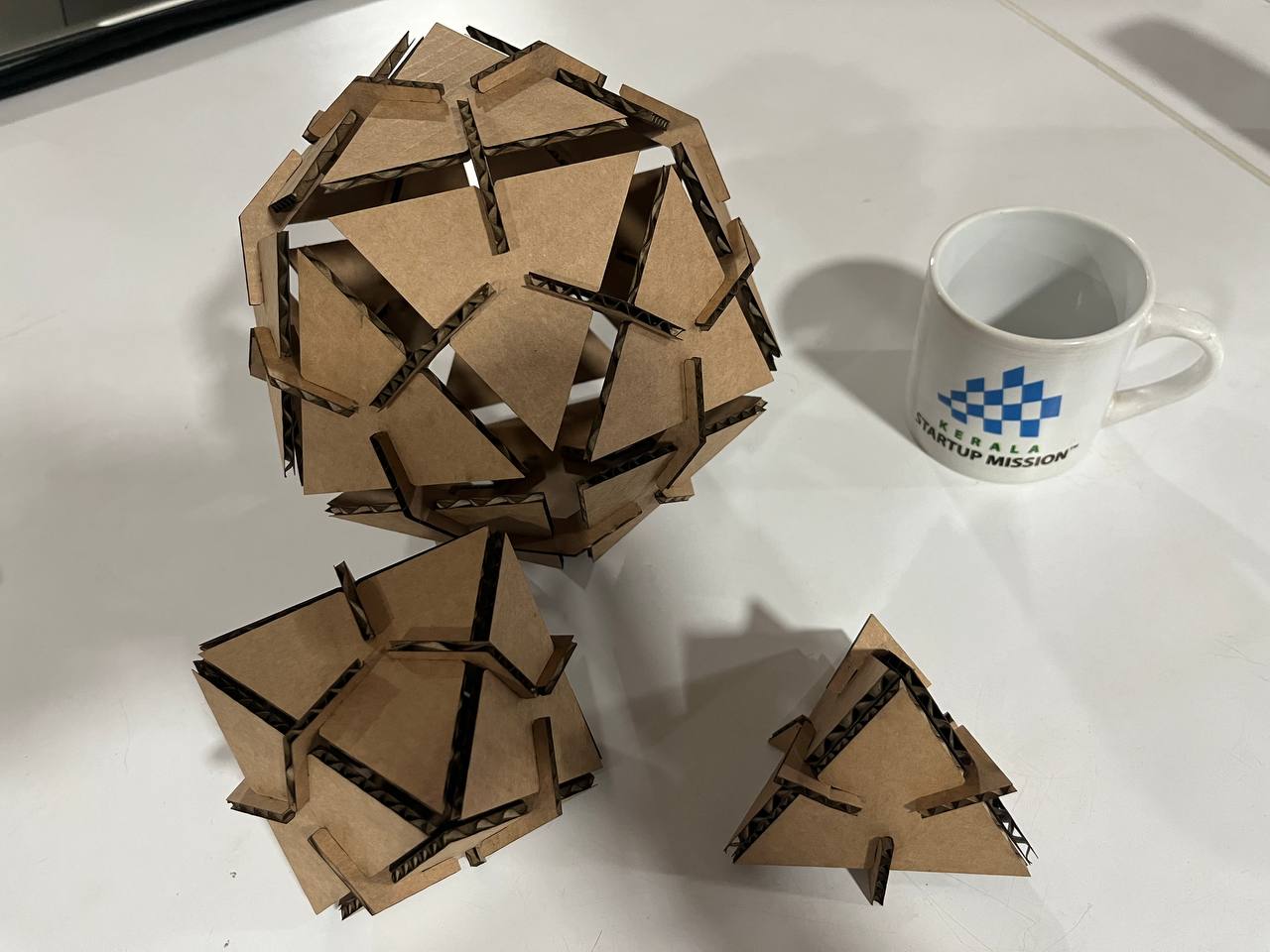
Using Vinyl Cutter - Part 1: Cutting
Last part of this week's assignment is to use the vinyl cutter. I've got a business and it has a logo, designed by one employee and brilliant young man named "Chico Mysterioso". Of course I want this on my laptop. Let's go!!!
Here's the machine we will use. It's a Rolland Vinyl Cutter. Note on the right we have the computer we use to process and send the file to the cutter.

This is the software interface. The interface is called "Mods" and was developed by Dr. Neil. The benefit of this software is that it can be used to prepare a digital designs for a variety of different machines.
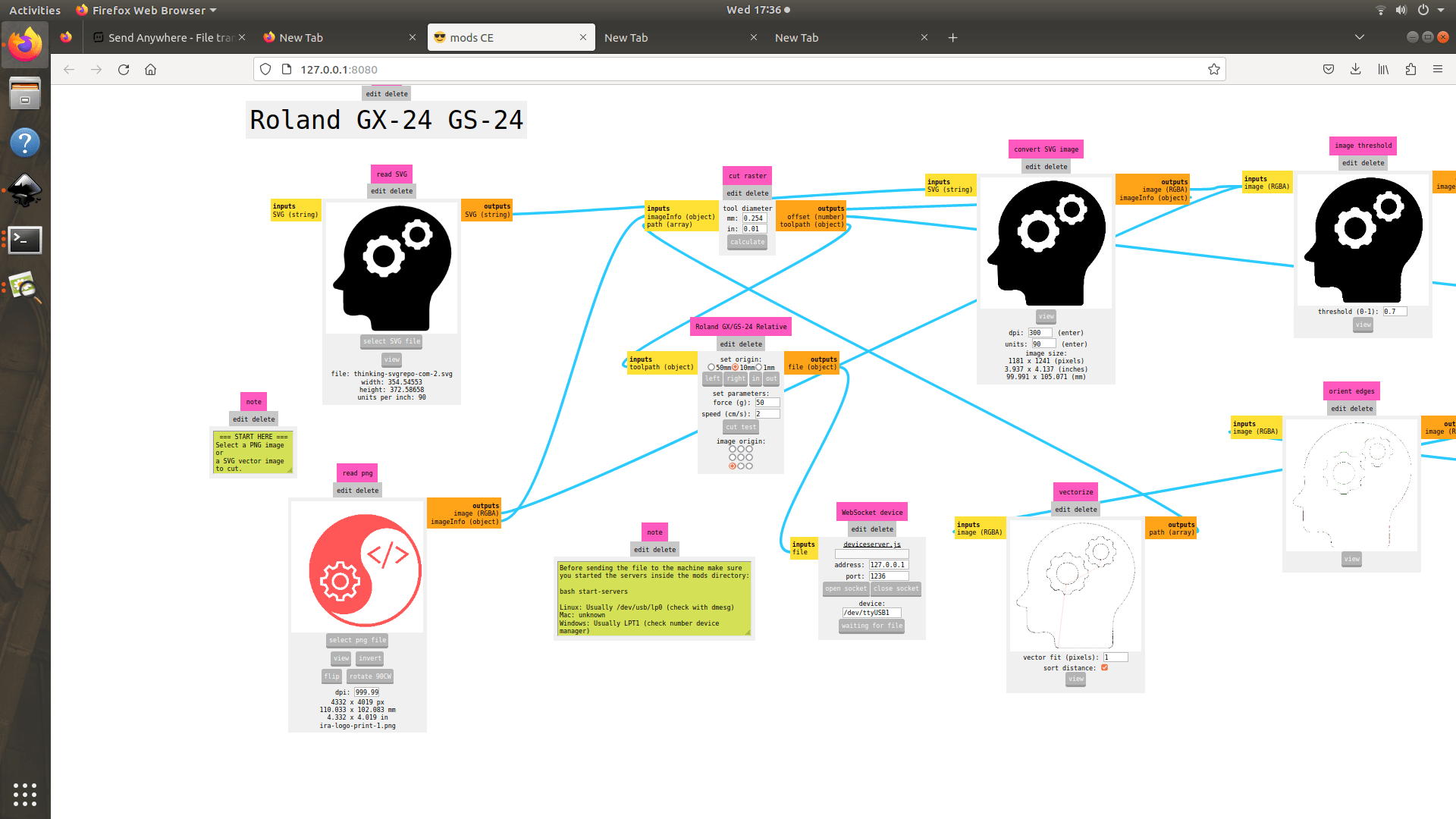
Initially there were some issues with processing. Specifically for Vinyl cutting we must remove the stroke and make it black
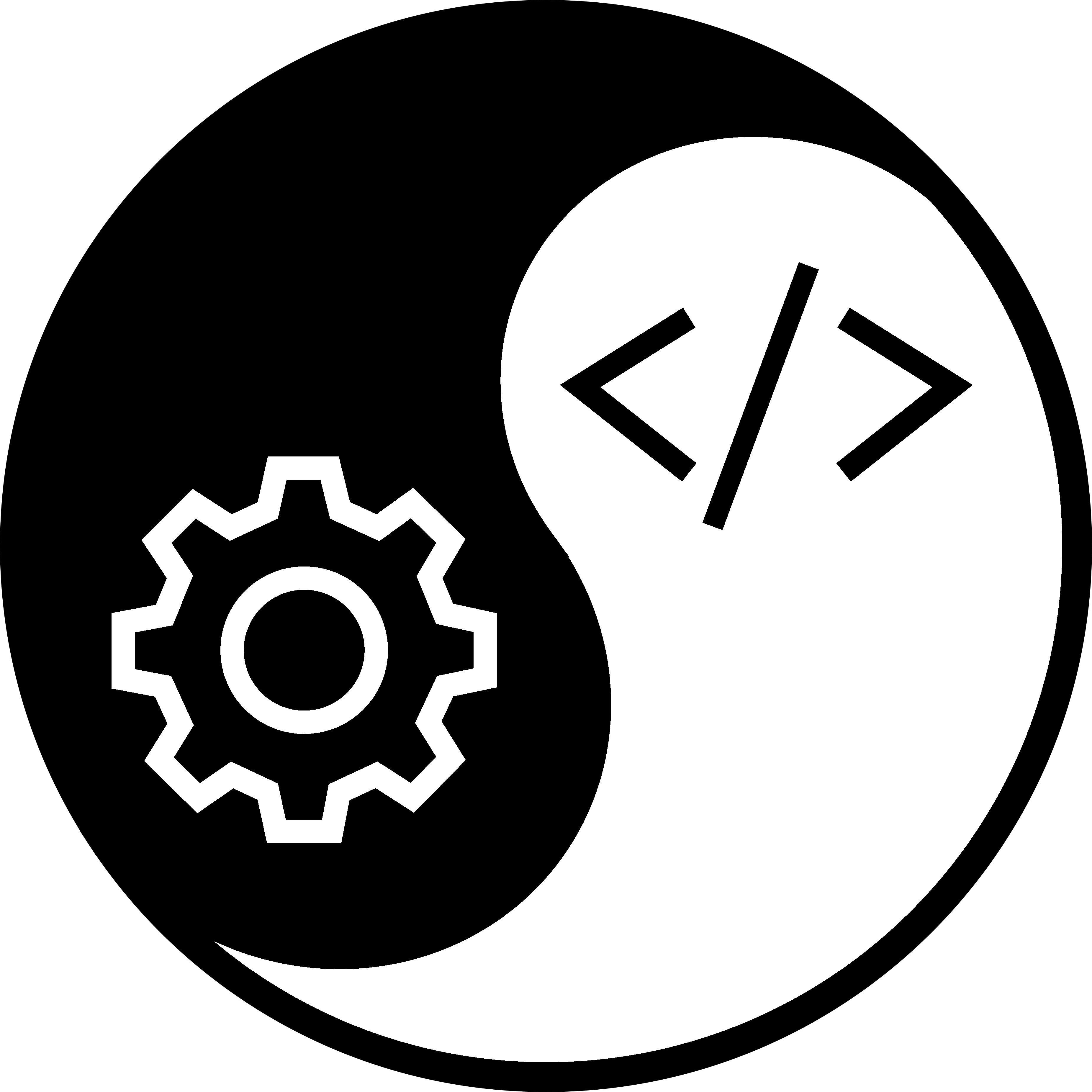
Then we gonna watch it cut!! Very nice, very smooth:
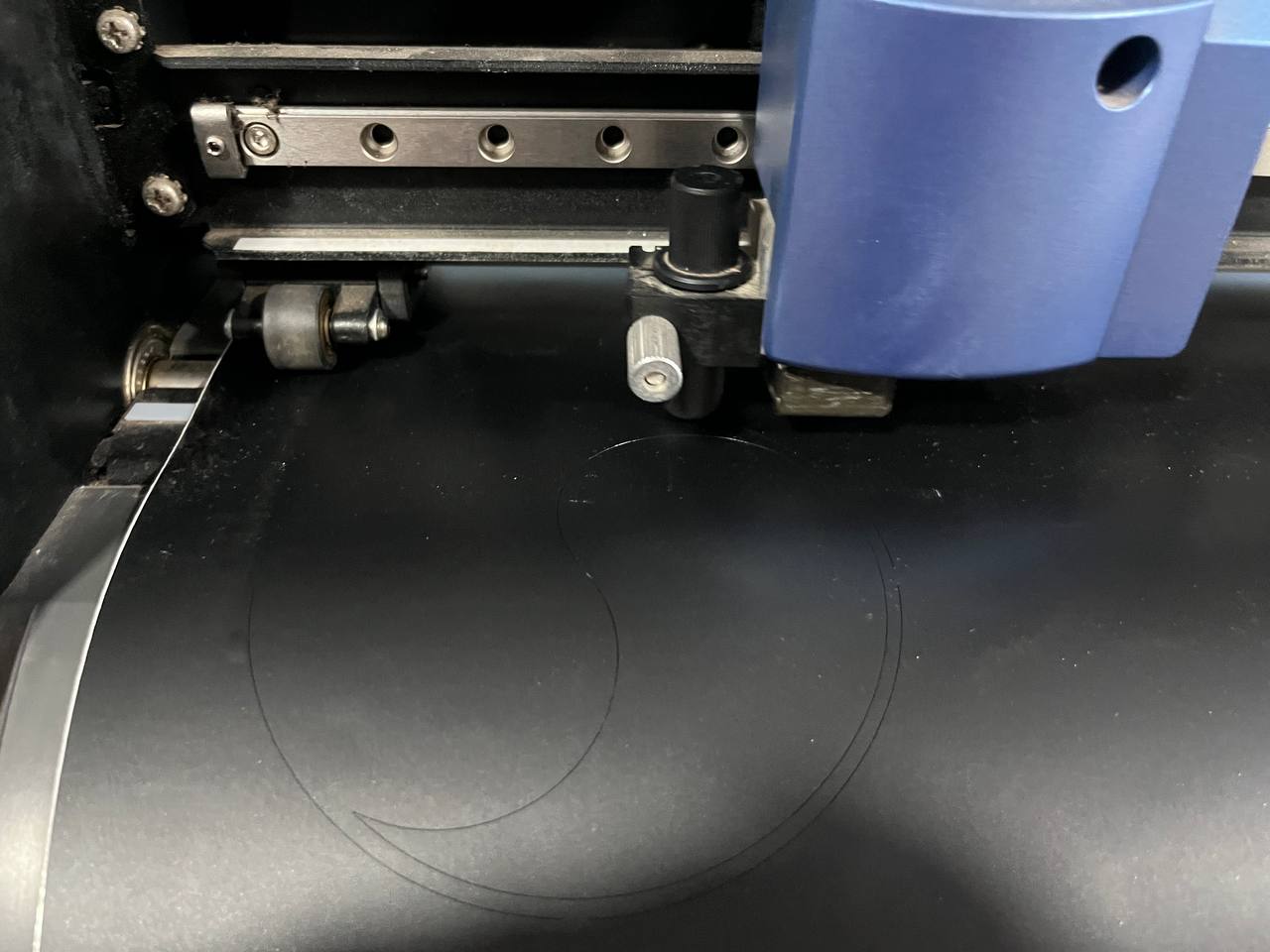
Later we also took the image of the kazakhstan flag for vinyl cutting, following the same process.
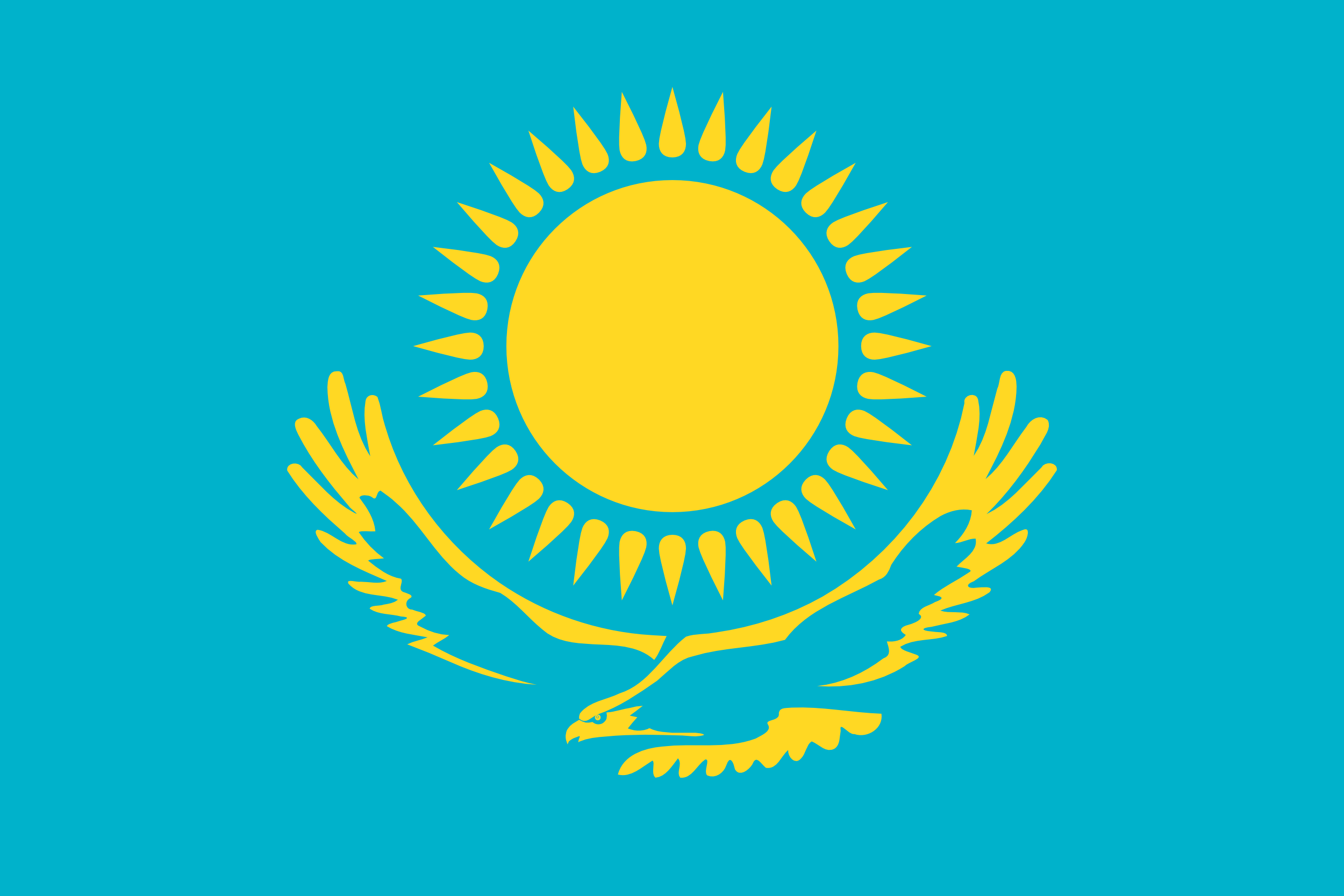
Using Vinyl Cutter - Part 2: Installation
1. Remove the non-essential parts of the design.
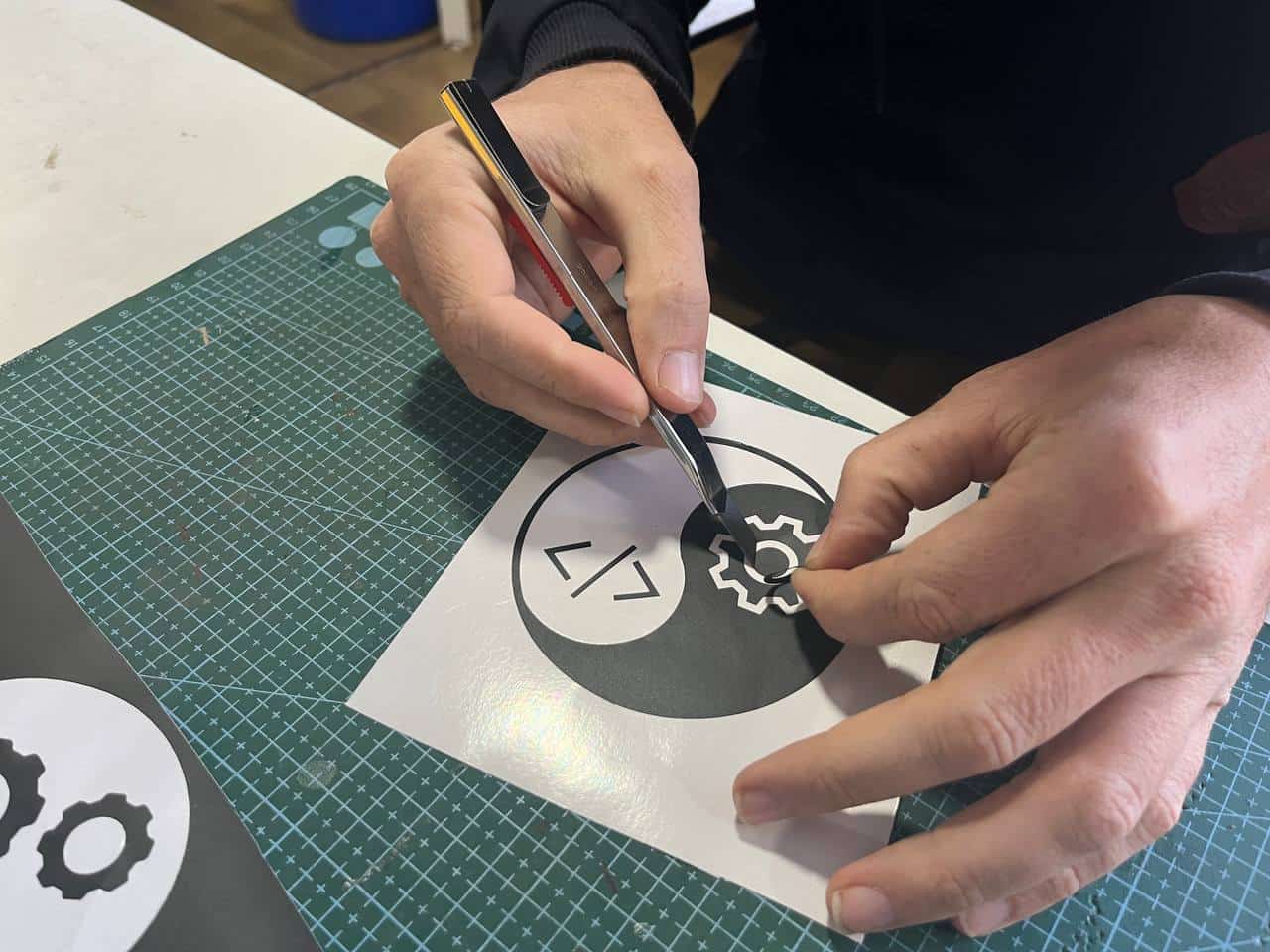
2. Take a piece of sticky tape and remove the back.
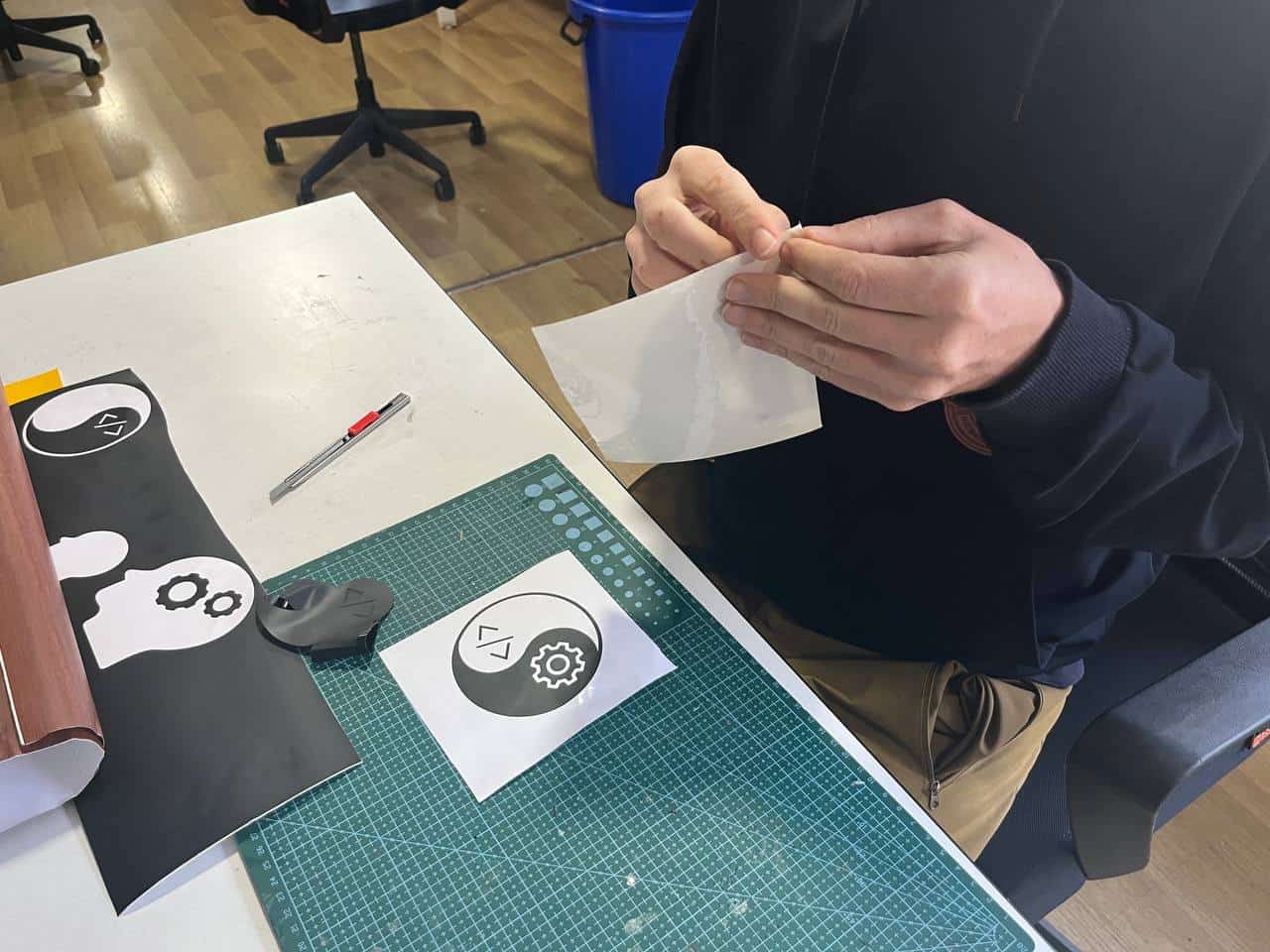
3. Press the sticky tape on the image.
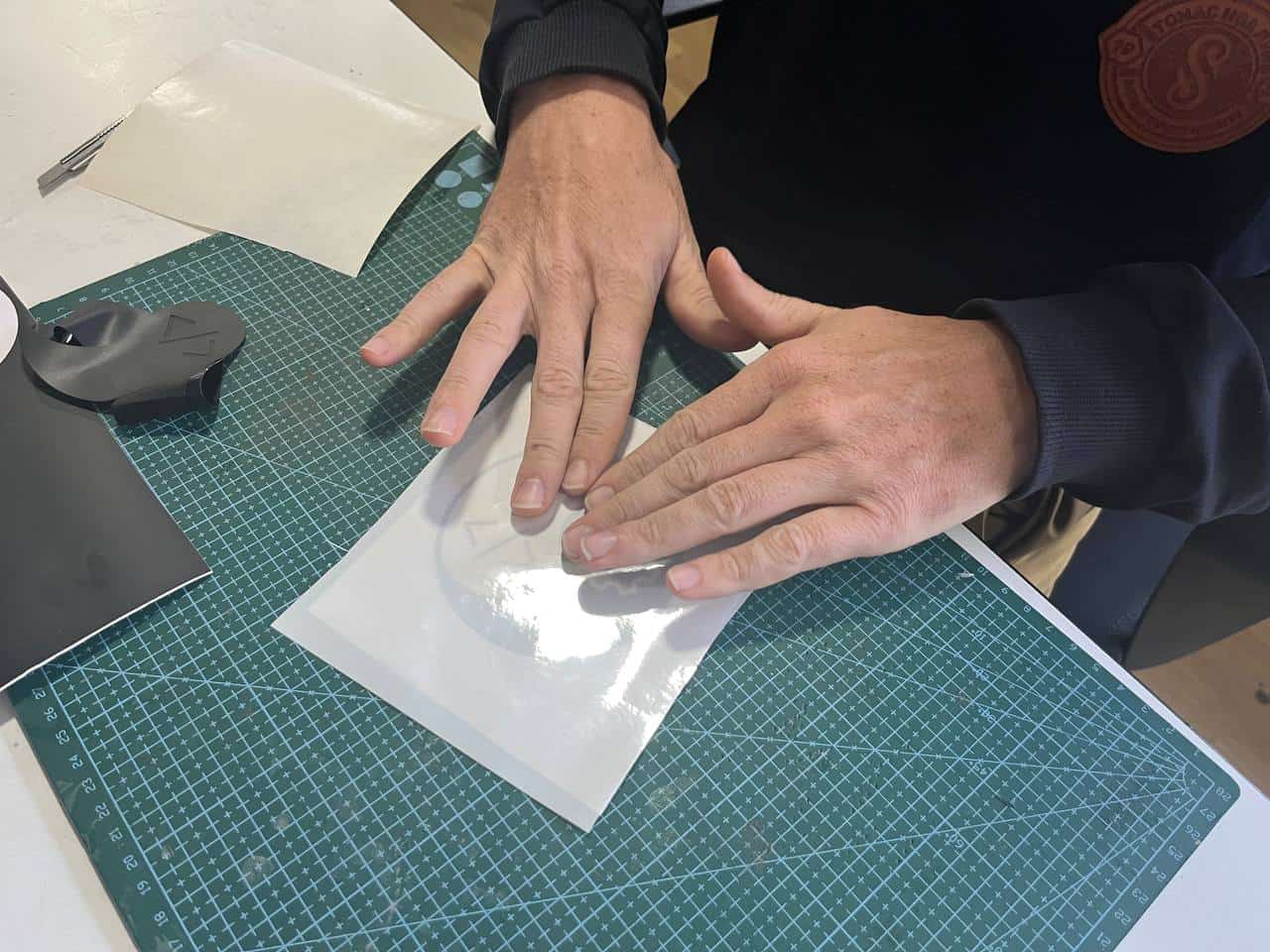
4. Now the design is ready for transfer.
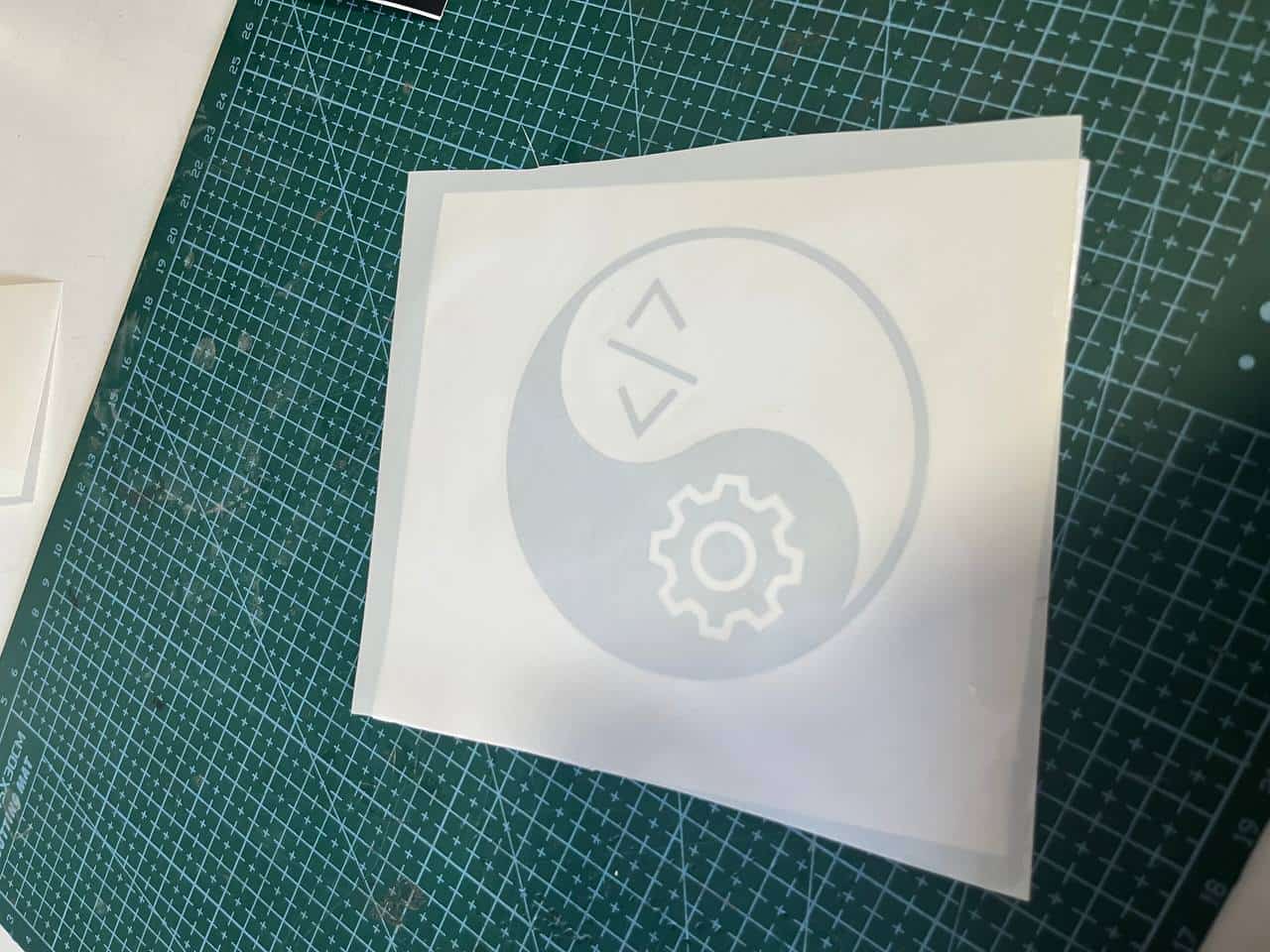
Now I installed the vinyl cutouts professionally. My laptop increased in value tremendously.
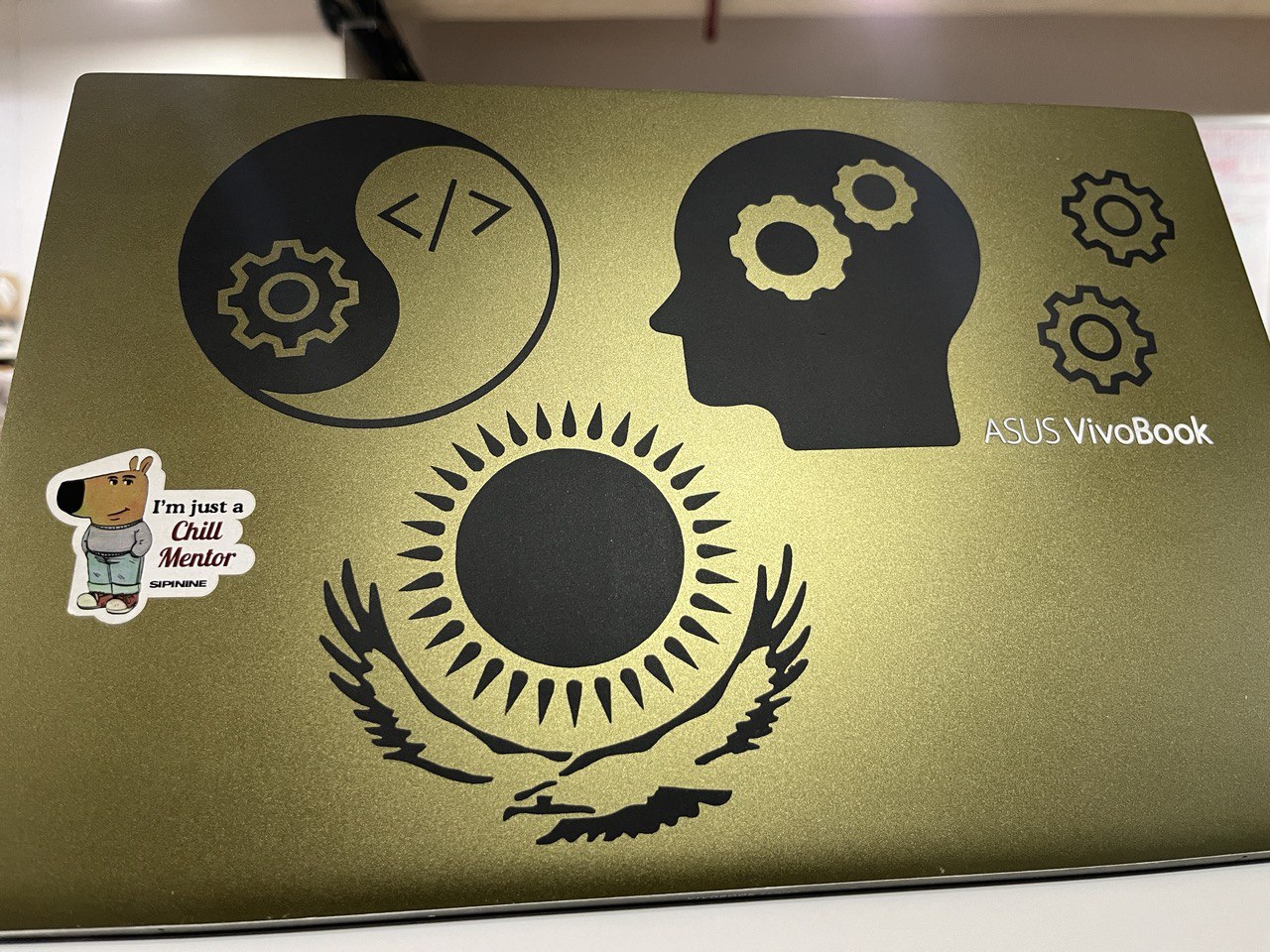