Group Assignment
Click to access the group assignmentMy Contribution – Week 11 - Mechanical Design & Machine Design
Claw Mechanism Design and Iteration
During Machine Week, I was responsible for designing the claw mechanism that grabs the tennis balls. I used Fusion 360 to model and simulate the claw, focusing on simplicity, strength, and synchronized motion.
The claw features two symmetrical hemispherical arms that close via a gear mechanism. The fingers are curved to match the shape of a tennis ball and ensure a secure grip.
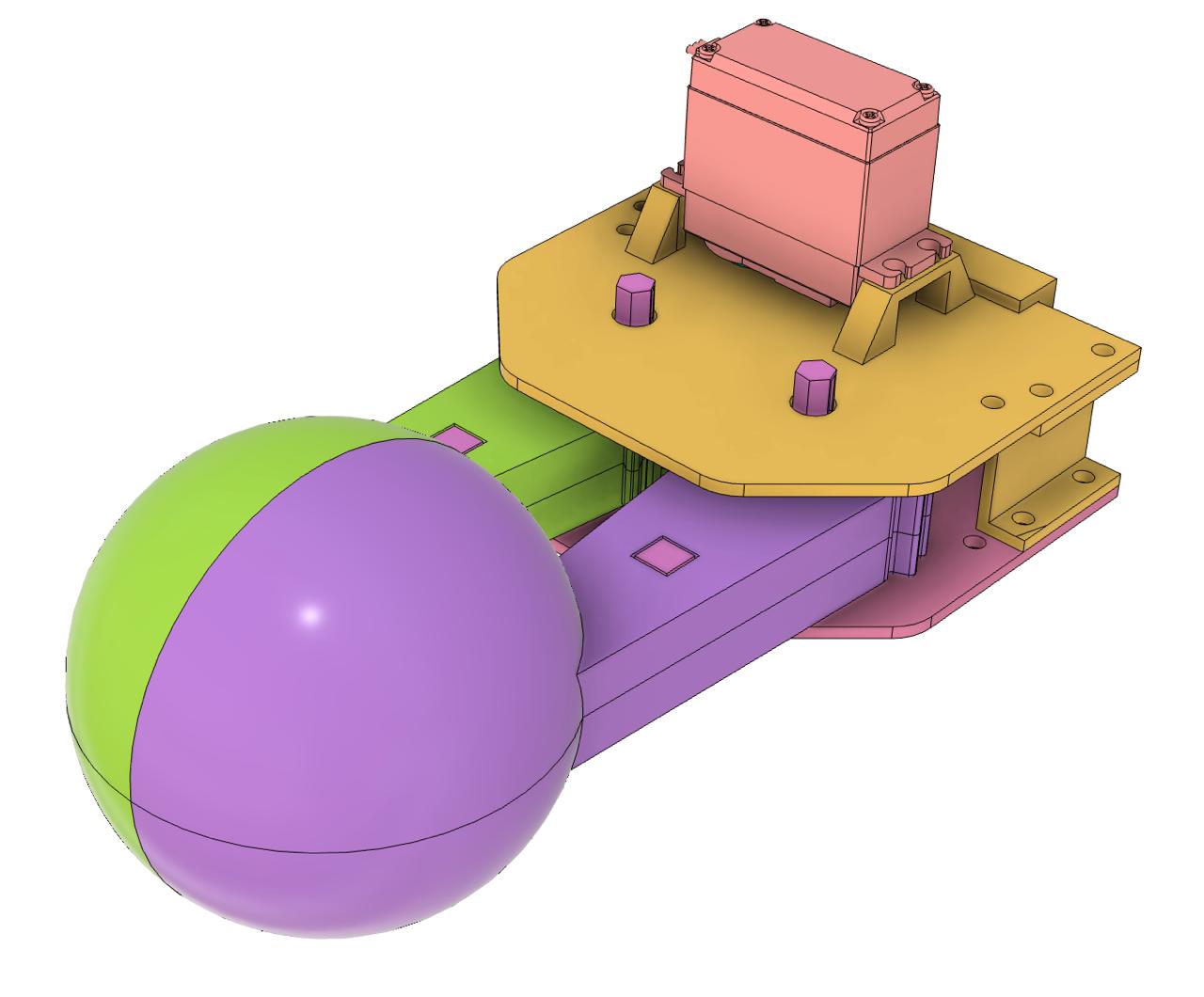
This is the final CAD version of the claw mechanism, including the MG995 servo mount and base plate.
In the first version (v1), I used a SG90 servo motor, but it didn’t provide enough torque to move the claws reliably. I then switched to a MG995 servo, which performed much better and allowed smooth and powerful operation.
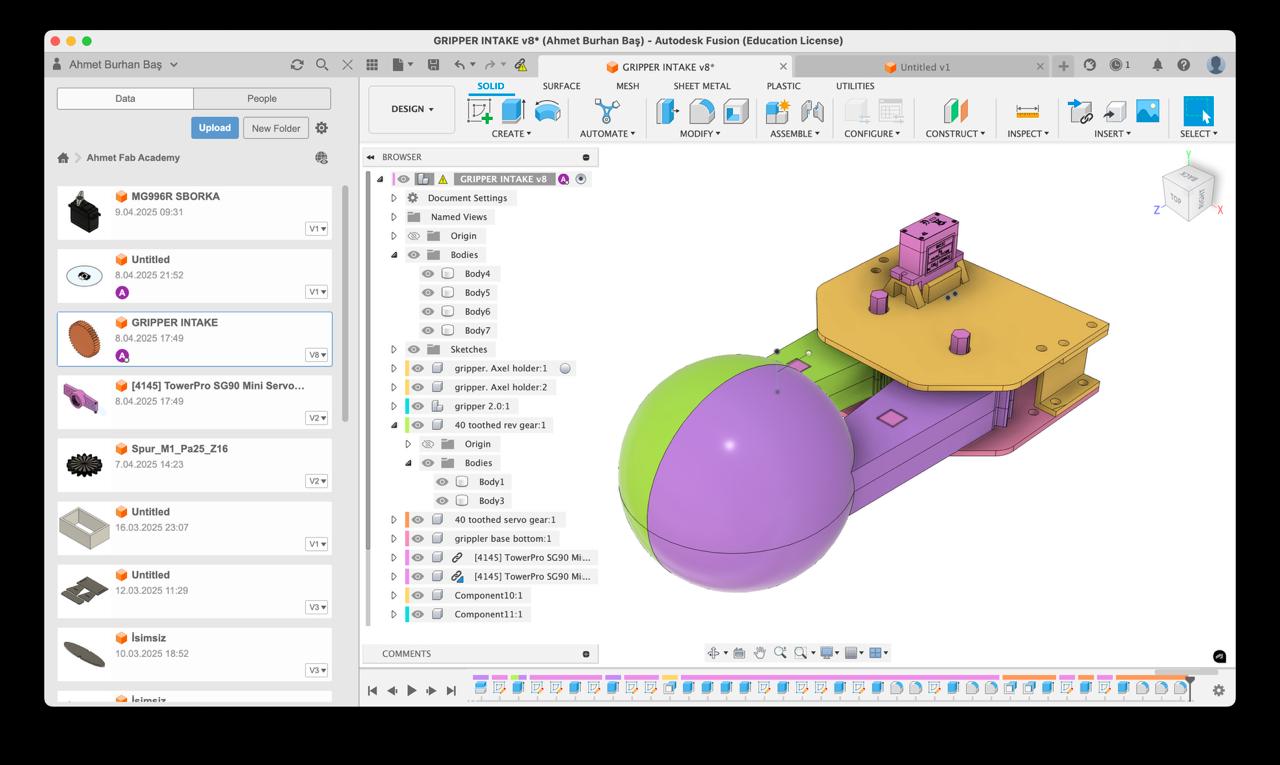
Fusion 360 CAD Environment
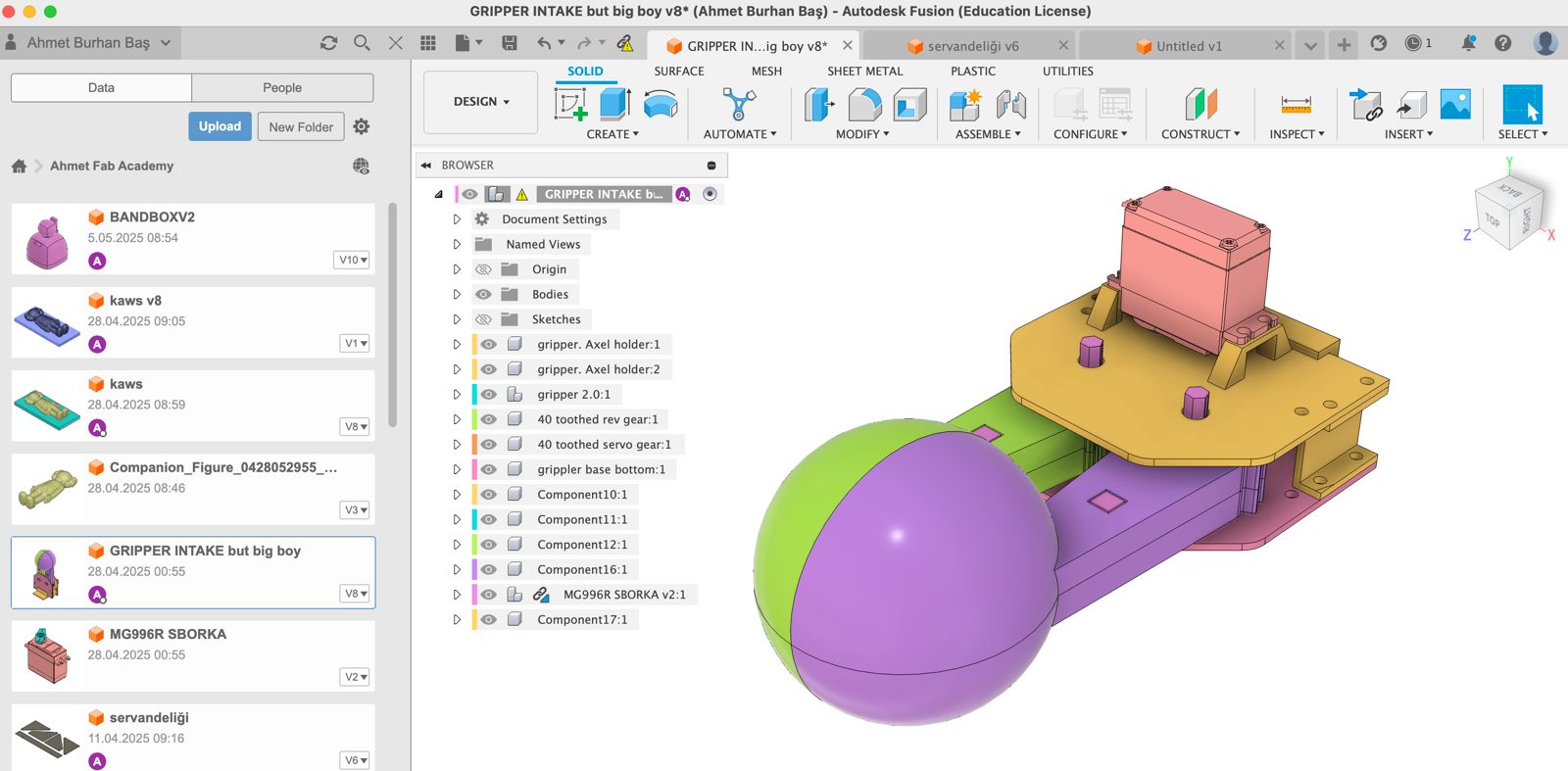
Here’s a view from inside Fusion 360 showing the component breakdown, sketches, and body structure of the gripper assembly. I used multiple components and sketches to keep the design parametric and modular.
3D Printing and Assembly
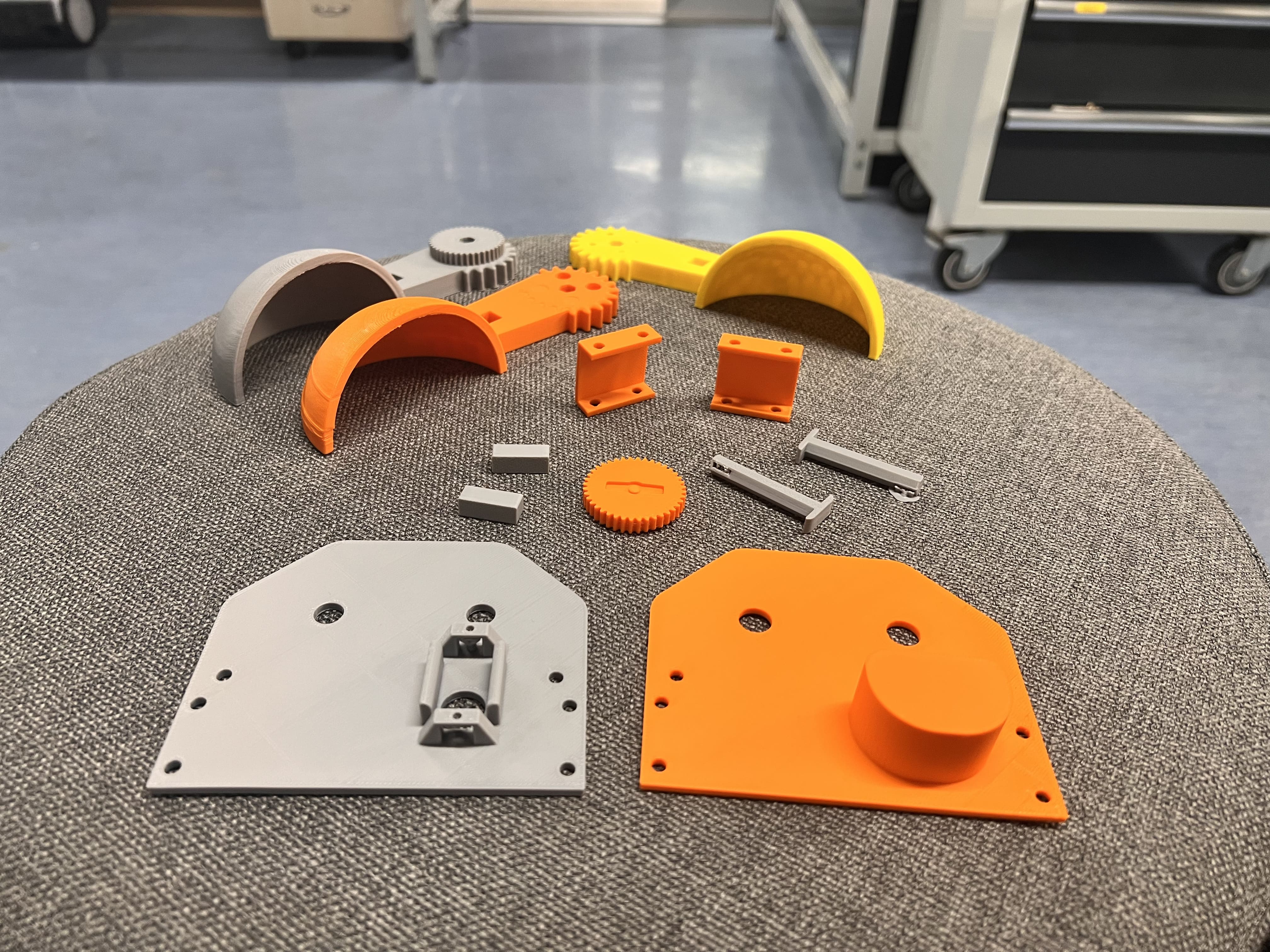
After the design was finalized, I printed all the parts using PLA. The image above shows all printed pieces laid out before assembly.
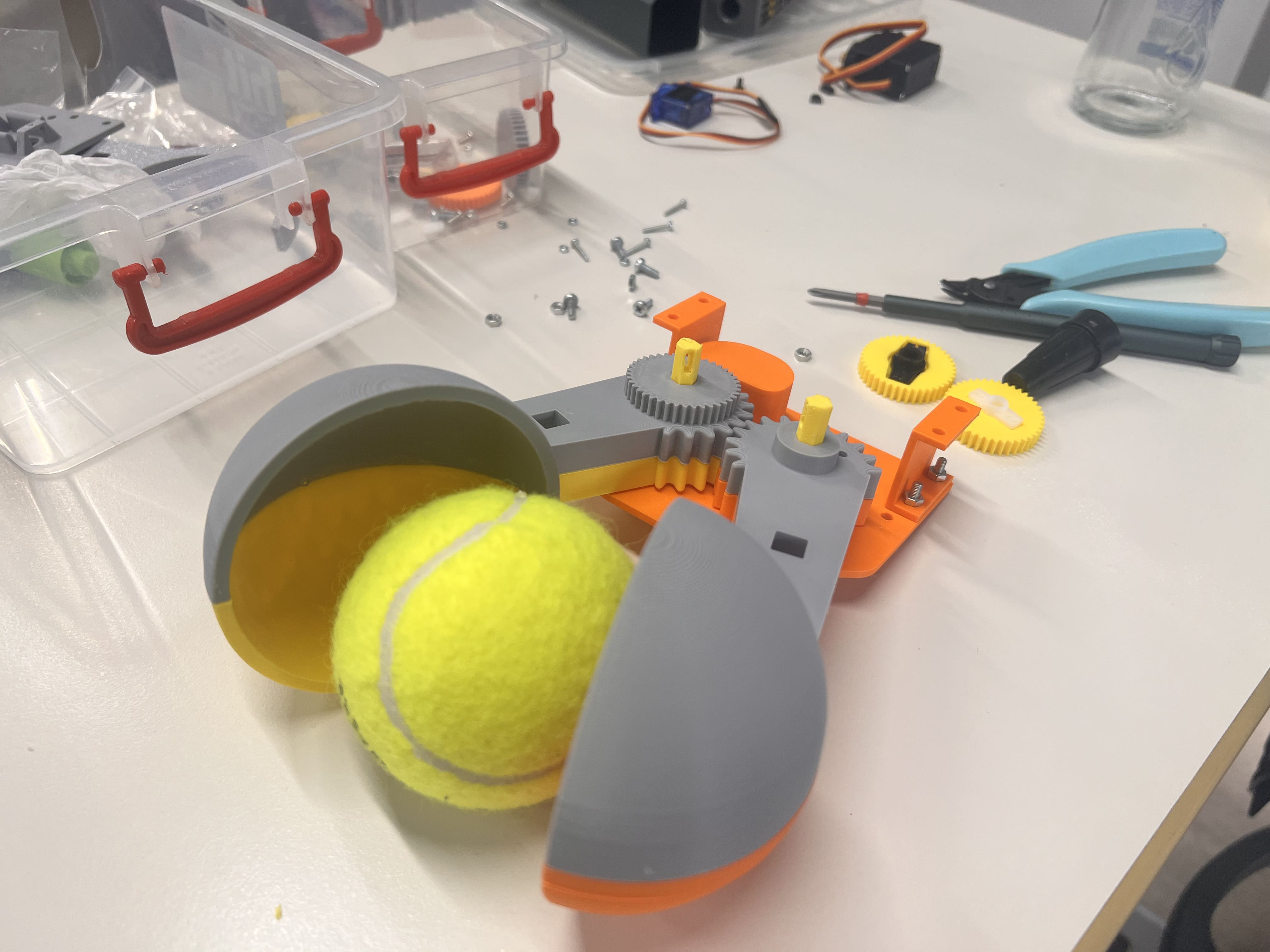
I assembled the claw mechanism with bolts, inserted the servo, and connected the gears. The gripping motion was tested with a tennis ball and worked successfully.
Video Production
I was also in charge of editing the final video for our Machine Week project. I used CapCut as the video editor — it's a simple and powerful platform that allowed me to quickly cut clips, add transitions, and overlay text.
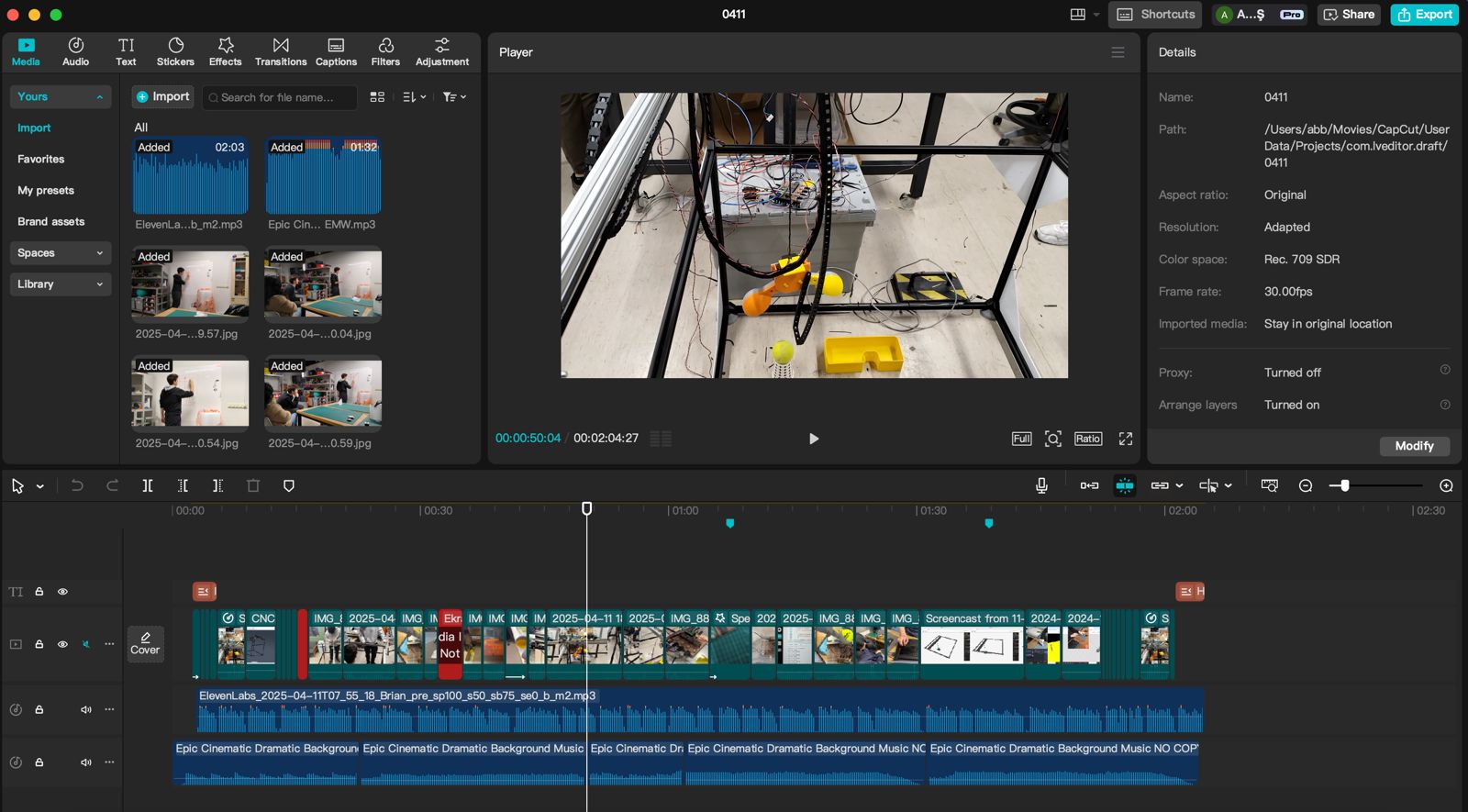
The final video included footage of the machine operating, Fusion 360 CAD views, and scenes of our team collaborating. To make it more engaging, I added AI-generated narration using ElevenLabs, a voice synthesis platform that delivers realistic and natural-sounding speech.
This combination of visual editing and AI narration made the video clear, professional, and fun to watch.