W7 | Computer-Controlled Machining 🔧
GROUP ASSIGMENT
- Complete the laboratory safety training.
- Test runout, alignment, fixturing, speeds, feeds, materials and toolpaths for your machine.
- Document your work to the group work page and reflect on your individual page what you learned.
INDIVIDUAL ASSIGNMENT
- Make (design+mill+assemble) something big
Make Something Big
Designing, Milling, and Assembling
For this week's assignment, I took on the challenge of designing, CNC milling, and assembling a large-scale object—approximately one meter in size. The goal was to apply everything I had learned about CNC milling. After training with the ShopBot PRS Alpha, it was time to put our training into practice.Earlier this year, ESAN Ediciones challenged us to create a backlit sign featuring their logo. Excited by the opportunity, I accepted the challenge and got to work! 👩🔧

We were provided with a reference image of the design, along with the required dimensions and the designated installation space. The challenge was to illuminate each letter of the logo, as well as the base, while ensuring that the wiring for the lighting remained completely hidden. 🔌✨
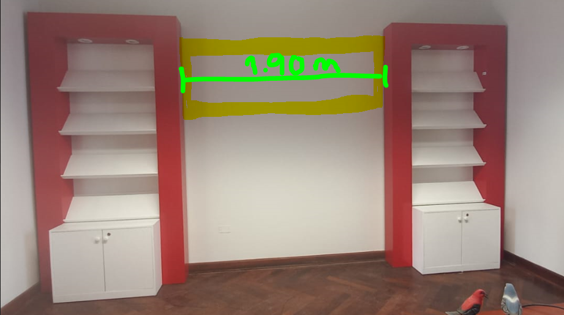
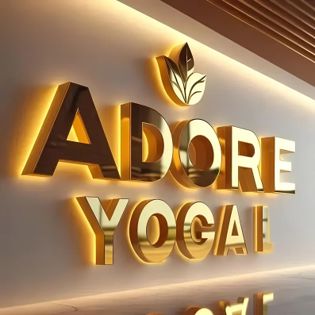
Designing
For the design ideation, Victor and I brainstormed ways to make the letters stand out from the board. We decided to design joints for better support and designed a box at the back to hide the wiring. The box was made to match the thickness of the nearby bookshelves, allowing us to cover it with the board where the letters would be mounted. To assemble the box, we designed press-fit joints around its edges for a secure fit. Additionally, a groove was milling on the back of the board to accommodate the LED strip.The design was created using Autodesk Inventor for the board, box, and joints. For the letter connectors and the letters themselves, we used CorelDRAW, where the logo was successfully vectorized without any issues.
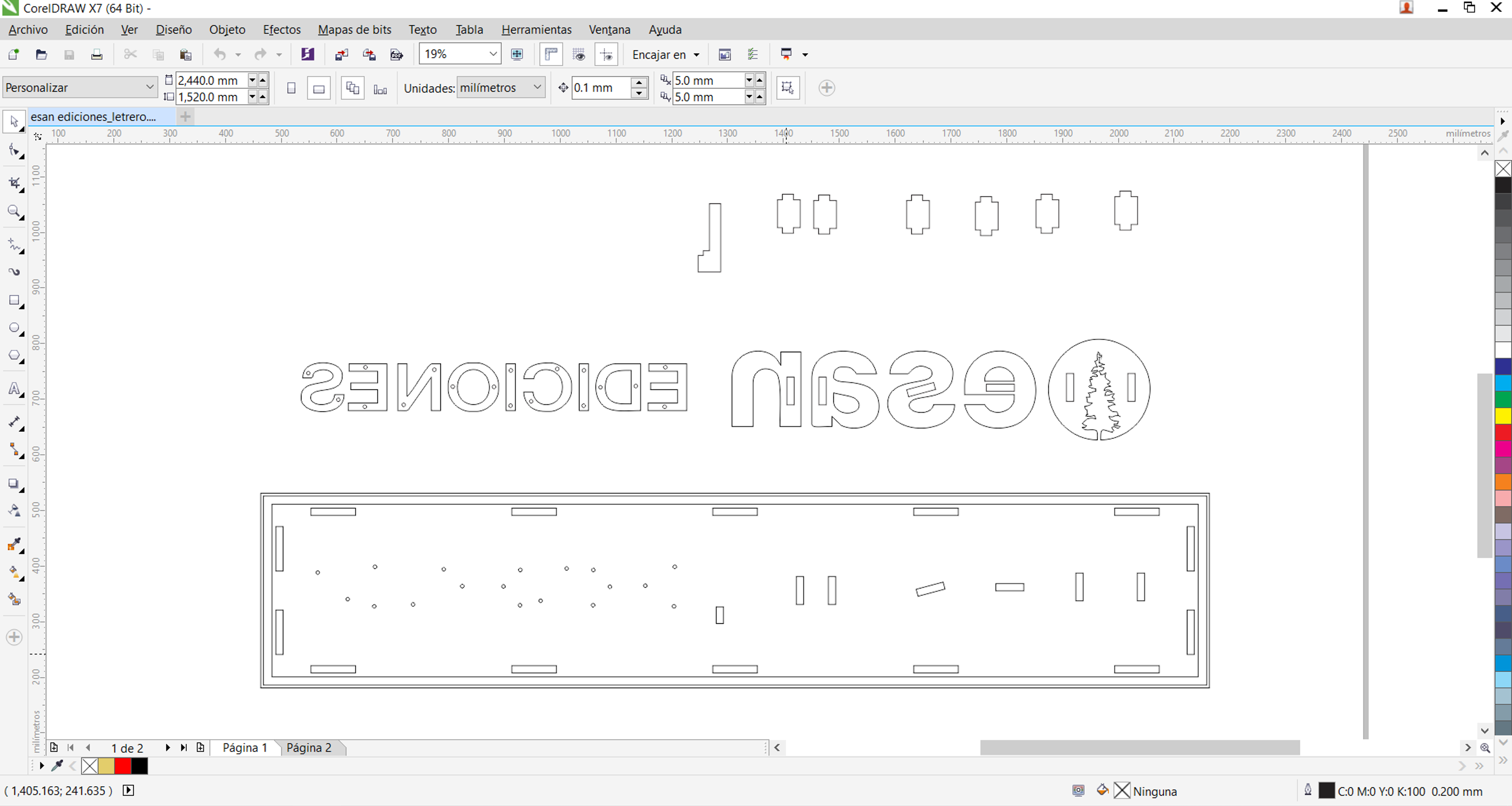
CorelDRAW
Note: Before starting the design, I first chose 12mm MDF as the material. I took measurements and ran tolerance tests to ensure everything fit perfectly, making the assembly process smooth and hassle-free.Settings VCarvePro
In the group assignment, we had an introduction to the ShopBot along with all the necessary safety measures. We also received training on how to use the CNC router. Now, it's time to get hands-on, but always with safety in mind—wearing gloves, safety glasses, staying within the designated areas, and, of course, knowing exactly where the emergency stop buttons are… not that I plan on needing them, but you never know. 😌Before starting the ShopBot, I had to generate my toolpaths using VCarve Pro. As I worked on them, I also made some final adjustments to the design. To make the most of my time and ensure I didn't end the day without milling, I sent the files in batches as I progressed.
I was almost forgetting...Before generating the toolpaths, I had to make sure the CNC router wouldn't struggle with the corners of my design. That's where fillets come in! Fillets are small rounded edges that help the machine move smoothly, prevent sharp stress points, and even make assembly easier. In press-fit joints, they ensure everything aligns and snaps into place without any trouble
I used T-Bone fillets and configured them in VCarve Pro like this:
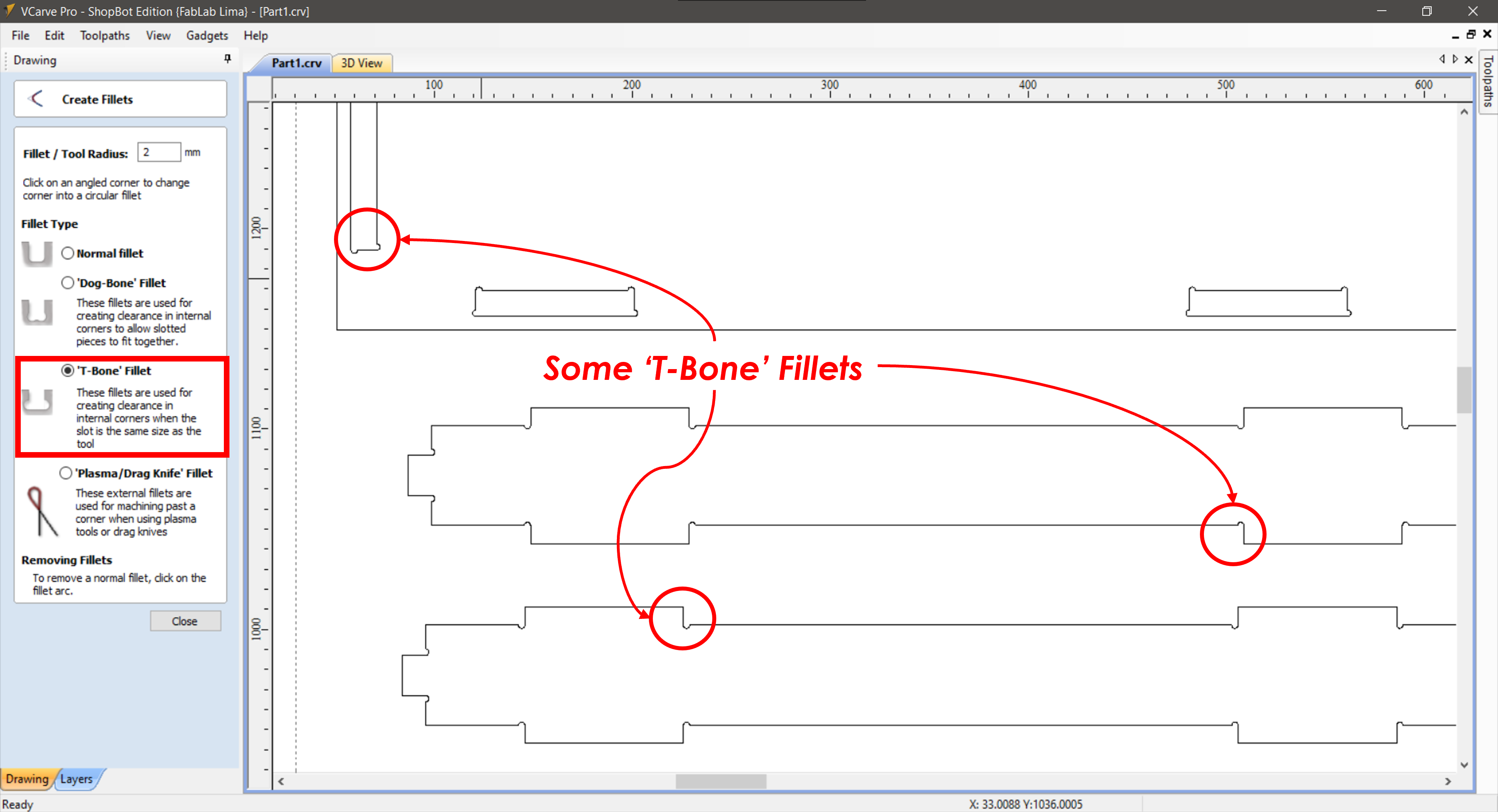
I repeated this process for all the batches before generating the toolpaths
Once I added fillets to all the pieces, it was time to generate the toolpaths for each batch.
For the first batch, I set up three machining processes:
1️⃣ Pocket Toolpath
2️⃣ 2D Profile Toolpath (Inside Cuts) — for the inner details
3️⃣ 2D Profile Toolpath (Outside Cuts) — to cut out the final shape
Then, for the second batch, I added one more:
4️⃣ Pocket Toolpath (Groove) — This was a special groove around the base where I would hide the LED strips.
And for the last batch, I followed the same setup as the first one.
To get the best results, I went with a 1/8” bit—small enough to handle the intricate details of the letters without causing any damage.
So, once I had all the toolpaths ready, I switched to the 3D preview to see how everything would look before cutting. Here's how it looked: 👀
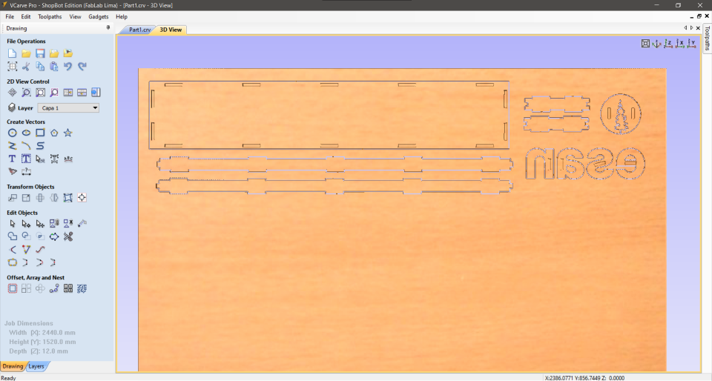
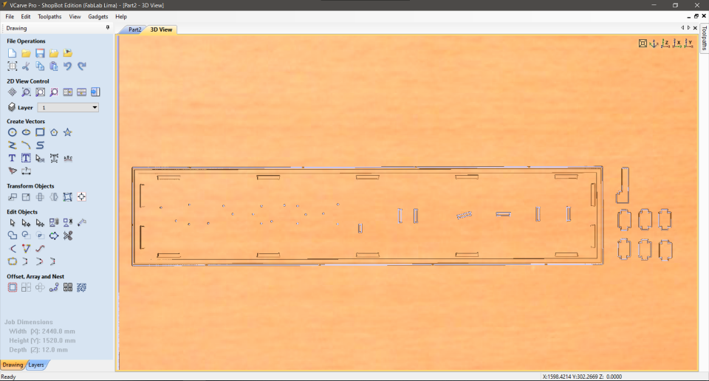
Milling
For the milling process, I followed the proper steps to ensure everything ran smoothly:
- First, I turned on the computer.
- Then, I powered up the ShopBot by switching it from OFF to ON.
- Next, I pressed the reset button on the control panel beside the main computer.
- After that, I moved the spindle to a specific reference point—ideally, the highest part of the material.
- I calibrated the Z-axis first, followed by the X and Y axes to ensure proper alignment.
- Once the bit was positioned at (0,0) and the calibration was complete, it was finally time to send the toolpath and let the machine do its magic!
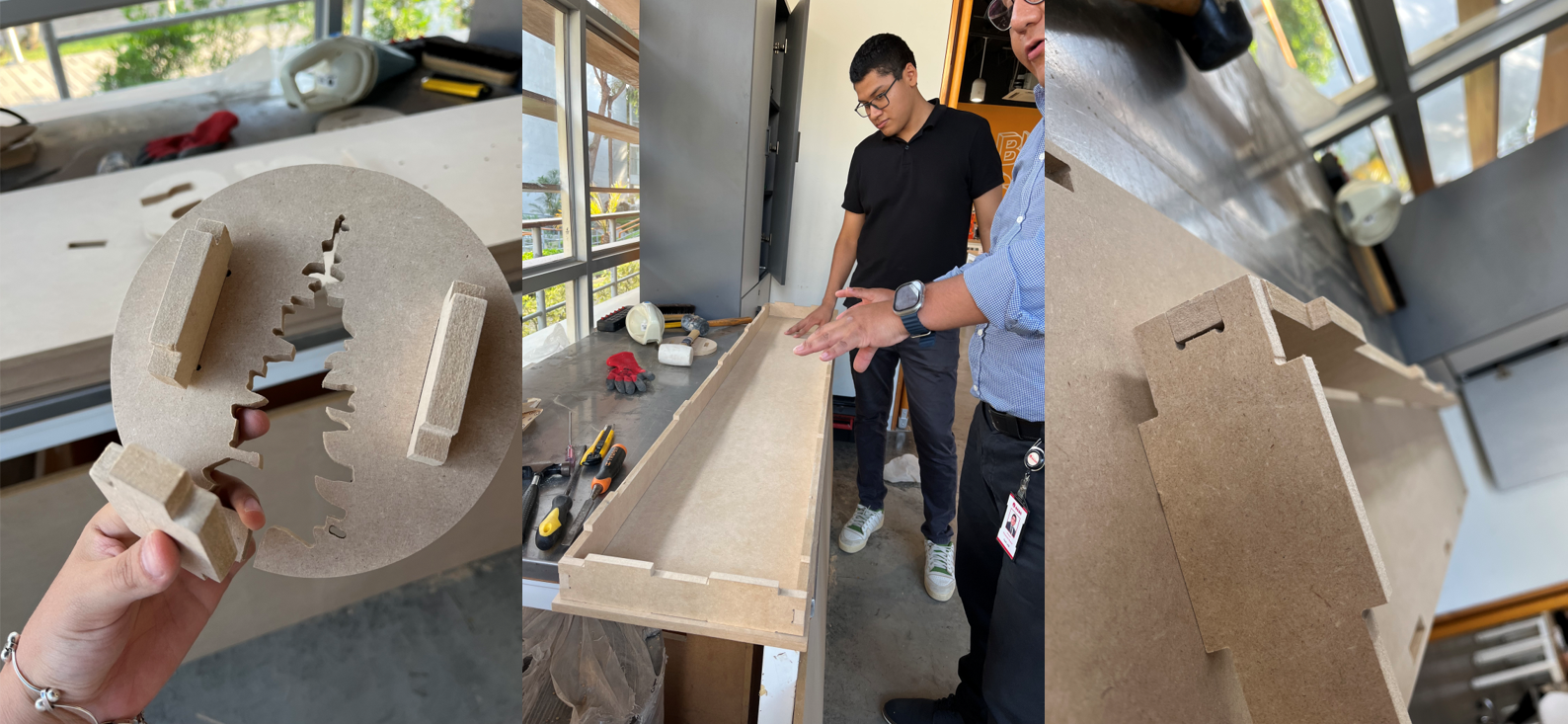
Assembling
With the milling done, it was time to remove the pieces from the MDF sheet. Making sure the machine was off, I carefully started taking them out. The problem? Some pieces were hard to reach, so I had to climb onto the machine bed to get them—talk about a full-body workout! To separate the parts, I used a screwdriver as a lever to break the small tabs I had added for stability. It was actually fun… but by the end, I was exhausted! 😅 Next step? Sanding! I had to smooth out the edges and remove any excess material before finally putting everything together.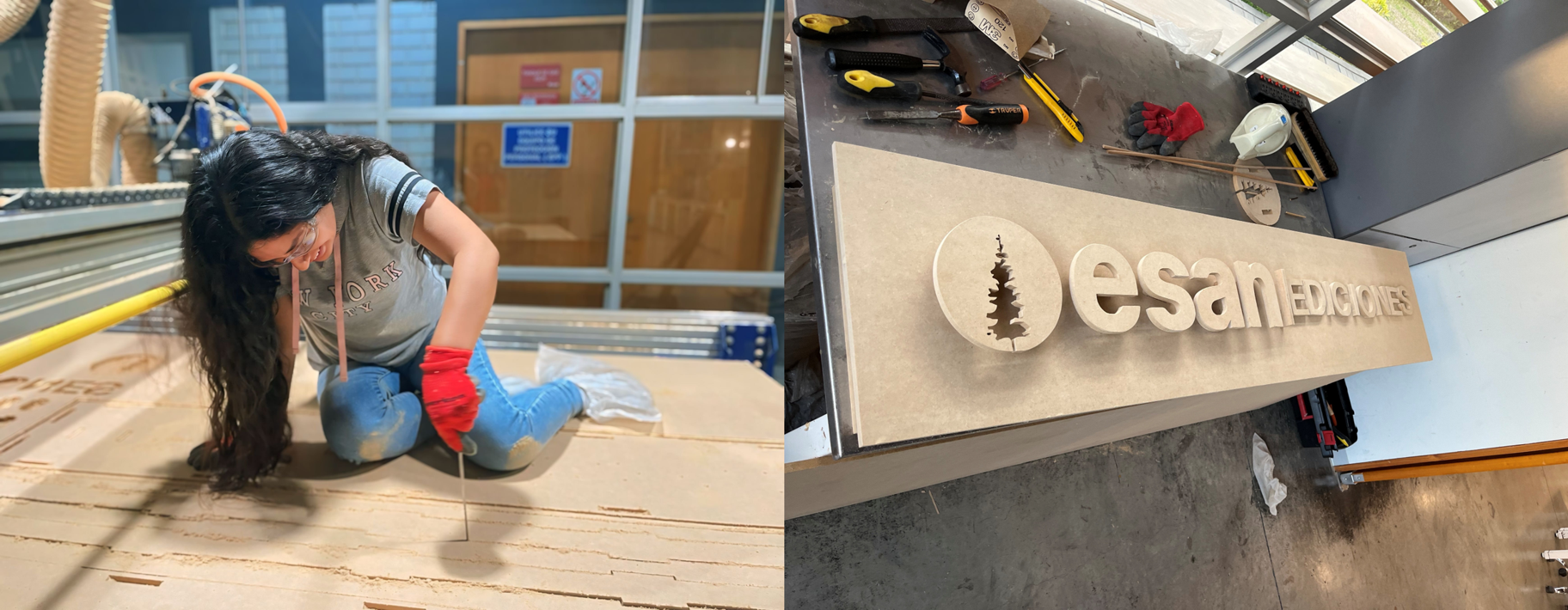