Assignments
- Complete your lab’s safety training.
- Test runout, alignment, fixturing, speeds, feeds, materials and toolpaths for your machine
- Document your work to the group work page and reflect on your individual page what you learned
Individual apport
- Ernesto: My contribution to this week's group work was working with the dog-bone corner, alongside varying tolerances of 0mm (needs sanding), 0.1mm (press-fit), and 0.2mm (smooth fit).
- Jorge: This week's group assignment required me to design and CNC route two types of joints. I chose parametric modeling for ease of use due to its numerous benefits. I focused on T-bone and dogbone joints with different center positions from Ernesto's tests.
- Marcela: I was responsible for testing the flexible pattern.
ULIMA FABLAB Safety Training
The safety training emphasized the importance of adhering to specific safety protocols to prevent accidents and ensure the well-being of all lab members. This document outlines the key safety measures discussed during the session, which we must follow while working in the lab.
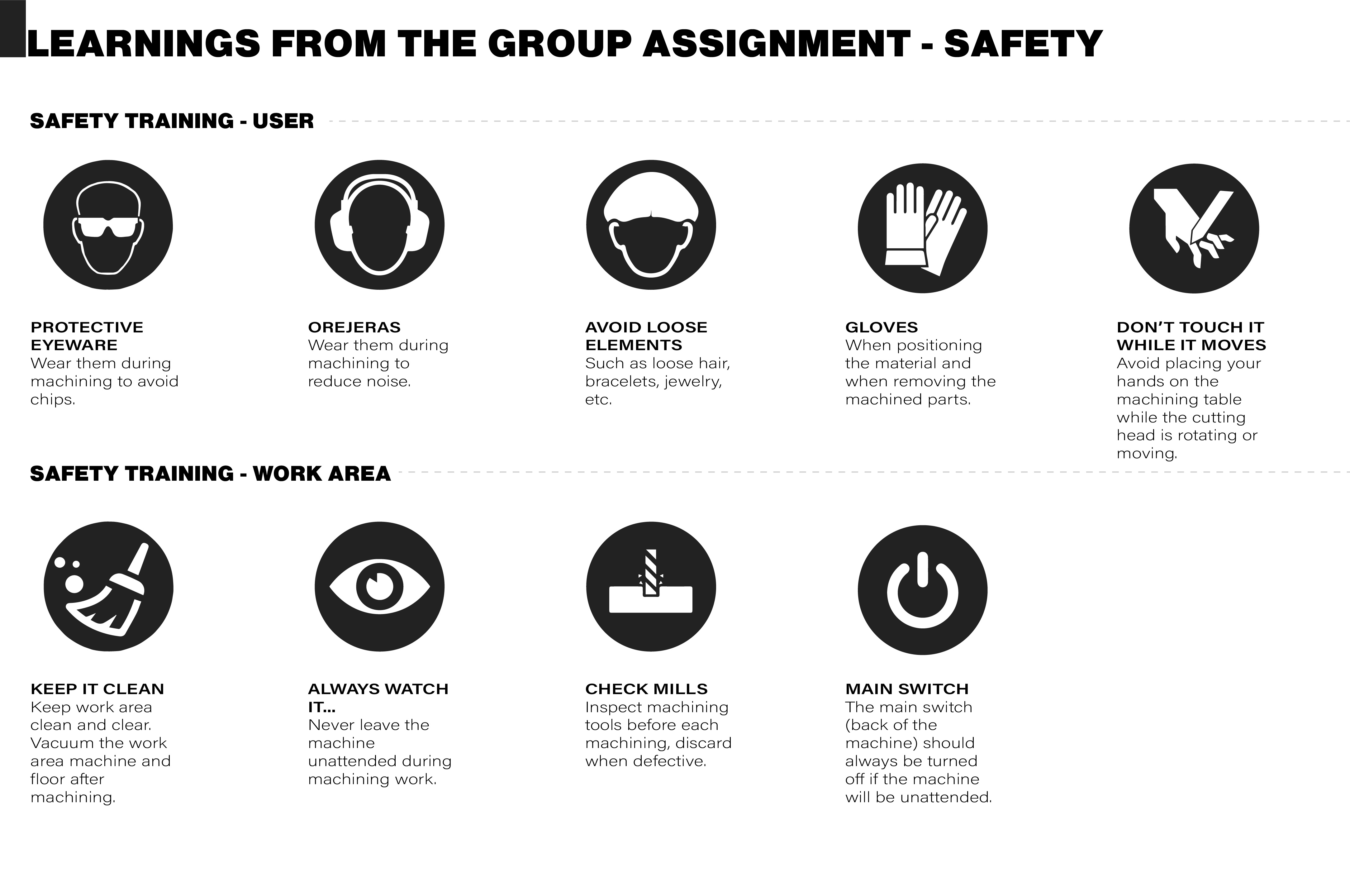
Machine Optimization Tests:
This week's assignment focuses on exploring CNC routing joint designs, specifically the simple corner, T-bone corner, and dog-bone corner, alongside varying tolerances of 0mm (needs sanding), 0.1mm (press-fit), and 0.2mm (smooth fit). The objective was to conduct tests using these joint designs with different tolerances to assess their fit and functionality in practical applications. Following the initial tests, we proceeded to evaluate various flexible patterns. This involved calculating the number of milled and non-milled parallel slots required to cut 15mm from an 18mm plywood sheet, anticipating the resulting radius upon rolling. The implementation yielded successful outcomes, achieving precise results and highlighting the effectiveness of these designs and patterns in CNC routing applications.Additionally, the experimentation extended to varying feed speeds and spindle RPMs to optimize cutting performance.
3D Design:
For the 3D design, we utilized Inventor Professional, leveraging its user-defined parameters such as material thickness, fit tolerance, and pin width. These parameters were crucial in creating and testing various joint designs, ensuring precision and functionality in the assembly process. This approach is more time-efficient as well."
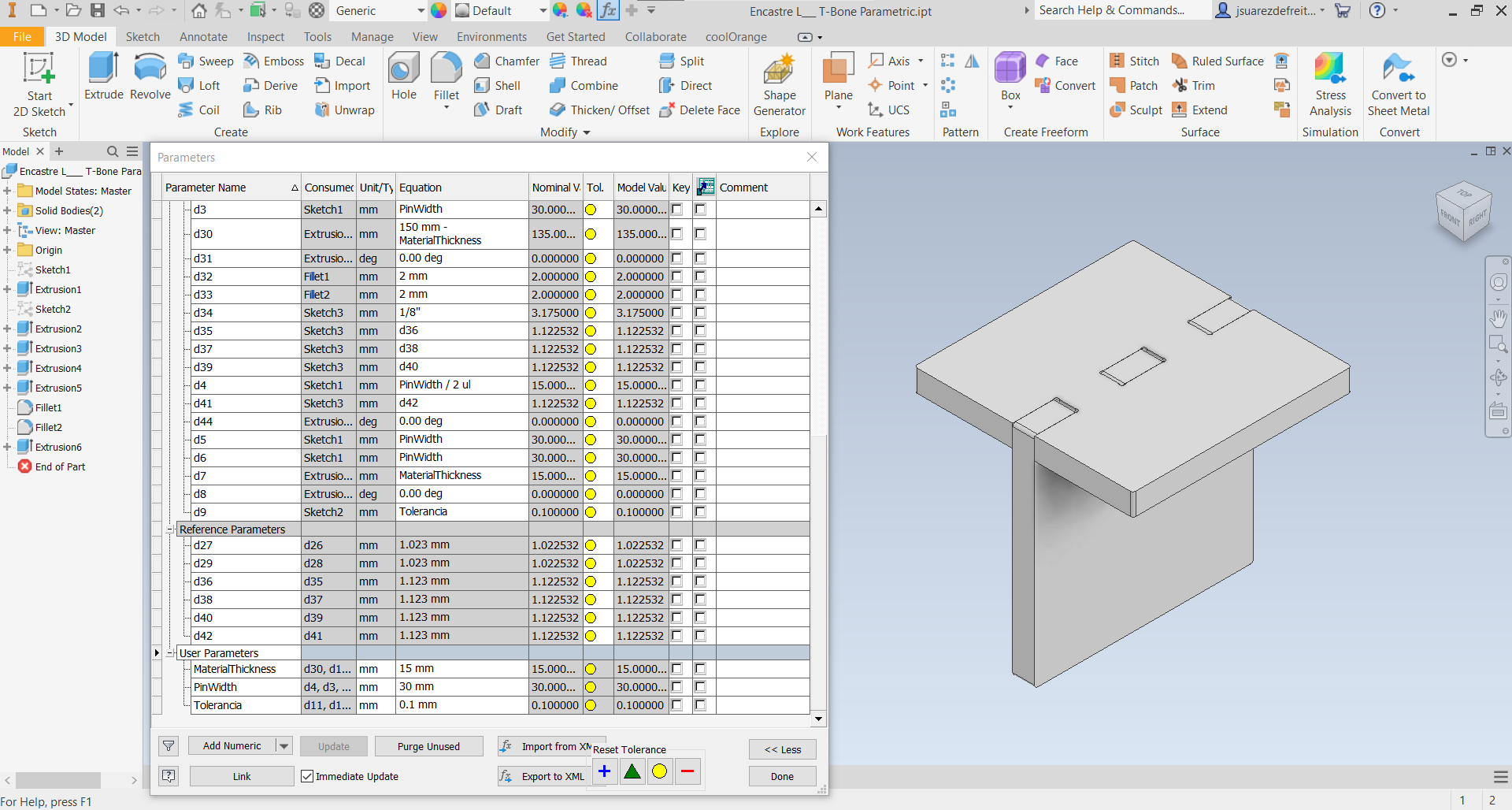
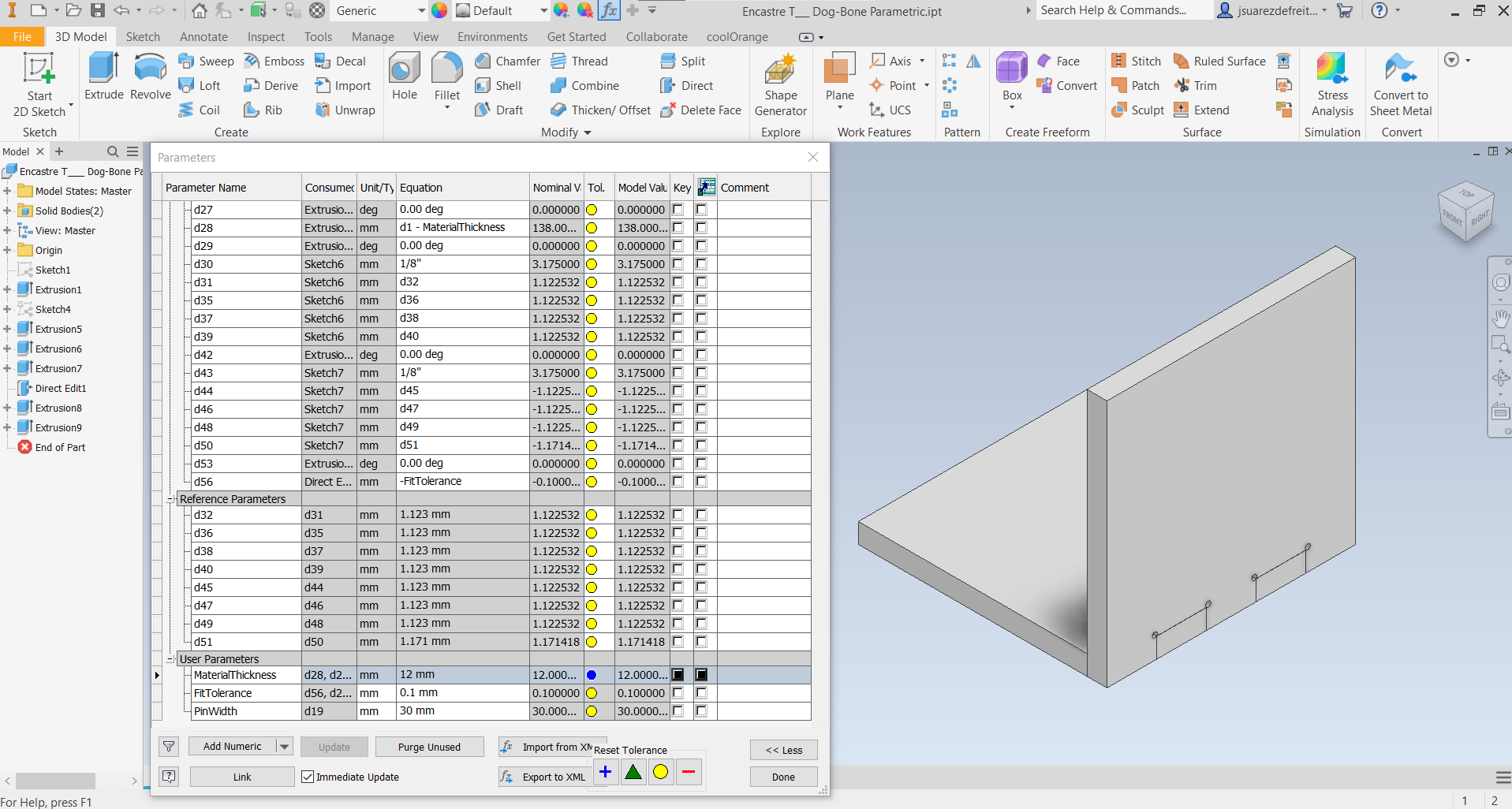
File Export:
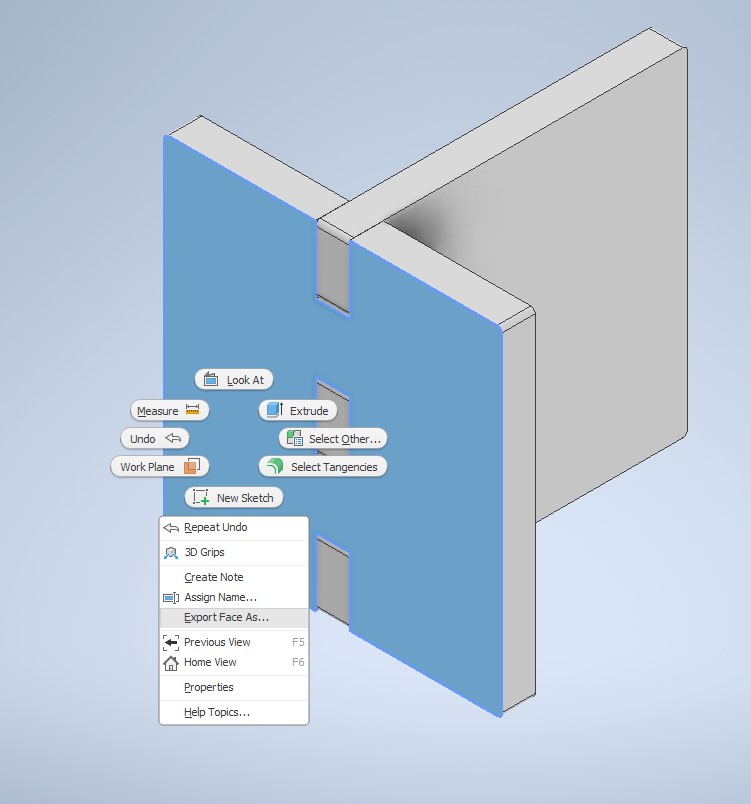
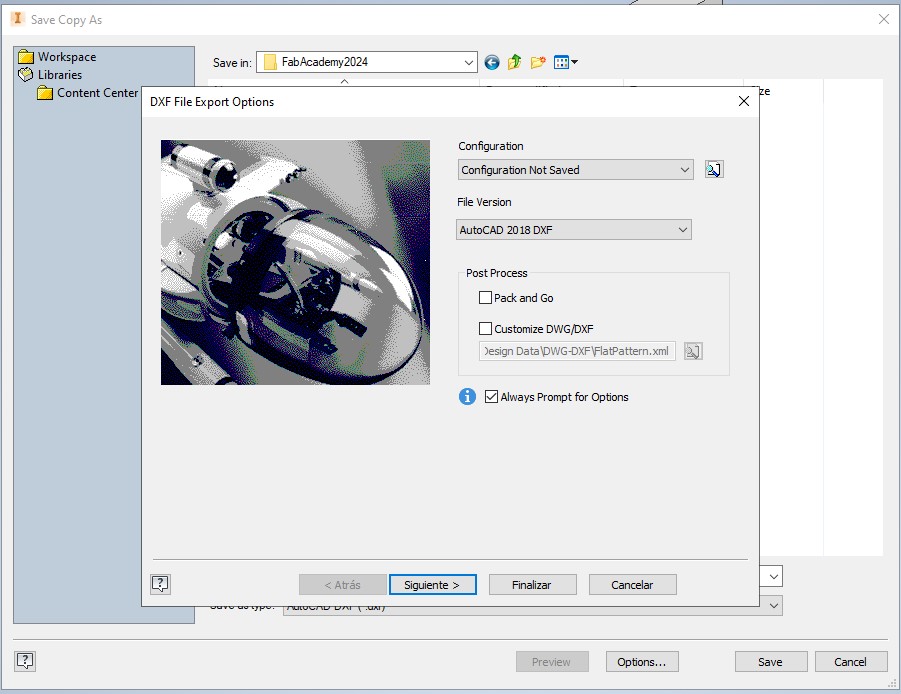
Following our initial tests, we focused on calculating the number, width, and spacing between milled slots required to bend the plywood into the calculated radius. This phase involved determining the precise parameters needed to leave a thin, flexible piece of plywood with appropriate spacing in the milled slots, ensuring it would bend according to the desired radius upon shaping. The implementation of these tests was successful, delivering precise results and highlighting the effectiveness of these designs, patterns, and optimized machining parameters in CNC routing applications.
Test Results:
Joints:
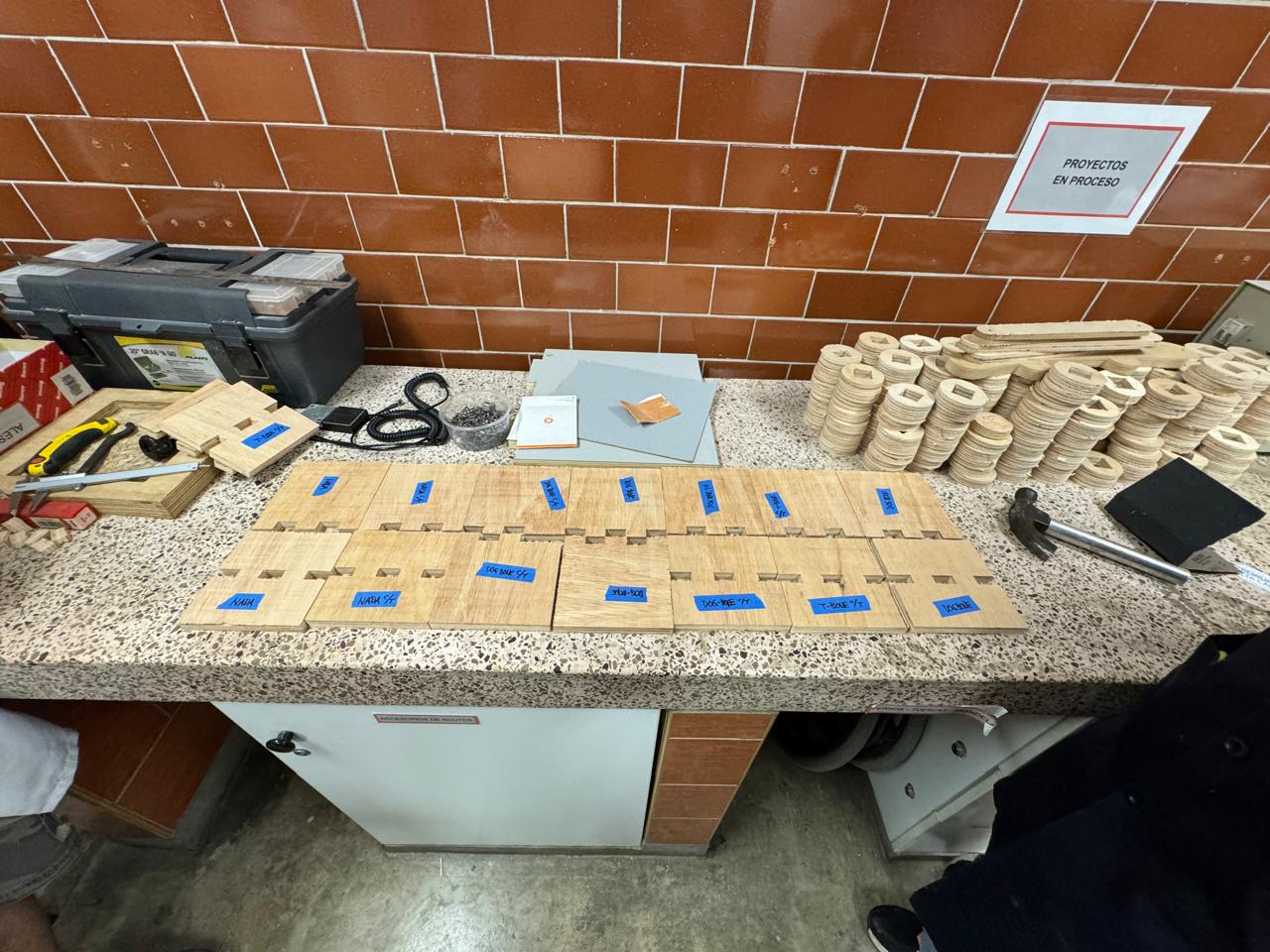
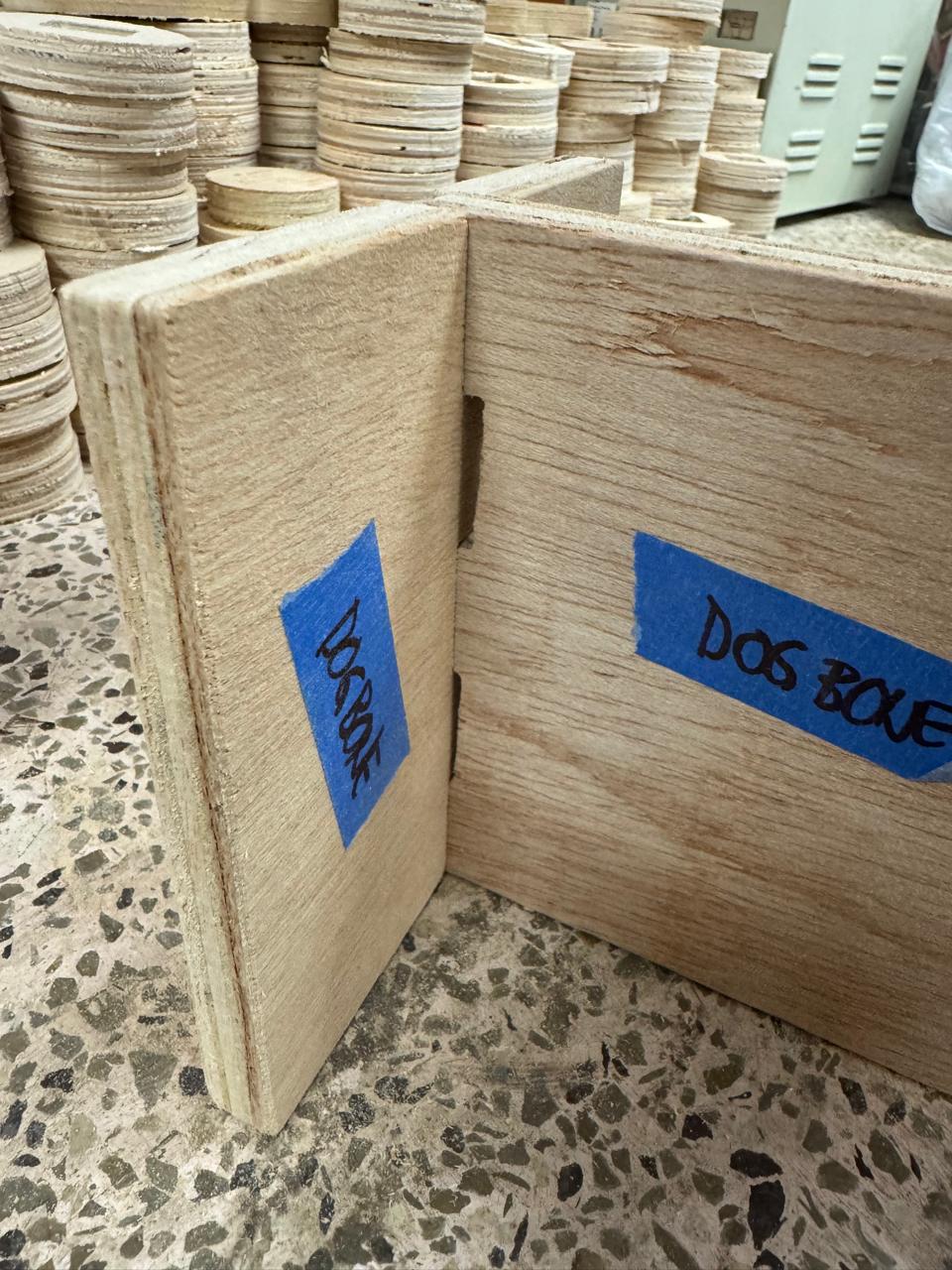
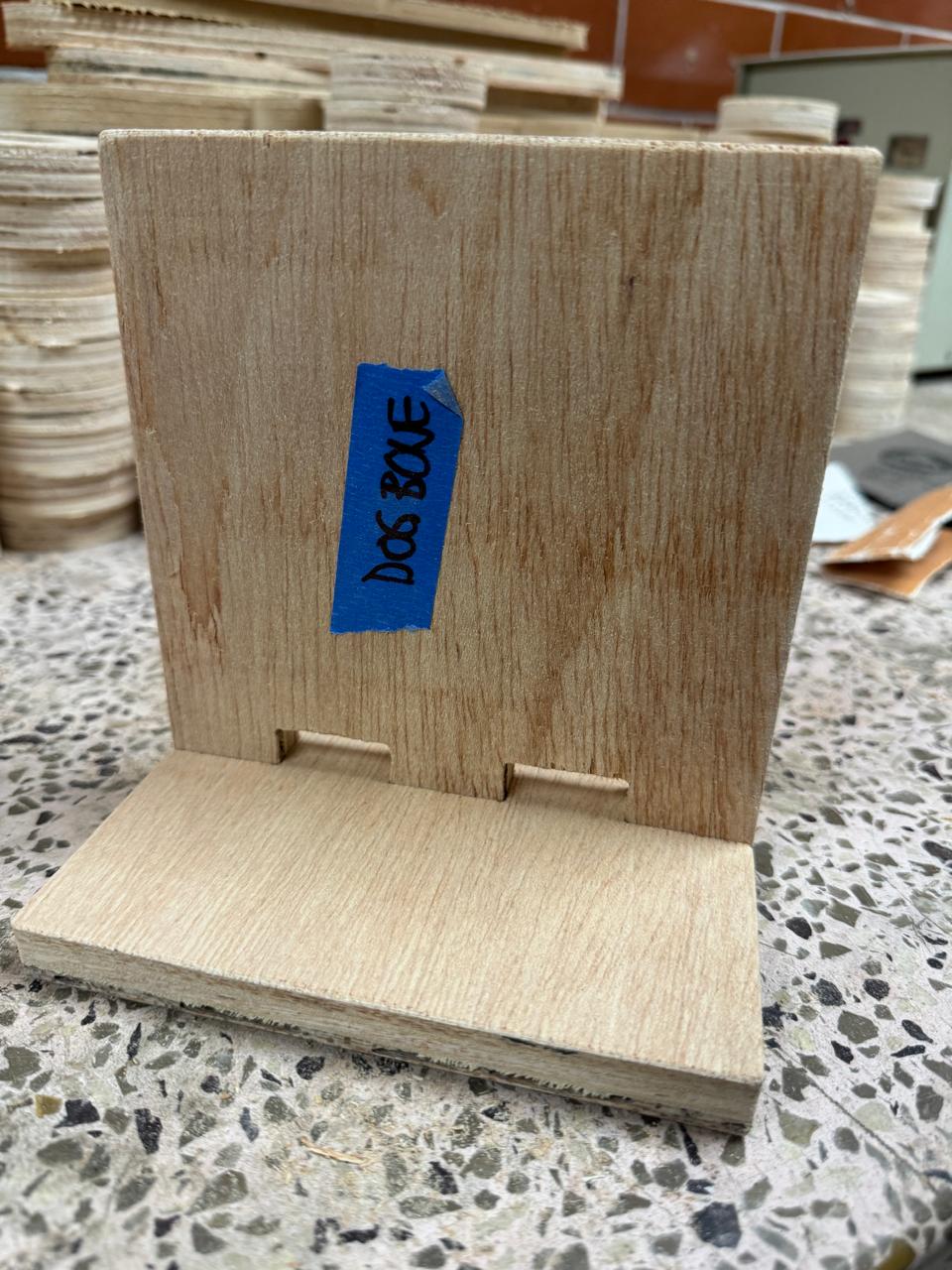
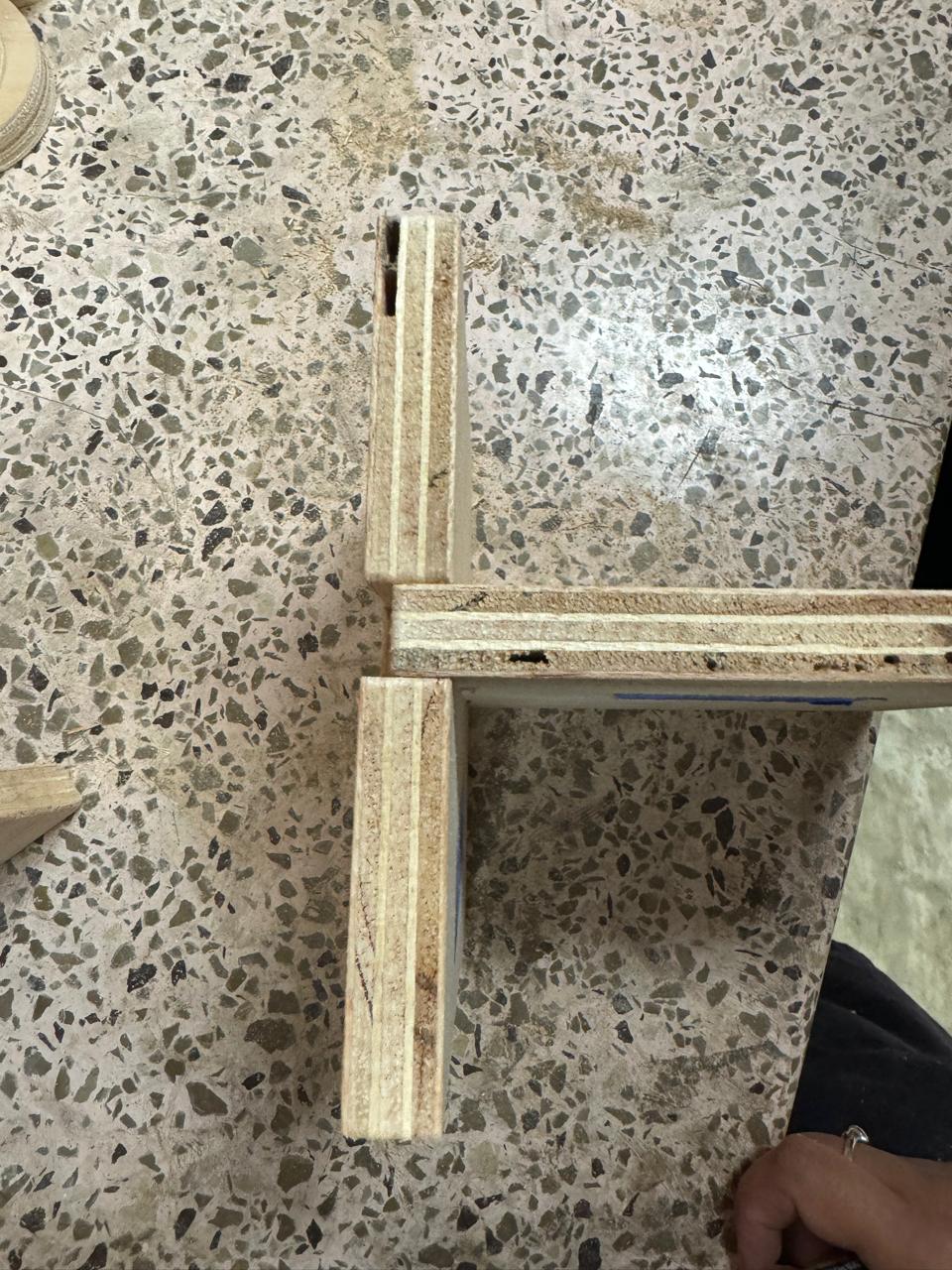
Flexible Pattern:
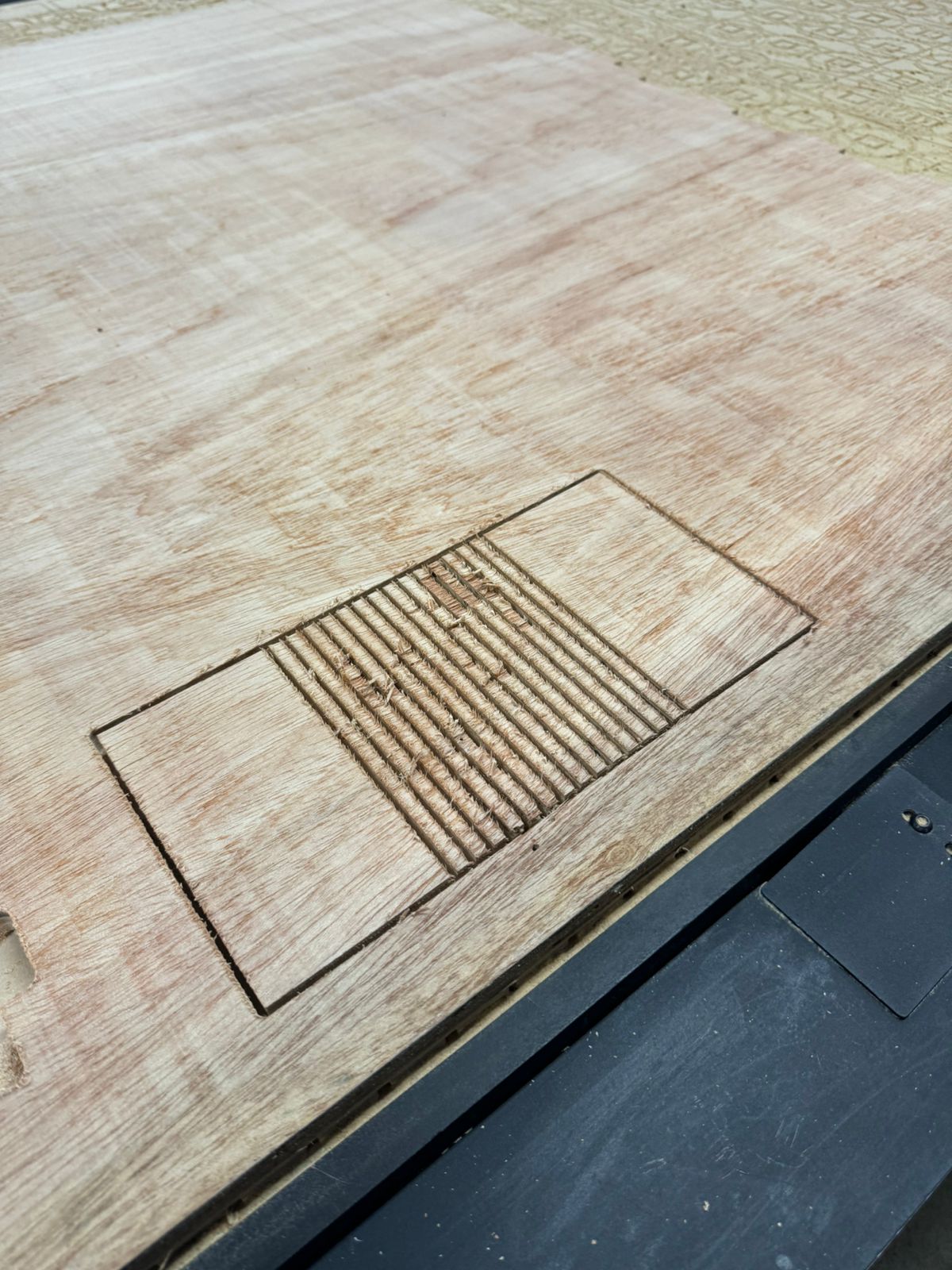
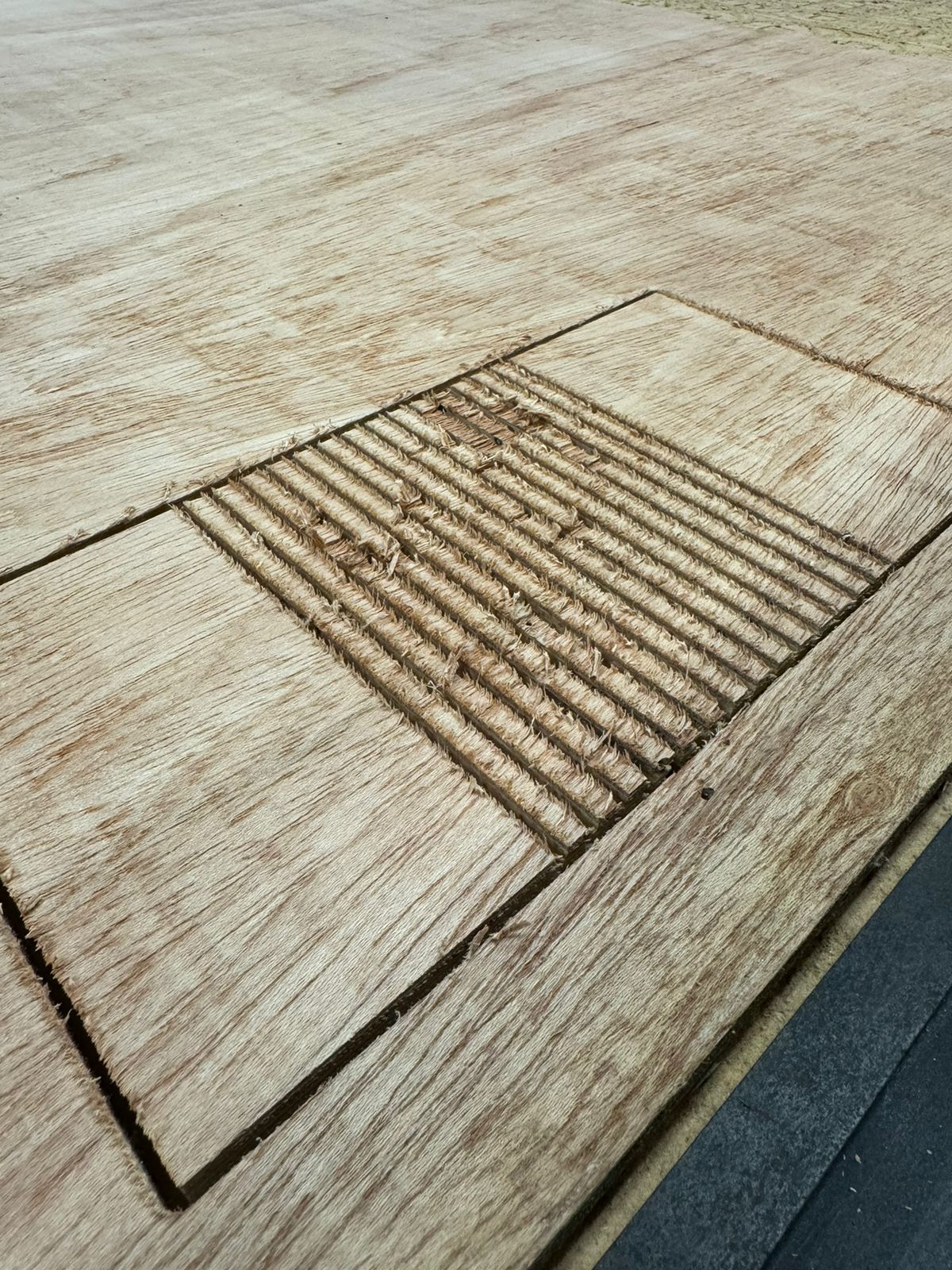
Flexing Test:
Cutting Parameters:
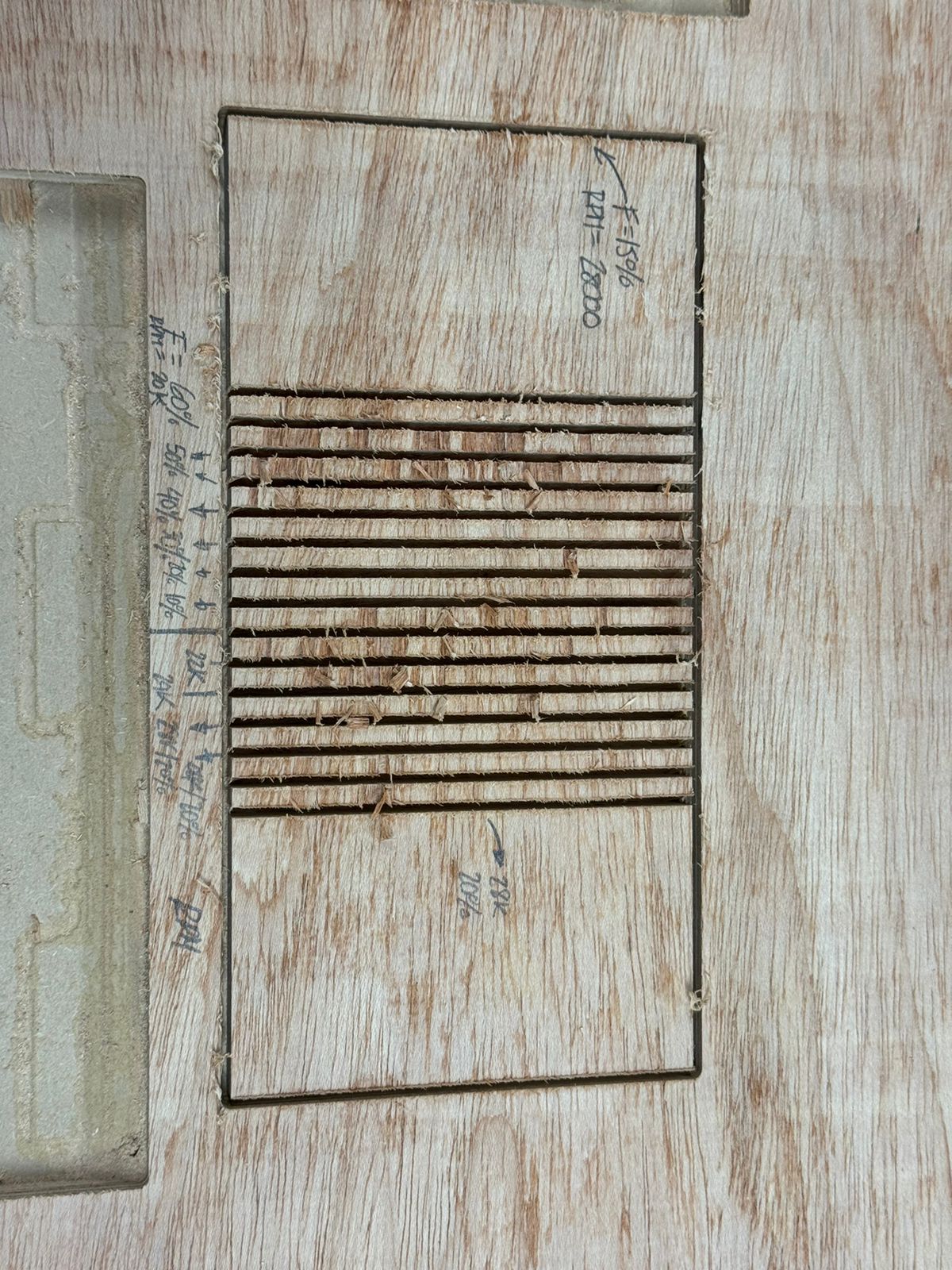
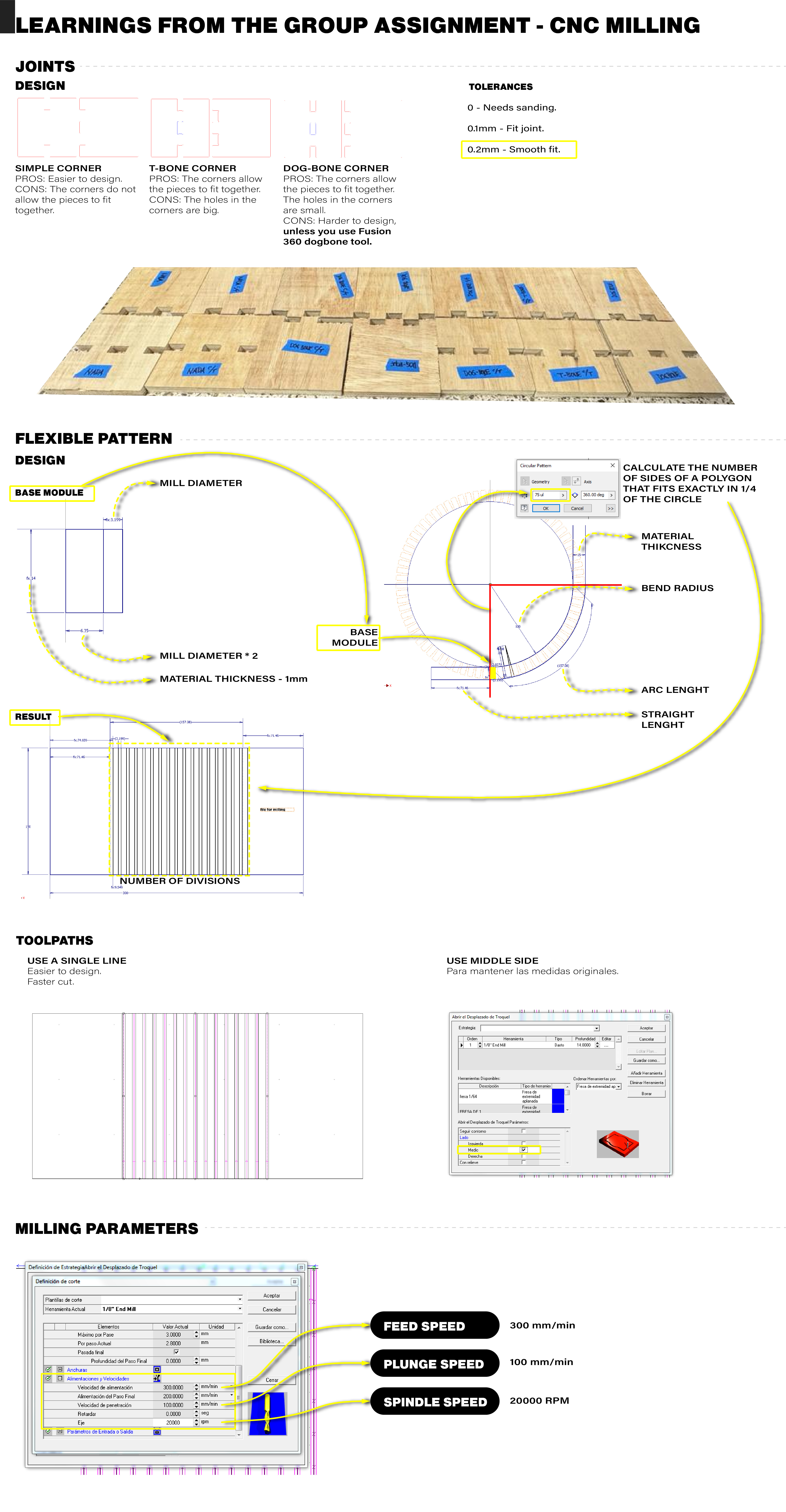