Assignments
- Review the safety data sheets for each of your molding and casting materials.
- Make and compare test casts with each of them.
- Compare printing vs milling molds.
Individual apport
- Ernesto: My contribution to the group project included testing different materials such as a composite made from plaster and cement, and experimenting with chocolate casting. Additionally, I used food-safe silicone RTV for molding.
- Jorge: I analyzed RTV PLATINUM 1510 Silicone Rubber, Mold Release Wax, Polyurethane Rubber, as well as castings such as Glycerin Soap with Chlorhexidine, Chocolate, and Ceramic Plaster.
- Marcela: My contribution to the group work was to review the datasheets of the materials and extract the most important points.
Process
Safety data sheets Moldings:
Product: RTV PLATINUM 1510 Silicone Rubber
- Manufacturer: Silika moldes e insumos
- Excellent Flexibility and Elongation
- Compatible with all addition-cure or platinum-cure silicones
- Color: SEMI-TRANSLUCENT
- Mixing Ratio: 1:1 by weight or VOLUME
- Working Time: 15-20 minutes
- Curing Time: 4-6 hours
- Medium Viscosity
- Does NOT require a catalyst
- Manufacturer: MEGATIENDAS
- Composition and Ingredients:
- CNot classified as hazardous according to Regulation (EC) No 1272/2008.
- May cause slight skin and eye irritation.
- May cause respiratory irritation if inhaled.
- Natural or synthetic waxes
- Petroleum distillates
- Additives
- Hazards Identification:
- In case of inhalation, remove to fresh air. If experiencing respiratory discomfort, seek medical attention.
- In case of eye contact, rinse cautiously with water for several minutes. Remove contact lenses if present and easy to do. Continue rinsing.
- n case of ingestion, rinse mouth. Do not induce vomiting. Seek medical attention if symptoms occur..
- Manufacturer: Silika Moldes e insumos
- Composition:
- Not classified as hazardous according to Regulation (EC) No 1272/2008
- calcium sulfate hemihydrate
- additives for setting and processing
- May cause slight skin and eye irritation.
- May cause respiratory irritation if inhaled.
- Polyurethane elastomer composed of diisocyanates and polyols
- Hazards Identification:
- Not classified as hazardous.
- Manufacturer: Glici
- Composition and Ingredients:
- Glycerin
- Chlorhexidine
- Hazards Identification:
- Eye Irritation: May cause moderate irritation upon contact with eyes
- Skin Sensitization: May cause allergic reactions in sensitive individuals.
- Acute Toxicity: Low risk of acute toxicity from accidental ingestion in small amounts.
- Manufacturer: Donofrio
- Composition and Ingredients:
- Cocoa Mass/Cocoa Solids
- Sugar
- Cocoa Butter
- Milk Solids
- Emulsifiers
- Flavorings
- Hazards Identification:
- Allergies: Chocolate contains ingredients such as milk, nuts, and soy, which can trigger allergies in susceptible individuals.
- Manufacturer: Martell
- Composition:
- Not classified as hazardous according to Regulation (EC) No 1272/2008
- calcium sulfate hemihydrate
- additives for setting and processing
- In case of inhalation, remove to fresh air. If experiencing respiratory discomfort, seek medical attention.
- In case of skin contact, wash off immediately with plenty of water.
- In case of eye contact, rinse cautiously with water for several minutes. Remove contact lenses if present and easy to do. Continue rinsing.
- Hazards Identification:
- Not classified as hazardous.
- For the group part we did different mold and casting tests
- Using SLA resin technology, we designed and manufactured the pieces for which we wanted to make the molds.
- We had already tested and tested this print in week 5: 3D printing, so we already knew that it had a much superior finish compared to other printing technologies.
- With these designs, we proceeded to generate the molds with food grade RTV silicone rubber.
- In addition, we use a wax as positive for making a mold to compare different experiments.
- After having the molds, we did several tests of different types of materials.
- This took us longer than expected because in some cases, such as the plaster, the finished piece broke because we thought it had already dried.
- Finally, we did the test with wax and the results were very similar to those obtained with molds made of SLA printed parts.
- Milling Wax: This method offers high precision and is suitable for creating detailed molds. Wax is an excellent material for achieving fine details. •
- SLA 3D Printing: SLA 3D printing provides high precision, capable of producing molds with extremely fine details, making it ideal for intricate and complex designs.
- Milling Wax: Produces a smooth surface finish with minimal post-processing required. The final product is typically smooth to the touch. •
- SLA 3D Printing: Produces a very smooth surface finish. Some minimal post-processing, such as cleaning the piece in a tank with alcohol and curing it with a powerful 405 nm ultraviolet light, is often needed.
- Milling Wax: Wax is a soft material that can be easily shaped and detailed but is prone to deformation under pressure and heat.
- SLA 3D Printing: The resin used in SLA printing is generally more durable than wax, offering greater resistance to deformation.
- Milling Wax: The cost is relatively low for both the wax material and the milling tools.
- SLA 3D Printing: Involves higher costs due to the price of the resin, the initial investment in an SLA printer, and additional equipment such as a cleaning tank and ultraviolet light curing chamber.
- Milling Wax: Speed decreases with the complexity and detail of the mold. Milling can be time-efficient for straightforward designs but becomes slower for highly detailed work.
- SLA 3D Printing: Slower production speed, especially when printing high-resolution models. The layer-by-layer process can take longer for detailed and complex designs.
- Milling Wax: Limited by the constraints of the subtractive process, which can restrict the complexity of the designs. However, wax's ease of milling allows for considerable detail.
- SLA 3D Printing: Highly flexible, allowing for the creation of complex geometries and intricate details that are difficult or impossible to achieve with milling.
- Milling Wax: Requires a milling machine, such as the Roland, and appropriate bits for the wax material.
- SLA 3D Printing: Requires an SLA 3D printer, compatible resin, a cleaning tank, and an ultraviolet light curing chamber.
- Milling Wax: Generates moderate waste due to the subtractive nature of milling, where excess material is removed to create the mold.
- SLA 3D Printing: Produces minimal waste, primarily from supports and excess resin. However, working with resin can be somewhat messy.
- Milling wax is cost-effective and suitable for creating detailed molds with high precision and a smooth surface finish, although it has limitations in design flexibility and material durability.
- SLA 3D printing offers greater precision and design flexibility in the shapes for making the mold, producing highly detailed molds but at a higher cost and with slower production speeds for complex designs.
Product: Mold Release Wax
Product: Polyurethane Rubber
Safety data sheets Castings:
Product: Glycerin Soap with Chlorhexidine
Product: Chocolate
Product: Ceramic Plaster
Make and compare test casts with each of them
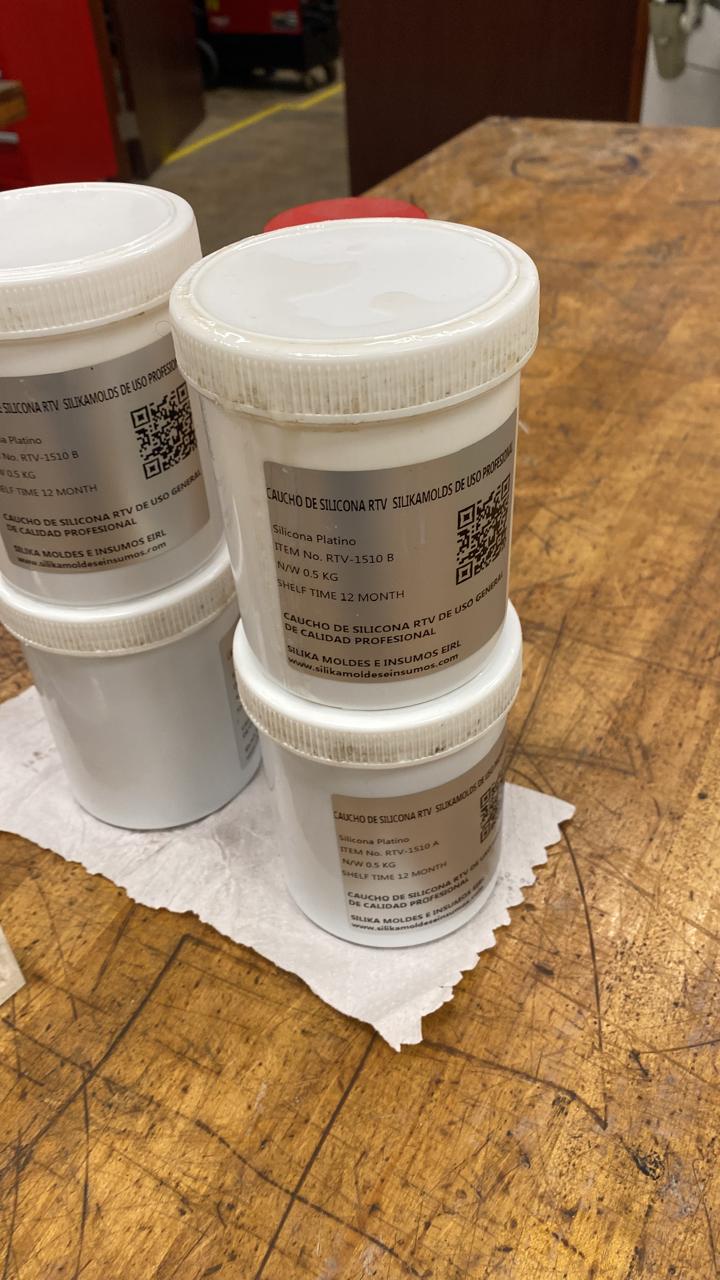
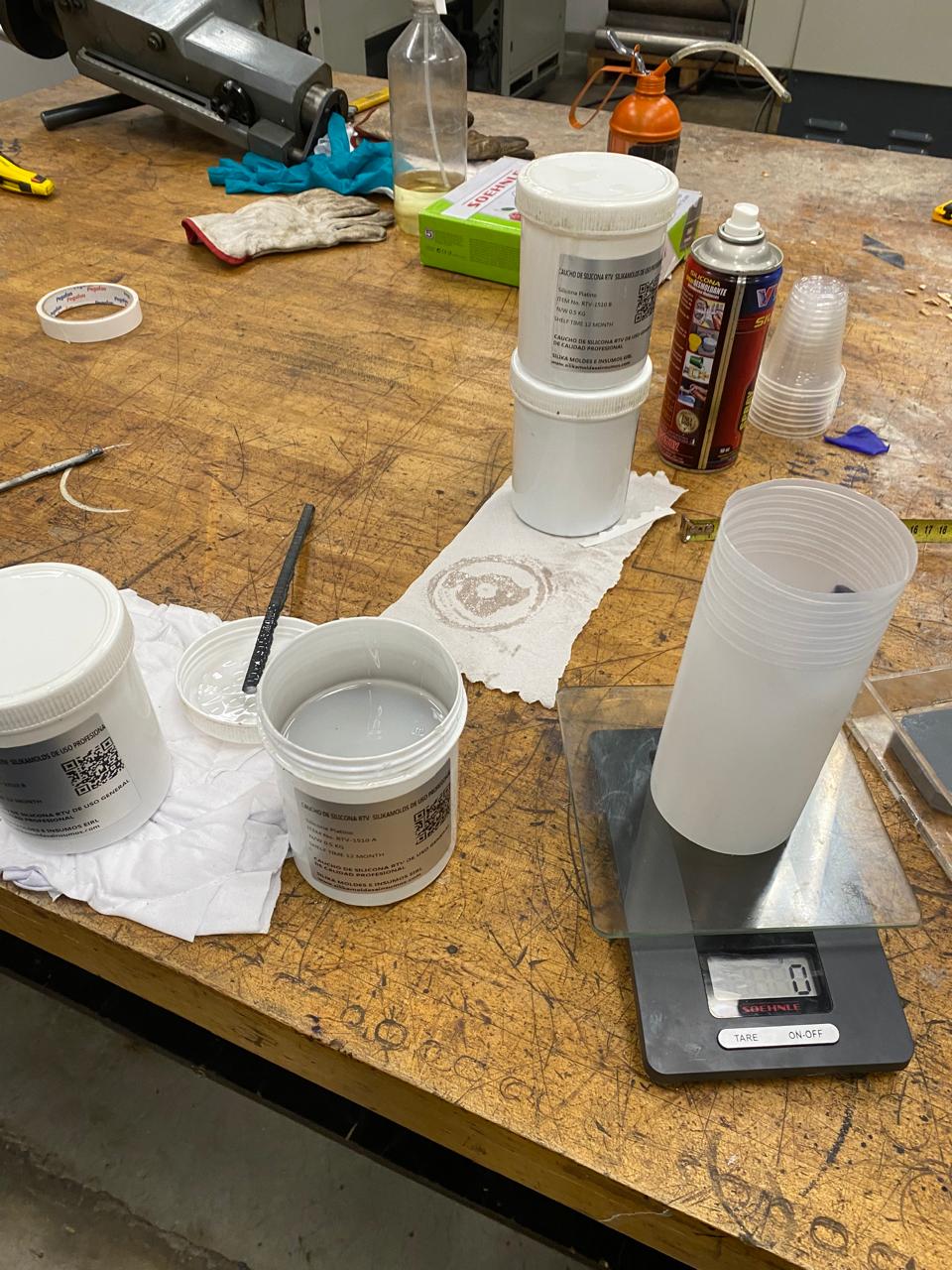
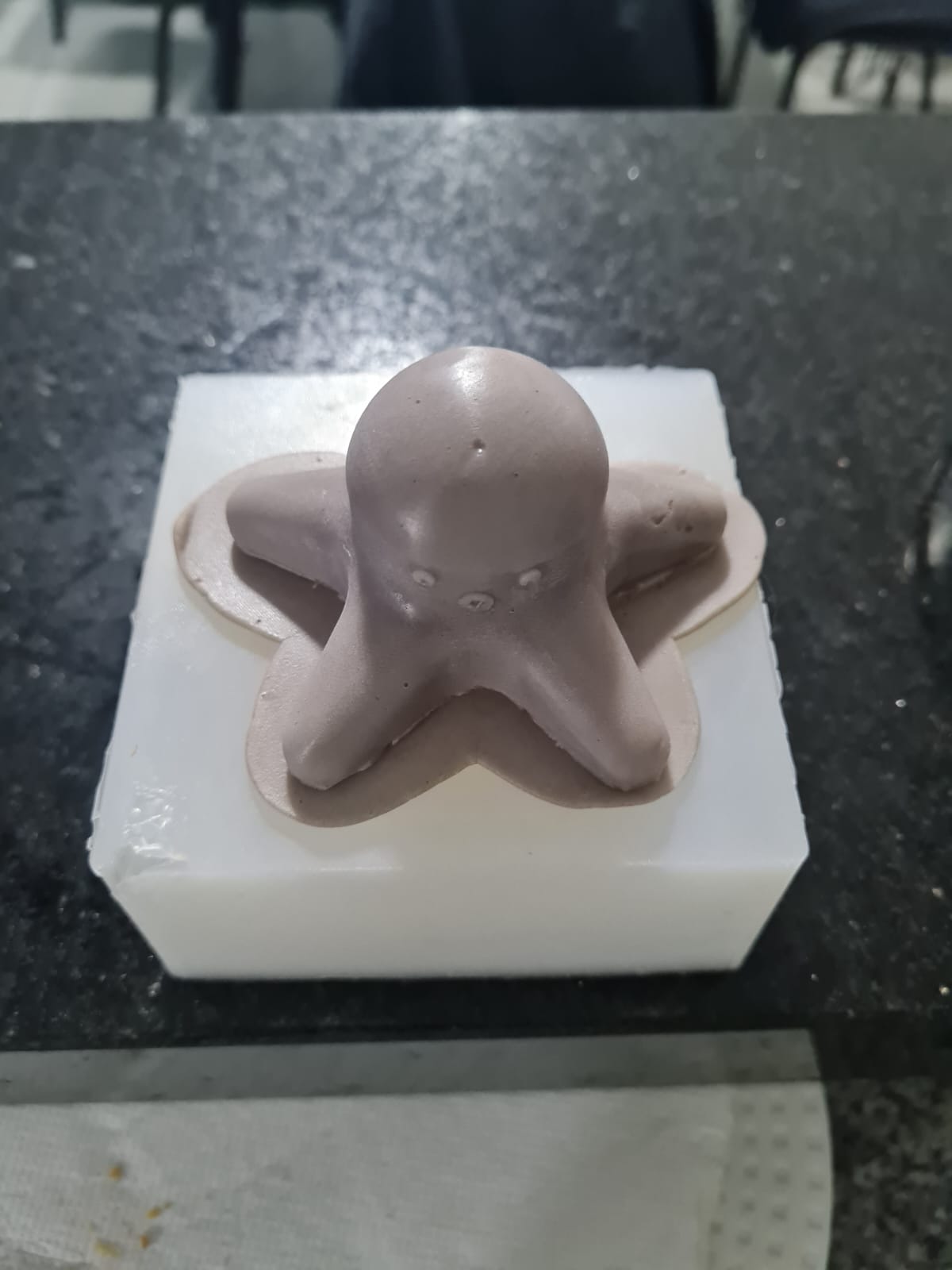
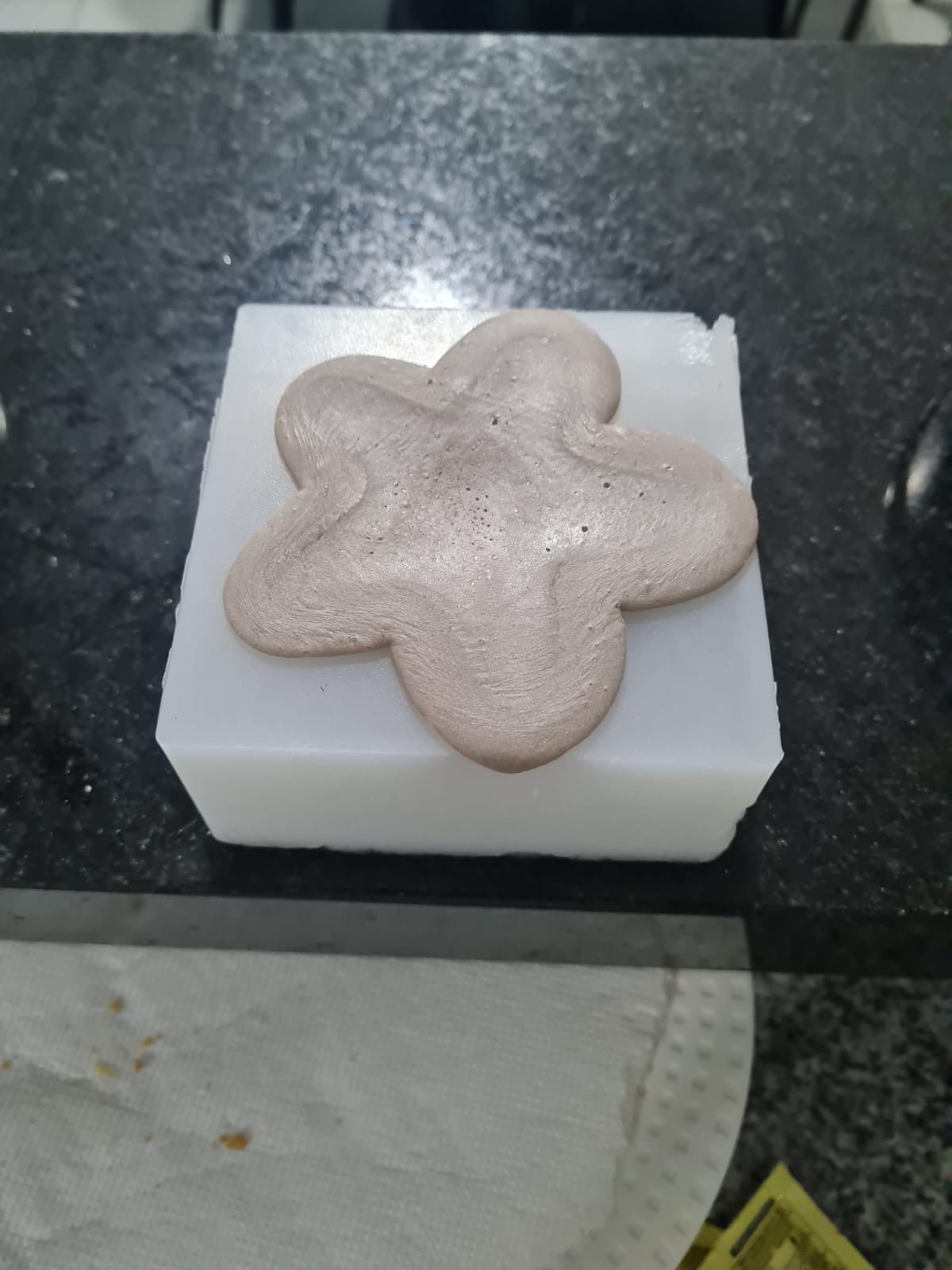
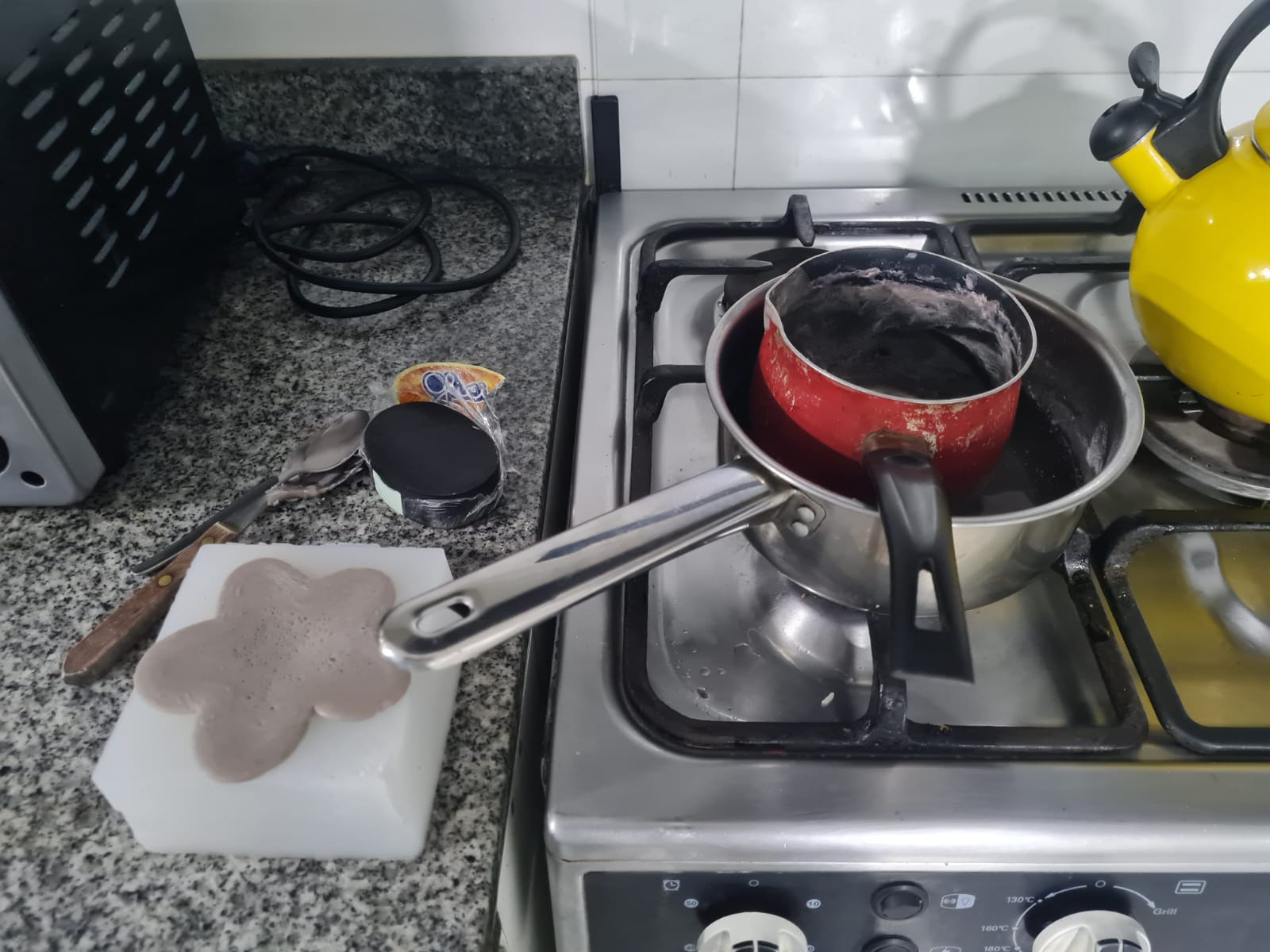
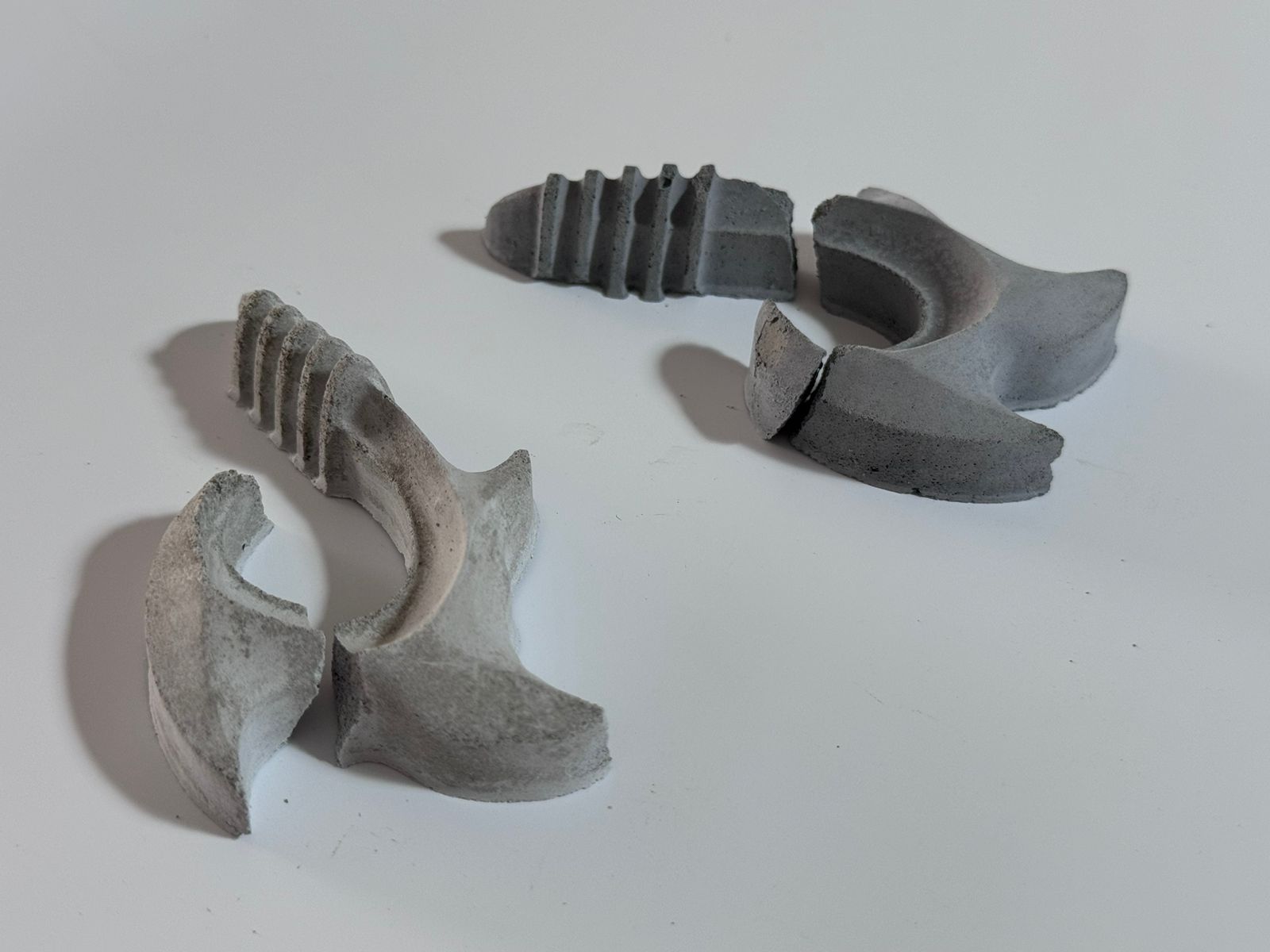
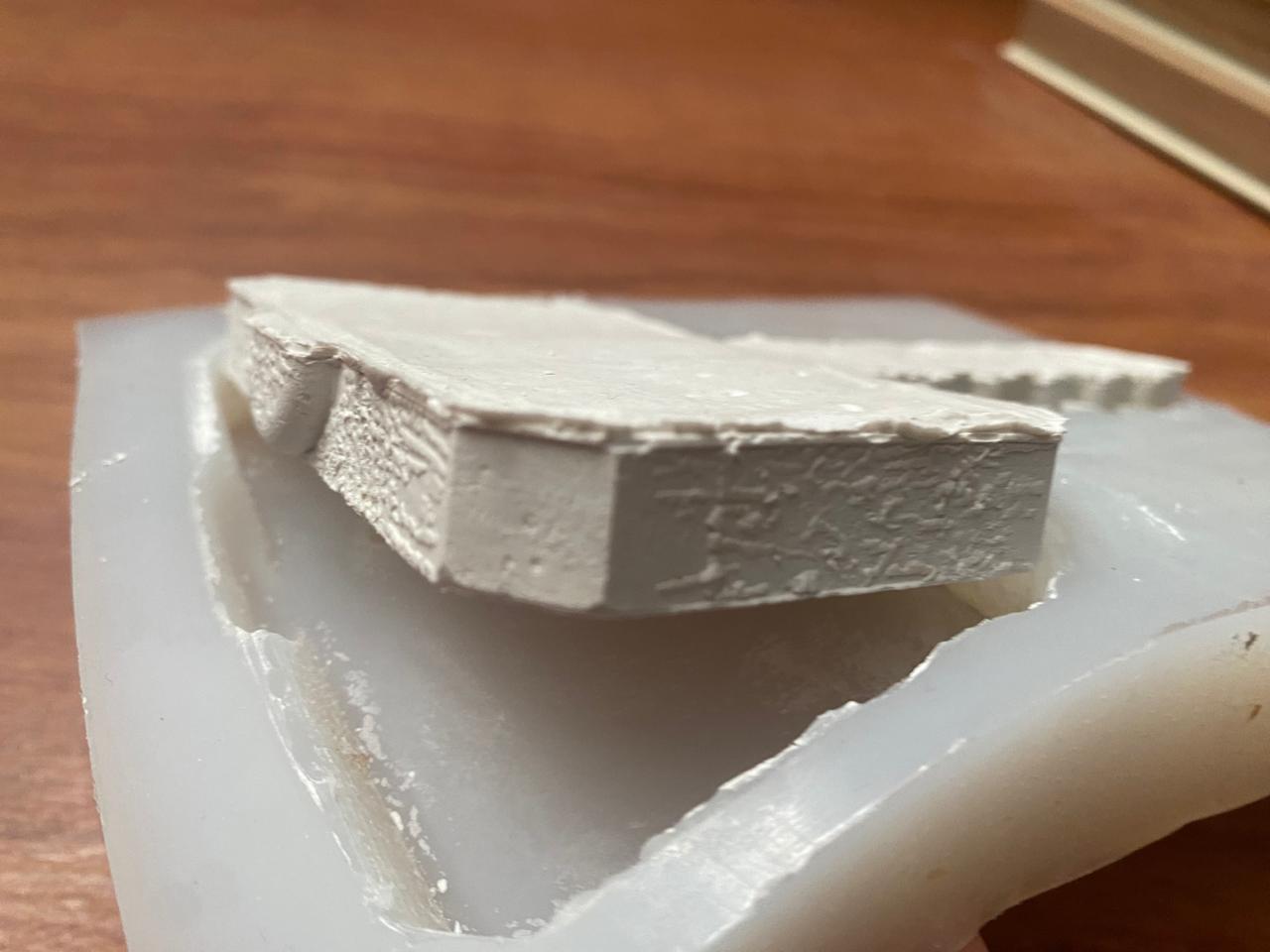
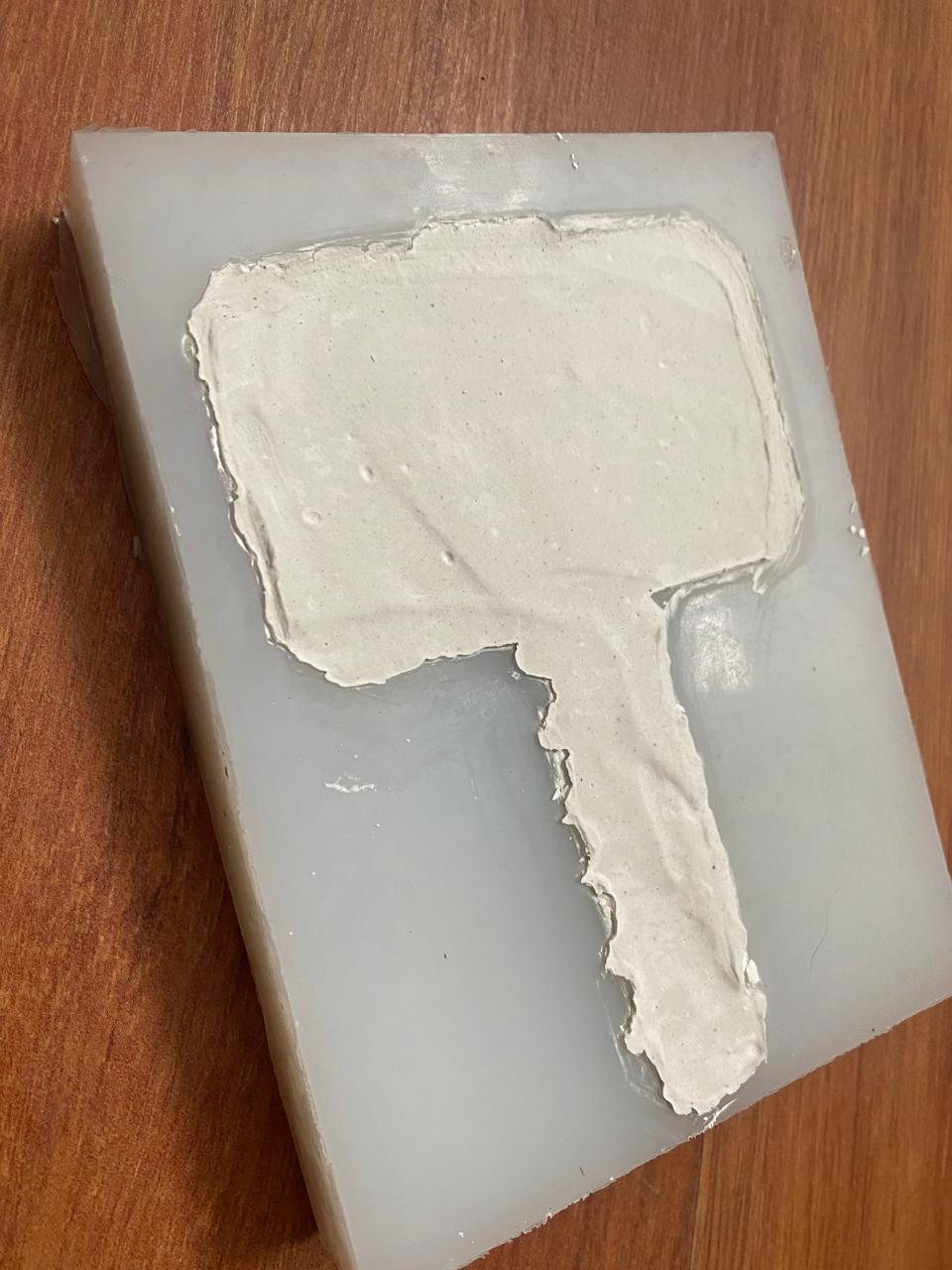
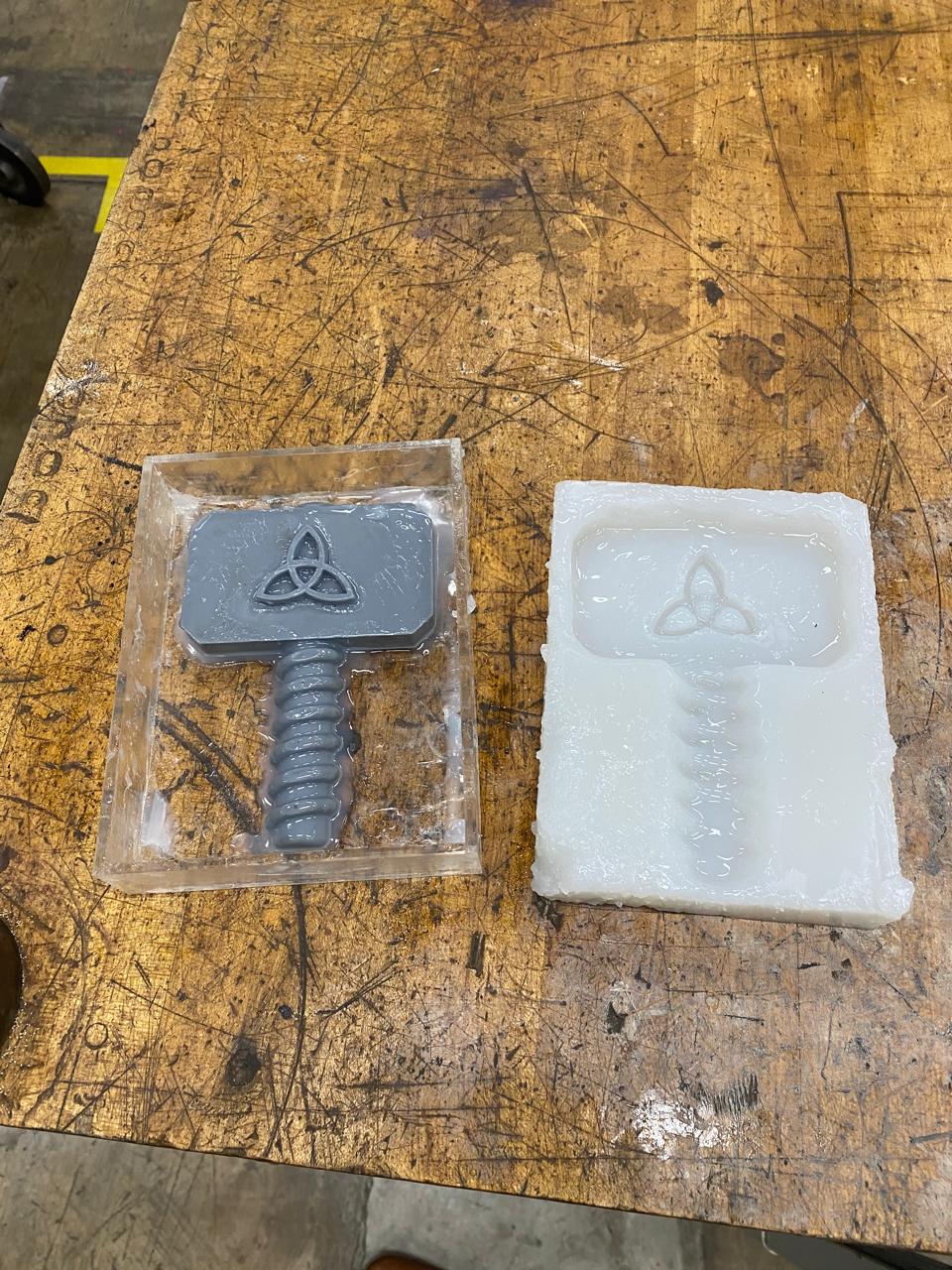
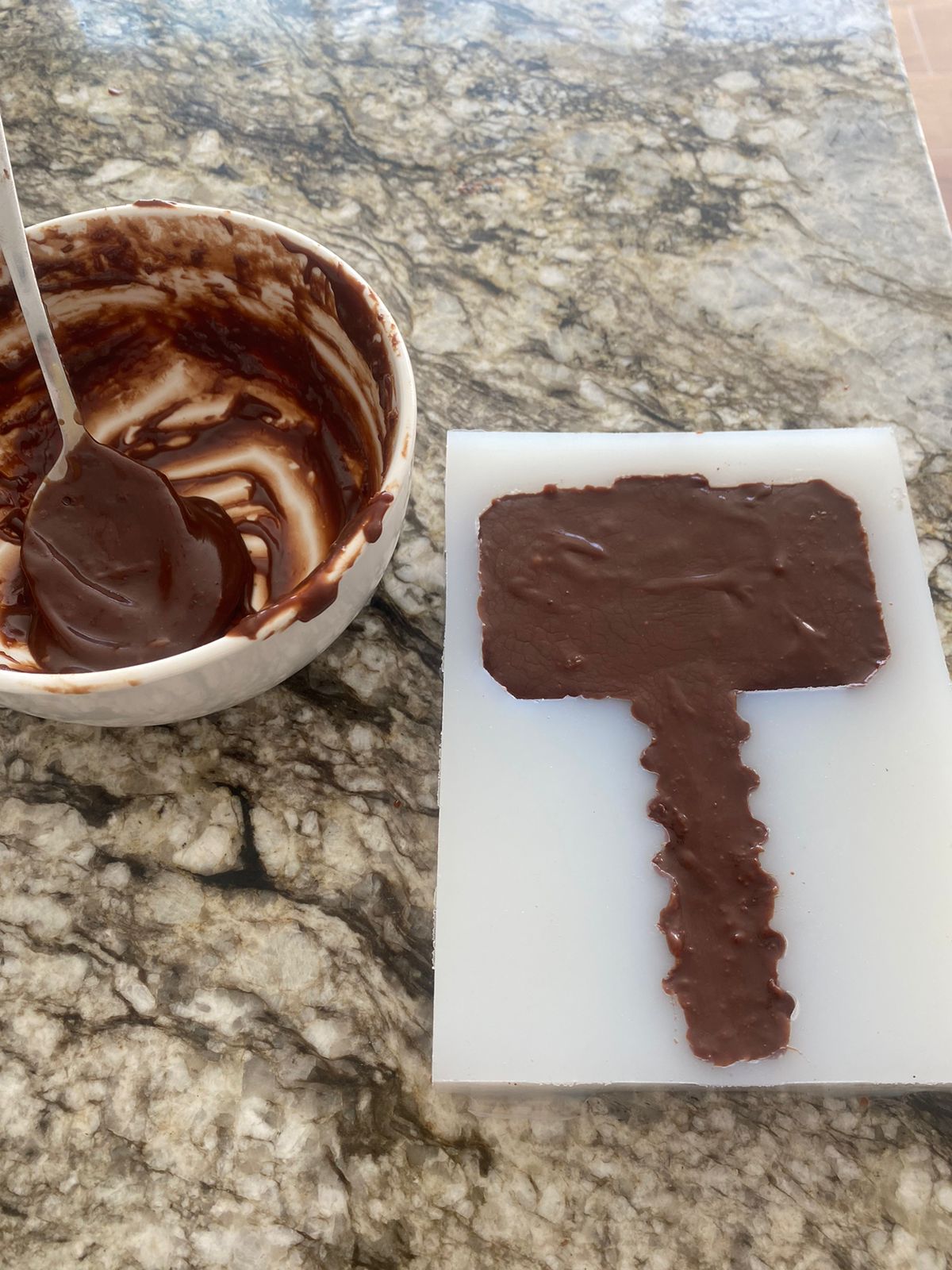
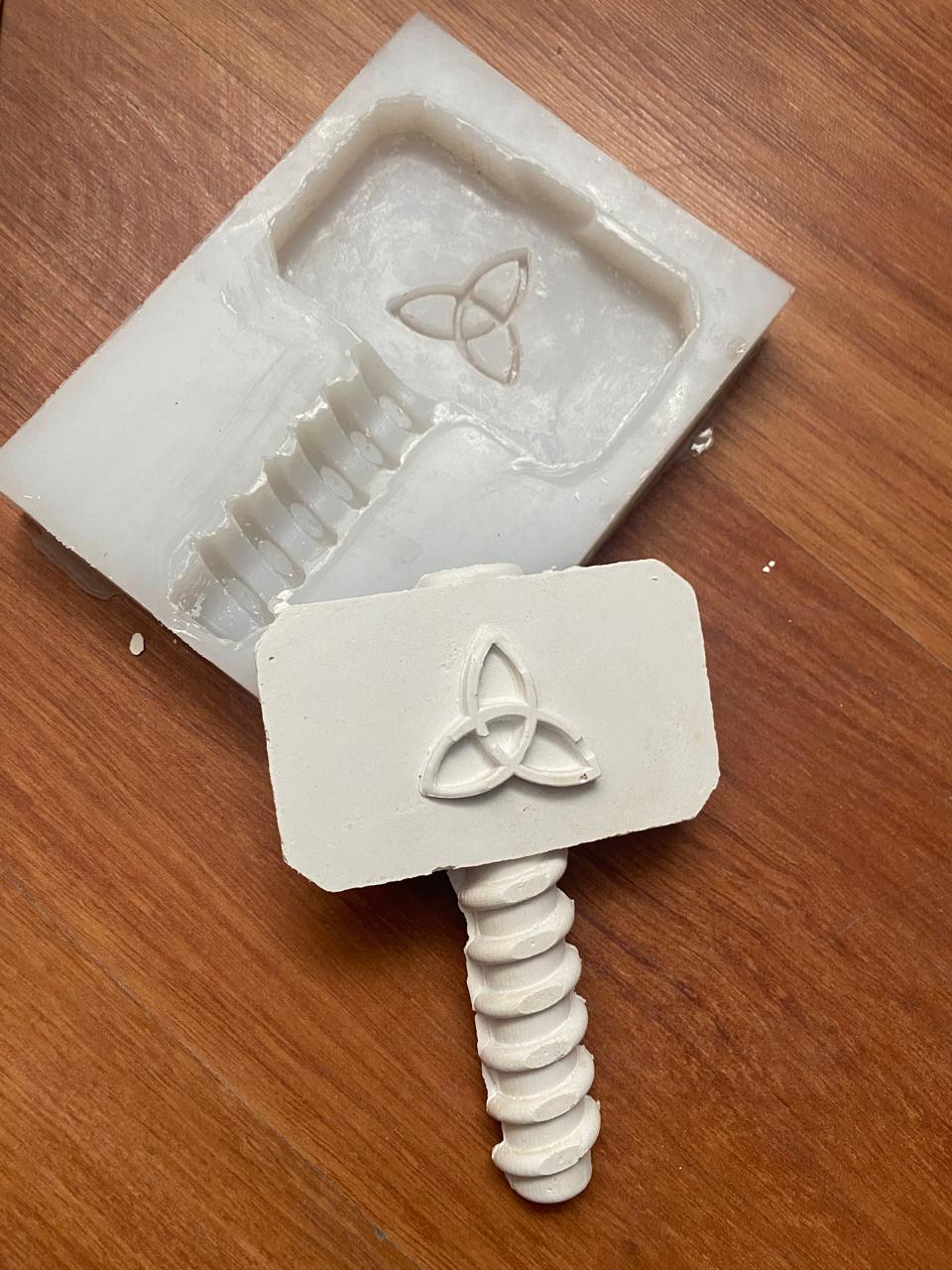
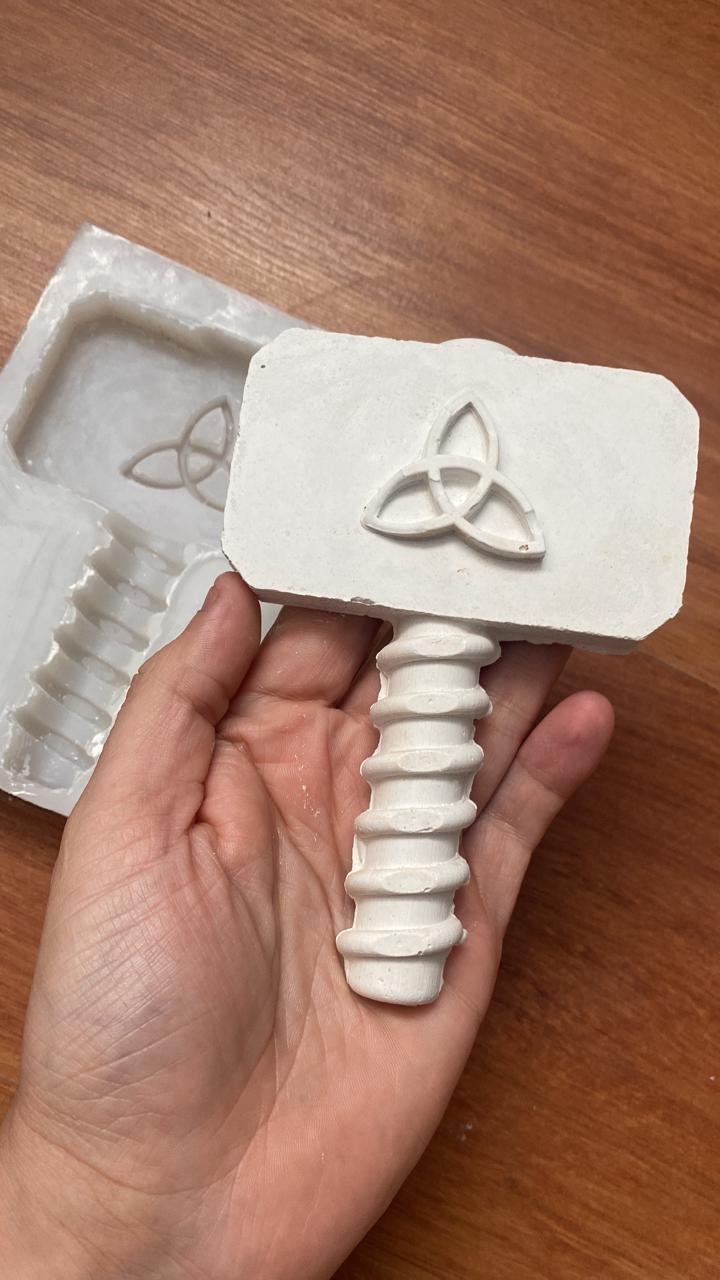
We used the RTV PLATINUM 1510 Silicone Rubber in 1kg presentations. This product was mixed in equal parts from container A and B. It is a Semi-Translucent and colorless Silicone Rubber in GEL and has a Shore hardness of 10-A.
It can also be used in the production of molds that require high resistance to acids, alkalis, high temperatures (250°C), and aggressive solvents. These are some technical characteristics that I found on the website of the company that sells the product:
Excellent Flexibility and Elongation
Compatible with all addition-cure or platinum-cure silicones
Color: SEMI-TRANSLUCENT
Mixing Ratio: 1:1 by weight or VOLUME
Working Time: 15-20 minutes
Curing Time: 4-6 hours
Available Packaging: 500g part A + 500g part B
Does NOT require a catalyst
Medium Viscosity
Shelf Life: 1 Year
Store Covered, in a Dry and Cool Place
The website where I acquired this information is from this: Caucho silicona RTV platino
These are all the products that the company "SILIKA modes e inputs" has for RTV Platinum Silicone Rubber.
On this website, we search for the product that says: Bi-component platinum silicone gel 1510.
Its translation is the following:
Semi-Translucent and Colorless Silicone GEL, with 10-A Hardness, Similar to MEDIUM Human Tissue, which allows it to be used in Reproduction of body parts, Prostheses, FX Makeup. Gore, Wound Reproduction, Living Tissue and all Types of Applications in Creating Special Effects. It can also be used in Molds in which Resistance to Acids, Alkalis, High Temperatures - up to 250 degrees C - Solvents and Aggressive agents is required, in addition to very high Flexibility and Elongation.
Its Semi-Translucent color allows it to be easily Pigmented with our Powder Base Pigments for Silicones.
Compatible with all our Addition Cure or Platinum Silicones
Color: SEMI-TRANSLUCENT
Mixing Ratio 1 to 1 by Weight or Volume
Working Time: 15 to 20 Minutes
Curing Time: 4 to 6 Hours (can be accelerated with heat) Presentation: 500gr Component A+ 500gr component B Exclusive Product and Imported in Peru by:
SILIKA MOLDS AND SUPPLIES EIRL
Specialists in Molds and Reproductions.
IMPORTANT!!
The silicone we use, which according to the manufacturer's specifications, is food grade, having been in contact with the 3D printing resin, it loses its food properties and is NOT suitable for making food molds. In our tests, the chocolate casting was only demonstrative and not edible.
In addition to this, when we cast plaster with cement, the silicone also loses its food grade, since having been in contact with non-edible elements, it is contaminated and completely discarded for another casting of edible foods.
Comparison: Milling Wax vs. SLA 3D Printing for Mold Making
Here is our comparison between manufacturing a mold by milling a block of wax and using SLA 3D printing.