13. Molding and Casting
This week's main objective is to design a mold around the process you'll be using, produce it with a smooth surface finish, and use it to cast parts.
Research
The group assignment of this week you can found it here.
This week, I will engage in the design and construction of a soft robot actuator, which will consist of a manipulator hand.
Soft robotics is an emerging subfield of robotics, that seeks to replace traditional and rigid robotic components with flexible sensors and actuators that achieve greater flexibility and degrees of freedom. Conventional industrial robots demonstrate excellent performance in environments for which they are designed but are not sufficiently adaptable to work in unknown or changing environments where unexpected situations can arise. In the future, robots will be required to respond flexibly to unpredictable environments and possess characteristics such as precise positioning and high output. This is where soft robots are introduced. The concept of “soft” includes not only a soft body in a physical sense but also soft movement and the ability to respond flexibly to any situation.
Conventional robotics has been built on the assumption that the physical characteristics of a robot do not change; however, in soft robotics, the shape, dimensions, and mass distribution of the robot's body change when external forces are applied. In addition, soft robots may be deliberately fabricated using materials with properties that change over time or are affected by temperature.
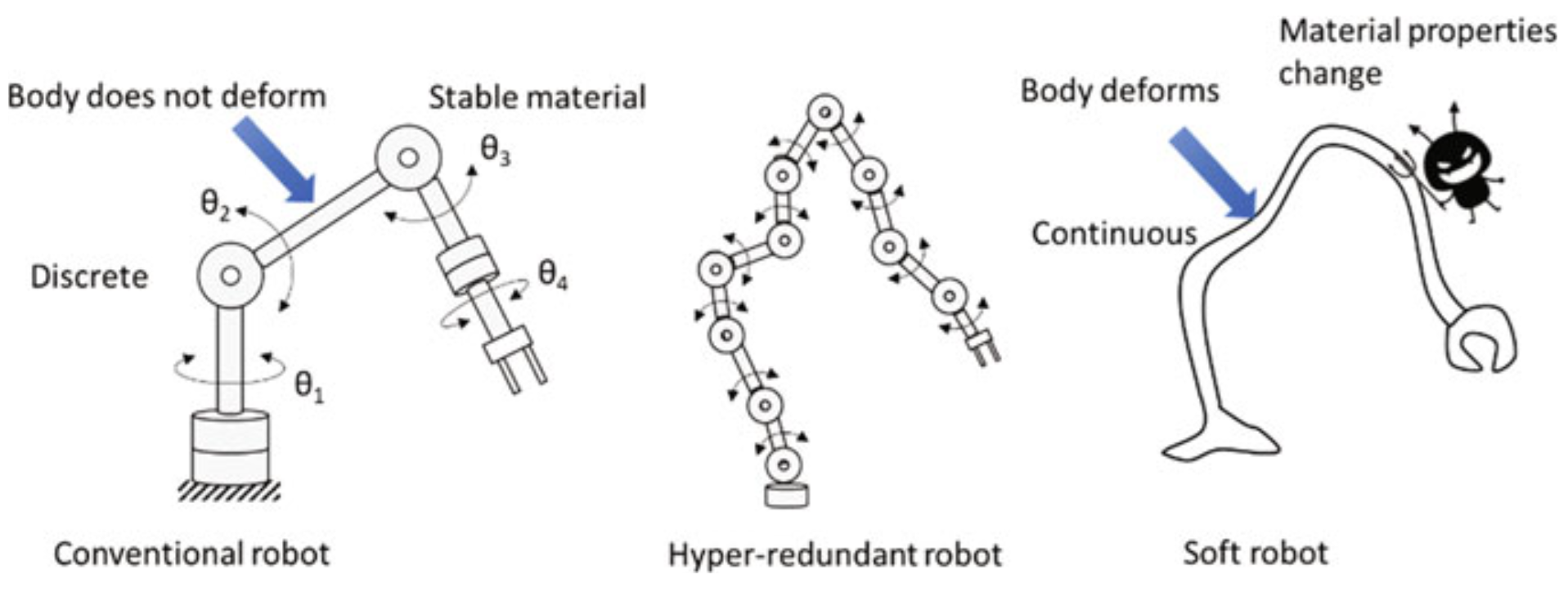
Robots configuration
Image taken from: Suzumori, K., Fukuda, K., Niiyama, R., & Nakajima, K. (Eds.). (2023). The Science of Soft Robots: Design, Materials and Information Processing. Springer Nature. https://doi.org/10.1007/978-981-19-5174-9
Soft mechanisms are of critical importance in the development of soft robots, enabling them to adapt to dynamic environments and collaborate safely with humans. These mechanisms are inspired by biomechanics and offer a number of advantages, including the ability to manipulate delicate objects without damaging them, impact resistance, and the flexibility to navigate through tight spaces. Furthermore, soft robots equipped with gentle mechanisms have significant potential in fields such as medicine, space exploration and disaster relief.
Pneumatic soft robots represent a revolutionary innovation in the field of robotics, representing a paradigm shift from rigid to soft robots. Using air or liquid to control their movements, these robots offer significant advantages over traditional rigid robots, such as adaptability to complex environments and safe interaction with humans. Their versatility allows them to perform tasks that would be impossible for rigid robots, making them an exciting and promising tool for the future of robotics, with applications spanning a wide range of fields.
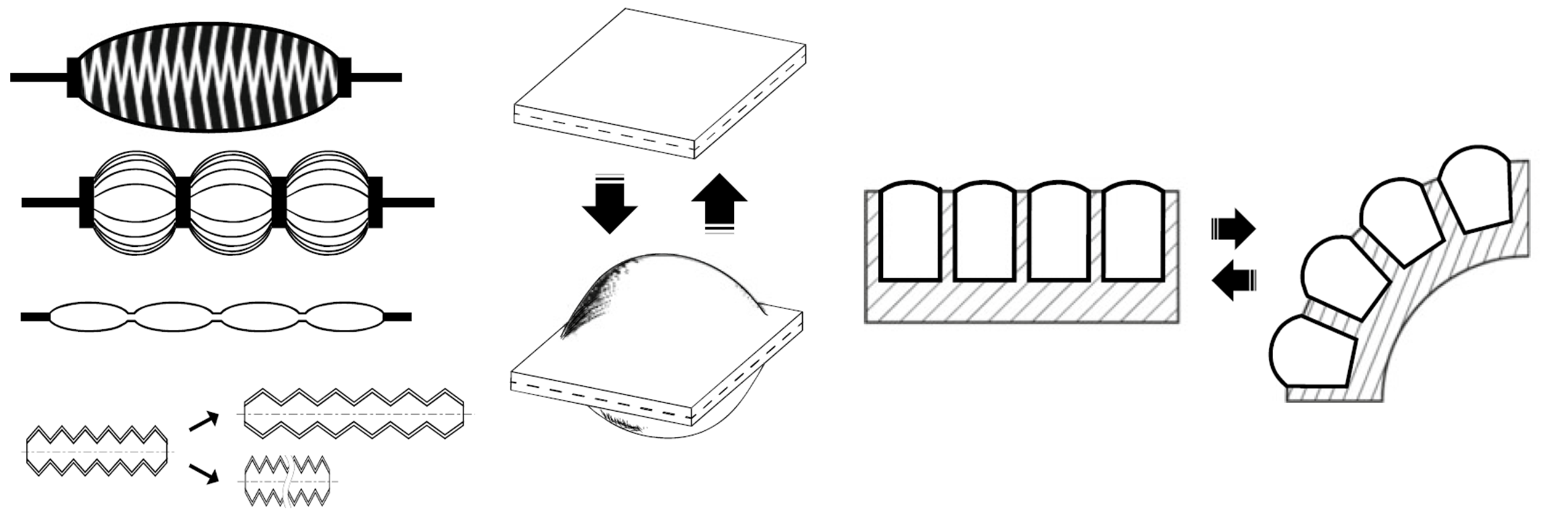
Examples of pneumatic Soft Mechanisms
Image taken from: Suzumori, K., Fukuda, K., Niiyama, R., & Nakajima, K. (Eds.). (2023). The Science of Soft Robots: Design, Materials and Information Processing. Springer Nature. https://doi.org/10.1007/978-981-19-5174-9
Polymers play a critical role in the construction of soft robots due to their distinctive properties and versatility. These materials offer a diverse range of applications in the field of soft robotics, enabling the creation of complex shapes and facilitating the necessary flexibility for motion and interaction with the surrounding environment. Elastomers, for instance, are utilized to develop soft actuators that replicate the natural motions observed in nature. Additionally, hydrogels are employed to impart responsiveness and adaptability to external stimuli. Furthermore, polymers facilitate the fabrication of lightweight and robust components, which is of paramount importance for the development of efficient and functional soft robots in a multitude of applications, including medicine, space exploration, and manufacturing.
Three-dimensional (3D) printers have been used to fabricate soft robotic parts for almost a decade. They have advantages over traditional machining like the ability to print complex shapes with low material waste. 3D printing is preferred for making soft parts that won't injure people if an accident occurs.
The design data from 3D printers can be used directly, while casting requires converting the data to a mold first. Open-source CAD software is sufficient for academic and small businesses to design 3D models in STL format, which slicing software uses to generate printer instructions. Setting the correct nozzle speed, material flow, and layer distance is important for soft materials since print quality varies significantly with these parameters.
Different 3D printing methods are used depending on the material and deposition technique. Inkjet methods spray photocurable resin from a print head, curing each layer with UV before depositing the next. Unlike other methods, support material is dissolved away after printing. Rubber-like materials from Shore 90-30 hardness can be used.
Fused deposition modeling (FDM) draws molten material in layers. It's widely used with polylactic acid (PLA) filament. The printer design impacts suitability for soft materials - Bowden extruders risk buckling while direct drive works for softer items but not below Shore 60 hardness. Complex shapes and pneumatic parts can't be reliably printed.
Stereolithography (SLA) cures liquid resin layer-by-layer with a laser or projector. Support structures are needed but limit overhangs and interior cavities. Flexible resins are available but larger or oddly-shaped parts may distort during lifting. Bind jet methods use inkjet heads to selectively bond powder layers.
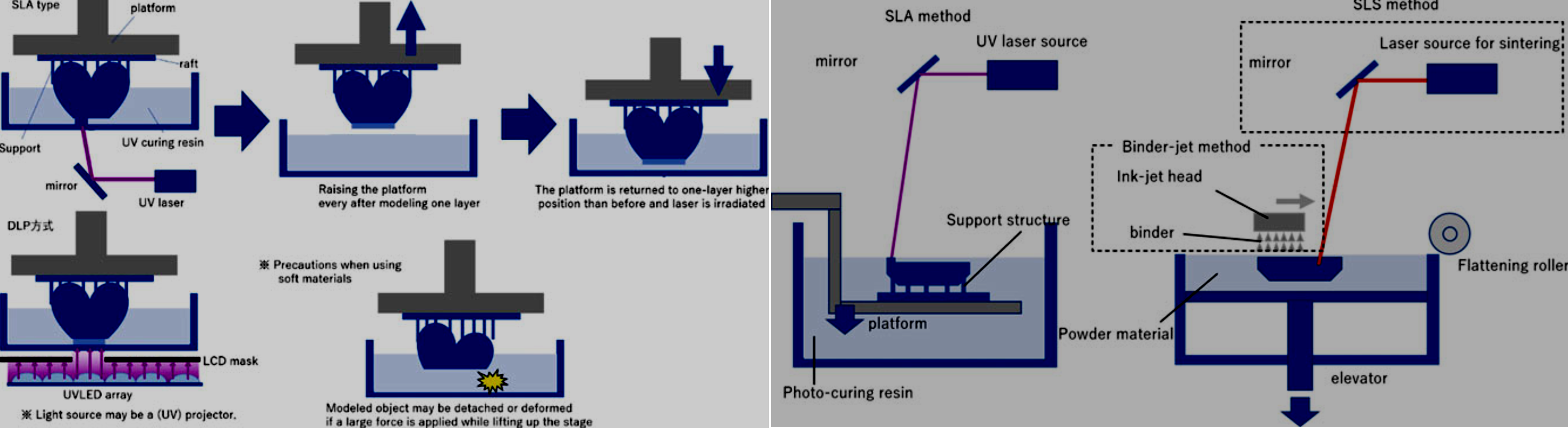
Illustration of the printing principle of materials used to build Soft Robots.
Image taken from: Suzumori, K., Fukuda, K., Niiyama, R., & Nakajima, K. (Eds.). (2023). The Science of Soft Robots: Design, Materials and Information Processing. Springer Nature. https://doi.org/10.1007/978-981-19-5174-9
Fluidic soft actuators are a common component of soft robots, as they are capable of generating smooth forces and movements. These actuators leverage the properties of fluids, such as air or liquids, to achieve the necessary flexibility and compliance.
A fundamental understanding of fluid mechanics is a prerequisite for the design and operation of fluid soft actuators, although in some instances, a more advanced grasp of this subject matter may be necessary.
To begin, it is necessary to define the concept of pressure. Pressure is defined as the force applied perpendicularly to the surface of an object per unit area:
\( P = \frac{dF}{dA} \)
The unit of measurement in the International System of Units (SI) is the pascal (Pa). In incompressible fluids in a steady state, Pascal's Law is observed, which states that the pressure in a fluid is transmitted in equal value in all directions under the conditions described above.
Another crucial variable to be considered is the fluid flow rate. The flow rate is defined as the volume of fluid passing through a given surface per unit of time.
\( Q = \frac{dV}{dt} \)
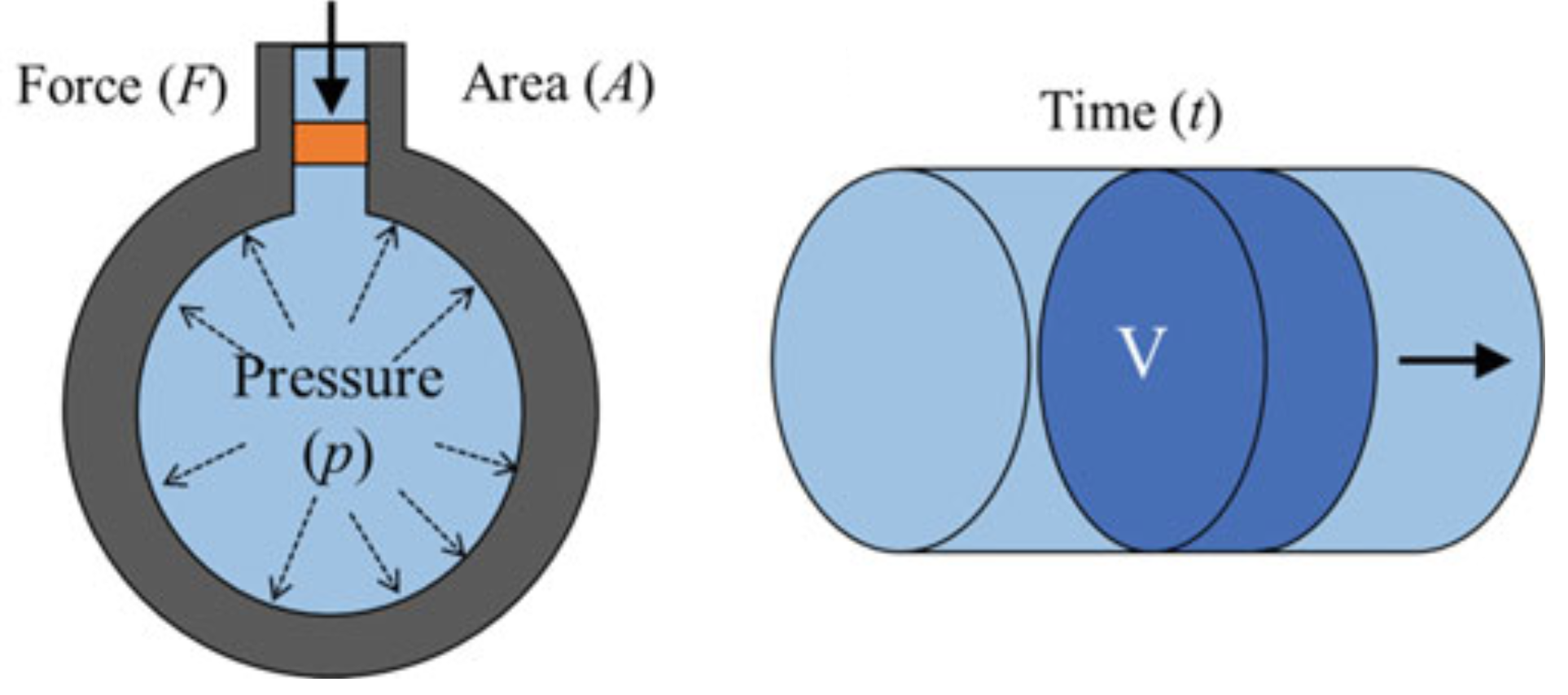
Schematics demonstrating a Pascal's law and b the volumetric flow rate
Image taken from: Suzumori, K., Fukuda, K., Niiyama, R., & Nakajima, K. (Eds.). (2023). The Science of Soft Robots: Design, Materials and Information Processing. Springer Nature. https://doi.org/10.1007/978-981-19-5174-9
In order to comprehend the operation of laminar incompressible fluids in a steady state, it is essential to be acquainted with Bernoulli's principle. This principle states that in a frictionless fluid flow, the sum of static pressure, dynamic pressure and potential energy per unit volume is constant along a fluid stream.
\( \frac{P}{g\rho} + \frac{v^2}{2g} + z = const.\)
It should be noted that the symbols \(\rho\), g, v and z represent the density, gravity acceleration, fluid velocity and elevation, respectively.
To calculate the pressure and flow rate of a fluid under complex conditions, the Navier-Stokes equations may be employed, which describe the motion of viscous fluids. The Navier-Stokes equations express mathematically the conservation of both momentum and mass for Newtonian fluids, in accordance with the laws of conservation.
\( \frac{D\mu}{Dt} = \frac{1}{\rho}\nabla·\sigma + f \)
The variables \(\mu\), t, \(\rho\), \(\sigma\), and f represent the flow velocity, time, density, stress tensor, and body forces, respectively; D\(\mu\)/Dt and \(\nabla\)·\(\sigma\) are the material derivative of \(\mu\) and the divergence of the stress tensor, respectively.
Materials
Polymers are employed extensively in the fabrication of actuators for soft robots due to their malleability, resilience, and responsiveness to external stimuli, such as temperature changes, pH fluctuations, and electrical stimuli. This renders them optimal for soft robotics applications where adaptability and strength are paramount. Furthermore, their capacity to be shaped and processed in diverse ways enables the fabrication of bespoke actuators for diverse soft robotics applications.
In fulfillment of the weekly assignment, two polymers were subjected to testing in order to ascertain their suitability for the construction of a soft actuator: Ecoflex™ 00-30 and OOMOO™ 25.
The initial step in the process was the creation of the design for the actuator molds using FreeCAD:
The initial step was to assess the viability of resin printing for select molds, as this was a stipulated objective for the current week. To this end, the Form 4 printer was employed with Gray Resin V5.
Once the file had been uploaded to the PreForm printer application, the print location was set according to the instructions shown in the following image.
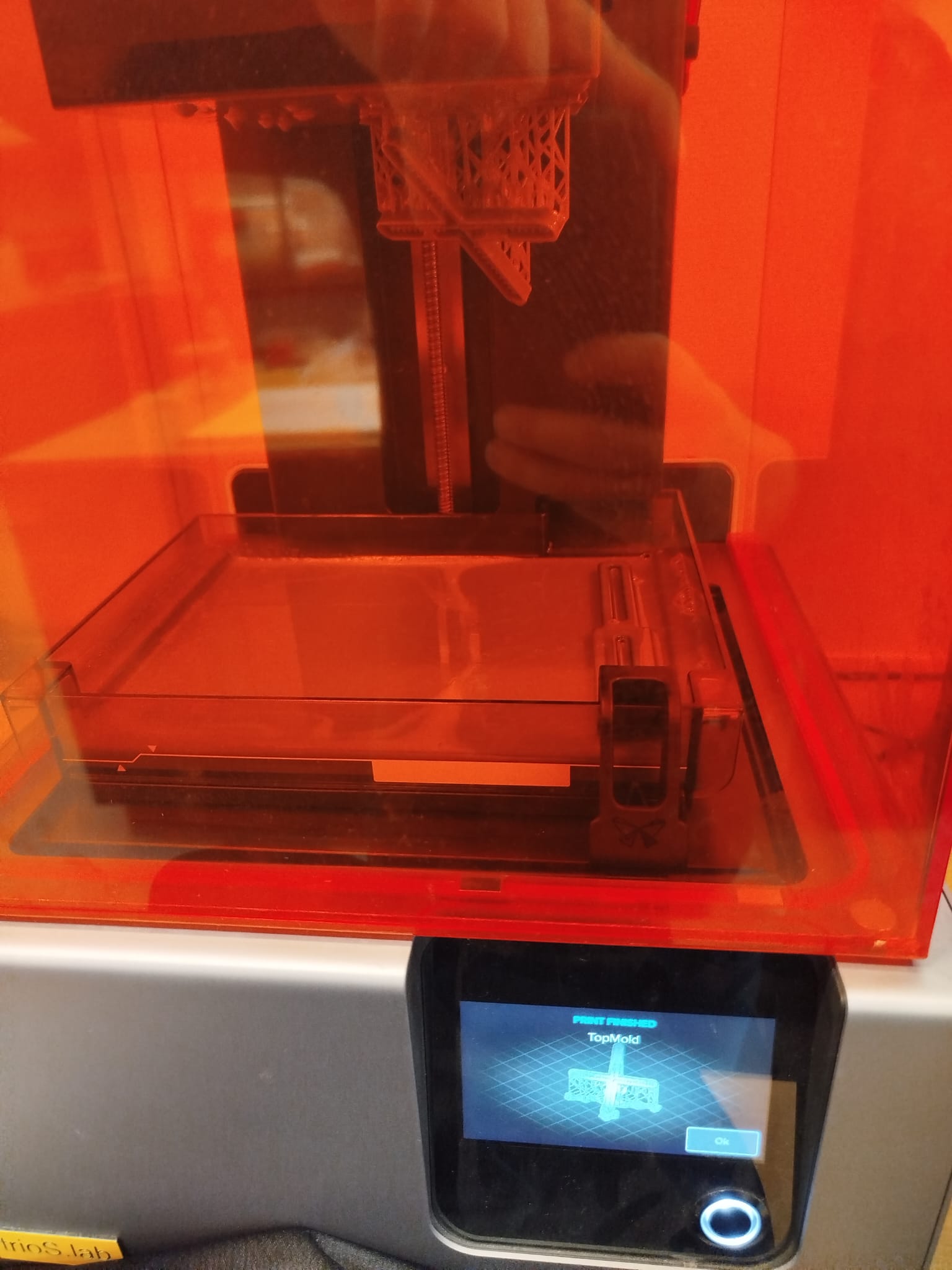
Following the cleaning of the piece in isopropyl alcohol, it is transferred to the ultraviolet curing bed for the final stage of curing.
Additionally, the mold was printed using a filament printer for comparison purposes. The results of this experiment can be observed in the images below.
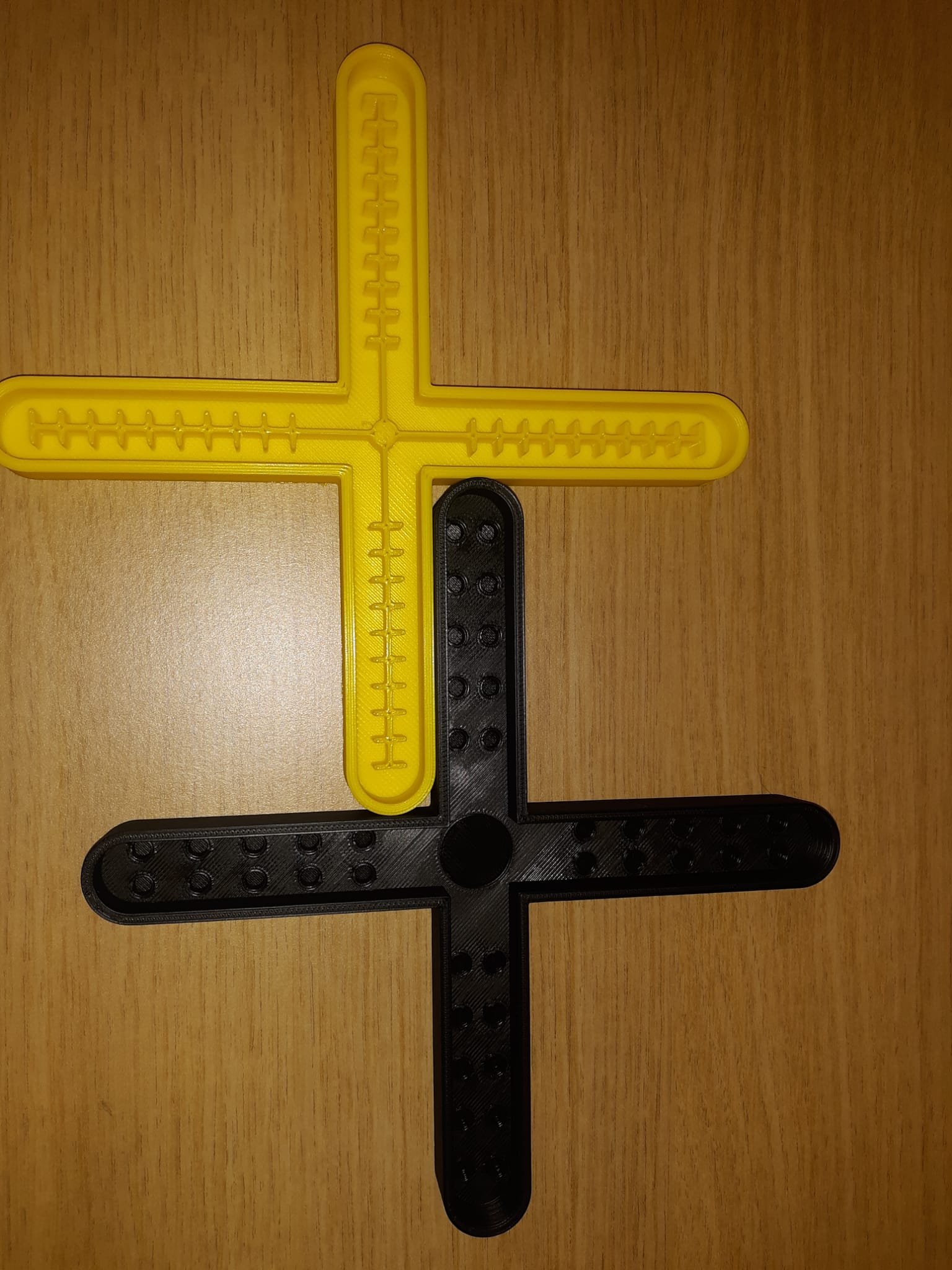
The deposition of layers during filament printing results in a more "layered" appearance for the printed objects. This gives them a rougher and less uniform surface. Additionally, filament-printed parts are weaker and more prone to warping and cracking, particularly in areas with volume or complex geometries.
In contrast, 3D printing with liquid resin results in the production of objects with a markedly smoother and more uniform surface. This is due to the fact that the resin cures in extremely thin, homogeneous layers. Additionally, objects printed in this manner tend to exhibit enhanced strength and durability. However, it should be noted that the resin printing process is more intricate and necessitates greater attention to detail, including the final curing of the part.
With regard to precision and detail, resin printing typically yields superior results, as it enables the creation of finer and more intricate structures. This renders it more conducive to applications that necessitate high definition, such as jewelry, miniatures, and high-quality prototypes.
Molds can be downloaded here.
Following the printing of the molds, the next step was to fill them in the laboratory. In order to perform this action, it is essential to adhere to the safety measures for working with these materials:
- It is imperative to wear a lab coat at all times to prevent the staining of clothing. In the event that contact is made with certain materials, it is often impossible to remove the stain or the remaining material from the clothing.
- It is imperative to wear gloves at all times to protect the hands and prevent injury. Some materials can be harmful to the skin, so it is crucial to take the necessary precautions.
- It is advisable to have paper at hand for immediate cleaning of any surface that is smeared with the material used. This should be kept in the front pockets of the lab coat.
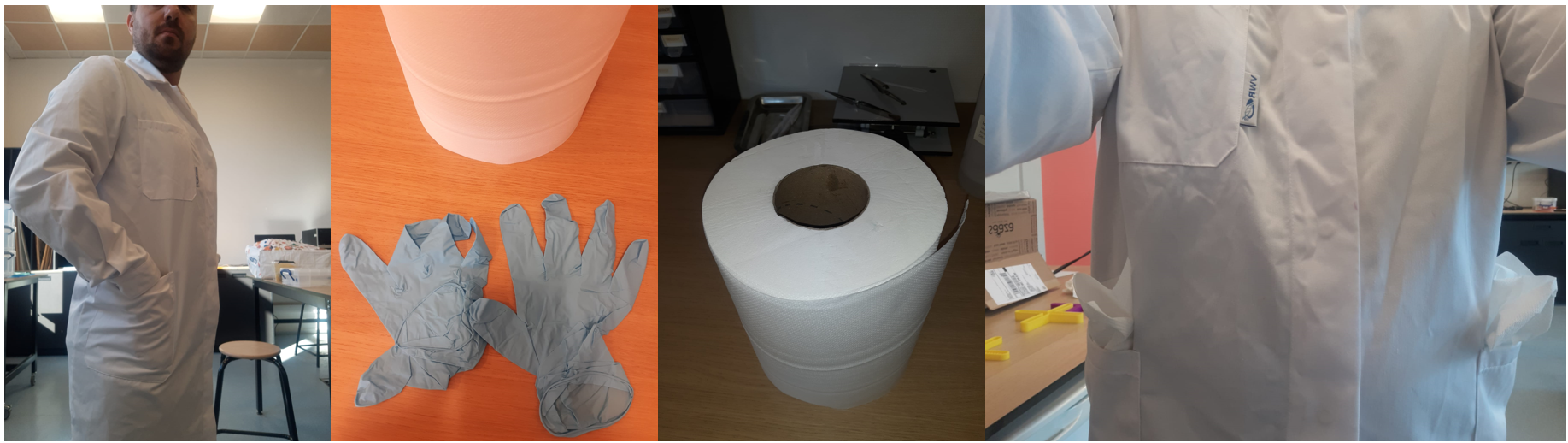
Prior to the preparation of the mixture, it is essential to ensure that all components are stirred in a gentle manner in order to prevent the formation of excess air bubbles.
Given the limited quantities of material to be used, it was necessary to employ a laboratory microbalance, which is capable of measuring 10 micrograms. It is therefore beneficial to be familiar with the Tare function, which resets the current weight of a vessel or container to zero, thus enabling the weight of the objects placed inside it to be measured accurately. This is useful for obtaining precise measurements of ingredients or products, regardless of the weight of the container in which they are placed.
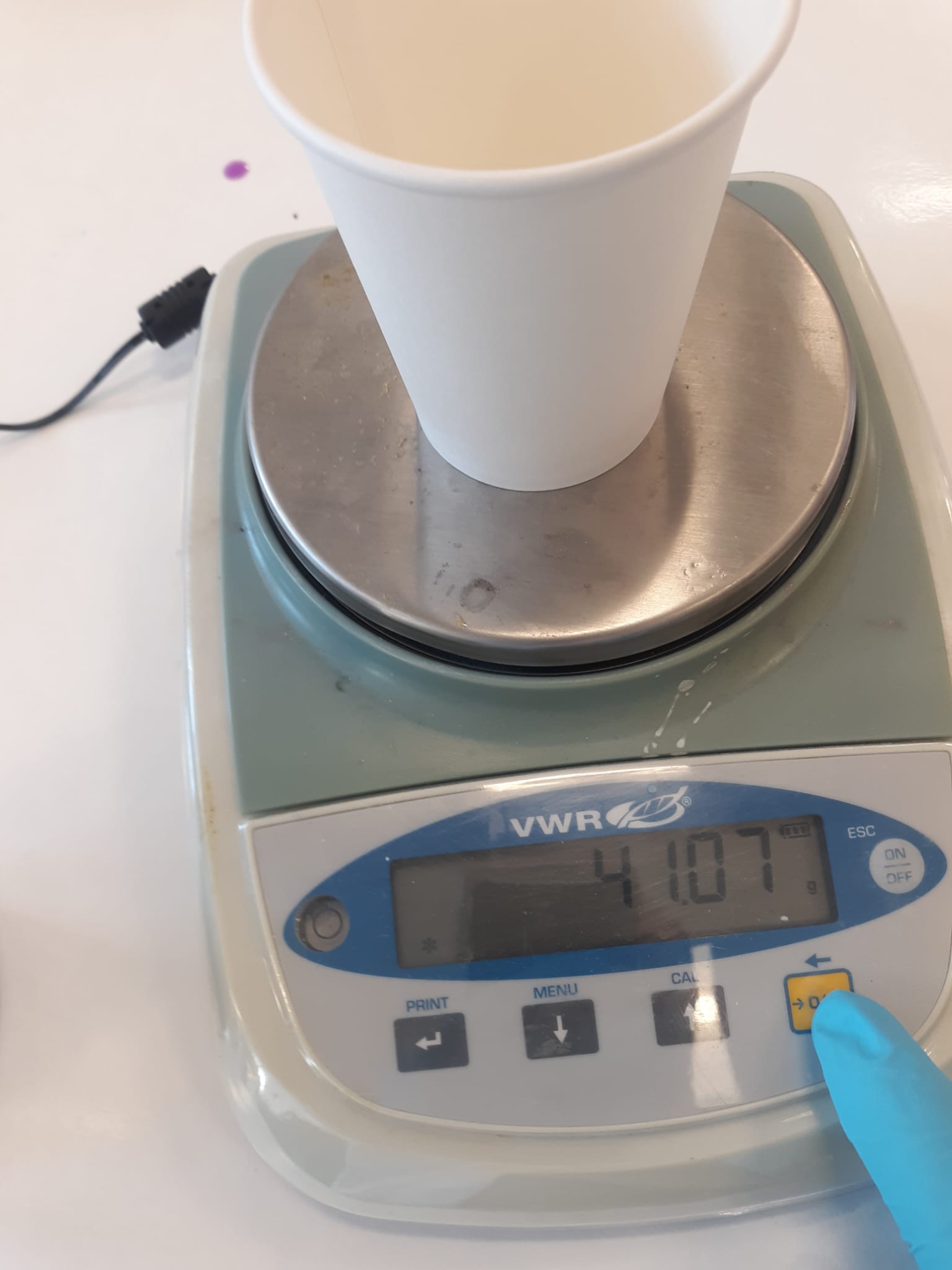
Both polymers must be combined, with equal parts of A added first and then B. This is done using a disposable wooden paddle and a disposable paper cup. The mixing process should be carried out with gentle movements in order to minimise the number of air bubbles in the mixture. Once the mixture has been prepared, it is poured into the molds, which have been placed on a horizontal surface. Finally, the molds are shaken by means of small blows to the surface to help the trapped air bubbles to rise to the surface and avoid weaknesses in the structure. This technique is equivalent to that used in construction for casting reinforced concrete parts and would be much more effective if a vibrating table were used, which we do not have in our laboratory. It is of the utmost importance to exercise caution when utilising vacuum pumps, as a reduction in pressure may result in the transition point between the liquid and gas phases being reached.
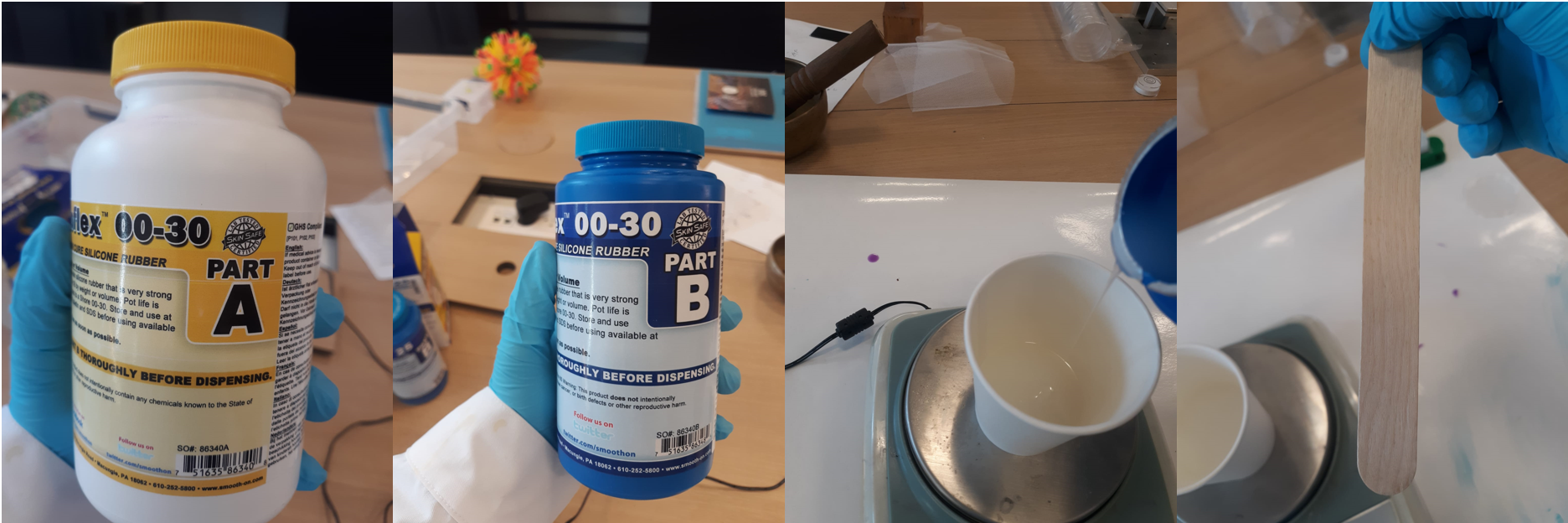
The two materials in question possess comparable characteristics. Ecoflex™ 00-30 exhibits reduced stiffness following a curing period of four hours. Additionally, it exhibits decreased viscosity, which facilitates the elimination of entrapped air bubbles within small, irregular surfaces. OOMOO™ 25, on the other hand, exhibits increased stiffness upon curing for a period of 75 minutes, yet retains a certain degree of flexibility. Its high viscosity, observed immediately following the blending of components A and B, serves to facilitate the trapping of air bubbles within small irregular surfaces.
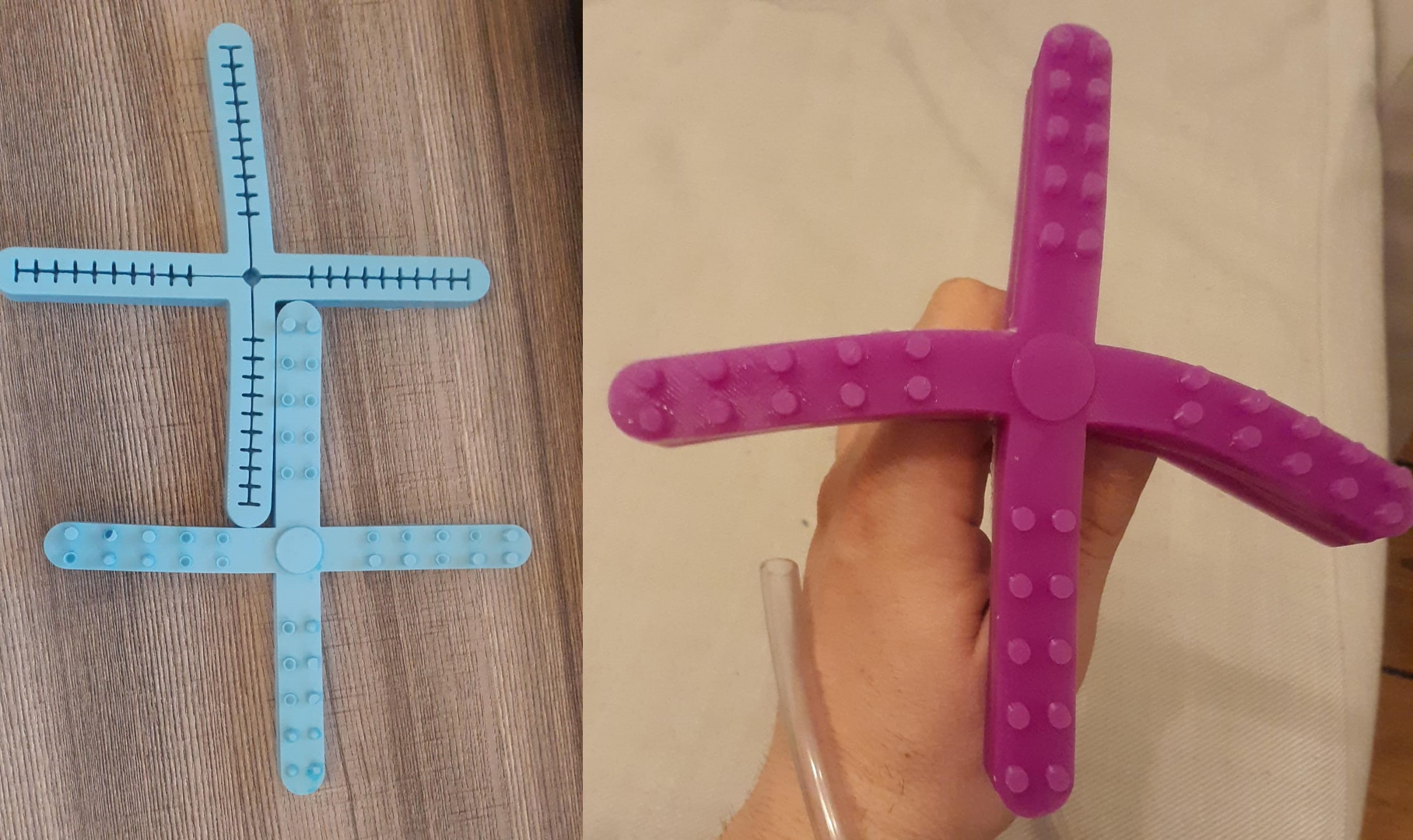
Due to the presence of imperfections in the OOMOO™ 25 part, only the Ecoflex™ 00-30 was employed in this instance. To facilitate the joining of both actuator parts, a new mixture of Ecoflex™ 00-30 was prepared and applied to the surfaces in question. While this approach resulted in the formation of a bond between the components, it was not as effective as desired. Consequently, the bonding procedure left behind areas with reduced strength. To address this, it is recommended that a third mold be utilized, which should be slightly larger than the previous ones. This will allow for the placement of both parts of the actuator.