Wild Card
This week assignment was to design and produce something with a digital process (incorporating computer-aided design and manufacturing) not covered in another assignment.
For this week's assignment, I decided to learn the basic controls of the Universal Robot robotic arm here in Ibero Puebla.
Robotic Arm
The robotic arm is a mechanical device commonly used in industrial manufacturing, it possesses multiple axes that allow it to move at different angles to mimic the function of a human arm. Here in Ibero Puebla, we have the UR5e robotic arm . This robotic arm is an 850mm reach robot that performs precise movement and is useful for a variety of applications.
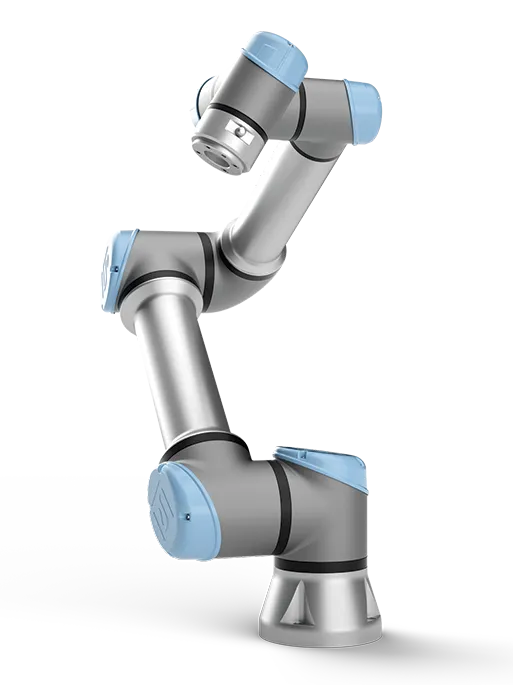
How does it work?
The robotic arm has three primary types of movement: MoveL (Linear movement), MoveJ (Joint movement), and MoveP (point-to-point movement/ circular movement).
- MoveL: Command the arm to move in a straight line to a target position.
- MoveJ: Direct the joint to move in specific angles, resulting in a smoother and faster path to target movements.
- MoveP: It refers to either circular movement or point-to-point movement, this focuses on efficient positioning without specific path constraints.
Set up
- Controller: The robot's controller acts as the brain of the system. It receives commands from the user or a pre-programmed script and translates them into movements. The controller calculates the necessary position and velocity for each joint to achieve the desired end-effector position.
- Inverse Kinematics: The UR5e uses inverse kinematics algorithms to determine the joint angles required to position the end-effector (the tool at the end of the arm) at a specific point in space. This involves complex mathematical computations to ensure smooth and precise movements.
- Motion Planning: After determining the joint angles, the controller plans the motion paths. This includes calculating the trajectory for each joint to move from the current position to the target position without colliding with obstacles or exceeding the robot's physical limits.
- Motor Control: The controller sends signals to the servo motors at each joint, dictating the required rotation. The servo motors, driven by these control signals, rotate the joints to the specified angles. Encoders provide continuous feedback, enabling the controller to make real-time adjustments.
- Safety Features: The UR5e is designed for collaborative operation, featuring built-in safety measures such as force sensing to detect collisions and halt motion if an obstacle is encountered. This allows the robot to work safely alongside humans.
Drawing
First, we need to set up the drawing tool on the robot, we used sharpener and a support that goes on the tip of the UR.
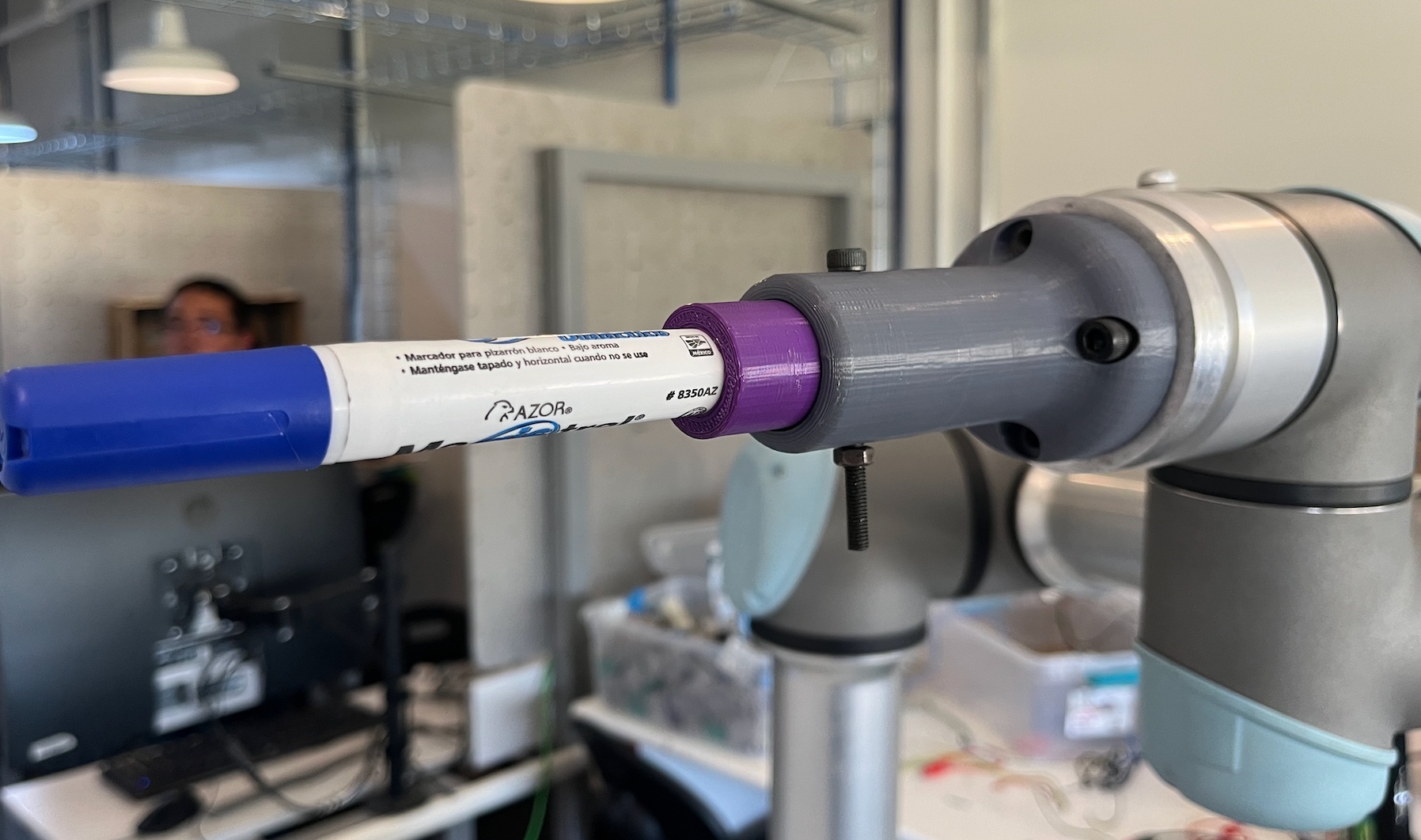
Robot set up:
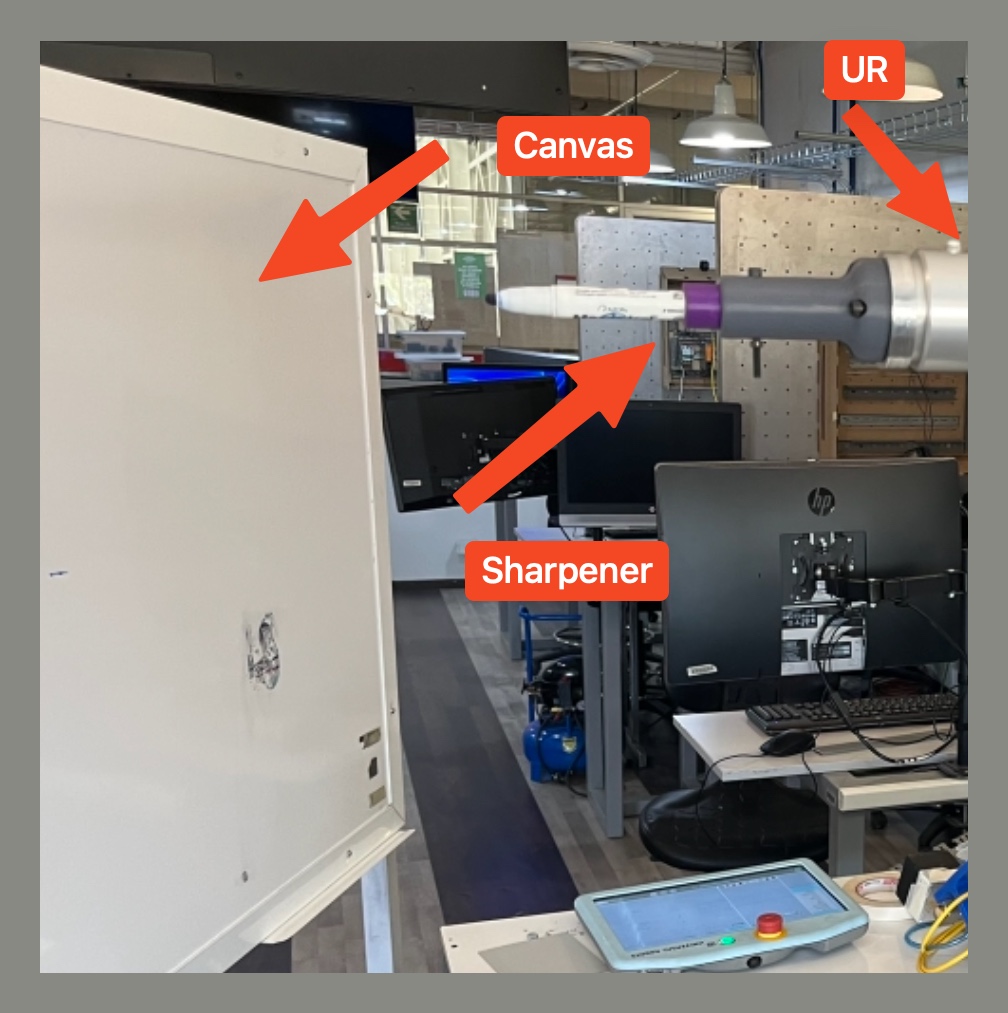
For this week's assignment, I used the UR controller to make a drawing by establishing different points on a whiteboard.
The first step is to press "program" on the UR interface, there we can program waypoints using the "Block programming" option. Each waypoint is a different point in our drawing.
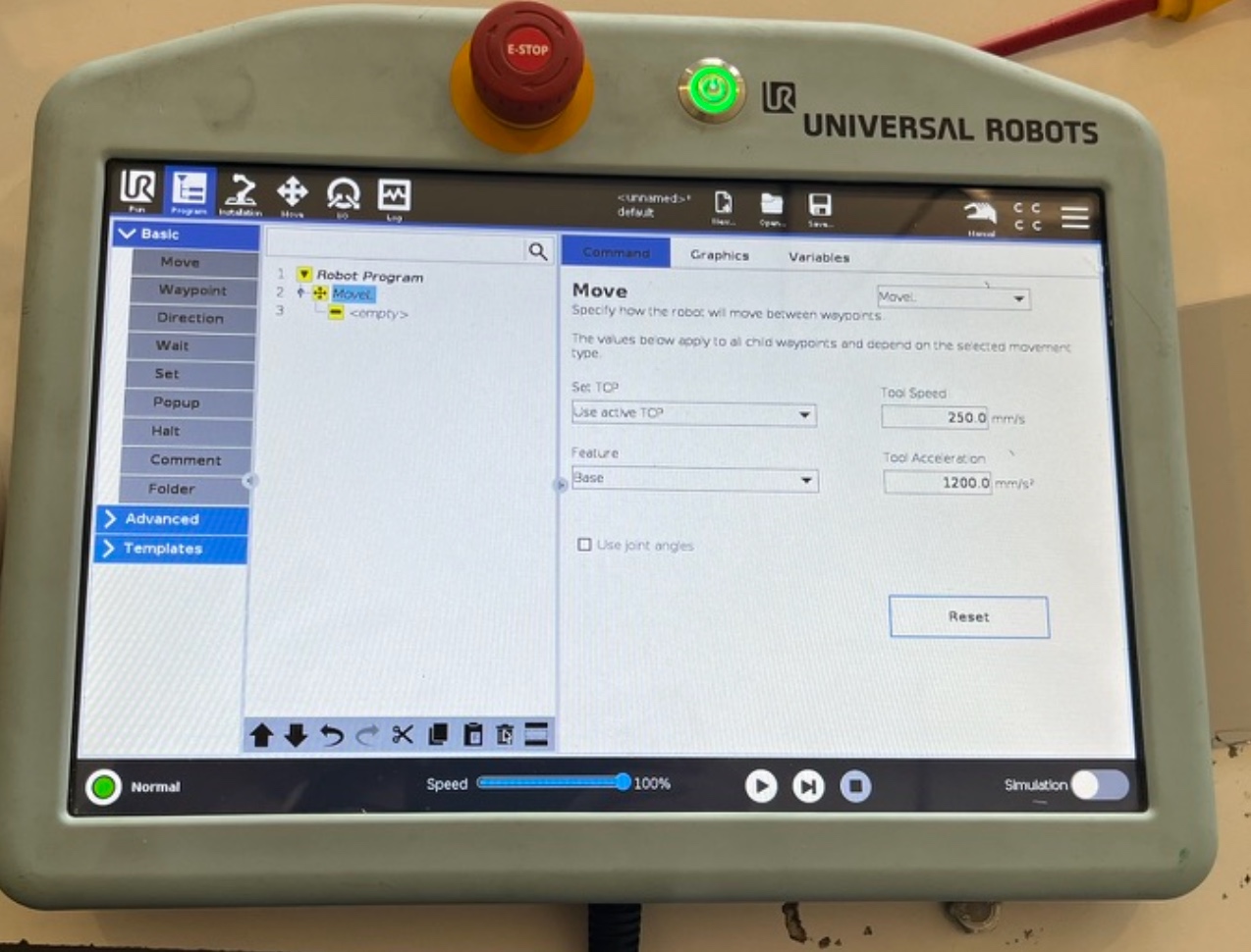
There we can choose which type of movement we want, as I explained before there are three different types of movements that the UR can perform. Each waypoint that is established can have a different type of movement.
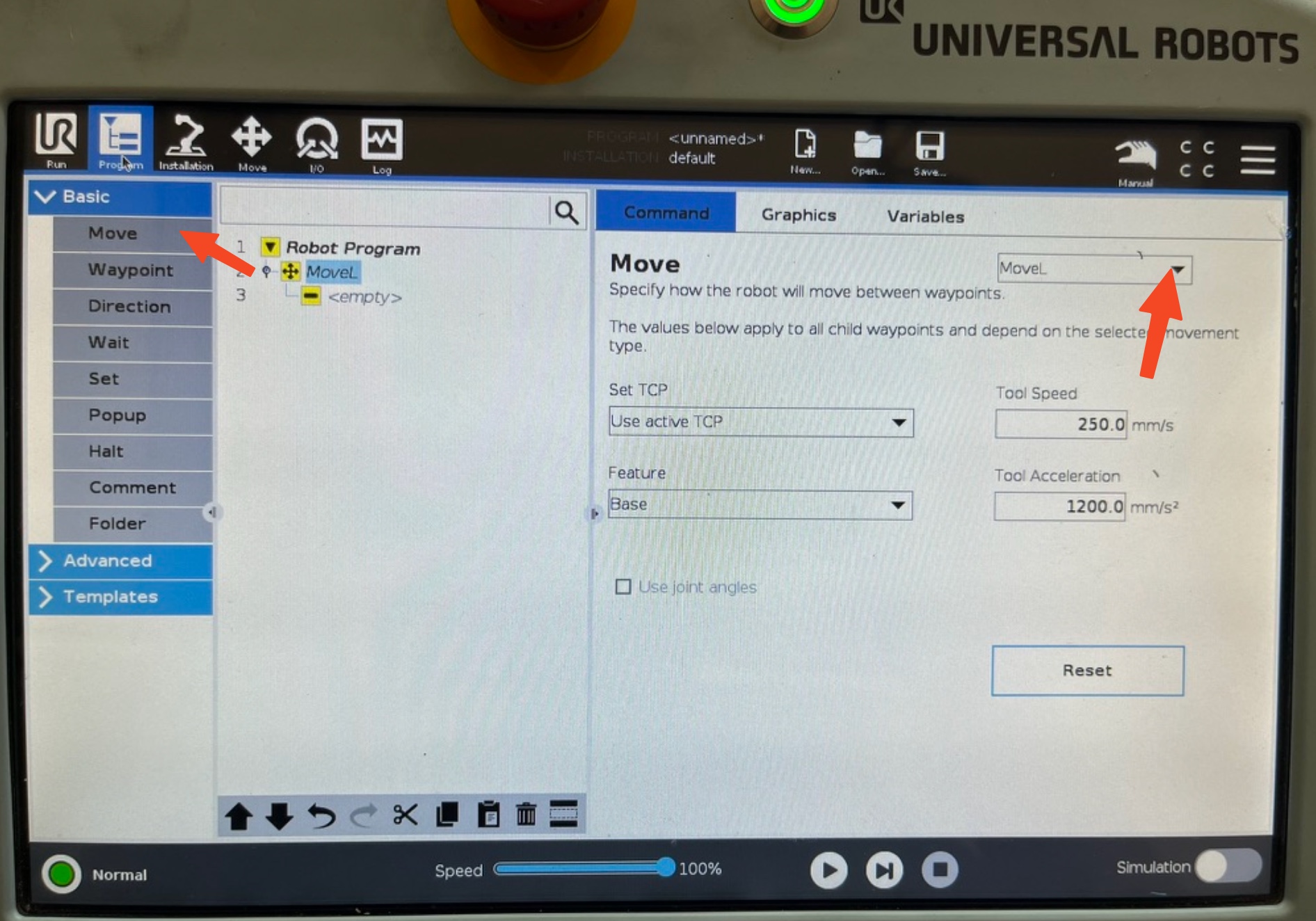
To set up each waypoint on the UR, press the free movement button to manually move the robot to the desired position.
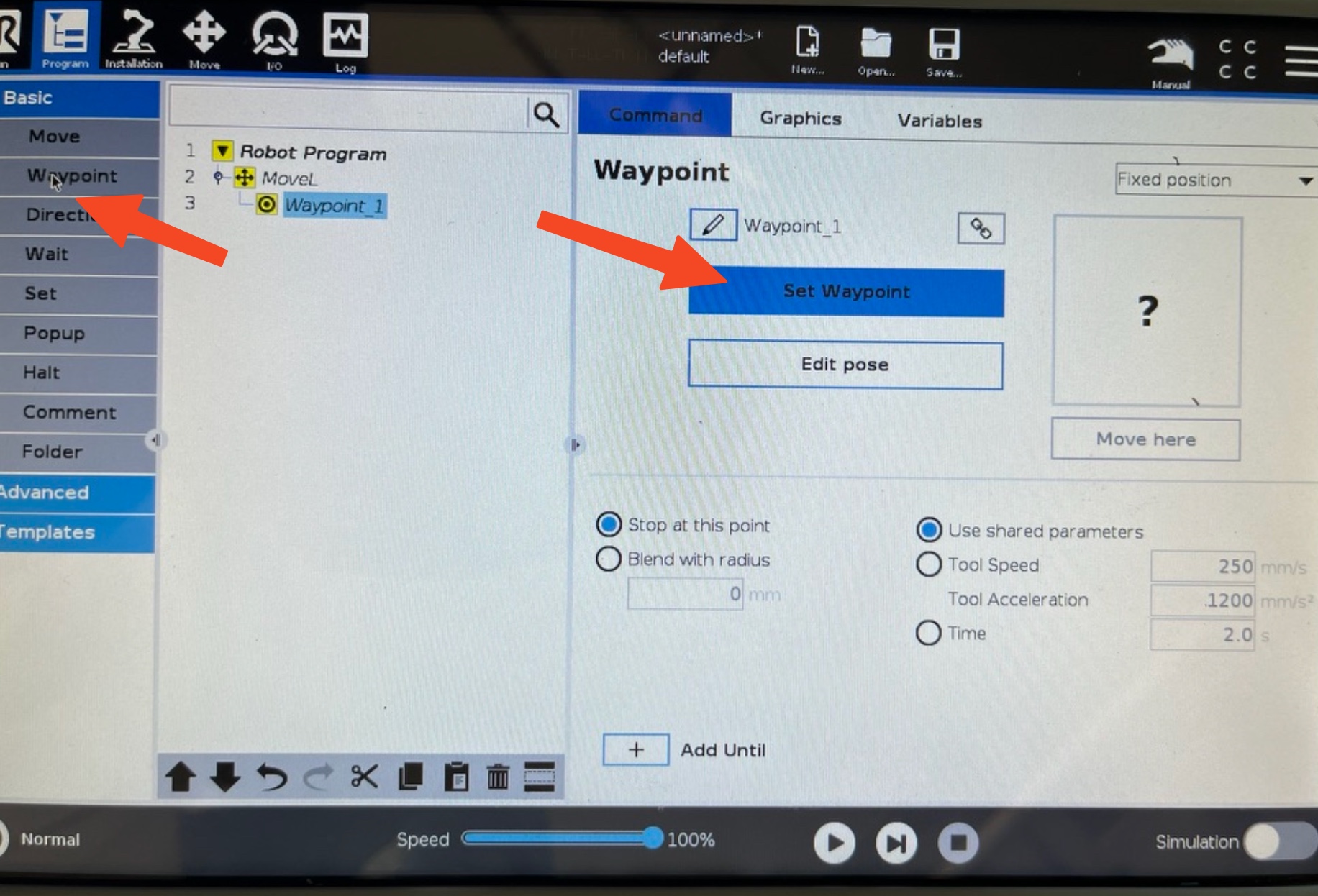
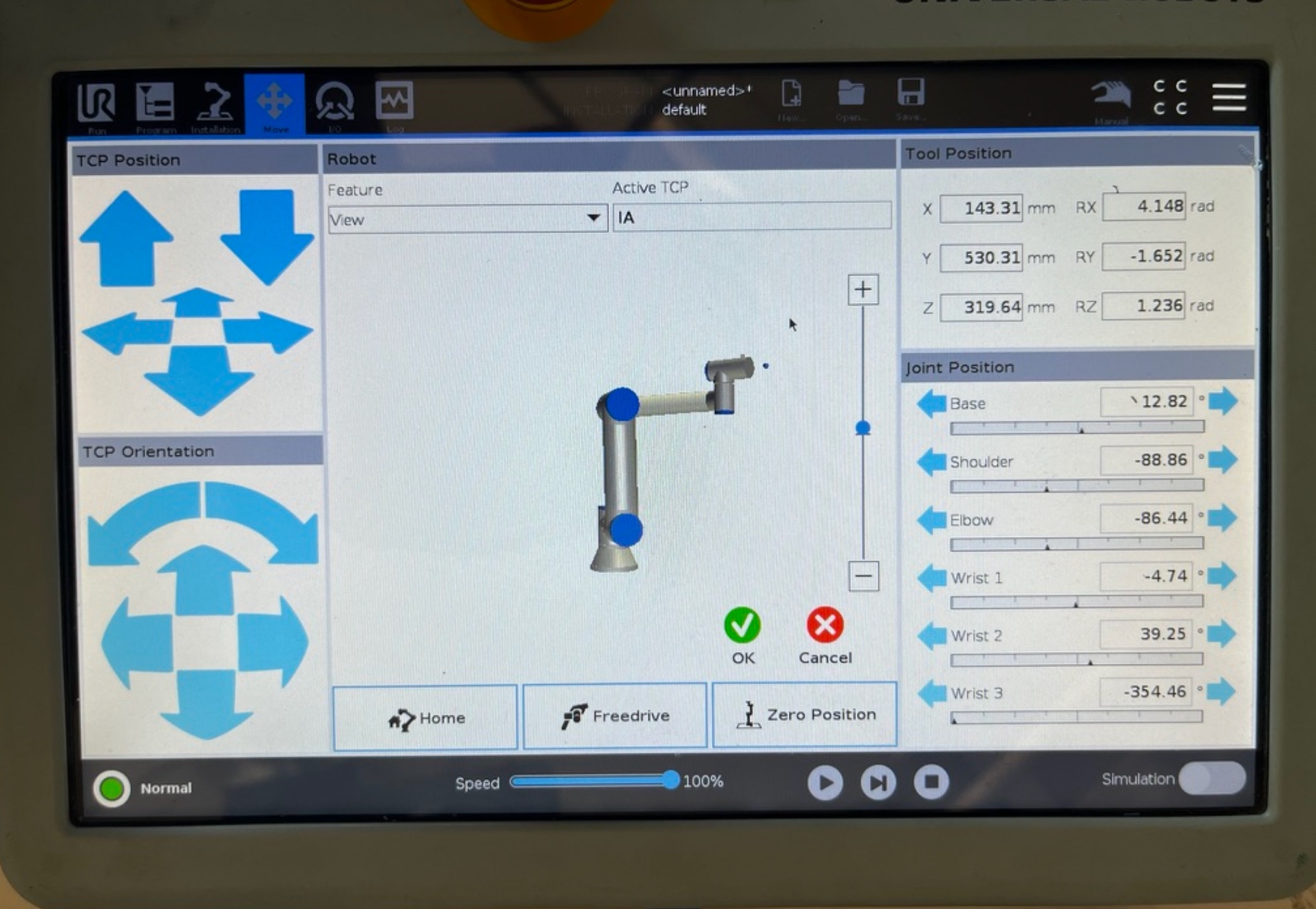
We repeat this process until all desired waypoints are set. Once completed, we run the code.
All waypoints:
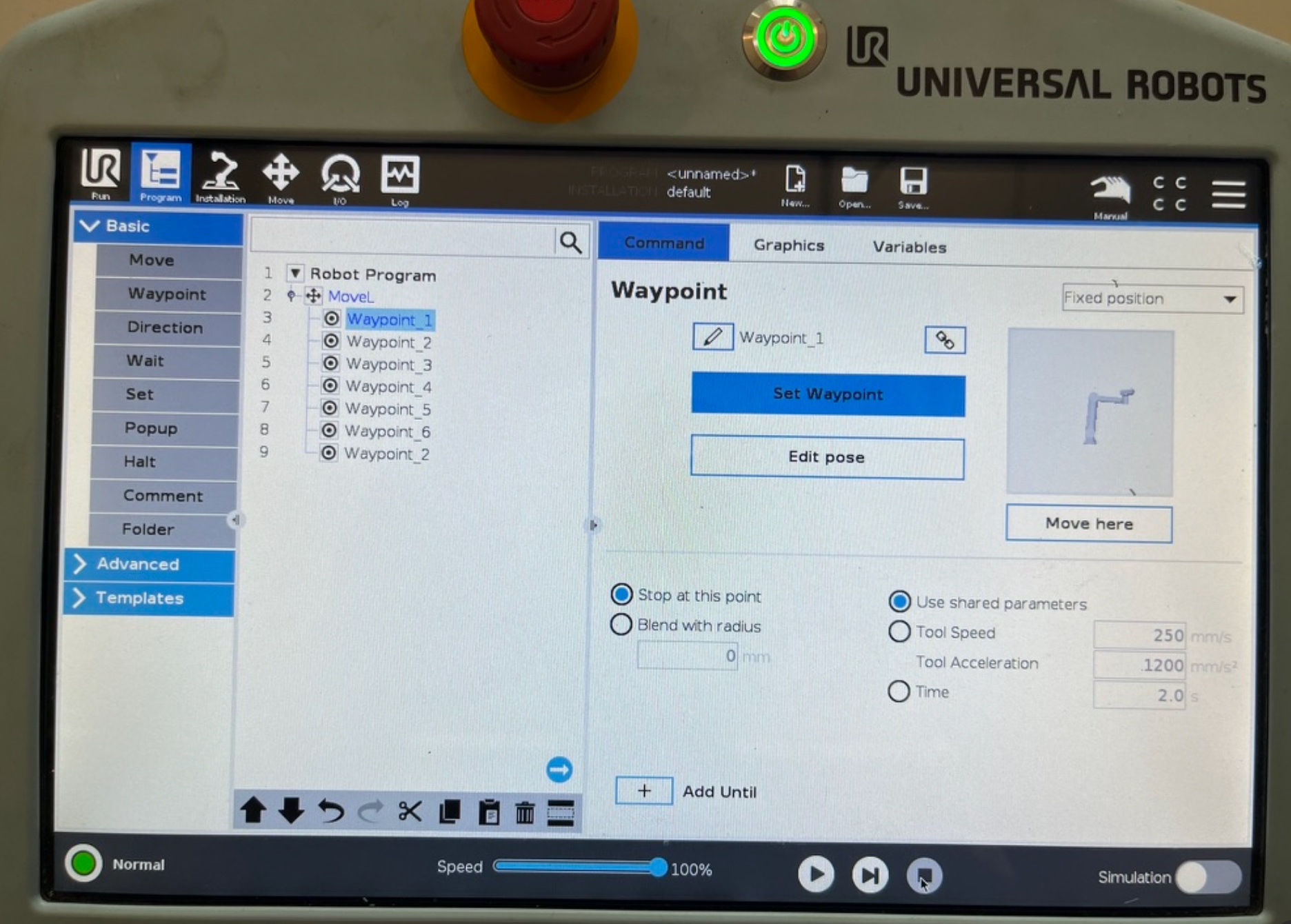
Running the code:
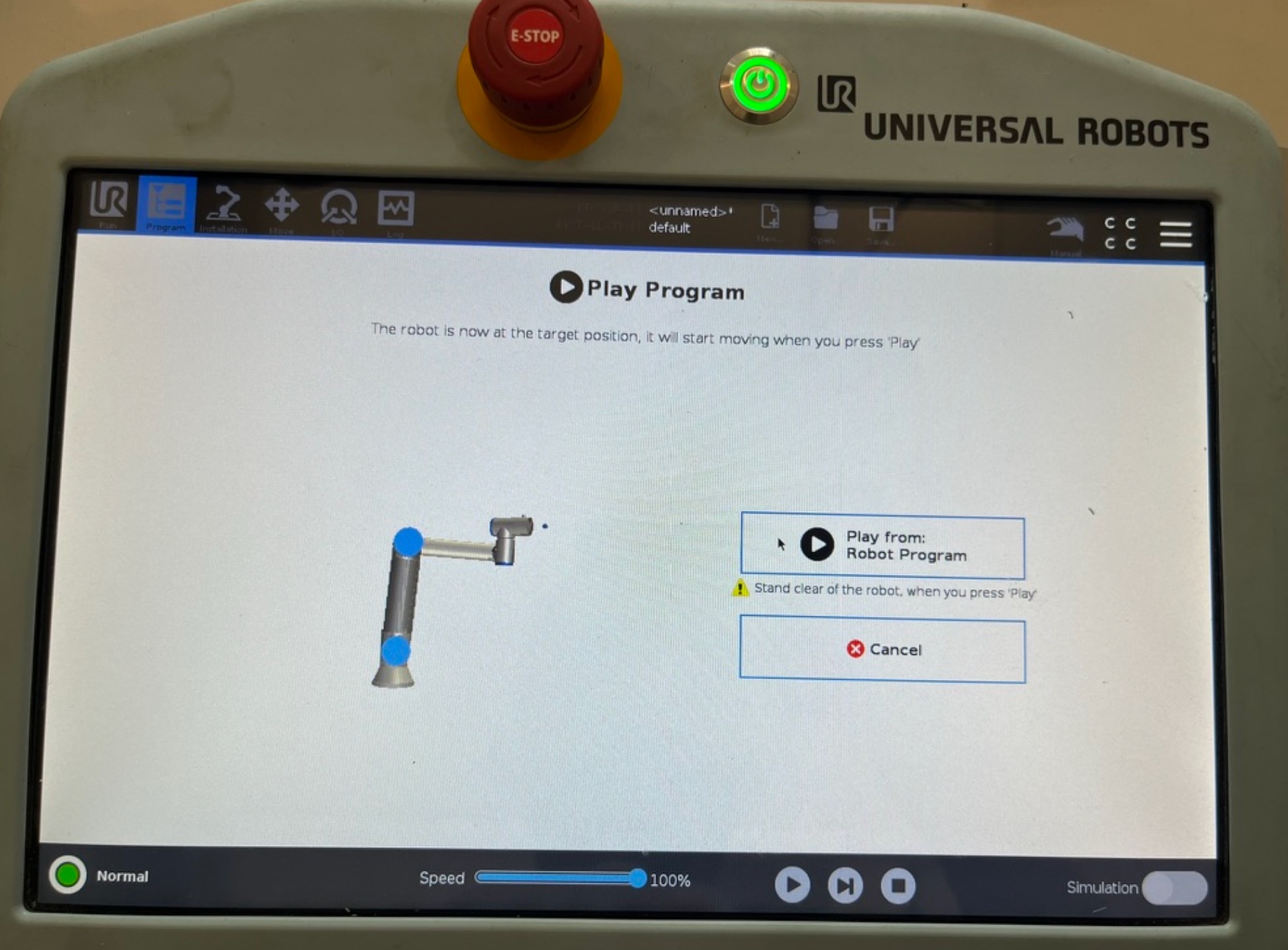