INTERNAL BASE
First I would like to explain why an internal base, the answer is simple, if I was going to use transparent acrylic, the least I wanted was for the neopixel strip to look tangled and without order. In addition, I had the idea that the neopixels would gradually yield upwards, integrating the nine levels of the Enneagram. Now that I have explained it, the following process will make more sense (I hope).
In Rhinoceros I modeled a cylinder, which inside I made some slits in the shape of an ellice, then I split the cylinder in two and joined it to a rectangular base of about 20 by 25 cm with a depth of 3 cm.
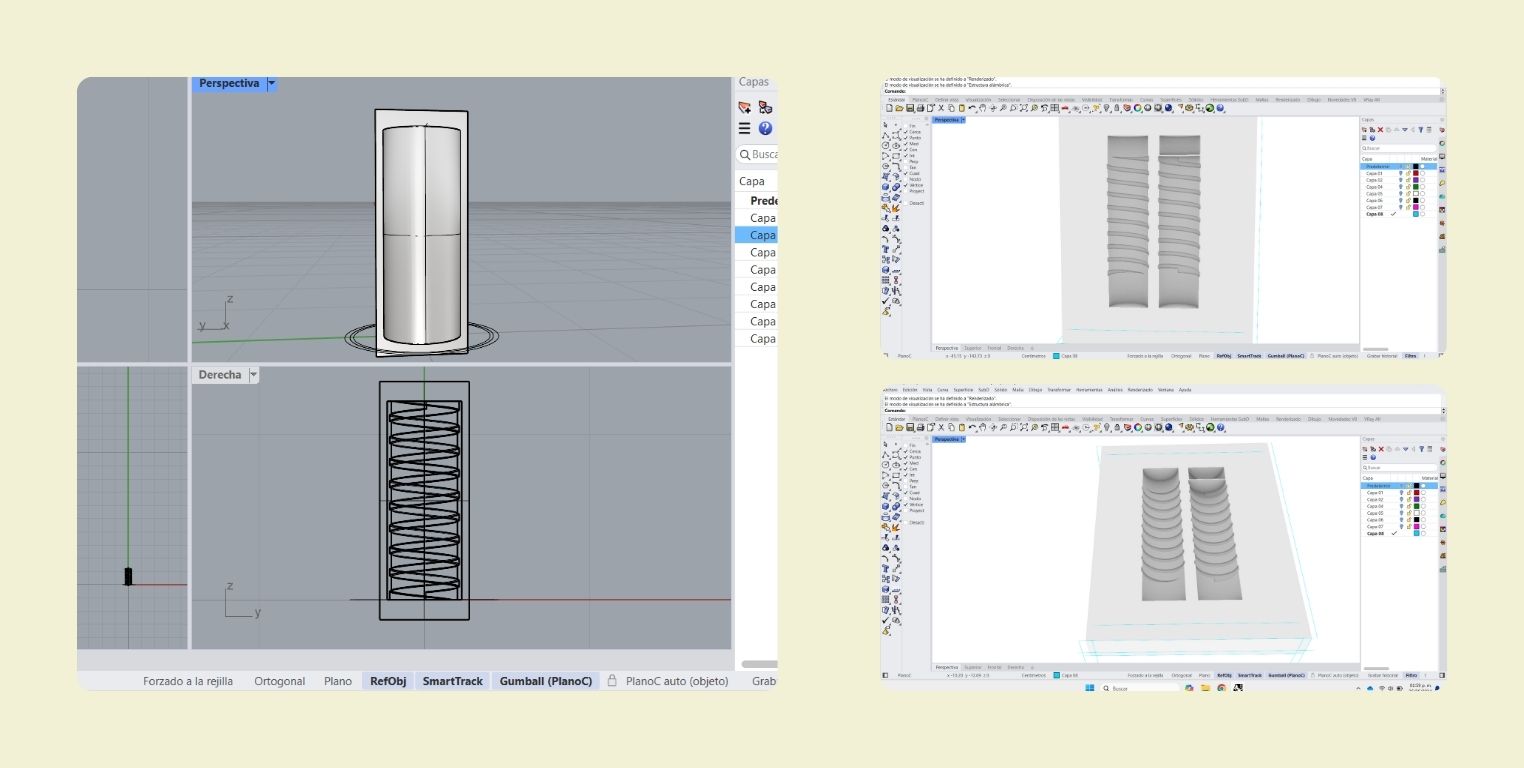
Then I ran it through VCarve to configure the cut and finish of the piece, the idea is that the 5mm indentations were the best possible portrayed, basically I was looking for a finish like the wax I used for the molding and casting week, but now with MDF. In this process I was helped by one of the local instructors to make the Router only cut to the center, where the piece was, and that the tool was not at risk in the peripheries.
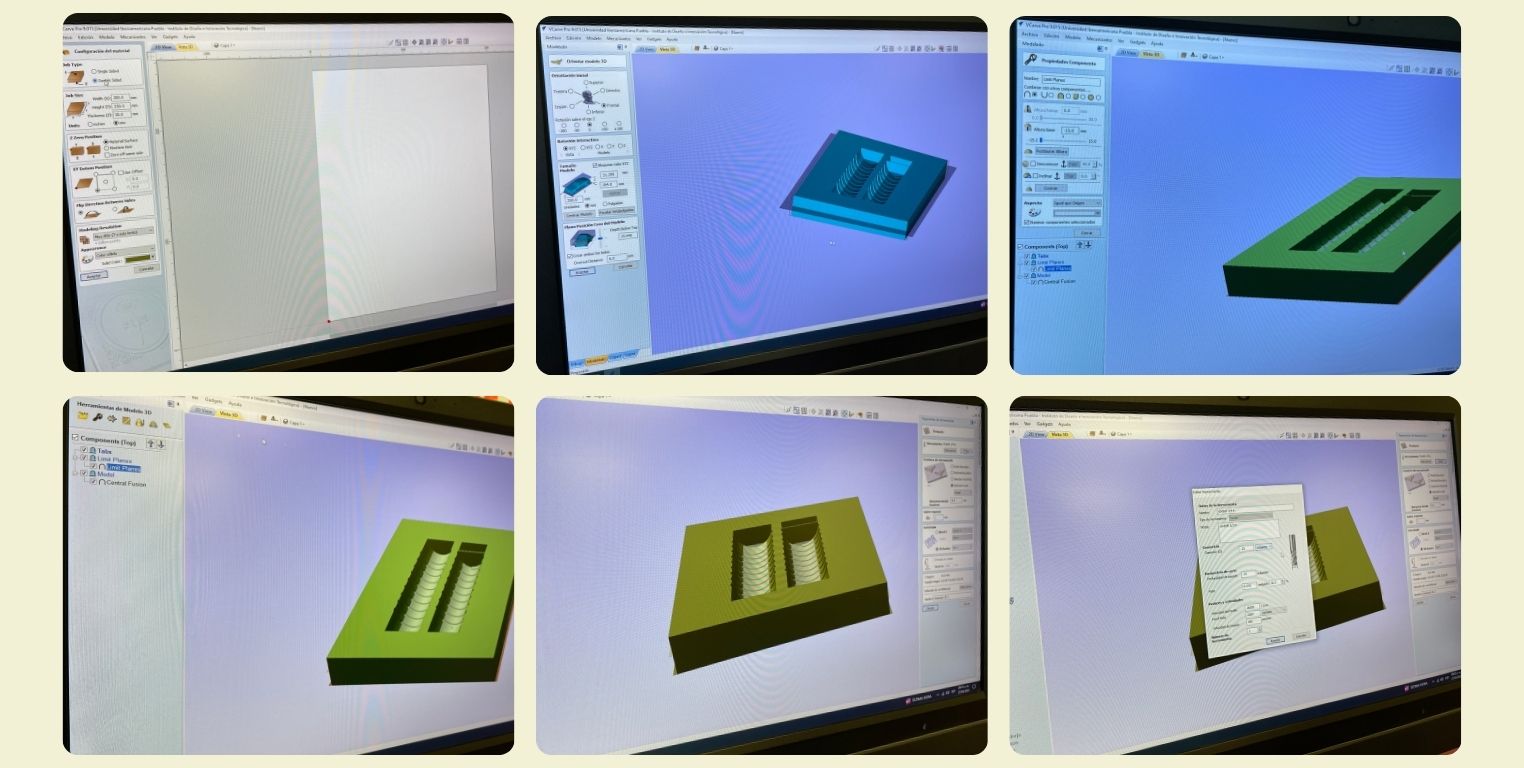
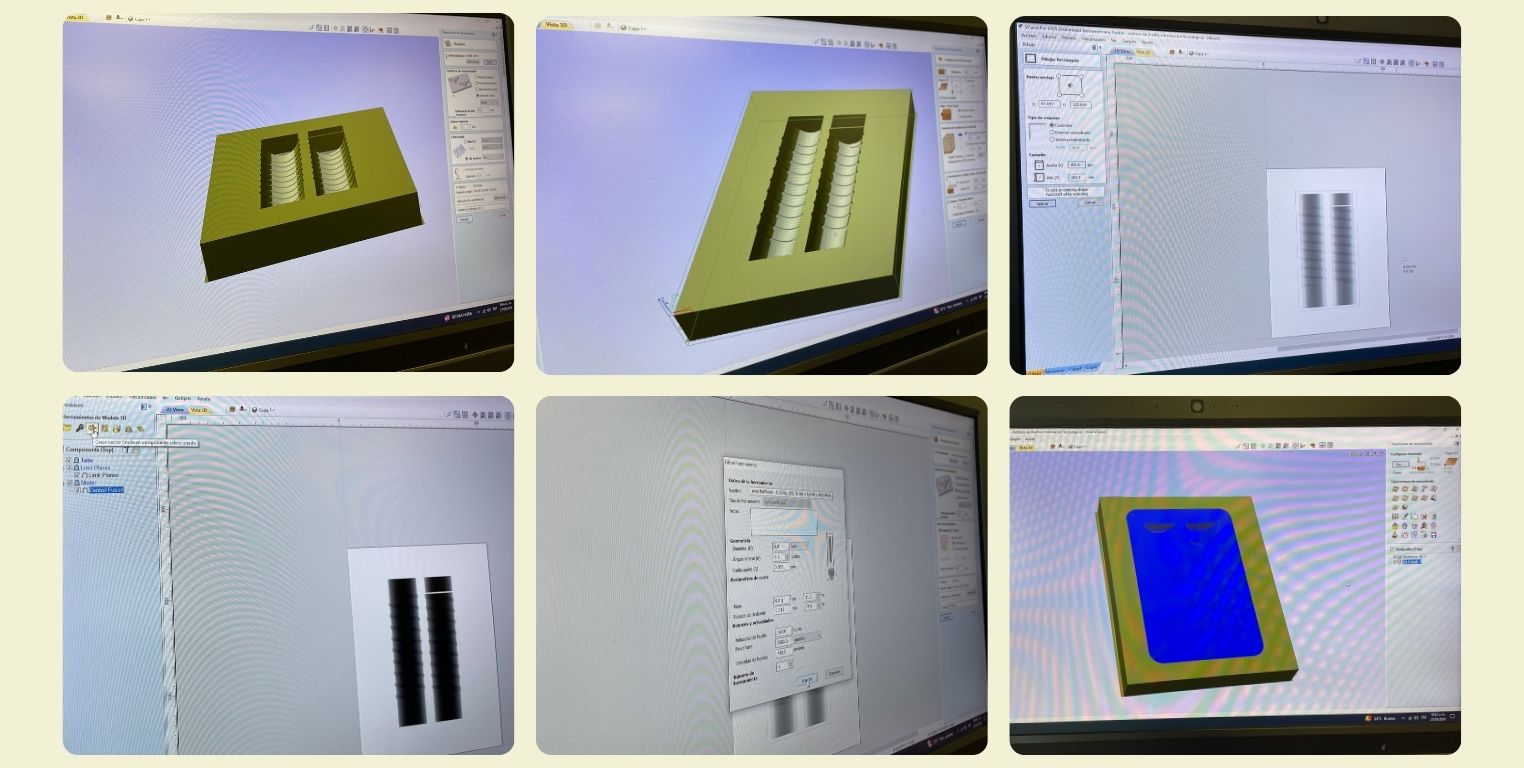
To do this, a day before I glued two 1.5 cm thick MDF pieces of wood to obtain my cutting piece and then place it on the cam table. In the same way I got the pieces and their respective adapters to the Router nozzle.
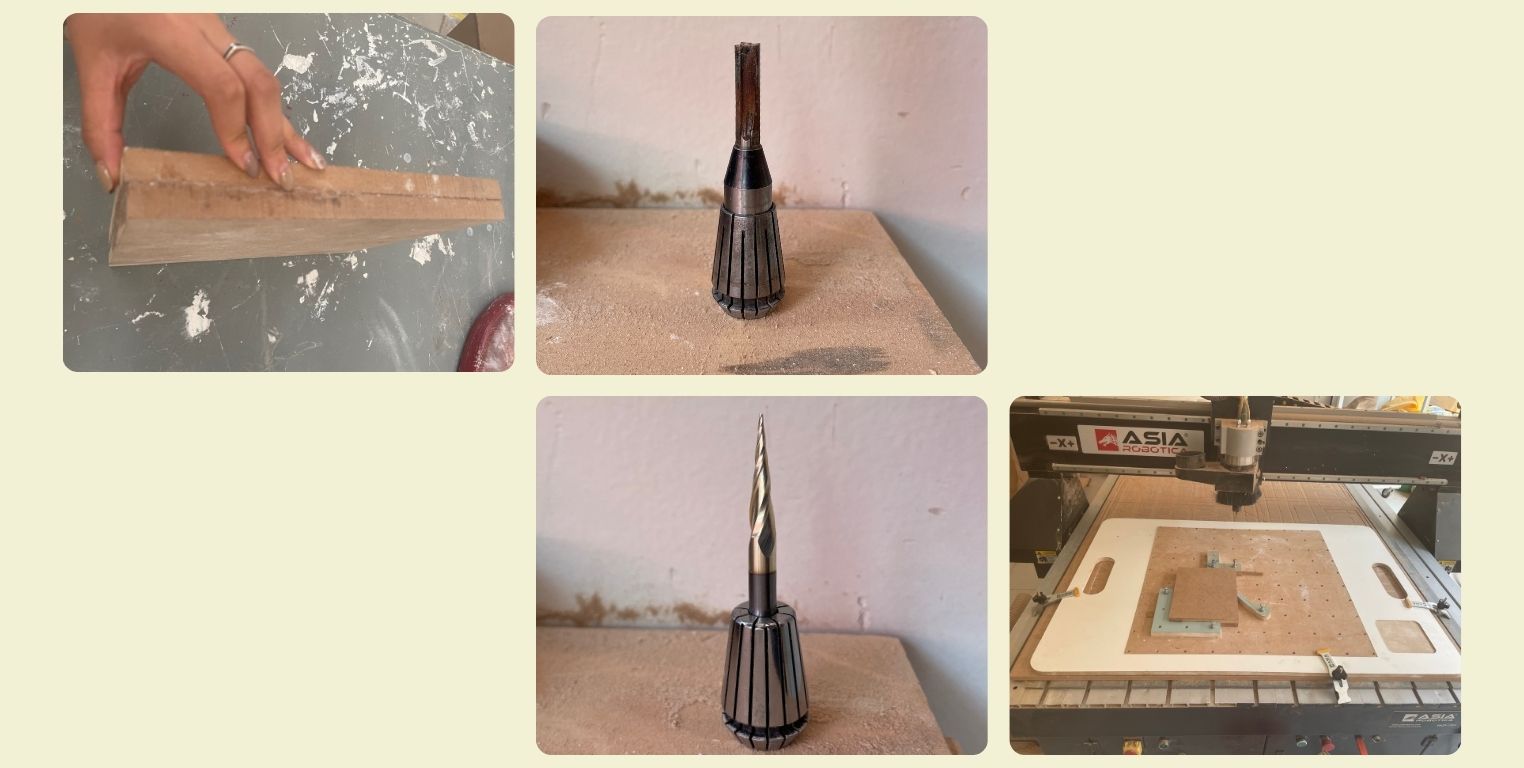
With the help of the monitor I guided the cutting and finishing. Between these processes I also had to change the tools I would use for each one, allowing me to learn a little more about this process, as I had not had the opportunity to change the nozzle adapter before.
Once the cut was ready in the Router, the next step was to make some small holes around it with the router, for this I had to get another piece of wood that I could put underneath and hold both with the help of some presses so that they would not move. This is necessary because with this piece I had planned to do a thermoforming that would give me the final piece of the internal base, and when doing thermoforming, especially for details it is necessary to have perforations in which the air can be sucked better.
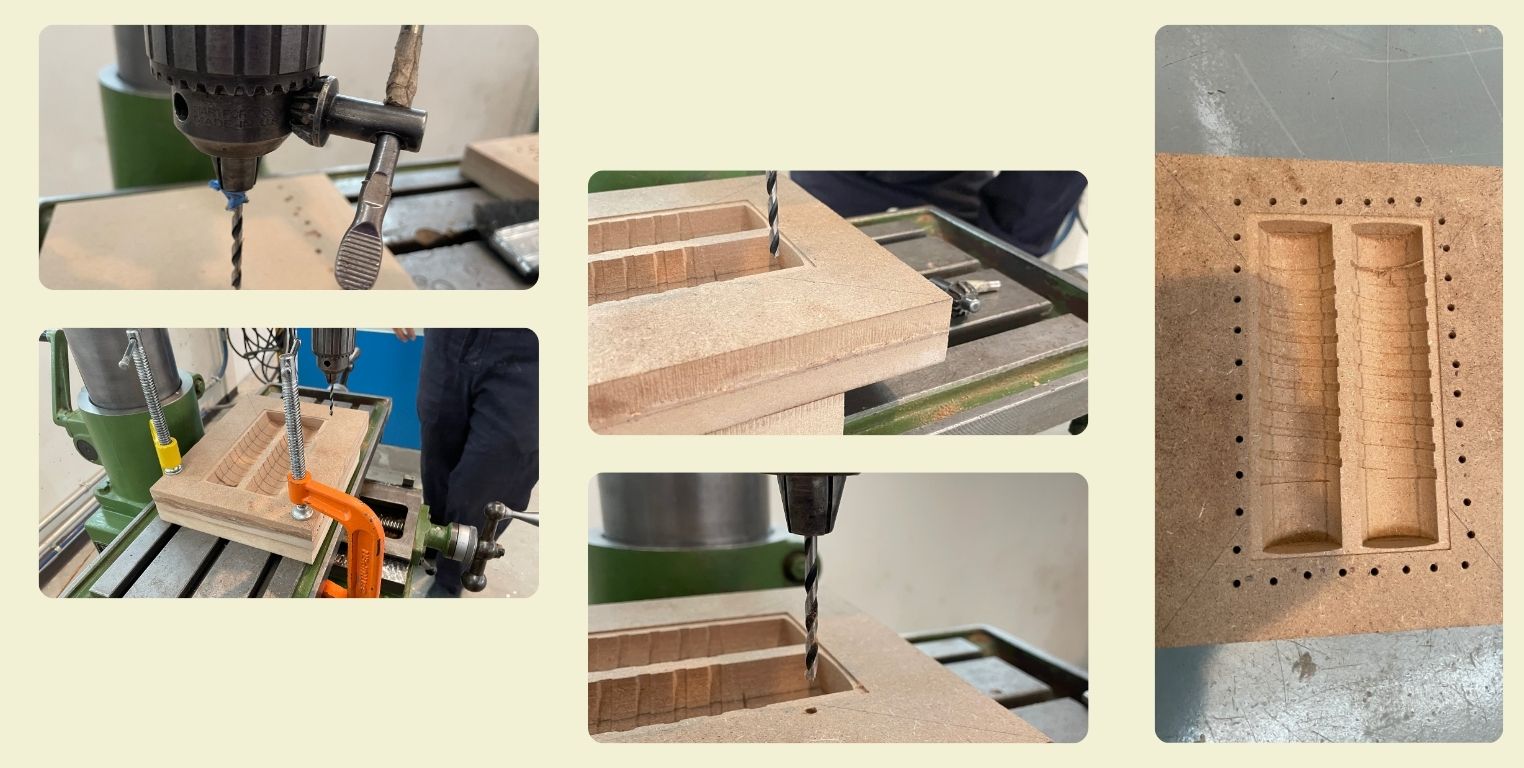
Once the larger perforations were ready, I moved to a work table where I clamped my pieces again, and with the help of a mototool and a thinner drill bit I made the perforations in the middle of the indentations. In the last photo in the lower right corner you can see that I also sanded the corners a bit to ensure that there were exit angles and the part would come out of the thermoforming.
THERMOFORMING
In the thermoformer the first thing to do is to place the material on the base and secure it, in my case I used PET, because it resists heat quite well and the neopixel strip could be heated a little, so it would hold quite well.
I was also helped by a guide made by the local instructors at all times, although I must say that they also accompanied me in this part of the process.
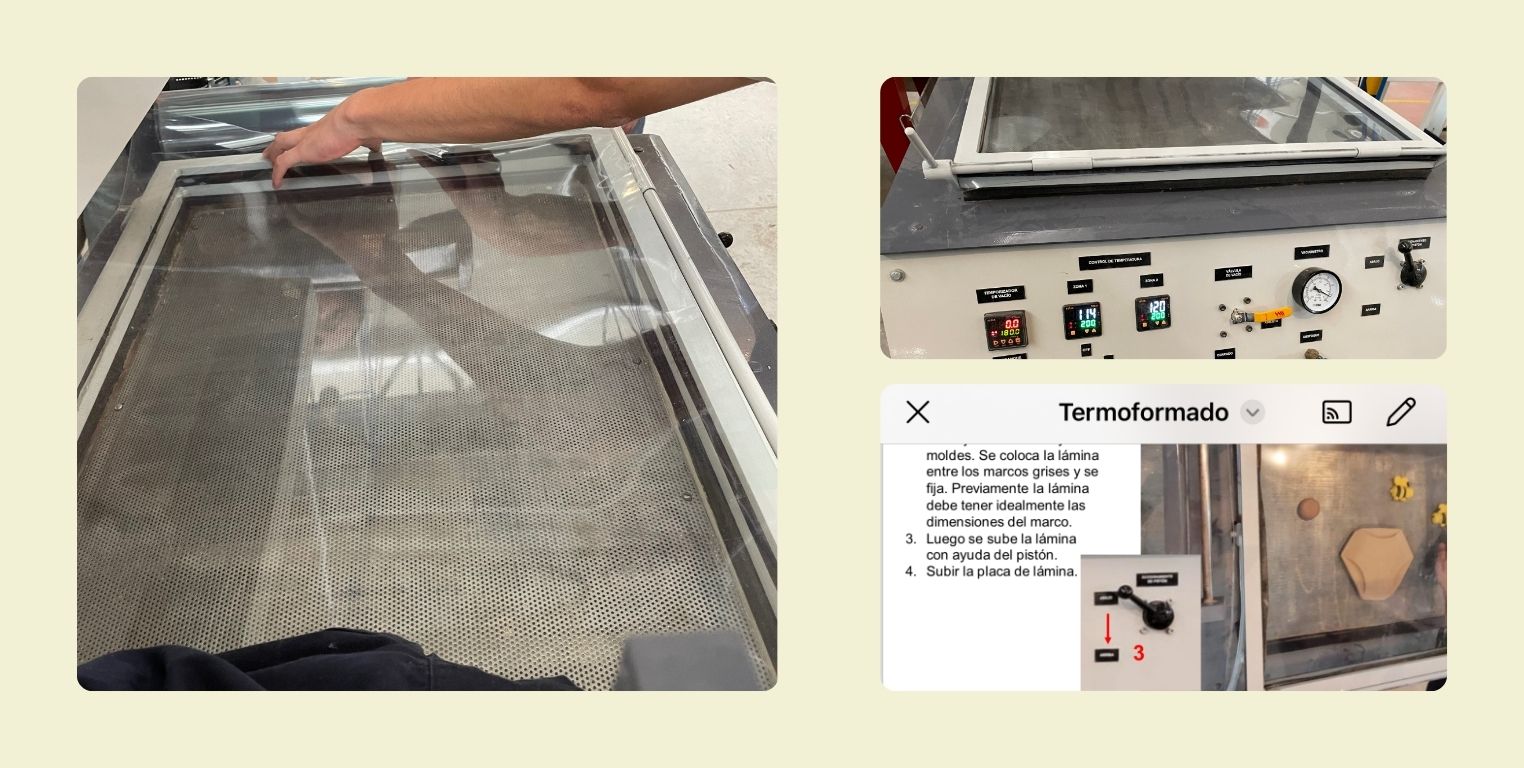
It is important to set the temperature on the two screens of the thermoformer so that it heats evenly, at the beginning it is set and a countdown starts in which the machine gets ready.
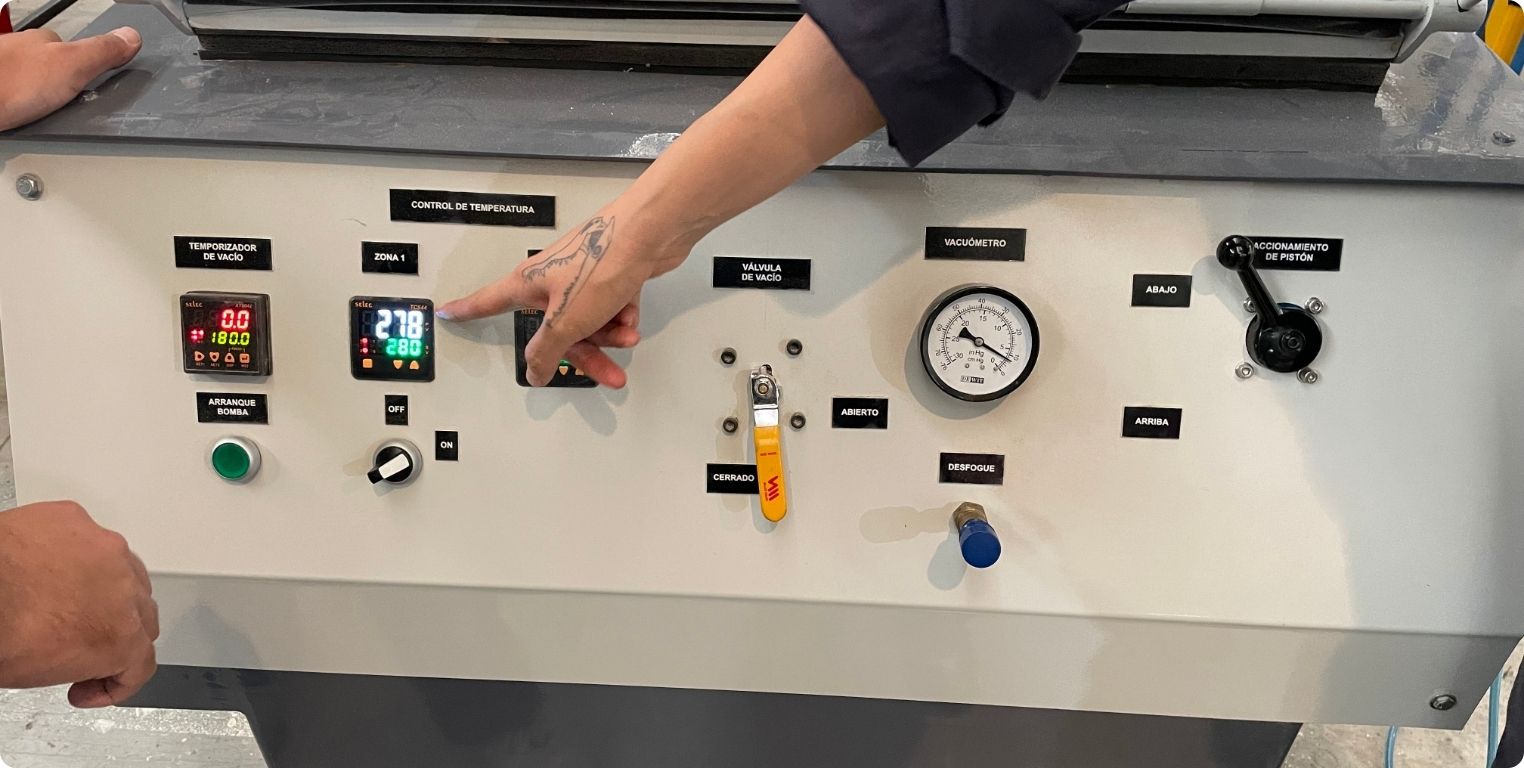
At this time the top white part should be at the bottom, and for the moment it is not necessary to raise the material.
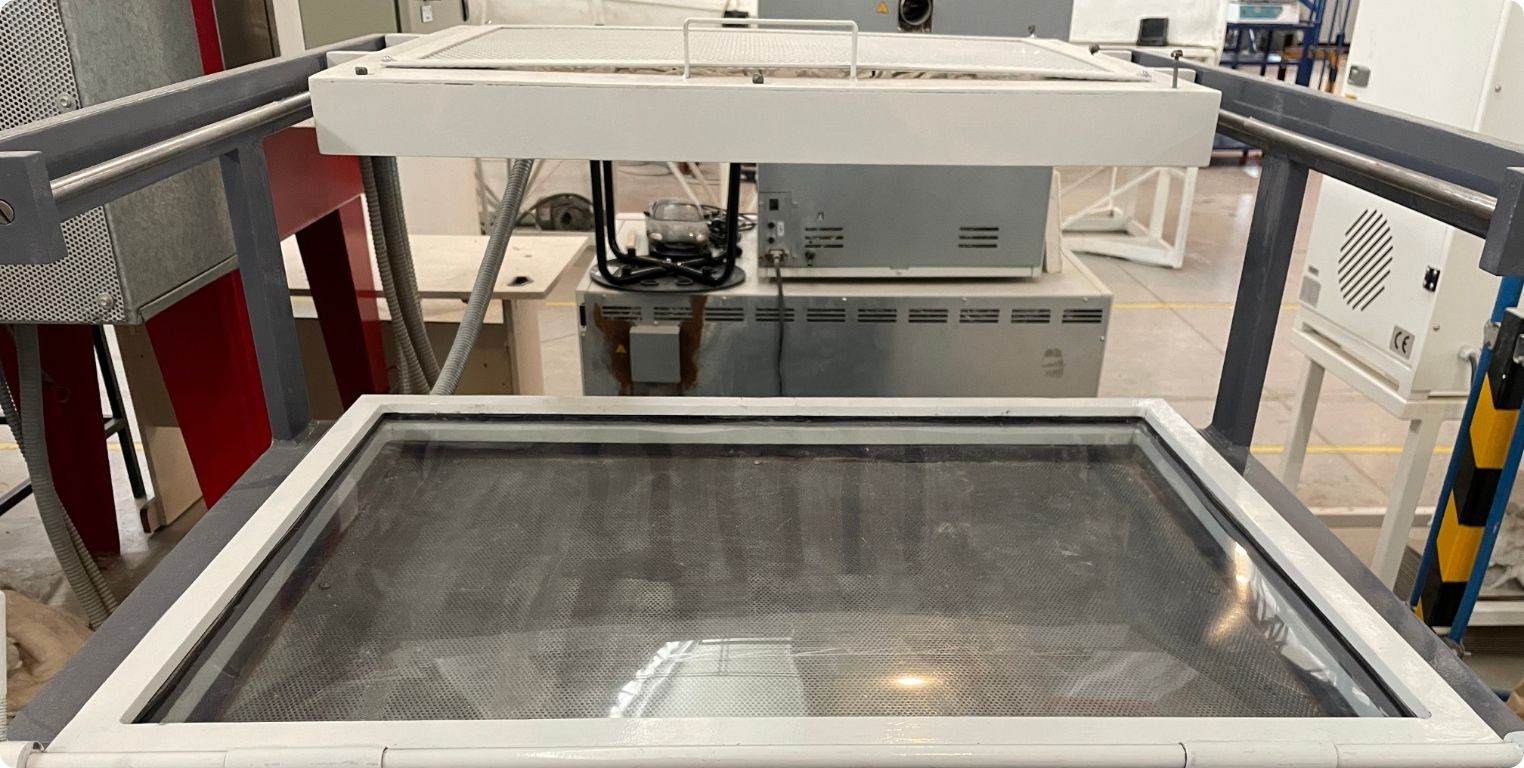
After a while it can be raised to begin to place the piece to be portrayed with the machine in a position that helps, it is usually recommended that the piece leaves a considerable margin at the ends.
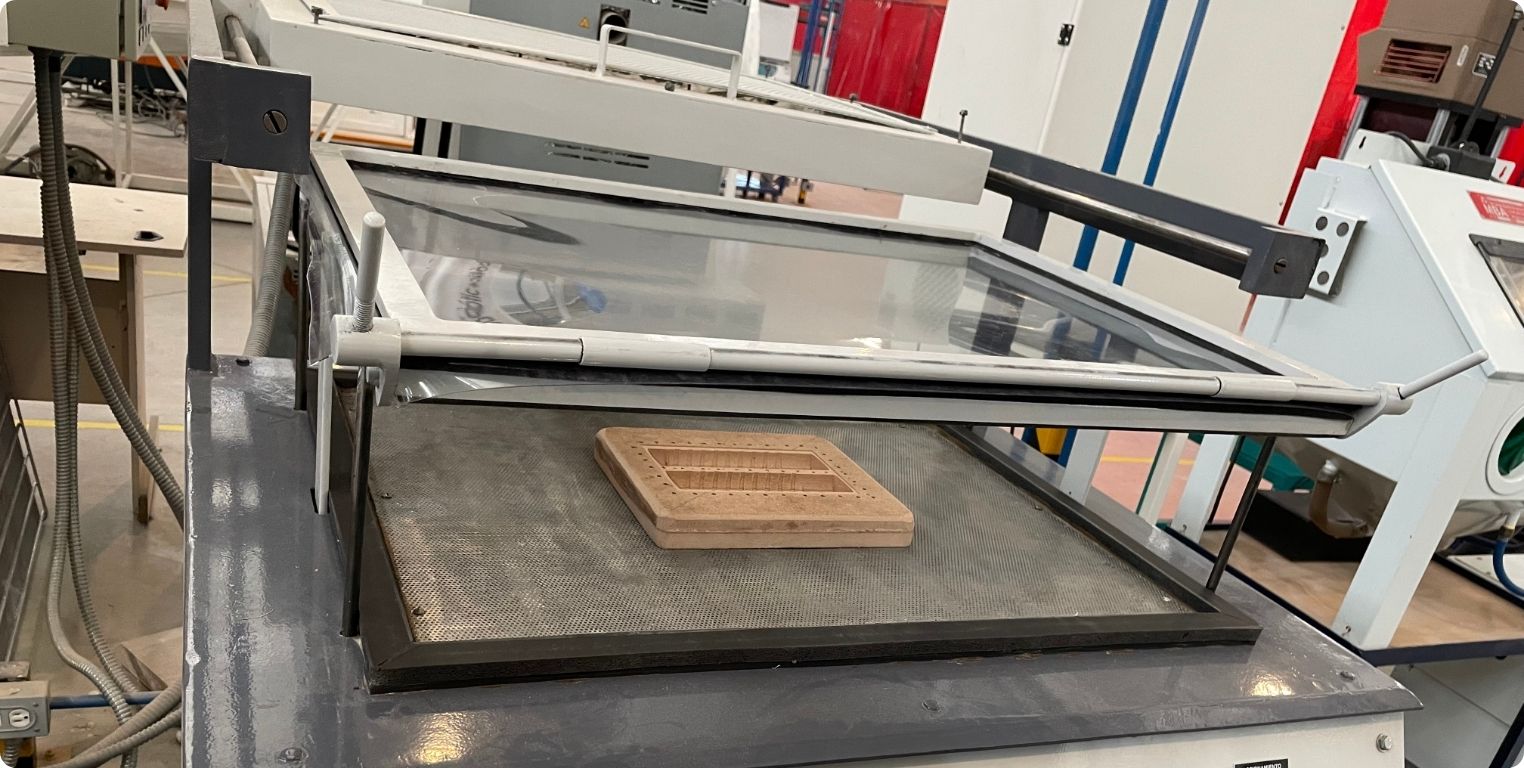
When it has reached the countdown, the white base is moved so that it is on top of the material and begins to heat it. This must be done carefully, as this is the part where the heating elements are already hot, so it is best to wear gloves.

I left a glove there for when I have to remove the base again.
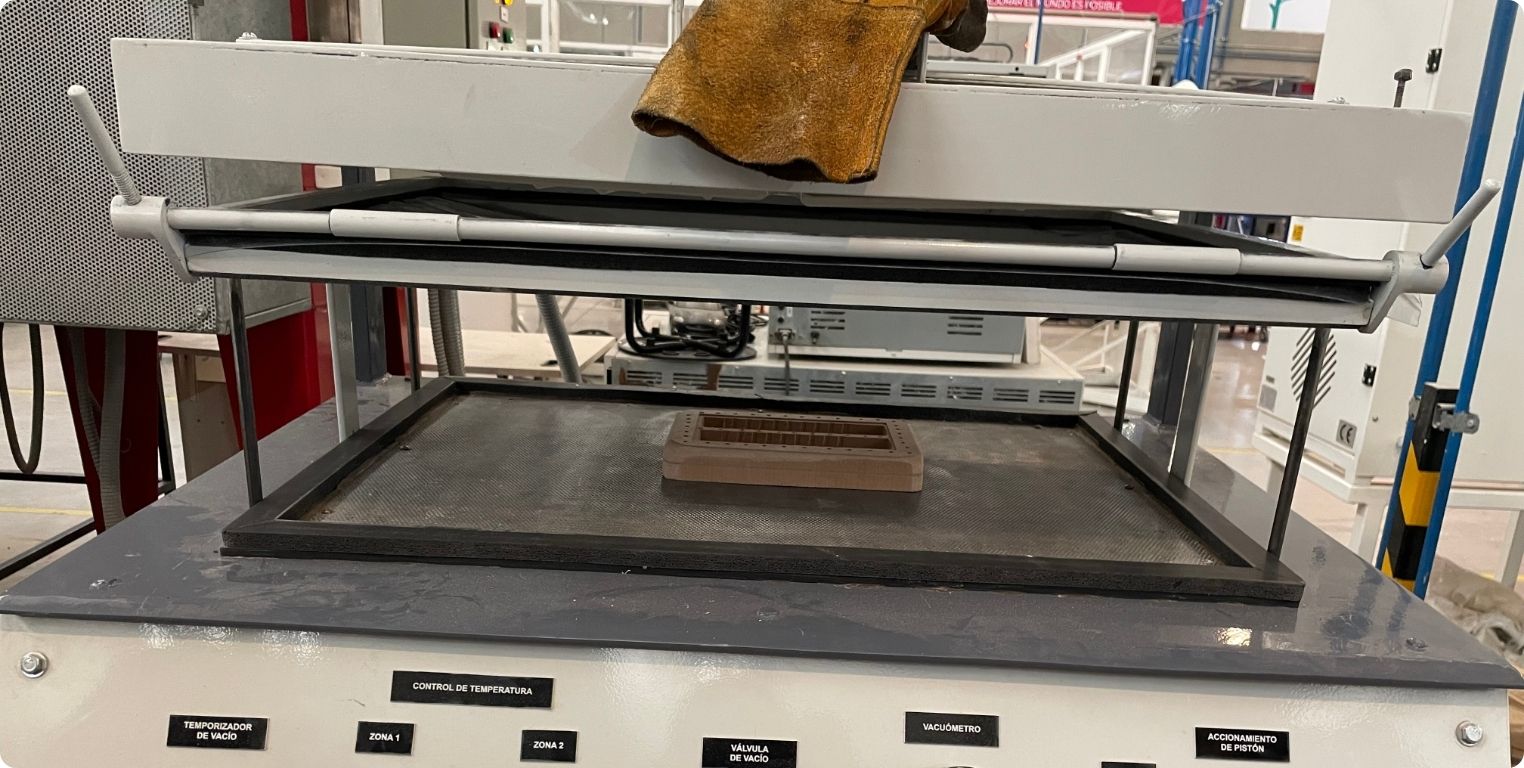
You have to wait until the material starts to hang considerably as in the photo.
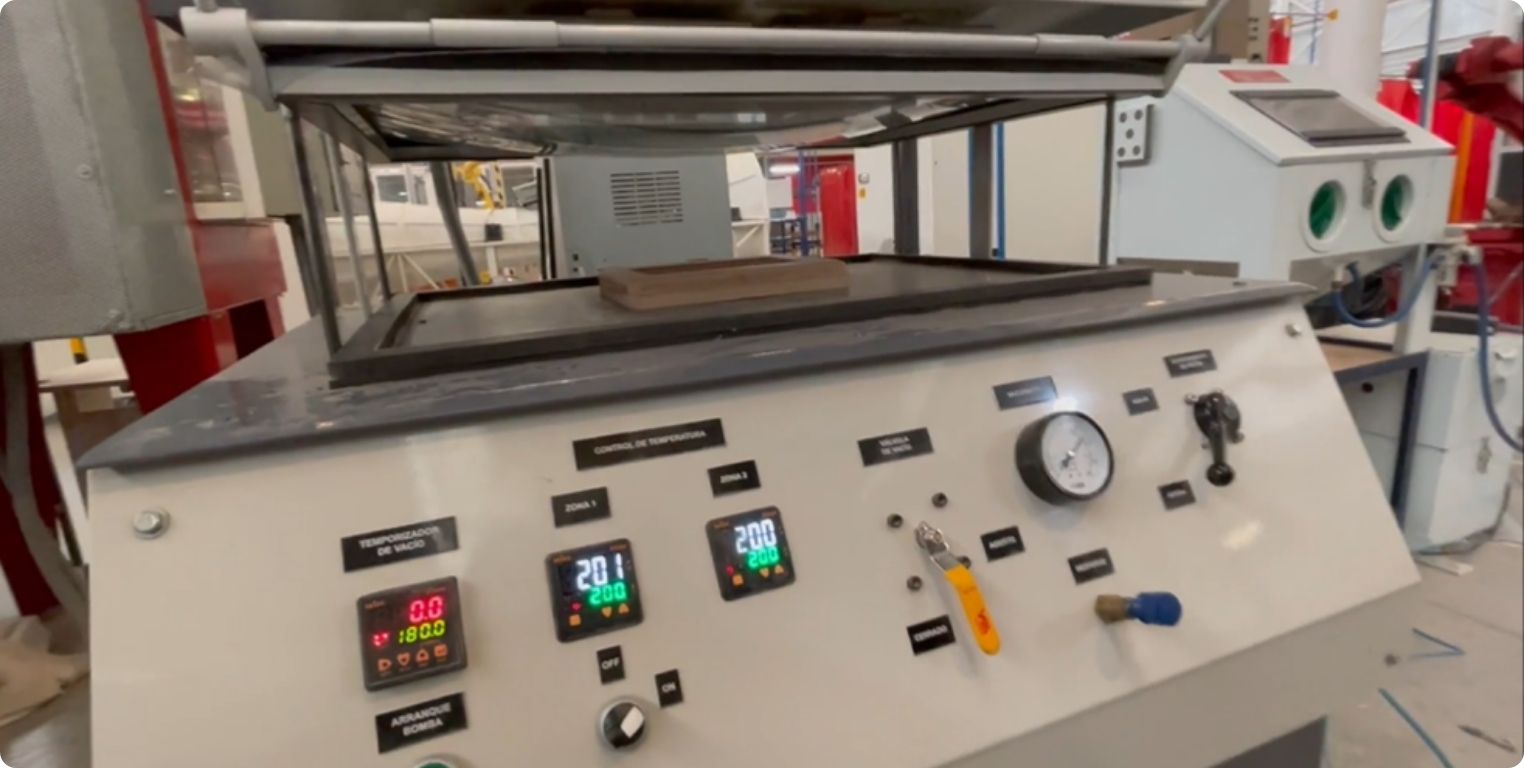
Once it is ready, the material is lowered by raising the black lever.
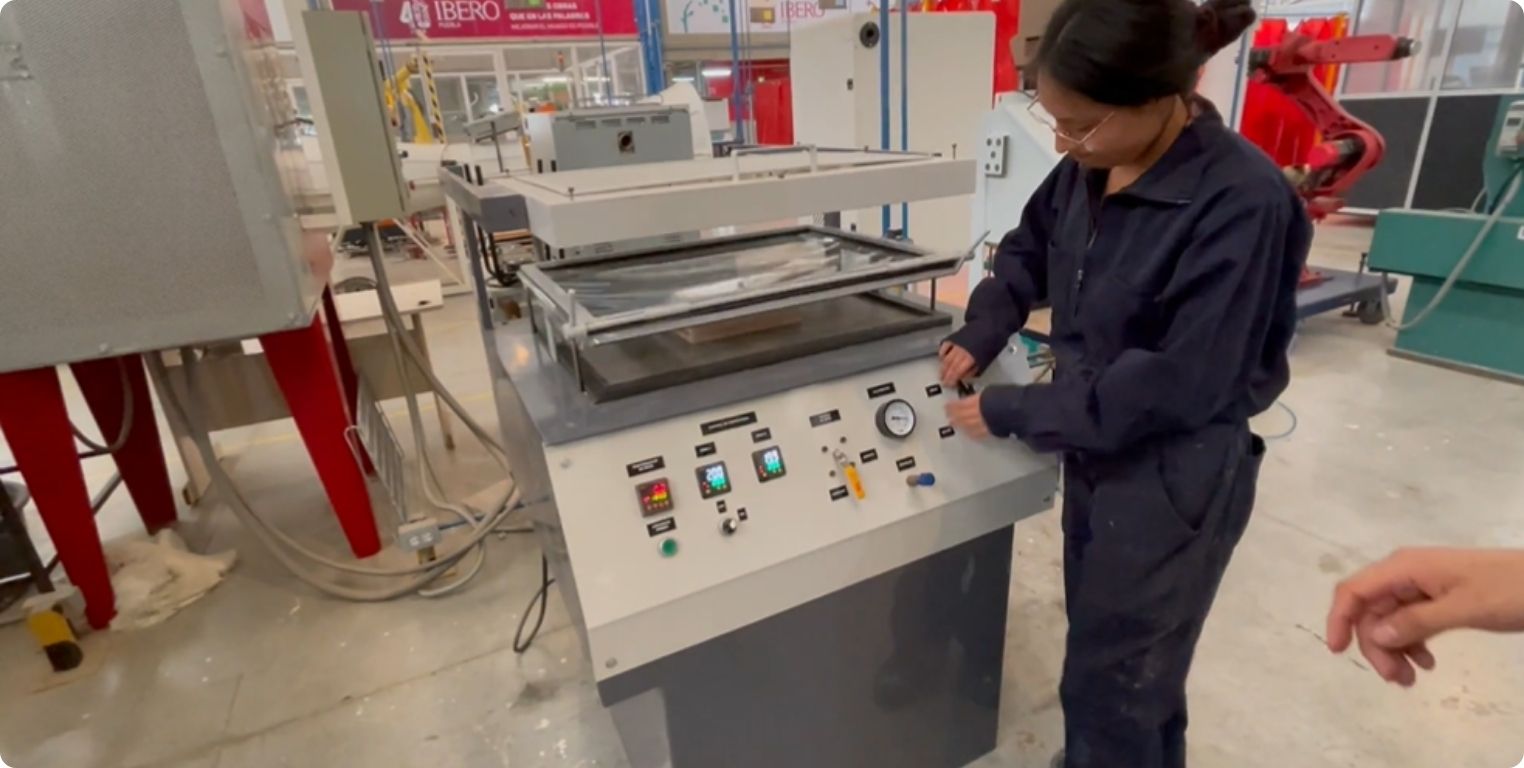
And to start the vacuum it is necessary to raise the yellow lever.
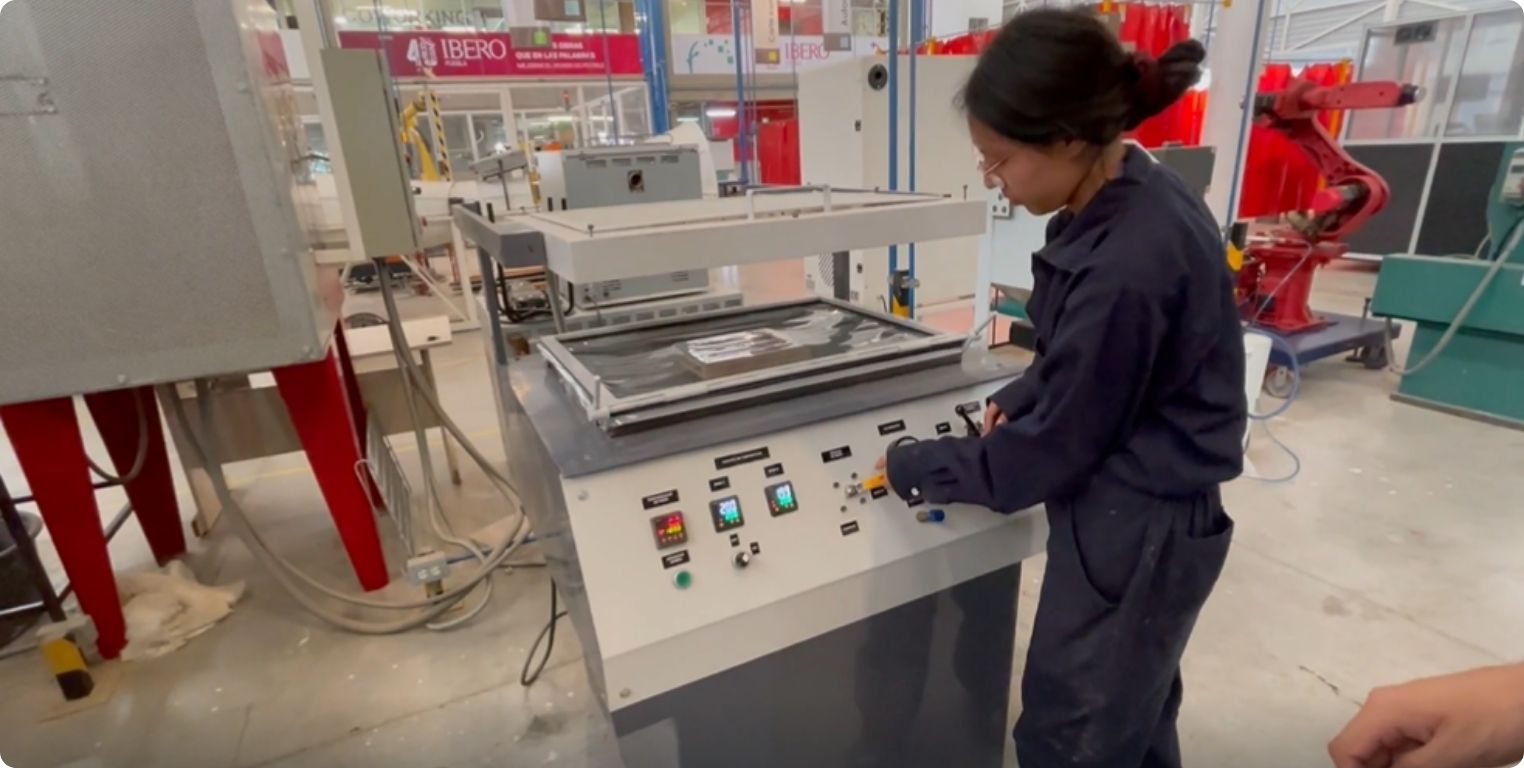
Something like this is seen after all the vacuum is gone. It is necessary to wait until it cools down, and for that the top white base is removed again.
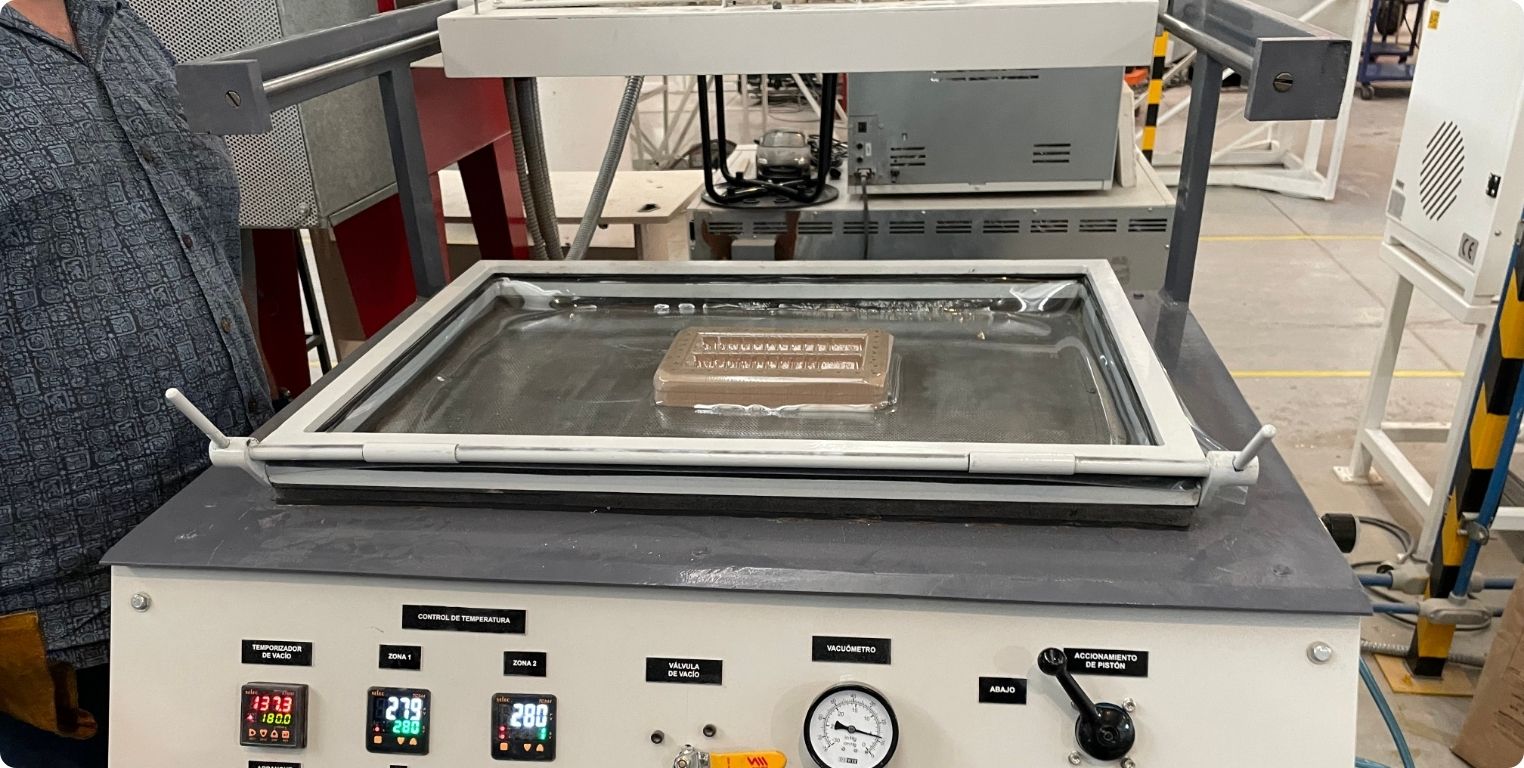
This is what a part looks like after thermoforming. With the help of a glove you can check if it is cool enough to remove it from the base.
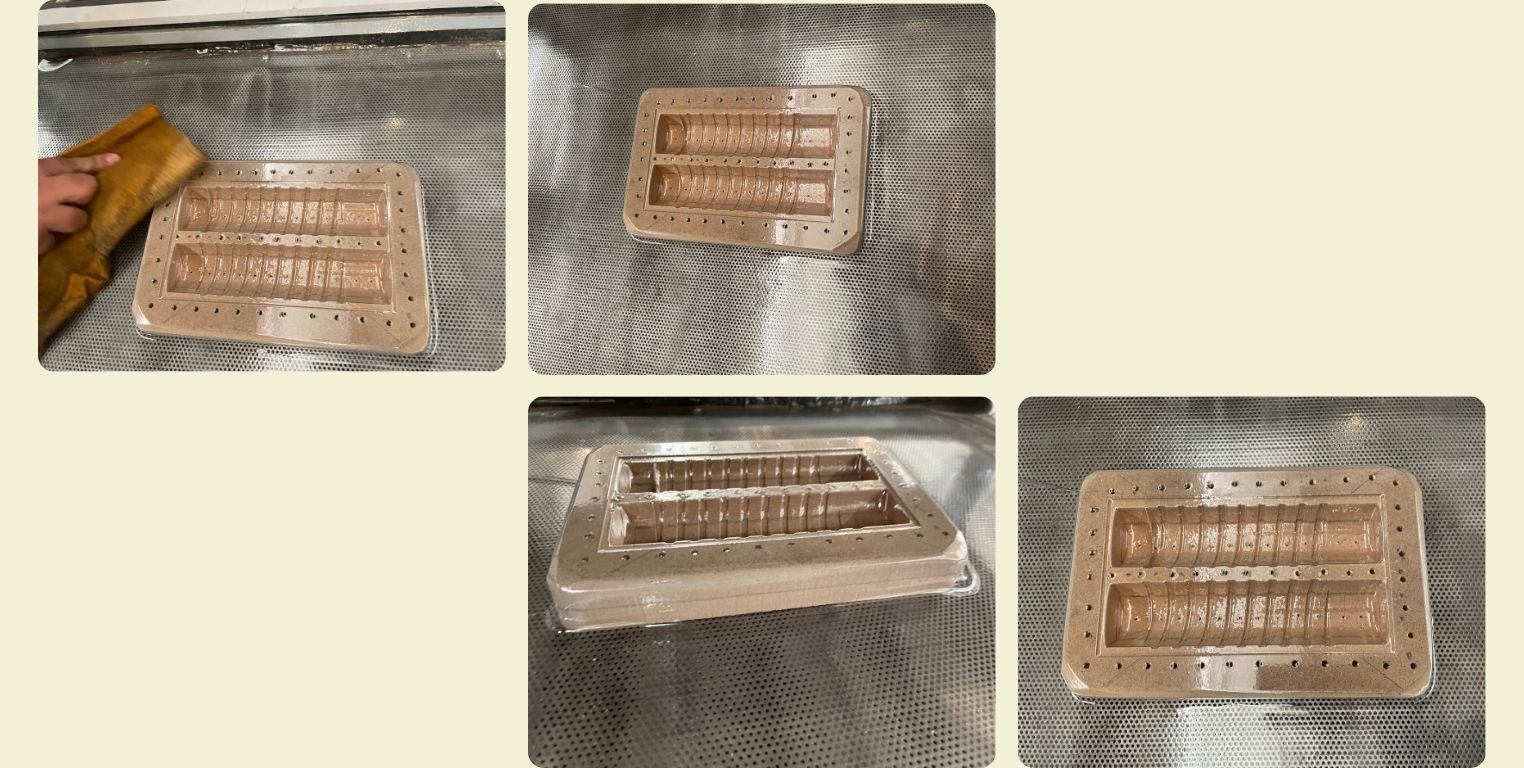
And although I explained it in a simple way and it seems that it came out the first, the truth is that not, here some photos of the trials and errors that had to happen before it came out successfully.
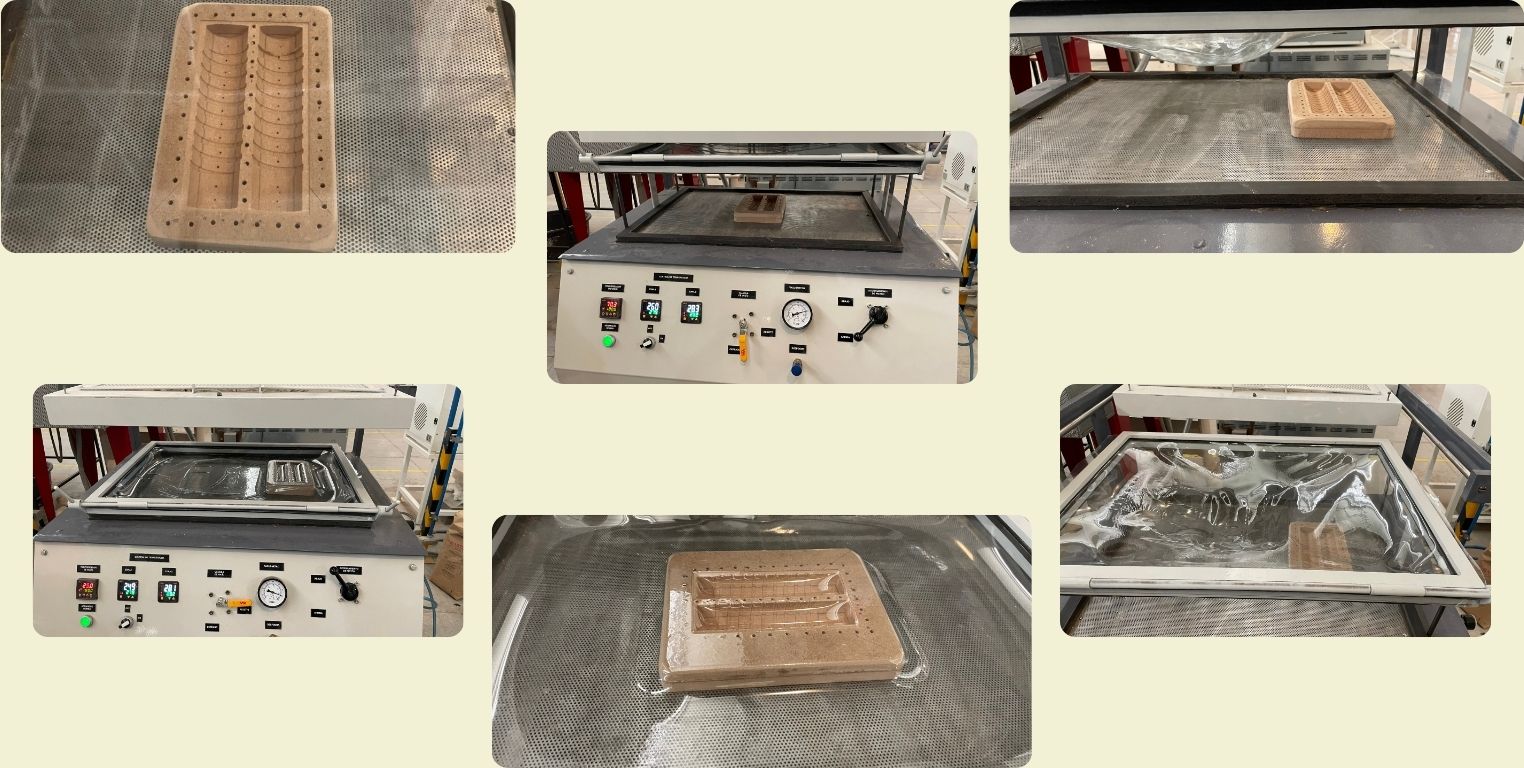
I also share with you a little video of me in this process.
The last thing to get the base (finally), was to remove the MDF piece, and start to cut little by little the two halves of the cylinder, and then join them into a small but nice PET cylinder. That's how it was ready for the neopixel strip.
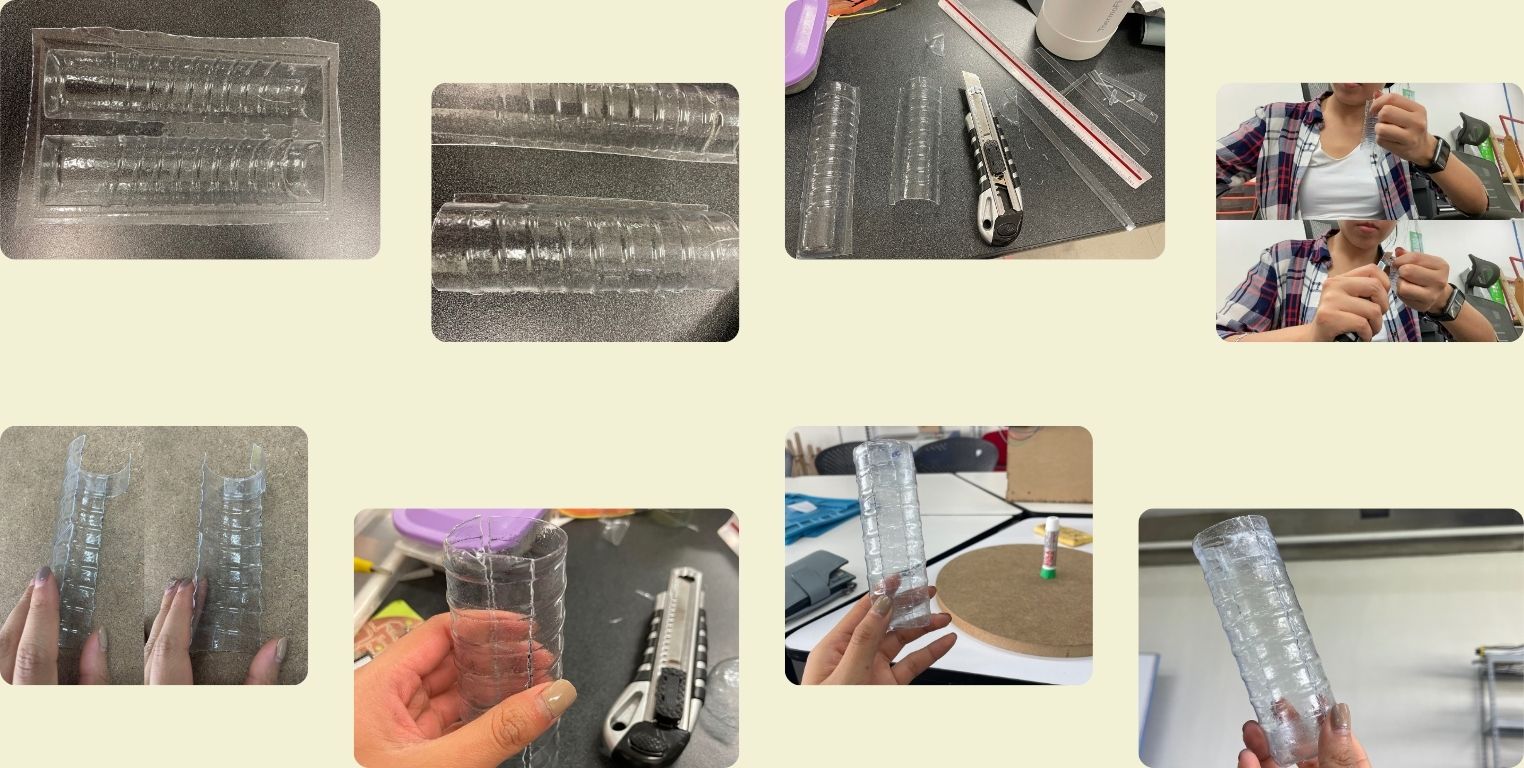
Final Proyect PCBs