Individual Assignment
✅
What will it do?
✅
Who's done what beforehand?
✅
What will you design?
✅
What materials and components will be used?
✅
Where will come from?
✅
How much will they cost?
✅
What parts and systems will be made?
✅
What processes will be used?
✅
What questions need to be answered?
✅
How will it be evaluated?
✅
Your project should incorporate 2D and 3D design, additive and subtractive fabrication processes, electronics design and production, embedded microcontroller interfacing and programming, system integration and packaging
✅
Where possible, you should make rather than buy the parts of your project.
✅
Projects can be separate or joint, but need to show individual mastery of the skills, and be independently operable.
Table of Content
Abbreviation
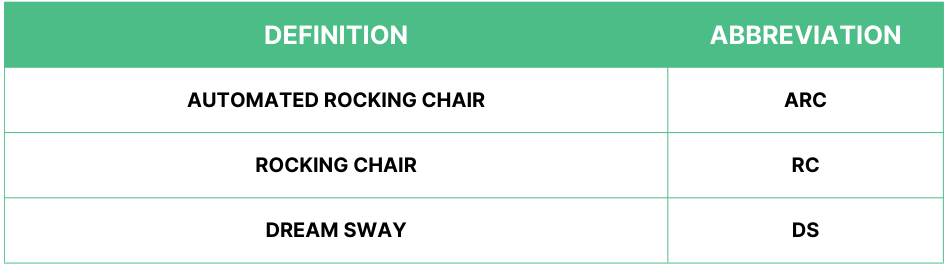
What will it do?
📢
My final project is an automated rocking chair [ARC] called Dream Sway [DS]. The plywood construction of the chair allows for automatic rocking by adjusting its center of mass. I must construct a mechanism beneath the rocking chair to alter the system's center of mass. A knob is used to adjust the amplitude of the swing.
Who's done what beforehand?
📢
I have searched for projects similar to my ARC using the Google and the Fab Academy search engine. However, I failed to identify similar projects. I have mentioned a few projects and works done by Fab Academy alumni that could be considered slightly similar to my project.
Project Related to Cradle
⬇️
Below is a link to Greg Buckland's automated cradle project.
Fab Academy 2015 - Greg Buckland
demonstrate 2D & 3D modelling capabilities applied to your own designs
CNC Machining Week
⬇️
The links to the documentation of the different rocking chair furniture pieces completed during CNC machining week is mentioned below.
W5 CNC Machining
MAS.863 HTM(A)A, Fall 2022
Make something big
I designed a rocking chair in Fusion 360. It can also flip up and became a small tabletop. I added small dog-bone structure for any straight inside corners and chamfer for easier fitting.
https://fab.cba.mit.edu/classes/863.16/section.Harvard/people/Liu/Week%205/week5.html
Landon Ferda
http://fab.cba.mit.edu/classes/863.18/Harvard/people/landon/hw5/hw5.html
Copplestone
Our assignment this week was to 'make something big'. The main machine available was the 5ft x 10ft Shopbot. We were provided with 4ft x 8ft sheets of OSB, a cheap wood chip board. I decided to make a rocking chair
Make Something Big
This week the task was to make something big using the shopbot. I decided to build a rocking chair although I ran into several design challenges that made a functioning rocking chair unfeasible for this week. First, I wanted to make some flexures in the wood for the seat and back of the chair to be one piece. I wanted this piece to press fit into two rockers that would hold it in place. I made a test design in Fusion 360 for some flexures.
https://fab.cba.mit.edu/classes/863.17/Harvard/people/joshuacoven/week5_big.html
MAS.863 How To Make (Almost) anything - Yoav Shterman
https://fab.cba.mit.edu/classes/863.11/people/yoav.shterman/rockingBench.html
Fab Academy
Computer-Controlled Machining
Group
1. Do your lab's safety training
2.Test runout, alignment, speeds, feeds, materials, and toolpaths for your machineIndividual
1. Make (design + mill + assemble) something big (~meter-scale)
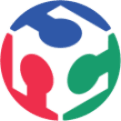
What will you design?
🏗️
For this project, the first and foremost work to be done is to fabricate the RC using plywood. This is one of the most challenging parts of this project. I have completed this task in the Computer-Controlled Machining week’s assignment (week 7).
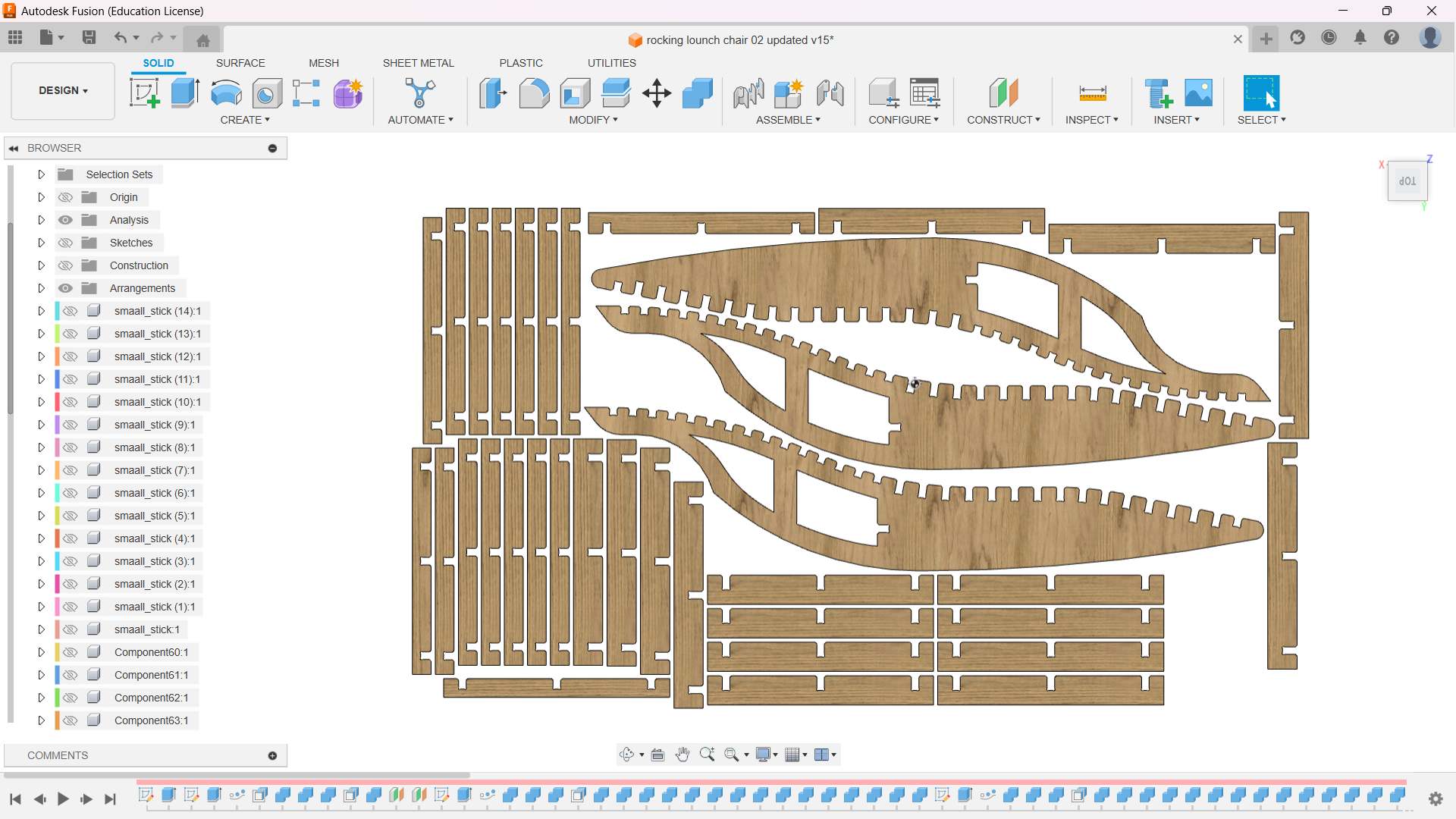
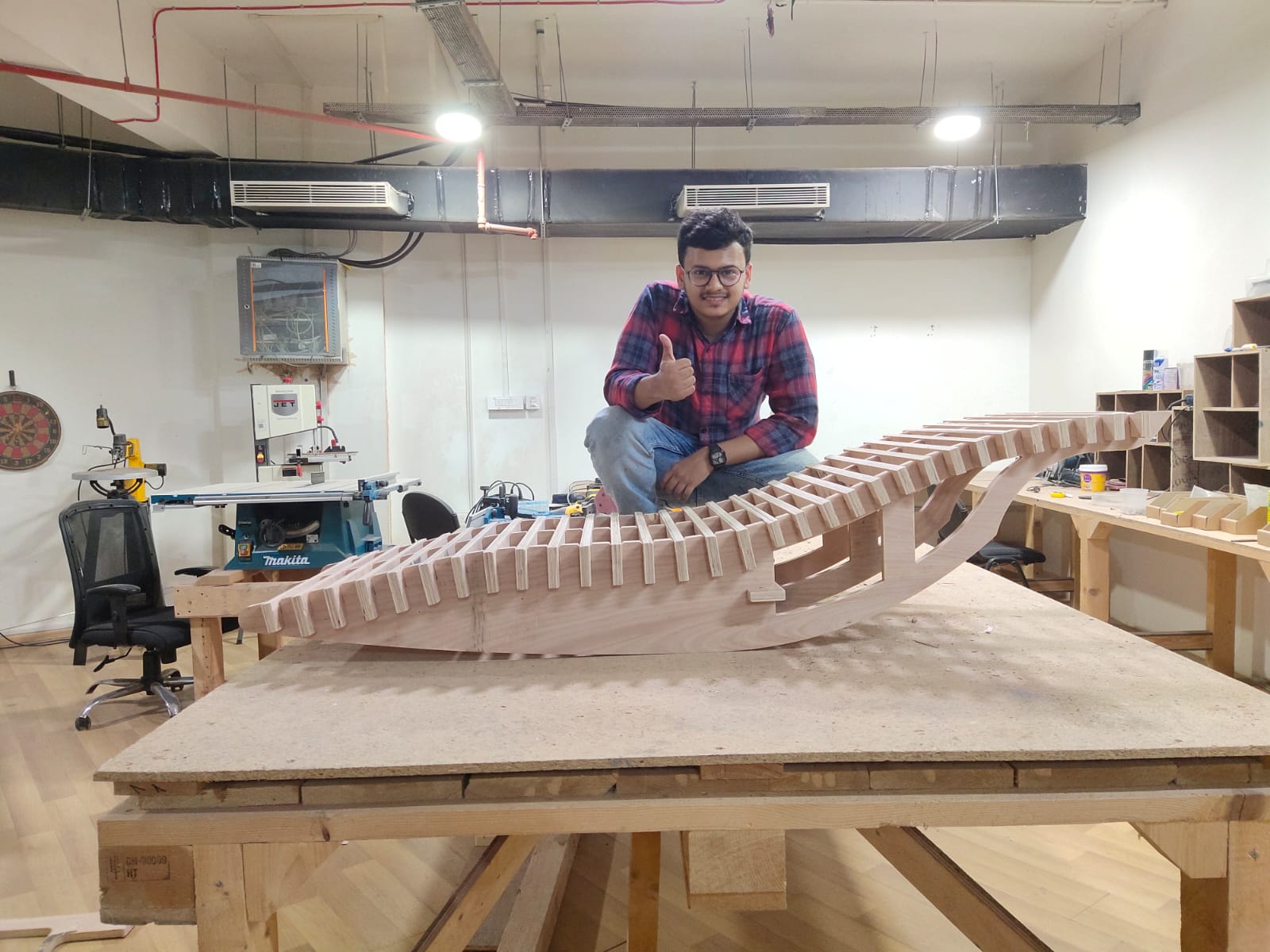
⬇️
For the detailed documentation follow the link below.
Rayan Abdul Gafoor - Fab Academy
© 2024 Rayan Abdul Gafoor. All rights reserved. Students Agreement.
🏗️
The next phase of the project involves developing a mechanism to change the system's center of mass.
🏗️
The final project requires the completion of the electronics design and production.
🏗️
Design a separate case for the PCB and MPU6050 accelerometer and gyroscope modules.
🏗️
Design the knob to adjust the amplitude.
🏗️
Finally, I need to design a logo for my final project and laser cut it on an acrylic sheet.
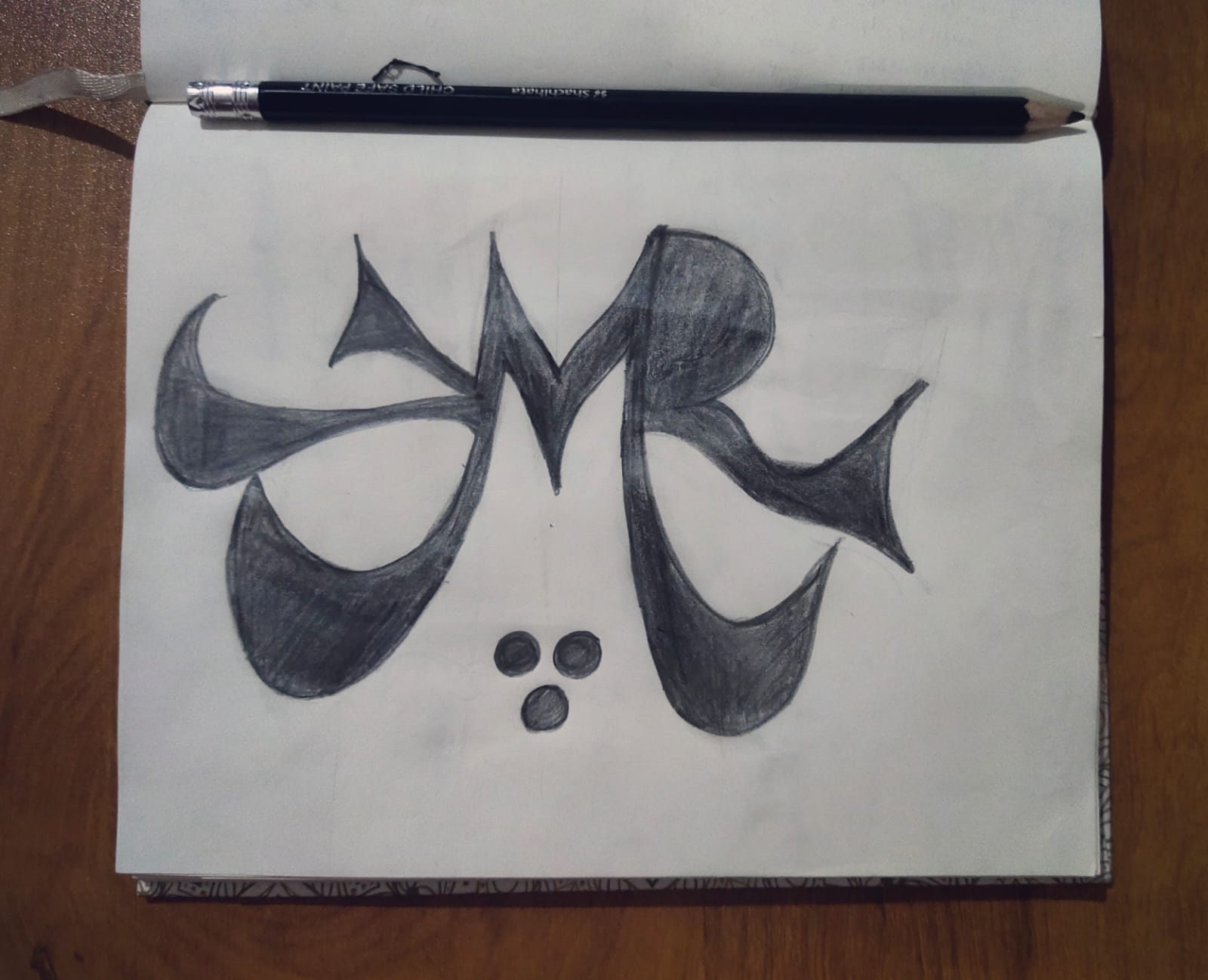
What materials and components will be used?
📢
I have listed the materials and components I will be using for this project below.
Rocking Chair
Material | Quantity |
---|---|
PLYWOOD | 1 sheet |
Linear Mechanism
Material | Quantity |
---|---|
PLA | UNK |
Components | Quantity |
---|---|
ALUMINIUM EXTRUSION PROFILE | 0.5 m |
ENCODER | 1 |
DC MOTOR | 1 |
MASS | 2 |
BELT | 1.5 m |
T-NUT | 15 |
M5 BOLT | 15 |
M6 BOLT | 10 |
PCB
Material | Quantity |
---|---|
Double Sided Copper Clad Laminate Circuit Board | 1 |
Components | Quantity |
---|---|
ESP32 | 1 |
MPU-6050 | 1 |
POTENTIOMETER | 1 |
MOTOR DRIVER | 1 |
BUZZER | 1 |
RESISTOR | 10 |
CAPACITOR | 6 |
LED | 3 |
MOSFET | 6 |
VOLTAGE REGULATOR | 2 |
PUSH BUTTON | 2 |
Logo
Material | Quantity |
---|---|
White Acrylic Sheet | UNK |
Red Acrylic Sheet Translucent | UNK |
Where will come from?
➡️
The majority of the components are available in the fab lab inventory. However, to control the DC motor, I took it from one of the unused automatic doors, and one of my instructors, Mr. Jogin, gave me the motor driver.
How much will they cost?
📢
I have listed the approximate cost and quantity of the components I will be using for this project below.
Rocking Chair
Material | Quantity | Price |
---|---|---|
PLYWOOD | 1 sheet | 2300 INR |
Linear Mechanism
Components | Quantity | Price |
---|---|---|
ALUMINIUM EXTRUSION PROFILE | 0.5 m | 500 INR |
ENCODER | 1 | 1000 INR |
DC MOTOR | 1 | 33990 INR |
MASS | 2 | 500 INR |
BELT | 1.5 m | 200 INR |
T-NUT | 15 | 225 INR |
M5 BOLT | 15 | 90 INR |
M6 BOLT | 10 | 60 INR |
PCB
Components | Quantity | Price |
---|---|---|
ESP32 | 1 | 262 INR |
MPU-6050 | 1 | 100 INR |
POTENTIOMETER | 1 | 14 INR |
MOTOR DRIVER | 1 | 2500 INR |
BUZZER | 1 | 15 INR |
RESISTOR | 10 | 20 INR |
CAPACITOR | 6 | 18 INR |
LED | 3 | 9 INR |
MOSFET | 6 | 24 INR |
VOLTAGE REGULATOR | 2 | 42 INR |
PUSH BUTTON | 2 | 24 INR |
What parts and systems will be made?
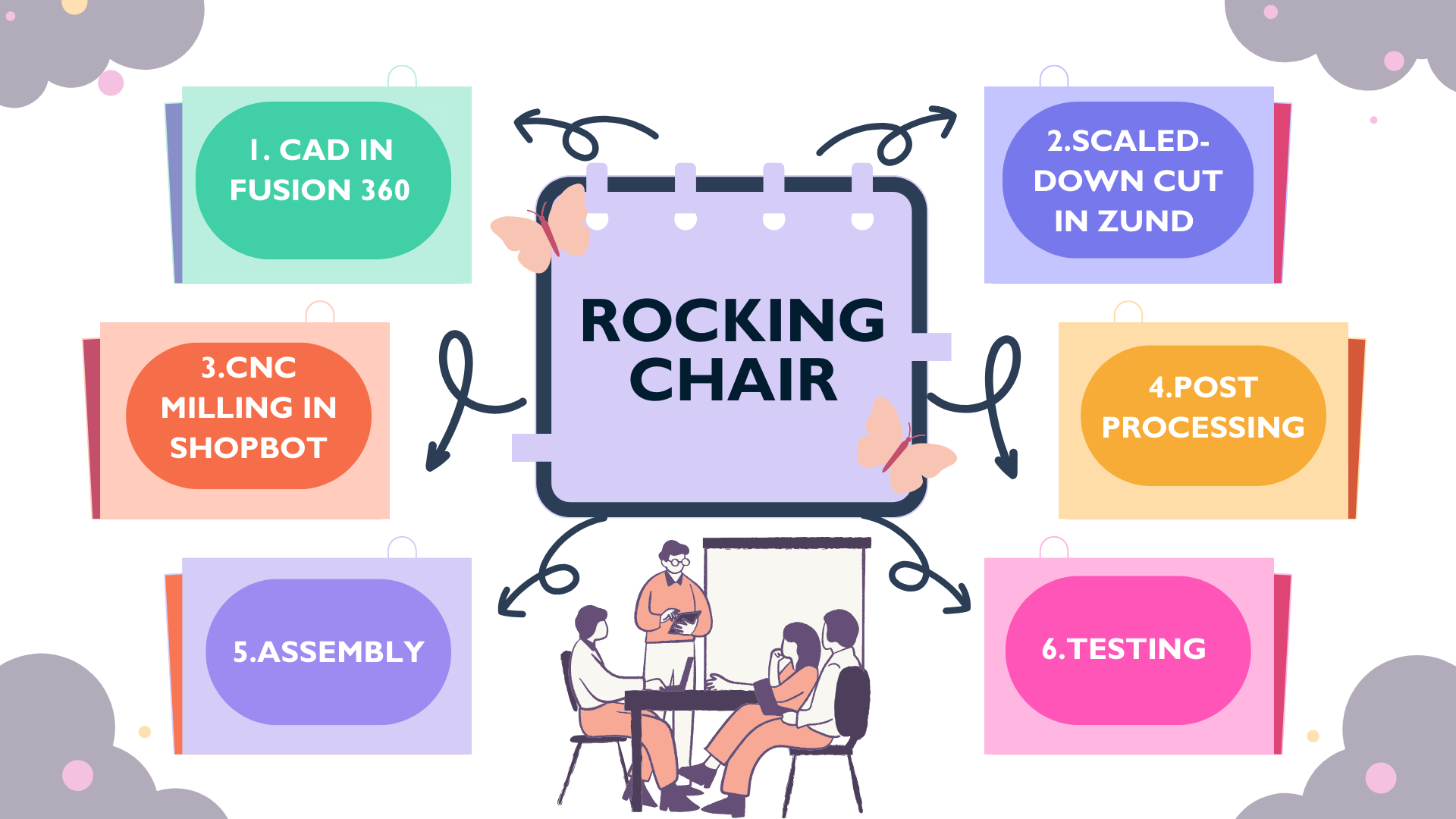
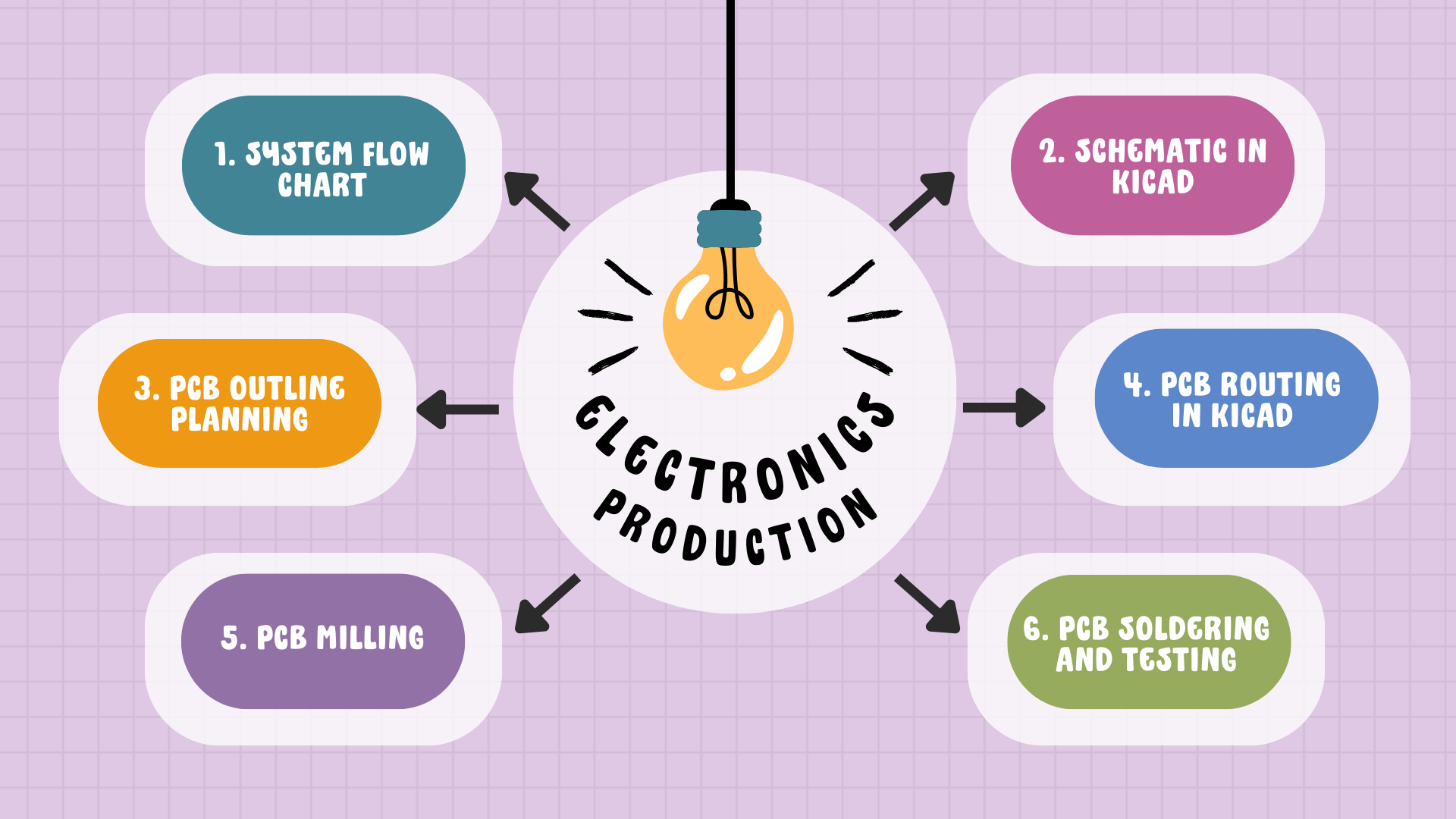
What processes will be used?
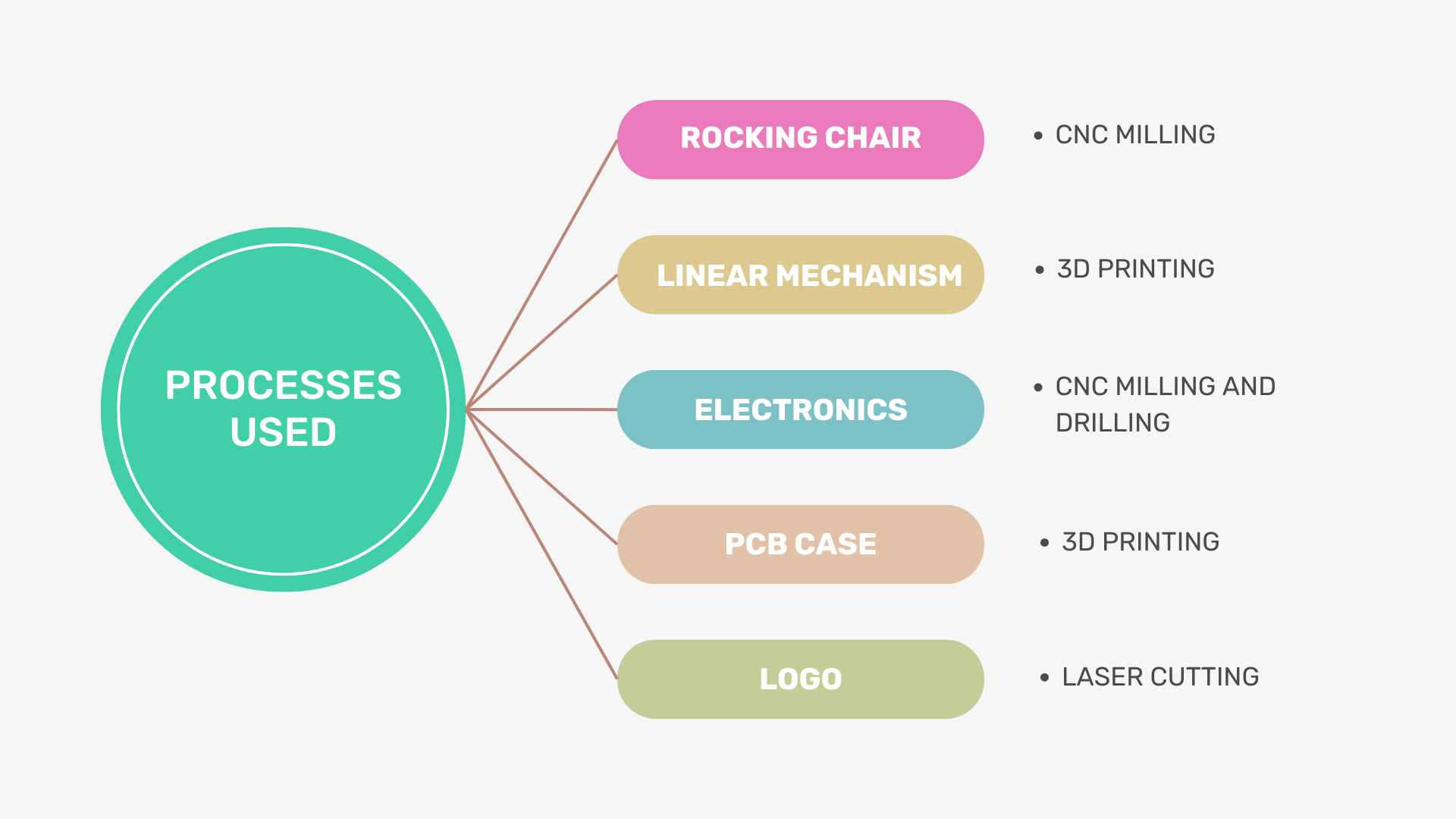
What machines will be used?
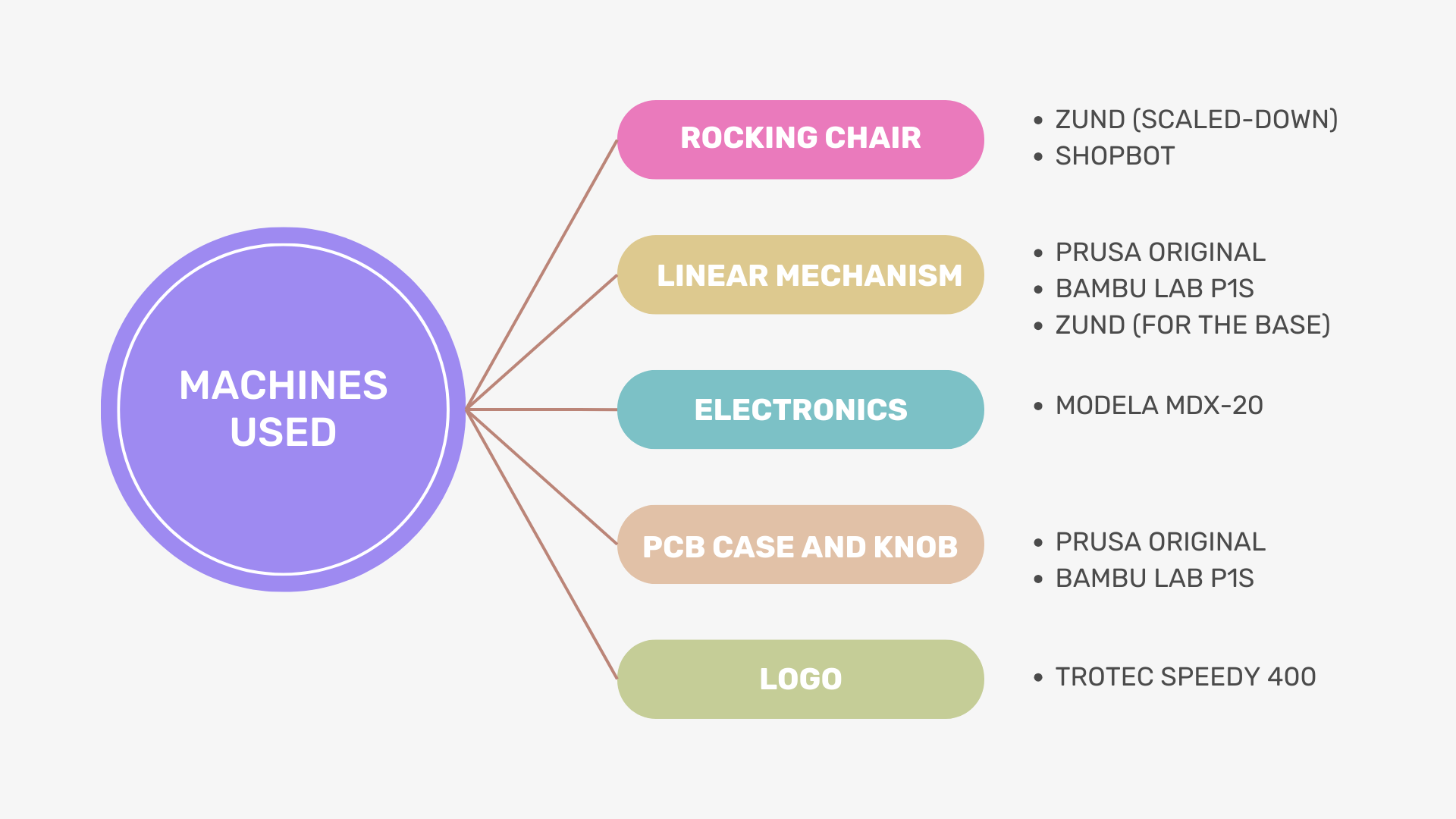
What questions need to be answered?
❓
How much mass is required to move linearly in order to change the complete system's center of mass ? 🏋️♂️ 🏋️♂️ 🏋️♂️
❓
Which motor do I need to use ?😵
❓
Is it necessary to make an H-bridge motor driver using MOSFETs ?🤔
❓
Is there any suitable motor driver available in our fab lab inventory or in the local market for my application? 🏬 🚶🚶🚶
❓
Which encoder can I use for the DC motor that I am going to use? Do I need to make one?
❓
Which microcontroller would be suitable for my application? 😵
❓
How do I change the amplitude of the oscillation? 😵💫
❓
Does my application require an interface? 🤔
How will it be evaluated?
✅
To effectively evaluate and answer the questions mentioned above, follow the steps below.
Mass to Change the System's Center of Mass
📢
Determine current mass distribution.
📢
Define desired COM.
📢
Calculate required mass movement.
Choosing a Motor
📢
Calculate the torque and speed needed to move the mass.
📢
Find motors with the required torque, speed, voltage, and current ratings.
📢
Consider motor type (DC, stepper, servo).
H-Bridge Motor Driver Necessity
📢
Assess if I need to control the direction and speed of the motor.
📢
Compare building an H-bridge with buying a pre-made driver.
Available Motor Drivers
📢
List available motor drivers in my fab lab.
📢
Ensure the drivers meet the voltage and current requirements of your motor.
Encoder for DC Motor:
📢
Define resolution and type (rotary, linear).Compare available encoders or integrated motor options.
Suitable Microcontroller
📢
List all inputs/outputs, communication needs, and processing power requirements.
📢
Compare available microcontrollers against my list of requirements.
Changing Oscillation Amplitude
📢
Identify how oscillation is being generated (e.g., motor, spring system).
📢
Modify the control signal or mechanical parameters to change amplitude.
Interface Requirements
📢
Identify the type and amount of user interaction needed.
📢
Choose appropriate interface elements (buttons, screens, communication modules).
Future Scope
🚀
The future scope of this project is that it can be implemented in various places. For instance, it could be placed in airport lounges, shopping malls, and other lounges. Now that this is a prototype, I am planning to make it into a product and implement it in one of the malls near my town.
🚀
In the market, the lounge chairs are really expensive, and when it comes to automation, the prices would be extremely high. Buying this type of lounge chair from the market costs me an arm and a leg. When it is fabricated in a fab lab, it is very cost-effective and can eliminate the service charge, GST, etc.
🚀
I am planning to further develop this project by adding a cushion and implementing an interface feature that allows users to connect online, adjust, and monitor.
License
The work mentioned on this page is licensed under a Creative Commons Attribution-NonCommercial-ShareAlike 4.0 International License
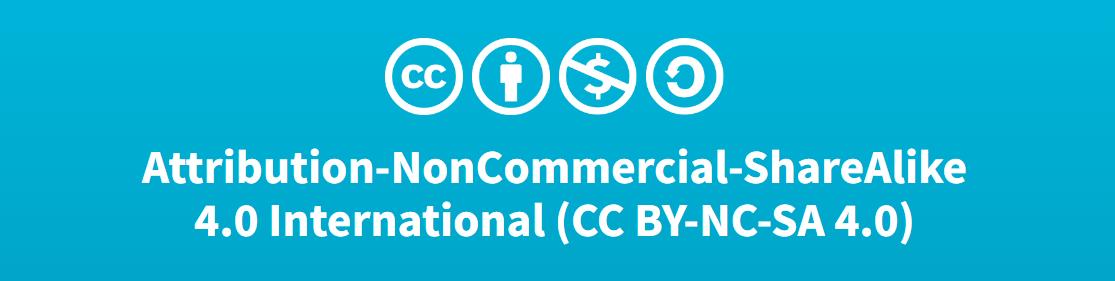