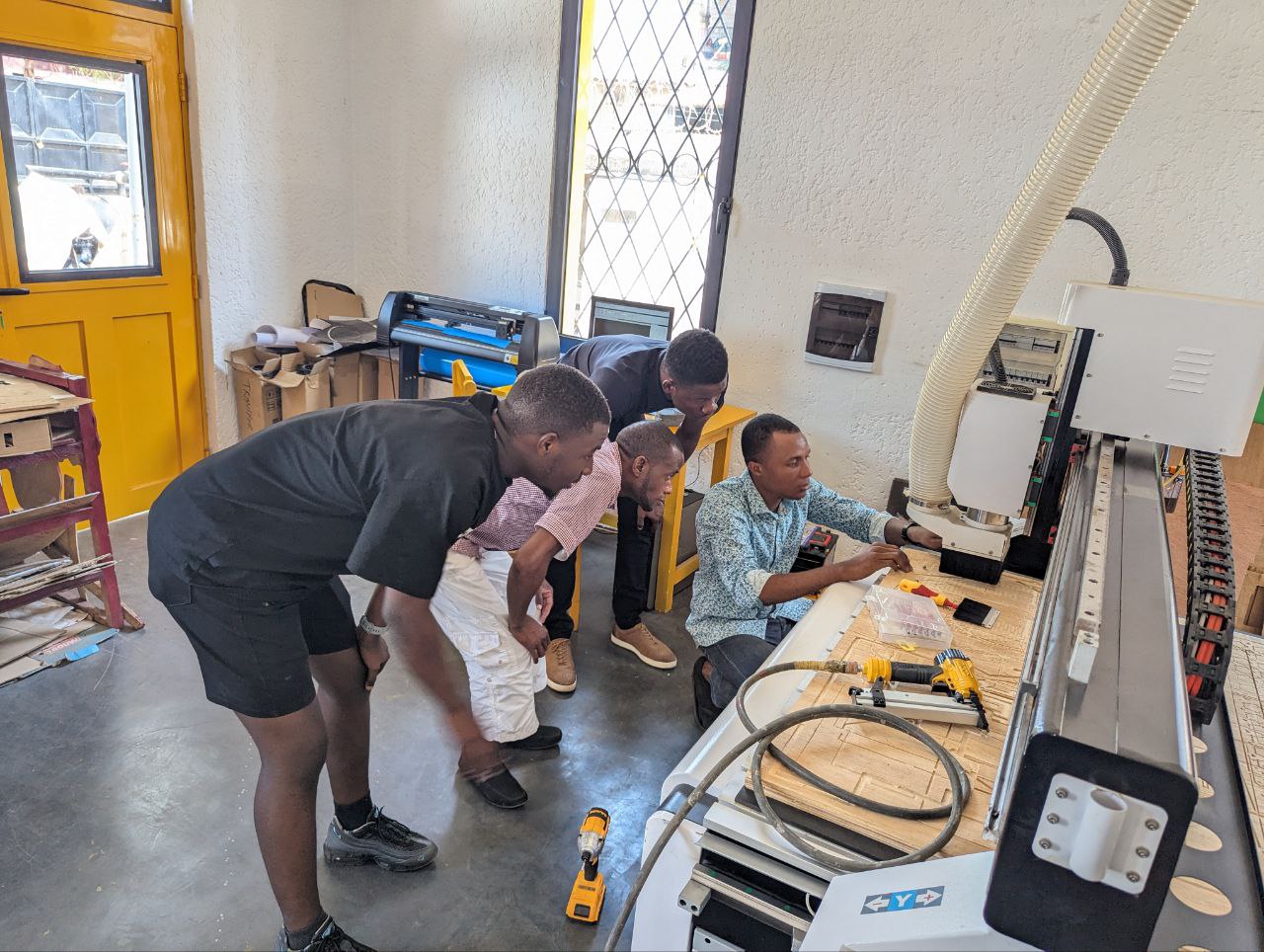
Group assignment:
We used our “Big Bertha” CNC to complete this group assignment, and you can find more information and features here
Safety
For the safety training, It is very important that to put on safety personal protective equipment like:
Safety glasses to protect our eyes Ear plugs to block loud noises ,leather gloves to prevent splinters when handling the wood pieces. Also wear a blouse. Make sure the blower and water pump were working to avoid any fire hazards.

Runout
We performed the runout test on the Spindle to know the amount of runout error it had. CNC spindle runout refers to the amount of deviation or wobble in the rotation of the spindle. It affects the accuracy of machining operations, with higher runout leading to reduced precision. Minimizing runout is crucial for achieving precise cuts and maintaining consistent quality in CNC machining processes.


Speed and feed rate
Speeds and feeds are the cutting variables used in every milling operation and vary for each tool based on cutter diameter, operation, material, etc. reference. With large format CNC machining, the speed and feed can be calculated knowing the chip load. the number of flutes on the bit, and the spindle RPM.
An easier method to determine speed and feed is using an online calculator such as the one given at this link here. An image of the calculator is shown below.

For our group assignment, we calculated and test the speed and feed using the calculator above for plywood with a 1/4” bit and a spindle speed of 20000 RPM.
Fixturing
To fix materials on our CNC, we use a pneumatic nailer or screws.

Materials
With our CNC, we mainly cut wood and Plexiglas.

Alignment
As part of our teamwork, we had to carry out an alignment test on our CNC machine to check the alignment of our rails. The rails on our CNC machine provide the X-Y-Z axis movements. If the machine doesn’t pass this test, this will result in a right-angle milling alignment problem. To carry out this experiment, we simply created a square plate (100 mm x 100 mm and 141.4213 mm diagonally) in Fusion 360 and milled it on the machine.
Milling | Parameters |
---|---|
Spindle speed | 20,00 rpm |
XY feed Rate | 200 mm/s |
Z feed rate | 5 mm/s |




Joints
Before finishing, we also talked about joints and dogbone and Tbone.

