19. Invention, Intellectual Property and Income
Dissemination of My Project
This is the license I plan to use for my project as I like the idea of people following the instructions and using the provided files because it makes it more accessible..You are free to:
Share — copy and redistribute the material in any medium or format
Adapt — remix, transform, and build upon the material
Under the following terms:
Attribution — You must give appropriate credit, provide a link to the license, and indicate if changes were made. You may do so in any reasonable manner, but not in any way that suggests the licensor endorses you or your use.
NonCommercial — You may not use the material for commercial purposes.
ShareAlike — If you remix, transform, or build upon the material, you must distribute your contributions under the same license as the original.
I really like the range of processes in my final project however I want to make the spinner easy to produce and potentially post. The idea is to make the machines condense and streightforward enough that they can be made with a 3D printer considering how common they are from files and any key extra componants like the pcbs and bearings flatpacked and easy to post.
I want to lower the cost barrier to entry of these machines.
This does require redesigning the spinner but there are a few points I need to fix with my final design.
Key changes
I plan to change the inrunner motor to be a outrunner moter as they are much easier to mount, usually with 4 bolts that can be slots to adjust belt tension. This allows the motor to be shorter which was one of the main limiting dimentions. I will also get a less powerful motor as I did not nearly need all the 2600Kv. Kv is the motor velocity constant, RPM per volt and this was at a ratio of 1:4 which will be reduced in this version as well. There will likly be another pully 3D print pressfit onto the outside on this outrunner motor instead of using an existing pully.
Depending on how things work it may be possible to reduce the power requirement if a 3v or 6v motor could be usable. Possibly using a power QC hack or a high power USB-C cable and power delivery but this could be quite tricky.
ESCs tend to be quite bulky and majority of them only go forward. I would accept only going forward in this second version but there is a possibility of creating our own ESC and making it fit the form factor of the machine. This will simplify the machine to having the motor attach to the board which contains the microcontroller and other components. By creating out own ESC it will allow us to control the phases directly and therefore the direction.
I would highten the walls, possibly putting the motor under the drum to raise everythin up so that a larger bobbin can be used. The bearings could be pressfit into these walls similar to those I used during machine building week.
There is a slight issue of how to mount the hubs securly whilst keeping them a slim formfactor. Possibly some sort of right-angle bracket into a baseplate that they both stand on.
Rough Design
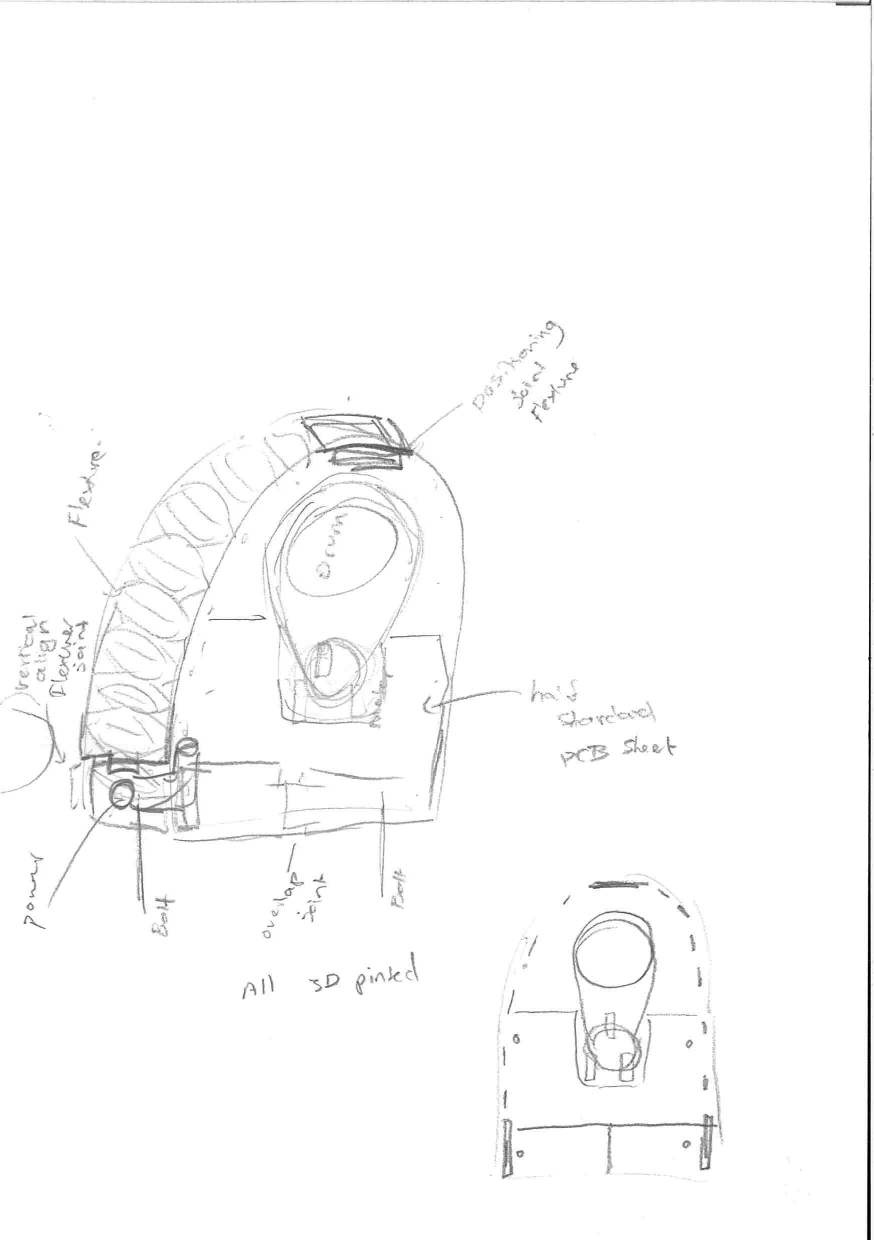