The design of the puzzle piece was parameterized, the thickness of the material was chosen to be able to change and calculate
the kerf of the piece at the time of cutting, For this I use the Spreadsheed which is an excel file that allows us to create variables,
assign them a unit of measure and an alias, in order to place the restrictions
Finally the file is exported to DXF to be able to be opened with the laser cutter program, in my case it is RDWorks
Problems found
Initially because of my little experience in handling design programs, I am inclined to think that FreeCad, due to its easy
interface and intuitive tools, was the right choice for parametric design. But in my first attempt I made several mistakes,
the first one did not place all the shape restrictions, this causes that when the size of the piece varies it is deformed,
You can verify it by downloading the file and changing the size of the part in the SpreatSheet.
Second, I include two pieces in the same design, this makes it even more difficult to control the restrictions, and finally in the
end you have so many restrictions that it is a real headache to understand what is happening with the design, As a recommendation, use different sketches
Solid works
Now with a little more experience, really not much .... lol, after several weeks and with the arrival of the laser cutting machine to the
laboratory I have been able to carry out more tests, and try other programs such as solid works
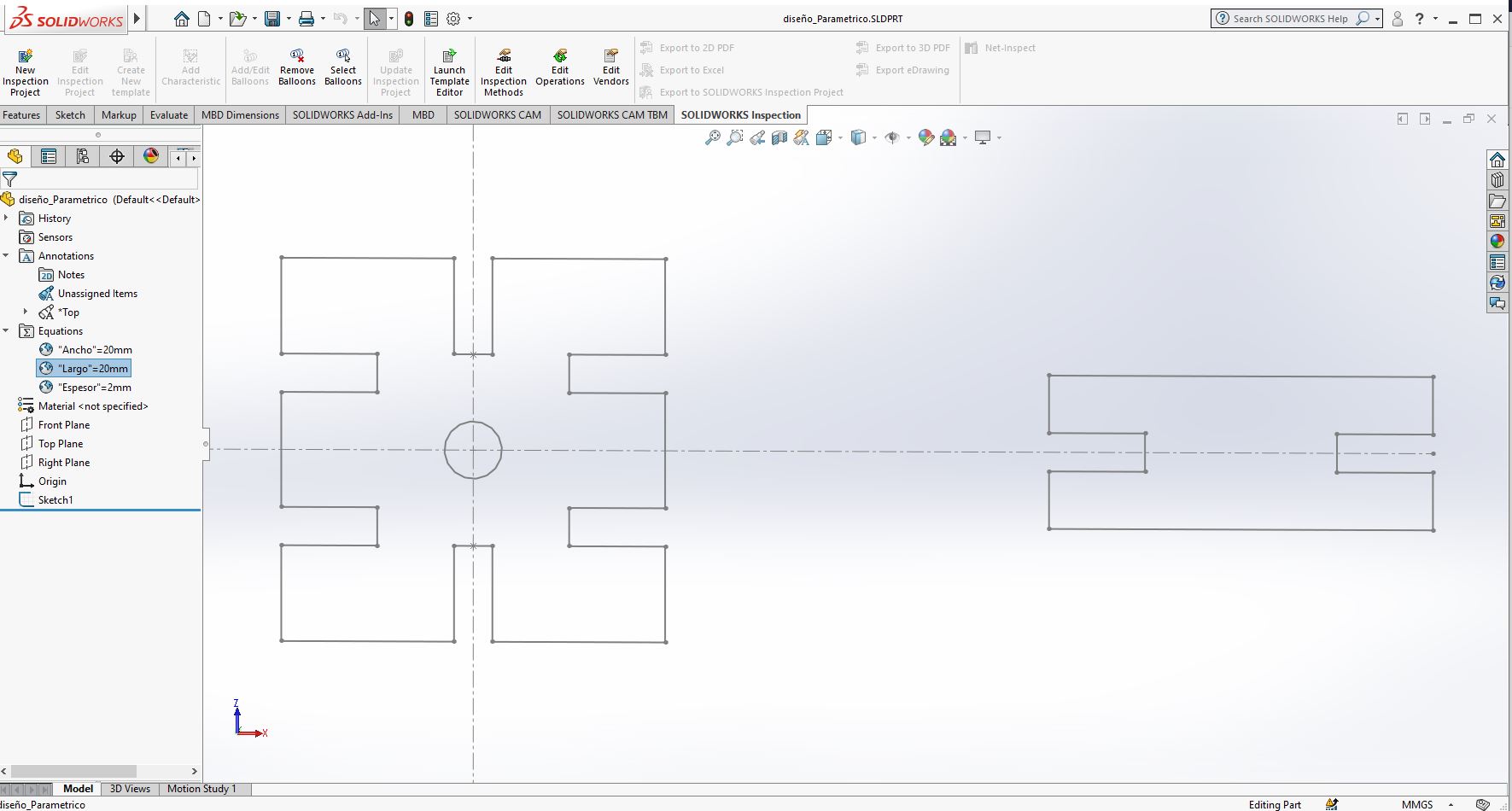
To start with the design, I drew the basic shape of the piece, in this way we will place the restrictions on the general geometry
Then I continue to place the constraints on the different segments that shape the puzzle.
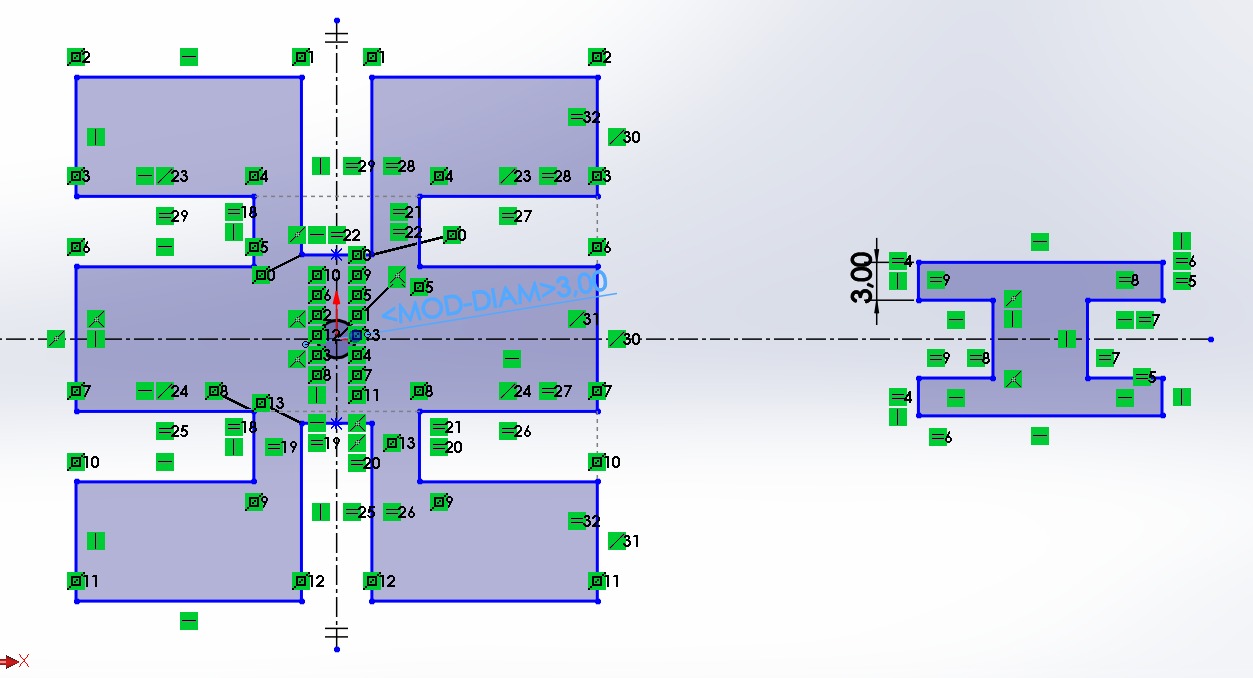
Finally I created the Spreadsheed file something similar to freeCad, Solid Works can define variables these are created
in the equations folder, in which the final restrictions are defined, these restrictions will parameterize our puzzle, in
this file I defined the size of the piece as well as the thickness of the material to be cut by the laser cutter.
Conclusion
Although freeCad is quite intuitive, there are other tools. that although they seem more difficult
to learn at first. They will allow us to have a better control of our designs, these tools can be Rhino + GrassShoper or SolidWorkss
Kerf is defined as the width of material that is removed by a cutting process. It was originally used to describe how much wood was removed by a saw,
because the teeth on a saw are bent to the side, so that they remove more material than the width of the saw blade itself, preventing the blade from
getting stuck in the wood.
Kerf width is a measure of how much material is removed.When talking about CNC shape cutting with typical cutting processes, kerf is the width of material
that the process removes as it cuts through the plate.
Over the years I’ve heard some people use the term when referring to the angle on the edge of the part, but that would be an incorrect use of the word.
The “cut angle” on the edge of the part makes measuring the kerf width sorta tricky, but for consistency, the word “kerf” should only be used when talking
about the actual cut width.