Moulding and Casting.
For the assignment of the 10th week: Moulding and Casting, it will be divided into 6 parts: 3D Design, 3D machining, Moulding, Casting, Group assignment and Download.
3D Desing
For this week, I made a replicated the head of Bender, from Futurama series by Matt Groening, because it is necessarily made a 3d design with some curves.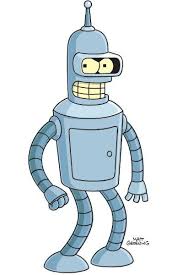
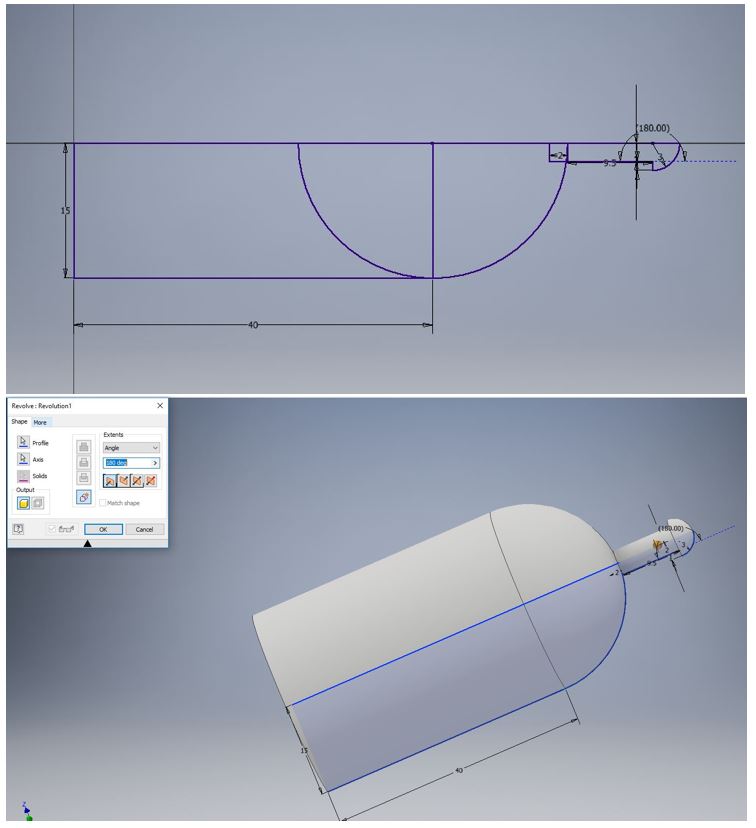

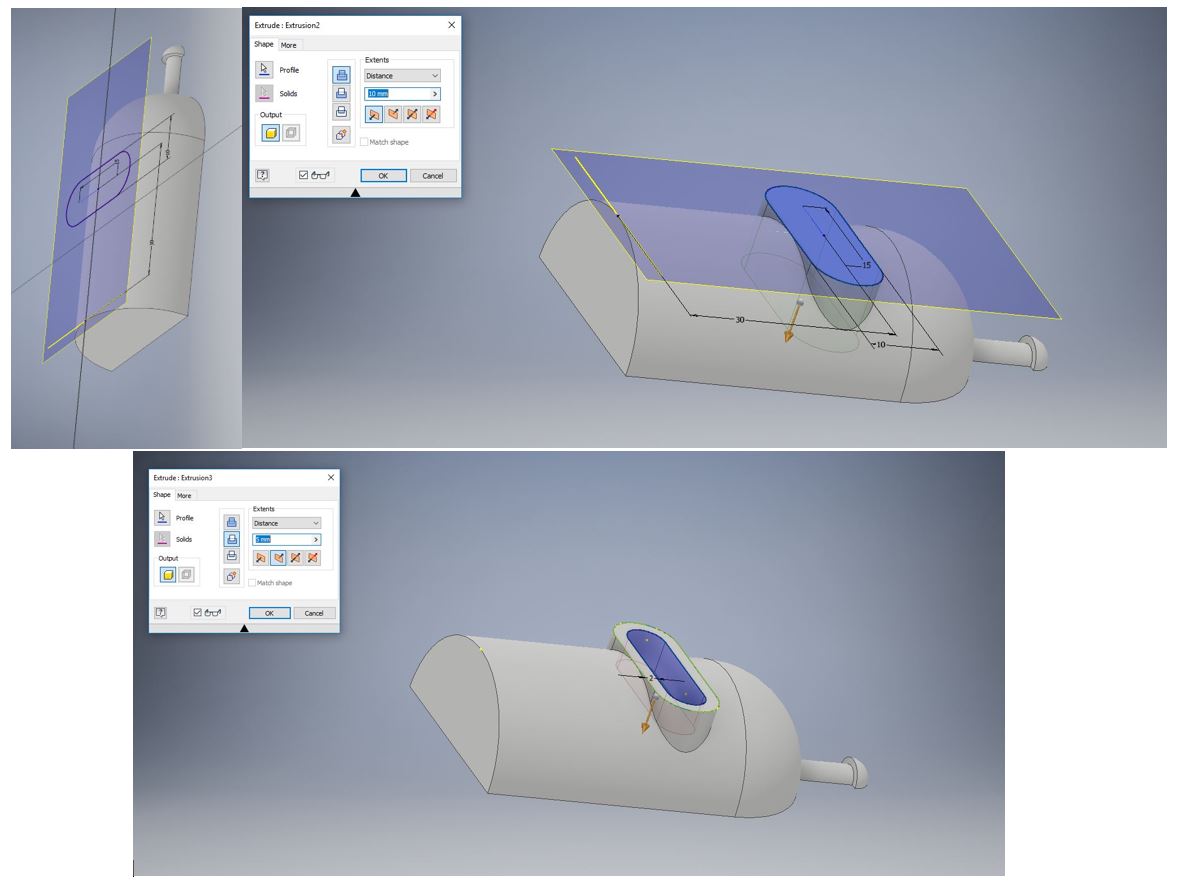
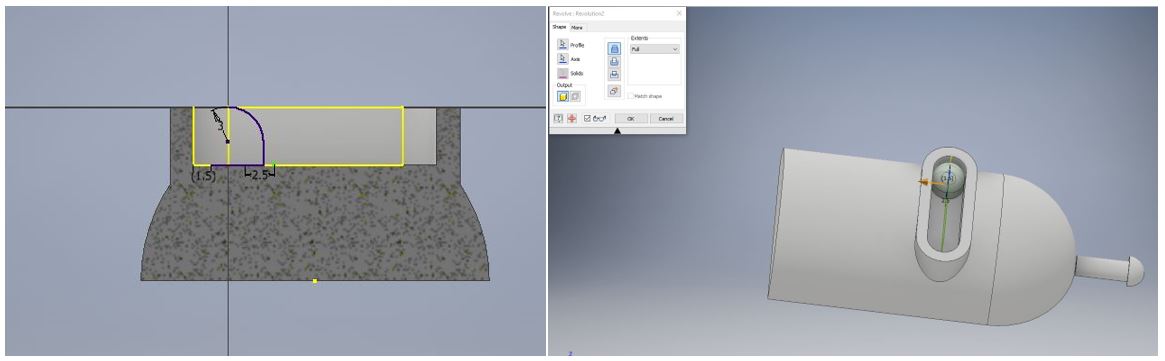
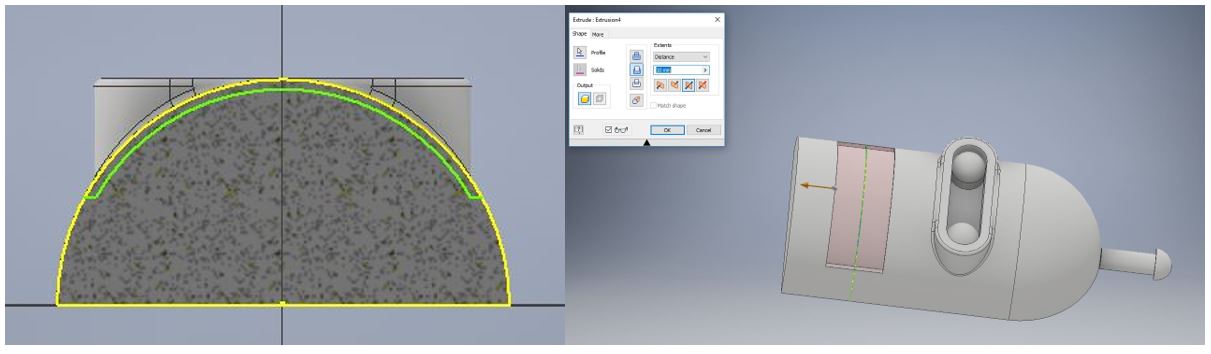
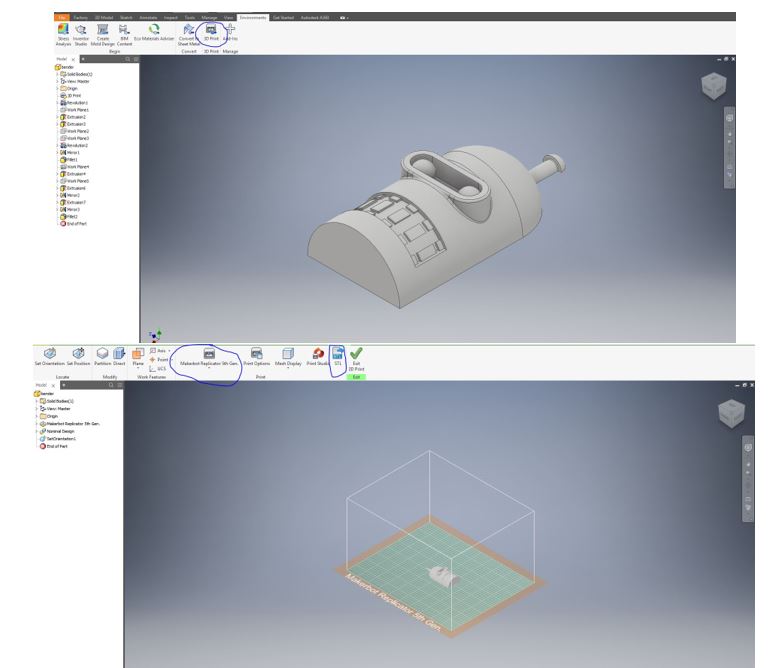
3D Machining
Material
To create the positive of the mold, a block of blue machinable wax with the dimensions of 77 mm x 160 mm will be use.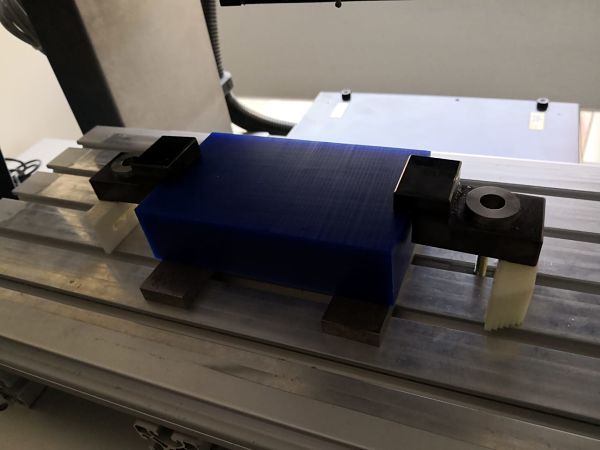
Machining
We use the Roland mdx-540 machine with the SRP Player software to perform the positive machining of the mold. The first step is to indicate the measurements that our design will have, in my case is this size:X | 30mm |
Y | 67.5mm |
Z | 15mm |
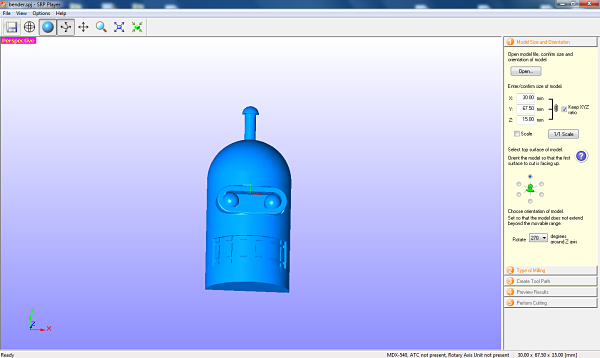
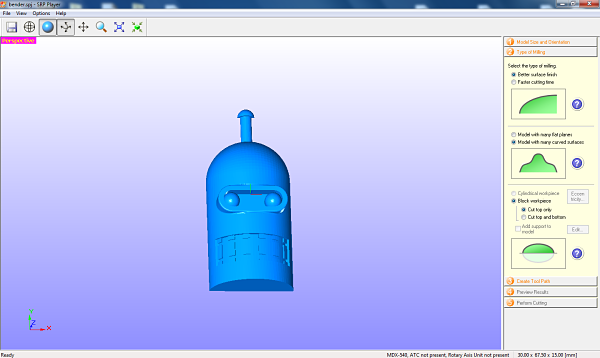
X | 55mm |
Y | 82mm |
Z | 36mm |
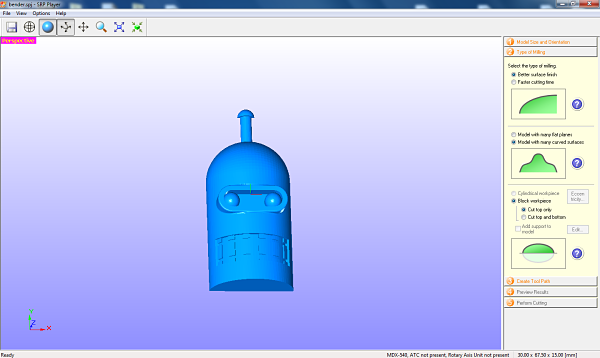
Margin | 5mm in all faces |
Tool | 4mm flat endmill |
Feed rate | 1000mm |
Spindle | 9000 RPM |
Cutting-in amount | 0.27mm |
Path interval | 1 mm |
Finish margin | 0.2 mm |
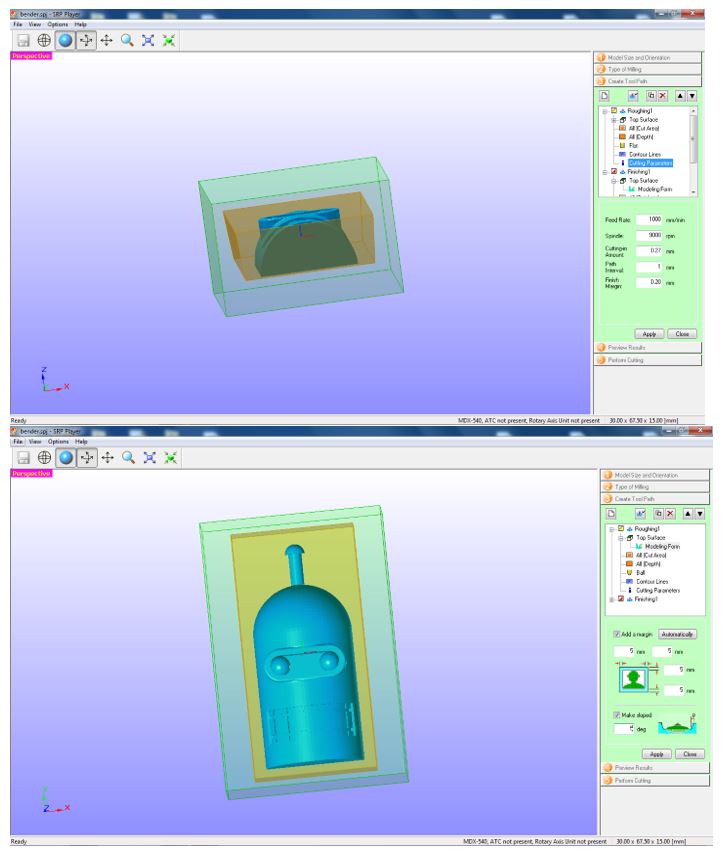
Margin | 3.2mm in all faces |
Tool | 3mm ball endmill |
Feed rate | 800mm |
Spindle | 9000 RPM |
Cutting-in amount | 0.1 mm |
Path interval | 0.1 mm |
Finish margin | 0 mm |
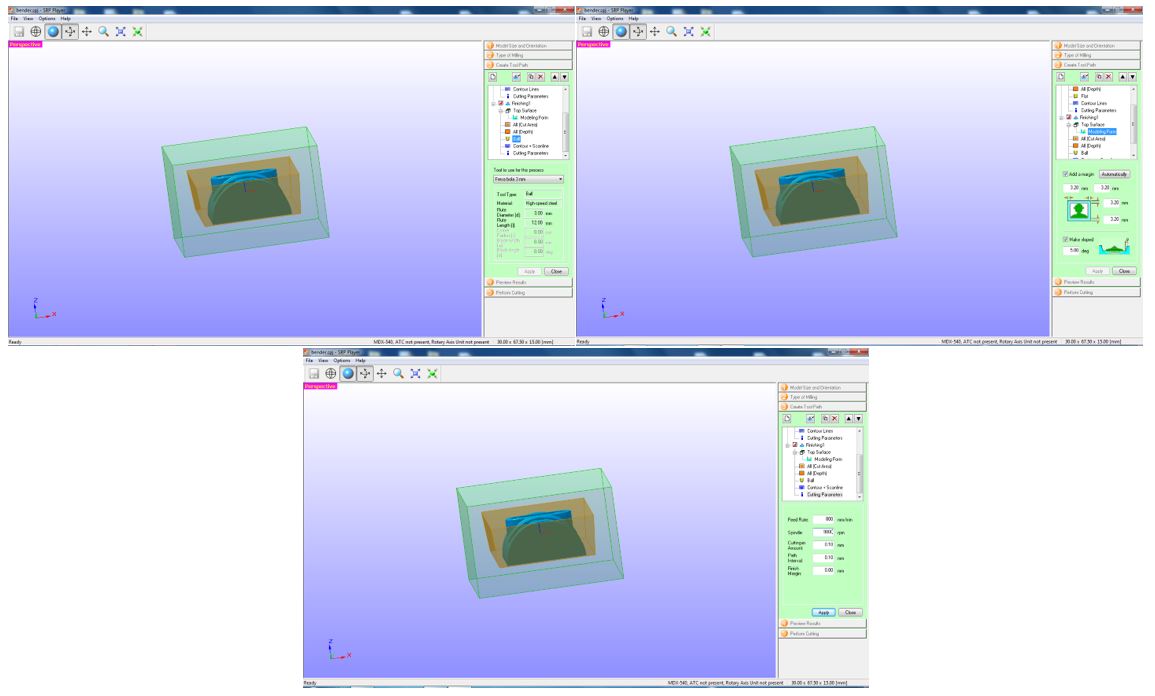
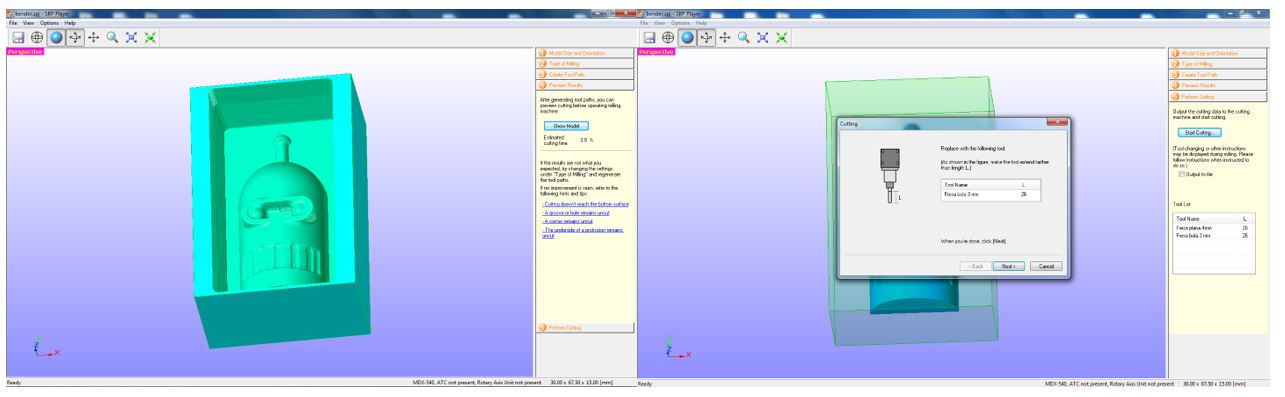
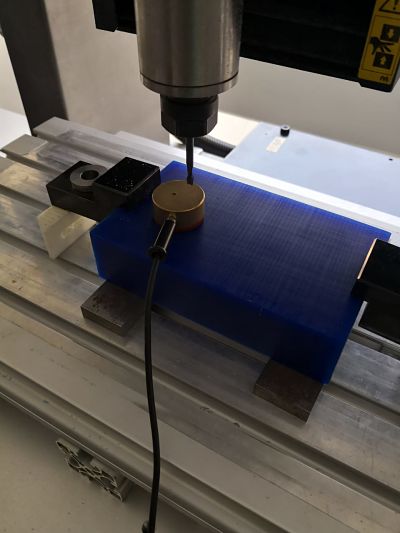
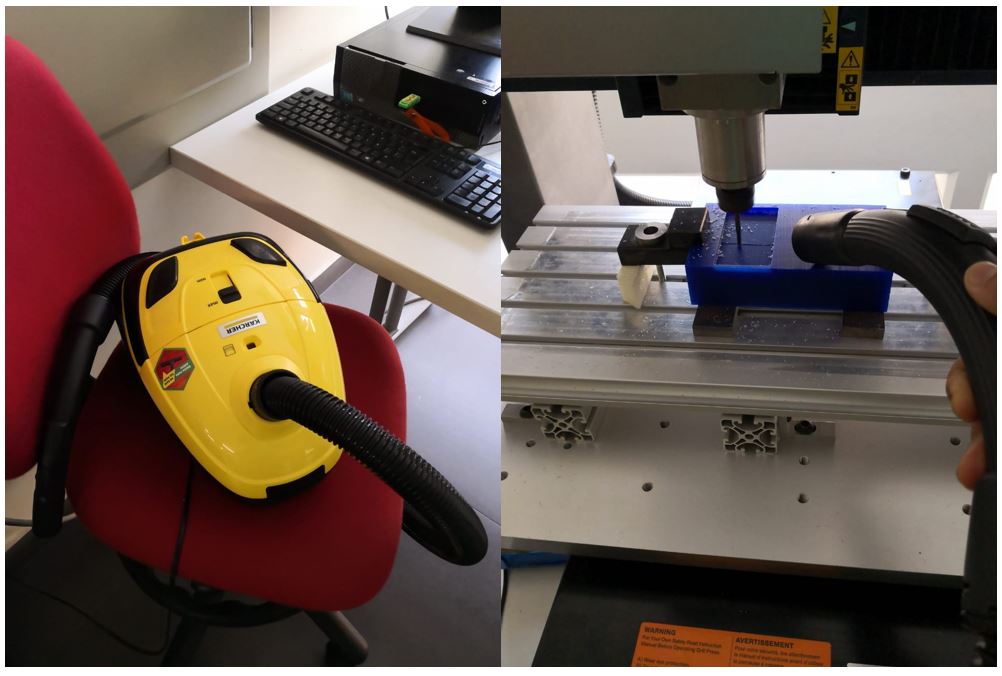
Before clicking start cutting, we can select in the software that we export the cutting file. The first will be the roushing cut and the second file will be responsible for giving shape and details to our design.
In summary, once the stock and design have been defined, a roushing cut of the entire model is made. We must clean the impurities every so often to avoid damage. Once the main cut is made, the tool is changed and the design cut is made.
The parameters are described before each photo of the process.
Moulding
After the machinig, it is time to create the moulding, in my case I use 3 materials, all of them are foodfriendly, that means we can also make food.Materials
The main material that I used in the laboratory is silicone rubber, it is very important to know the safety and hygiene precautions of this type of products, as seen in the picture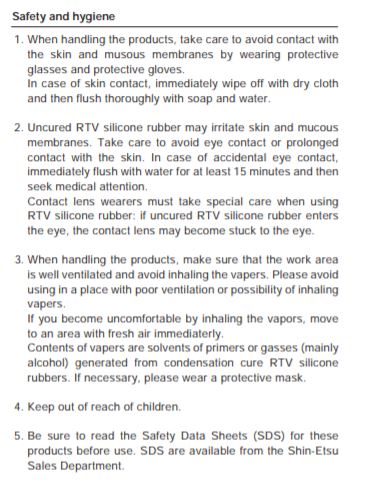
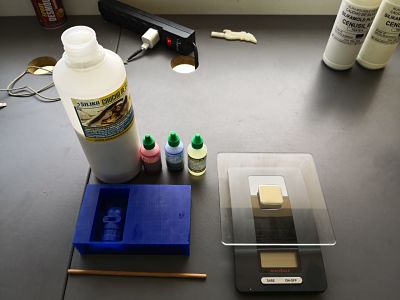
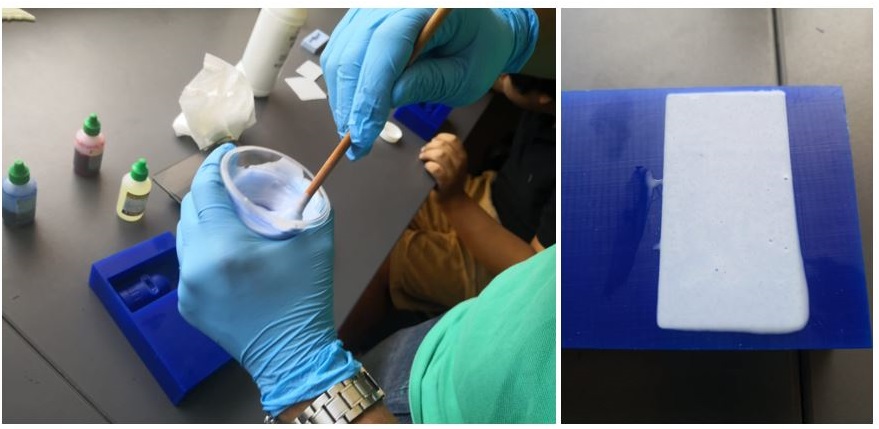
It is recommended to pour the contents of the mold first into the deeper areas of the mold to avoid the generation of excess bubbles. The process is similar for all materials, in case the catalyst is not used, the mixture is half of compound A and half of compound B. Here is the result of the moulding.
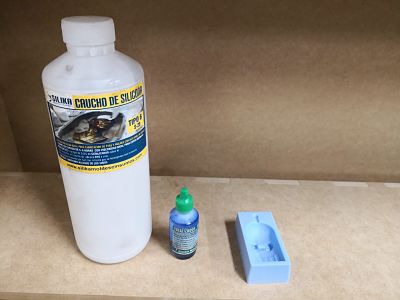
Casting
For the casting process, I use a crystal resin polyester with UV protection with a catalyst.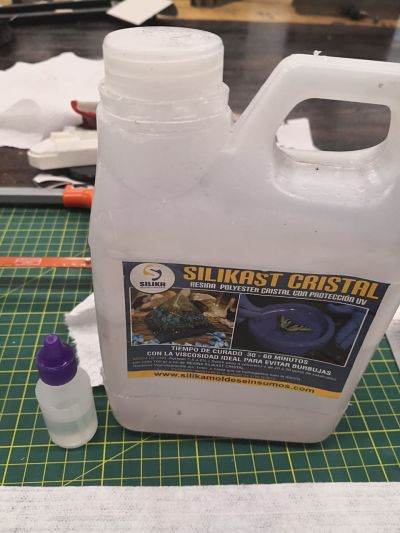
Using the necessary protections to avoid intoxications, we proceed to make the mixture of the resin with the catalyst with the proportion of 5 drops every 100g.
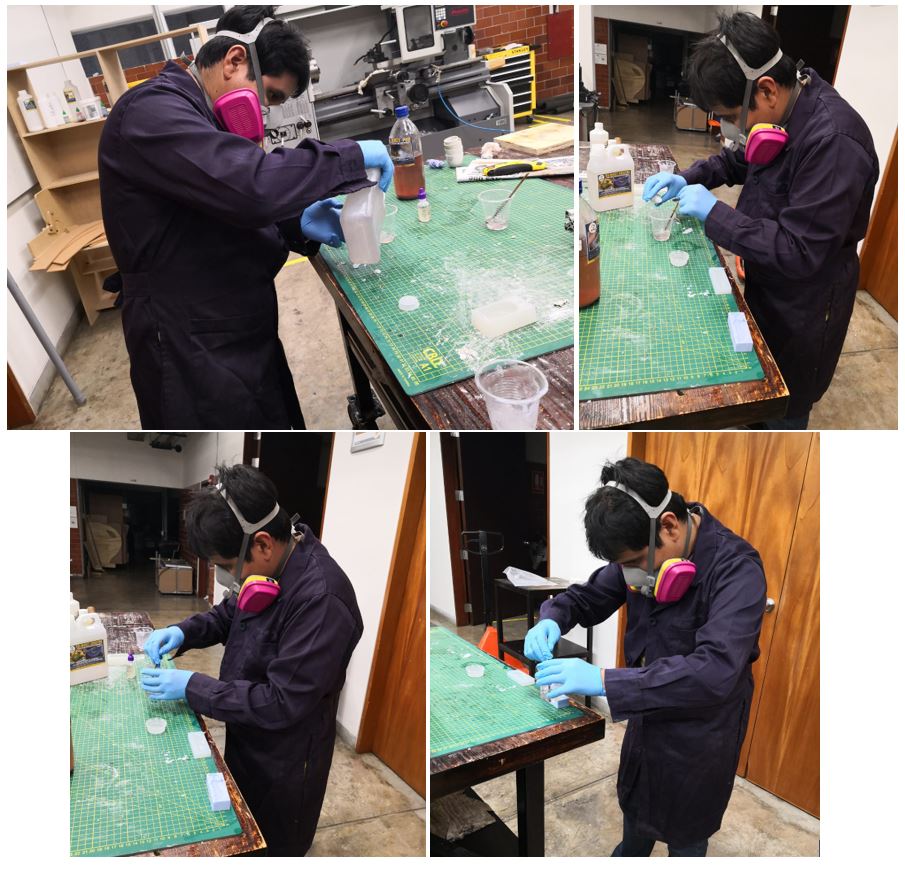
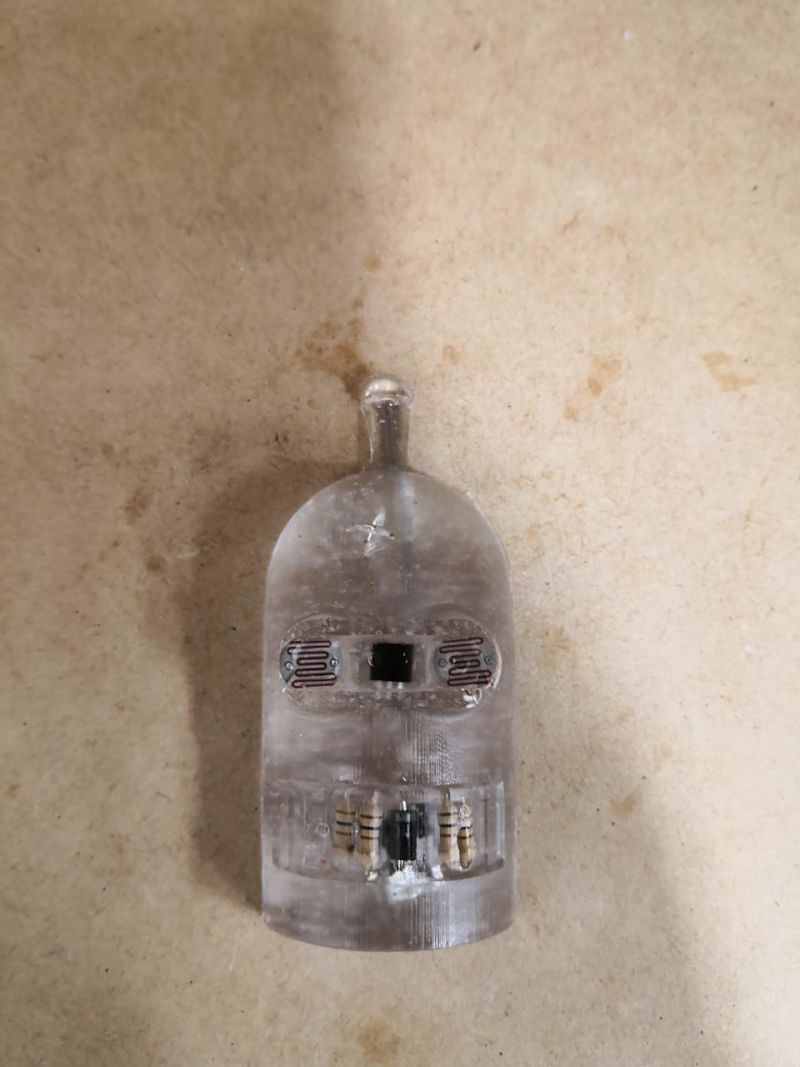
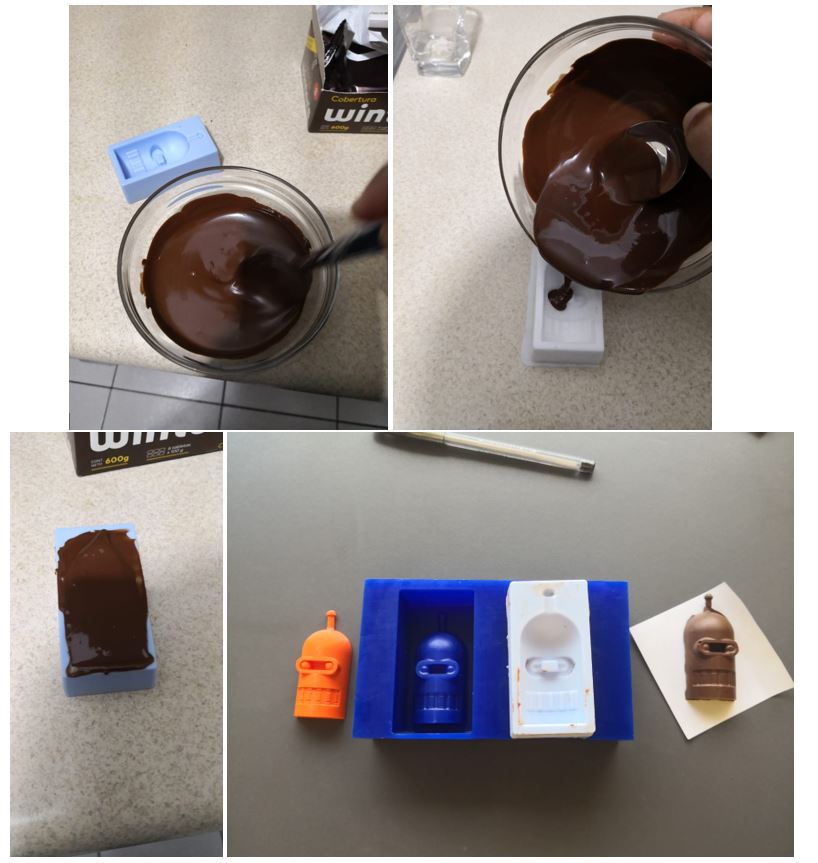
Consideration
In the molds and resins used, almost all of them came with fixed indications: for every 2 drops of compound A one drop of compound B must be thrown, that means that it goes in a 2 to 1 ratio.
To avoid the formation of bubbles, although it is true that we can use a vacuum pump, the method used is quite rustic: give small blows to the mold so that all the bubbles rise and do not distort our mold.
It is recommended to allow the resins to cure for approximately 12 hours, since the process is long and expels a lot of heat.
It is also not advisable to help healing, that means that we should avoid leaving our work in the open.
We must never forget to use the necessary protection elements because the odors emitted by the resin can be carcinogenic. Always wear gloves, masks and lenses.
Hero shot
And Here are all my moulding and casting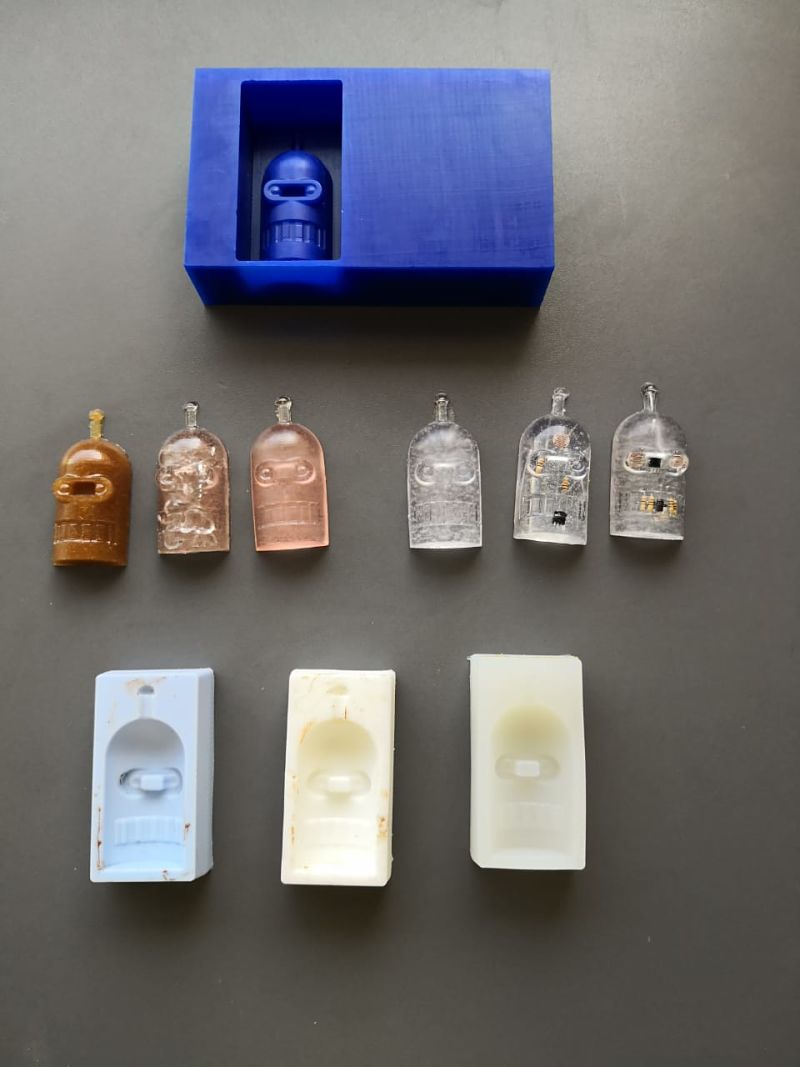
Group assignment
For the group assignment, we have made several tests with different types of resin, in my case I made polyester resin.The difference of the previous processes, the design, a box was printed and the resin of the negative of the mold was emptied inside, as seen in the picture.
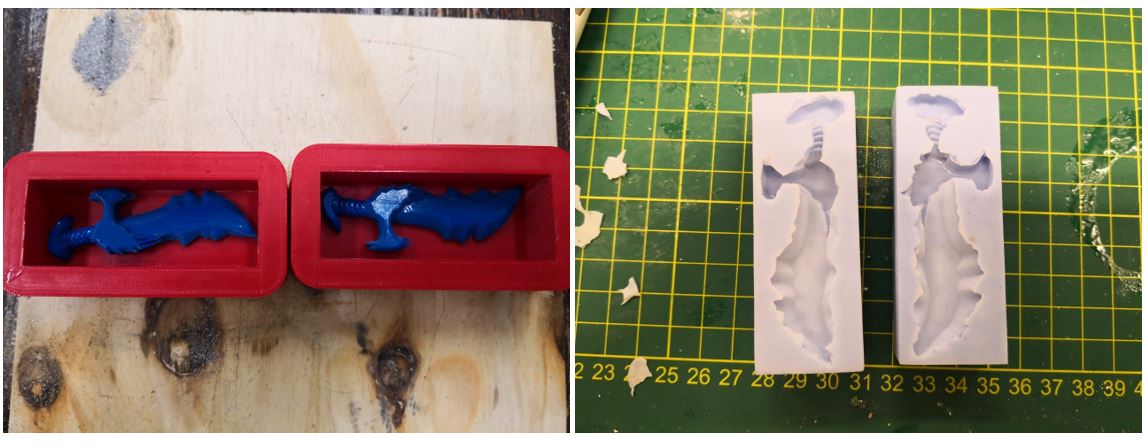
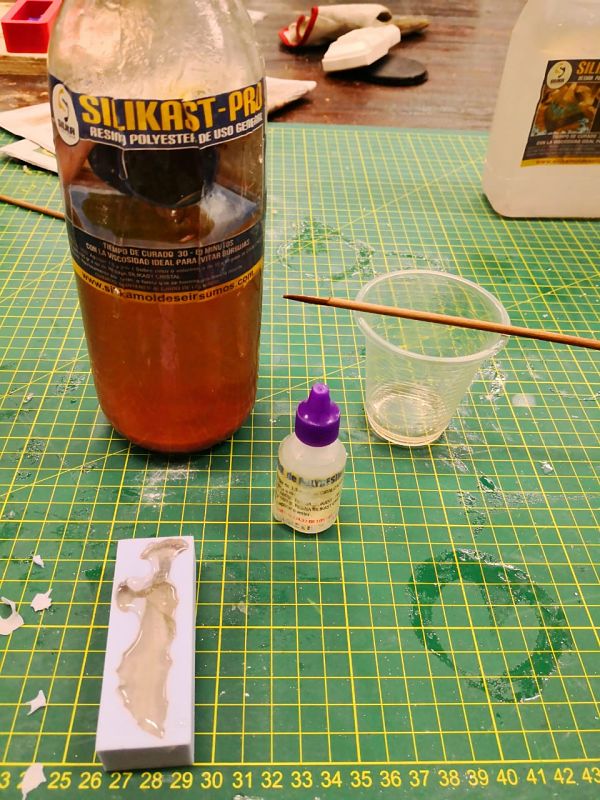
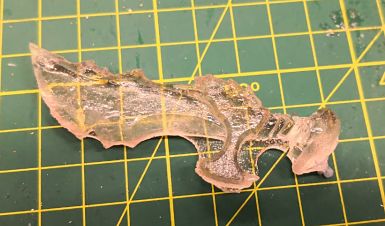
Problems and solutions
It is very important to keep in mind that we can not delay a lot of time mixing the materials of casting and molding, but these materials harden and we will not be able to work.Another important factor is to have patience so that the molds are dry enough to be able to remove them and avoid what you see in the picture.
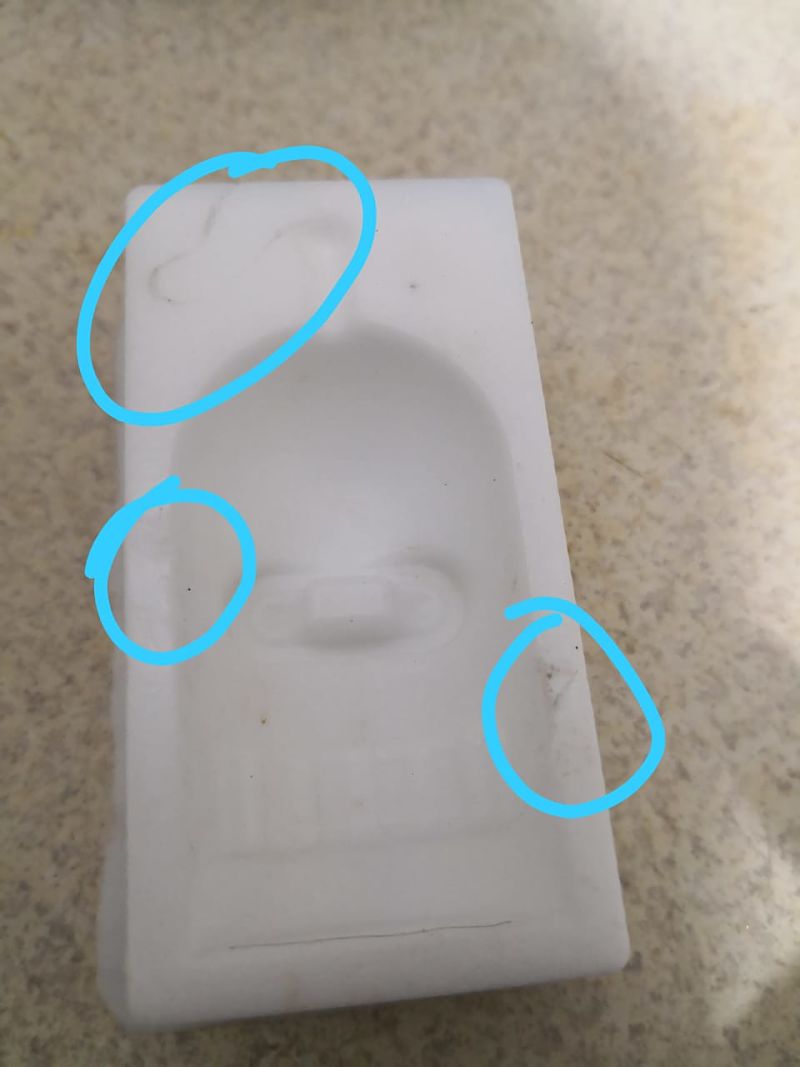
Download files
You can download files Here:Desing
Bender (Inventor 2018)
Roughing
Roughing (Modela MDX-540)
Finishin
Finishing (Modela MDX-540)
STL file
Bender STL