Home
OBJECTIVE
- Learn about wood joints
- Build a structure with wood joints
PROCEDURE
1. I wanted to relate this assignment with my final project
2. I thought that my final project's wood joints were too simple for
this assignment; therefore I chose to do another thing this time
3. I decided to build a desk that could be used for the assignment of Make Something Big
4. Here is my sketch
5. I searched the main types of wood joints, because I was driven to include them all. This is the main link I used:
WOOD JOINTS6. I designed my drawing in Inventor
7. As I didn't know what my cartboard's thickness was going to
be, so I used a wooden piece's thickness (5 mm), I cutted in the Pre-Fab Academy,
as a reference.
8. I determined the lines I would have to change if the referential thickness was not right.
9. When I went to mhy Fab center, I found that the wooden piece's thickness was 4mm; therefore, I changed it.
10. I exported my designs to Rhinoceros
11.
I cutted my designs with a 40% Speed, 90% Power and 2356Hz
Frequency. By the way, Ricardo taught me that it was better to
keep power under 90, because it could cause fire and increase the
Frequency up to 5000Hz for acrylic. I used a solid metal piece for stopping the cartboard from folding.
13. Here are my parts after assembly
CONCLUSIONS
1. Narrow cartboard pieces are weak
2. Too much weight at both sides of a structure can cause it to fall instead of balance its weight.
3. It is really important that the dovetail joints should have trapezoid shapes.
4.
After experimenting with cartboard joints, I realized that I could have
applied them to my final project...they were not that simple.
AFTERWARDS
I
talked with Miguel, a Mechanical Technician at TECSUP about ways for
improving my final project design according to my observations in
Step 2. These were the results:
1.
For strengthen the 3D Printer part of my final project while using
hinges, I can make some holes in my blocks and put removable pins.
2. For completely folding my machine I can increase the height of the wall below the 3D Printer part.
3. If I use a small valve with a tube, my container can be at the same level of my machine.
4. My blocks can have half their actual height and some sliders below (to make it movable)
5. My Y-axis can be folded like a 2D Printer top part, instead of going out of the structure.
6. An L-zone shape is compulsory for filling the entire square zone of my machine.
FURTHER WORK: OBJECTIVE
I will design my final project with a structure at a 300 mm scale for making it more easy to work with, using joints.
1.
I will search for more types of press fits now that I have watched how
other people did the assignment in the Fab Latin America network.
2. I will try apply as many press fits to my final project new design while caring about its efficiency.
3. I will cut my new design.
FURTHERWORK: PROCESS
DESIGN1. I observed the fitting-ins of Luis Peņa's final project and I realized that once you put them in, you could not put them out.
2.
I decided to adapt this fitting-ins to final project and began
measuring the lengths of another machine's fitting-ins with a pencil
and a ruler.
3. Then, I applied Cross Multiplication
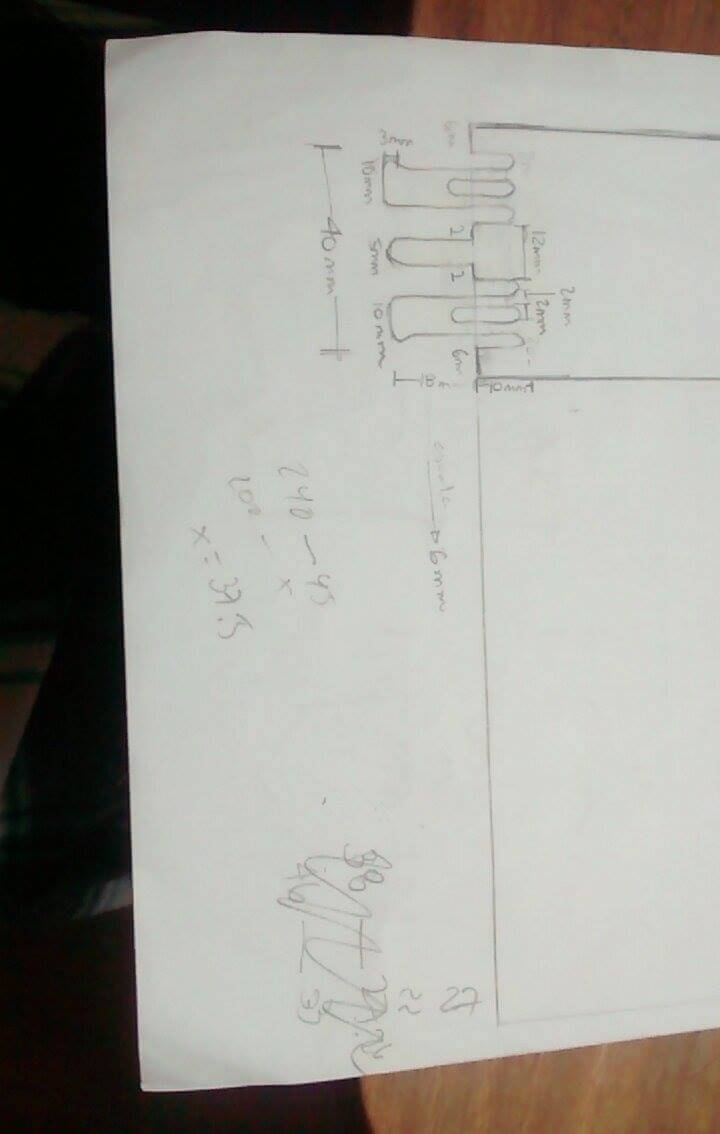
4.
I designed my project using fitting of two lengths: 35 mm and 19 mm. I
should say Inventor gave me trouble when I wanted to correct drawings,
because I could not extrude them easily. I recommend to copy the
correction to a New File and extrude it there.
SOFTWARE AND EPILOG
1. I opened Corel DRAW -> I imported my design in pdf format as you can see
Here -> I clicked on Print -> I clicked on Preferences
2. Here are is the data I entered:
- Job Type: Vector
- Piece Size: 900 (Horizontal) and 600 (Vertical)
- Options: Autofocus (just that)
- Vector Setting: 20 (Speed), 80(Power) and 1500(Frequency)
3. I clicked on OK
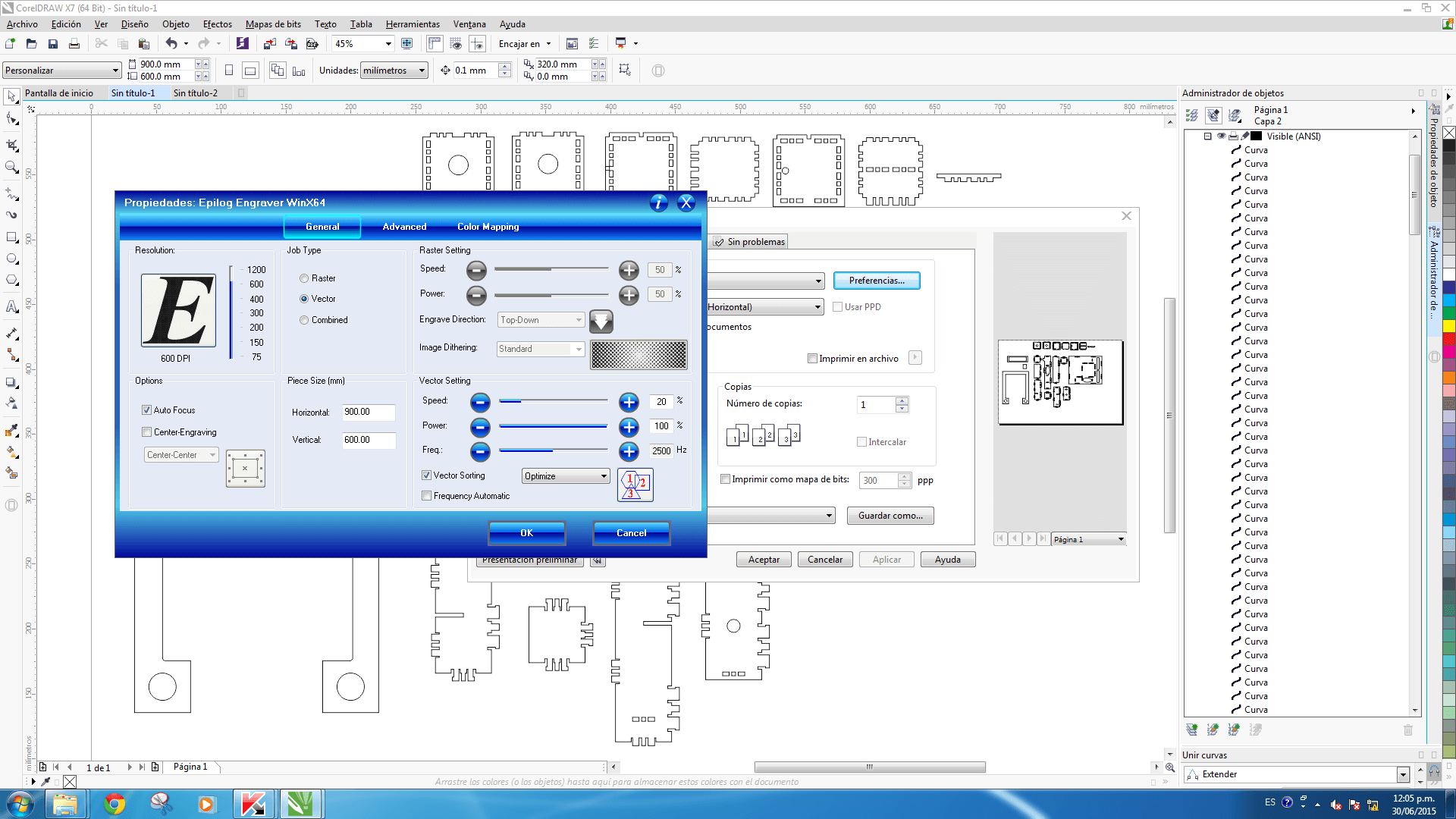
4. I clicked on Accept.
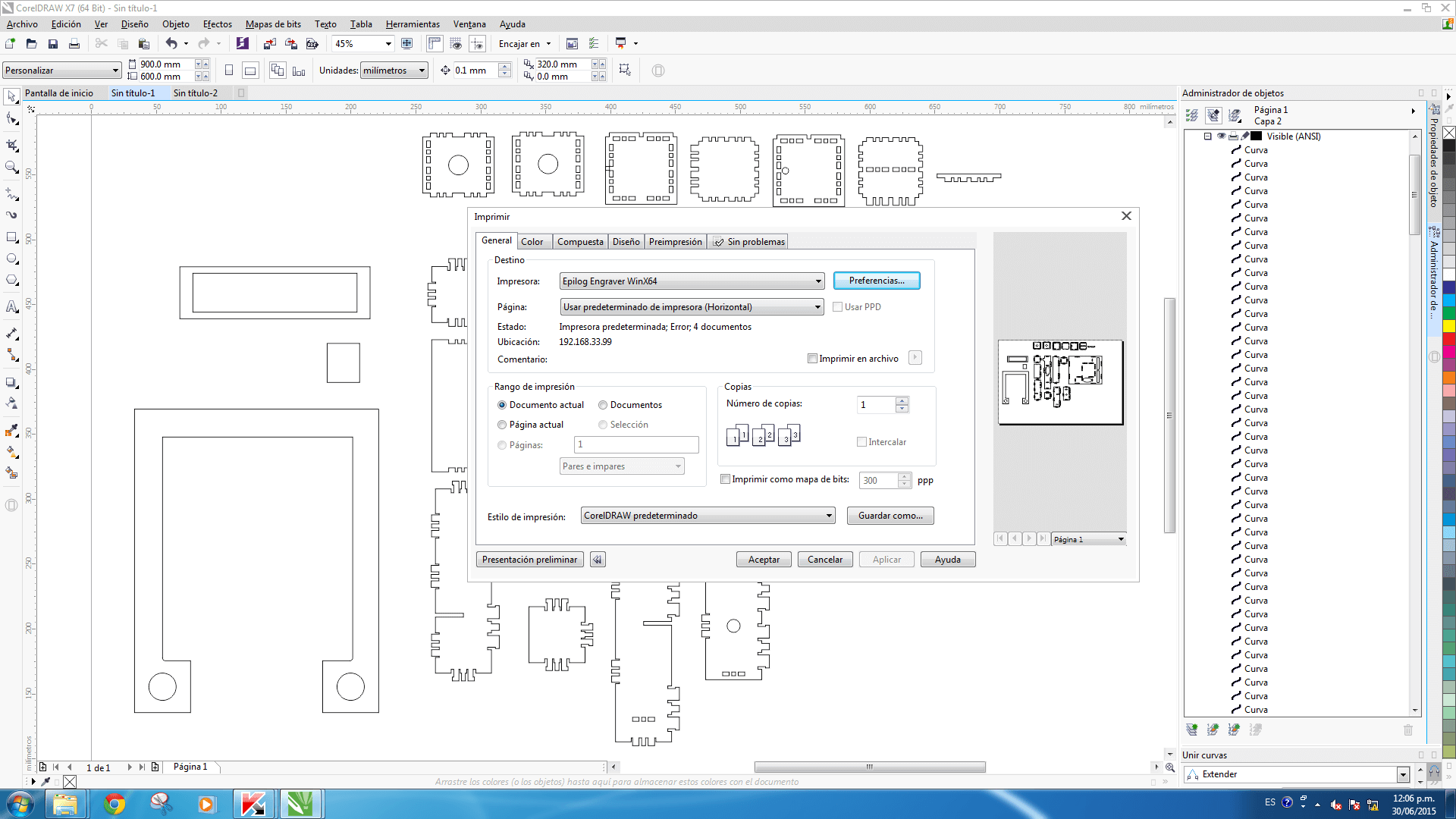
5. I put the material I wanted to cut inside the Fab Epilog
6. I closed the Fab Epilog door
7. I confirmed that the gas filter and the air assistance were on
8. I pressed 'Job'
9. Using up and down arrows I found my archive
10. I pressed 'Reset' for starting from x0,y0
11. I pressed 'Go'
The picture above has been modified from this
archive, due to its clear resolution (my camera has not very good resolution).
CUT
1. I cutted my project.
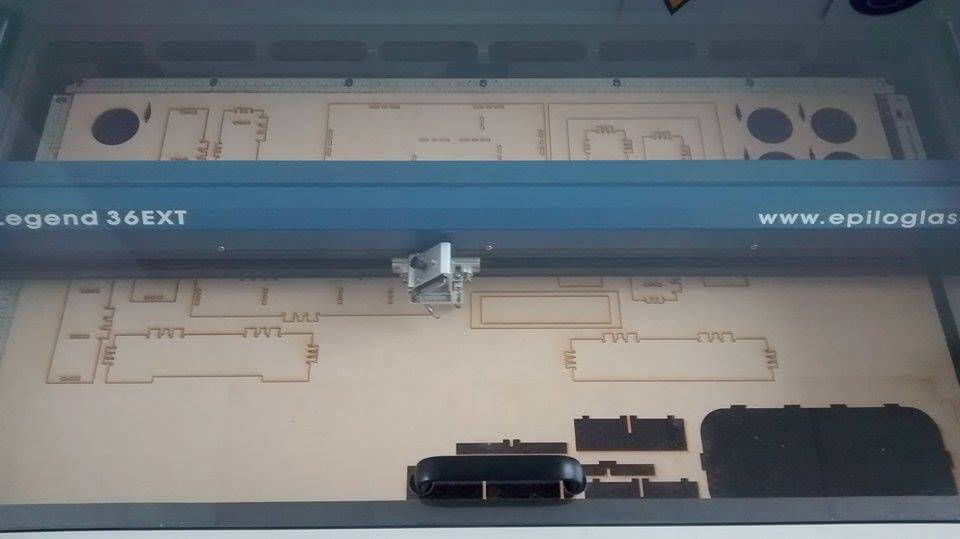
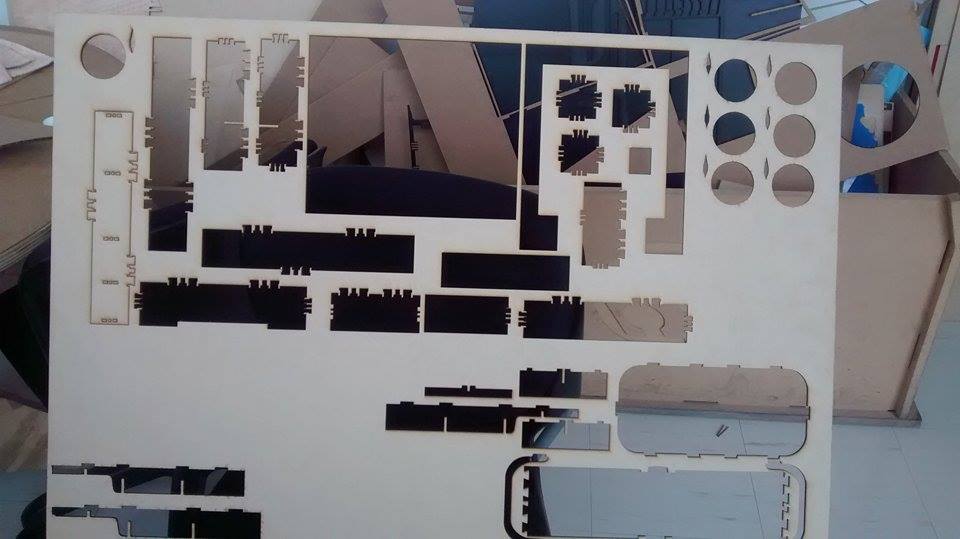
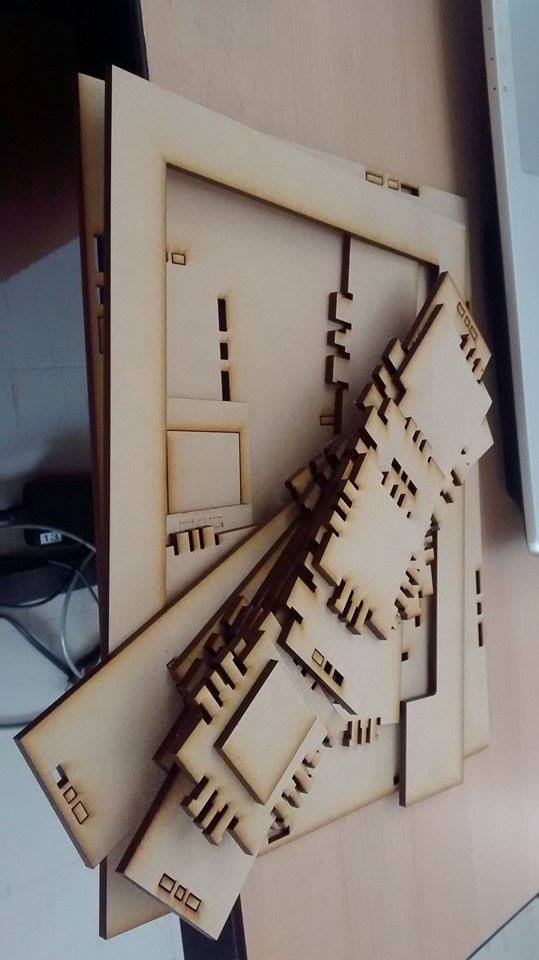
2.
Three of my projects' pieces had mistakes. The first one was broken in
one side, the second one didn't cut a fitting-in and the third one
didn't cut the frame well (I had to break it).
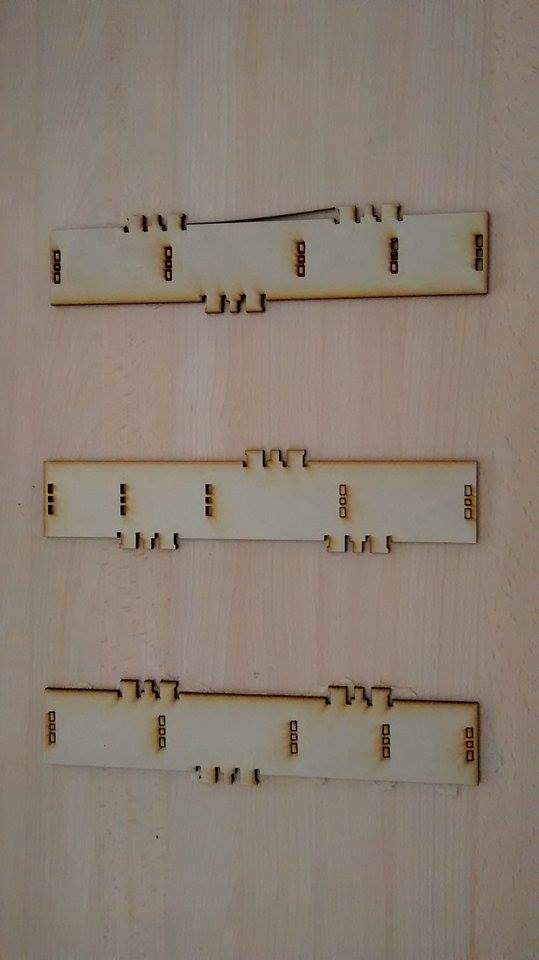
3.
I tried to figure out what was the best way to assemble my project. I
first thought I needed to add everything to the base in order to
assemble hole by hole.
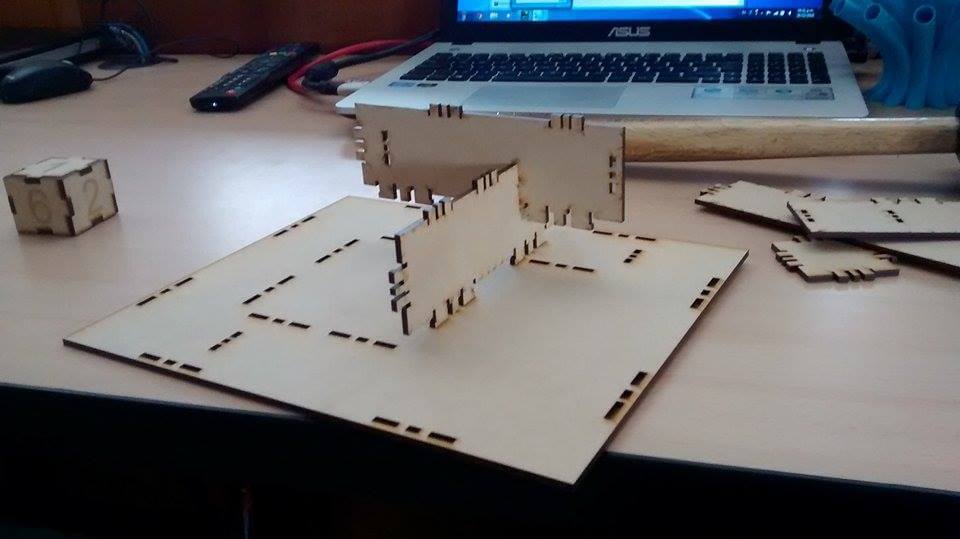
4.
Then I realized that as I went through, there were some pieces I could
not add, because they were being blocked by the pieces that surrounded
them. So I decided to assemble the walls first, then the internal
structure and finally the base.
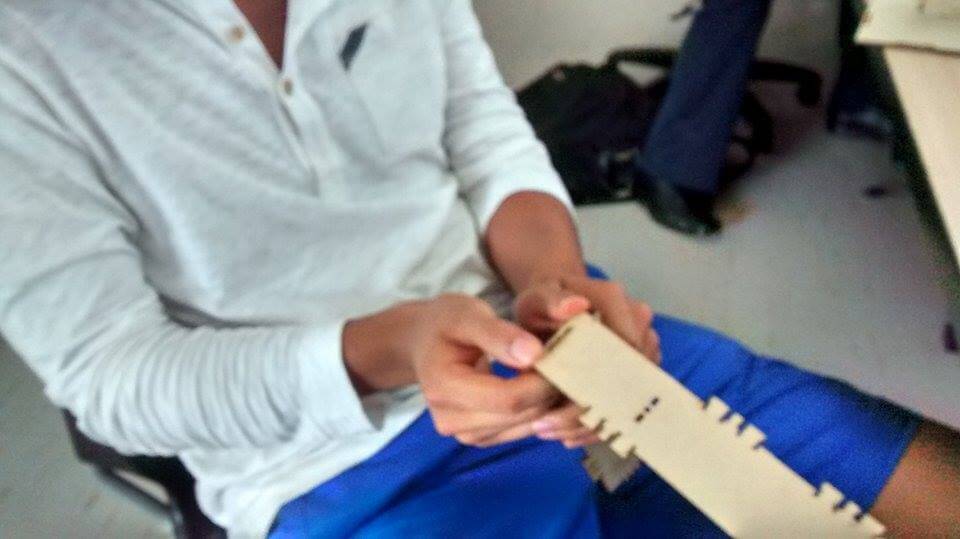
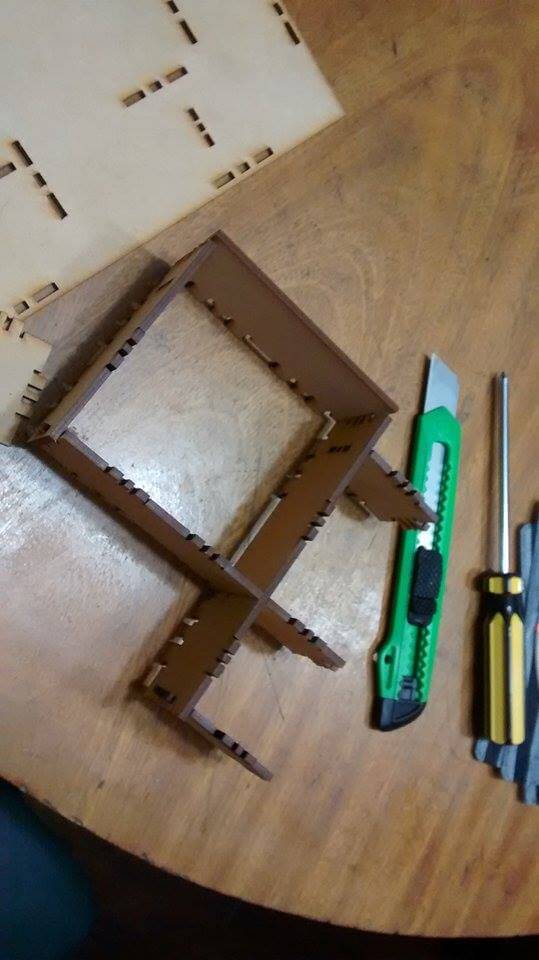
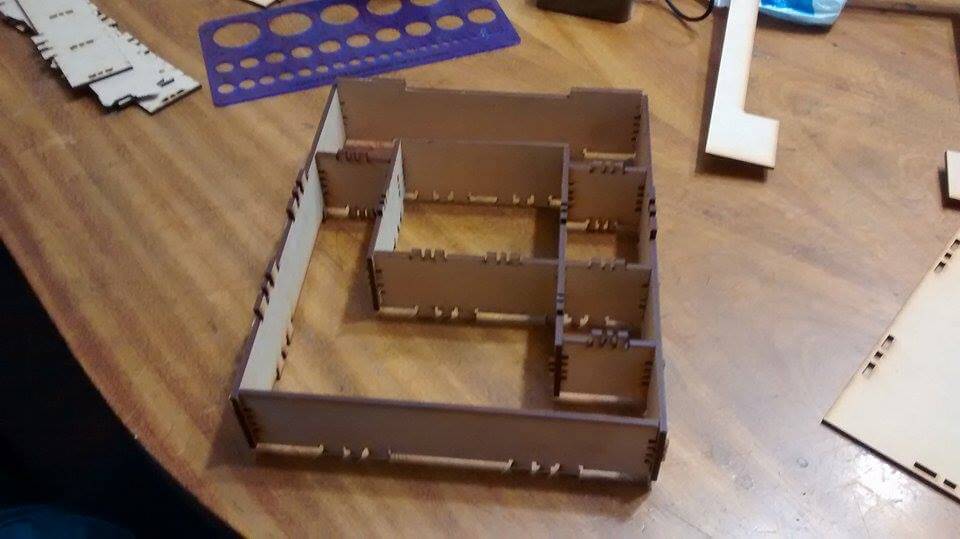
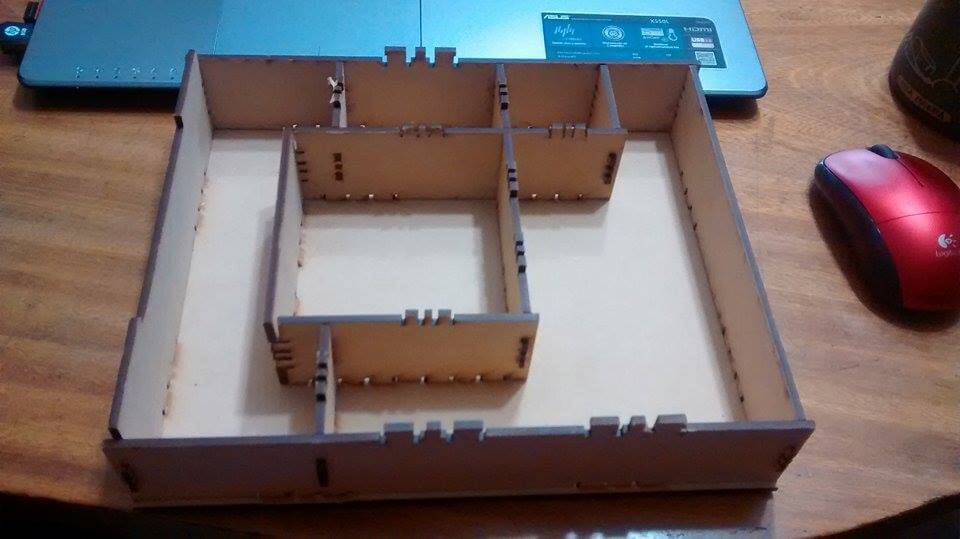
You can download the Assembly
here and the press-fit kit in dwg. format
here.
CONCLUSIONS
1.
I should make tests before cutting everything. In this assignment, I
made the male fitting-in 1mm bigger than the female fitting-in and I
wasn't able to connect them easily. That's why I used a hammer.
2. The fitting-ins need to have circular ends in order to to make better insertions.
3. Fitting-ins should be placed not so near the borders of the base or they will break apart.