About me
Final project -
development
Final project
Weekly projects
Wk3 Computer-aided
design (Feb 11)
Note:
At beginning of this week, I was finally able
to upgrade my laptop so that I could install more
applications. I am now running Mac OS 10.10
(Yosemite), so I'm now trying to get familiar with
the new system, trackpad and gesture control. It
has been noted that for CAD it is easier to use a
mouse!
Tuned in to regional reviews to
learn from others process or at least the ones that
transmitted well. This was followed in the afternoon
with Neil Greshenfeld's
introduction to computer controlled cutting
tools.
Links of interest:
XY axis CNC : http://corexy.com
Nice website on parametric design: www.parametriccamp.com/en/what-is-parametric-design
DM gave demo on simple laser cut process from
Inkscape. This helped me to see the workflow required
from vector to pdf to lasermachine (Epilogue).
Thursday
Upgraded laptop
Installed Inkscape/X11
Installed Rhino
Installed Affinity Designer. This is not open source
but a very serious and powerful competitior to
Illustrator, at a fraction of price, and very
intuitive.
Read some guides to laser cutting, eg http://www.cutlasercut.com/resources/drawing-guidelines
Friday
Followed Rhino
and Grasshopper webinar at 4pm.
Unfortunately Grasshopper not yet installable on Mac.
Watched Affinity
Designer tutorials.
The ease of use, power and intuitive interface of this
programme really appealed to me. The tutorials are very
clear and easy to follow. A very elaborate and
customisable guide system is also a very powerful
drawing aid. The cloning, step and repeat feature is
great and the zoom appears infinitesimally powerful. I
used affinity and inkscape to create artwork for lasercutting.
KERF TEST
It's often
tempting to want to jump straight to printing, but
persevering with producing the Kerf test was of
critical importance in Week 3. Traditionally, the
term 'kerf' defines the width of the saw cut (in
woodwork). This is shown clearly in the diagram
below (courtesy of wikipedia). Taking this 'waste
line' into account at the CAD vector drawing stage
is key, especially in push fit construction, where a
very close fit is necessary to achieve good
structural strength. In lasercutting, the high
temperature of the laser means that some materials
burn away more easily on the cutting line, so the
kerfing allowance needs to be varied ( ie cardboard
will burn more than wood, therefore any slots for
push fitting joints need to allow fr this. It has
also been noted that making sure the Vector drawing
is editable for future correction is also a very
important point to bare in mind!
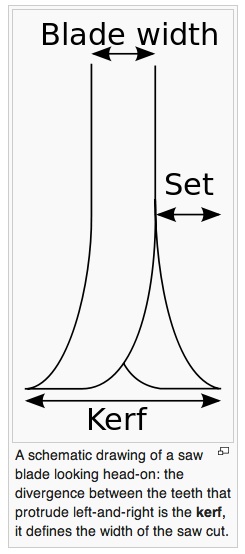
I produced
a kerf test to demonstrate what allowance should
be given to 3mm cardboard for push fit
construction, relative to the conditions of the
machine tool (Epilogue) in our lab.
The images below show the linework for the laser
to enable push fit testing across a range of
increments (±0.1).
ALSO, as
you can see, this also includes the creation of
a CHAMFER, to aid smooth push fitting. As I
found out later on, slots without chamfers make
it very difficult to 'slide' into the joint,
making push fitting more difficult. This can
also damage and compress cardboard, thus
weakening construction and structure.
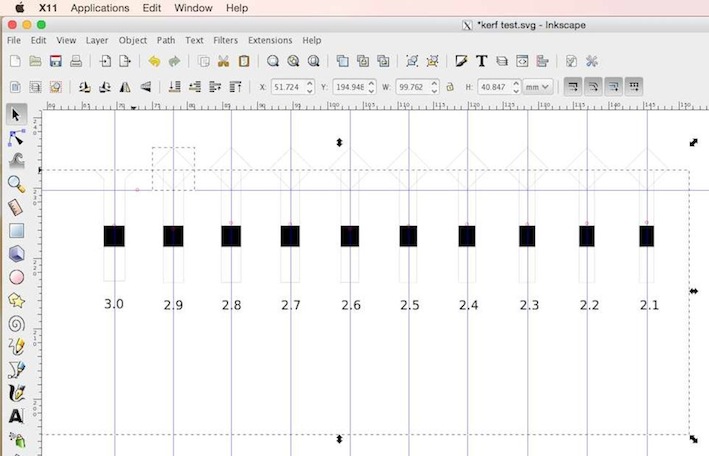
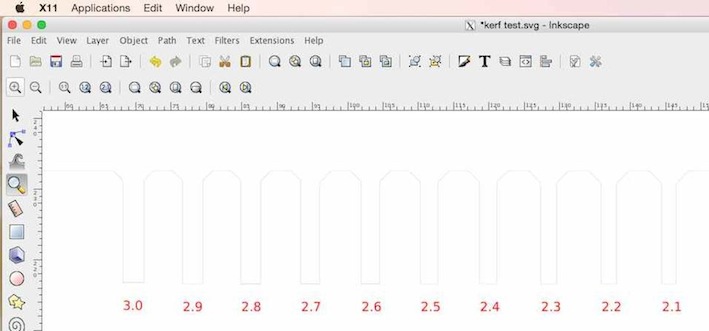
This image
below demonstrates a push fit tolerance that is TOO
TIGHT. This shows that the cardboard has distorted
beyond what should be a 90º joint.
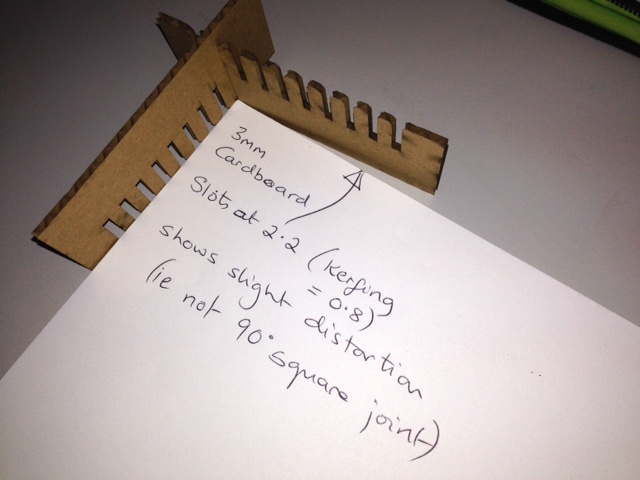
The image
below shows how the kerf test has allowed the
optimal kerf allowance without any distortion in the
joint. It also provided the firmest strucural joint.
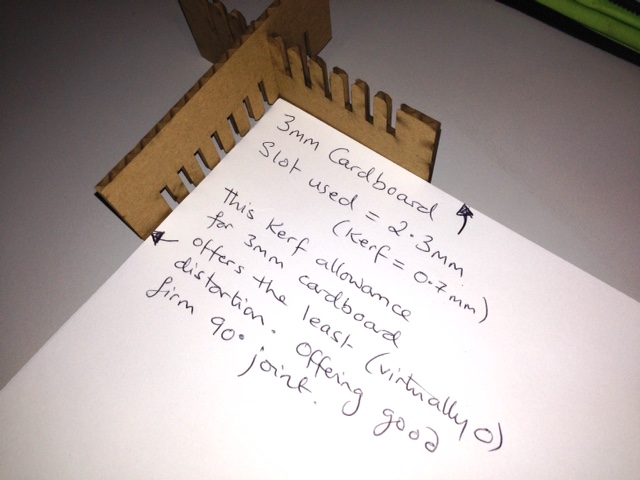
PROJECT FOR
WEEK 3
I decided that I
would use these findings to test and explore the
strength, balance and aesthetic that I could achieve
with an organic form in cardbord. This would help
highlight considerations for structural integrity of
my indoor garden project. I wanted the design to be
light and airy - suspending plants in space.
Initial
sketches for indoor garden:
Whilst I would be interested in exploring
construction of the inter-connecting 'X' form above,
I was not convinced that cardboard would be the best
material, so for the purpose of getting acquainted
with the laser cutting process, I chose to develop a
linear version.
I decided to draw this using Affinty
Designer (not open source but a very good value and
intuitive 2D drawing alternative to Adobe Illustrator)
so that I could try out its cloning and use of guides.
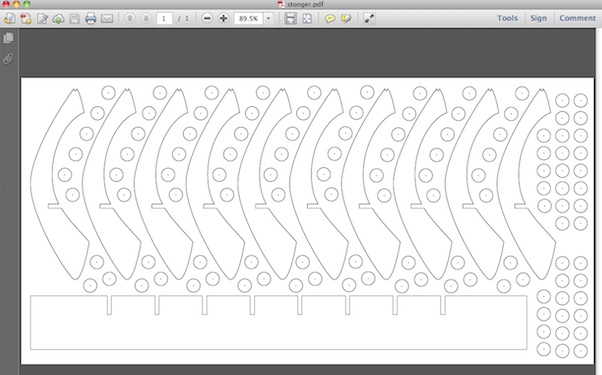
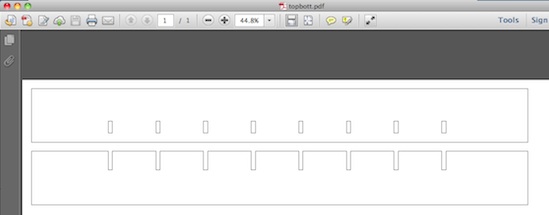
Overall, I really
liked working with Affinity. It is the most logical
and intuitive drawing tool I have used to date. It
also has a great range of capabilities and
convertability.
NOTE: I
will just mention here its cloning tool, repeated
into infinity would be great for
pattern work and gaming graphics. I need to do
further tests to check its editability of changing
the 'master' for global and efficient changes to
many parts, but it looks very promising. See star
repeat below.
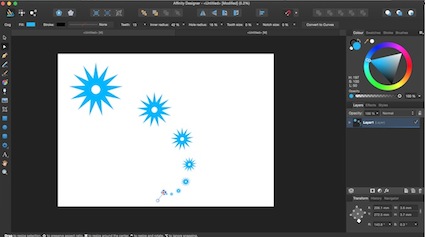
Here are
some images of the cardboard being cut on the
lasrecutter (Epilogue).
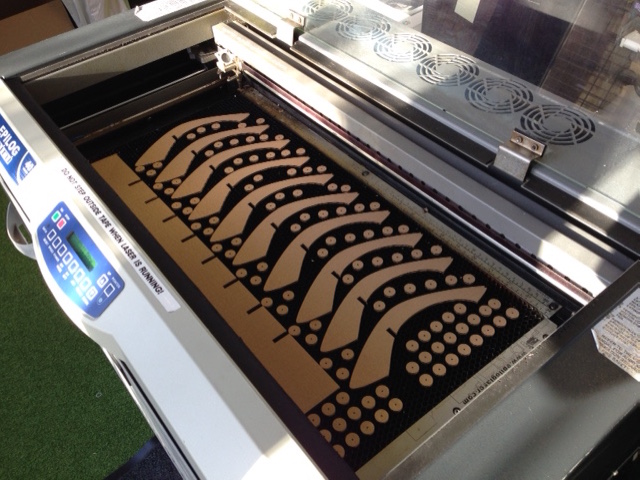
Push
fit model of structure, showing
balance, strength and proportions.
Seeing and holding the actual model in
hand (so quickly, once artwork
created) was very helpful for future
development.
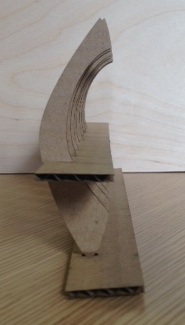
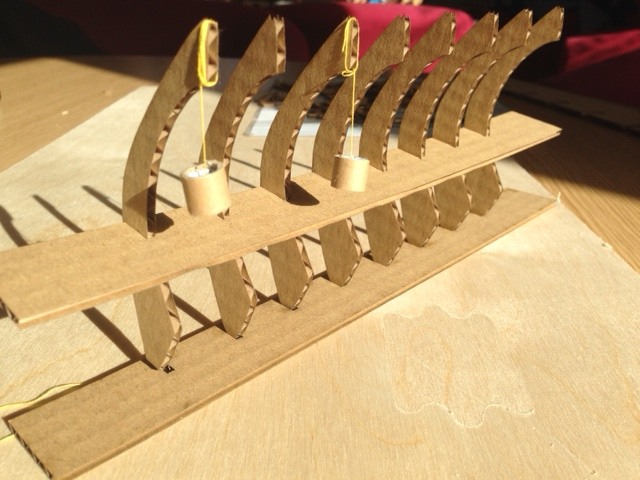
Download files:
Stronger2.pdf
topbott.pdf
kerftest.svg
©
Sally Williams 2015