CONCEPT:
Digital
Mala - A wrist
wearable
device for
buddhists
(or
mindfulness
trainers) to count
mantra
recitations,
moments of
mindfulness
and
prostrations (a
foundational
Buddhist yoga
practice).
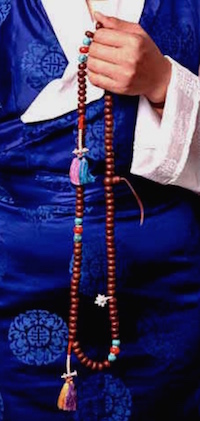
The
idea behind
this device is
that it will
help to
support
buddhist
practitioners
and those trying
to develop the
habit of
mindfulness in
everyday
life.
Problem is,
it's not that
easy to be
mindful for
even just some
of the time -
try being
mindful,
present and
aware even for
just a few
minutes, it is
more than
likely that
distractions
of all kind
will arise in
the mind to
take you away
from the
present moment.
However, as
the great
spiritual
masters tell
us, everything
is just
practice and
its possible
for anyone to
develop
mindfulness
and awareness
which in turn
is very good
for our mental
and emotional
health and
well-being.
There is a
Tibetan
Buddhist
saying that
its a long
walk to the
meditation
cushion.
However, in
any day, there
are thousands
of opportunities
to practise
mindfulness
and awareness.
Functions
of the
digital
mala:
• Mantra
recitations
to
be
counted as
single counts
with
button presses;
•
Moments
of mindfulness
to
be counted by
holding the
button (for a
few seconds)
to start and
end counting mindfulness
time;
• A secondary
button counter
that will
semi-automatically
keep track of
the number of
prostrations
or Yoga
postures (ie
'Sun
Salutations’).
The device
allows the
practitioner
to be fully
present in the
practice or
movement
itself and not
be distracted
by the task of
counting;
• When the
wearer is
ready to see
the statistical
progress
of
their practice,
they will be
able to
connect the
device to a PC
to view their
accomplishment
in a graphic
display.
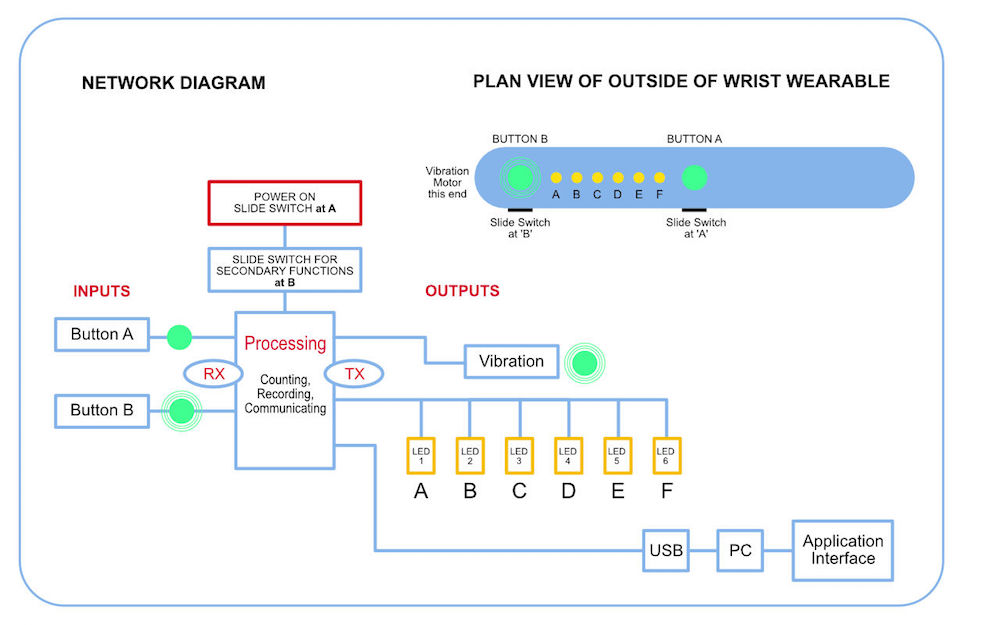
Which
Processor?
AtMega Vs
Attiny44
Intitially,
I was very tempted to use the ATMega, as it would mean
that there would be plenty of pins to accomodate 6 x
leds, 2 buttons,
a motor, plus Rx and
Tx comms; I could even have the luxury of an external
clock.
However, it became apparent that this could have a
serious effect on the size of my wearable, which I
wanted to be as compact and discreet as possible.
Furthermore, when I really looked at the functions
required with my mentor James, the ATtiny44 was just
about perfect in size; offering the exact number of
pins required.
Both options are compared below:
ATMEGA328
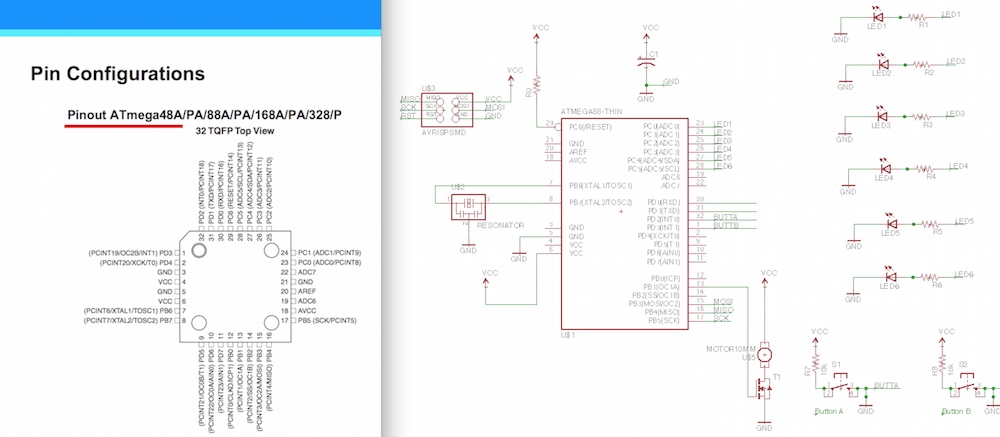
ATTINY44:
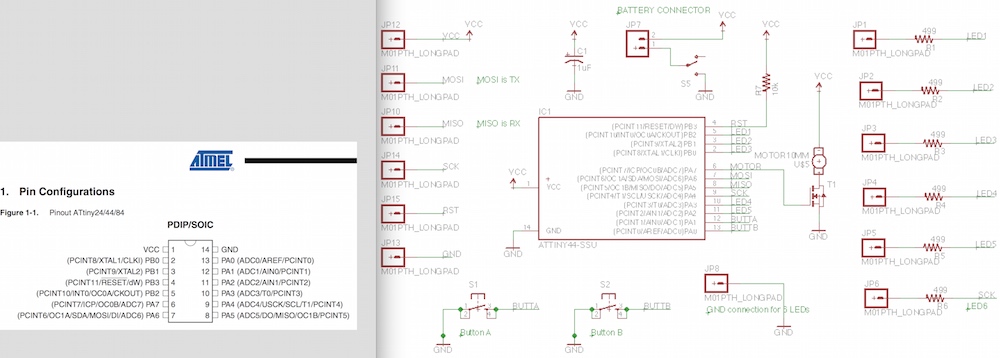
Initially, I was going to
use a 2.5mm Audio Jack for
Rx / Tx communications.
However, I came to a
stumbling block as I could
not find the correct
footprint for the
component listed in the
fab inventory. I set about
learning to create a
footprint in Eagle, a
skill that would be useful
to have given that
footprints are not always
available. By the time I
had begun to undertake
this, it was suggested
that I could share the TX
/ RX with the MOSI / MISO
pins, so the audio jack
was eliminated. This would
mean that I would have to
create a simple adapter to
bridge between the board
depending on whether I was
programming the board
(input) or sending the
data as output.
Components:
Circuit board,
Electronic components (processor,
2
x button, 6 x LEDs, 1 x
motor, switch x 2, 1 x
rechargeable Lithium Ion
Polymer battery (LiPo),
charger), Silicone Rubber,
Machinable wax, steel band
(wide-band tape measure).
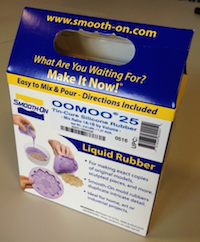
Steel
band core
- a bistable
structure
within a
silicone
rubber wrist
wearable
I
wanted to use
the simple but
effective
properties of
steel band snap
bracelets.
This would
provide both
core integrity
and a
wrist-clasping
mechanism
within my
wearable
silicone
device, whilst
eliminating
any need for
an extraneous
closing
mechanism,
which from a
commercial
point of view
would make it
more
cost-effective.
The
bistable
properties of
a steel band means
it can be
stable in two
states -
straight and
curved in a coil.
This
is enabled by
a
curve that is formed
into the steel
at the
factory.
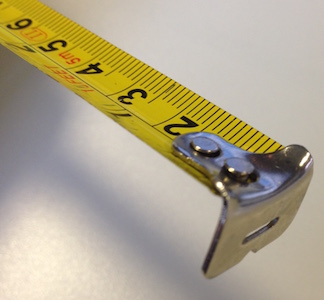
Battery
specification
By
using a
Lithium Ion
Polymer
battery, I would
be able to
have a
reasonably
thin,
light,
portable
and reachargeable
power
source ,
with enough power
to charge
the device for
a day's usage.
(image
from
Adafruit):
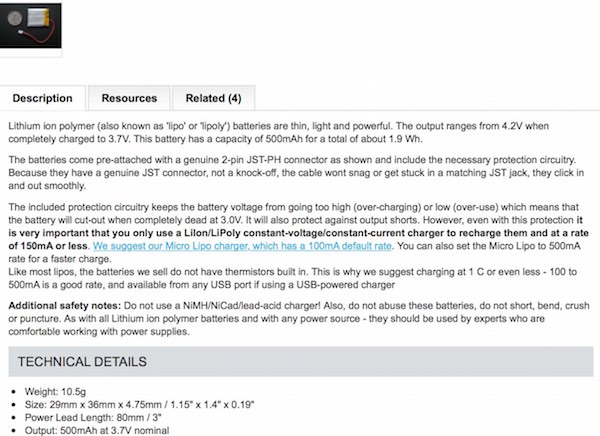
Estimated
Bill of
Materials
(BOM) to
produce 1
x clear
silicone
prototype of
D'Mala:
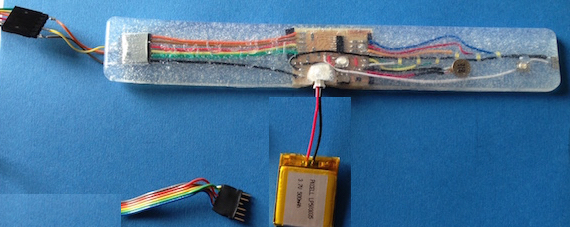
Fab Lab Inventory components :
Copper
clad board
Electronic
components:
ATtiny
44processor
2
x button
6 x LEDs
Slide switch x
2
Machinable
wax to create
mould
FTDI cable and
connectors
Estimated
Fab
Lab
components
COST:
£6-8
Non-FabLab
Components:
1 x
rechargeable
Lithium-Ion
Polymer
battery (LiPo)
(4tronix.co.uk):
£7
Vibration
motor
(fastcomponents.co.uk):
£1
Charger
(4tronix.co.uk):
£6
Silicone
Rubber ("Sorta
Clear 37" by
Smooth-On -
supplier
Bentley
Chemicals UK):
£6-£8
Estimated Non
Fab Lab
components
COST: £ 18
– £20
Total
ESTIMATE to
produce one
clear silicone
working
prototype:
£26 – £30
Creating a
flowchart for
device
operation
This was
really helpful
to try and
help me
visualise all
the different
states that
would need to
be included in
the code to
help for both
function and
programming:
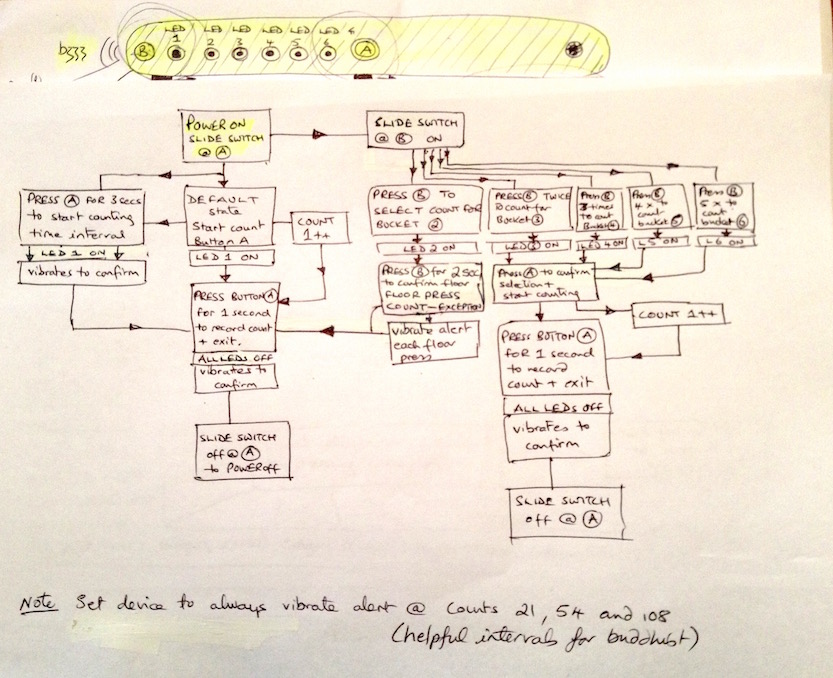
VERY Rough Prototyping
By
mocking up
rough
protoypes, it
helped me to
eliminate or
select
different
possibilities,
work out where
to best place
buttons for
different
functions
and to see how
materials
might
behave.
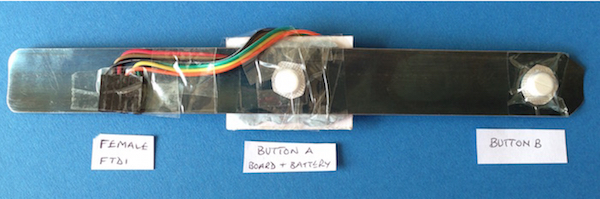
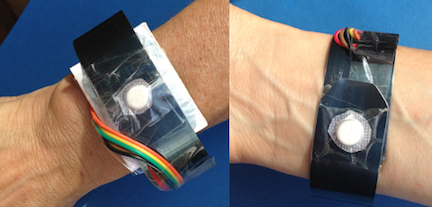
Exploring
the ergonomics
I wanted
to explore how
the user might
actually
interact with
the device. I
wanted it to
be as
comfortable
and
strain-free as
possible.
After all, it
was a device
that would
require
repeated
button
clicking for
certain count
functions.
To help me
with this,
first I cut
out a strip of
cardboard to
the rough
dimensions I
imagined would
accomodate the
components. I
then marked my
thumbs with
colour (left
and right) and
established a
comfortable
hold on the
strip. The
thumb print,
depending on
whether I used
left or right
hand left a
different
impression. I
felt it would
be good to
reflect fair
use for both
left and right
handers. This
shaped my
initial
thoughts on
the design and
look of the
device, as
shown below:
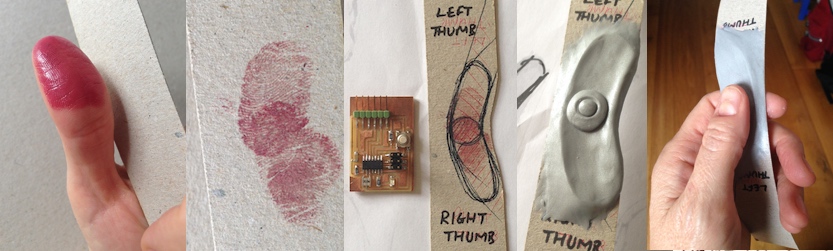
Electronics
As
it was very important for the device to be as
compact and discreeet as possible I set about trying
to get all the components on a board size 28mm X
40mm, as shown below. The second button would not be
required to be on the board itself but at the end of
the strap.
I chose to use individual solder pads to make a
custom FTDI connection. This helped me get all the
parts on board. I wouldn't want to give the
impression this was easy. This was a mammoth task
and took 2-3 days of manoeuvering!
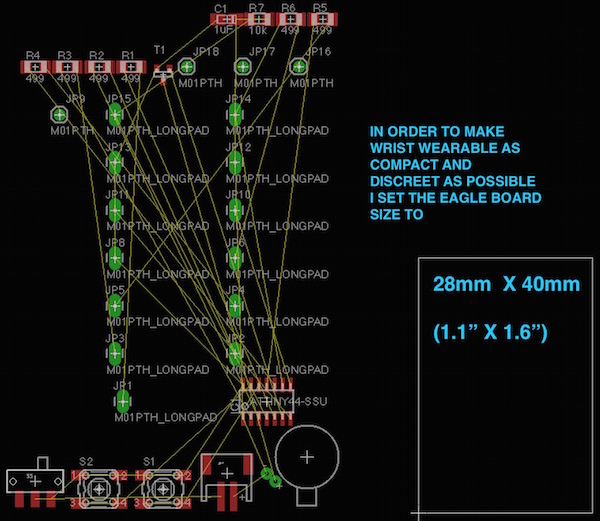
The
best possible
board design I
managed to
get, would
still require
that 3
connections
would have to
be soldered
over the top
of the board
with insulated
wire.
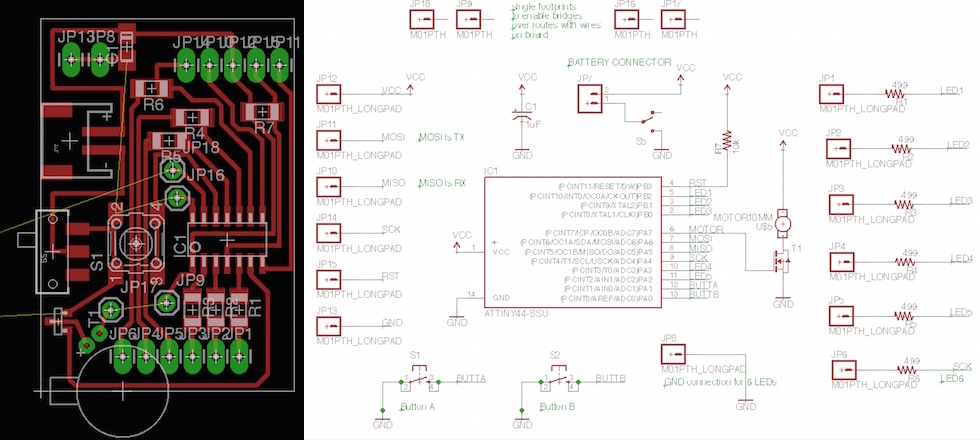
Some
finer
details
had to be
refined in
Gimp, to make
sure spaces
and clearances
were going to
be sufficient.
The board was
then ready to
mill
on the Modela.
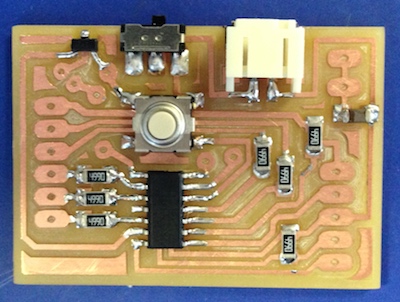
Moulding
and Casting
I
wanted to see
how all the
components
mights works
together, to
get a sense of
scale,
flexibility
and to
highlight any
problem areas. I
needed
to make
something quick,
and at home,
so I sculpted
some
plasticine,
coated with
cling film. I
thought the
cling film
would serve to
restrict any incompatibility
between
materials and
also
to create a
better
mirror-like
finish.
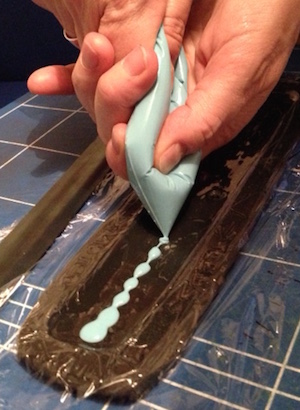
Having
learnt from
the Moulding
and Casting
Week, I had
wanted to try
and have more
control to get
the liquid
(high viscosity)
material into
detailed areas
quickly
whilst
reducing the
chances of
trapping air
bubbles. I used
the principle
of the piping
bag. This
worked really
well as the material
could be
directed
with control
and pressure.
Things
were going
so nicely that
I forgot
to embedd the
steel band!
There
was also a
significant
consideration
highlighted at
this
stage. The steel
band has a
curve
alongside the
centreline.
For the device
to bend in the
right
direction, the
curve would
have to face
down,
which would risk
trapping a lot
of air in the
very core of
the device -
very undesireable.
So
on this
occasion, I
decided to
slide
the steel band
into the
oomoo, the wrong
way up, otherwise
air
would surely
get locked in.
This meant
that the
buttons would
be on the
wrong side
but at this stage
it was more important
for me to see
the steel core
bending
whislt
embedded.
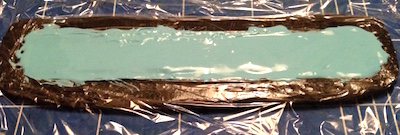
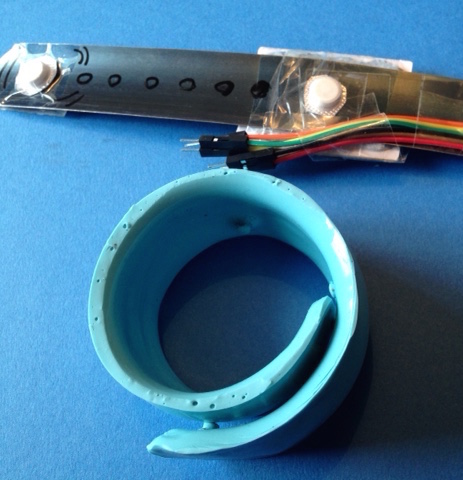
On
seeing
and interacting
with my
first cast, I
developed an
idea for a
protective
travelling
case for the device (when
not being worn
on the wrist).
The most
stable
position for
the strap
would be when
coiled.
The design is
shown in the
sketch below.
Two
elliptical
slots, allow
the user to
press the
silicone coil
inwards to
release it
out
of it's
friction grab
within
the case.
This would
be a
good
project to use
the 3D
Printer:
Back
to the
Electronics
Checking
continuity
on the board,
and so
far,
connections
were good.
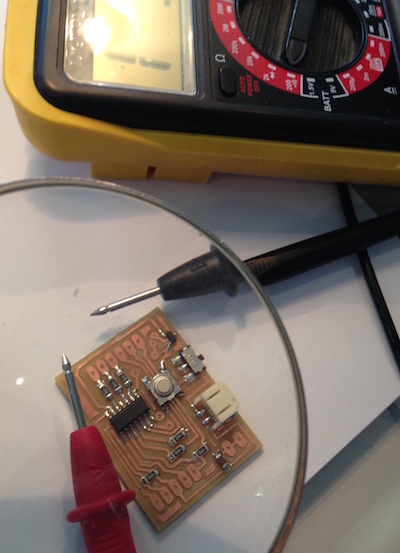
Next
it
was time to
solder the
insulated
wires (that
could not be
routed in Eagle)
and add all
the off-board
connections. I
found it
helpful to
have a clear
picture of the
connections
that I would
be soldering,
as
shown in
the image
below.
I kept
the prototypes
nearbye so
that I always
had reference
for scale
and how long
wires/cables
needed to be.
My
mentor
James showed
me a great way
to connect all
the LEDs
in an
organised
line, and
provide the ground
line on the
other side
(see below):
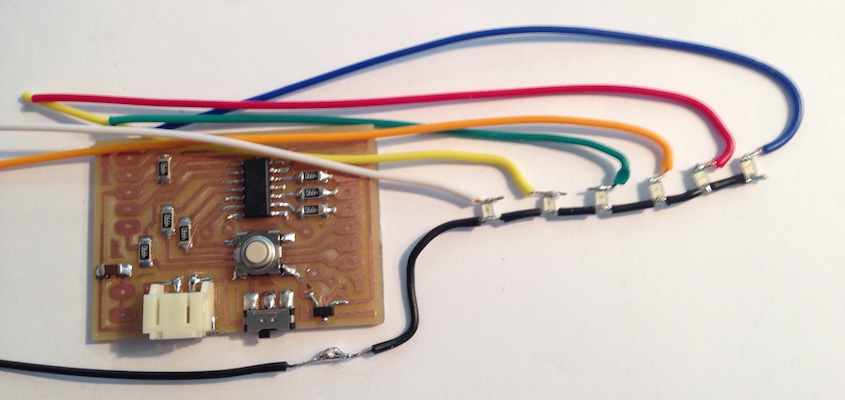
The
device would
be programmed
via an FTDI
cable.
As
the Tx and Rx
communication
lines would be
sharing the
MOSI and MISO,
the ftdi cable
had
to be reconfigured
to
suit (shown in
sketch below).
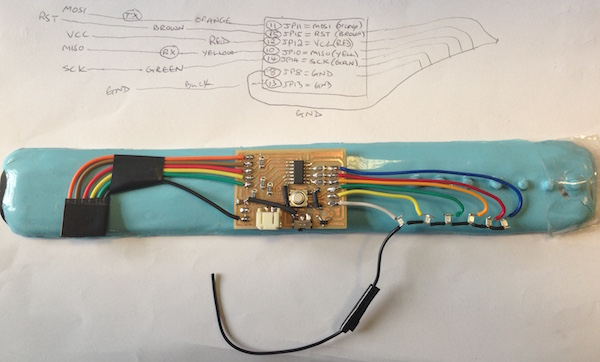
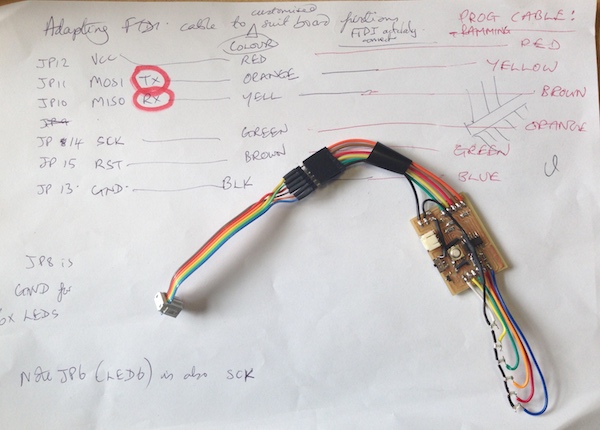
Testing
the board for
the first time
So,
before
going any
further
(adding the
motor and
second off-board
button),
it
was
a good idea to
test
the
board.
I
connected
the Fab ISP,
power from the
miniUSB and
opened Arduino
to choose the
Attiny44
board, clock
(8Mhz
internal),
programmer and
port. I
was quite
surprised that
the bootloader
burned without
any error,
but that's
what it did. A
good moment.
Then,
I loaded the
example code
"Blink" in
Arduino. I
wanted to
check each LED
in turn, so I
changed the
pin to match
the Arduino
pinout
in the code.
Error.
With
closer
inspection,
all
LEDs were
oriented the
wrong way
round -
I'd
misapplied my
logic for the
positive and
negative.
Ouch.
So
back to the
soldering
station to
spin round LED1
to
test. Having
done this and
on re-doing
the test, the
LED flashed exactly
as the code
requested. Relief.
I went
to de-solder
and re-solder
them
all. The
6
LEDs flashed
successfully
in turn.
There was one
unexpected
behaviour:
LED
6 flashed for
half
a second just
at the
beginning,
before any one
of the
other LEDs
flashed.
This
was likely to
be the
programming
pulses, and
that this
would not
happen
post-programming.
So all was
good so far. I
was now happy
to continue to
solder the
additional
off-board
elements with
wire links.
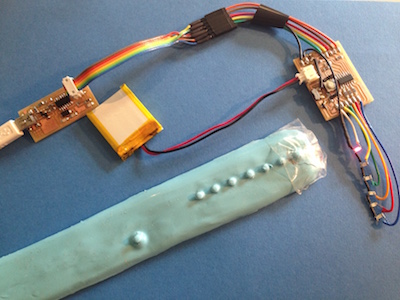
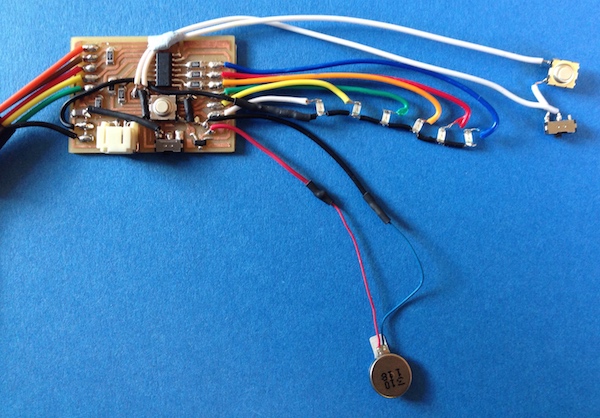
Having
soldered and
connected the
second button,
second switch
and motor to
the board,
a
poor
connection
showed up.
This was
revelaed as
the motor
just
statred up on
its own
without any
command. After
testing
under
gentle
movement, it
was noted that
when
the
transistor
area was pressed
a little,
the motor state
would
change (ie it
would start
or stop or
vibrate at higher
frequency).
This suggested that
the
motor was
receiving fluctutating
power
and only
intermittently,
revealing a
short circuit.
The
transistor
area of the
board was one
of the
narrowest of
routes, so
this will need
attention. I
had created
a route
underneath the
transistor,
so I may have
to create
an over board
link
instead.
Before
setting out to
test the function
of each of the
buttons
and motor with
code, I made
it easier for
myself
by creating
a quick reference
pin chart
so that I
could refer to
it as I tried
simple
code tests.
Functions
PIN CHART (for
quick
reference when
coding):
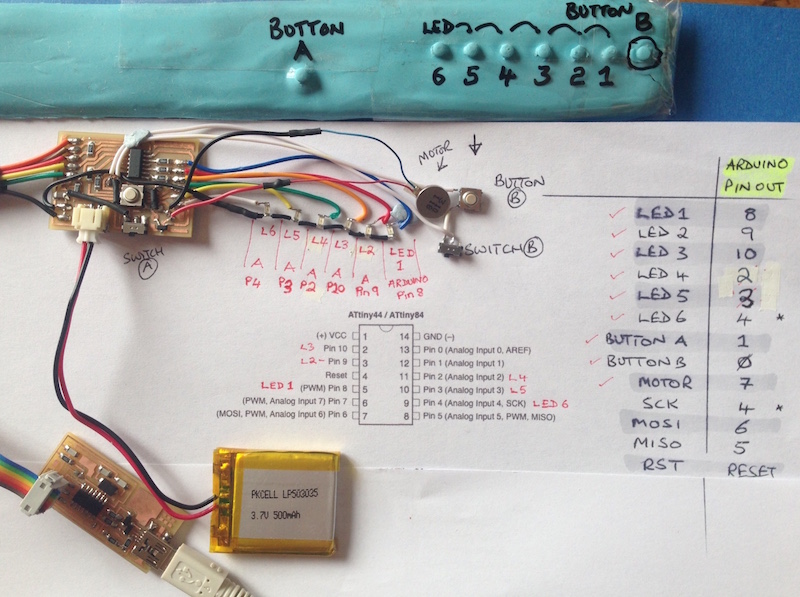
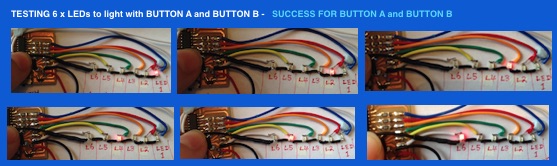
Testing
the function
of button A
and Button B
and the motor
with
the Arduino
IDE
I
adapted
the basic code
examples found
in Arduino
libraries to
test
each of the
buttons and
the motor.
Whilst
this showed
the code to
program the
board successfully
in each
instance, there
did appear
(in behaviour)
some
areas of
instability
and
sensitivity.
Further visual
inspection
checks were
made, and the
transistor was
replaced,
however, the
board was
still not
responding
with 100%
power to 100%
task. The
image below
shows the
working code
that was used
for this
testing.
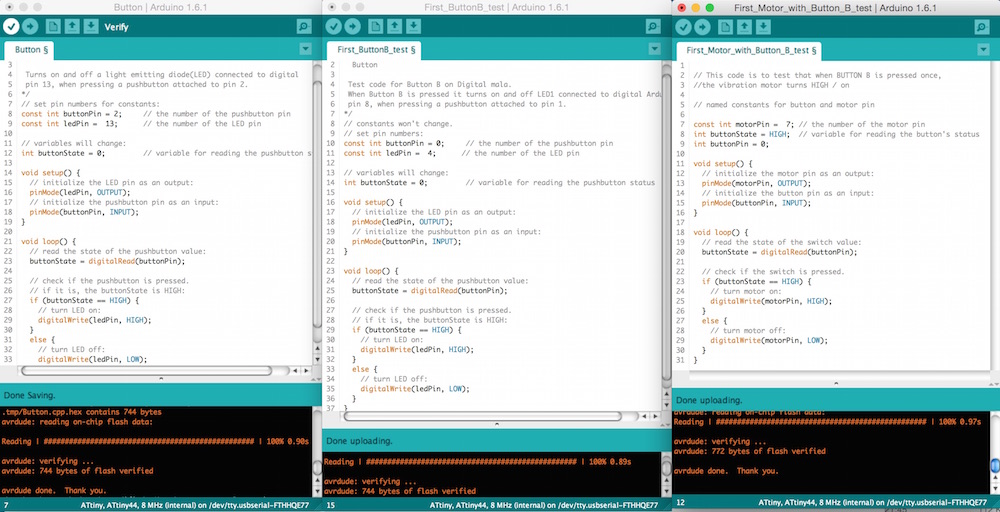
Defining
Inputs
and Outputs
As
some of the pins
on the
ATTiny
44 were
multi-functioning,
some lines
were being
shared during
processing,
and whilst
some charge
residue may be
remaining in
the circuit, were
creating
ambiguity,
appearing
like poor
connections.
However
when all inputs
/ outputs
/ pins were
defined in the
code set up
this was all
clarified and
the board
showed 100%
engagment with
each
test command.
See
definitions
below:
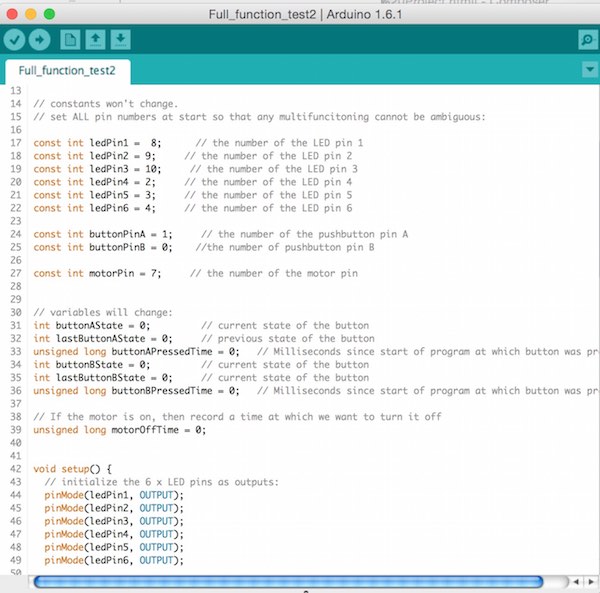
100%
Button,
LEDs and Motor
response:
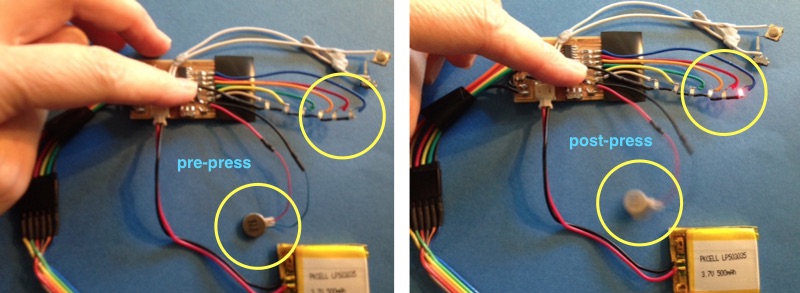
3D
Printing of
case to tranport
and protect digital
mala
Here
is
the result of
the first
3D printing
attempt of the
mala case,
produced
without
supportive
material
capability,
on a
custom-made 3D
printer
in Manchester:
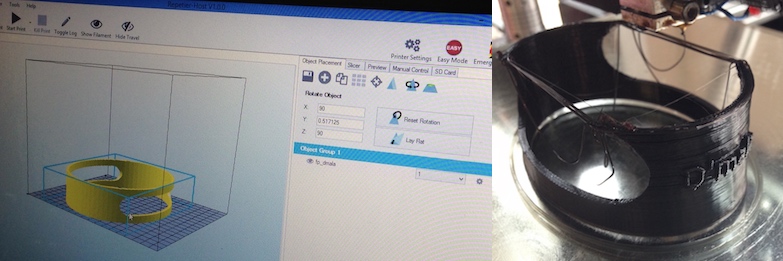
Second
mala
case design 3D
Printed by
Dimension:
As
is shown in
image above,
the 3D printed
failed
for lack of
supporting subtractive
material. Therefore,
as the
slots were
central to the
design,
I printed
the case
on the
Dimension
(sst
1200esDimension
sst 1200es),
where
supportive
material is
printed and
then dissolved
in a solution
post.
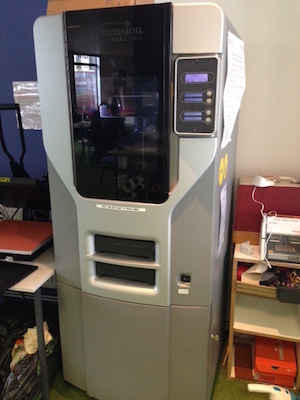
Below
right, the
support
material is
shown in the
set
up:
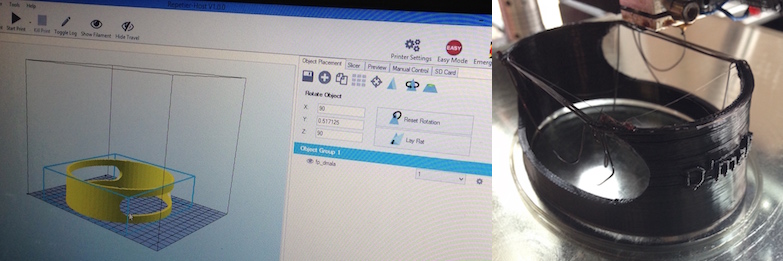
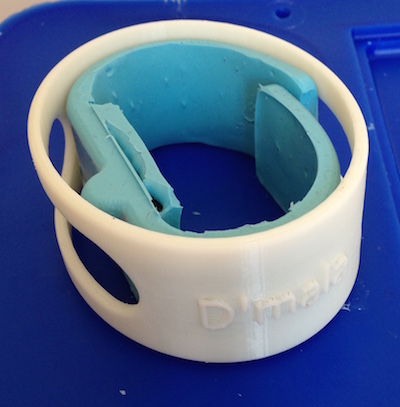
Based
on 21 cm3 model material and 12 cm3
support material, the cost of material for this
design would be approximatelay £7-8, whereas using
the first 3D printer (custom made in Manchester)
would have cost £1.50 (but this was proven unable
to 3D print the arch area successfully).
Computer
Aided Design - Drawing the digital mala design
in Solidworks
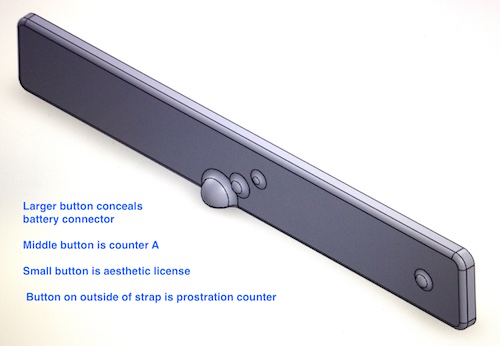
Milling the machine wax to create the mould for
the silicone
The settings for the milling are shown below.
Tools used: 3mm Flat End Mill; 1/32" Ball Nose
Mill
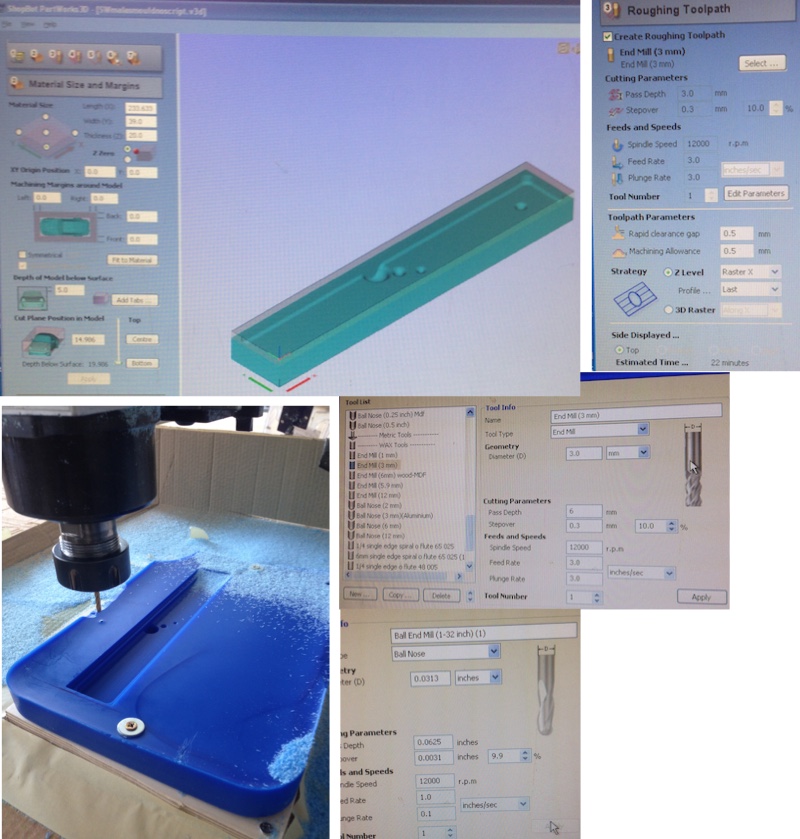
Surface detail (Mantra of
Compassion in Tibetan script) shown below was
converted from a pdf file, and added as a bitmap
trace in Partwork 3D:
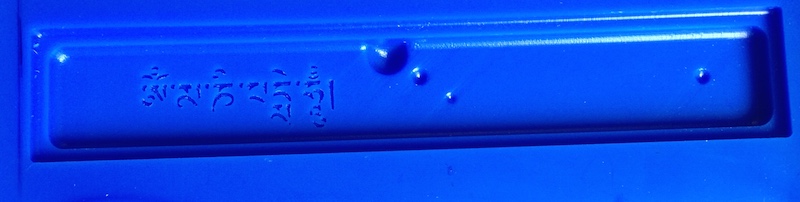
The overall quality of the milling was very good.
There was a very subtle 'scratch' surface defect
that showed up around the flat areas where the
travelling end mill was recovering from z axis
increment - shown in the close up below:
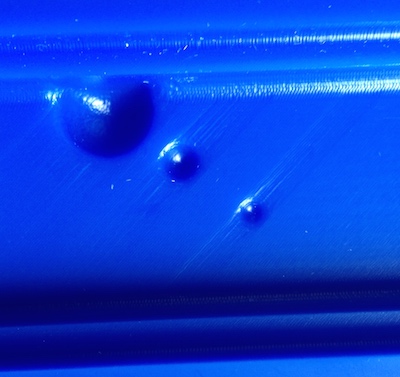
Back to the Electronics - developing the
second board - incorporating improvements
Currently I only had one working test board.
Having been through the process once, I could see
small ways in which to make improvements in the
wiring and to plan it as efficiently and as slim
as possible.There was a real risk that in moving
the board around during testing / coding that the
copper wire / solder joints were being fatigued
and were in risk of breaking off.
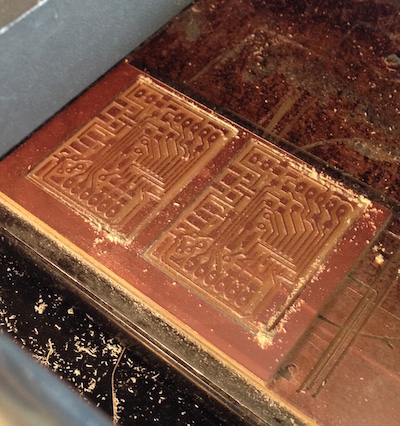
Scale drawing to guide placement of
components into mould (6 x LEDs, Button A
& B, Motor):
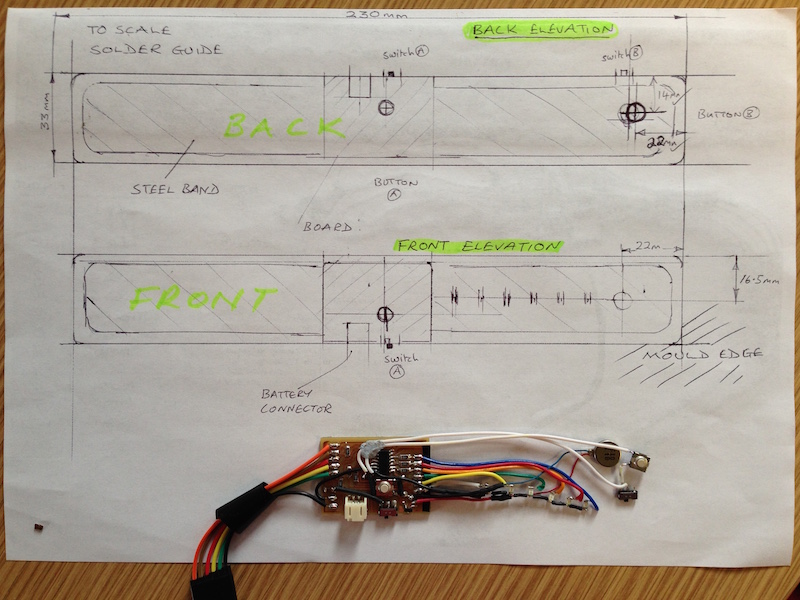
Finding ways to clamp the wire when soldering the
fiddly LEDs to try and reduce any twisting in the
wire, so that they would all face the right
direction:
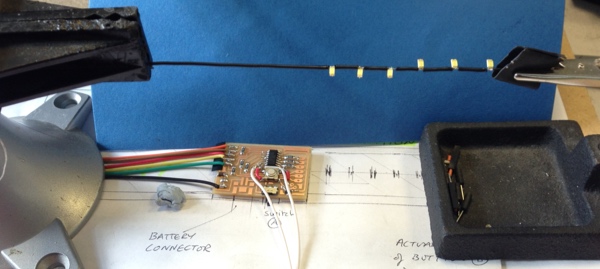
Incorporating improvements; removing 'kinks'
in wire and utilising ground at other points to
reduce wires on board:
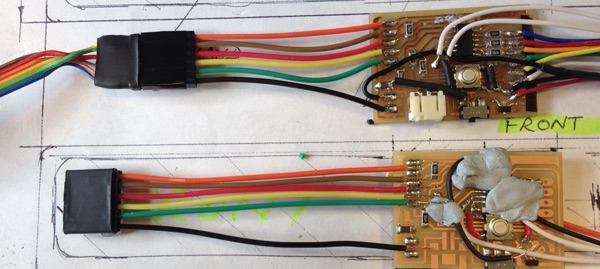
Testing the second board
Once the second board was completed, I
set about testing and programming the board with
James.
The photo below also shows the adaptor for the Rx
/ Tx comms in and out of the board:
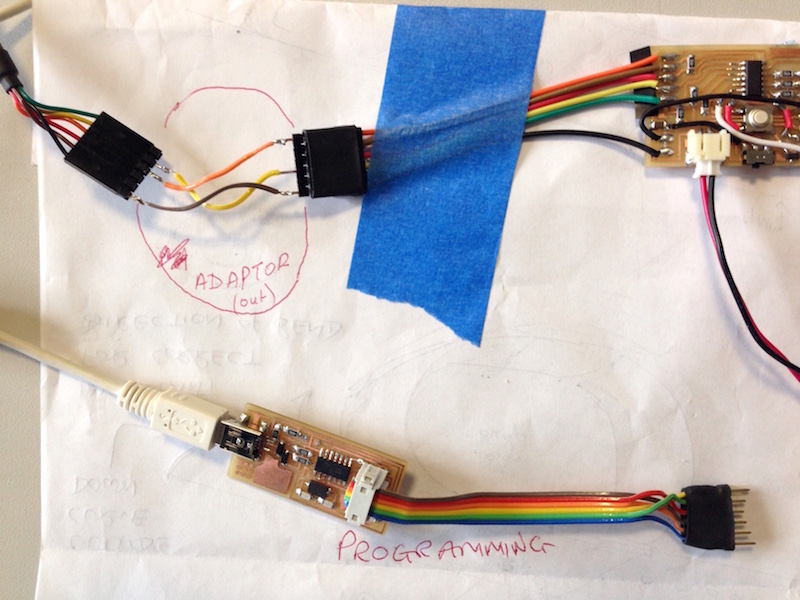
With various board test routines, all the
essential functions outlined in my intital plan
for the device worked successfully. This included
haptic feedback when a basic button press target
was reached; all 6 LEDs worked to show which count
selection was being counted, and blinking to
confirm that time mode was selected (counting
minutes instead of button presses). With these
functions in stable working order I was ready to
cast the second electronics system once I'd
completed my mould tests.
Mould development
In my first cast I had forgotten to include the
required depth to contain the 3mm LiPo battery.
However, the inclusion of the battery would mean
that the wires of the battery would have to emerge
from the main body, bend and return back to
connect with the board within the body (to give
power during use and charging during programming).
I experimented with adding a second makeshift
mould (out of cardboard) in the middle of curing
to build space for embedding the battery:
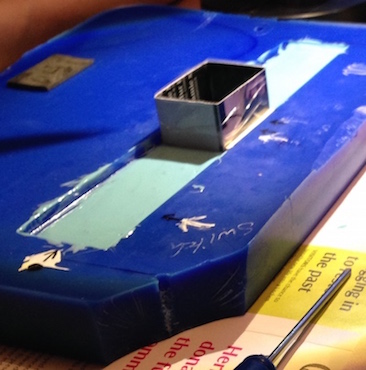
Following
this test, I decided that I would scrap
the inclusion of the battery and use it
externally for the prototype.
There
was quite a few other considerations to bare in
mind during the moulding process. For example, for
the strap to bend in the required direction, it
was critical for the curve of the steel to be set
in the direction shown below (with the curve steel
edges facing up in same direction as buttons).
Below, I
simulating the effect of the wires
and board to see how it might
affect the bend of the steel band:
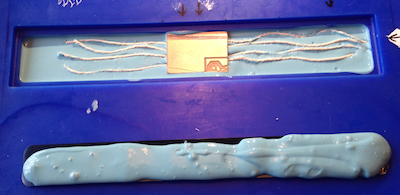
As
shown below, I designed the device around the
constraints of the electronic board and
components; the battery connector was particulary
obtrusive but totally necessary. I designed a
series of spheres: the largest to house the
connector (and in this way, reducing the
impression of the depth of the central body); the
seond to house the counting button; I introduced a
third dimple simply to create a sense of rhythm in
the spheres - and a homage to traditional mala
beads.
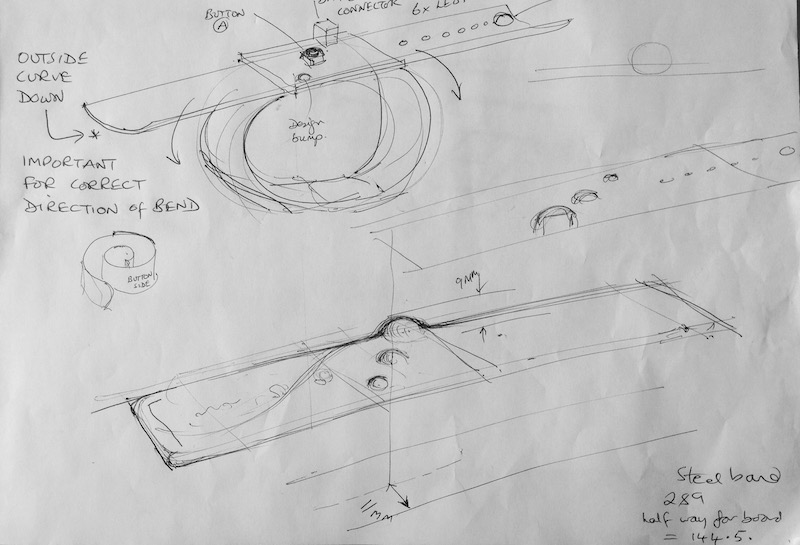
Transparent vs Opaque SIlicone
I produced a number of moulds. The one below on
the left was made with "Sorta Clear" Liquid
Silicone. The advantages to this silicone was that
it was semi-transparent and would improve the
luminescence of the LEDs. Also it was interesting
to see the placement of
the electronics
and behaviour of the steel band embedded inside.
This particular prototype proved to be much too
thick, with the steel finding it impossible to
bend uniformly due to the board thickness (mocked
here by a 3 mm thick plyboard). I began to concede
that the steel band would not bend and clasp with
a square circuit board embedded.
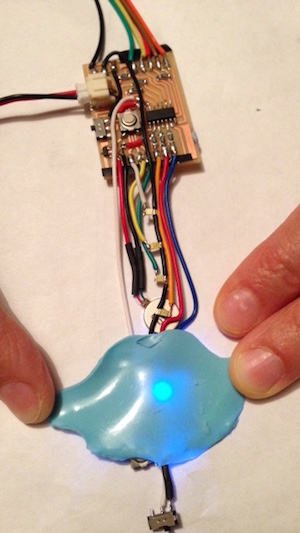
Below, a traditional mala is shown next to a
D'mala casting. The image on the right shows the
inner wrist button for floor pressing (counting
prostrations).
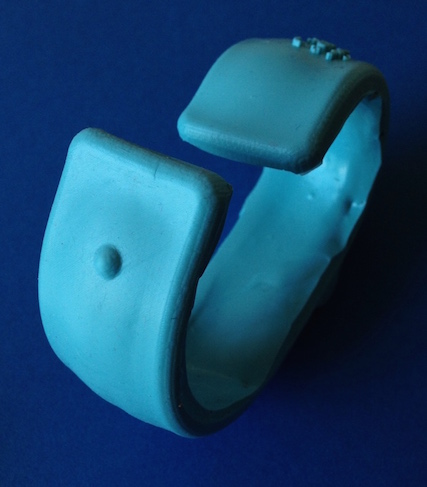
Casting the actual electronics
So
far, all the prototypes did not include
any electronics. When it came to casting
my actual first programmed and working
electronics system, there were a few
things I had to consider. I
had decided that I
would not embedd the
battery in the
prototype, as it
made everything too
cumbersome. I would
connect the battery
as an external unit
for the time being.
To make sure
that silicone
would not fill
voids (such as
the battery
connector
cavity and
ftdi
connectors) I
filled them
with blutack.
It worked
well, and as
blutack sticks
to blutack it
was quite easy
to remove.
Having
mixed the 2 part liquid rubber
solution, I used a piping bag to place
the first layer. Then, I had
to try and place the 2 buttons and LEDs
as accurately as possible in their
respective mould recesses in the cast.
With experience from the earlier casts,
I felt the silicone would begin to hold
the loose components in place after a
short while. Therefore I used toothpicks
to hold button B and the switch in place
for about 10 minutes.
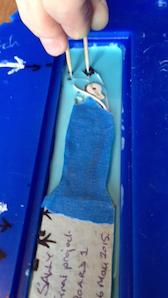
Once
I had the electronics curing
in position, I was able to add
the remainder of the silicone
into the mould.
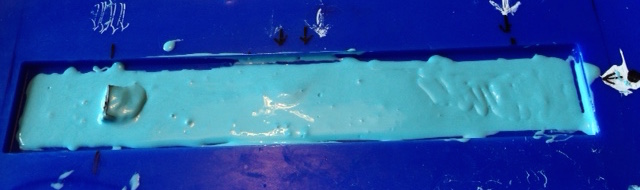
Curing time = 1.5 hours
Post-casting tests
I removed the blutack, cut away any excess
silicone and connected the power and cables to
check connections post-casting.
Everything connecting well.
I pressed the buttons to test the code. As
expected, a button count of 5 activated vibration
alert form the motor and lit LED 1. This was a
very satisfying. All the LEDs worked apart form
one (this was explained by a resistor I found on
my work bench). However, the opacity of the
turquoise silicon made the luminosity of the LEDs
virtually ineffective. Fortunately, the LEDs that
I used in my second electronic system were much
more powerful with a greater lumnens value.
Nonetheless this made me decide to cast my second
board in the Sorta Clear so that the lights had a
greater chance to be more effective.
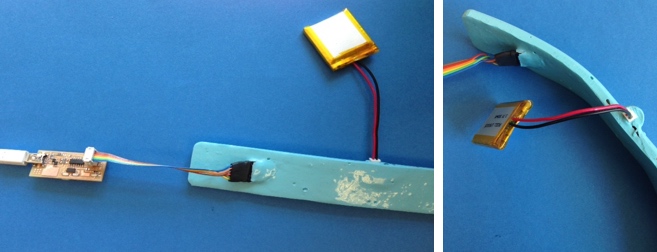
Arduino
test code to
run to serial
monitor
In
this
test, the
second
electronic board
was programmed
to
discern 2
different kinds
of button
press - single
presses and
button
hold
press and
to send
7
unique
sets of
data (reflecting
simulation for
7 days of the
2
kinds of data)
to the serial
monitor;
this was a
succesful
output test,
as shown below:
(For
fuller comments
- see code
file at end of
document)
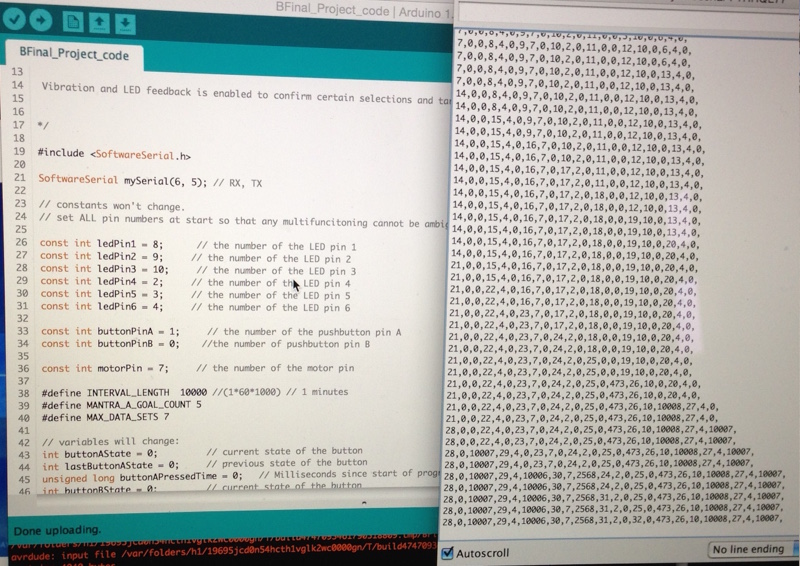
Processing
Next,
I could return
to the basis
laid out in
the Interface
and Application
week, to use
'Processing'
to convert
the data
from the
device into a
meaningful graphic
display for
the user to
see progress
in mantra
recitation
or mindfulness
training
(again,
I could
not have done
this without
the help of James
Fletcher -
a legend).
The visual
graphics
below appear
(virtually live)
from direct
button
presses
into the
electronic
board:
(For
fuller
comments - see
code file at
end of
document)
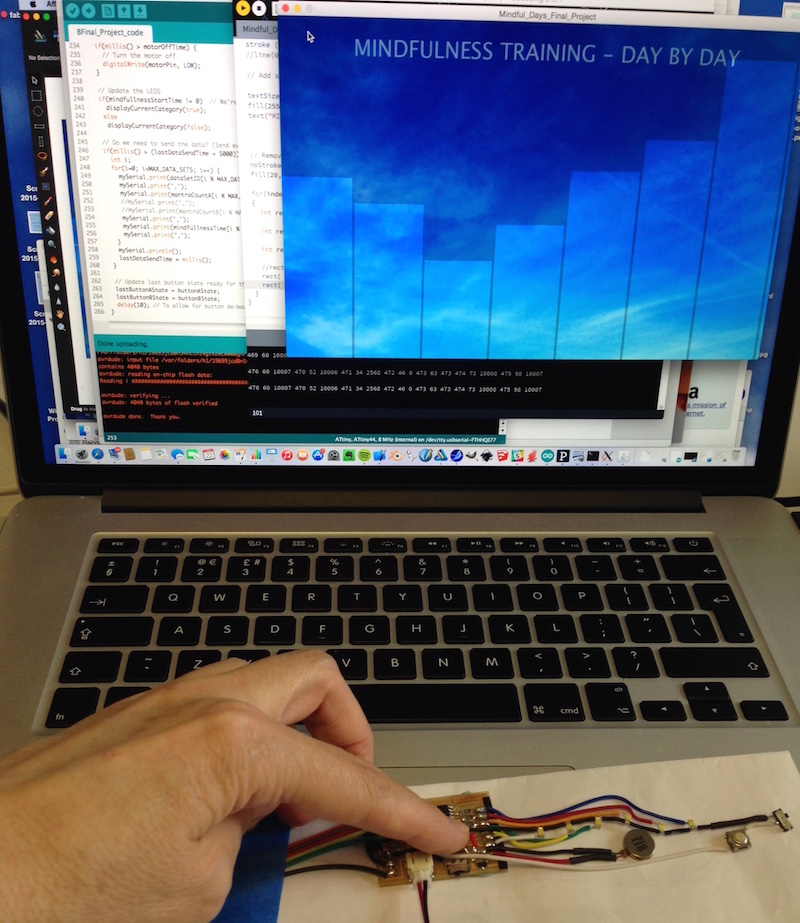
Final
Casting
With
the input
and output
code now
working, I
felt ready to
undertake the
final casting
for the second
electronic
system. I had
decided to use
the clear
silicone, so I
could see how
the electronic
detail behaved
inside and
to improve
luminosity
of LEDs.
Planning
I took
care in
planning how I
would
secure the
buttons and
board in place
before
I prepared
and mixed
the liquid silcone:
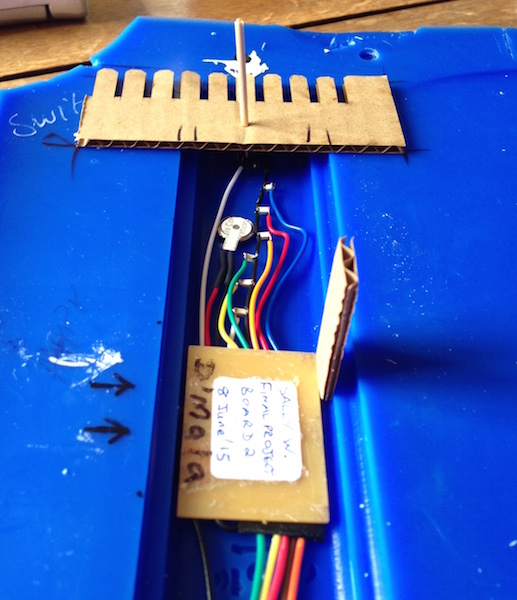
As shown above,
I held
the button and
board in place
with a few props
until the
silcone
started to
cure.
Then,
I
added the
remainder of
the silicone
to cover
the components.
Trying
to take care
not to
overfill:

Failings
of
design
The
only area
where there
were clear
failings in the
design
were
the methods
I trialed in securing
the mala
around the
wrist.
Steel
band
clasp - Failed
This
failed due
to
the
size,
straightness,
depth and
strength of
the electronic
board, prohibiting
a
consistent
bend.
As the steel
band is
bistable, it
cannot be both
flat
and curved.
My design was
asking for too
much
flexibility
around the
board. The
clasp would
not snap
around the
wrist. I
still envisage
that
the steel band
would work
well with
felxible
electronics
- a solution
that would
be ideal
for future
development.
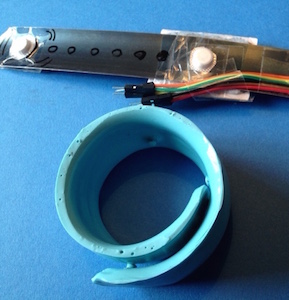
Magnetic
clasps - Failed
I
experimented
with several
different
magnetic
solutions.
I tried
embedding
small, but
powerful (1kg
pull) magnets.
The problem
here was that
when
the magnets
were embedded
in the
silicone, the
flush and
direct
magnetic
contact
required for
the 'pull' to
be effective
was
significantly
reduced
to the point
of being
ineffective. However,
if the
magnets were
embedded too
near the
surface, the
silicone was
not strong
enough to keep
them
contained
and the
surface
gradually
fatigued and
they fell
out (see image
below).
As
a last
attempt
solution
before
submitting my
final project,
I tried to glue
polarised
magnetic
strips, on the
outide surface
of the silcone
(so that
at least the
magents could
be in
direct contact
with each
other).
However, silicone
is non-stick,
and I have not
found
a flexible
adhesive that
has worked). Online
comments
suggested
silicone
adhesive would
not work
either. Even if
it would work
in the
short-term,
it would not
be an
effective long-term
solution as
the magnet would
pull
itself
off over time.
Final Cast removed
Below, all connections for inputs and outputs are
shown with final cast (with adaptor connection on
right):
I was happy to see the D'mala flexing well and
stable whilst testing:
Evaluation
As
outlined in
Application
and
Implications
in week 15, my
final project
would be
evaluated by
the questions
shown
below;
and this time
I can include
the findings:
• Does the
digital mala count, record and function
as a counter (in reliance of a PC to
output data)? Yes
• Are the counting functions and modes
working as expected? Yes
• Does the vibration feedback provide
alerts as and when expected in the
functionality? Yes
• Does the silicone encased steel work
effectively as a wrist clasp? No
• Does the app effectivley communicate
the data to the user?
Yes
And again, the end of one road, the beginning of
another...
Thank to Michael, James, Simon and of course,
Neil.
FINAL PROJECT
DOWNLOAD FILES
ELECTRONICS
Eagle:
Schematic
Board
Files
to
mill board:
Traces
Outline
CAD
Mould
Solidworks file
stl
file
without script
3D
Printing
D'mala
case stl file
CODE
Arduino
Arduino
code:
Inital
function
test code
Final
Project
Arduino Code
Processing
Processing
Code:
Code
for graphic
visuals to display
output
data
Background
image
© Sally Williams June
2015. All rights reserved.