WHAT
In the past year I have been experimenting with 'printing' hydro-span, a swelling material, onto textile surfaces to obtain shape change. I am fascinated by the ways physical patterns and patterns combinations can implement different physical configurations of structures.
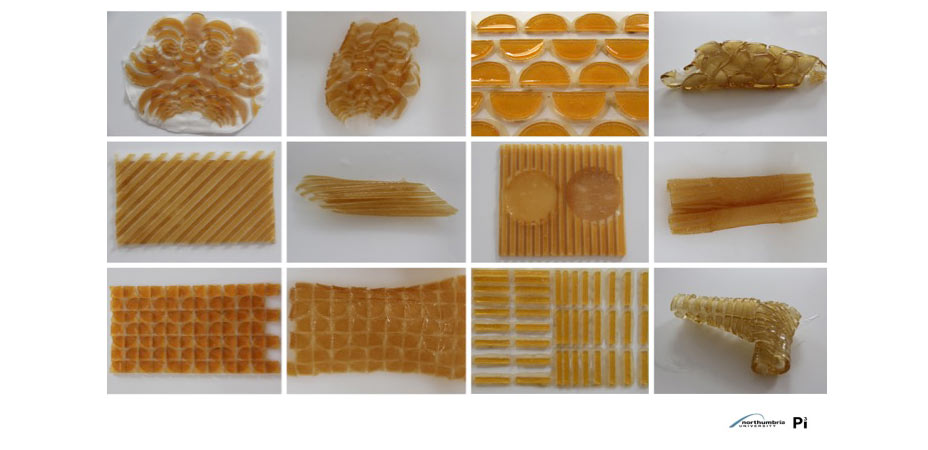
I am interested in studying more this effect, and make more complex experiments, with different techninques, but most of all, I want to start understanding how can I KEEP TRACK OF THESE EXPERIMENTS, feed them into a system that can STORE DATA about the effects obtained.
What will it do?
The final project wants to start tackling these question: HOW TO BRIDGE A PHYSICAL PROTOTYPE WITH A REAL-TIME INTERFACE.
I want to create an ACTUATING AND SENSING (MODULAR) SOFT SURFACE, AND BRIDGE IT WITH A DIGITAL SIMULATION.
The substrate will be subdivided in multiple HINGES.
The inclination of each hinge will be SENSED (sensors and microprocessors) and informations sent via serial inforamtion to a 3D MODEL of the same structure, which will respond in real time to the changes happening on the surface.
(Ideally I would also be able to store the information for future purposes.)
>>This last part of the development of the project had to be abandoned due to the timescale The 3D SURFACE STRUCTURE will happen through an interaction between materials .
The substrate will go from flat to a 2.5/3D structure either through:
- swelling material printed/casted on rigid textile
- flexible filament 3d printing on lycra textile
- rigid PLA 3d printing on lycra textile.<<
How will it be evaluated?
The aim of the project is to :
- implement a surface with different material characteristics in selected area (originally shape change, then composite surface)
- develop a sensing system embedded in the surface itself
- visualise in real time surface change
I suppose I will evaluate the prototype based on few factors:
- quality of fabrication of surface
- quality of fabrication of sensing system
- accuracy of material system visualisation
- how much have I learnt in the process
WHO
Has done what beforehand?
This project is moving in the direciton of:
'DIGITAL MATERIALITY'
'4D PRINTING / SELF ASSEMBLY'
'SOFT ACTUATORS'
Here some references:
Theoretical perspective
QUESTION: How can we program physical materials to 'build' structures and change shapes without the use of electrically actuated materials, and without the need of human interaction (responsive materials)?
> Skylar Tibbits Self-Assembly lab
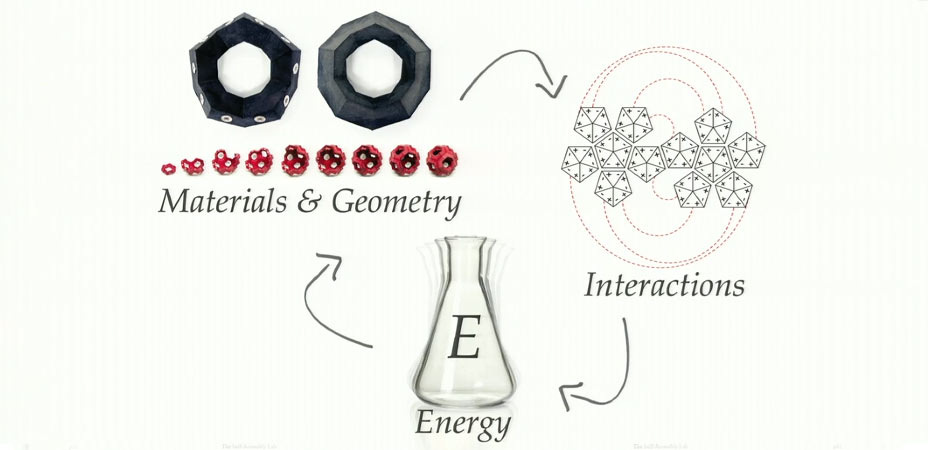
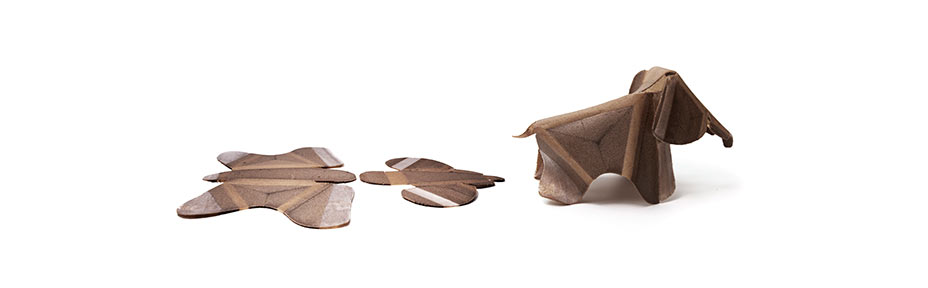
> Research for hydrogels applications as soft actuators
Hydrogels are responsive materials that have been extensively investigated in the literature, and can be formulated to respond to specific environmental/chemical stimuli by swelling or shrinking.
Processes of photomasking can selectively cure areas of these substrates, rendering them more or less responsive to specific stimuli. Such photomasked patterns can be tuned to obtain shape change.

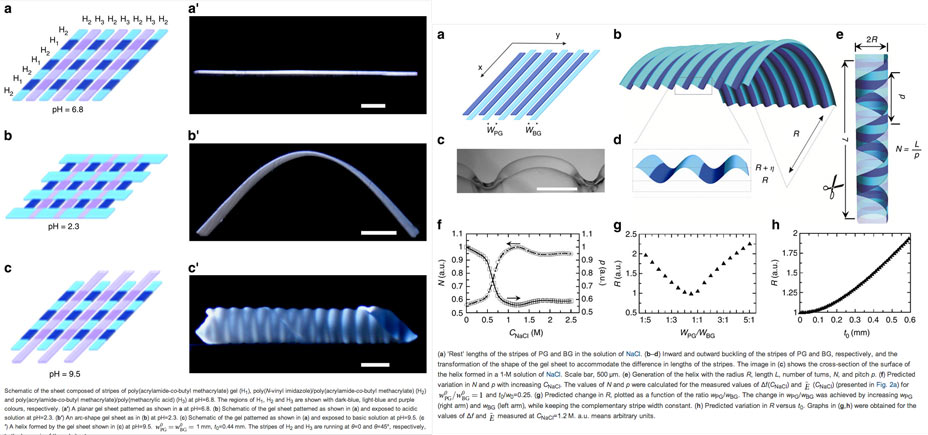
These materials and the research around them works at a much smaller scale than the one proposed by Tibbits: for medical applications and sensors mostly attached to the skin of a user, or for internal implants due to the biocompatibility of the material.
Practical development
QUESTION: What type of structures can I start implementing?
QUESTION: How can we keep track of the occurring changes on the surface in a digital system?
> Research in Origami techniques
Origami structures are perfect examples of geometric structures that can 'shift' shape. Their geometrical patterns make it easier for me to start investigating the final project.
Designing Freeform Origami Tessellations by Generalizing Resch's Patterns
New Deployable Structures Based on an Elastic Origami Model
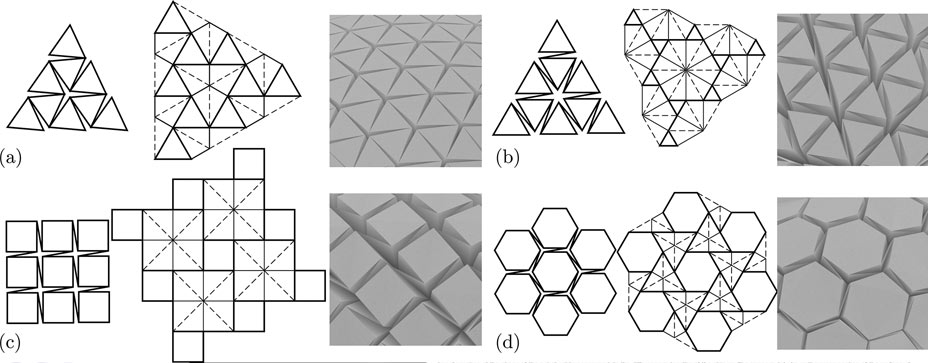
> Surface Simulation behaviour
Bartlett Morphogenetic Programming
Rhino + Grasshopper + Kangaroo Origami examples
Rhino + Grasshopper + Kangaroo Origami examples
Rhino + Grasshopper + Kangaroo rigid Origami examples
Origami simulation software
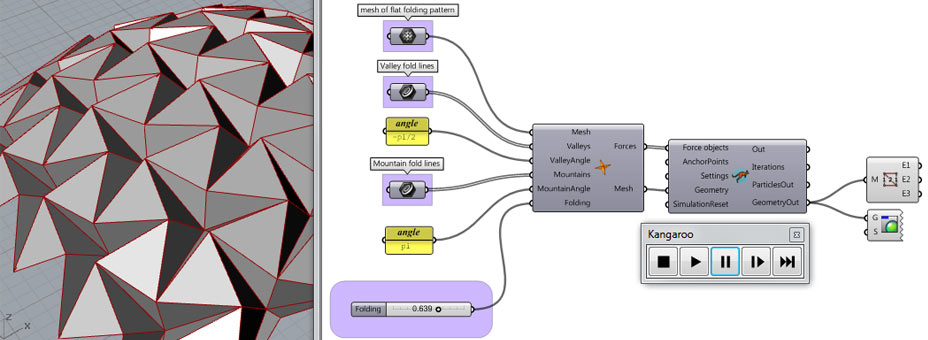
Possible future applications
- Research in smart packaging
- Intuitive consumer haptic feedback system
- Interactive installations development
- Textile sensing systems
- Textile/garments construction
- Modular toy for kids
- Assistive health-care / skin care
HOW
What parts and systems will be made?
What processes will be used?
What tasks need to be completed?
HINGES: SENSE INCLINATION
S1. WHAT SENSOR TESTS
- Capactive step response
- Capacitive rxtx
- Capacitive
- basic 'Switch'
- variable resistance of conductive thread
- Hall effect sensor
S2. DETECT VALLEY AND MOUNTAIN
- quick design hall sensor board for more than 1 sensor (sensors loose from board to be attached on surface)
S2.2 IDENTITY SENSING:
- detect threshold mountain/valley/touching
- do I need 'Identity' sensor for each of them?
- faster in grasshopper to visualise what face or in processing?
- precision in detecting when touching: capacitance or fine tuning hall sensor?
- locking system?
S3. ELECTRONIC COMPONENTS FOR SENSING SYSTEM
- List components for single hinge
- Soft fabrication of sensor(embedded in surface through casting, vynil cut traces etc...)
S4. SERIAL COMMUNICATION ?
- Send single serial data to grasshopper
S5. MULTIPLY COMPONENTS FOR AMOUNT OF HINGES
- How many components
- how many pins in use
- What/how many microprocessors needed (Fab Leo, Fabkit, Barduino)
S6. FINAL SYSTEM
- Design of complete schematics
- Fabrication
S7. SENSE ALL HINGES
- Testing on paper prototype
- Sending multiple serial identities through serial port
SOFT STRUCTURE
A1. WHAT STRUCTURE
- Research possible origami structure
- Design possible origami structure (basic pattern with 4-8 hinges)
- add nr of sensors and positions (both hall sensors/magnets and capacitive locking points)
- Make in paper and choose one to work with BASED ON POSSIBILITIES TO ACTUATE
A2. WHAT MATERIALS / TECHNIQUES
- Hydromorph + ortogonal textile / molding & casting / wet system > waterproof electronics
- flexible filament with lycra/ 3d printing
- PLA with lycra / 3d printing
- How to choose between the different possibilities? - If any of these techniques doesn't work, what other option? composites?
A3. TESTS OF ACTUATION:
- Buy unresponsive bases
- Design patterns to 3d print / lasercut to cast & mold (start with few hinges)
- choose which material with which technique
- how to structure folds? bimaterial?
- how to make sure tension material is the same across whole pattern if using lycra? ex. draw small rectangles where relaxed that need to correspond to whole surface makerbot
A4. LOCKING HINGE?
FABRICATION
F1. LAYERS
- choose materials /fabrication techniques for system
- vynil / Lasercut to protect pattern if casted?
F2. ORDER MATERIALS
- order materials
F3. EMBEDDING THE ELECTRONICS
- Electronics need to be as light as possible or will influence shape change, threads included
- How to embed the electronics in the bottom layer (vynil cut / mold & cast / composites)?
- Flexible circuit?
F4. EMBEDDIGN THE MAGNETS
- what fabrication techniques to fix it to surface?
F5. ELECTRONICS TO MICROCONTROLLER CONNECTION
DIGITAL INTERFACE
D1. SINGLE HINGE - GRASSHOP
- Interface single hinge with grasshopper (serial port data)
D2. MULTIPLE HINGES
- When origami structure chosen design structure for simple origami example and simulate change
- where to add incoming data from sensor
D3. RECORDING DATA
- ? processing? grasshopper? text file?
MATERIALS
This initial list is in development. Outcomes of the experiments will shape the materials in use. Please refer to BOM in Final Project page for a full list of materials used.
INITIAL TESTING:
- Paper
- Textiles
- hall sensors and magnets
PRODUCTION:
- acrylic for lasercutting
- vynil for vynilcutting
- flexible ninja filament
- PLA filament
- thin flexible wire (Fablab)
- textiles: Ribes y Casales
- plastic glasses and sticks for composites
- hall sensors - IC SENSOR SOT23W - 620-1021-1-ND
- magnets
- silicone for molds
- epoxy for composites
COSTS:
Please refer to BOM in Final Project page for costs.
The outcomes of the experiments will heavily influence the choice of materials and production processes and therefore the costs involved.
Still to answer:
- complete list of materials
- where will they come from?
- how much will it cost?
- clarify what processes will be used?
WHEN
WEEK 1 (13-19)
/ plan
/ A1 research possible origami structures
/ S1 test and choose sensors to work with
/ A1 Design basic patterns, with different colour mountain valleys
/ * based on shape change possibilities *
/ A1 work out contiguity of sensor / magnets / hinges locking points
/ S2 quick design hall board (at44 - 8 analog input pins) for a section of origami chosen, let sensors loose for attaching to textile
/ A1 make tests with sensors & choose paper experiments easier to sense
/ S2 mill basic board
/ add sensors
/ S4 serial communication of 4 hinges - arduino
/ the sensor doesn't know if it is in mountain or valley configuration so I will have to find a solution to this !!!!!!!!!!!!!!!
WEEK 2 (20 - 26)
/ list of known materials WED MORN
/ buy magnets
/ A3 buy fabrics to run test
/ A2 decide techniques
/ F3 S3 choose soft fabrication technique for sensors
/ lightweight wires
/ S3 How to fabricate final electronics and place them on substrate?
WEEK 3 ( 27 - 2)
/ A3 Design shape change patterns
/ A3 3d print tests
/composites tests / F1 choose fabrication technique in detail for composites system / S3 fabricate electronics test
/ move sensors to triangular structure
/ convert to values that can be understood by grasshopper
/ import serial to grasshopper and split
/ D1 start visualising single hinge
/ turn example grasshopper in your single tiling
/ S7 test on paper prototype
WEEK 4 (3 - 9)
/ how many modules????
/ sensing mountain and valleys on one module? or expand modules?
/ test magnet on surface attachment
/ test silicons and glues for sensor fabrication
/ decide how to attach all electronics
DEPENDING ON THIS CHOICE:
/ fabricate electronics FINAL
/ Acrylic as frame for composites
/ buy other materials for FINAL composites production
/ choose materials for composites
/ design files
/ fabricate composite surface
/ S3 attach electronics
/ S5 S6 Fabricate and design total electronics: Fableos/... OR ATTINY networking needed design
/ S7 interface all serial data (network?)
/ D2 design mesh for whole grasshopper visualisation
/ Actuate grasshopper visualisation without data
/ D2 import all serial port data
/ fulfill project docum requirements
/ Design diagram sensors placement
/ Design slide TUES
WEEK 5 BONUS (10 - 17)
/ intellettual property / compile list of materials and bill of materials
/ files online
HOME | ABOUT | WORK | CONTACT
Francesca Perona © 2015

This work is licensed under a Creative Commons Attribution-NonCommercial 4.0 International License
Original open source HTML and CSS files
Second HTML and CSS source
Francesca Perona © 2015

This work is licensed under a Creative Commons Attribution-NonCommercial 4.0 International License
Original open source HTML and CSS files
Second HTML and CSS source