Mechanical Design
Machine Design
June 22, 2015
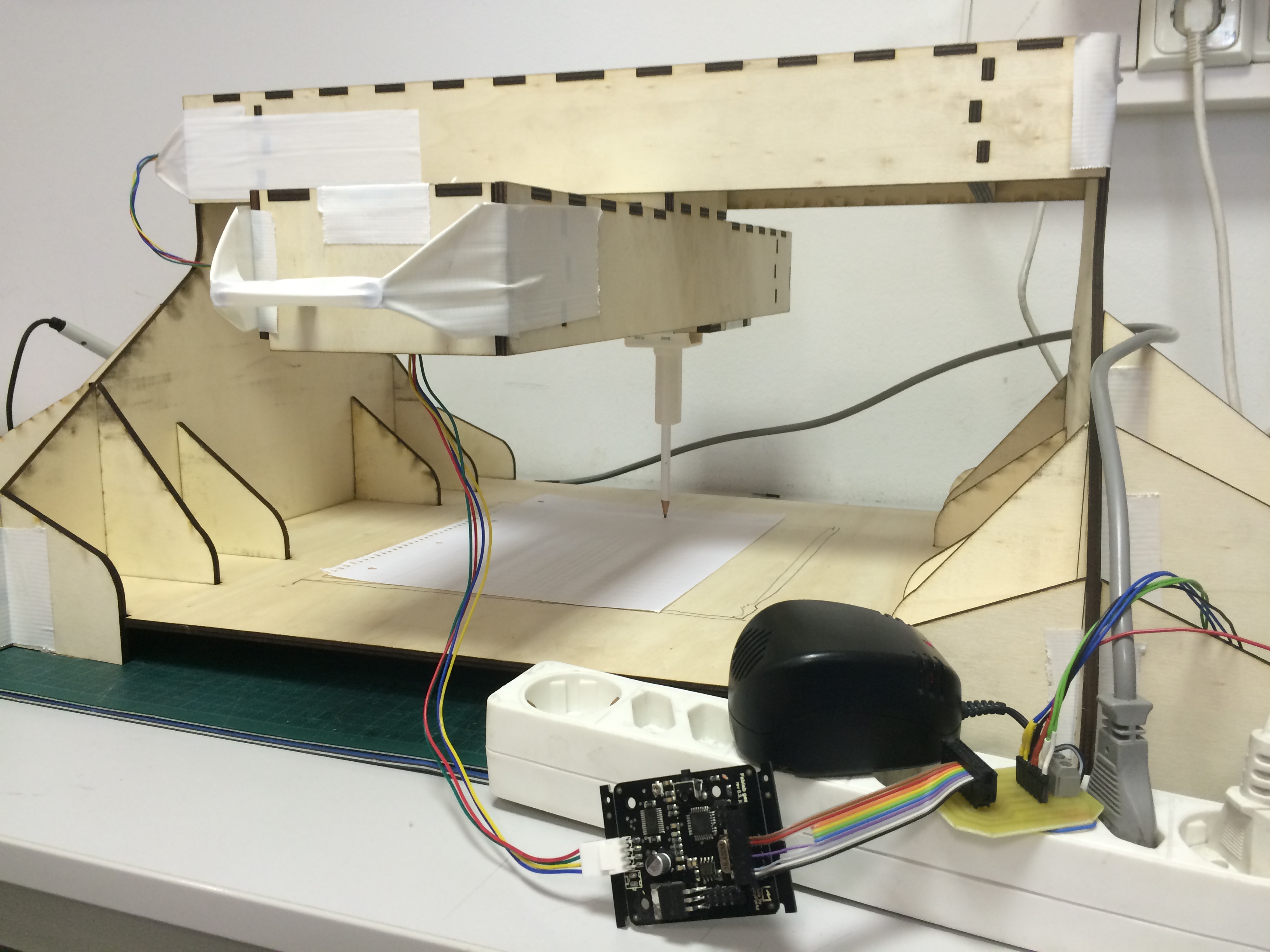
Assignment:
Make a machine including the end effector. Build the passive parts and operate it manually, then automate your machine as a group project.
Mechanical and Machine Design was a group assignment. Even though we are only two students at our Fablab - Happylab Vienna (Myraida
and Juliette) we managed to complete our machine, a Wooden Plotter.
Our division of tasks were primarily:
Electronic Design by Juliette and Mechanical Design by Myraida.
We began by downloading Rhino and Grasshopper. After a few online tutorials to understand how these programs work we proceeded to download the files for the stages fom the
tutorial page.
Our first problem was that we did not have 3mm thick cardboard available locally but instead a 6mm cardboard. We tried
using the parametric model with grasshopper but for some reason it was not possible for us to modify it easily for a 6mm
thick cardboard.
We decided to use 3mm thick cardstock instead which was much denser and brittle than poster cardboard. The results were not successful (see photos below):
Without a good cardboard available to us we decided to use a 5mm thick plywood. We adjusted the design of the stages for wood and ended up with a new machine design. The design was drawn on Autocad and laser cut. We then proceeded to assemble the pieces together with tape. Minor adjustments were needed on the design but at the end everything came together.
For the tool head, we decided to make a pen holder. After designing it together on Solidworks we 3D printed it. Here is the pen holder file.
Once all mechanical parts were finished, we glued almost everything together, mounted the stepper motors and axis. Myraida will re-use the stepper motors and axis for her final project hence the white tape on portions of our final machine.
For the electronics, we re-designed and built the FabNet in Eagle. Here is the eagle file.
We then proceeded to download and install all the programs that were needed to run the gestalt nodes on Happylab's computer (python 2.7, pyserial, guestalt-master, wxpython ...) and wired everything accordingly, following the instructions on the tutorial page.
Unfortunately, when asked to click on the Gestalt button to identify the corresponding axis the gestalt nodes were unresponsive. The message received was:
"XAxis: Could not reach virtual node..."
After weeks of trying to figure out what was wrong and asking for help from others in the Fab Academy, without success, we decided to test the hardware of our two gestalt nodes. We programmed the gestalt's microcontroller directly and with a simple C program the motors were able to move. We then proceeded to test the FTDI cable with the oscilloscope and no problems were perceived. Nevertheless, one of the recommendations received was to replace the cable, so we went ahead and ordered a new one. With the new cable we are able to receive a signal back from the gestalt node, when identifying the corresponding axis.
We were happy to finally move forward on this point even though not all problems were resolved. Now, when the pink light at the node turned on and we clicked the gestalt's button to identify the axis, we received a new message:
"XAxis: http://www.fabunit.com/vn/086-005a.py"
We retried 11 times and received the following message:
"XAxis: Could not reach virtual node. Retrying (#2 through #11).
Unfortunately, the web link was not functional and we were unable to proceed further.
Our lab manager really tried to help and we have tried all previous recommendations from our FabAcademy community. Unfortunately, we have absolutely no idea what is wrong and we are helplessly lost. It's all very disappointing especially after so many attempts to figure it out.
Our machine does not work....
Update:
While working a few days later on my final project, An Affordable CNC Machine, we took Neil's advice to program directly the micro-controller of the gestalt and came up with the first draft of a C-Code which makes the pencil move in opposite directions. It changes directions when the button on the gestalt is pressed. It also moves at different velocities according to the direction.
Here is the link to the Machine Design C-Code File:
Here is a video of the functional Wooden Plotter:
Machine Design C-Code