Machine Design
The Machine Design week is a teamwork week, where we all team up to design and make a machine. Here I will tell about what I have done as a part of the team. We decided to make a maze that could be controlled by two step-motors. Besides calibrating the axis with David I made the design of the maze it self. We also had a discussion in the group about how many axis was needed to control the maze in all direction.
Designing the maze
For a start, I wanted to make a simple maze so it would be easy to navigate through, but after doing some sketching, I got the idea to make a generic design.
The generic design, makes it possible to change the maze, which would be good because we could then practice and make the machine work with an easy maze, and after that we could make a more difficult layout. The maze is attached to the axis with two long pieces of plywood with living-hinge so they can bend in all direction, they do not have to bend much to make the maze tilt.
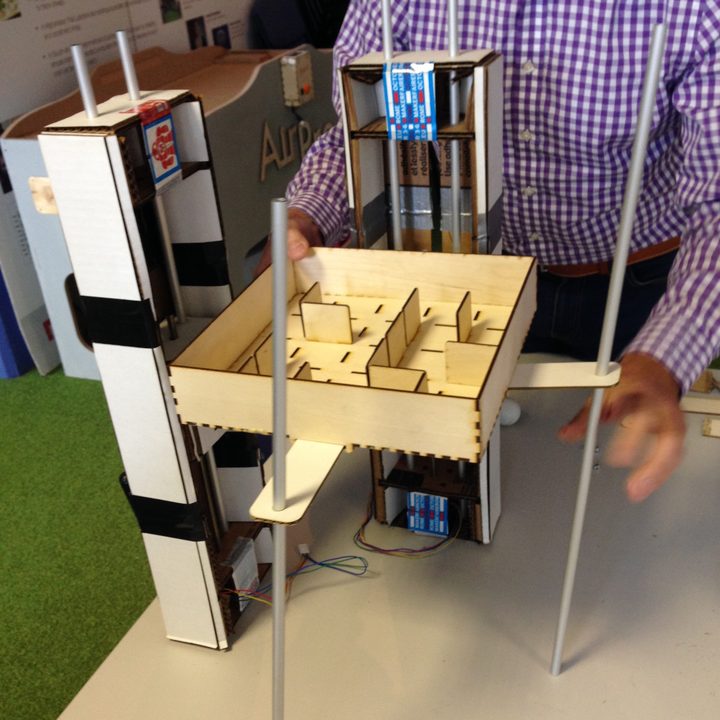
Creating the maze
A made the maze by combining makercase.com with solidworks. Makercase is a clever weppage where you can define the dimension of the box you want to make, and which kind of slots or taps. The webpage generates a svg file with the box layout. I convert the svg-file to a dxf in illustrator, an after that imports it into solidworks as a sketch. I make a simple extrusion, and now I can work with the solidbodys. As you can see in the final design i have deleted some of the taps, so the edge of the maze is smooth. In the bottom I have maked some slots for the walls there will form the maze. To the right of the box layout, I have added the last two parts there are needed, the wall and the fixture.
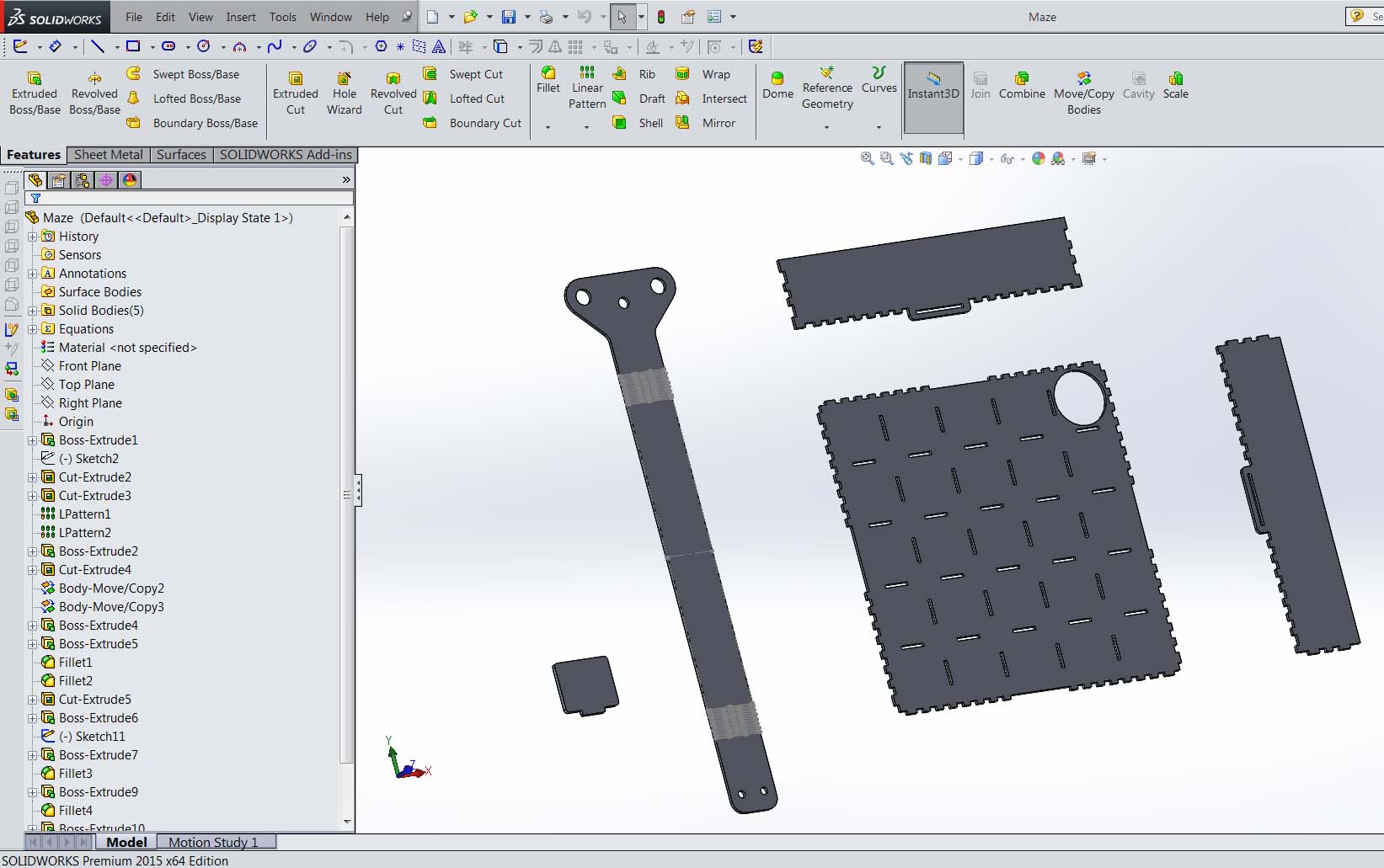
All the design files can be downloaded here.
Body>