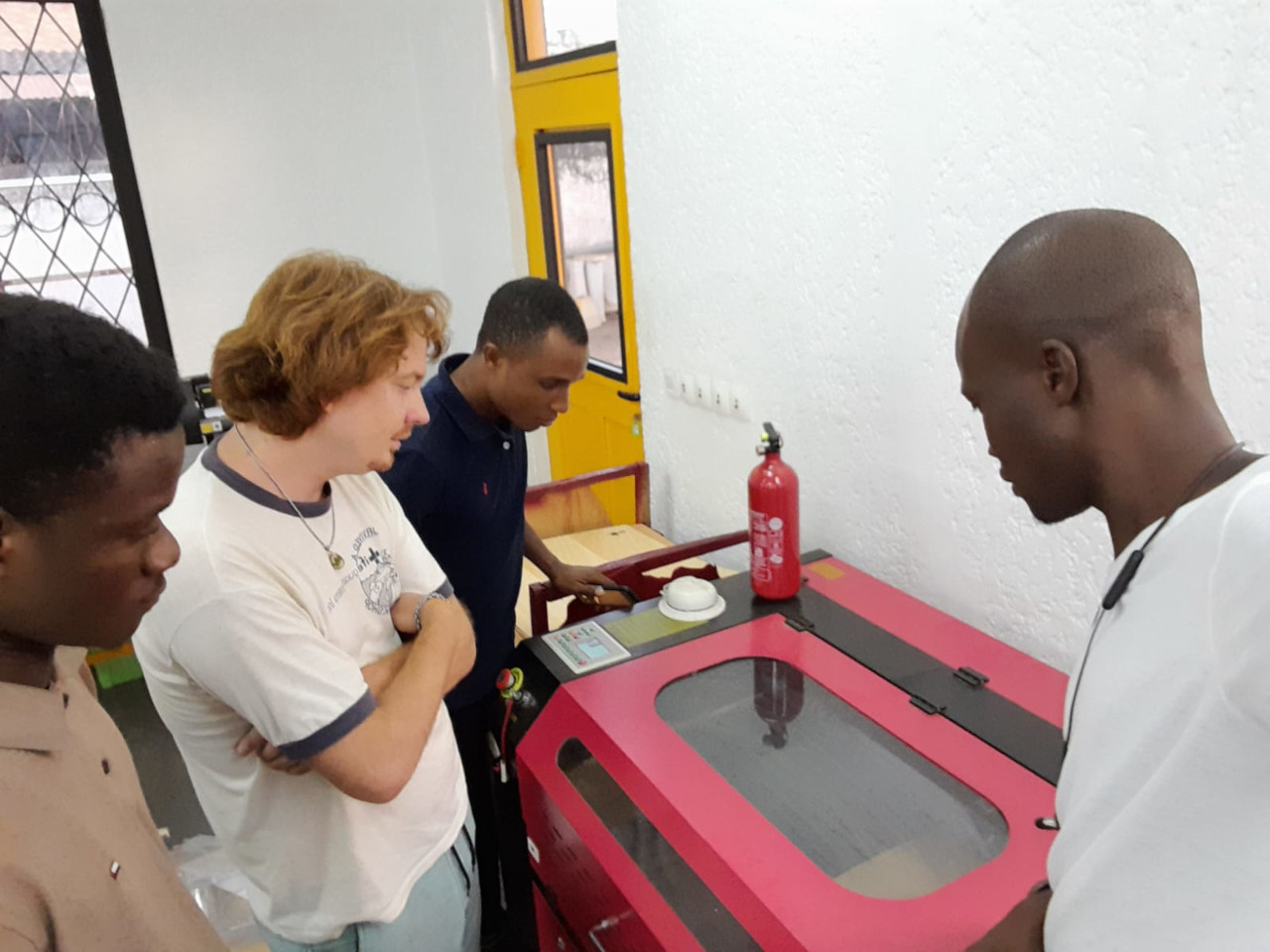
group assignment: characterize your lasercutter’s focus, power, speed, rate, kerf, joint clearance and types
Focus
We started by calibrating the focus of the machine. We leveled the bed from bottom to top until we reached our bare level. We did some laser drilling tests to observe the different cases of focus until we had the perfect height

Speed, Power, Rate and Kerf
Power, speed, and frequency are essential parameters in laser cutting. Power refers to the energy delivered by the laser beam, affecting cutting capability and speed. Higher power enables faster cutting through thicker materials, but finding the optimal level is crucial to avoid damage. Speed determines the rate at which the laser cutter moves along the cutting path, impacting production time and precision. Faster speeds reduce time but may sacrifice accuracy. Frequency, for pulsed lasers, represents the number of pulses emitted per unit of time. Higher frequencies allow for faster cutting, but excessive frequencies can reduce efficiency. Balancing power, speed, and frequency is key to achieving desired results, considering material properties and desired outcomes. Modern laser cutting systems offer adjustable settings for fine-tuning the process. Understanding and managing these parameters optimally is crucial for efficient laser cutting in digital fabrication. the picture below represents our test results of speed and power in a grid(graph) form. with an interval of 0.100mm, a single pass and a frequency of 1.khz. the speed was gradually increased from 2mm/s to 15mm/s and the power also increased from 10% to 50%

Kerf
Laser kerf is a term used to describe the width of the cut produced by a laser beam during the laser cutting process. It refers to the material that is removed as a result of the laser’s heat and energy. The laser beam heats the material to its melting or vaporization point, causing it to be expelled and creating a narrow cut along the desired path.
The width of the laser kerf depends on various factors, including the type of material being cut, the power of the laser, the speed at which the laser cutter moves, and the focal point of the laser beam. Generally, the laser kerf is narrower when using higher-powered lasers and slower cutting speeds. However, it’s important to strike a balance between achieving a narrow kerf and maintaining efficient cutting speeds. Because the kerf is a dimension smaller than a millimeter, measuring it can be tricky. A good strategy is to cut six 10 mm strips in the CAD software (which means 7 cuts), cut them, place them next to each other and measure the total length. The kerf is then calculated as (planned length - measured length) / number of cuts

Joint Clearance and Types
we cut out test pieces using cardboard to test the joint clearance.


