3D Computer Controlled Machining
Intro to CNC
CNC standing for computer numerical control is a system that will take take in programmed instructions to automatically
run a job whether it be milling, lathe, drill... and so forth. Technically 3d printers, laser engravers, vinyl cutter, and
any other tool you program using a computer is a CNC machine. In order to use a CNC machine one need to take their CAD file
and import it into a CAM software which will then turn the design into machine code the machine can understand. Then you simply
using the machines controller or control panel in order to zero it and run the machine code.
The machine we are using in this project is a mill and more specifically a 3-axis mill. A mill is composed of a few different
important parts that are crucial to understand in order to use it effectively. Going through the basic parts there is the gantry
which is a general term used for the portion of the mill that moves along the axis, there is then the spindle which is a motor
that spins at around 18000 RPM. Connected to the spindle is the collet and collet nut which will hold the bit in place. The bit
simply being the actual tool used to make the cut. There is a vast array of available bits (that I will talk to you about buying)
more of, from endmills to drills, to surfacing tools, tapered bits and more. Next to the collet and bit and surrounding it is the
dust collector connected to a vaccum to keep wood and other material dust from flying everywhere. Finally the last thing to discuss
is the axis. The axis are the direction the spindle can move in (NOT THE GANTRY). Our CNC mill is 3 axis, and so can move in the
x,y, and z directions allowing it to do 2 axis, 2.5 axis, and 3 axis milling operations. In the other room we have a 5-axis mill
meaning that the spindle can now be angled in diagonal directions allowing for more complex cuts.
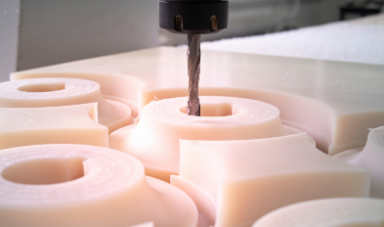
3 Axis Mill
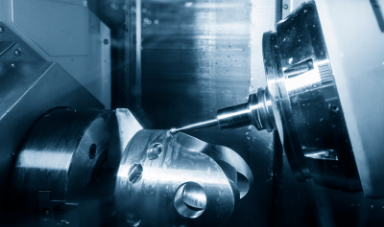
5 Axis Mill
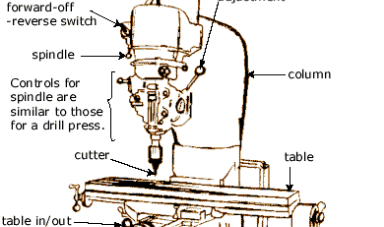
Anatomy of a Mill
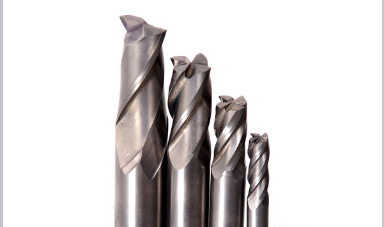
Endmill Bits
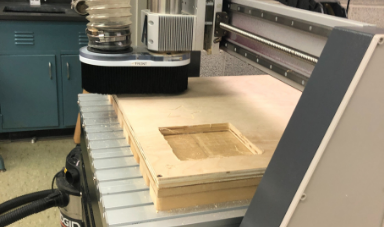
Dust Collector
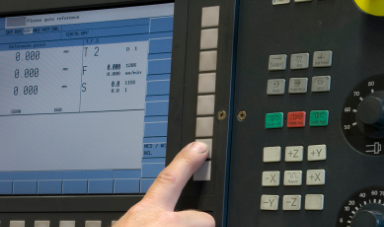
CNC Mill Controller
Group Assignment
For this group assignment we tested our CNC machine the axiom precesion CNC mill. We tested out
a few things and went through important terminology related to the mill. We discussed allignment
of the CNC which is the alignment of the gantry, the bed, and the spindle all together, and how long
they typically stay in alignment.Run out which is when the spindle and tool come
out of alignment more often encountered when working with denser material such as aluminium.
Speed is the roation of the toolpath in rpm, and feed is how path the tool is moving relative to
the stock typically is mm/minute (in Fusion 360).
To test out all of this stuff we made a quick design in V-Carve using a 1/4 inch
downcut endmill, using the reccomended speed and feed settings, and measured the
cut out stock to determine the precesion and kerf of the mill. We designed an Iphone
stand in V-Carve, and made sure to add fillets to the edges due to the mill not being very
good at making sharp angles. We then processed the design, and laoded the g-code to load into the machine.
We loaded the 1/4 inch endmill into the collet, turned on the vacuum and ran the cut.
The final cut was then measured and found to be withing a few fraction of an inch of their intended cut size.
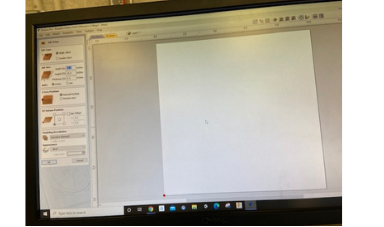
Setting Stock Dimensions
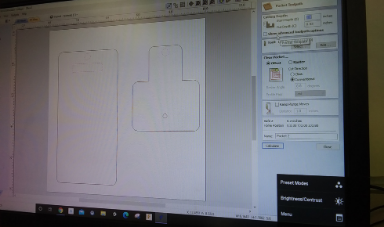
Adjusting Cut Settings
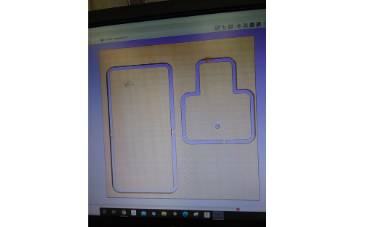
Simulating Cut
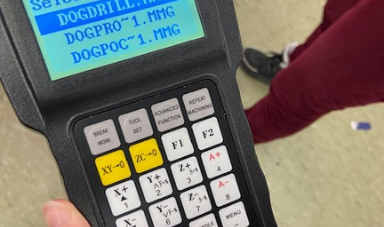
Axiom Controller
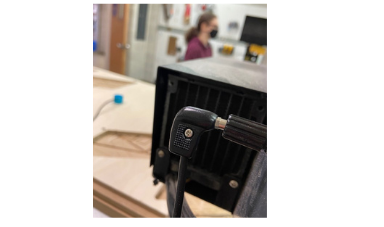
Plugging in Z-Probe
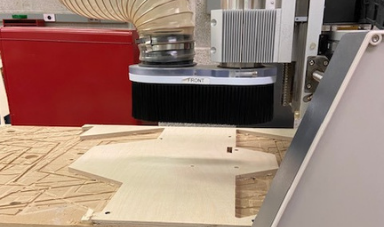
Milling
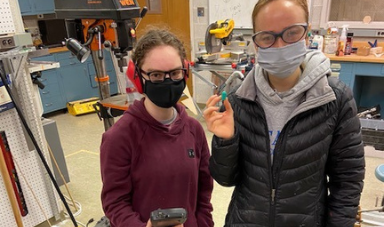
Group
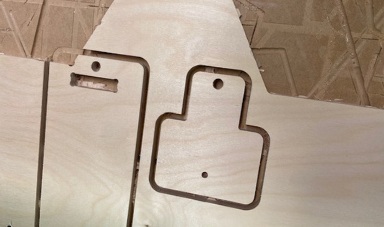
Cutout
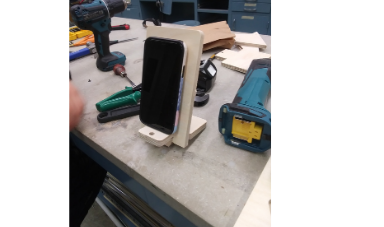
Final Assembly
Balista Prototype
For this project my friend, David Frey, and I decided to attempt to make a ballista, we ran into a lot of problems along the way but tried our best to find solutions for all of them.
Starting off this project we thought it be best to model and print the locking mechanism in Fusion 360. We sketched some ideas and discussed a few different locking mechanisms, but
agreed in the end on a locking mechanism with a gear with angled teeth. A locking mechanism of sorts will then get stuck in the teeth if attempted to rotate the gear in the opposite direction.
This model was 3D printed and tested, but was found to not work due to the gear not actually falling back into place as it was supposed to, and needing to go against gravity to get back where it
was supposed to be due to issues regarding center of mass of the locking mechanism. We redesigned it so the locking mechanism would fall towards the locking mechanism instead of away.
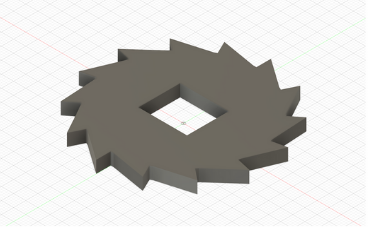
Locking Gear
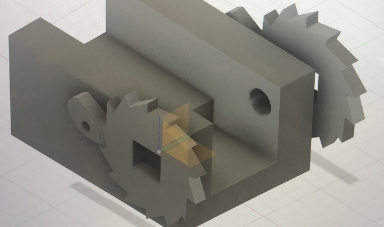
Prototype Assembly
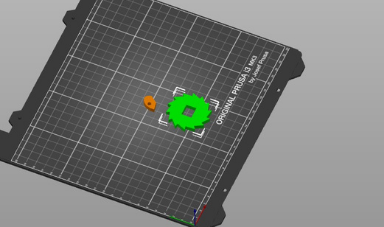
Importing into Slicer
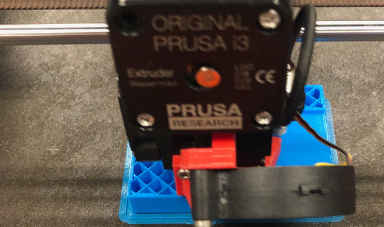
Printing
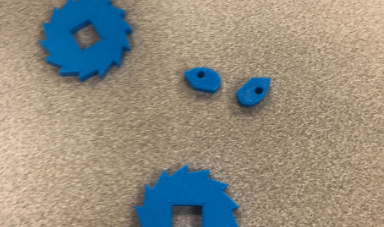
Printed Gears
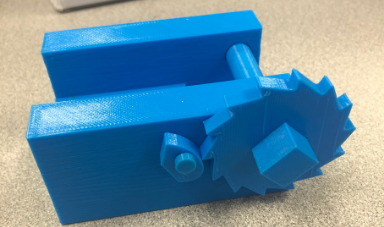
Prototype Print
CAM
The part of the project to do was design the individual components to be milled. We made an initial design, but ofcourse this could not simply be milled
out since we did not have access to a giant stock of wood and multiaxis milling, so we had to approach the problem in components. We used the designs for the
gear and locking mechanisms and set their heights and widths to fit comfortably in the stock we have. We then made a componenent for the rails which was broken up
into 4 diffent bodies, 2 walls, one track, and one support. Finally we made the tensioning holder which needed to be fairly thick so we broke its width into three different
bodies.
We then layed out the bodies flat into two different files. The first file contained the locking gears, mechanism, and rails, while the second file contained the tensioning component.
To mill the first file all was needed was a gew pocket cuts for the holes, an a contour cut with tabs to cut out the parts. For the tensionining componenet we had to use
a 3D adaptive milling for the curved protion, and then a contour cut to cut out the objects. We ran into some problems with Z axis limit which we quickly found out was us messing
up and not placing the origin in the correct location.
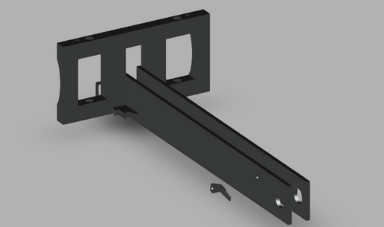
Fusion Assembly
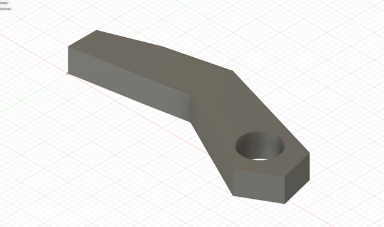
Altered Locking Mechanishm
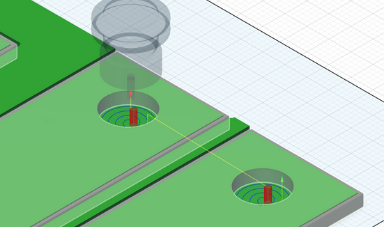
2D Pocket Cut
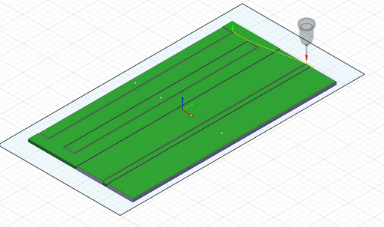
2D Contour Cut with Tabs
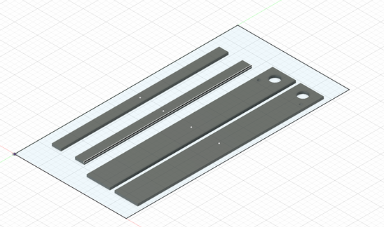
Rails, gears, and locking mechanisms
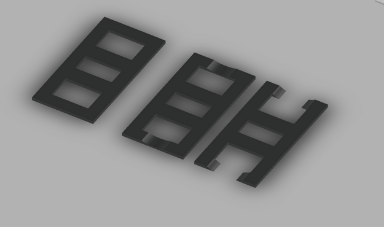
Tensioning holder
Milling
For the milling section we ran into some problems. The feed rate on the machine was far to slow compared to what was put in for it to go. The first cut nearly took an
hour, and we were not willing to wait that long again. Instead I went through the controller and found a reset to back up, but which messed up more things on the machine.
I then had to go through each individual setting, look them up, and set them properly, it seems like the backup stored on our controller originally was not designed for our
machine. I went through had to reset all the advanced settings including how and what it read from the nc file, disable tool change options, set up the correct value for the
pulses for the stepper motors, and get a pair of calipers measure the z probe, and a meter stick to measure the table size and set all those settings back. Finally everytyhing
was up and running again, but we lost our zero point in the mess. So we decided to go back to fusion set the origin at the edge of one of the holes we milled and used that as
a reference which worked like a charm. We cam back the next day and milled the second board as well.
The process to actually mill the board is incedibly simple all we had to do was put some tape on the back of our stock and screw it into the spoil board. We then set the XY zero
location to the desired location, and used the Z-probe which works by simply closing a circuit to zero the z axis. All thats left from there is to make sure the correct bit is loaded
into the collet, turn on the vacuum, and run the file. We did lead it was possible to decrease the feed by fixed percentage interval using the contorller, but we did not need to, we
did however slighly adjust the speed using the knob found on the machine base.
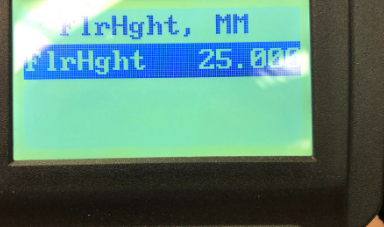
Z Probe Height Settings
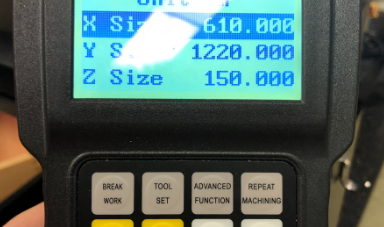
Table Size Settings
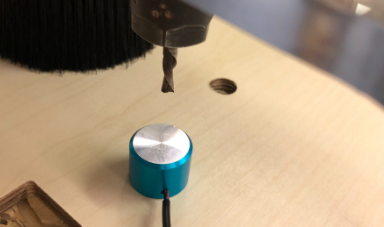
Zeroing the Machine with Z Probe
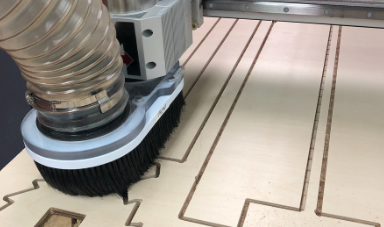
Milling the Board
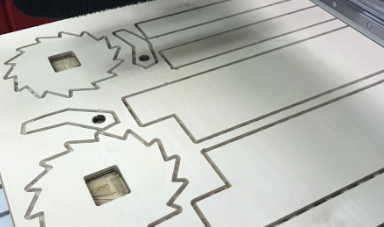
First Milled Board
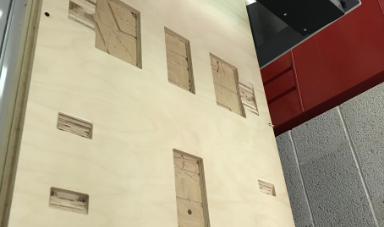
Second Milled Board
Assembling the Project
All that was left to do was assemble the project. The first thing to do was cut each comonenet still connected to the stock by tabs. Then we went through and sanded everything so it is all smooth.
We started of by attaching the rails together using screws, and pre drilling to avoid splintering. After doing this and assembing the rails we realized that we needed to add tube for the locking
mechanism from the inside which meant we had to disassemble it, attach the wooden dowel for the locking mechaninsm, and rescontruct the rail. Following that we were hoping to have a large square metal
stock we could use a lathe to turn cylidrical to connect the locking gears, we could not find one and were running out of time, so had to improvise with some pvp and pieces of wood. We went on
to atack the axle and gears and locking mechanism all to the rails completing the first part of the ballista.
First we stacked the 3 bodies of the tensioning componenet on top of one another and screwed them all together to make them into onr part. Next we went and drilled holes into the tensioning componeneonent to allow the rope to go into. We then realized that we made the whole thing was to small, and there was not adequate room to manipulate the rope propoely,
and attack the needed dowels that will be pulled back. We soon gave up on this and decided to return to it some time in the future. We then went to attach the componenent just assembled to the rails,
but had difficulty screwing the wood in parallel to the layers of plywood, and so decided instead to try attaching them with support components. Though in the end the ballista did not work as intended,
it was still a fun project with plenty of learning oppertunities.
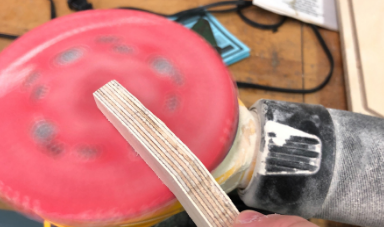
Sanding all Components
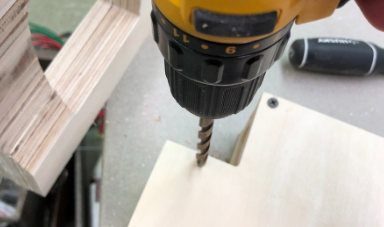
Axis to locking mechanism
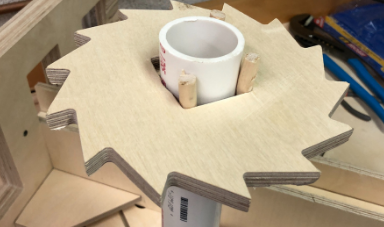
Jamming the gear in the axis
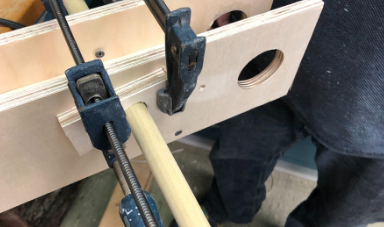
Screwing the Rails together
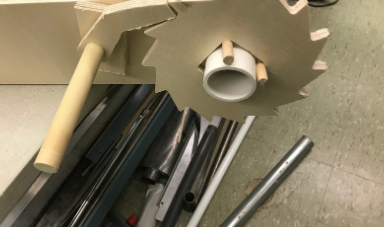
Gear and locking Mechanism
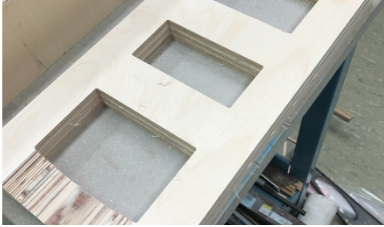
Assembling Tension Rack
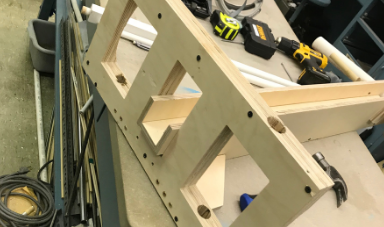
Adding holes in Tension Assembly
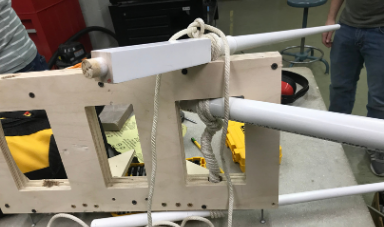
Attempting to Add Rope to Ballista
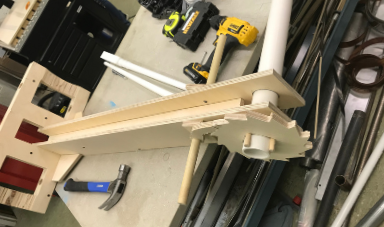
Assembled Ballista
Click Here to Download all the files from these projects!