Mechanical design. Machine design
For this week we're going to do a very funny and collaborative assignment. We're making a machine!
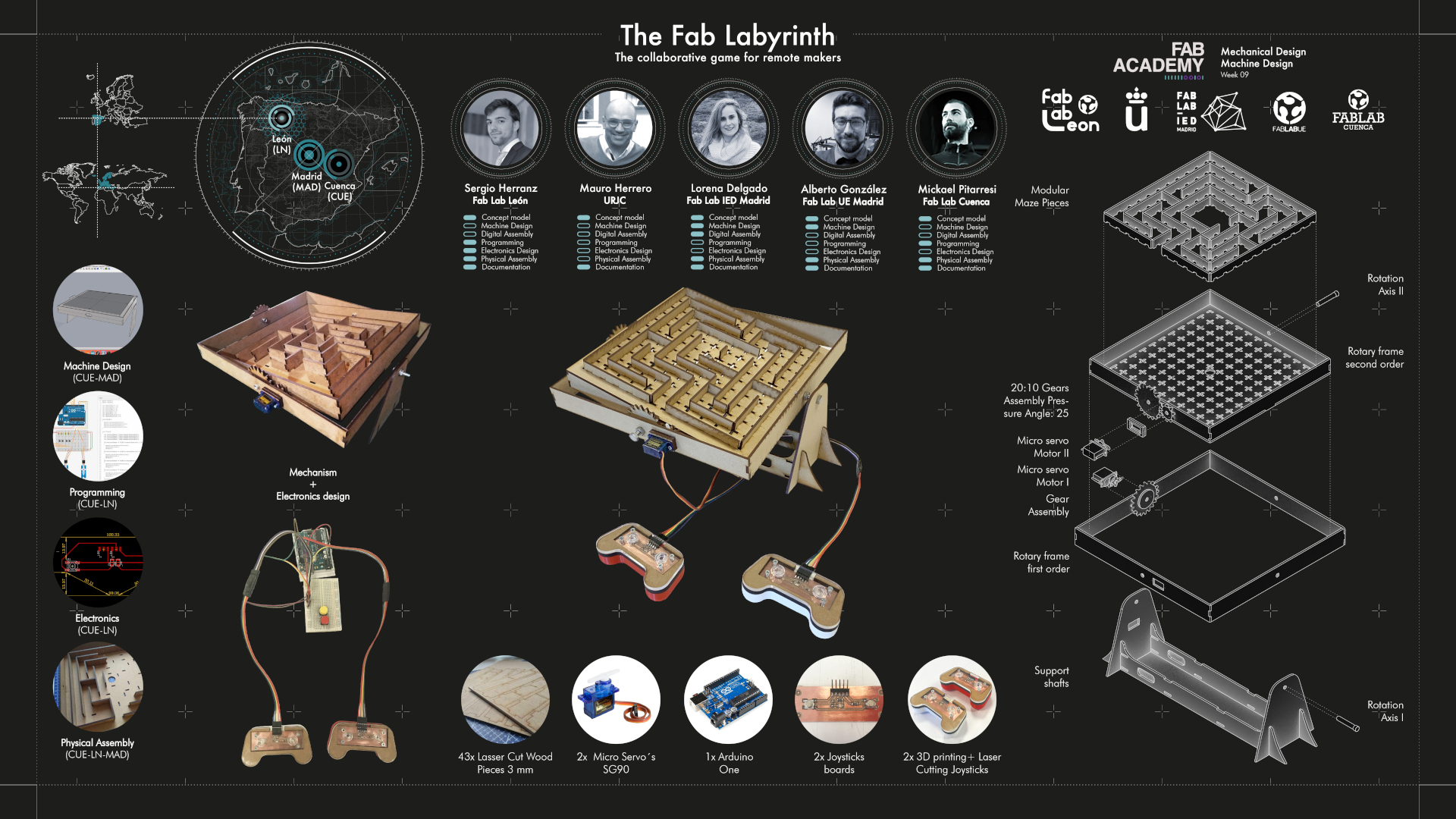
Group Assignment: building the machine
Chapter one: TASKS BRIEF
After many meetings, many ideas and many yelling, we decided to create a machine that could be interactive, like a game, that could be collaborative, easy to replicate and easy to set up. We came up with the FabLabyrinth. It is a machine to solve mazes.
It would have a surface on top where we could change the labyrinth, making it modular or interchangeable. It would have servos or step motors that would move that platform in two axis: roll and pitch. And it would have two controllers and some buttons that would do the different actions.
We wanted the machine to have different modes to play. The “self solving” mode would be the full automation of the machine, following a code and moving on its own to solve the maze. The “collaborative” mode would let you control the machine with the two controllers. Each player would control each of the servos or motors, so with the movements of both of them combined the machine would move in the correct direction for the ball to move through the maze.
We wanted the machine to be so easy to replicate that we could have one on each of our FabLabs. Our situation is not so common so I’ll take a minute to explain it. We are 5 students in León’s node this year. Sergio does the FabAcademy locally in León, but he’s the only one of us physically there. Mickael co-runs FabLab Cuenca, so he is in Cuenca. Lorena, Mauro and Alberto are in Madrid. Lorena works in FabLab IED. Alberto is the coordinator of FabLab UE (Universidad Europea of Madrid). Mauro usually works in URJC. However, the virus hit the team hard. Mauro tested positive a couple of weeks ago and has been in the hospital with a respirator for more than a week. Even if he’s evolving nicely and he’s at home now, his participation in the assignment could not be as active.
Sergio and Mickael would work on the code. Sergio would be the programmer and Mickael, as he had access to his FabLab during Easter week, could build the first machine and de-bug the design and the code. Alberto would engineer the machine, the mechanisms, the position of the servos and the interaction of the parts. Lorena would work on the visual part, creating the slides and the documentation. She was also responsible for the design of the maze itself.
Chapter two: MACHINE DESIGN AND MAZE DESIGN (Alberto and Lorena)
Even if Alberto and Mickael wanted to control the machine with four motors and four cables (it would be for four players, but the machine would have more degrees of freedom than axis and could potentially unbalance itself), so we went to check other machines and found this double-framed machines with servos or steppers.
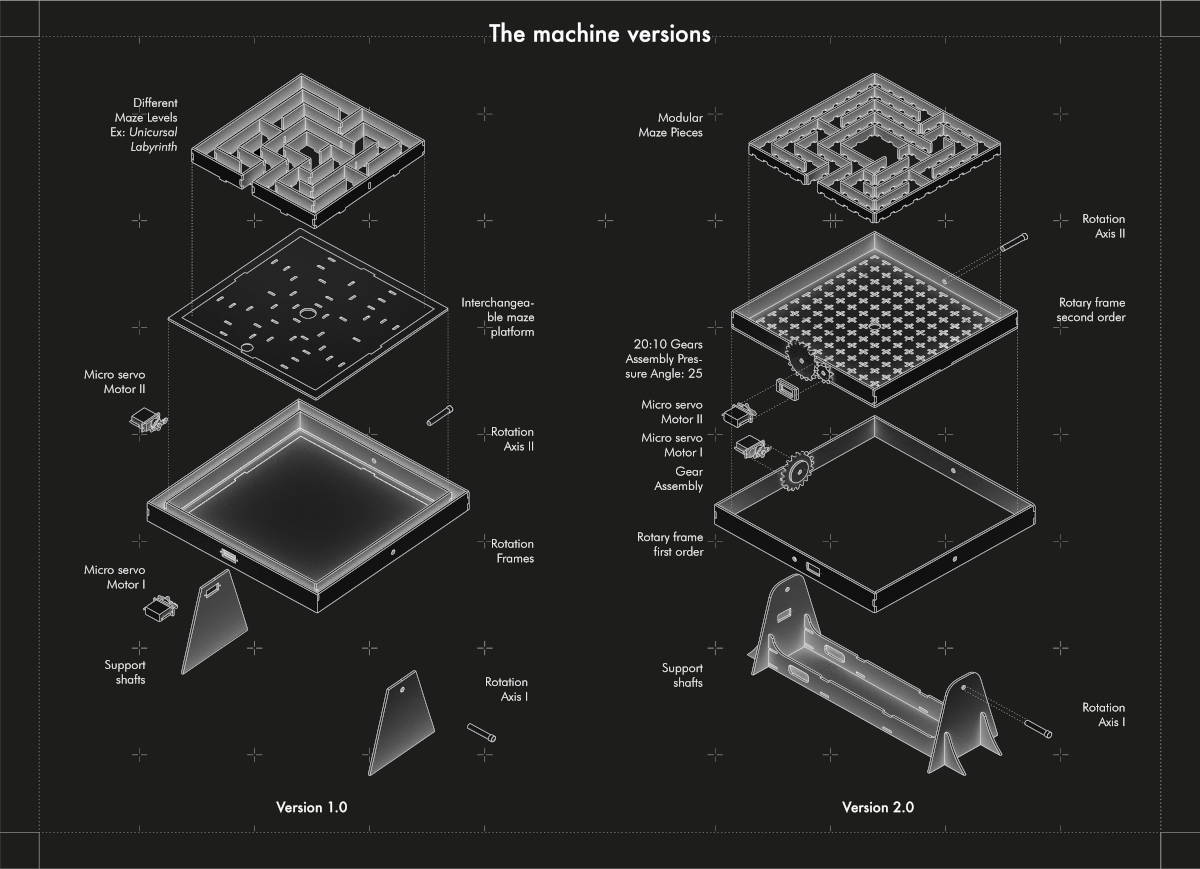
We took the idea and developed it a bit more. Alberto’s task was to design the physical parts of the machine. With feedback from Mickael, two versions of the machine were created. The V1 has the servos directly attached to the frames. The supports on the left and on the right hold the machine in place. One of the supports has the first servo in it, the other one has a shaft. In between this supports we place the first frame. In one of the sides of that first frame we have the second servo, and on the opposite side, a shaft. This first frame holds the second frame. Inside the second frame we can place the labrynths. All the electronics are in breadboards, as there are no controllers. There are four buttons, two for each of the servos.
The machine then evolved as Mickael built his unit and the group continued adding ideas. V2 has a 2:1 gear multiplication so the speed of the maze would decrease and we would have more control. Instead of an interchangeable maze design we went for a full modular one. The frame was also modified and made more sturdy, supports to place the Arduino in were added, and, with a lot of feedback from the group, we designed the controllers. Sergio designed specific boards to be milled, so the electronics would be soldered and permanent. A “self solving” and a “manual control” button were added.
Alberto wanted to create a 3D printed version of the controllers, with the board on a sandwich panel between an acrylic top with living hinges. Mickael wanted to create a wooden one on MDF. So the machine that lives in Madrid has 3D printed controllers and the one in Cuenca has more simple MDF ones (that work).
Assembling and debugging three identical (or very similar) machines got us so much work! Each machine was doing different weird things. We helped each other and in the end, the machines were able to move under their own power.
Chapter three: My contribution explained
For this assignment my main contribution was CAD design. As Sergio and Mickael were refining the code and Lorena was helping me with the digital assembly, I designed in CAD every single part of the machine, from the modular maze to the support, and even the contoller that was 3D printed was designed by me.
The first problem we encountered was the position of the servos. Mickael sent me the measurements of the units, and for the version two, he asked me if I could incorporate a reduction gear in order to reduce the speed of the movement.
The second problem was the modularity of the maze. We solved that in the second version as well
And finally, the last problem was the structural integrity. For the second version, both of the pillars were joined so the machine was much more stable, and furthermore, it also got the cables better organized.