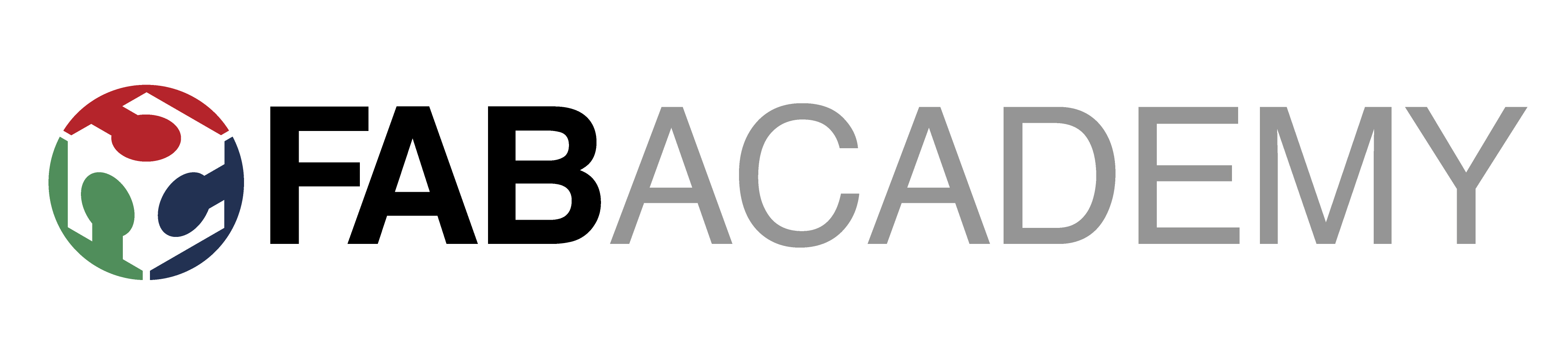
Week_16 - Wildcard
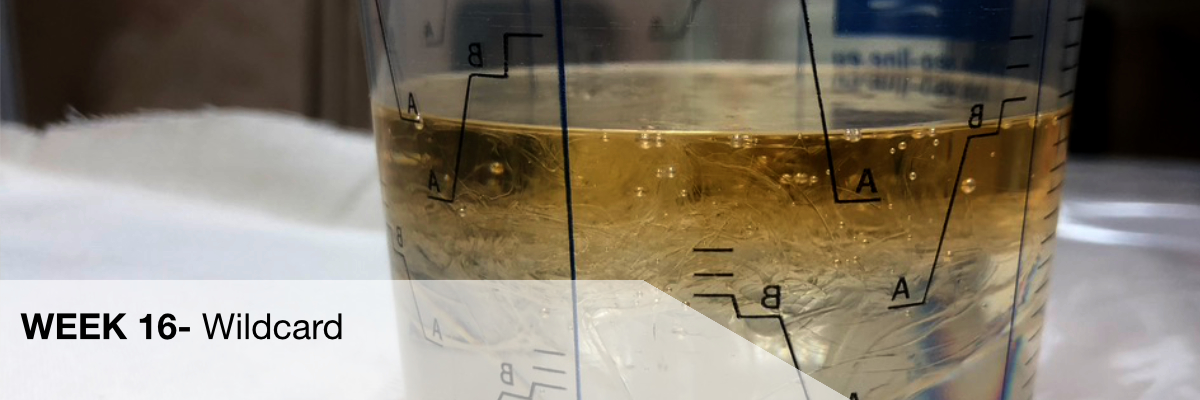
Group assignment:
Individual assignment:
The task for this week was to prepare an element using composites. I can divide the work on this task into several stages:Design:
My goal in this task was more fun with form and material than some very specific final project. Playing with the sculpting function in Fusion I created a simple soapbox model. Later I had a few ideas what I wanted to do next: -to make a form consisting of two elements where I put the material and resin between them.I chose the positive option. I prepared the model, remembering not to make any negative angles (in the case of sharp angles in the form you can not later remove the finished object without destroying the form).
CAM:
I add the model prepared in this way to CAM in fusion and using the knowledge gained in previous weeks I set the parameters and the program on the machine accordingly.The material I used as a form is styrofoam. Thanks to the fact that it is a very soft material it can be milled at very high speeds, which speeds up work on the prototype or the final product. I stuck the material to the table on the cnc milling machine with a double-sided tape, additionally there was also a suction table which could keep the mould in place by itself. However, due to the fact that in the CAM settings I chose very high speeds, I decided not to risk it.
CNC:
The material prepared in this way was ready for milling. (you can see process on video on the button) Before starting work, I checked the height of the tools using a height sensor mounted on the machine. This is an important process thanks to which we can easily use several milling cutters with a tool changer in one program.After milling, I cut off the mold and gently grind the surface.
Application of cotton raw material together with resin.:
I prepared the pieces of material/cotton raw material by cutting out ready-made formats that were to cover the mould. It is always better to cut a bit bigger pieces because it is always better to have a bit more material and cut it off than to put too little and lose a bigger piece already put on the mold. The resin I used is Epidian 652 and is mixed with IDA hardener in a ratio of 1:2 resin.Epidian 652:
Physical and chemical properties:GOOD PRACTICES WHEN WORKING WITH RESINS
HEALTH AND SAFETY
The product can be processed without risk, provided that appropriate precautions are taken as for chemicals. Keep uncured materials away from foodstuffs and children. Wear protective clothing, latex or vinyl gloves and goggles to protect against splashes. The processing room should be well ventilated. After each operation, hands should be thoroughly washed with soap in warm water and after washing dried with a disposable paper towel.
Application of resin:
I put the resins on the material with a brush. Spreading the chemicals in such a way that the material is covered with resin everywhere, but also not enough to spill around. After the resin was applied, I put the mould with the material into the bag and put it all into the vacuum bag, separating the mould from the top layer with a net to help air flow through the whole bag. Using a vacuum pump we suck the air out of the bag and wait until the resin starts to harden.
Then we take the mould out of the bag, cut off unnecessary elements and fragments. (Sometimes you also need to treat the foam with acetone to dissolve fragments that have stuck to the object).
Hero Shots:
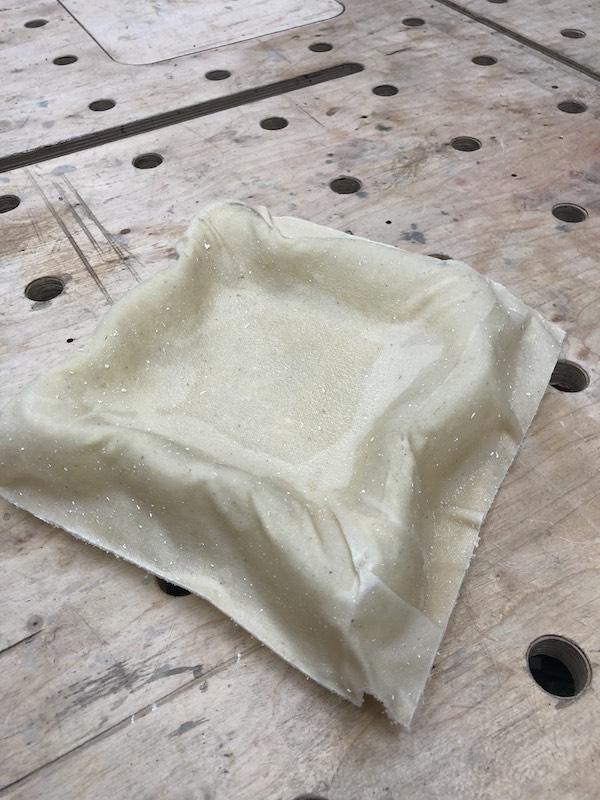
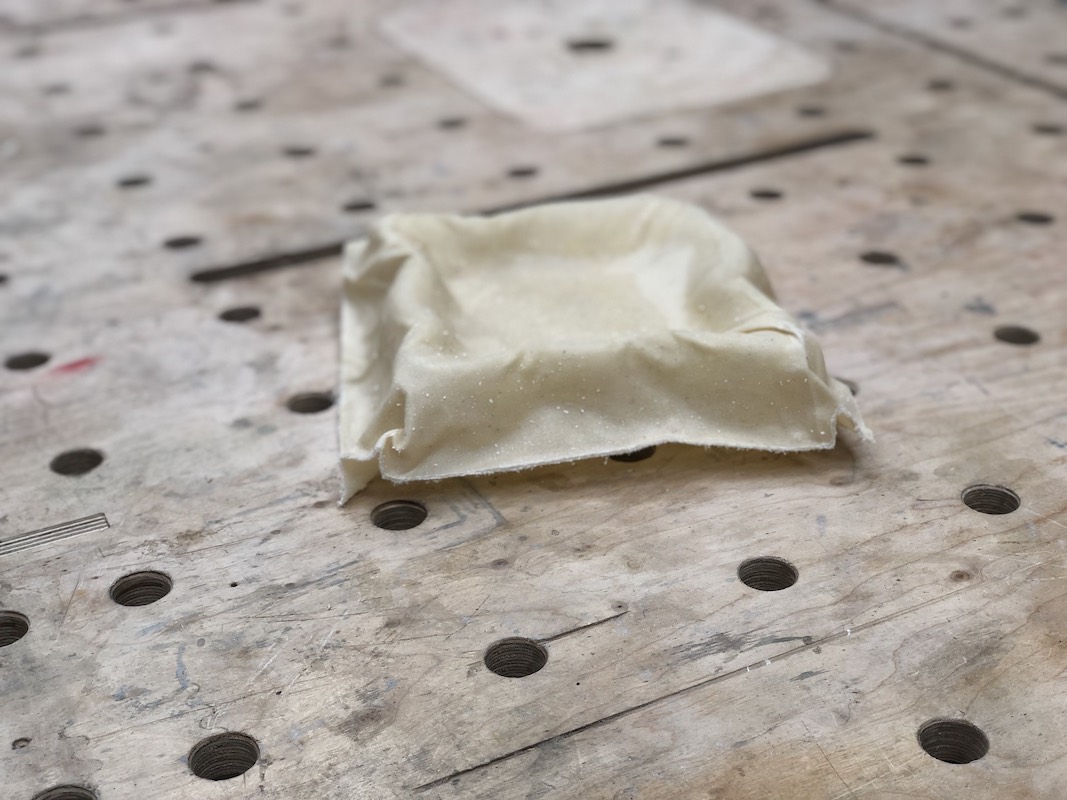