MOLDING AND CASTING
The goal of his week consists of pre-casting and from this create different molds with different materials.
1. Group Assignment
review the safety data sheets for each of your molding and casting materials, then make and compare test casts with each of them
1.1 Characterization of molding and casting materials
Carlos Nina. - Ivan Callupe.
Diego Santa Cruz.
Team Group
1.1.1 Machinable wax
Machinable wax is an extremely hard wax that has been formulated to deliver exceptional machining properties including high resolution detail. Since it is harder and has a higher melting temperature than most other waxes, machinable wax can be machined, cut, or shaped using standard metalworking or woodworking equipment. High quality surface detail and dimensional accuracy are possible. Machinable wax is ideal for verifying CNC machining programs. Machinable wax is often used for precision lost wax casting. Machinable Wax is available in both blocks and cylinders. We stock the most commonly requested sizes and can usually provide alternate sizes on request.(
Applications of machinable wax:
_
1.1.2 Machinable wax
RTV Silicone (Room-Temperature-Vulcanizing silicone) is a type of silicone rubber made from a two-component system (base plus curative; A+B) available in a hardness range of very soft to medium--usually from 15 to 40 Shore A. RTV silicones can be cured with a catalyst consisting of either platinum or a tin compound such as dibutyltin dilaurate.[1] Applications include low-temperature over-molding, making molds for reproducing, and lens applications for some optically clear grades.(
Features:
_
2. Individual Assignment
Design a mold around the stock and tooling that you'll be using, mill it (rough cut + (at least) three-axis finish cut), and use it to cast parts
2.1 CHOICE OF 3D MODEL
In this part of the assignment I had to design a 3D model. I chose the face of "Darth Daver" (I like "Star Wars"). Search the web, I found this design (
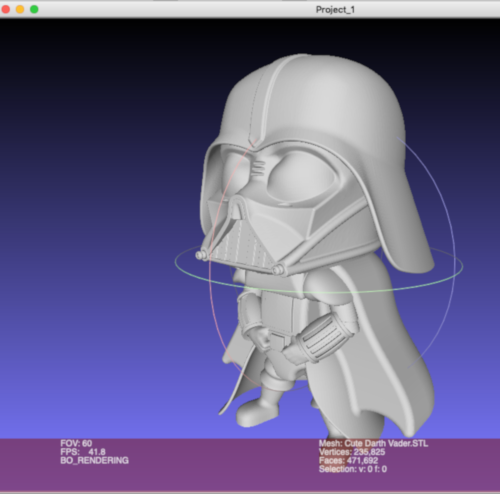
_
2.2 DESIGNING 3D MODE
I started editing the model in the "MeshMixer"; This is an open source software:
- First import the STL model.
- Then relice the cut in two planes of the model, until you get only the profile of the face of "Darth Daver".
- Then export the file in STL.
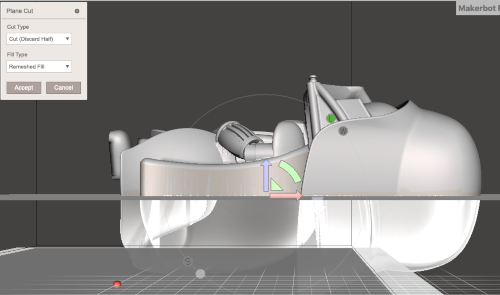
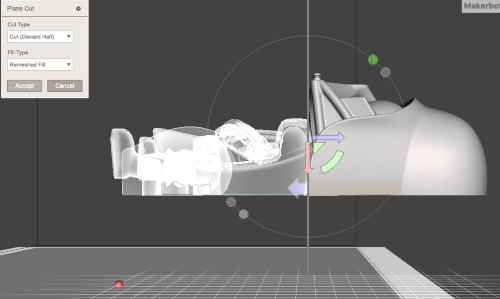
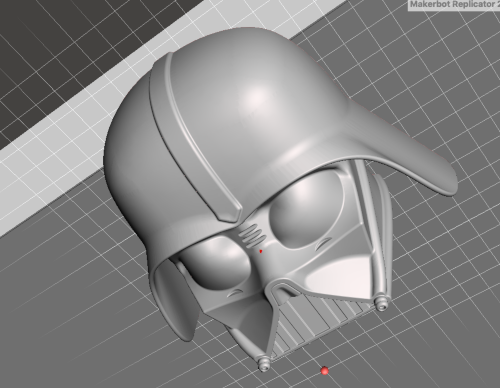
For the design, I used the FUSION 360 software, where I made changes to the model, until I got what I wanted.
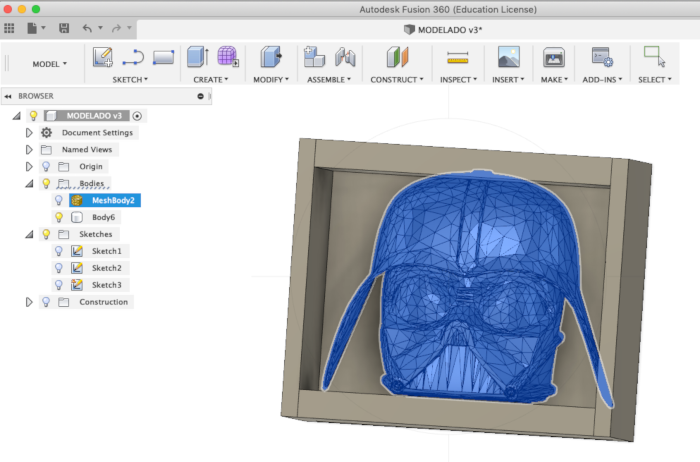
2.3 MOLDING
The material that I used for the pre-cast was "Paraffin 74". I made paraffin blocks from recycled material (previous projects). I placed the paraffin in a container under the direct heat of an electric stove. I waited for the heat to melt the paraffin to later place the wooden boxes. The volume of paraffin block 40mmx80mmx100mm. (
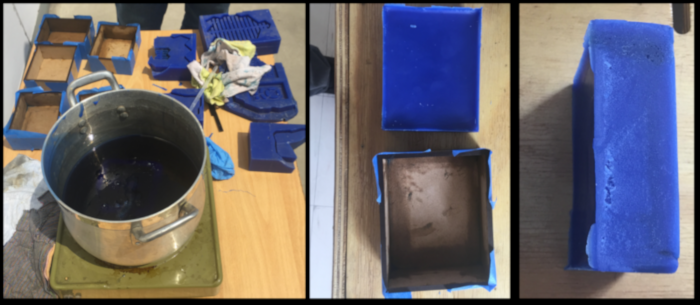
_
2.3.1 Machining the mold’s mold.
For the generation of the code for modeling the mold I did it in the software "SRP Player". It is an intuitive and easy to use software: (SRL PLAYER).
- First we have to choose the dimensions of our paraffin pre-mold (40x80x100mm).
- Then we choose the form of modeling (curved or straight).
- Then we choose the dimensions that our model will have machining.
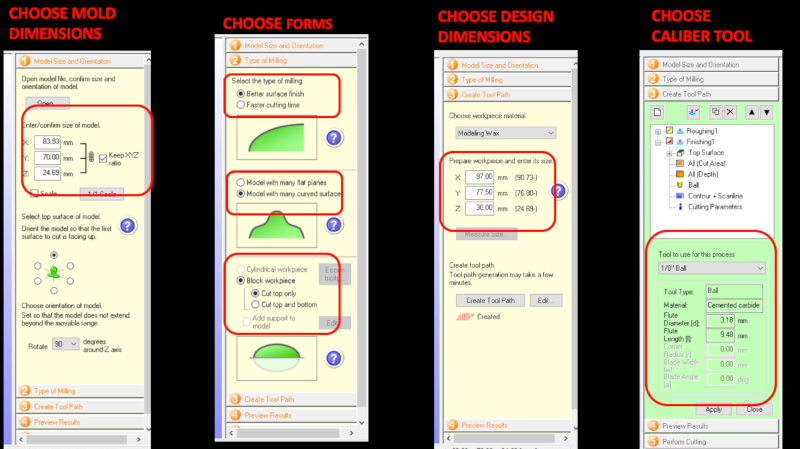
We create the step of the tool in modeling; the software allows you to simulate the modeling.
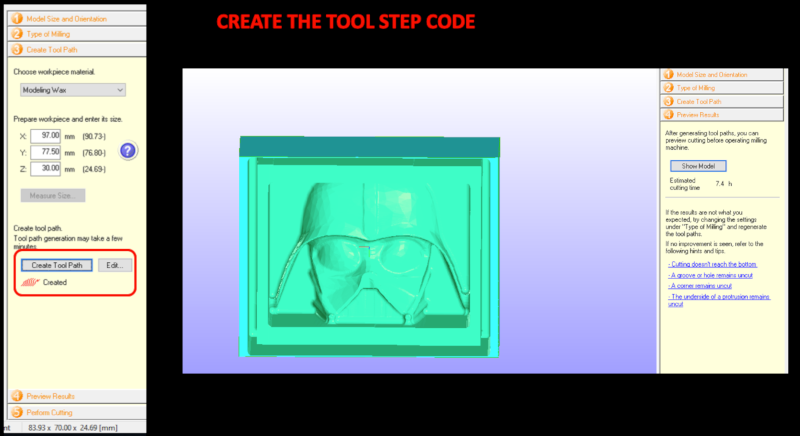
Finally we created the mold modeling code.

For the manufacture of my molding, I made it in a "Roland Modela MDX-20"
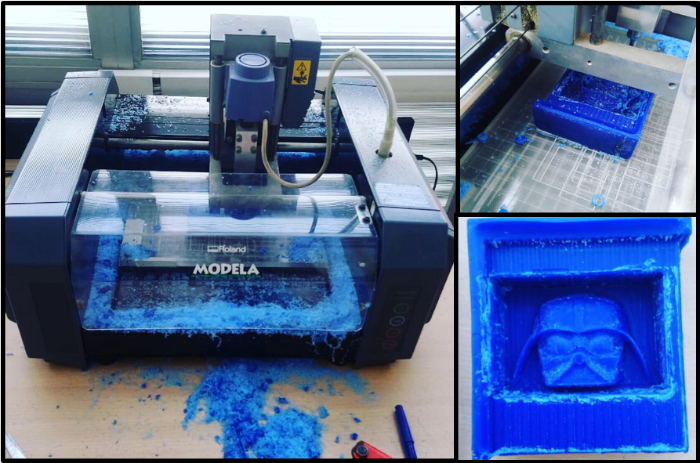
_
2.3.2 Casting the silicone mold.
To cast casting I used rubber silicone RTV and a catalyst. Mix both components in a ratio of 2 drops of catalyst per 1g of silicone. And I placed the mixture in the paraffin model and let it dry.
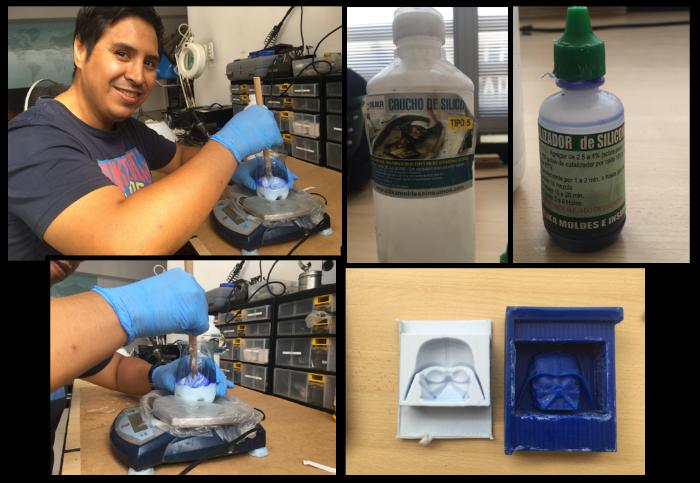
_
2.3.3 Results.
The first material I used was the polyurethane resin (Silikast70) in the presentation of two compounds (A and B) and mescal of 1/1 proportion. The advantage of this product is its rapid drying (10 minutes). The disadvantage is the rapid formation of bubbles.(this took approximately 2 to 3 hours) (
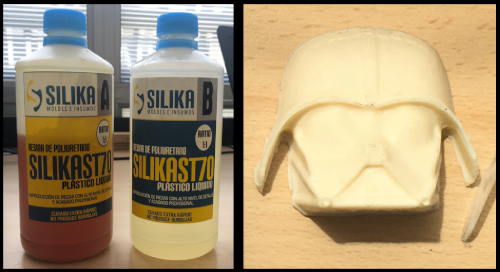
_
The second material that I used for my mold was the epoxy resin (POX BAK 1206). It is a mixture of two components. The advantage of this resin is the good finish. One disadvantage was the drying time around 24 hours (
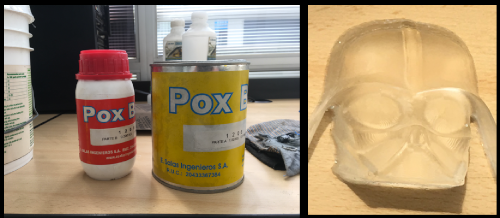
_
Another material that I tried was the paraffin of the candles. The advantage of this product is its easy drying and finishing. The disadvantage is that this material is fragile.
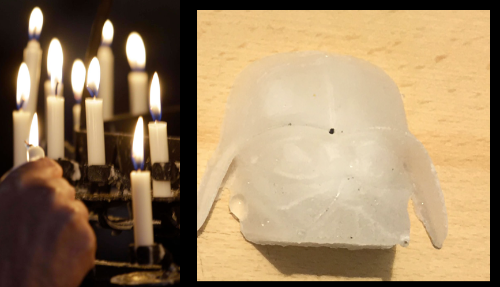
_
Another material that I used was silicone rubber (Sorta 37). The disadvantage I found in this product was the same as one of the recipients of the mix was open for several hours. The drying has been several hours and the result was not so good. Therefore, it is advisable to leave these products closed after using them.(
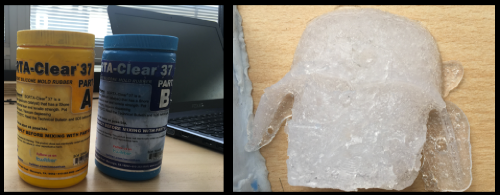
_
These were the results in the end.
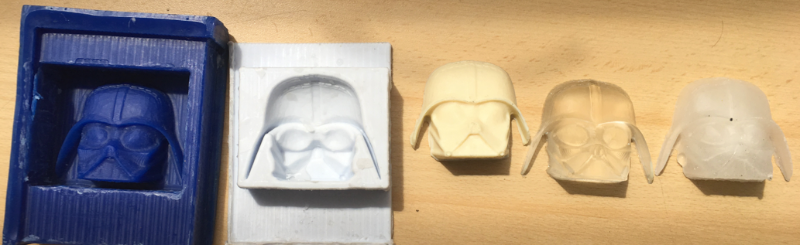
_
SELF EVALUATION
WHAT WORKED:
- I made the recycling and molding of paraffin.
- I used different materials and I could see the advantages and disadvantages of each one.
WHAT DID NOT WORK:
- I could not try cement or plaster.
THINGS TO IMPROVE:
- Be careful when handling materials. Some can be toxic or they can lose their properties.
Contact Me
Feel free to contact me via email or phone.