Week 6: 3D Printing
Assignment
BRAINSTORMING
Softwares
Skanect - To use with microsoft Kinnect to 3D scan
Meshmixer - Audesk software for quick and easy 3D edit
Cura - Free software to set up a file to use with your 3D printers.
**3D printing is different from the other digital fabrication machines that we use in that it builds on layers, not cut out in layers. Machines like laser cutters and cnc machines are done subtractively, cutting away from solid. 3D printing does it additively and can do convexity as well as concavity unlike the other machines.**
Characterizing your Machine
For group assignment we were to characterize our machine.
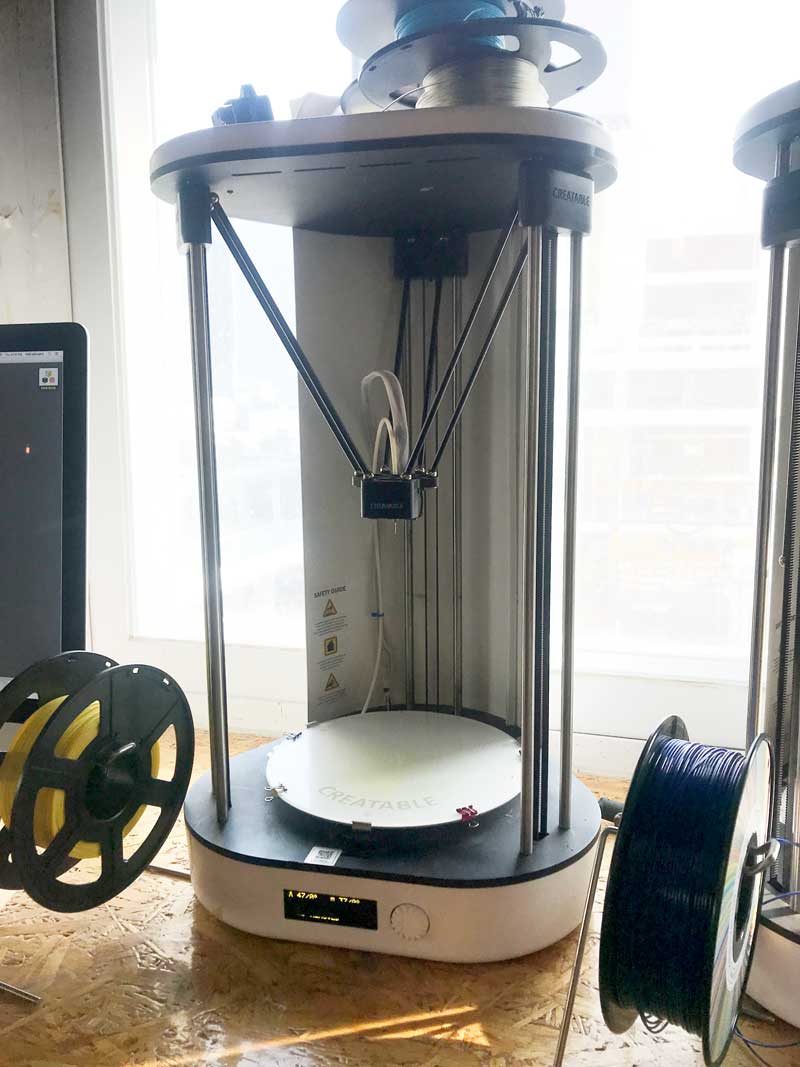
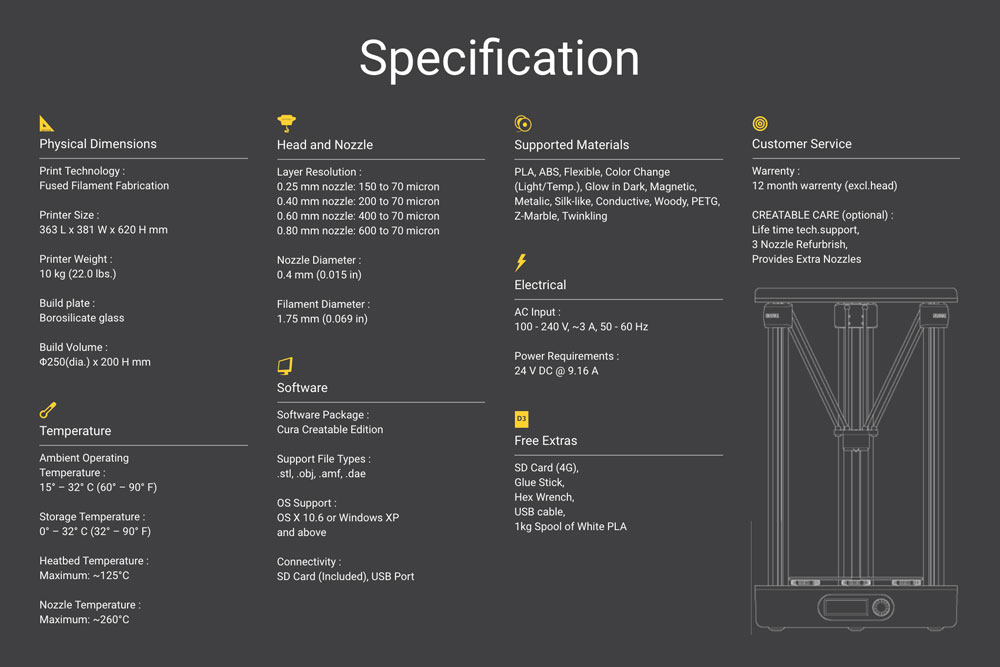
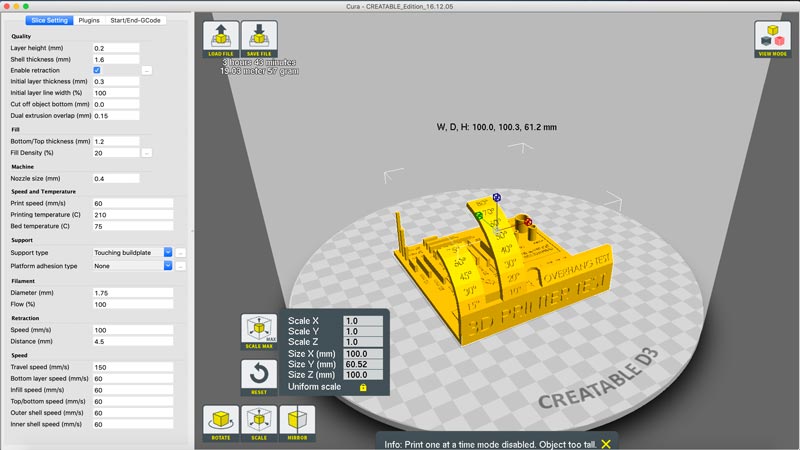
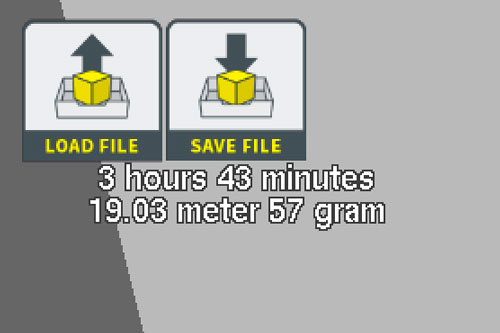
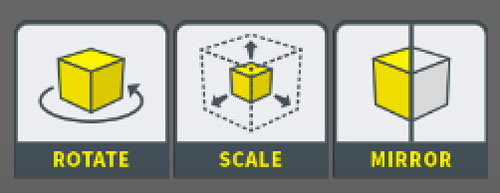
If you happen to want to make changes to the object, you can do
the rotation orientation as well as size and mirror.
The size changes in scale.
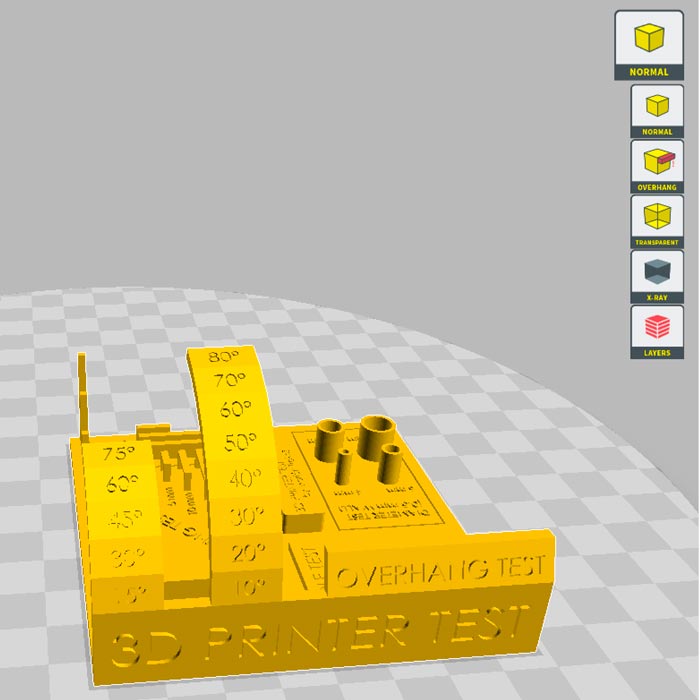
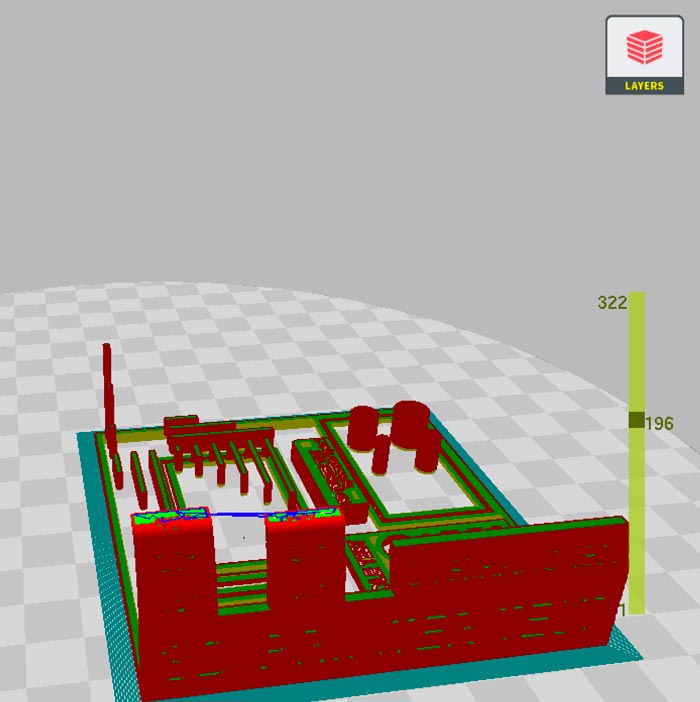
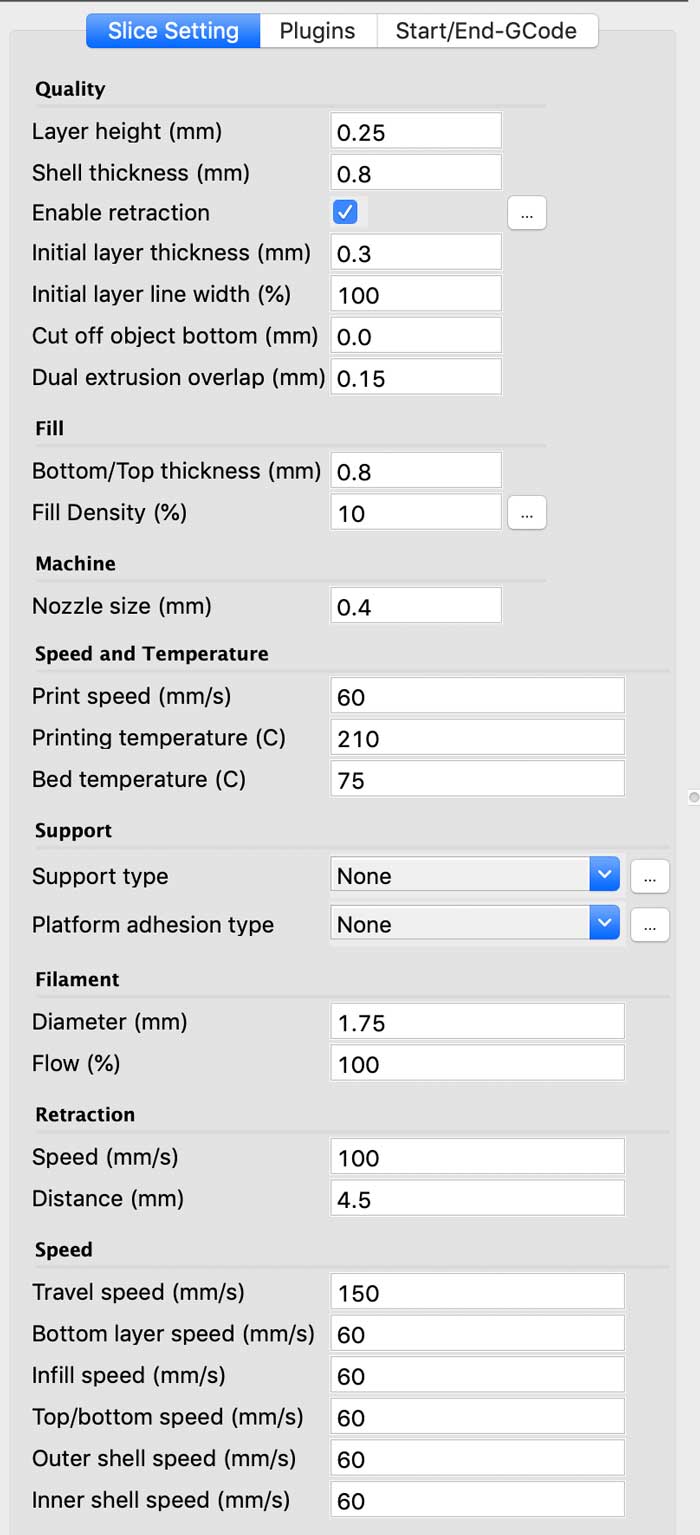
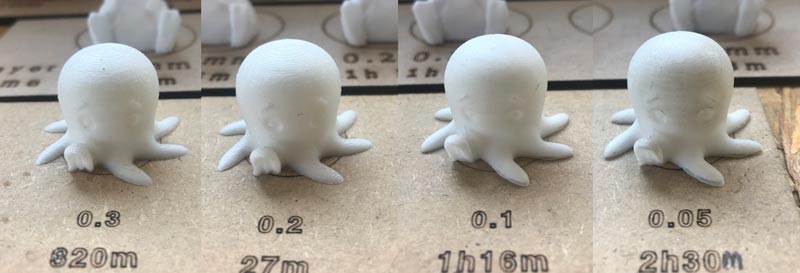
Quality
The layer height is how high each layer is, the height affects how smooth your surface is.
Shell thickness is the thickness of the outer walls of the print.
This depends on the size of your nozzle. so make the number an exponent of the nozzle size
Fill
Bottom/Top thickness is the thickness of the bottom and top outer walls.
Fill density is how solid the print will be on the inside.
(we rarely make it fully solid)
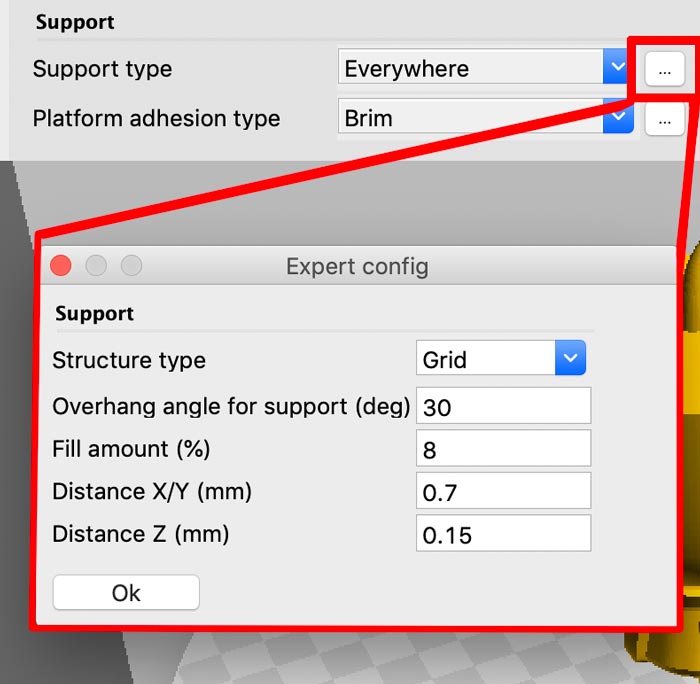
Support
This one is only if you need them. For the Sample print, I didn't need one, but for some prints with big overhang or specific orientation, you need to have supports to make sure they come out. You can change the specification by clicking the three dot button on the side.
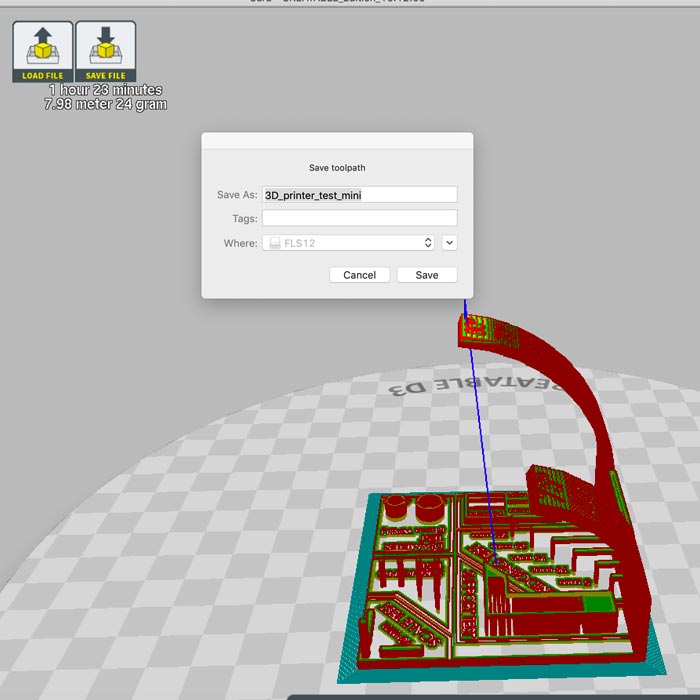
Once you are done and checked all the settings, click on the "save file" button and save it to your SD card.
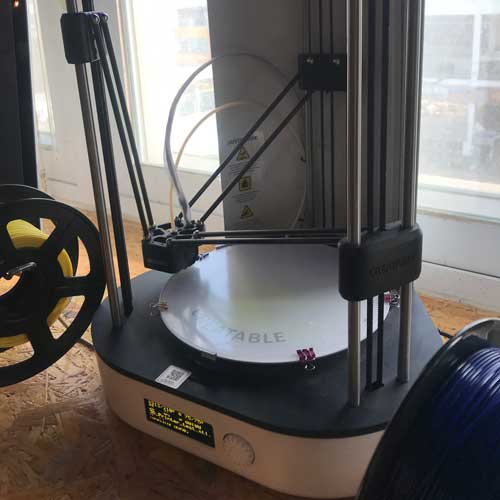
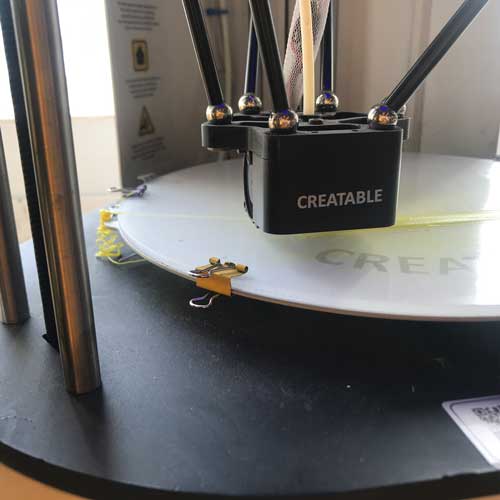
Once you start printing, the bed and the nozzle will start to heat up. When it gets to the right temperature, it will go to the side to poop out a little bit of the filament to get it running and start your print.
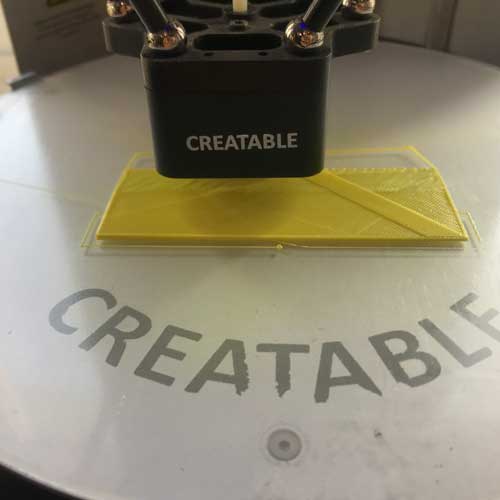
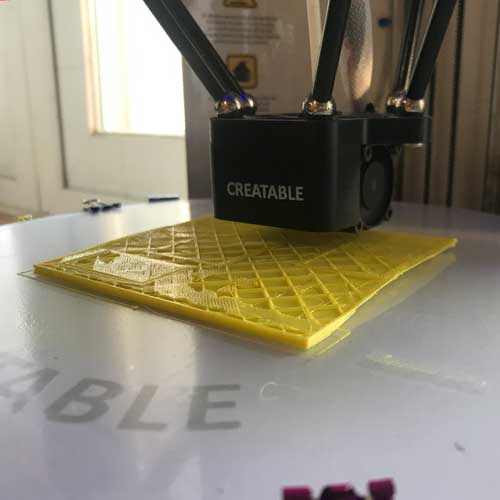
We were adviced to stay watch the printing process for the first 10 minutes to check that it was going correctly. The first sign of a problem can be seen when the brim and initial layer is made. Like in the photo above, I knew that my print was going to be wrong because the design has a flat square bottom, but the initial layer and brim was not. (I went on with it anyways just to see)
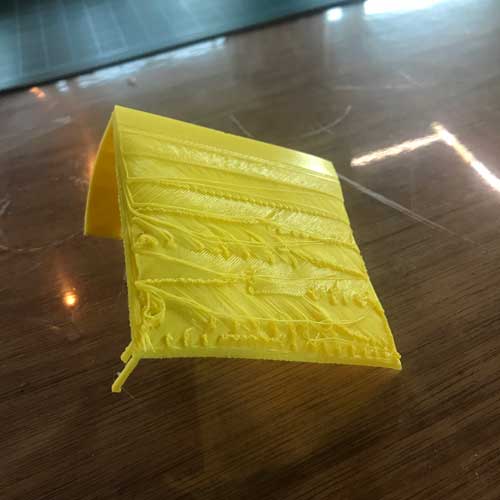
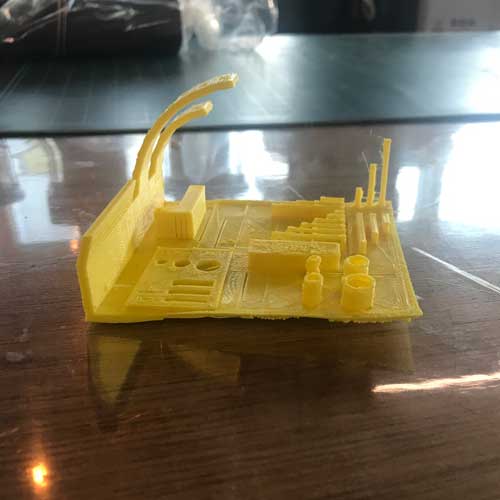
While the print finished well, we can see that the bottom is not flat, therefore unstable, and so the entire print was a little bit off.
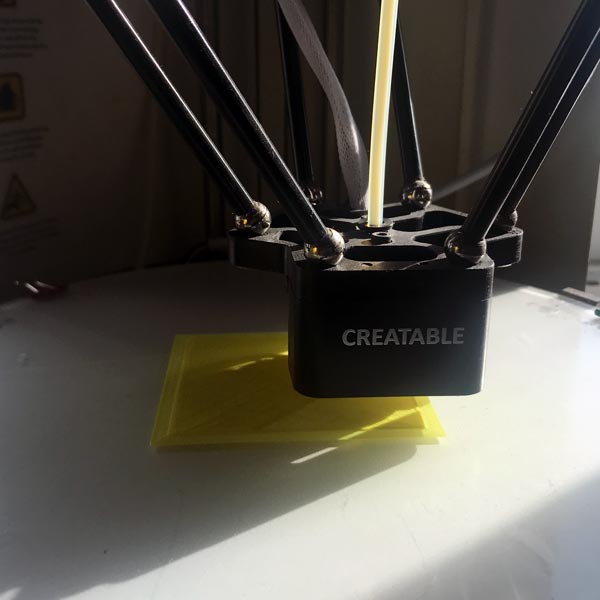
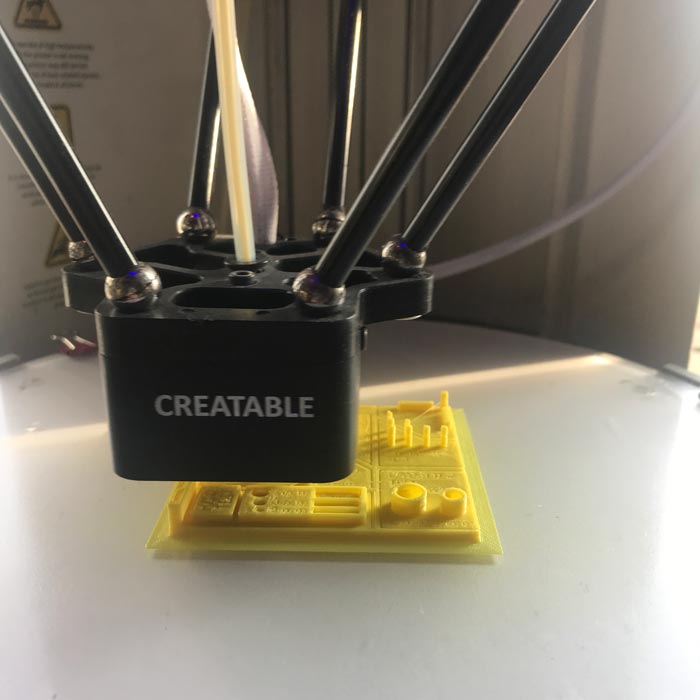
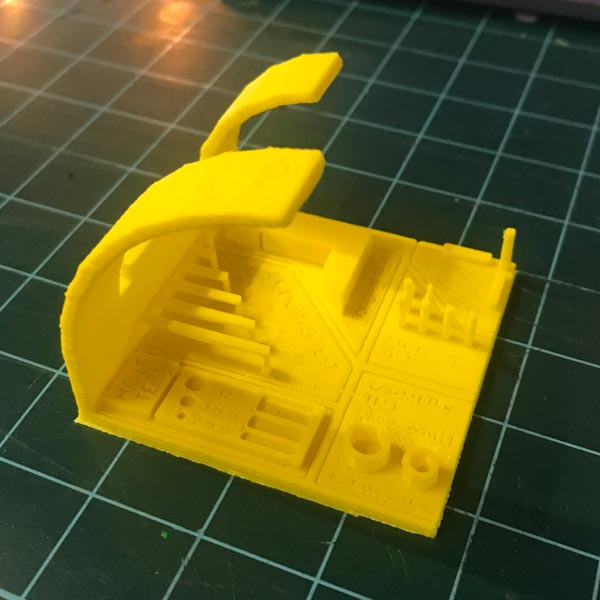
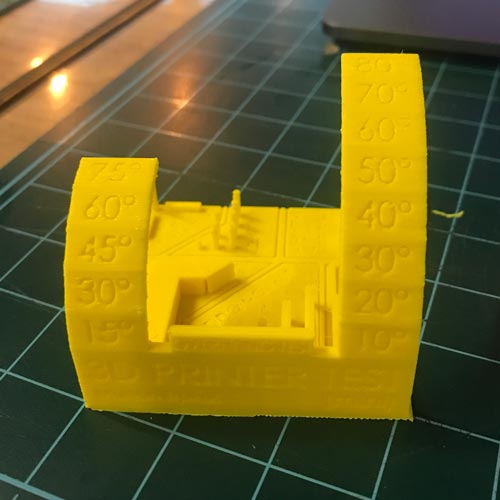
With the 3D printer test, I could check:
Scan Yourself
Kinnect uses infrared laser light with speckled pattern to first map out the depth
and then analizes the pattern (structured light) using depth from focus (astigmatic lens)
and depth from stereo (parallax).
Check the links on the left "links" bar for more detailed explanation on how Kinnect works.
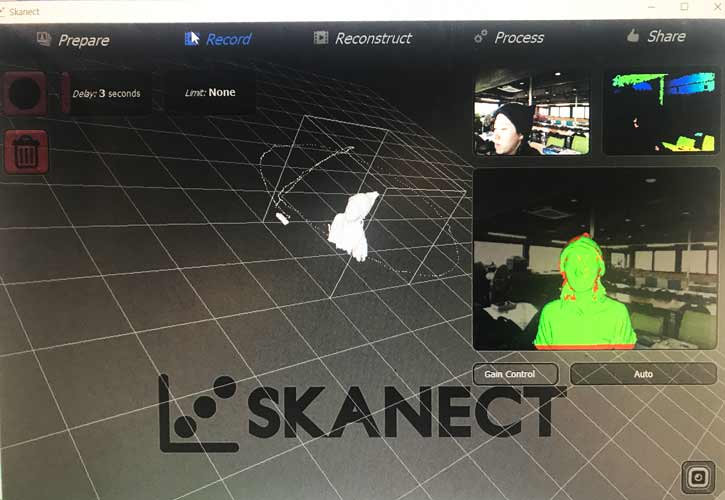
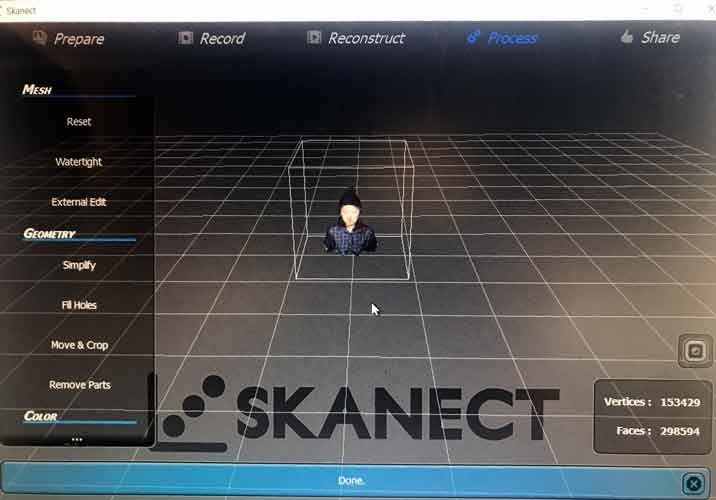
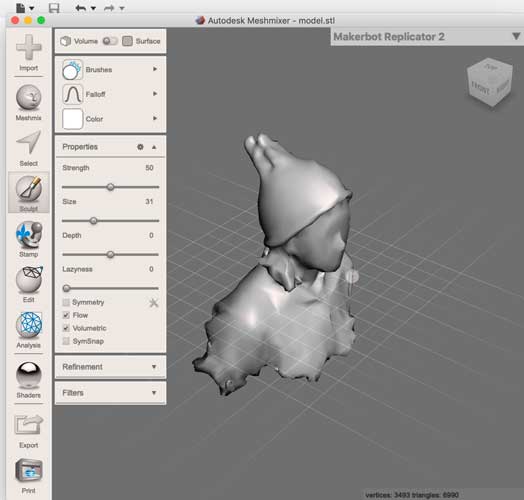
For me, there weren't any holes (that comes from bad scanning) like some people did,
but I had extra parts on my head from not moving evenly enough, and my nose was off center.
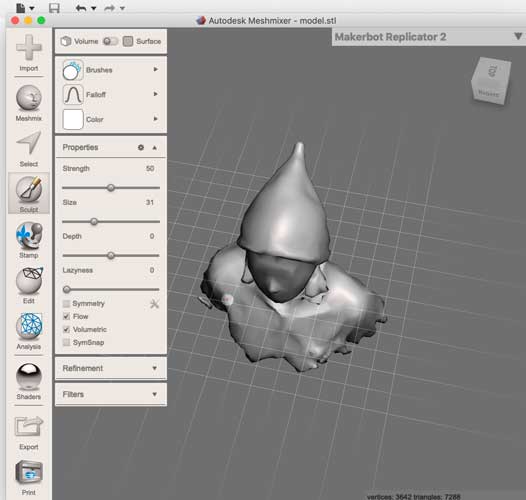
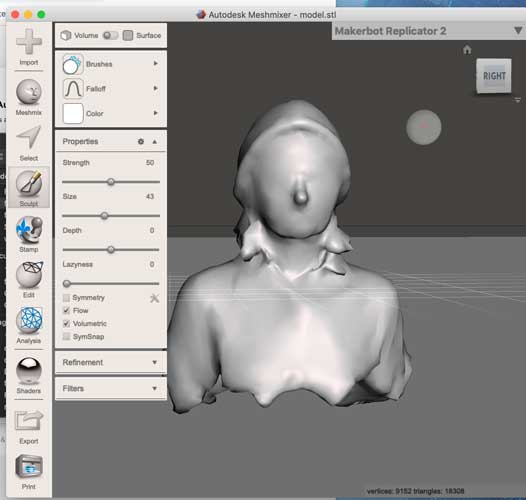
Using these, I was able to fix the weird parts, make the edges of the hat around my head
more apparent and fixed my nose.
You can adjust the size and strength of the tool from the tool bar for easy use.
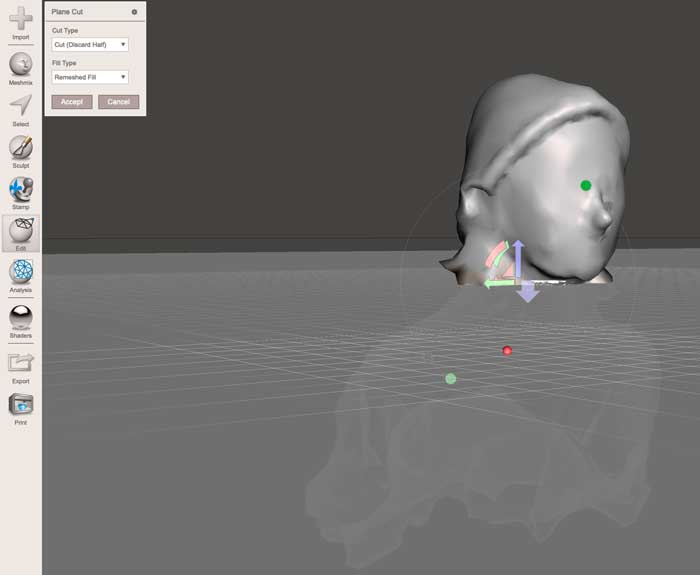
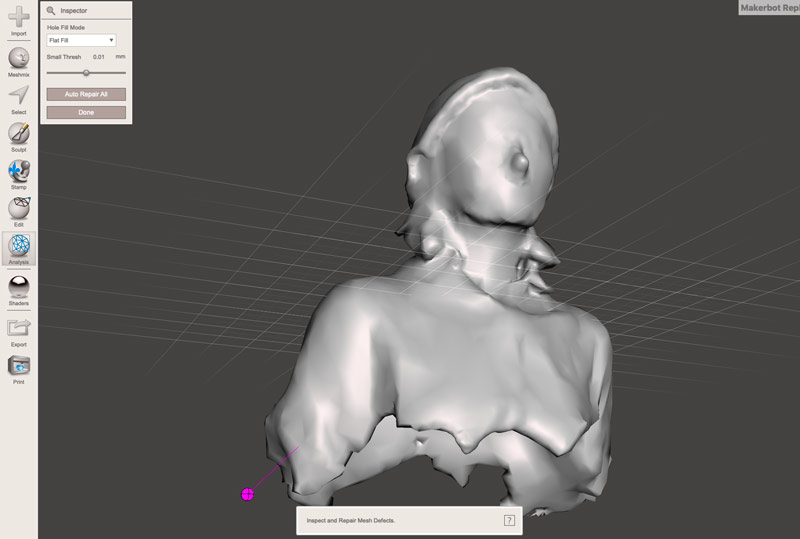
and delete any extra mesh that might have accidentally made it to your scan.
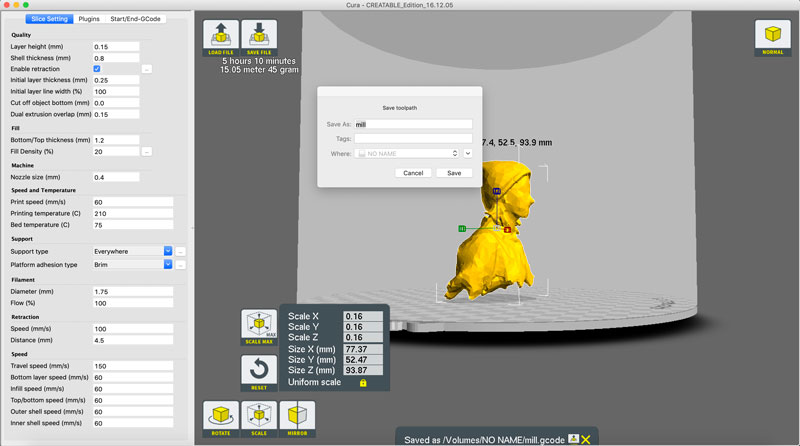
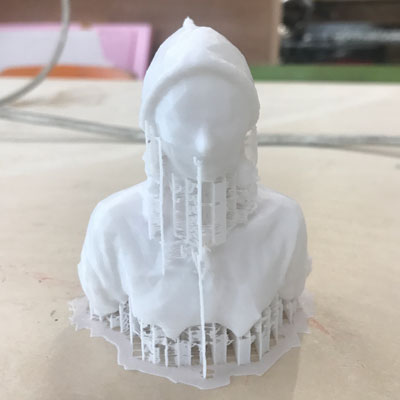
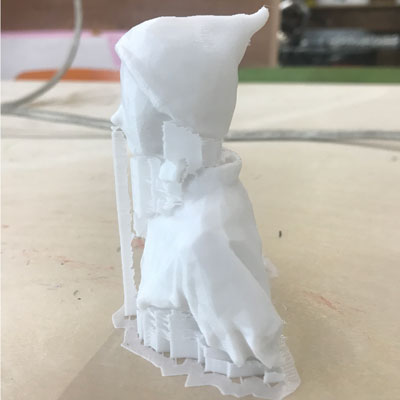
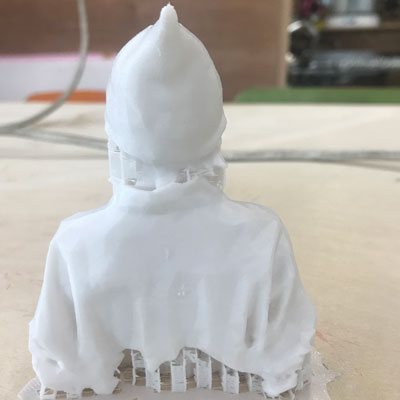
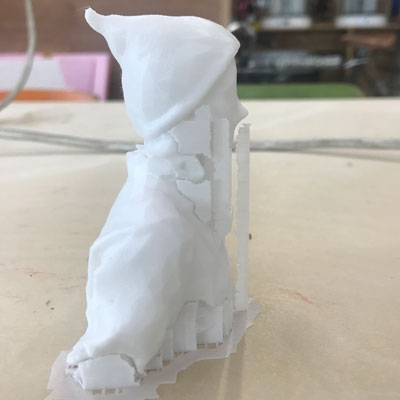
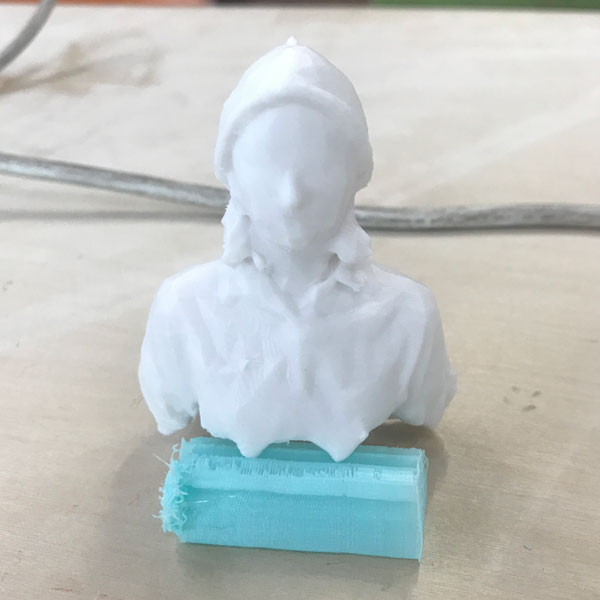
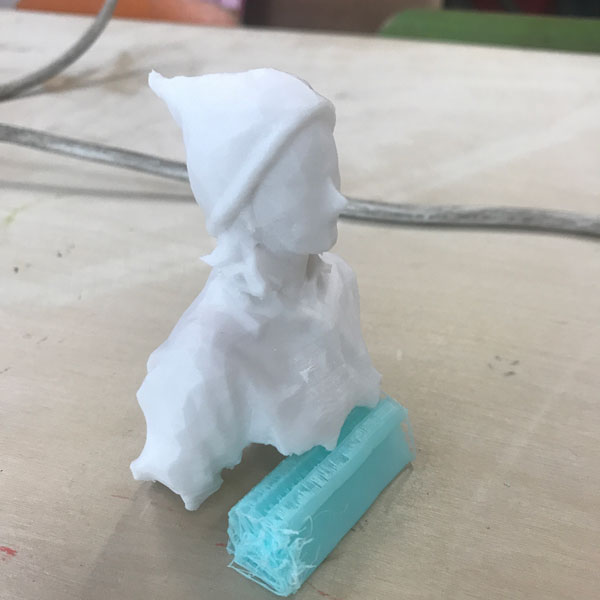
3D Print other things
My first 3d print practice was to print something with a bit of texture on the surface.
So I chose the piñata loot llama from the game Fortnite.

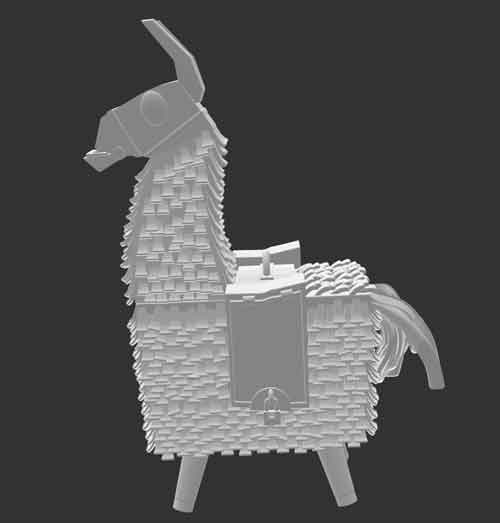
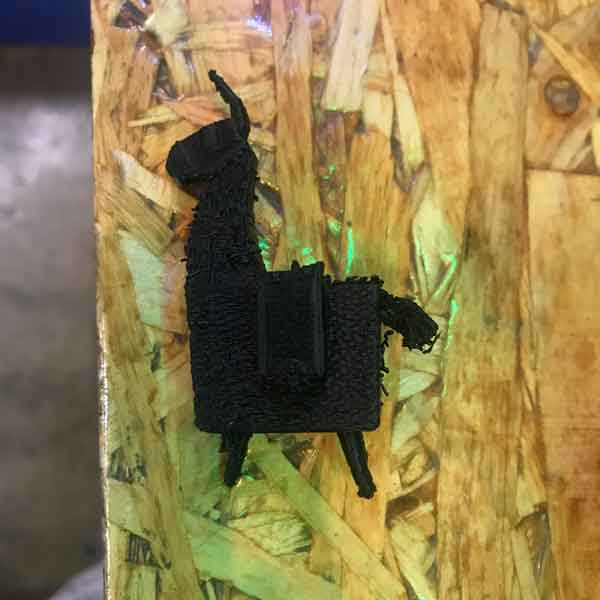
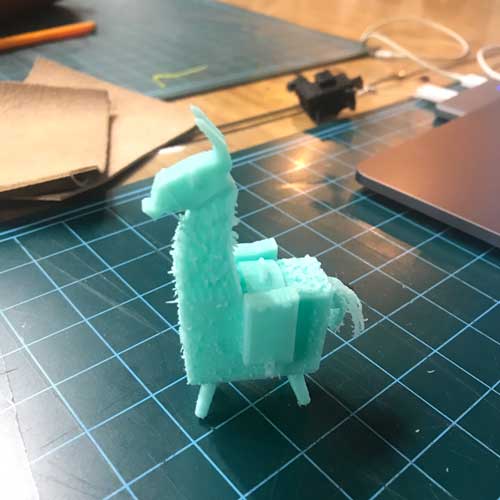
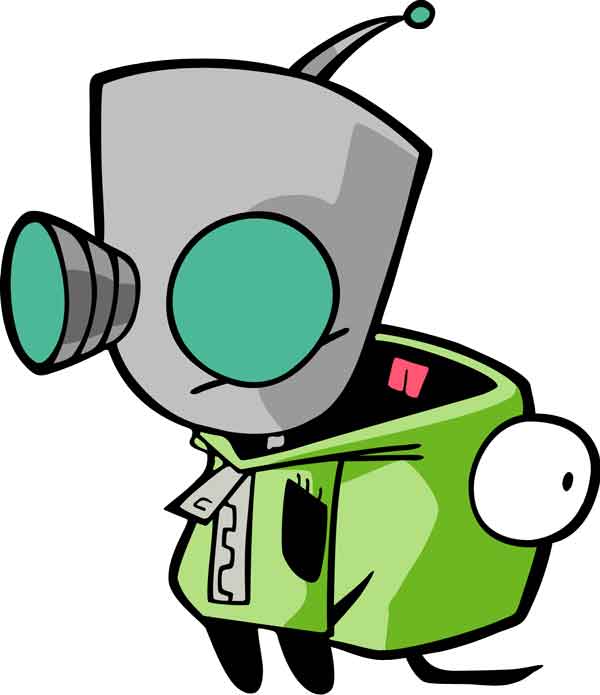
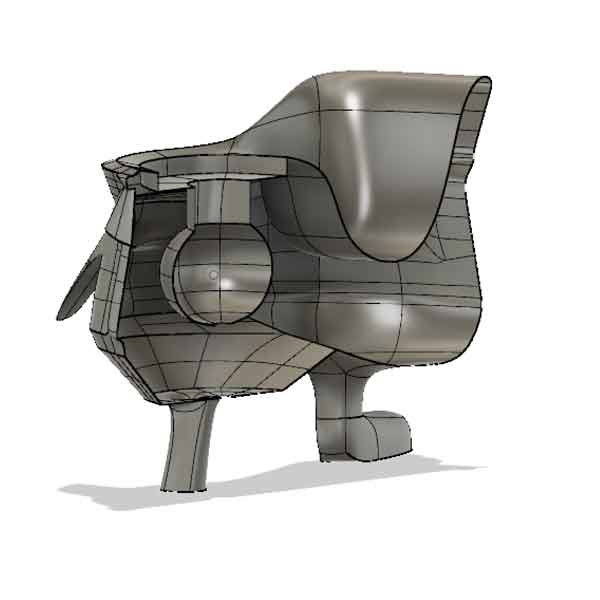
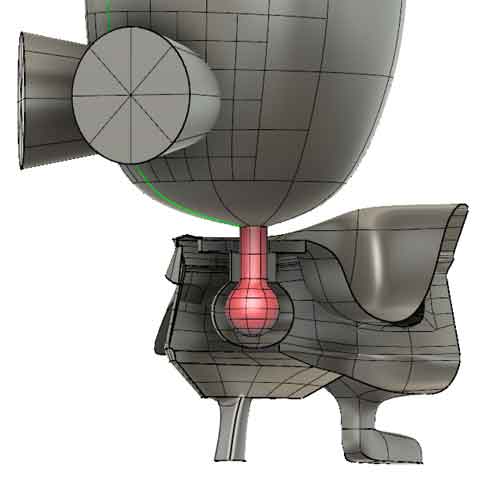
joints like this can be created by additive printing method.
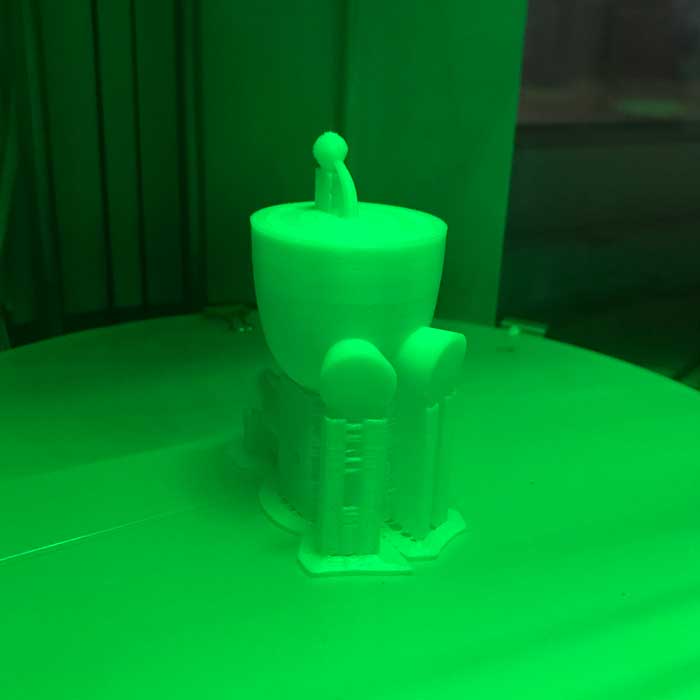
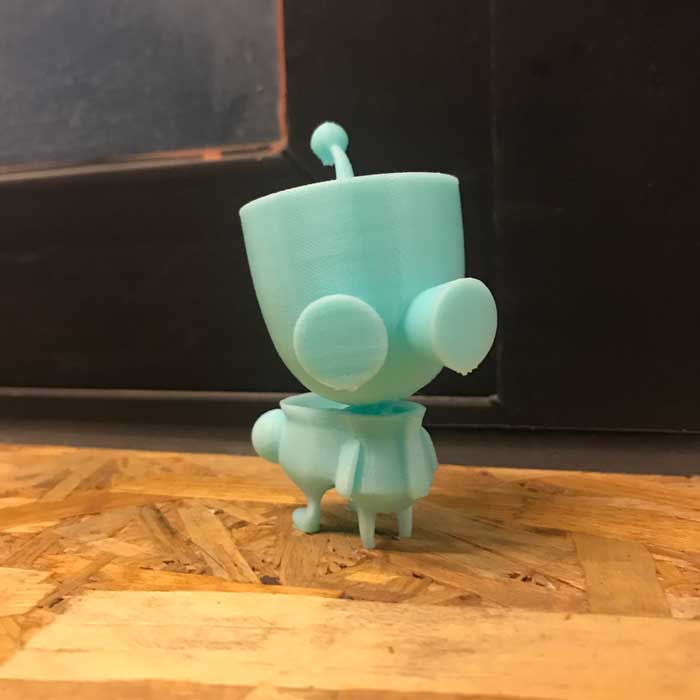