Week 4: Computer-Controlled Cutting
Assignment
Vinyl Cutter
The vinyl cutter at Fab Lab Seoul is a Silhouette Cameo 3...
I've used it a few times before.
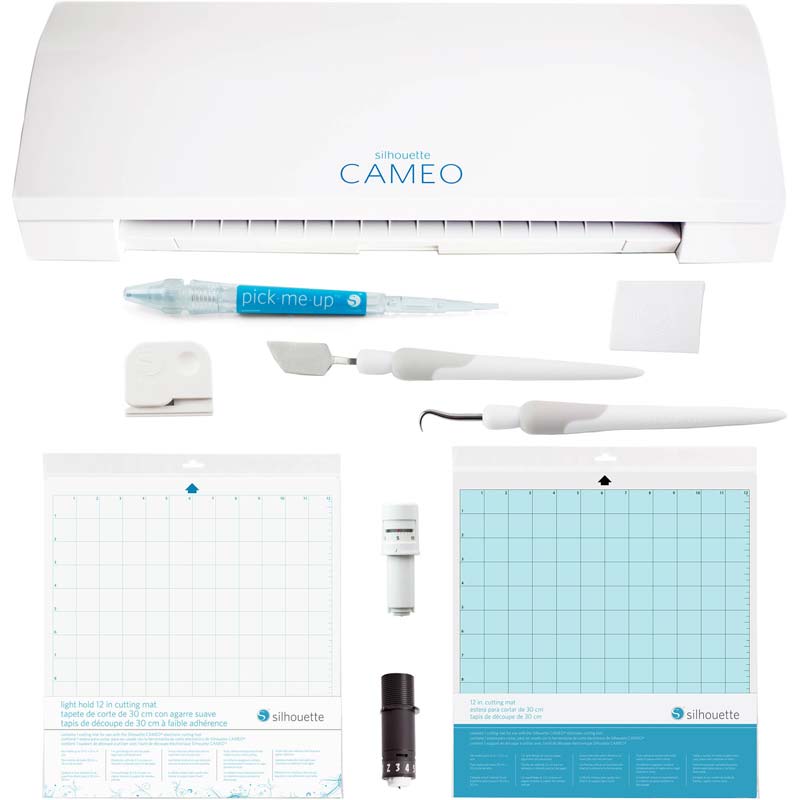
fabrication was too worn out.
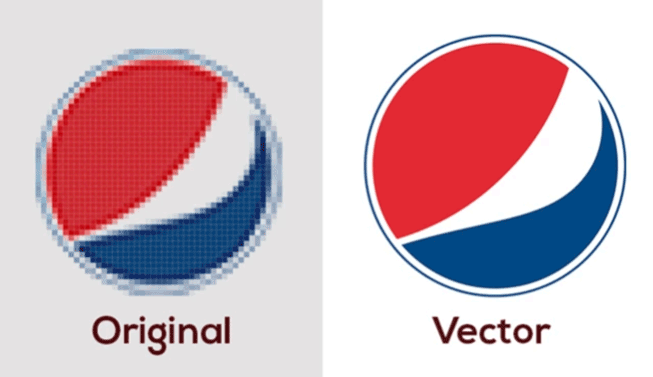
a dxf file ready will be most helpful.
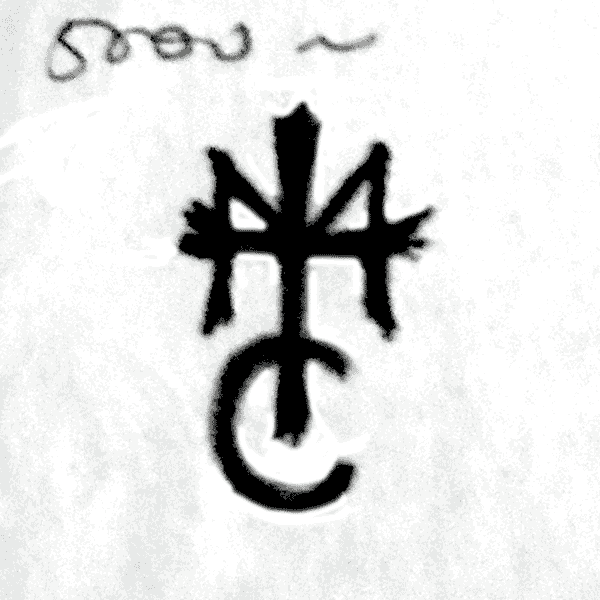
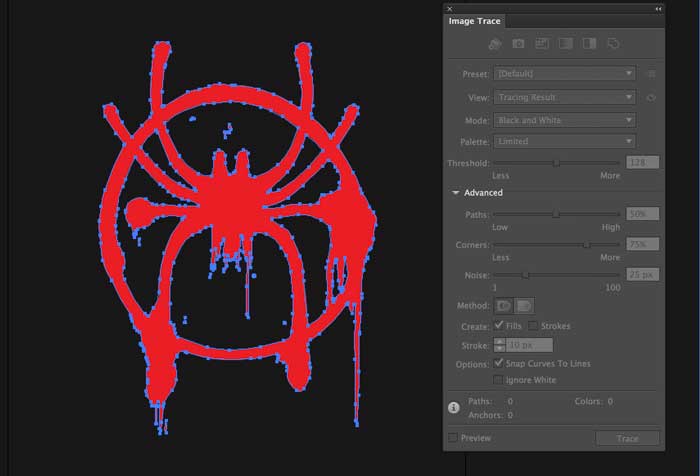
I vectorized it using illustrator.
(remember... you want a clear good drawing.)
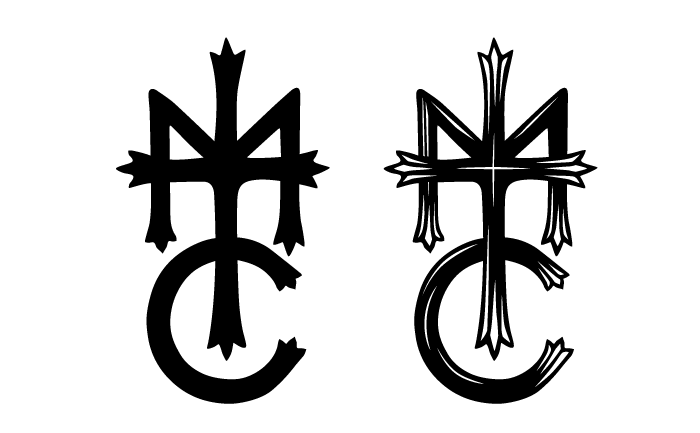
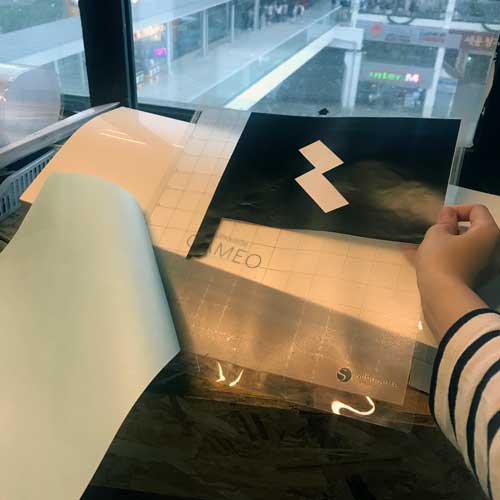
and stick your material onto it.
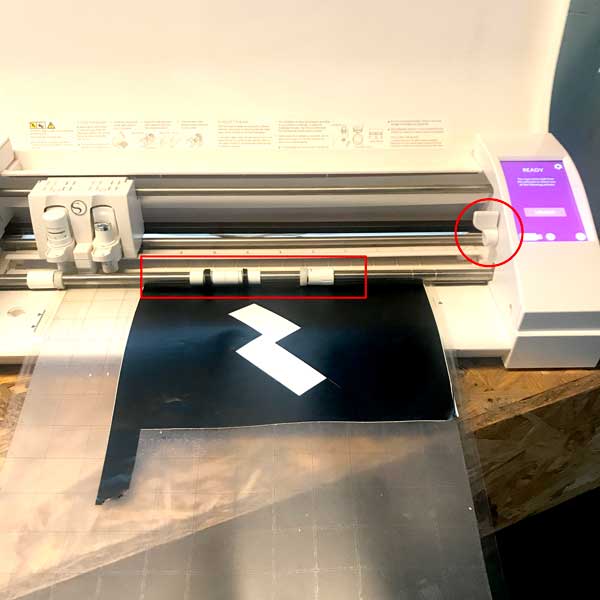
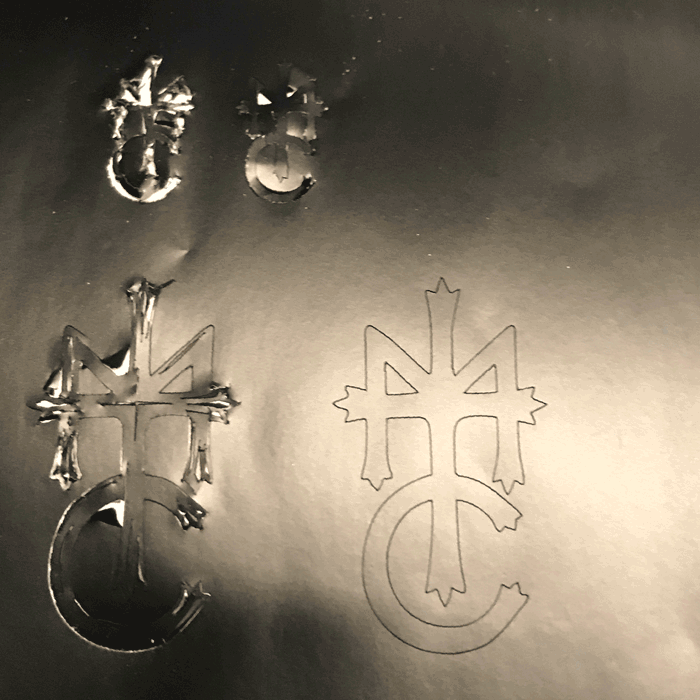
the smaller design did not make it.
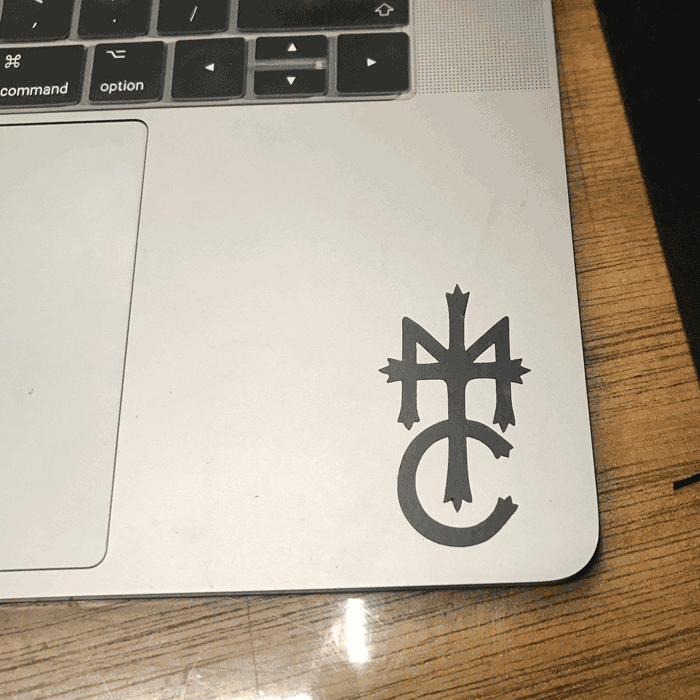
still was very nicely done.
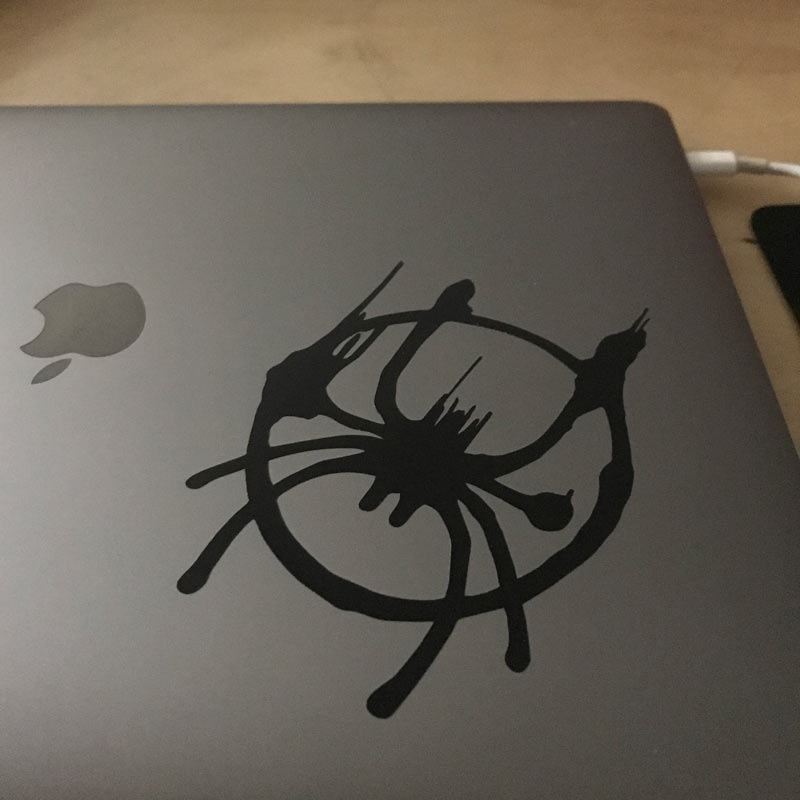
I found a picture of the Spiderman logo of the newest Spiderman movie, vectorized it and cut it.
Laser cutter
the laser cutter was pretty fun to use, and I want to make more stuff using it.
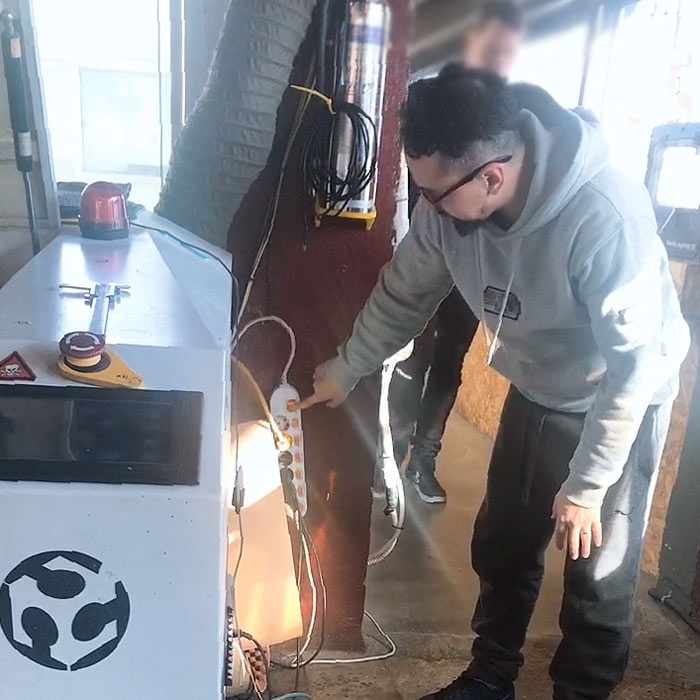
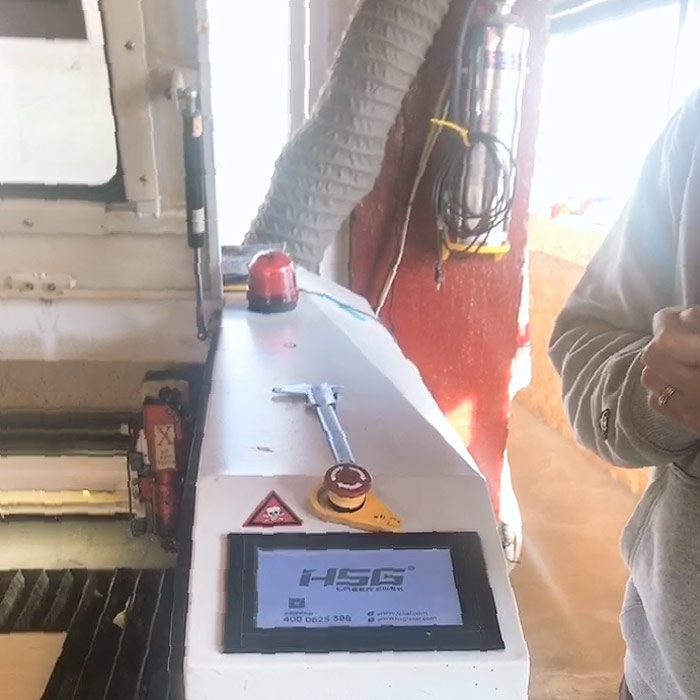
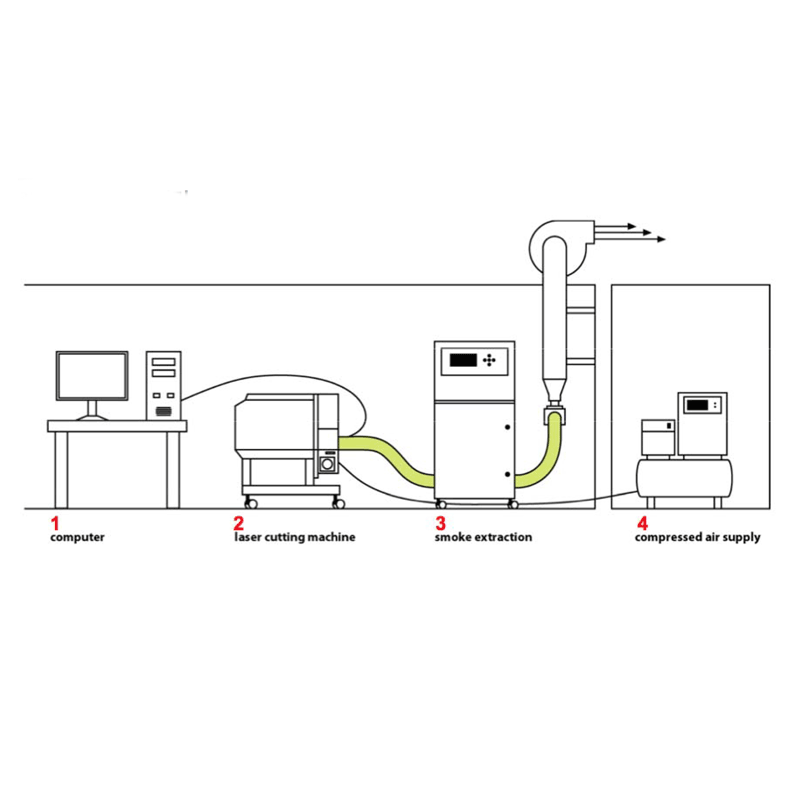
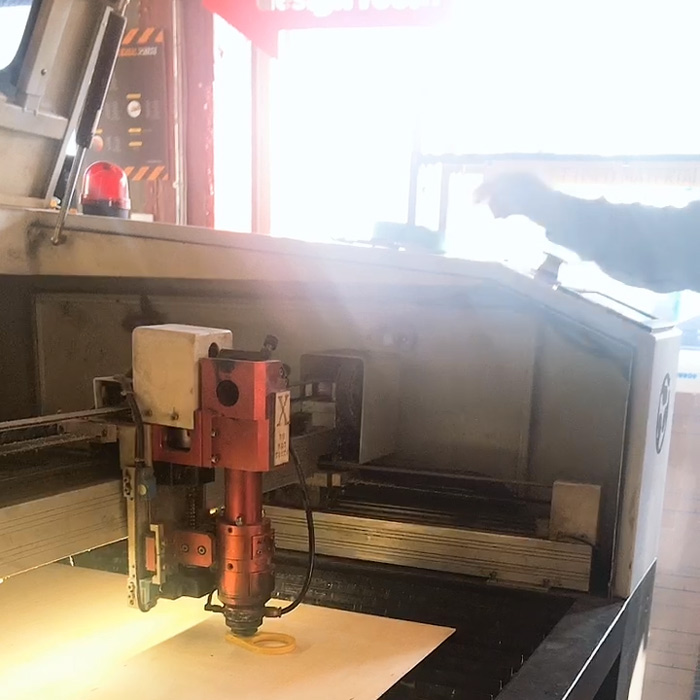
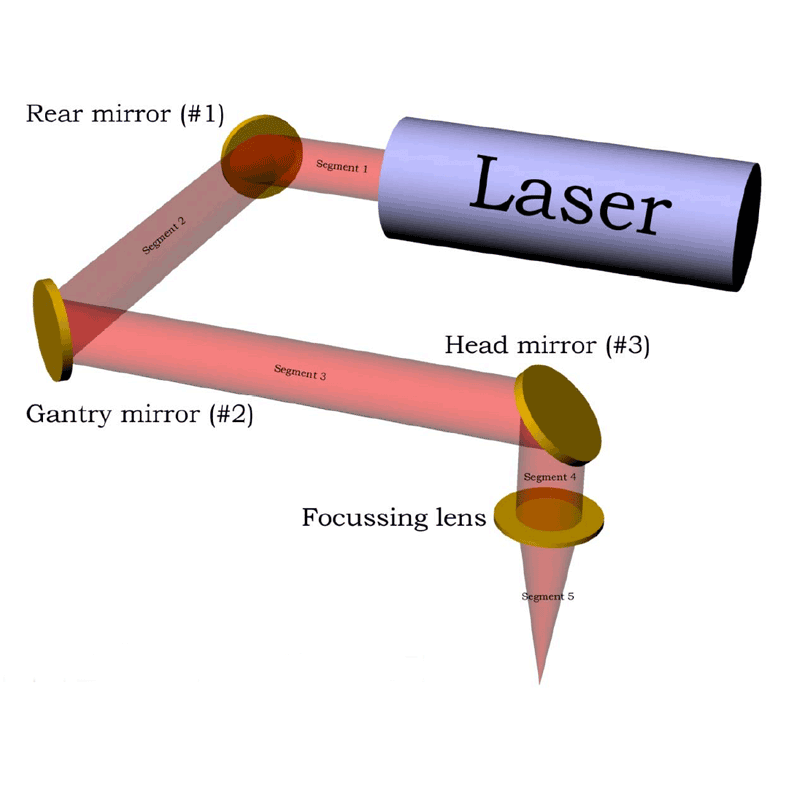
Laser is condensed powerful light. the light doesn't come out straight from the nozzle, but from a tube in the back of the machine. Light generated from there is reflected on mirrors to the focus lense that the user can use to concentrate the light on to the material.
Setting up
Set your material in the machine. Use the grate inside to line up your board. The following is a table about materials.
... Can Cut ... | Cannot Cut | Shouldn't Cut |
---|---|---|
Wood | Glass | Foam Core |
Paper | Metalics | Foam board |
Acryl | Inorganic Material | Styrofoam |
PETG | PolyCarbonate | Melting materials |
ABS | ||
PP | ||
Fabric | ||
Leather |
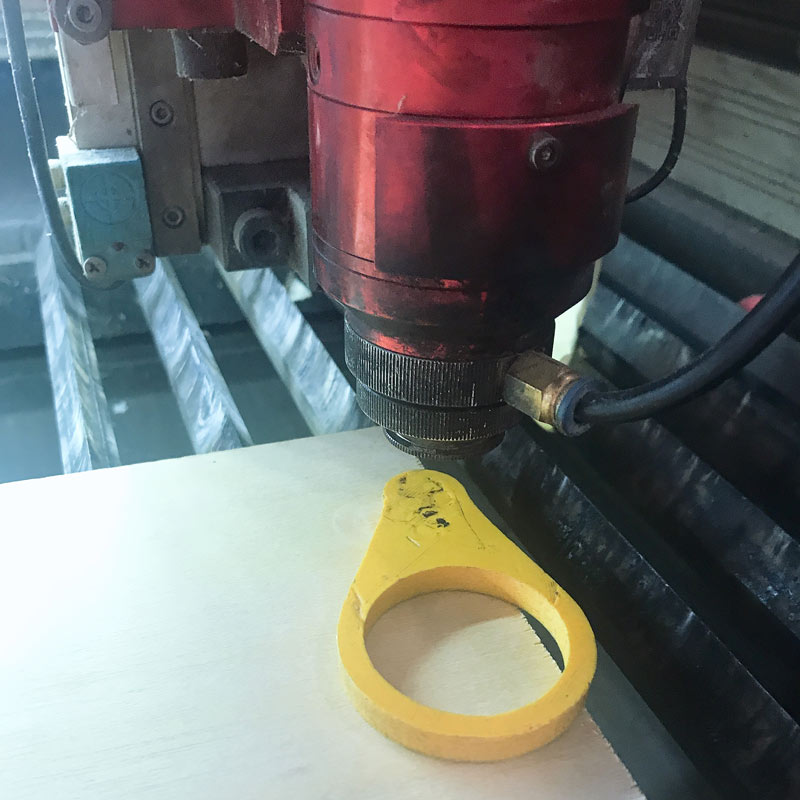
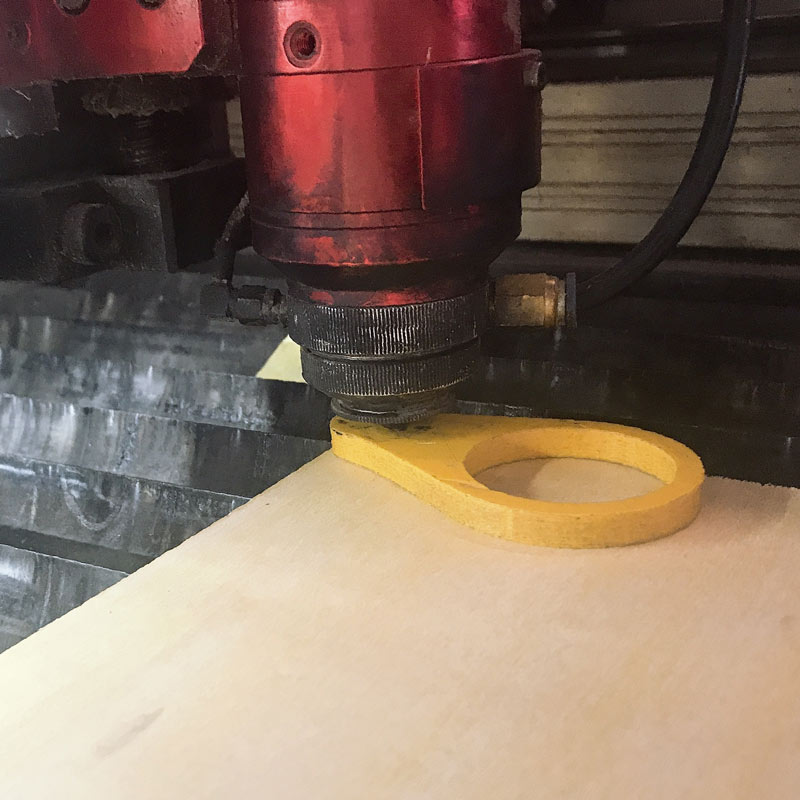
Set the ring on your material. On the screen to your right, navigate the axis to lower the nozzle on to the ring until they touch. Take out the ring, and move the axis to set your personal origin on the board.
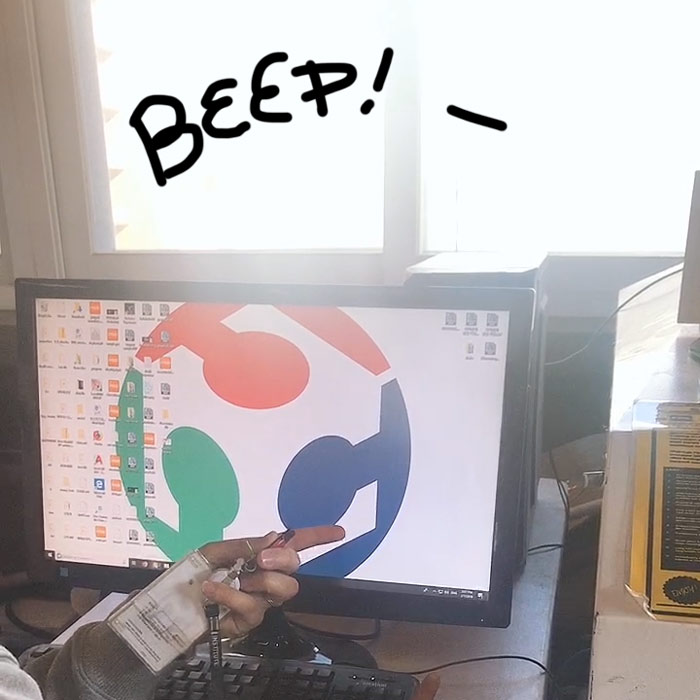
When you turn on your computer connected to the laser cutter, the machine will communicate that it is indeed connected, with a beep sound. When you open the program, it will make triple beeps. (I had an error, and when that happens, the machine will keep beeping. in that case, turn it off and on again.) now load your dxf file.

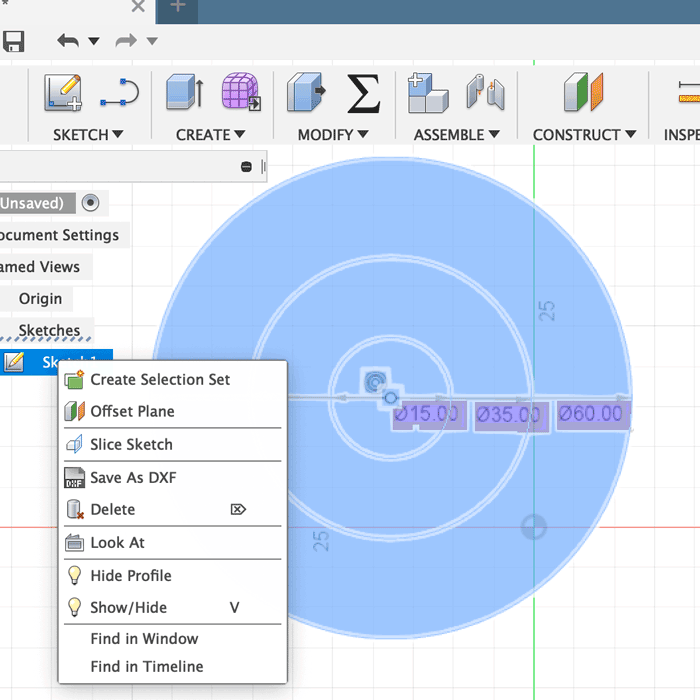
My instructor Rodrigo gave us an assignment to cut three ringed circle to practice, so I used fusion to make the rings, and saved it as dxf from the sketch mode.
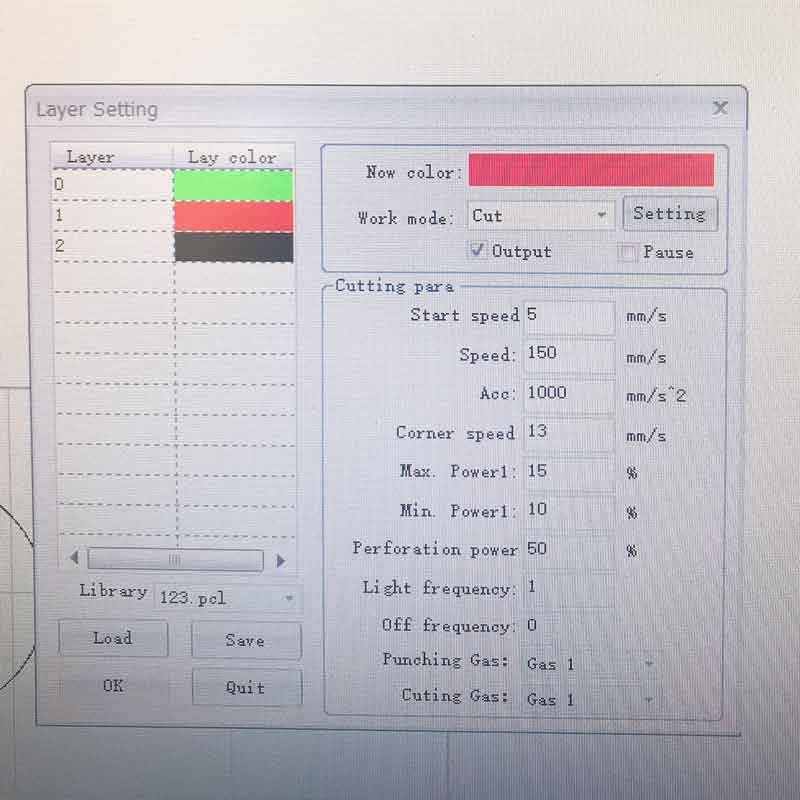
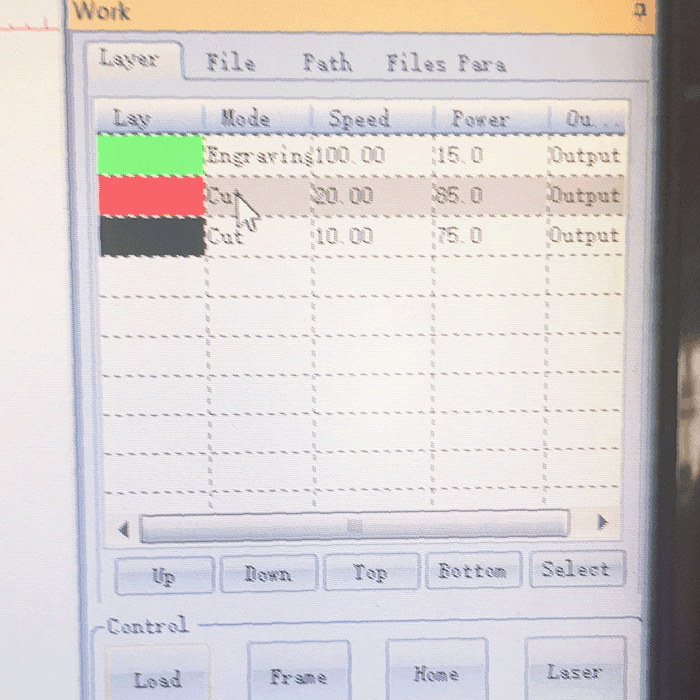
You can draw on the software as well, and edit them. I changed the colors for the three rings to test different settings. The green circle was set to engrave, the red circle was set for vector cut and the black line was set to cut out. The cut out has to be the last or else your material will fall out and the engraving will be inaccurate
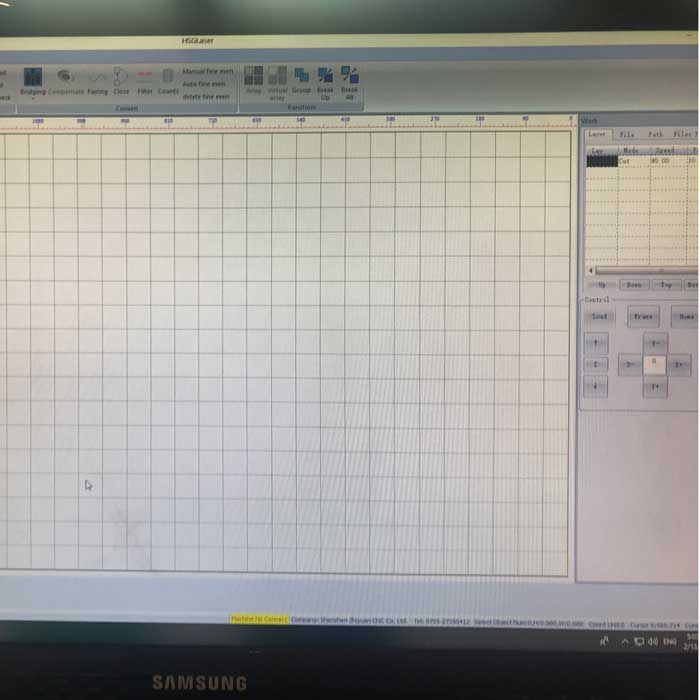
After loading and adjusting the position to your liking (after adjusting the speed and power, press ok. if you just tap enter, it goes back to the original setting...), click the load button. The machine will beep at you again.
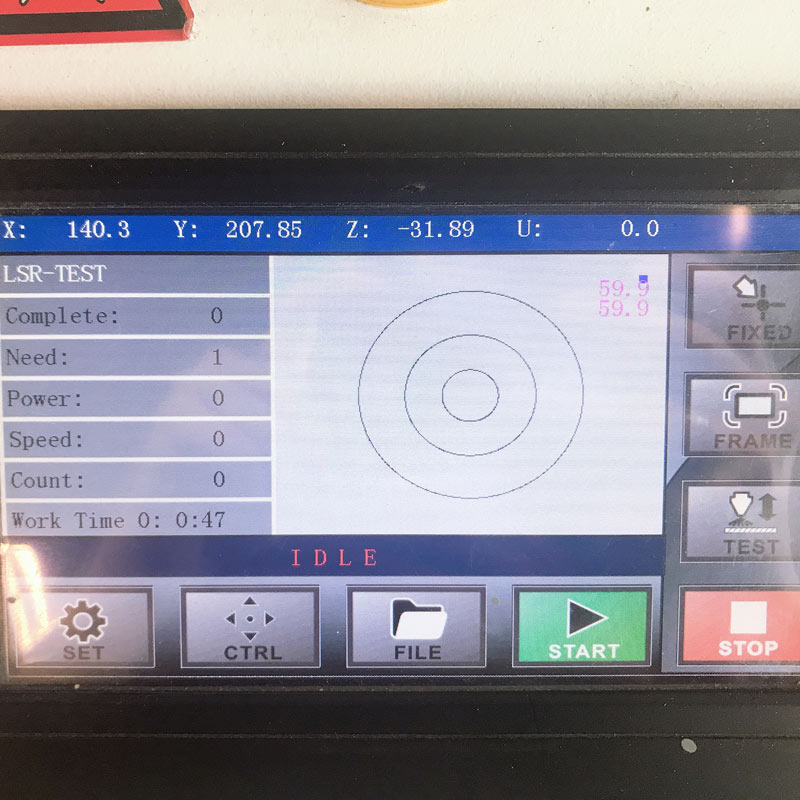
the screen on the machine will show your file loaded up. Here, you can check the frame to make sure your cut is within the material. and press start.
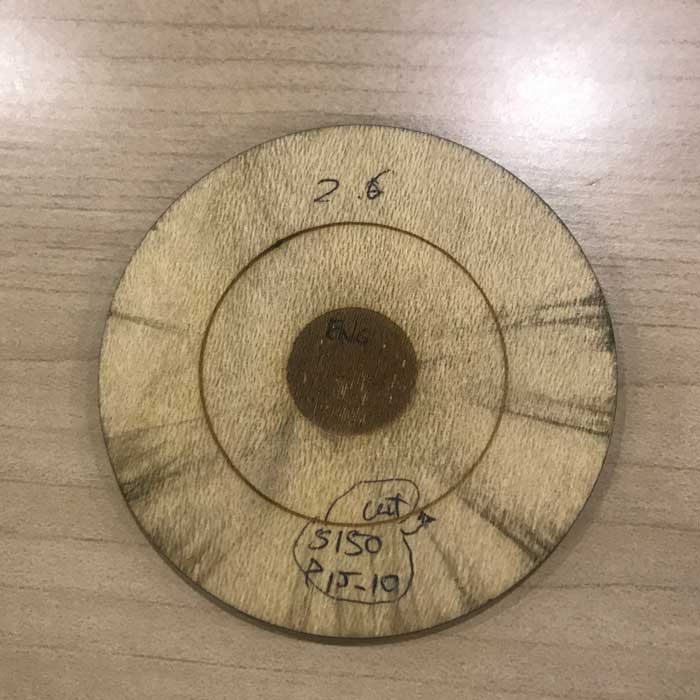
The following is a table of materials that I tested out for speed and power.
Cut | Vector Cut | Engrave | |
---|---|---|---|
Speed | 10-20 | 150 | 150 |
Power(%) | 70-75 | 10-15 | 15-20 |
Cut | Vector Cut | Engrave | |
---|---|---|---|
Speed | 10 | 300 | 300 |
Power(%) | 70-75 | 10-15 | 55 |
Cut | Vector Cut | Engrave | |
---|---|---|---|
Speed | 5 | 150 | 300 |
Power(%) | 80-85 | 10-15 | 55% |
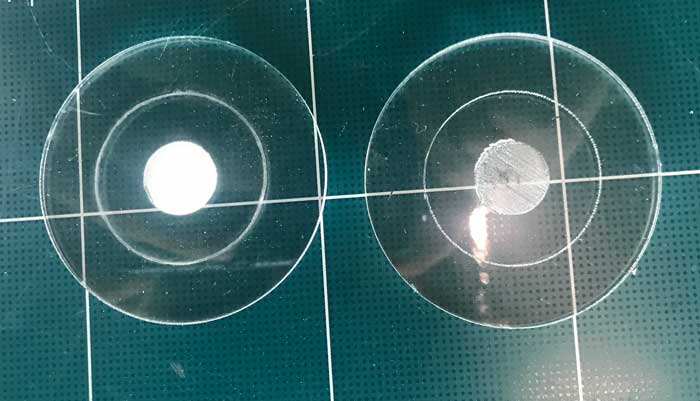
I tried with acryl, it worked fine except for the thin protective film on the acryl melted onto the engrave. So I made another one after removing the film.
Comb for kerfing
Kerf is the measurement of the part that is cut or burned away.
So if I were to use a saw to cut, the part that will be cut away will change depending on the thickness of the blade. I used a caliper to check the width of my material. I made the comb on fusion. I knew that the kerf would be in 0.0mm unit.
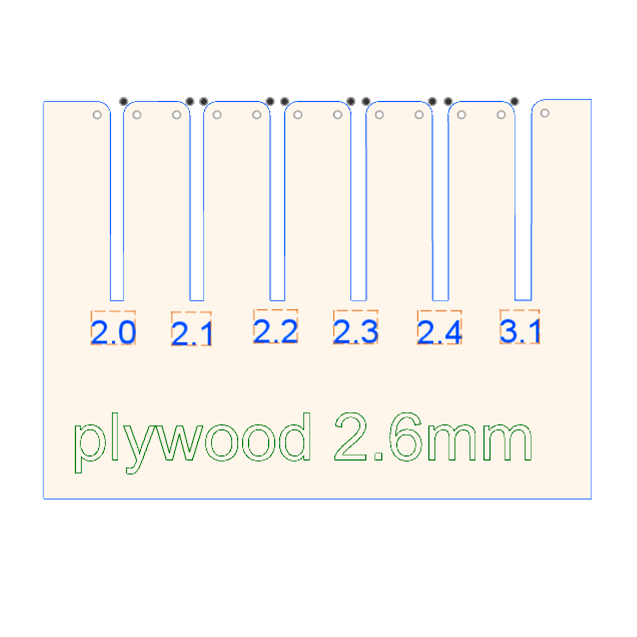
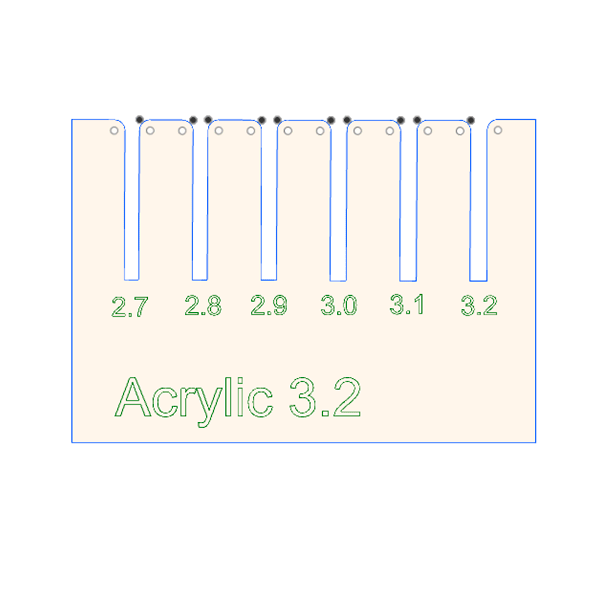
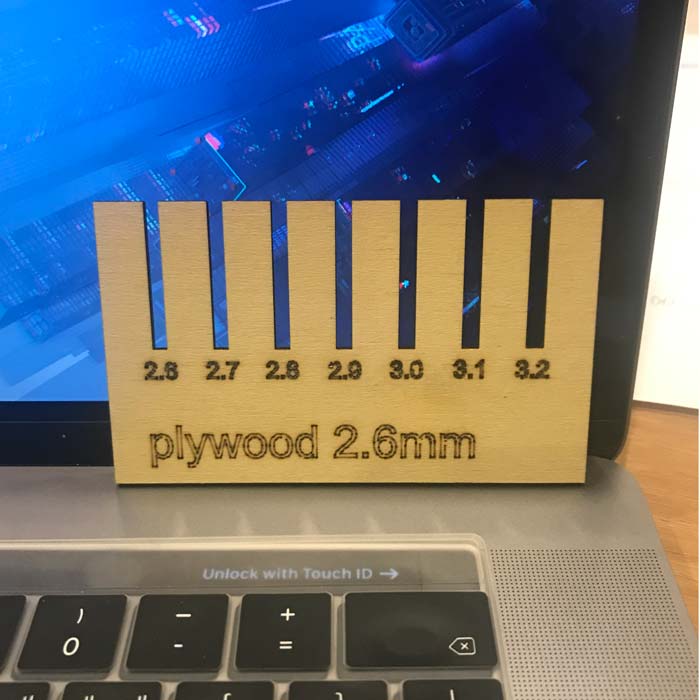
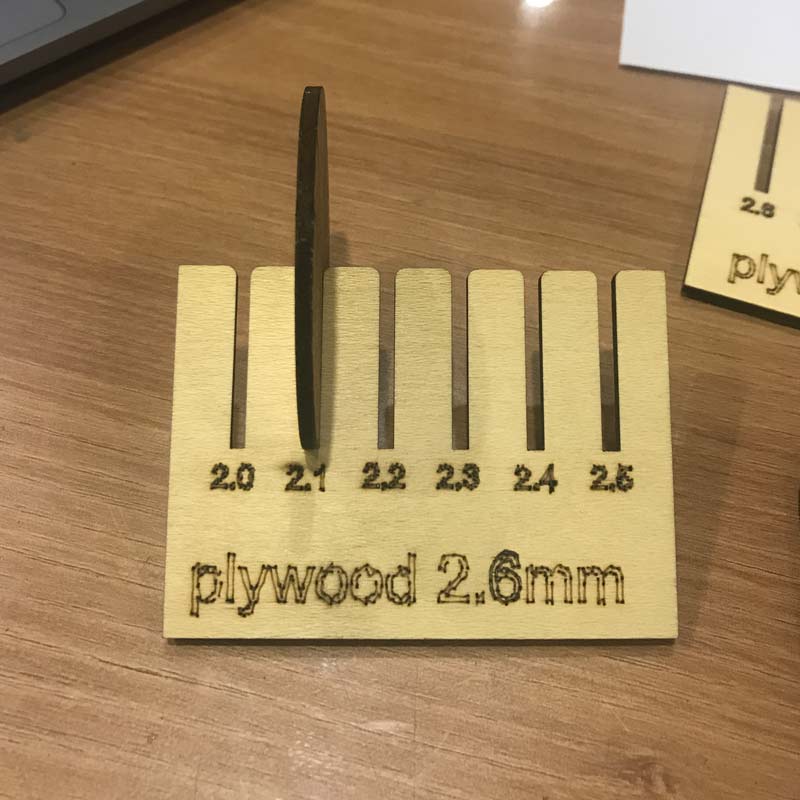
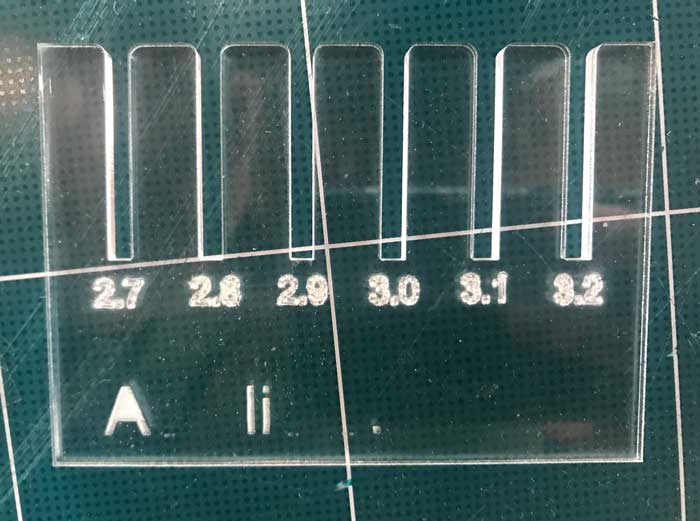
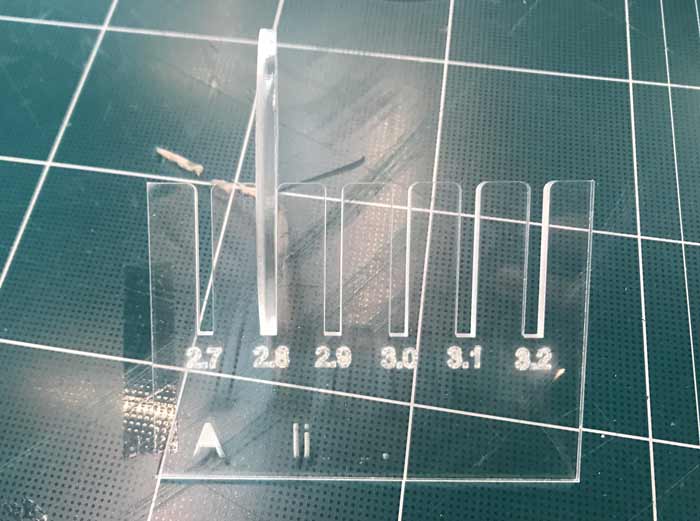
(Plywood is 2.6mm it fit into a slot that was 2.1mm so around 0.25mm)
(Acrylic is 3.2mm it fit into a slot that was 2.8mm so around 0.2mm)
Parametric Design Kit
Parametric Design is using a set unit measurement for multiple parts of the design so that when the measurement changes, the parts of the design that is applied will also change accordingly.
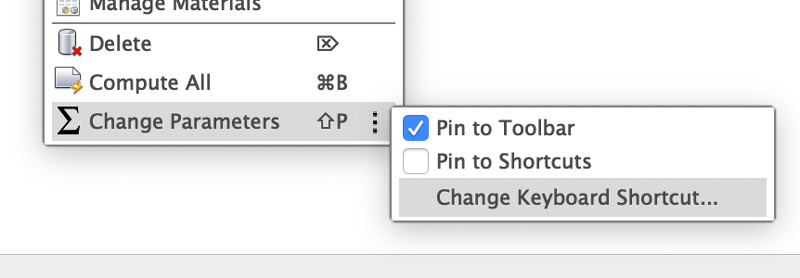
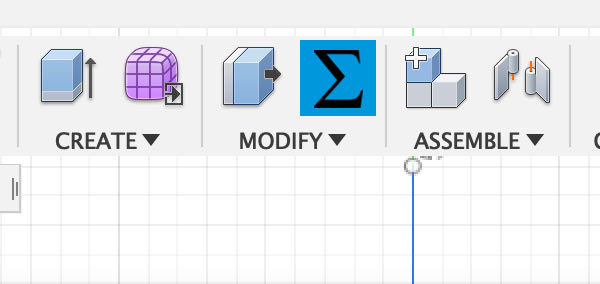
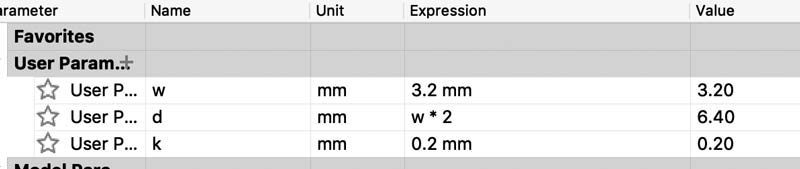
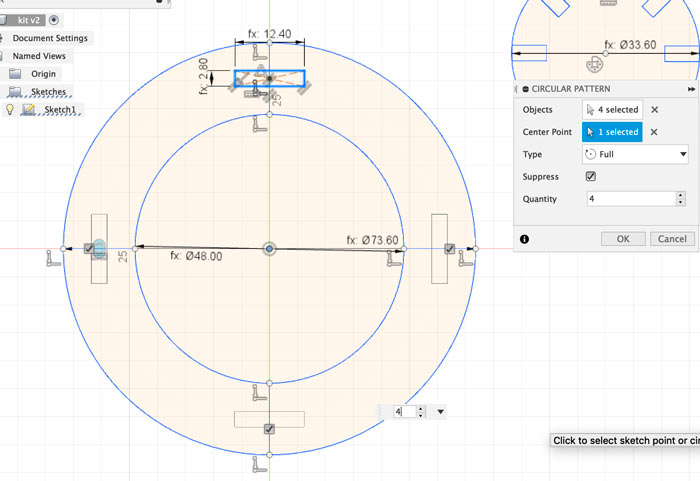
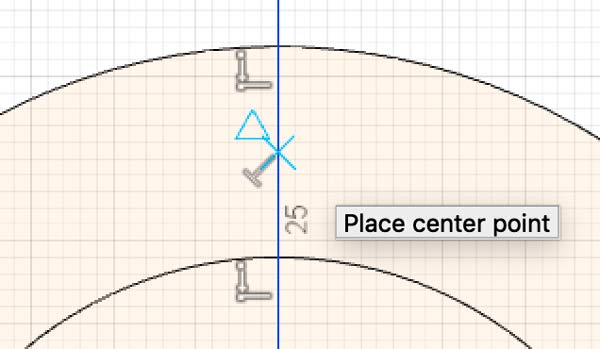
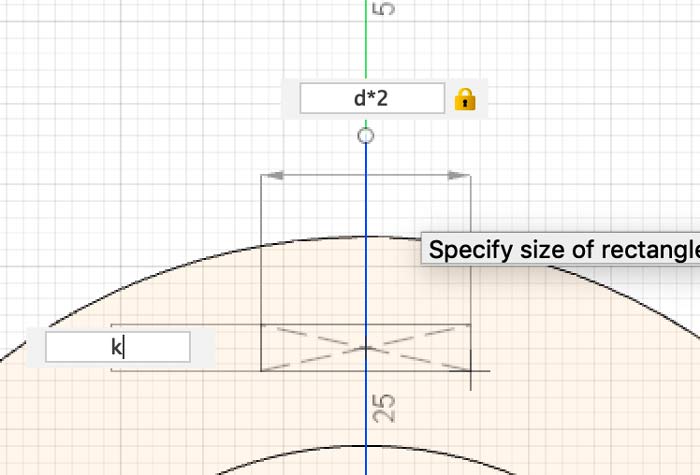
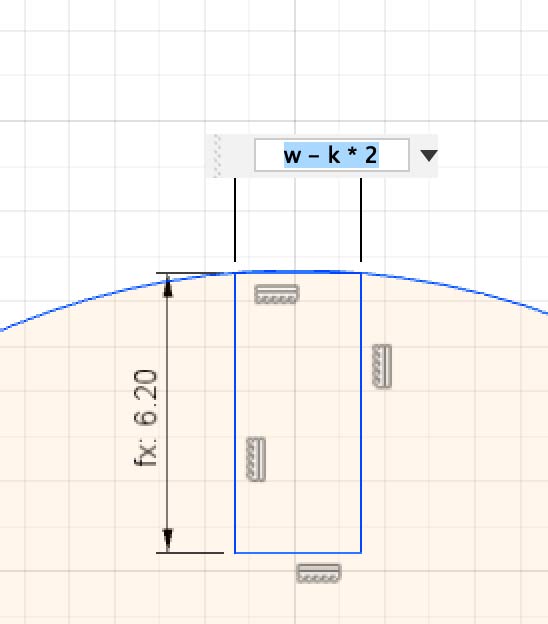
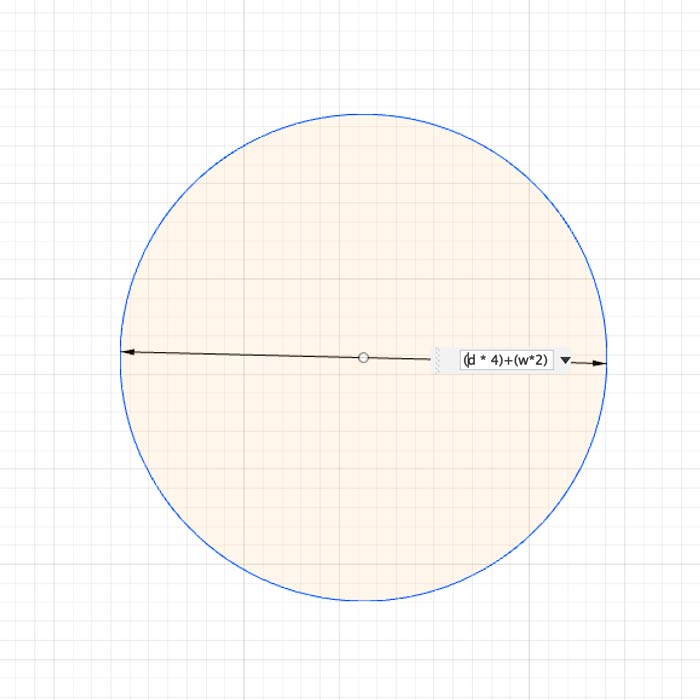
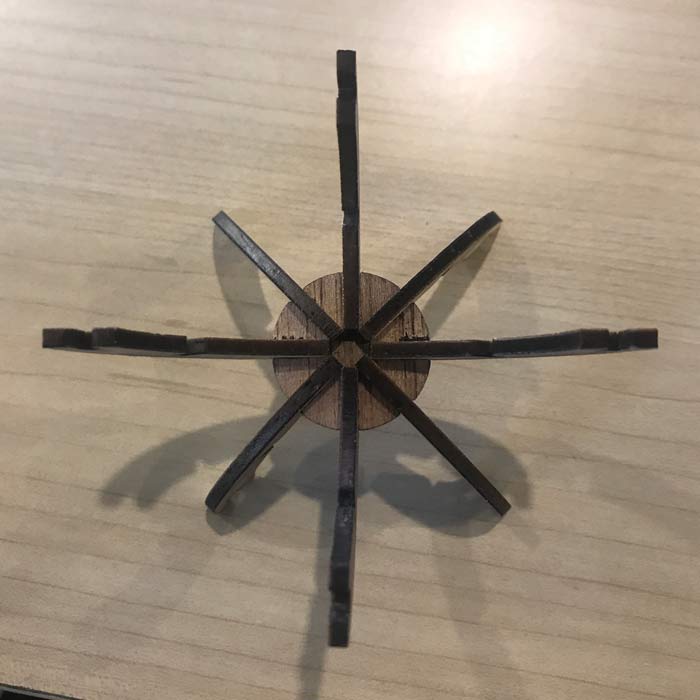
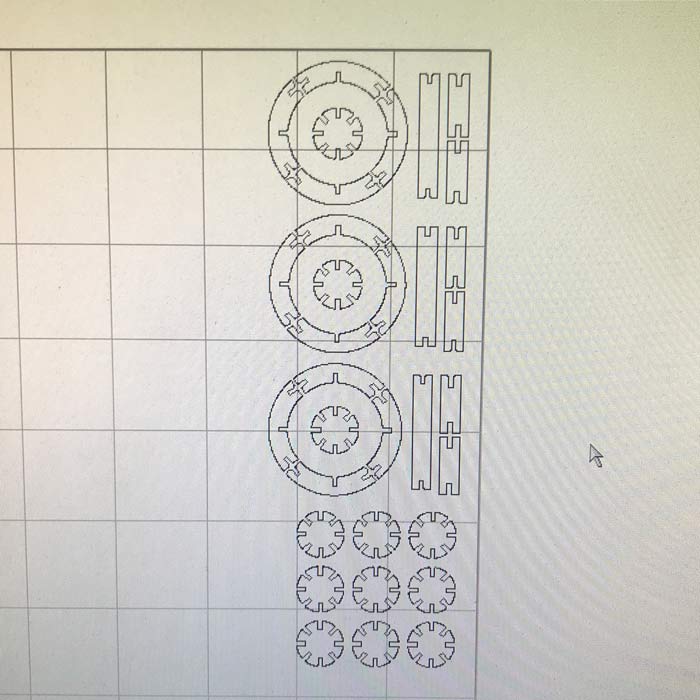
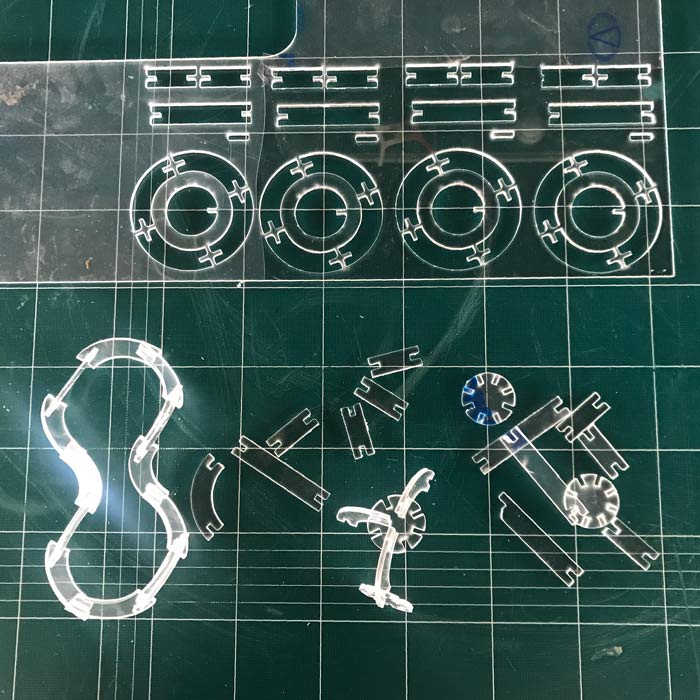
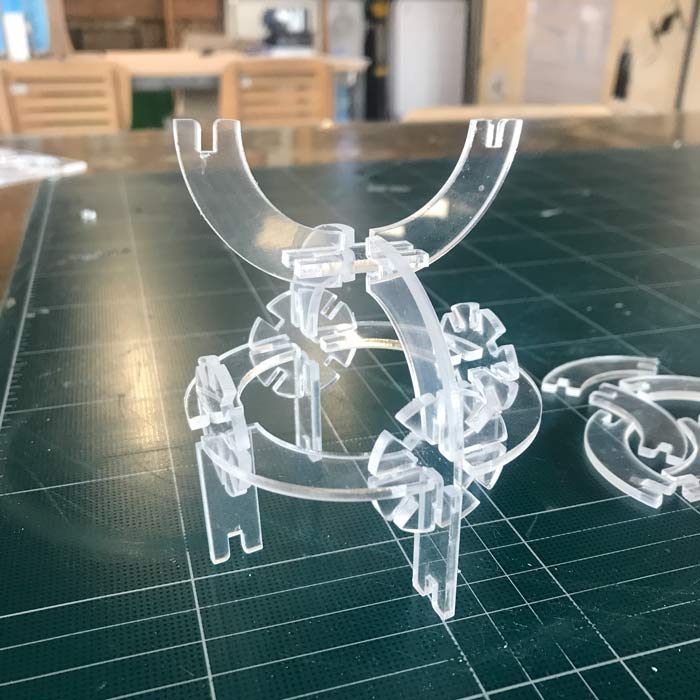
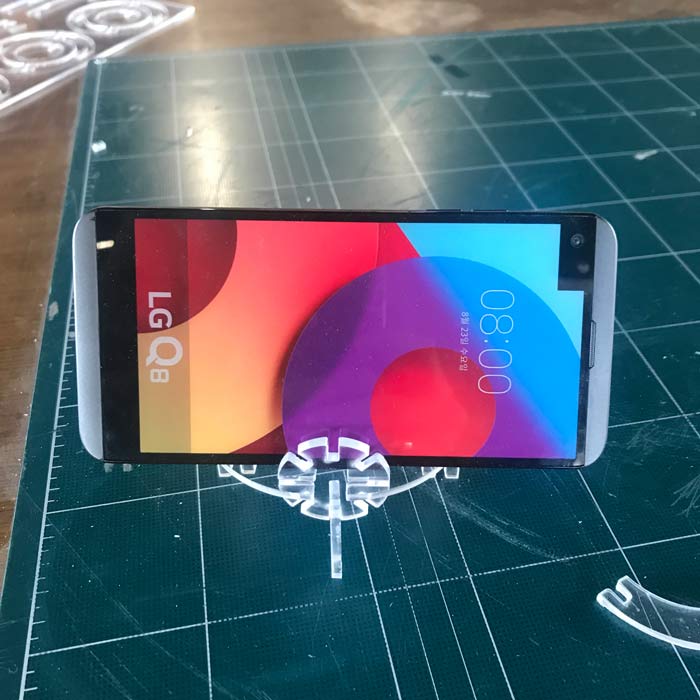
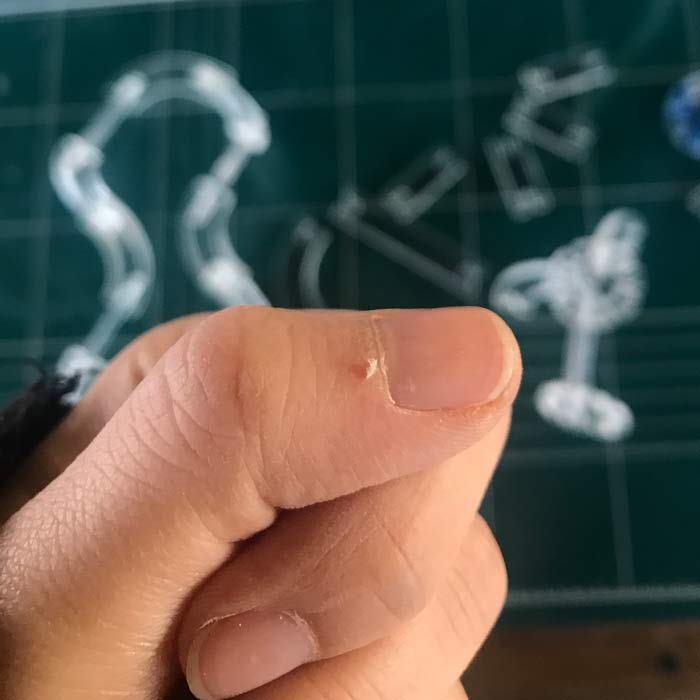
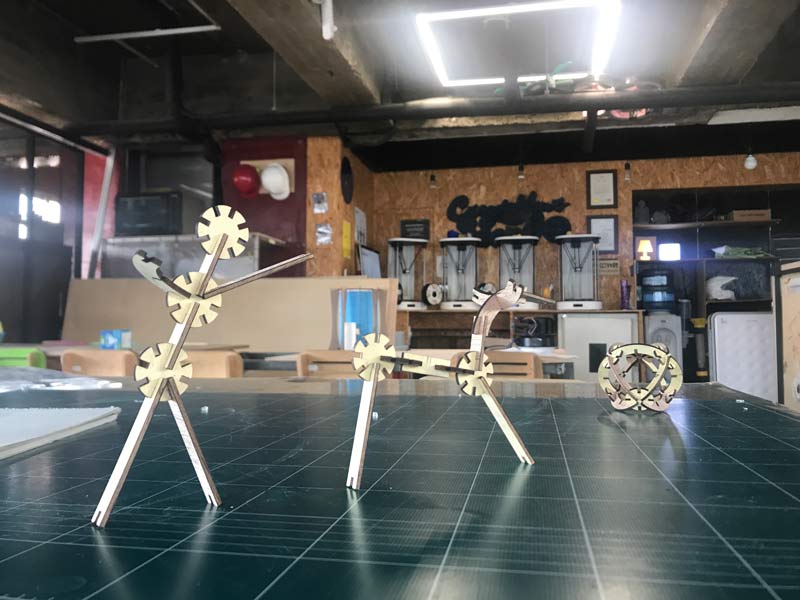
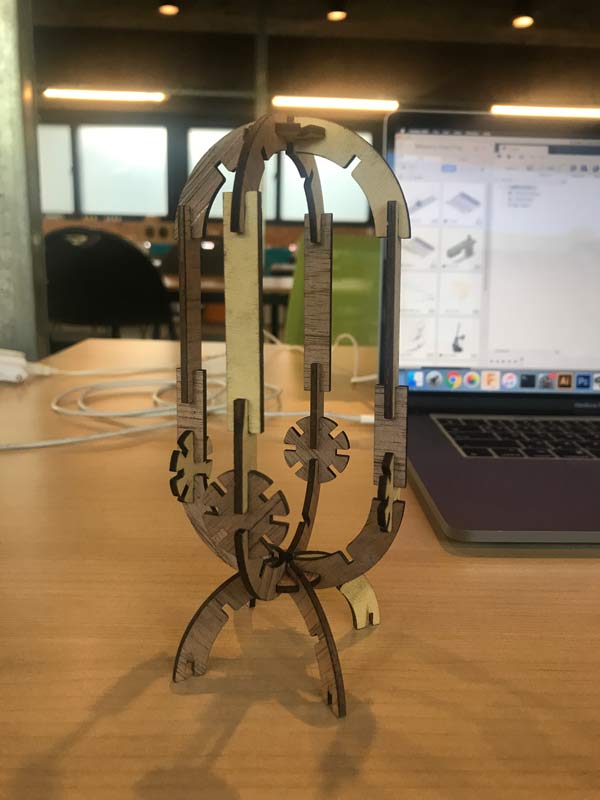
Troubles
The problems that I had before cutting, during cutting and after cutting.
- 1. didn't final check. so one slot is wider than the other.
- 2. the piece fell out during the laser cutting, and was burnt.
- 3. arc piece was hanging on during cutting, and was broken by the head as it was passing by.
- 4.broken while taking out of the board.
- 5,6. broken while disassembling.
EXTRA!!!
Here are some of the stuff I tried out using laser cutter.
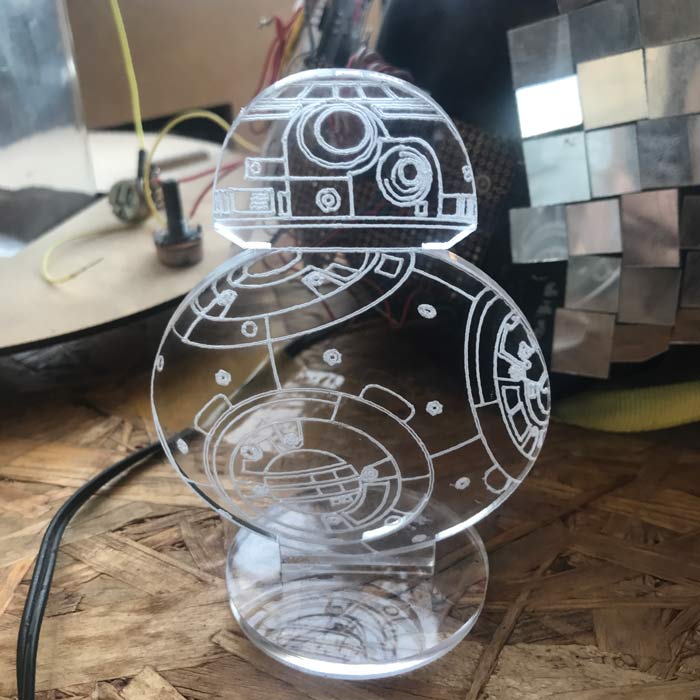
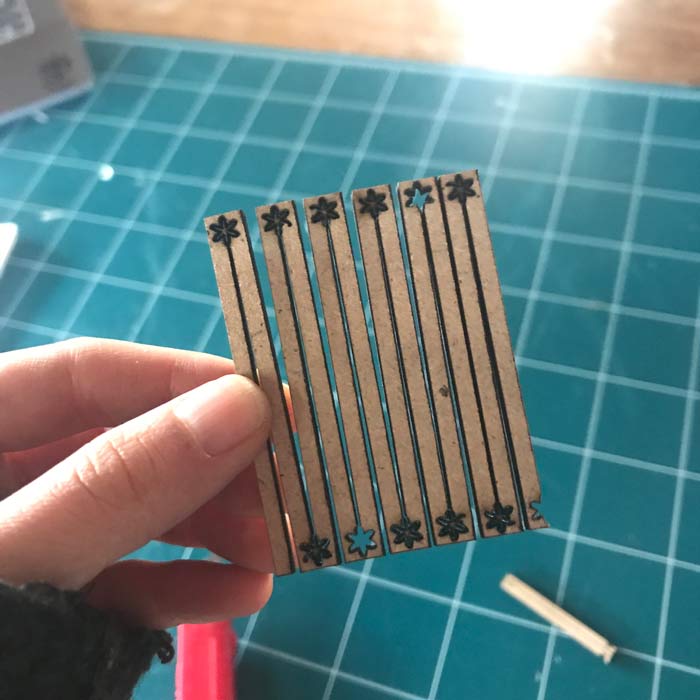
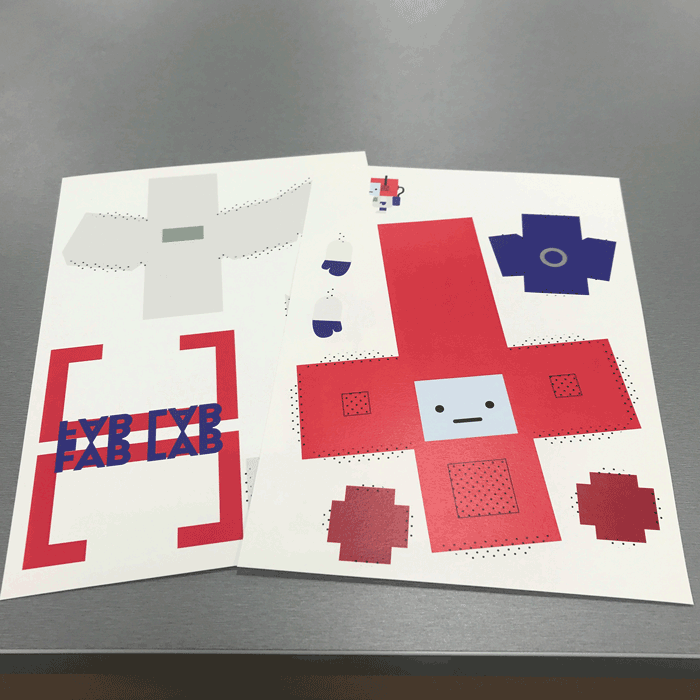
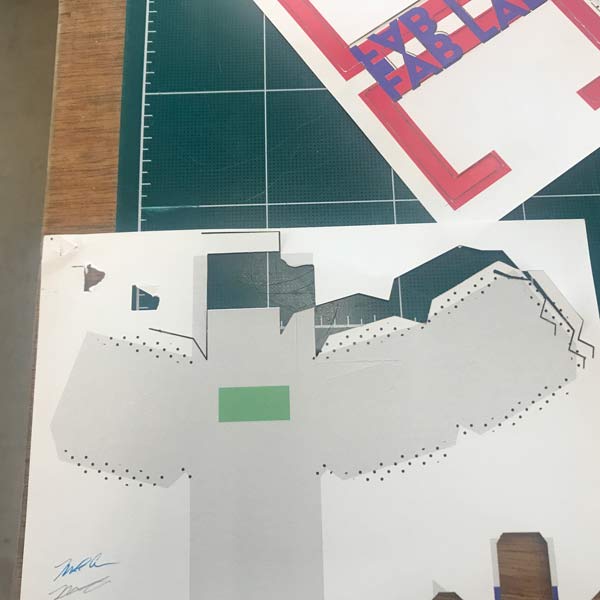
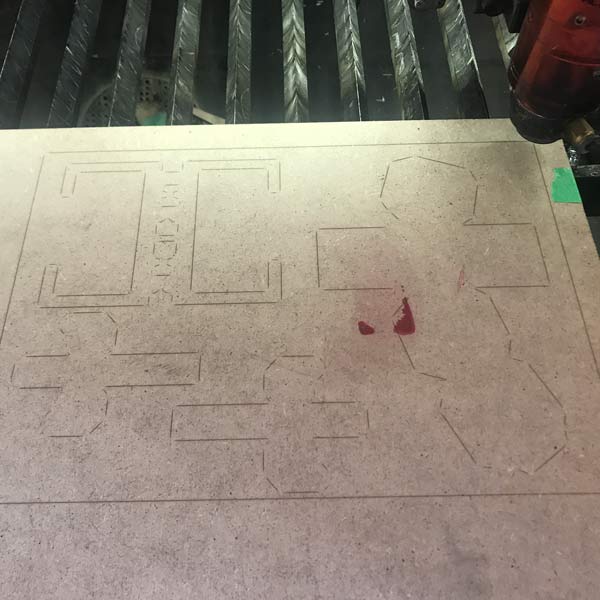
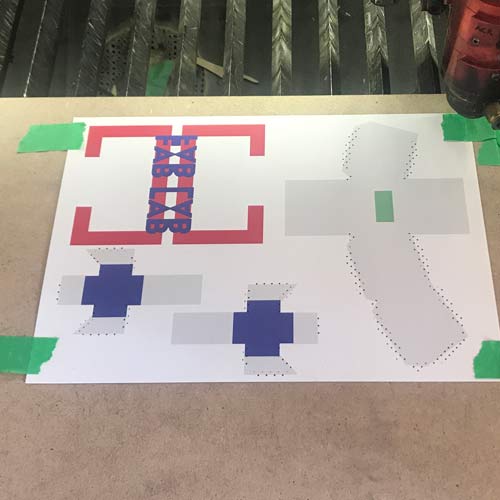
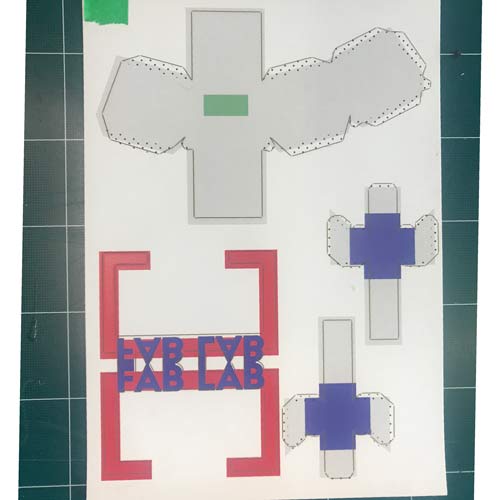
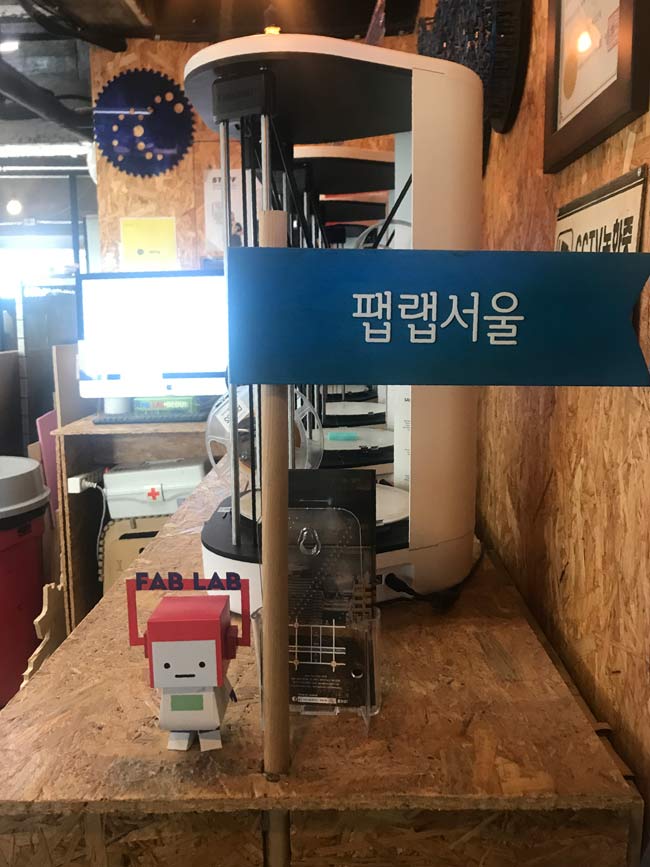