Giada Allocca
This is my website for the Fab Academy
Final result
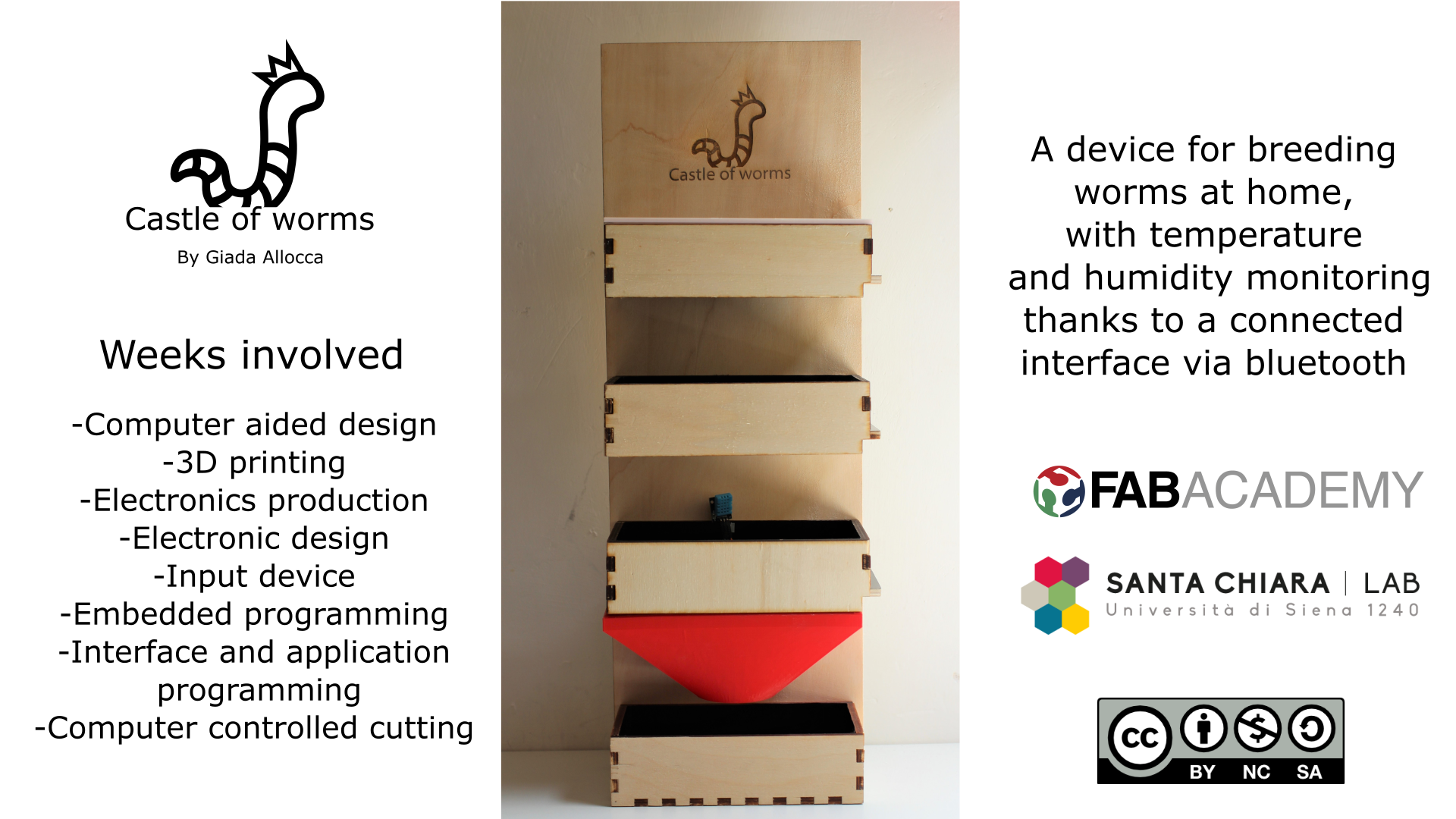
The concept
Since the delivery of the final project of my BA degree at University of Siena is approaching,
I chose to develop my thesis in human-machine interaction. My supervisor told me about an European project named PRIMA which might be a good opportunity
for me to get into the food and computing area and eco-sustainability, so I started researching on the subject.
These are the three main goals of the PRIMA project:
- Sustainable management of water for arid and semi-arid areas;
- Sustainable farming systems under Mediterranean environmental constraints;
- Mediterranean food value chain for regional and local development.
I found some articles presenting edible insects as a sustainable food of the future. Edible insect farming
could be a way to lower the emissions usually produced by other animal farms, and cut the costs compared to intensive breeding. However,
the adoption of such paradigm implies a deep cultural shift. In Western cultures, edible insects are not considered as a
sustainable alternative.
Schedule
Computer-aided design
Computer-controlled cutting
Electronics production
Electronics design
Input devices
3D printing
Interface and application programming
State of art
I searched projects about greenhouses for edible insects in the web and I found
The hive a sort of home for worms, a new way of
breeding insects and make them more accessible to the people.
Sketch
My final project consists in the development of a greenhouse for edible insects. I would like to develop an eco-sustainable
way of collecting, breeding and growing edible insects. Once the greenhouse will be developed, I would like to use the
prototype to provoke reflections and discussion on a possible future of food including and edible-insect-based diet.
I'll try to understand under what condition people would accept this perspective. Would and appropriate form, smell
or shape of insect-based food make it acceptable?
<
Update 15/04/2018
After some research I discovered that there are 17 species of edible insects, among these are the camole, an undemanding species that has three stages of growth:
larva, pupa and beetle. The three types must be separated to avoid canibalism, which is why breeders have come up with a drawers model that works in this way:
This gif helps to understand the process
So the new project will be more or less like this:
Update 09/11/2018
Thinking about a part of my final project I did not find a good solution to separate the pupae from the worms, so I did further research until
I found this very interesting image
Here you can see how they solved the problem, in fact the solution was simpler than I thought: the mechanism drop pupae and worms and let the
latters simply go away, passing to the box where they are collected to be eaten. So this is what my project will do: in the first box there will be the beatles which will mate
and make eggs. Below them I will put a network, so the box mate and the beatles will not fall into the box below, but only the eggs. To make the eggs fall down I will build the box so that the bottom is movable.
Moreover, the first box will have a perforated cover to let the air pass and prevents beetles from flying away. The eggs will pass to the second box where they will grow, then they will be moved to the third box (to allow the eggs of the first box go down to the second one). Under the third box there will be a sort of funnel that will channel worms and pupae into a dell, where the worms will come down and the pupae will remain. Now it is appropriate to move the pupae in the dell of the first box, so the cycle will starts again.
But who would use this product? Food consumption of insects and worms is still low in our part of the world, at the moment only elite chefs have started using them in the kitchen. Hoping to become the next fashion in the kitchen, this product could interest anyone who wants to have a healthier diet, without renounce the protein of meat but at the same time helping the planet not wasting water and not emitting CO2. Buyers can be families but also exotic restaurants.
After laser cutted the sides of the box I glued some wooden guides to slide the bottom. I finished the sides of the bottom with sandpaper to ensure smooth running.
Once the glue has dried I have finished the boxes with the vinyl sheet, in this way the worms can not climb to escape and I must say that even aesthetically it is not bad. Those processes was made for three boxes.
On Solidworks I made various parts of my project. This is a little dome where the beetles will mate and lay eggs. There is a dell at the top to accommodate the pupae and holes at the bottom to let the beetles enter. I was careful to take the measures to make sure it entered in the box. I printed 2 domes, one for the first box and one for the last.
Under the third box I thought to make a funnel that brings the worms into the dimple above the dome that will be in the last box.
The first box has a net to allow the eggs go down to the next box and avoid the dome fall down with the beetles. The network that I used is only representative, ideally the network should be more like a mosquito net. I placed the net above the guidelines of the movable floor.
I screwed the boxes and I made a hole with a column drill to allow the sensor wires to pass through and enter in the box. It doesn't matter that the tip is very large because the cables are small.
Then I took the measurements of the box that will contain the electronic part and cutted a small piece of wood that I glued in order to create a support where to screw the box.
I inserted the wires with the sensor and screwed the box with electronic components (and already programmed) inside.
Since the space above the first box is empty I decided to engrave a logo on my device. Initially I searched on internet for a captivating image of a cartoon-style worm and I immediately lasered it but I made a mistake: that image had copyright! Consequently I had to spend a good half hour erasing it with sandpaper. To avoid this kind of problems I personally create my logo with Inkscape.
In my project there is a humidity and temperature sensor, DHT11. I wanted to test it to see how it works and understand its features. The sensor has 3 pins: vcc, data and gnd and it works with a supply of 3-5.5V. I connected the data pin to the pin 2 of my arduino genuino uno.
I used the code in this page to check if the sensor was working right. Then I uploaded it on the board.
And then I opened the serial monitor. As you can see the sensor works properly
The next step is to read the sensor data via the bluetooth module. first of all it's necessary to set the bluetooth module as slave: connect the module through an FTDI cable and the enable pin to the power supply of 5V, then open the serial monitor on arduino ide and set the AT mode. You can see other way to program the bluetooth module in this page
Apparently the module is setted by default as a slave, so after made the AT command default the module only needs to be renamed to recognize it and connect it to the PC
This is the sketch to read the data from the bluetooth module to the pc.
Now it's time to create an interface. My intention is to create an interface that monitors the three drawers based on humidity and temperature. I found this tutorial on how to build a meter on processing, just what is right for me. I modified and customized it to my liking. To make this meter you need a separate library that you find in contribution manager on processing just typing "meter".
After adding the library I started making the meter. Further additions and modifications are possible thanks to the references found on this page
After deciding how to make the meter aesthetically I started to duplicate others and to place them in the window
And this is the final interface
Now it's time to send the data that the bluetooth receives from the sensor to the interface. To do this it is necessary to configure the access port so that the PC reads the input data and not the output, so go to the ->bluetooth settings to see what port is (in this case the COM 5) and when you add the module just select it as input.
For the electronic component I initially thought of networking among several boards, but having simplified my project I no longer need it, so I opted for a satshakit also to have the possibility of adding future implementations to my device. For the satshakit I looked at the documentation of Dario. Here is the schematic and below the board.
I must say that at the beginning the microcontroller worried me a bit with all those many pins close together, but in the end the final result I have to say is satisfactory
After programming the board I put it in the back box of the final project, which I screwed in to make it stable but also easy to remove. I created a hole to pass the thread.
During the presentation Neil pointed out to me that the components were not well fixed to the box and this could damage the wires and the various components, so I made supports for the board in order to protect it. For the bluetooth module I decided to simply glue it with double-sided tape. I must say that the result seems to be optimal.
I made some supports that included the use of screws for future modifications and therefore the possibility to remove the boards
Under suggestion of my global evaluator I decided to add another fabrication technique. I thought of adding the names to the boxes to distinguish the various functions of each part. For this part I used the vinyl cutter. First of all I made the PNG file on Inkscape.
Then I made the .camm file with the fabmodules with the right click of the mouse anywhere on the screen, then programs->open server program->Roland SRM-20->PCB png. The steps are the very similar to those of week 4, only this time the parameters to be changed are these:
Cutting Force: 70gf
Cutting Speed: 5 cm / sec
After saved the file I transferred it to the PC connected to the vinylcutter, loaded the vinyl sheet and set the parameters from the machine.
I removed the excess vinyl from the writings and put the transfer film on.
After that I applied the writings on the front of the boxes.
I don't mind the final result, even if the cut came out a little rough it gives an earthy imprint that is inspired by my final project.
Moreover, the first box will have a perforated cover to let the air pass and prevents beetles from flying away. The eggs will pass to the second box where they will grow, then they will be moved to the third box (to allow the eggs of the first box go down to the second one). Under the third box there will be a sort of funnel that will channel worms and pupae into a dell, where the worms will come down and the pupae will remain. Now it is appropriate to move the pupae in the dell of the first box, so the cycle will starts again.
But who would use this product? Food consumption of insects and worms is still low in our part of the world, at the moment only elite chefs have started using them in the kitchen. Hoping to become the next fashion in the kitchen, this product could interest anyone who wants to have a healthier diet, without renounce the protein of meat but at the same time helping the planet not wasting water and not emitting CO2. Buyers can be families but also exotic restaurants.
Hardware
The idea of the project is based on a sort of chest of drawers, the most used method by worm breeders. The structure will be vertically with 4 boxes: the top three will have a movable bottom that will be activated manually while the last one will have the function of collecting and base of device (to create stability). The first box will have a perforated lid. To get an idea of the final result I created an assembly with the various parts. I made the models with Solidworks
First of all I created the boxes, this is the one with movable bottom.
After laser cutted the sides of the box I glued some wooden guides to slide the bottom. I finished the sides of the bottom with sandpaper to ensure smooth running.
Once the glue has dried I have finished the boxes with the vinyl sheet, in this way the worms can not climb to escape and I must say that even aesthetically it is not bad. Those processes was made for three boxes.
On Solidworks I made various parts of my project. This is a little dome where the beetles will mate and lay eggs. There is a dell at the top to accommodate the pupae and holes at the bottom to let the beetles enter. I was careful to take the measures to make sure it entered in the box. I printed 2 domes, one for the first box and one for the last.
![]() |
![]() |
Under the third box I thought to make a funnel that brings the worms into the dimple above the dome that will be in the last box.
For the first box I made a cover with many holes for ventilation. Ideally the holes should be small enough to prevent insect from escape.
To make it I took the measures of the box and I made a little step on the corner to set it up.
The first box has a net to allow the eggs go down to the next box and avoid the dome fall down with the beetles. The network that I used is only representative, ideally the network should be more like a mosquito net. I placed the net above the guidelines of the movable floor.
I screwed the boxes and I made a hole with a column drill to allow the sensor wires to pass through and enter in the box. It doesn't matter that the tip is very large because the cables are small.
Then I took the measurements of the box that will contain the electronic part and cutted a small piece of wood that I glued in order to create a support where to screw the box.
I inserted the wires with the sensor and screwed the box with electronic components (and already programmed) inside.
![]() |
![]() |
This is the end result of the back
Since the space above the first box is empty I decided to engrave a logo on my device. Initially I searched on internet for a captivating image of a cartoon-style worm and I immediately lasered it but I made a mistake: that image had copyright! Consequently I had to spend a good half hour erasing it with sandpaper. To avoid this kind of problems I personally create my logo with Inkscape.
So this is the end result of the physical part.
Software
In my project there is a humidity and temperature sensor, DHT11. I wanted to test it to see how it works and understand its features. The sensor has 3 pins: vcc, data and gnd and it works with a supply of 3-5.5V. I connected the data pin to the pin 2 of my arduino genuino uno.
I used the code in this page to check if the sensor was working right. Then I uploaded it on the board.
And then I opened the serial monitor. As you can see the sensor works properly
The next step is to read the sensor data via the bluetooth module. first of all it's necessary to set the bluetooth module as slave: connect the module through an FTDI cable and the enable pin to the power supply of 5V, then open the serial monitor on arduino ide and set the AT mode. You can see other way to program the bluetooth module in this page
This is the first part where is described how to set the module, what pin must be connected and the baud rate. |
Those are the command to check if the module is connected and to reset the module so you can set the module with the desired function. |
This is the sketch to read the data from the bluetooth module to the pc.
#include#include int pinDHT11 = 2; SimpleDHT11 dht11(pinDHT11); SoftwareSerial btserial(10, 11);//bluetooth pin void setup() { btserial.begin(9600); delay(20); } void loop() { float temperature = 0; float humidity = 0; int err = SimpleDHTErrSuccess; if ((err = dht11.read2(&temperature, &humidity, NULL)) != SimpleDHTErrSuccess) { btserial.print("Read DHT11 failed, err="); btserial.println(err);delay(1000); return; } btserial.print((float)temperature); btserial.print(","); btserial.println((float)humidity); // DHT11 sampling rate is 1.0HZ. delay(1000); }
Now it's time to create an interface. My intention is to create an interface that monitors the three drawers based on humidity and temperature. I found this tutorial on how to build a meter on processing, just what is right for me. I modified and customized it to my liking. To make this meter you need a separate library that you find in contribution manager on processing just typing "meter".
After adding the library I started making the meter. Further additions and modifications are possible thanks to the references found on this page
After deciding how to make the meter aesthetically I started to duplicate others and to place them in the window
And this is the final interface
Now it's time to send the data that the bluetooth receives from the sensor to the interface. To do this it is necessary to configure the access port so that the PC reads the input data and not the output, so go to the ->bluetooth settings to see what port is (in this case the COM 5) and when you add the module just select it as input.
Electronics
For the electronic component I initially thought of networking among several boards, but having simplified my project I no longer need it, so I opted for a satshakit also to have the possibility of adding future implementations to my device. For the satshakit I looked at the documentation of Dario. Here is the schematic and below the board.
I made the Bom and then I soldered the board.
![]() |
BOM
|
I must say that at the beginning the microcontroller worried me a bit with all those many pins close together, but in the end the final result I have to say is satisfactory
After programming the board I put it in the back box of the final project, which I screwed in to make it stable but also easy to remove. I created a hole to pass the thread.
Update 17/06
During the presentation Neil pointed out to me that the components were not well fixed to the box and this could damage the wires and the various components, so I made supports for the board in order to protect it. For the bluetooth module I decided to simply glue it with double-sided tape. I must say that the result seems to be optimal.
I made some supports that included the use of screws for future modifications and therefore the possibility to remove the boards
Update 26-06-2018
Under suggestion of my global evaluator I decided to add another fabrication technique. I thought of adding the names to the boxes to distinguish the various functions of each part. For this part I used the vinyl cutter. First of all I made the PNG file on Inkscape.
Then I made the .camm file with the fabmodules with the right click of the mouse anywhere on the screen, then programs->open server program->Roland SRM-20->PCB png. The steps are the very similar to those of week 4, only this time the parameters to be changed are these:
Cutting Force: 70gf
Cutting Speed: 5 cm / sec
After saved the file I transferred it to the PC connected to the vinylcutter, loaded the vinyl sheet and set the parameters from the machine.
I removed the excess vinyl from the writings and put the transfer film on.
After that I applied the writings on the front of the boxes.
I don't mind the final result, even if the cut came out a little rough it gives an earthy imprint that is inspired by my final project.
Materials and costs
TOTAL: 47 eur |
Download the files