Week no.5
- 3D Scanning
- 3D Printing
Assigments :
- Group assignment: test the design rules for your printer(s)
- Individual assignment 1:
design and 3D print an object (small, few cm) that could not be made subtractively
- Individual assignment 2:
3D scan an object (and optionally print it) (extra credit: make your own scanner)
Group assignment
Since I started working at Insper FabLab I got my hands on a few 3D printers, the early ones were ultimaker v2. Now a days we have 3 compact Mousta and one Mousta Large volume, 4 GTMax printers and one brand new Zmorph v2.
For me, the path for a successfully 3D printed project is first to master a CAD software to create your own models. Then understand the basics of 3D printing, the mechanic of creating 3D objects by depositing layer by layer, this helps on creating support material on critical points and angles and help decide when to use it! Next step is to master at least two 3D slicing softwares like Repetier/Simplify3D/Cura/Voxelizer – the choice can vary depending on your printer. At last, understand minimal concepts of CNC manufacturing and G-CODE to know about referencing (zeroing) your printer.
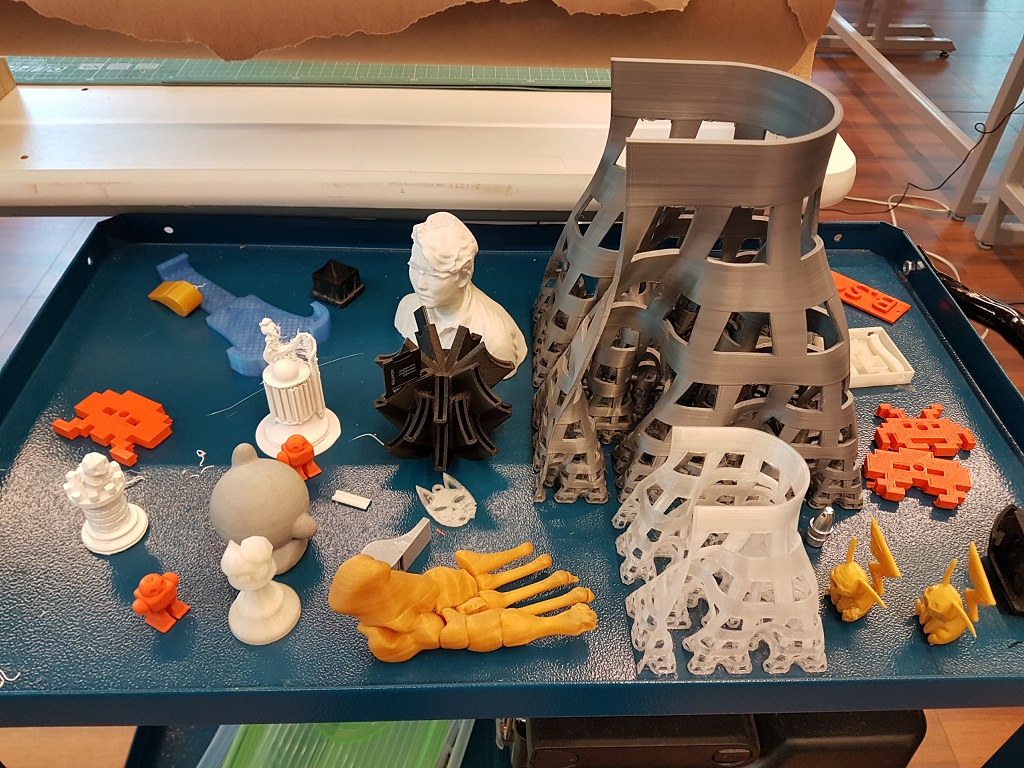
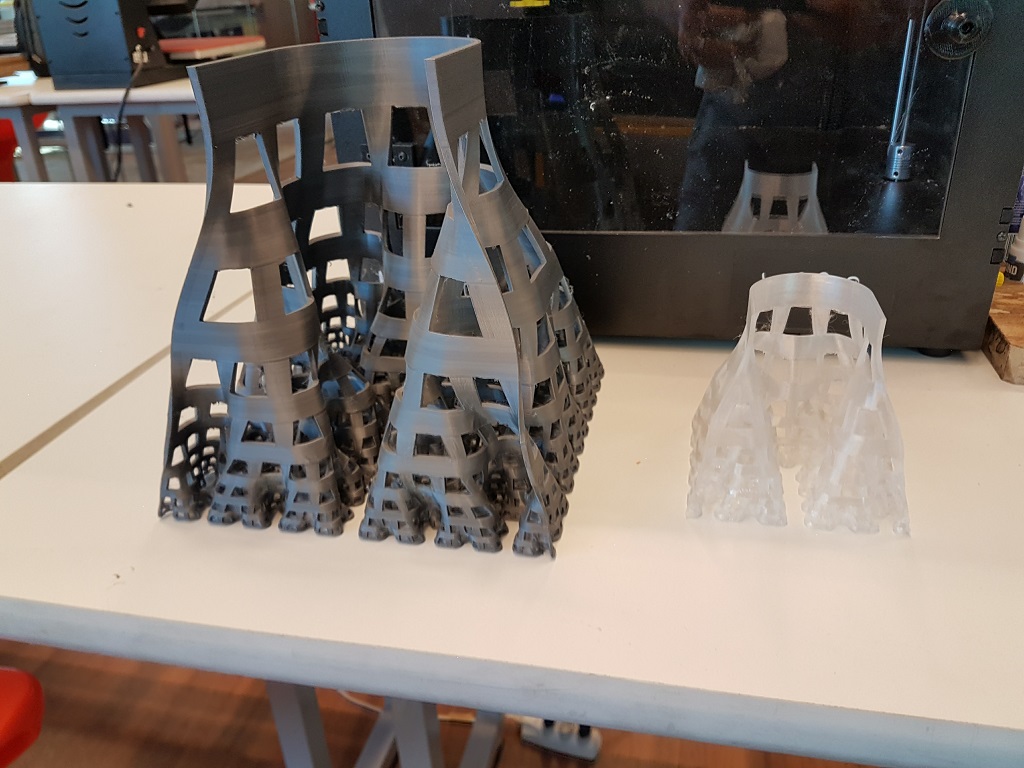
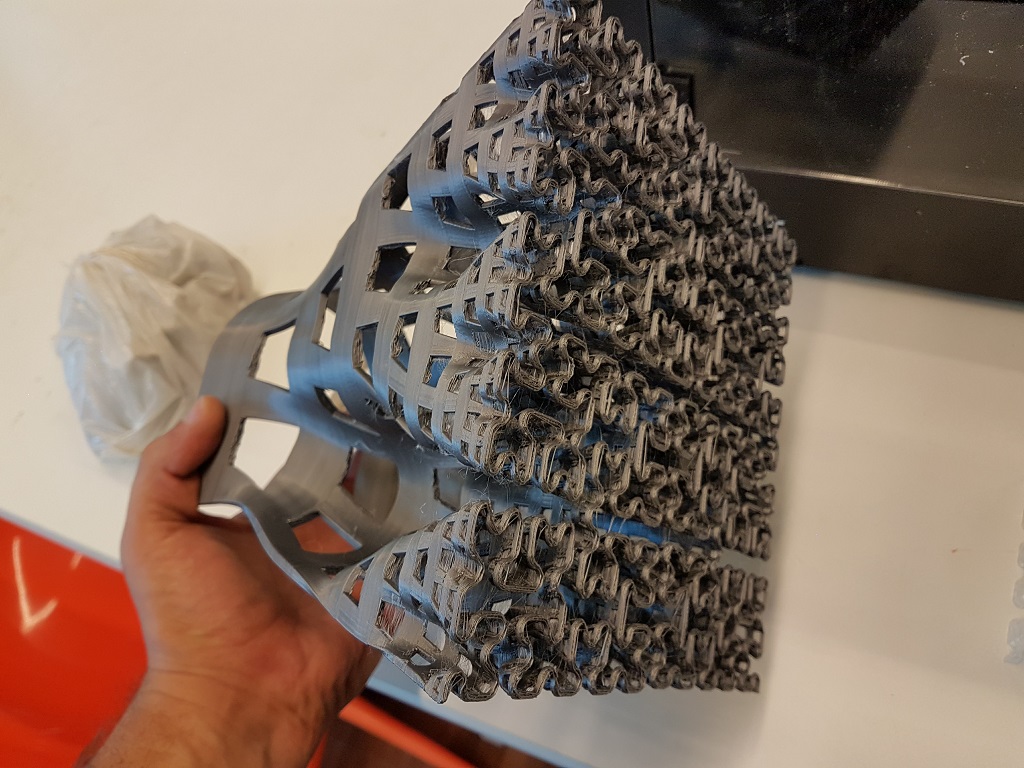
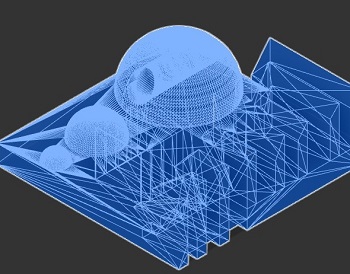
By an uncountable number of printing hours, we achieved a large display with printed parts that vary in size and complexity, some ABS, some PLA from 1.75 and 3mm filaments that came from our printer collection. As for the group assignment our mate Daniel Kras – Insper FabManager - led the documentation task on his website, a lot of information and hints from our tests can be found there as a Tutorial detailing print parameters for a test part.
For my individual exercise I choose to work with our new Zmorph printer with a brand new filament - Flexible PLA.
Object Scanning
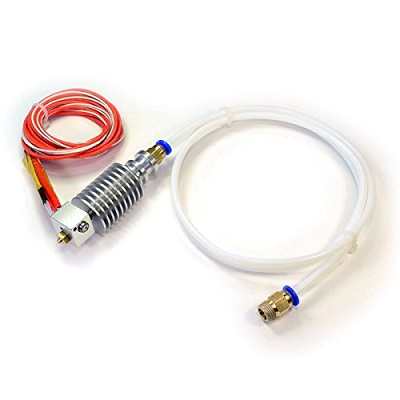
To my first scan test I used our 3DSystems Sense 3D scanner (1st. gen) and tried to scan a small object, mine 3d printer J-Head Nozzle for Bowden Extruder.
The software 3D Sense Scan is pretty simple and straightforward, I just followed his step-by-step guide that tells you what to do and how to move around your part. But mine first test was a failure, the part was too small. The cooling fins happened to be too much detail for the scan, even though I have improvised a contrast background with my work jacket.
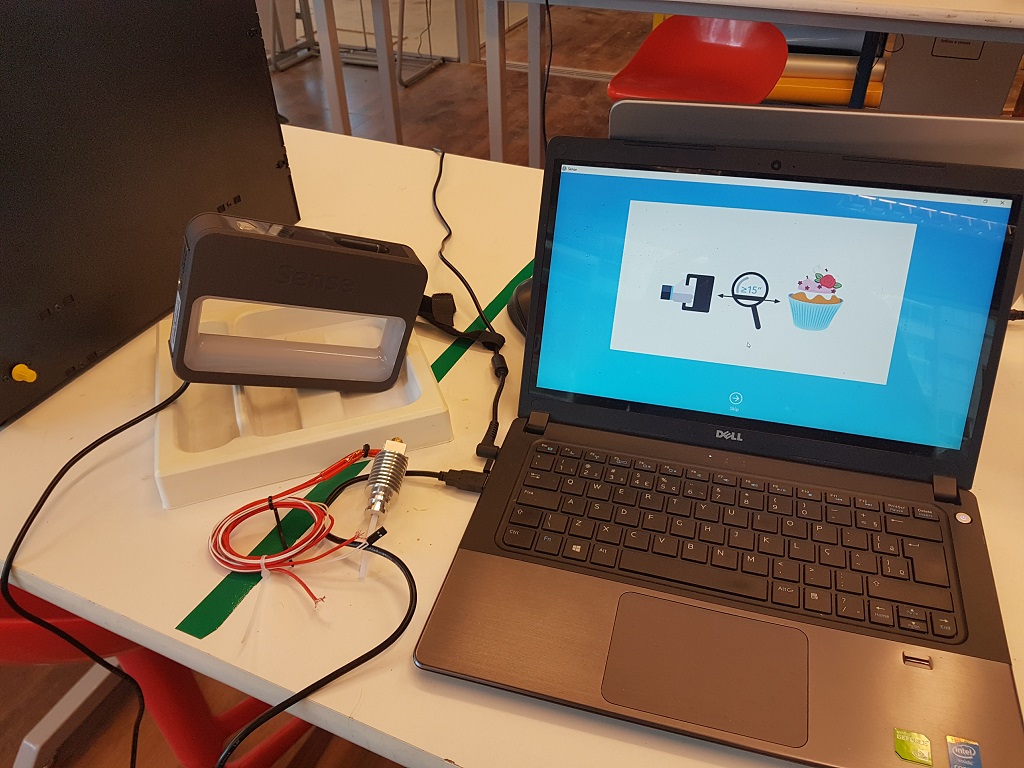
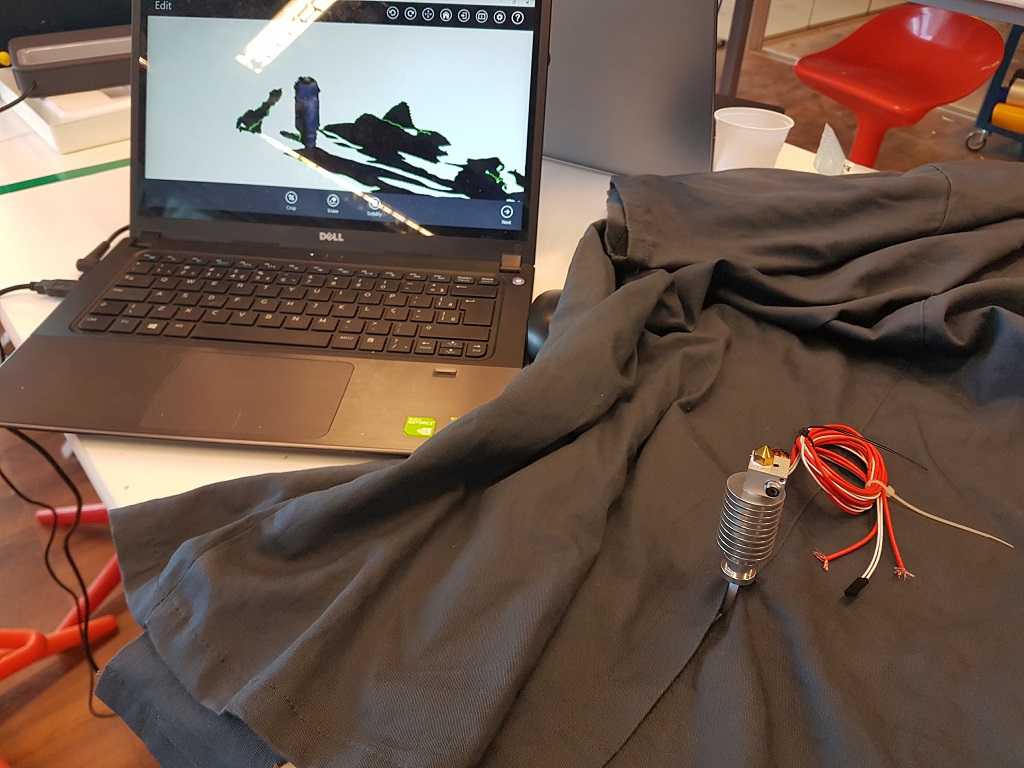
Moving on to test two, I couldn’t miss the chance to make a scan of myself, it was a lot of fun. For that I managed to get help from a colleague Pelicano and with a lot of patience we get the job done, the scanner was always loosing track. After that, I still spent considerable time to fix the 3D model and repair some mesh holes in sense software. But the final result was really neat!
And here is the browser rendered STL file off me:
Individual Assignment - Print an Object (part 1)
So I took the stl file of my self-scan and loaded into the Voxelizer that is the official software supported by the Zmorph manufacturer. Started with the custom configuration for 3mm PLA, just slowed down the printing speed and run it for the flexible PLA material.
But my first try was no good, the default raft support material was insufficient to hold down my relative big part making it loose contact with the bed on early printing stages (first 15min. of an 8h print). As I discover that this filament, by his flexible property, it retracts and fledge more than usual PLA loosing adhesion.
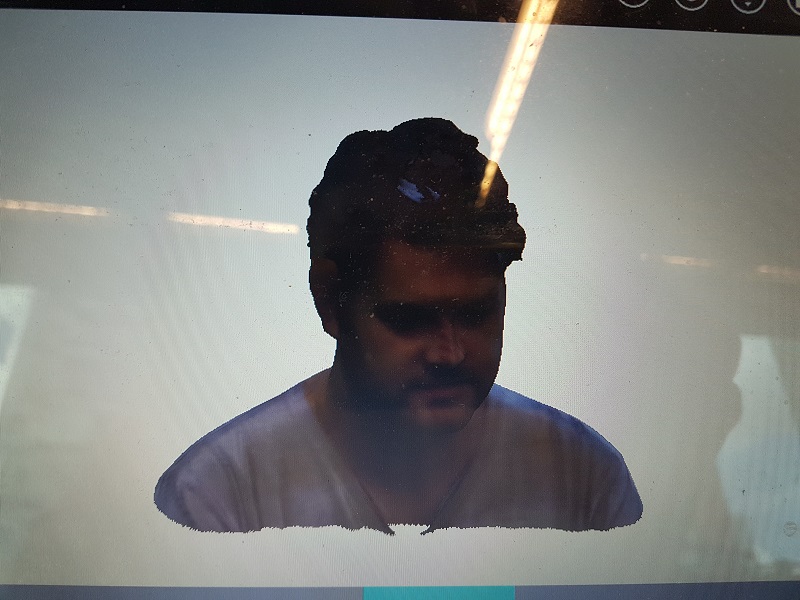
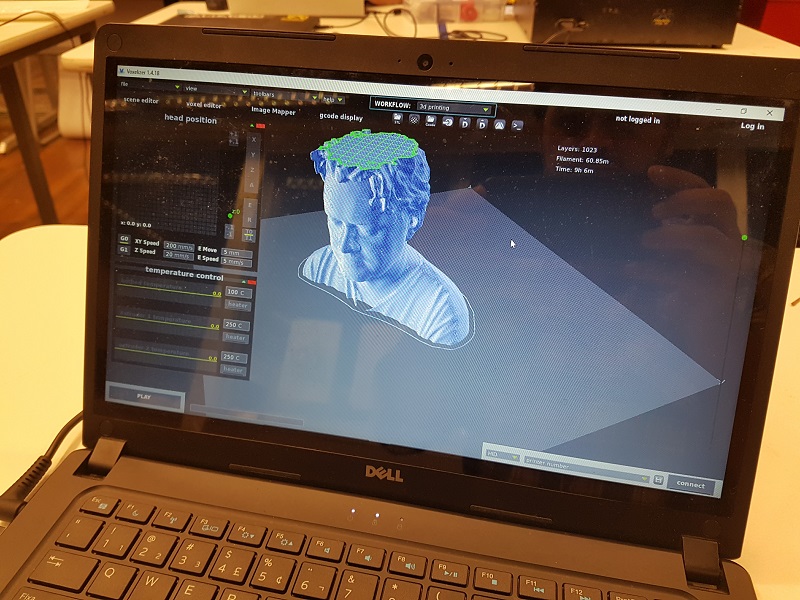
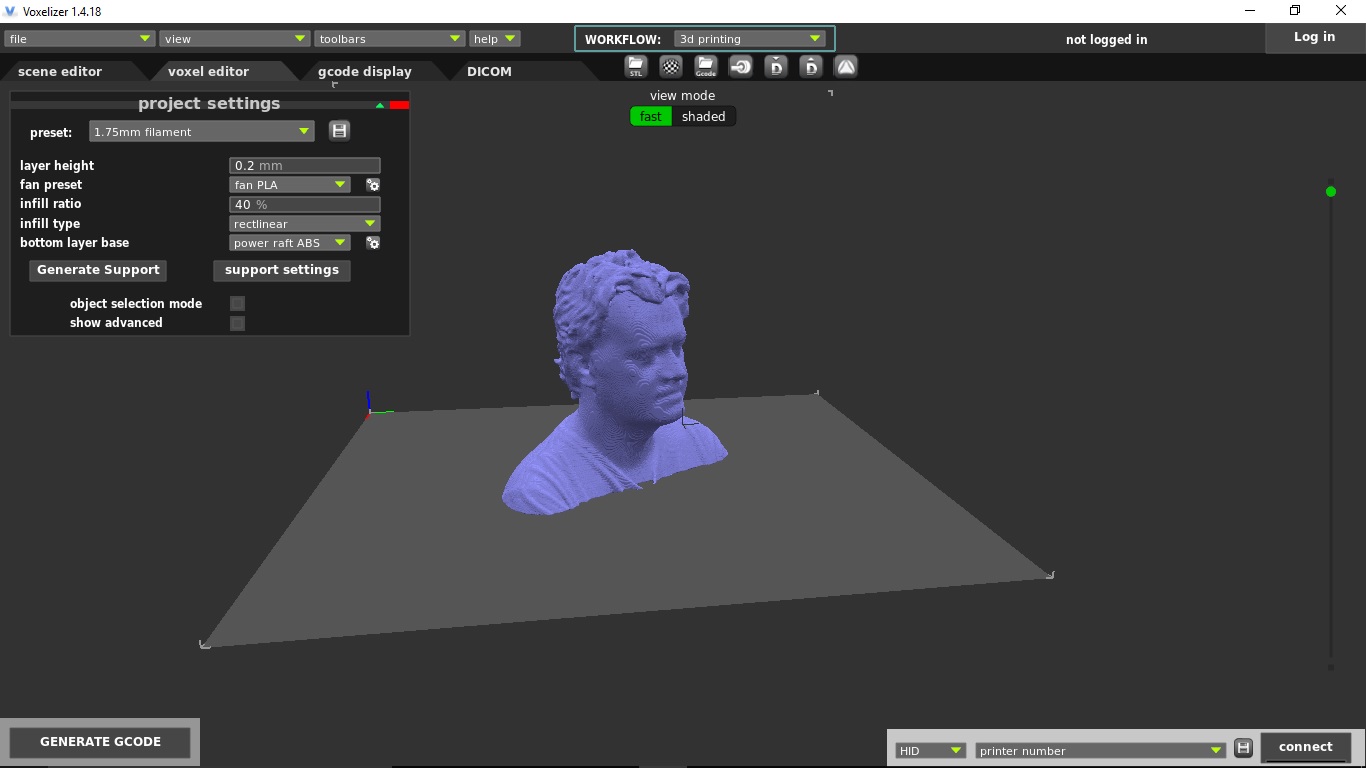
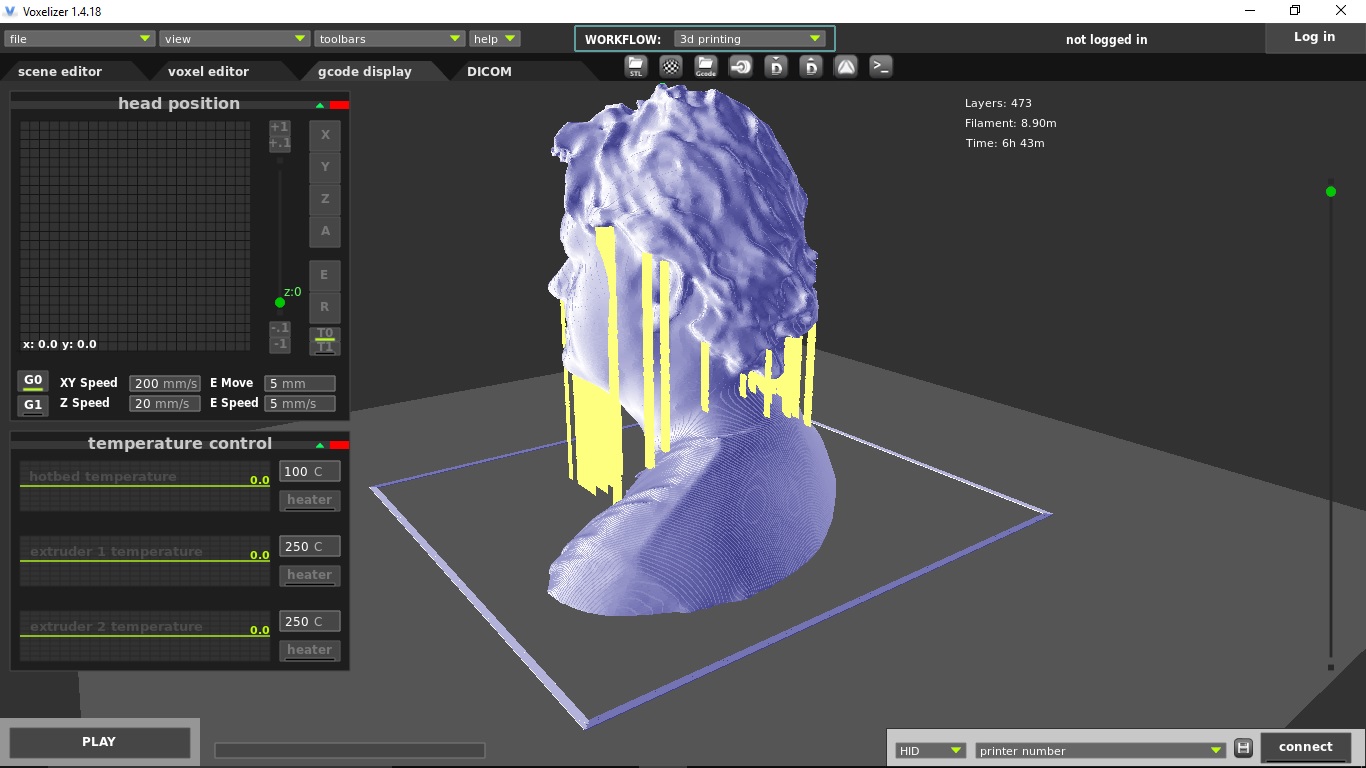
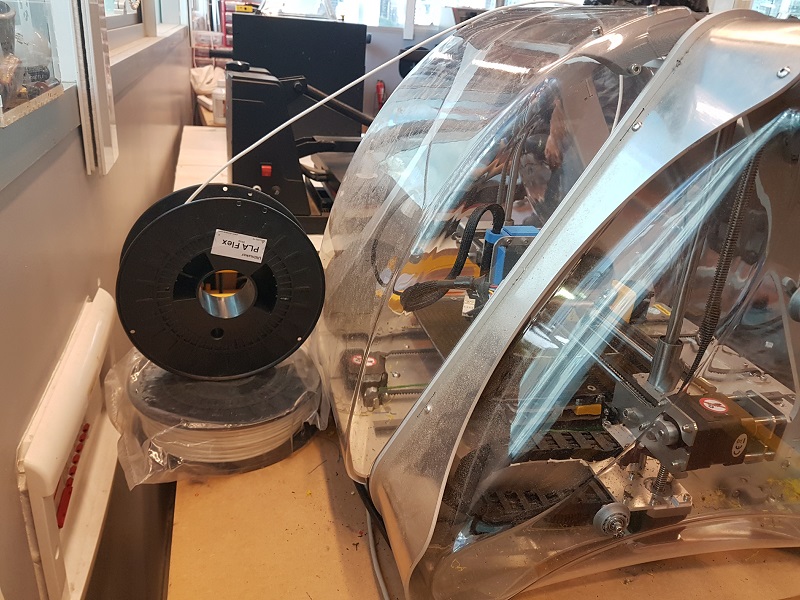
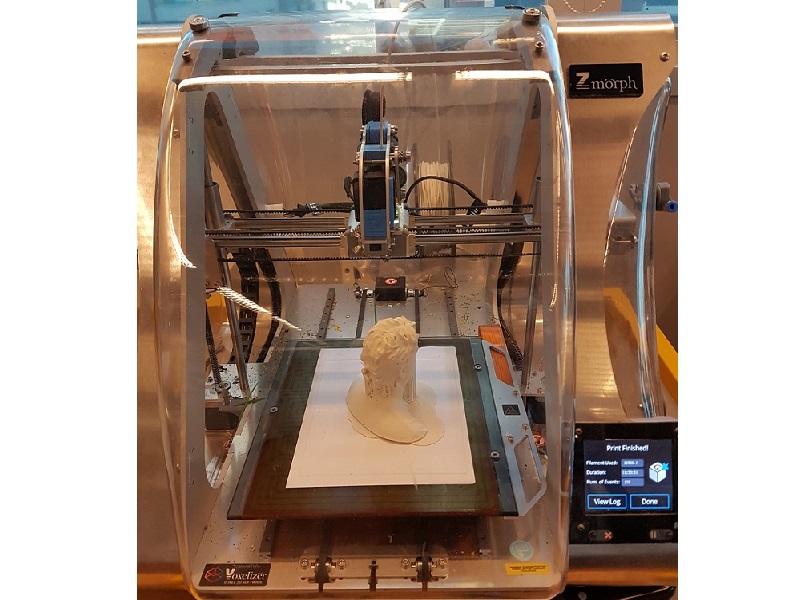
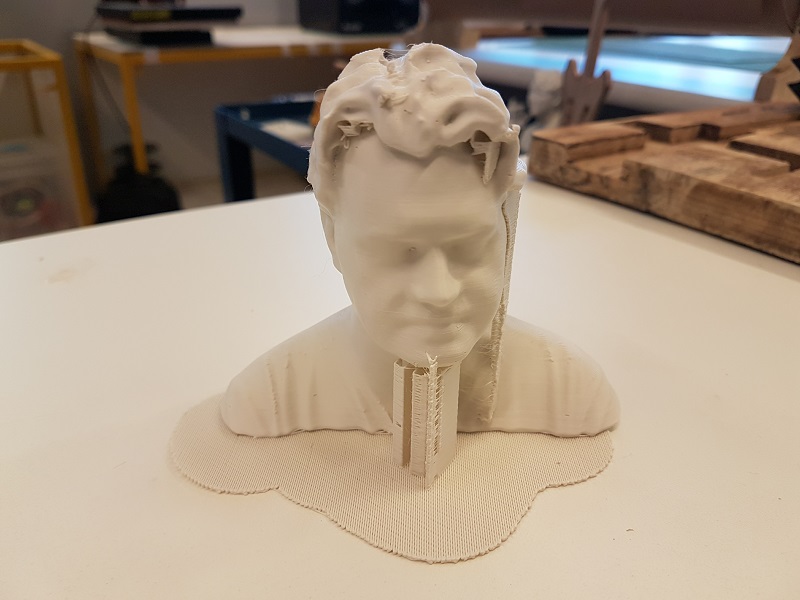
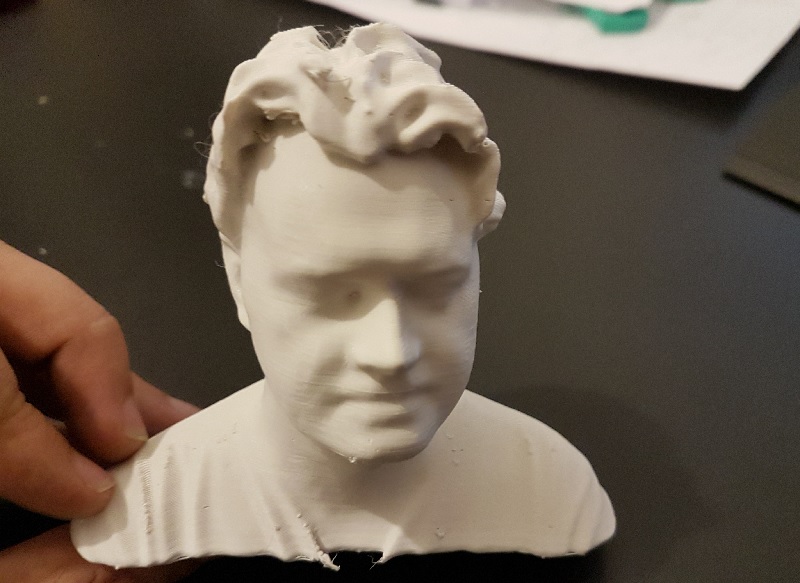
I went back and adjusted some parameters in the software: create a Power Raft, raised the bed temperature to 70ºC, slowed down the first layer speed to 40%. Also glued a white paper to the HeatBed to help holding things on. Parameters adjusted in the software Voxelizer, it delivered a beautiful print, with a mate effect and a soft touch.
What I liked most is the fact that this print could not be done in any subtractive machining method. Maybe you could mill a similar part, but it requires a 5-Axis Mill at least. Some detailing in the hair and lots of negative angles make it very hard to machine. If you consider the obtained part, it is actually hollow (infill of 40%), is impossible to make it that way by any other subtractive process.
Individual Assignment - Print an Object (part 2)
I wanted to try a different printing technology, and since my final project is a 3D printer I wanted to investigate also the heat transfer on my Printer nozzle !
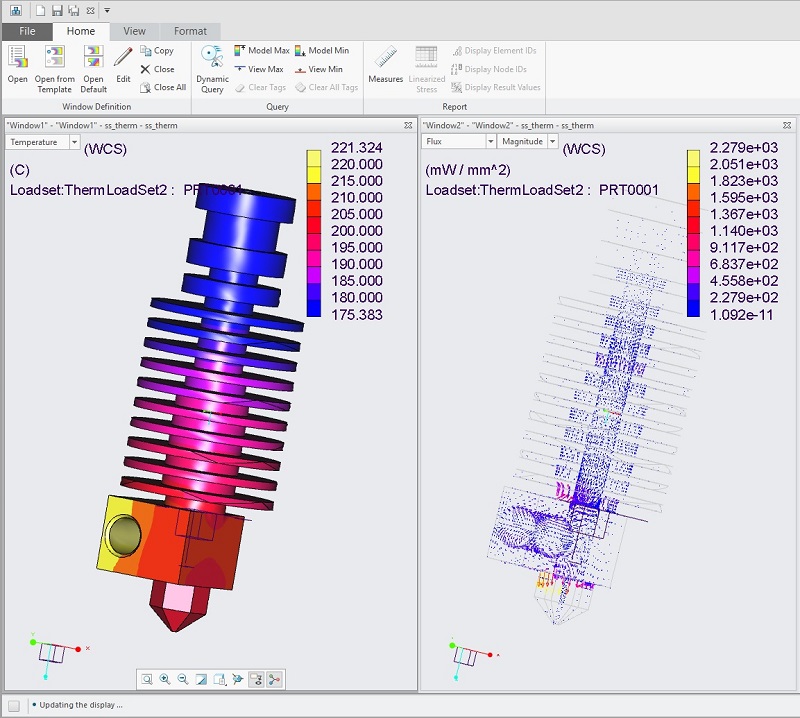
Since my Nooze scan didn´t worked as expected, I modeled it in 3D using Creo Parametrics and ran a Heat transfer Simulation for a full Aluminum body and a Heat element of 40W. The goal was to produce a colorful 3D ".wrl" file representing heat transfer in a 3D printing.
The resulting file was sent to print in our 3D systems Project 460Plus. It uses a technology that produces full color plaster parts, that in this case represents a FEA analysis. An interesting study case !
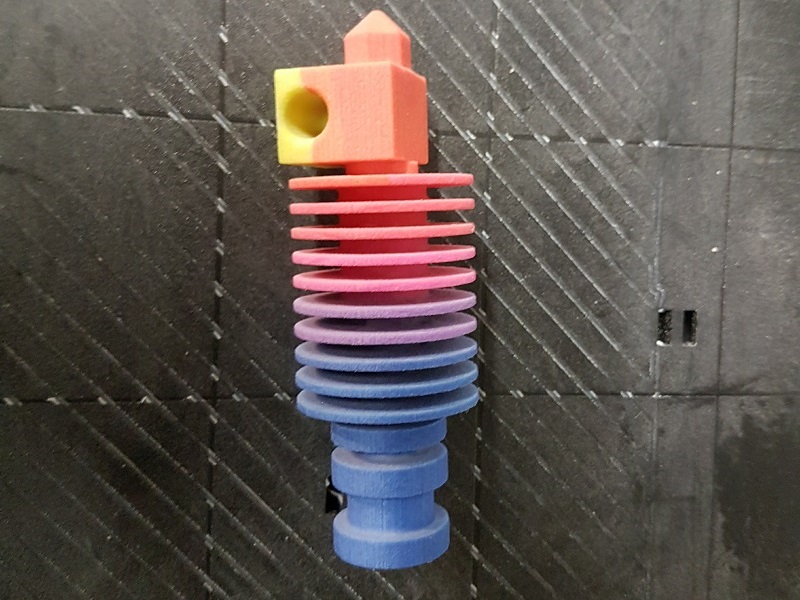
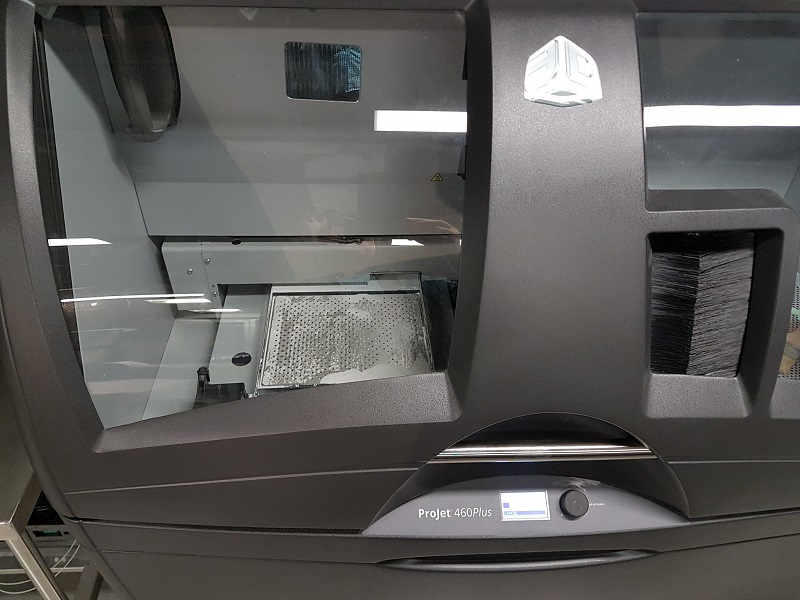
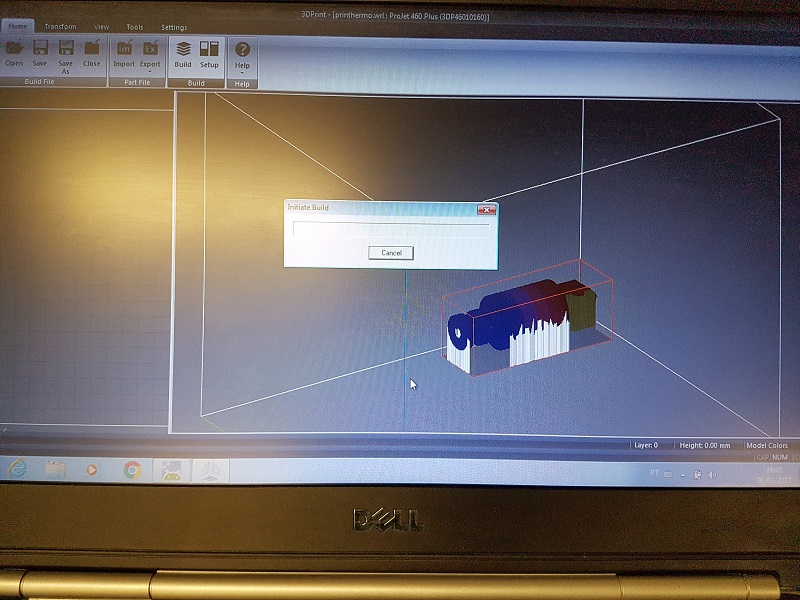
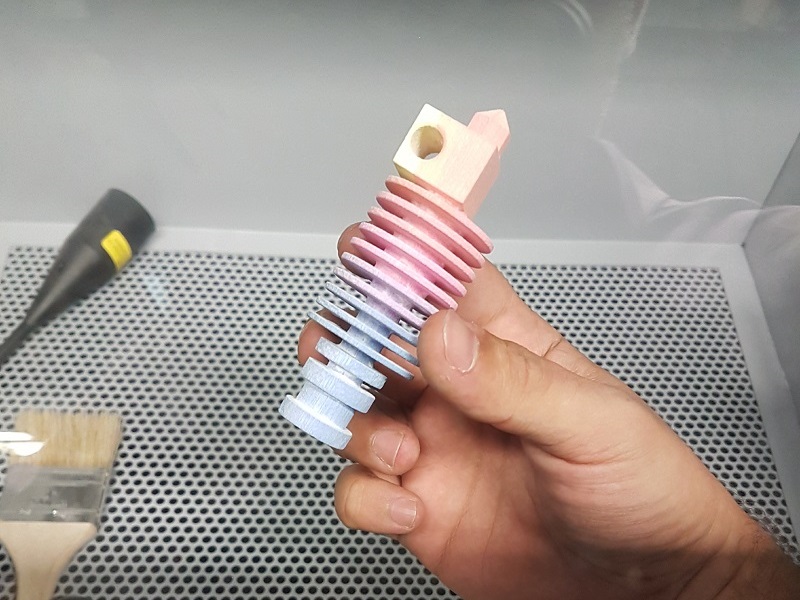