Week no.17
- Applications and Implications
Assignments :
- Propose a final project that integrates the range of units covered
- Projects can be separate or joint, but need to show individual mastery of the range of skills covered
- Where possible, you should make rather than buy the parts of your project
The KryvoDelta 3D Printer
The datailed documentation can be found at my Final Project.
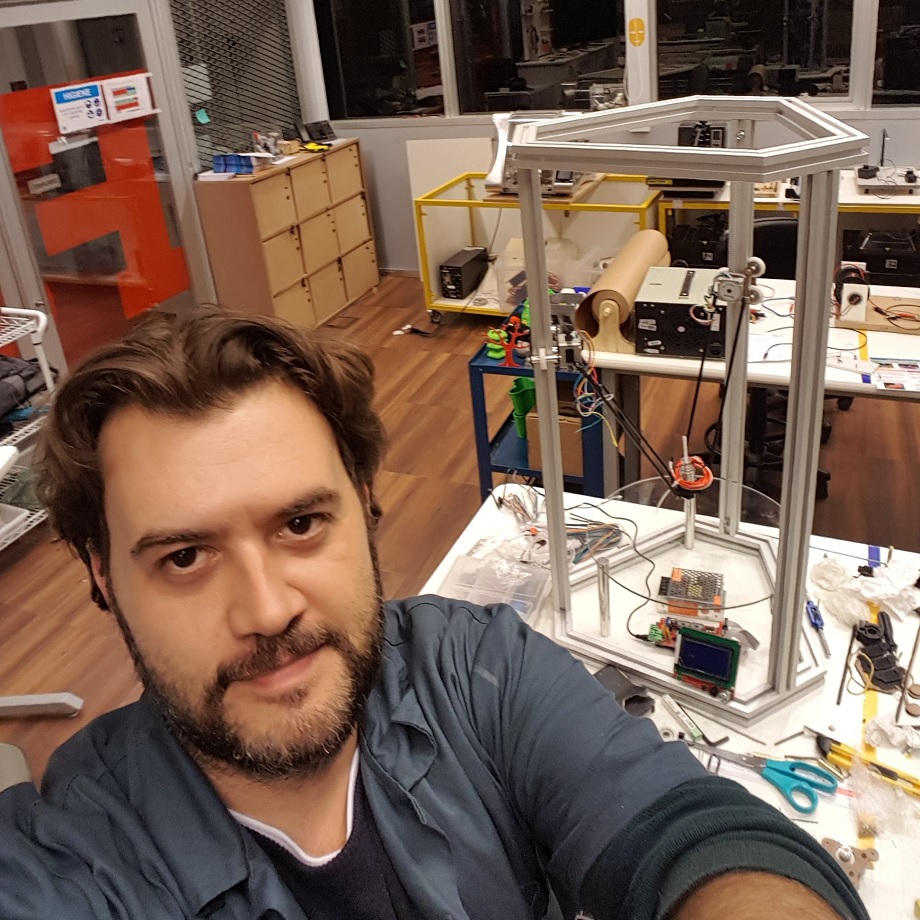
- What will it do?
- Who's done what beforehand?
- What materials and components will be required?
- Where will they come from?
- How much will it cost?
- What parts and systems will be made?
- What processes will be used?
- What tasks need to be completed and wat questions need to be answered?
- What is the schedule and How will it be evaluated?
What will it do?
The final project proposal is to build a Machine from scratch, more specifically a Delta style 3D printer.
The printer will have improvements related to size (Large!) and the movement mechanism, aiming to be resourceful, open source and low cost (less parts) machine.
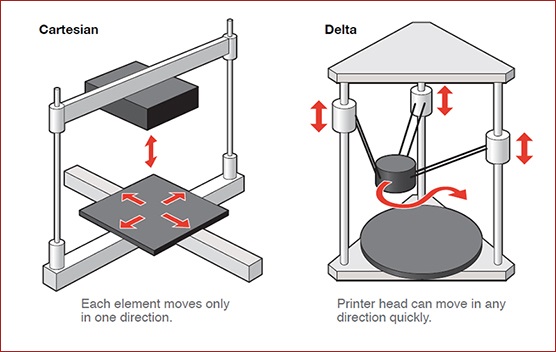
Who's done what beforehand?
There is an extensive development in 3D printers from the last few years, a countless number of designs and documentation can be found on internet.
What is most interesting is that a large and active community has emerged on the topic, providing plenty of resources for open and collaborative development.
Also some popular, low budget and reliable Delta models like SeeMeCNC Rostock MAX, FLSUN 3D Metal Frame Kossel Delta and He 3D – Mega Delta 3D Printer inspired the development of my Design.
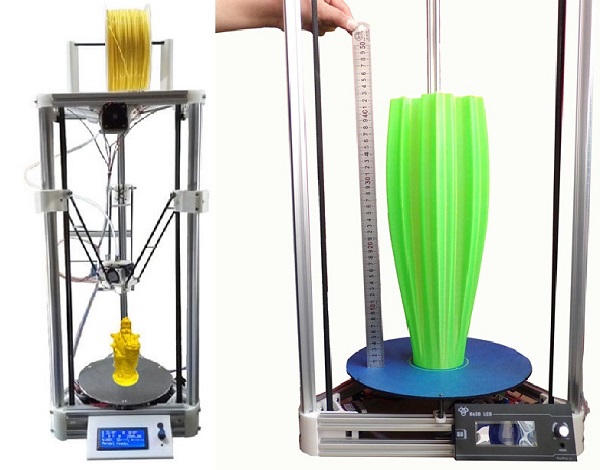
The major upgrade I designed is a Direct Drive coupling for the linear motors movement, I couldn’t find any previous reference for a delta printer using this strategy.
Apparently it´s the first Direct Drive Delta Printer!!
What materials and components will be required?
I have first made a full CAD Design that generated a complete Bill of Materials (BOM) for the Delta parts. This materials is detailed in my Final Project section.
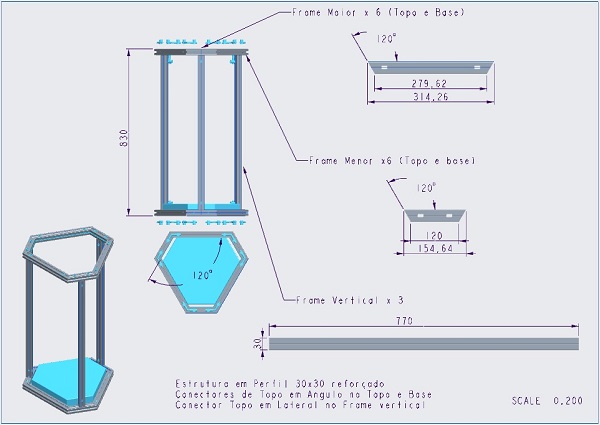
Where will they come from?
Since the goal is to make an affordable and replicable machine I choose components largely available like an Arduino Mega for central processing, Ramps 1.4 and Nema motors for movement and common aluminum extruded profiles as structural components.
Here in Brazil all electronic parts need to be imported, as price matters, they all came from China suppliers. But all the mechanical/structural parts are from local industries.
How much will it cost?
Here in Brazil we face a costly supply chain with crazy logistics and heavy taxes, with have a huge impact on final price especially for machines parts.
But he results are quite interesting, a fused deposition modeling (FDM) 3D printer for the final consumer starts from R$6.000 (~U$ 1800) from local manufacturers. One traditional MakerBot Replicator Mini prices R$9.000 (~U$2.600)!!
It’s a work in process, but I managed to make a simplified costs table (so far!) and the brute price (only materials not counting machine, tools and manufacturing time) are orbiting the R$1.000 (~U$ 300) price tag.
Worth remembering it´s a large size printer, detailed pricing at my Final Project section.
What parts and systems will be made?
As for the make-or-buy choice, I designed and made all the subassembly parts for the new Direct Drive system, including the pinion, aluminum profile mills, rollers, motor fixtures and linear guides.
Also manufactured custom parts for all structure, end effector arms and casings to attend it´s nonstandard large size.
An electronic system was also made from scratch to control the heated Bed including milled circuit boards for the power mosfets.
What processes will be used?
The processes I used were:
- 3D CAD and CAM software (3D assembly and manufacturing);
- 3D printing (effector, end-stops support)
- CNC machining (mill and lathe for Direct Drive system),
- Lasercut (Interface case),
- Electronics design and production (Heat Bed control)
- Programming (interface).
What tasks need to be completed?
The Direct Drive worked as a prototype, but I need to redesign the motor support to reduce some angular gap that sometimes jammed the system.
This was the greatest problem I faced, it also prevented me from calibrating the printer, another latter task to be completed as well as print the first part (of course!).
What questions need to be answered?
- Will the Direct Drive prove to be a feasible solution ?
- Will it be precise and reliable ?
- Can it print a large scale object (with quality) ?
- What will be the final parts cost (prototype)? And what would be the price for production?
What is the schedule?
This is a personal project of mine, it will run beyond the FabAcademy Schedule. The next goal is to fix the problems and get it printing until the end of July!
How will it be evaluated?
Simply put, it needs successfully print a large part with minimum quality!