Computer-Controlled Machining.
For the assignment of the 8th week: Computer-Controlled Machining, it will be divided into 6 differentiated parts: Design, Fabrication, Assembly, Problems, download files and group assignment. The goal of this week it is create something BIG.
Desing
My idea for this week is to create a shelf that can be scaled to have different levels, ideal to take advantage of some free space you have at home.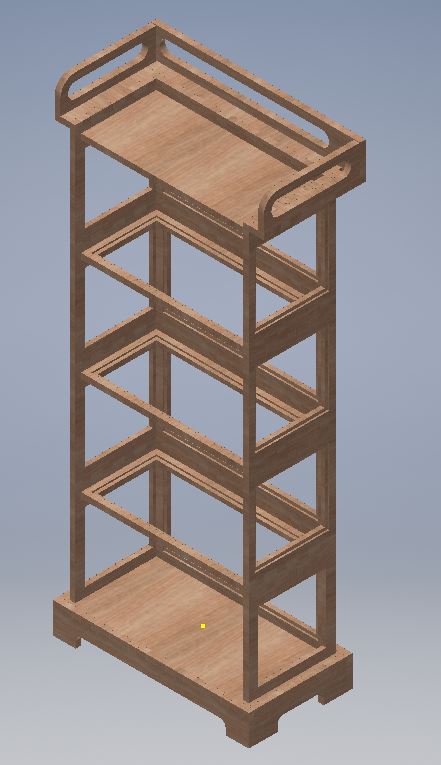
It will be divided into three main parts:
- Base Here will be the legs of the shelf.
- The body This area can be increased depending on the space needed
- The final part It will have some small ornaments where you can hold in case you want to move without disarming it
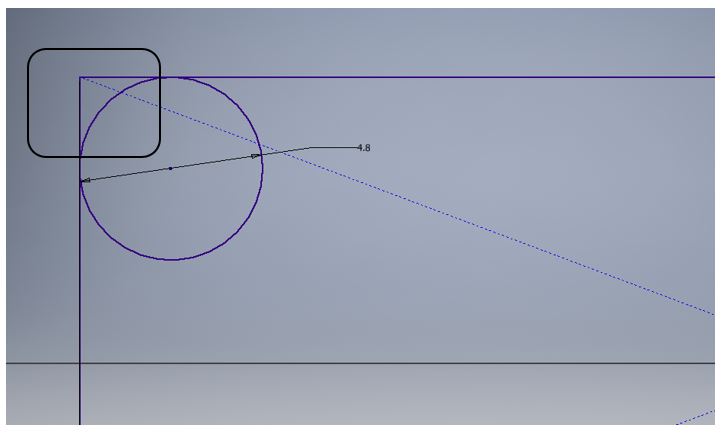
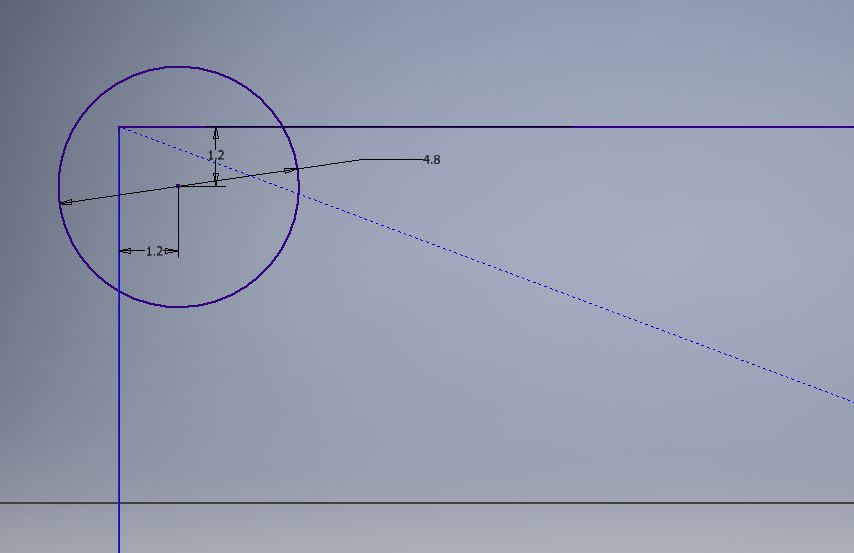
Base
The base consists of a table as a base and the front and side legs, as shown in the picture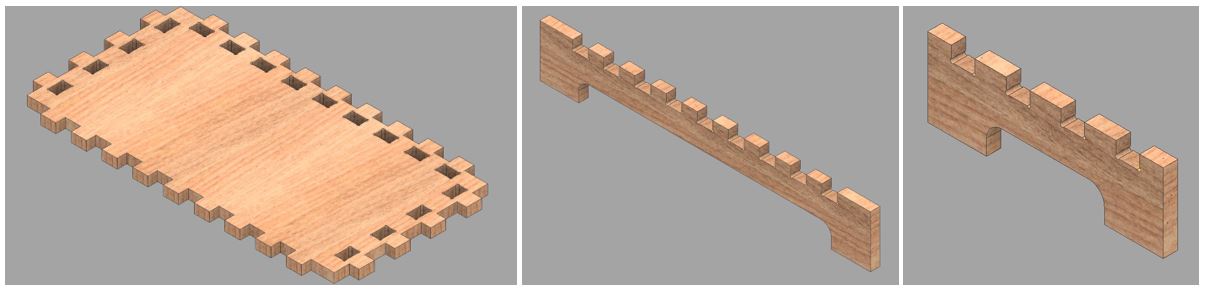
Central
For the central part, which is the modular zone, it is composed of 4 parts: left side, right side, base and back side, as you can see in the picture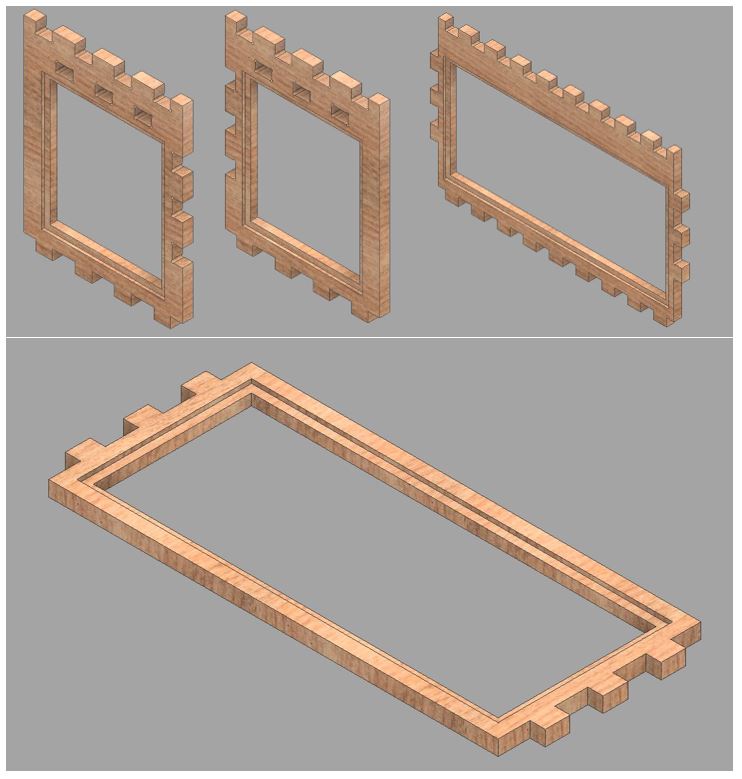
Final
For the final zone, two pieces of the central zone and additional pieces are used, as shown in the figure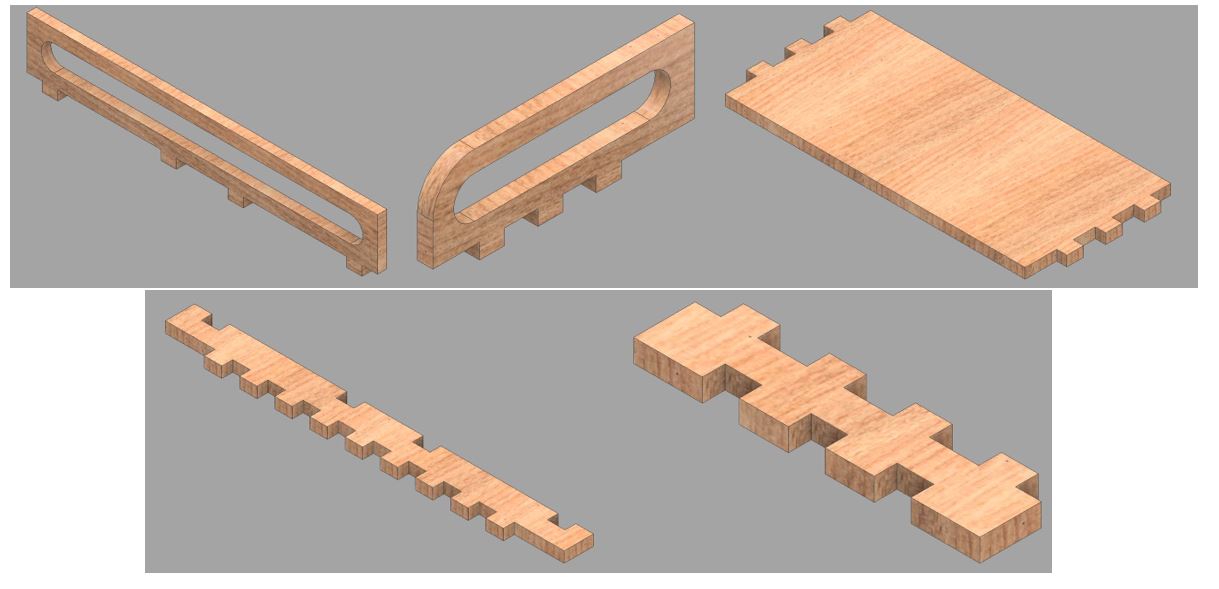
The material used is plywood is 18mm, after some tests carried out in group work, which will be seen later, this material does not need a tolerance in the inserts, as was done with the cardboard in the laser cutter.
Fabrication
The machine
In the lab, we use the CNC Multicam 3000. This machine is a CNC router that allows making 2D cuts in wood, plywood, MDF and other raw materials to perform, generally, carpentry work.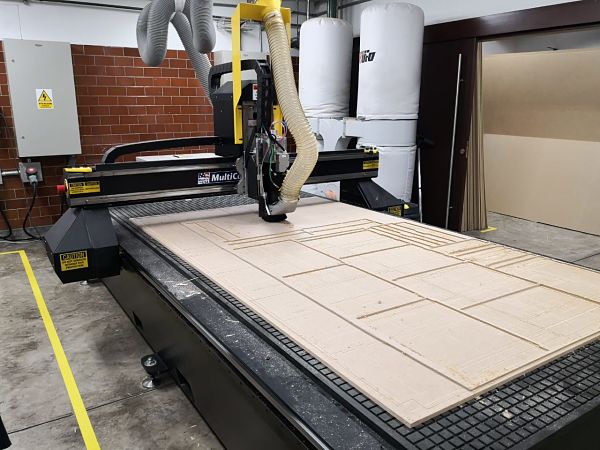
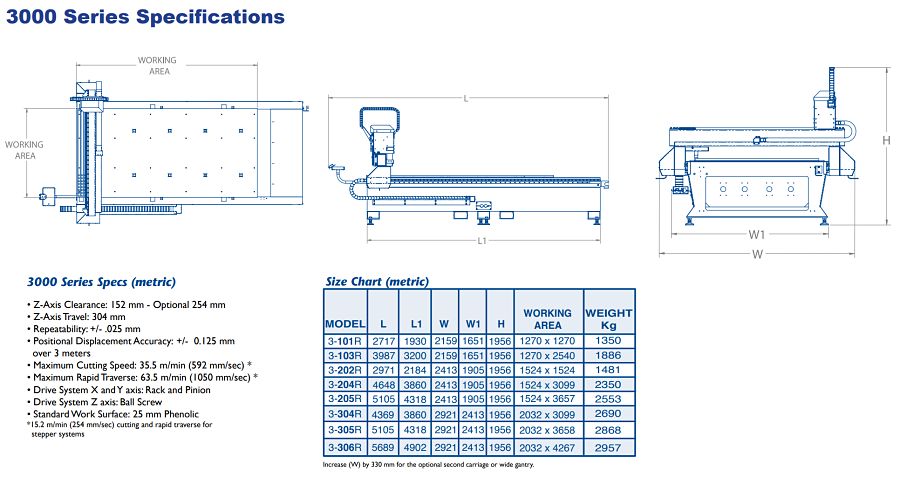
Source: https://www.multicam.com/3000-series-cnc-router/
An important characteristic of the Multicam is the vacuum that is produced in the work area, this is done to avoid that the material being cut does not move. However, in some occasions it is necessary to screw the material into an additional wood and in this way make sure that the material will not move.You can read more about the machine here (https://www.multicam.com/3000-series-cnc-router/)
Security protection: Personal Protection Equipment (PPE)
When working with wood, it is very important to work with the necessary safety elements to avoid accidents during work and in the long term. Many of the particles that are suspended in the air can be carcinogenic, so it is necessary to wear lenses, gloves, respirators,earmuffs, work clothes, safety boots and to be in the safety zone while the machine is in operation, this area we have it delimited by a yellow line on the ground.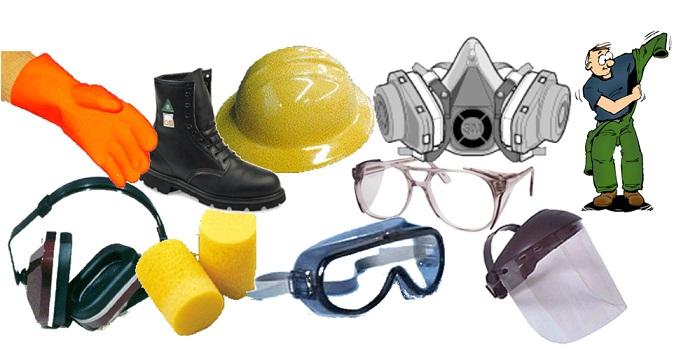
Source: http://www.abodana.com/personal-protective-equipment-market/
Test the machine
A good way to make an optimal design, is to know the limitations and operation of the machines, in this case I made some designs for its cutting and testing.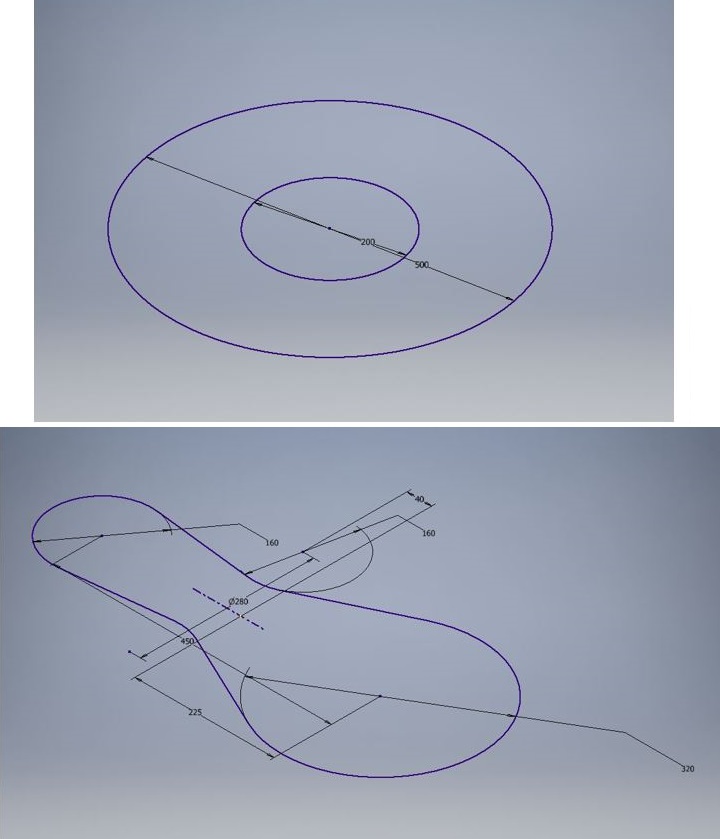
The tools that are used are the 3/16 "and 1/2" endmill. The material used is plywood because it is a resistant and quite economical material. For this task they recommended us to use it because it is the most abundant material available in the laboratory.
After the cuts we have the following results.
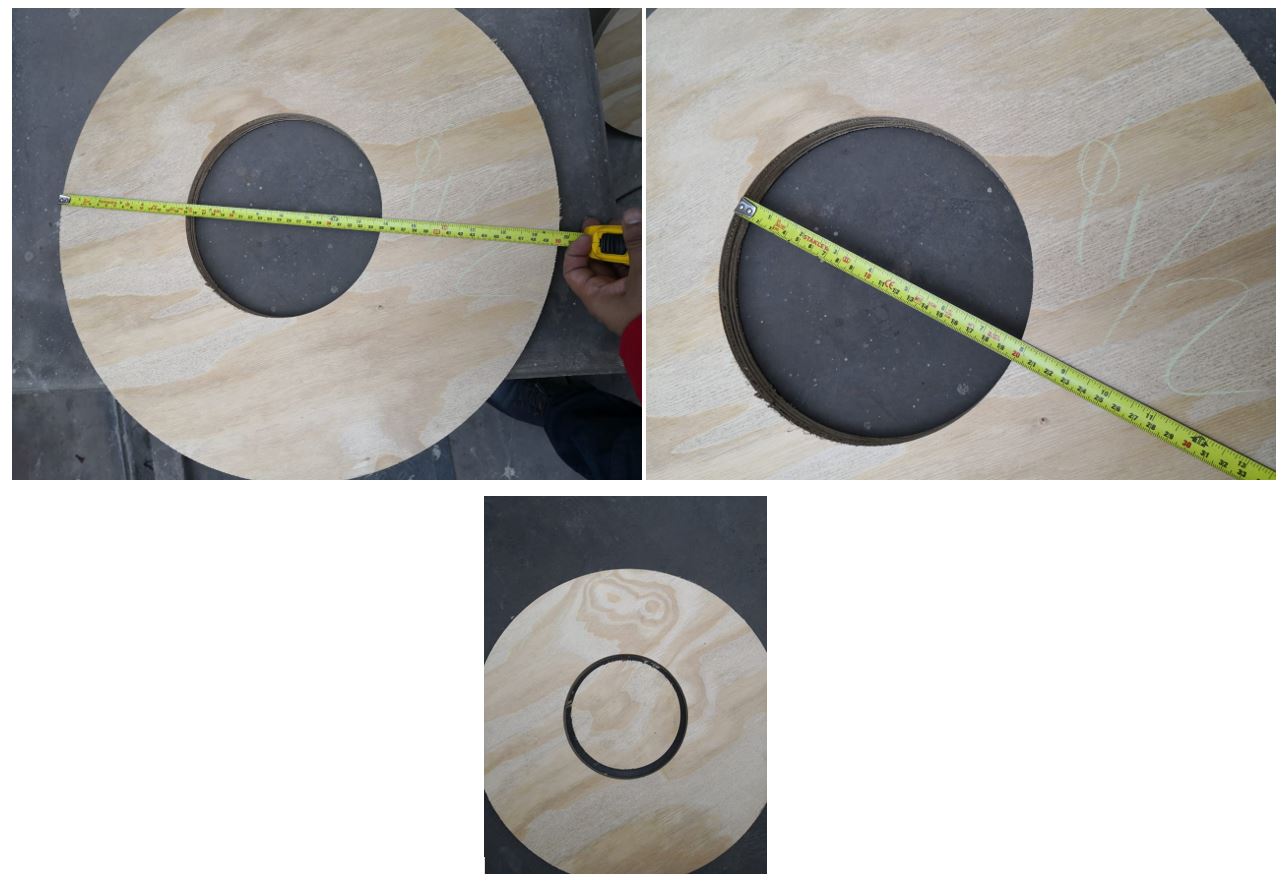
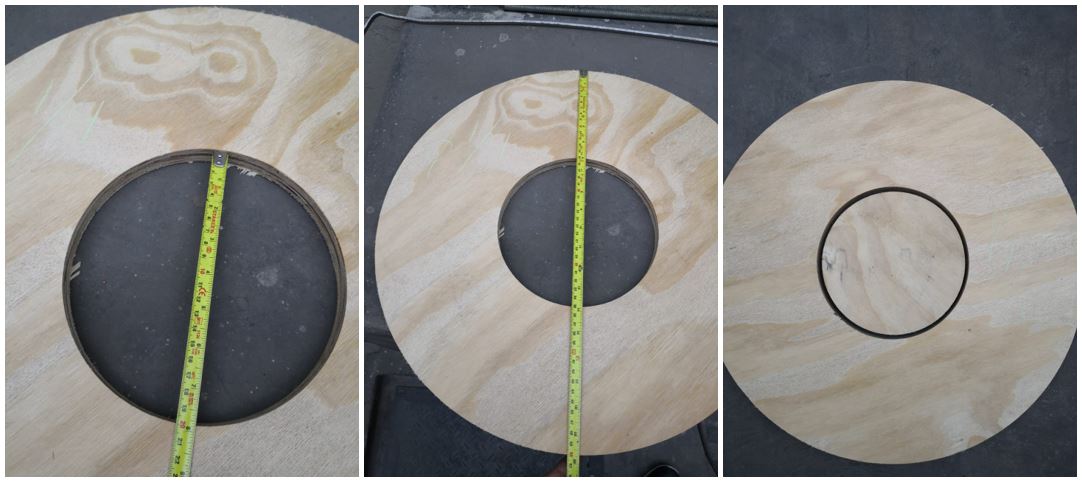
After this results I will use the milling of 3/16" when obtaining such favorable results.
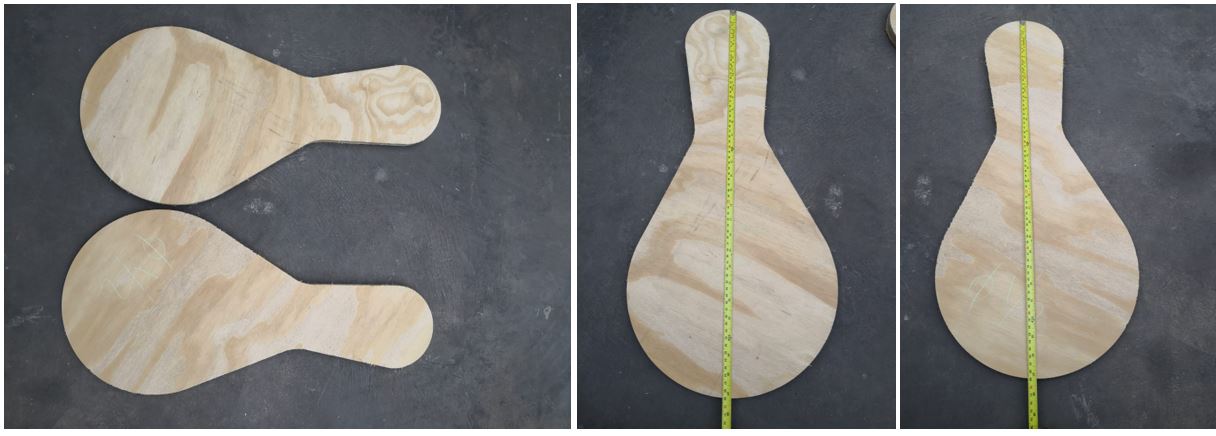
Export files
The software that uses the Multicam (enroute cad cam) only recognizes files of the DWG type, for it we must export each face of all the pieces, to carry out this process in a faster way by means of the Inventor software (software that I used for the design ), we right click on the face of the cut and select export with the DWG format, as shown in the picture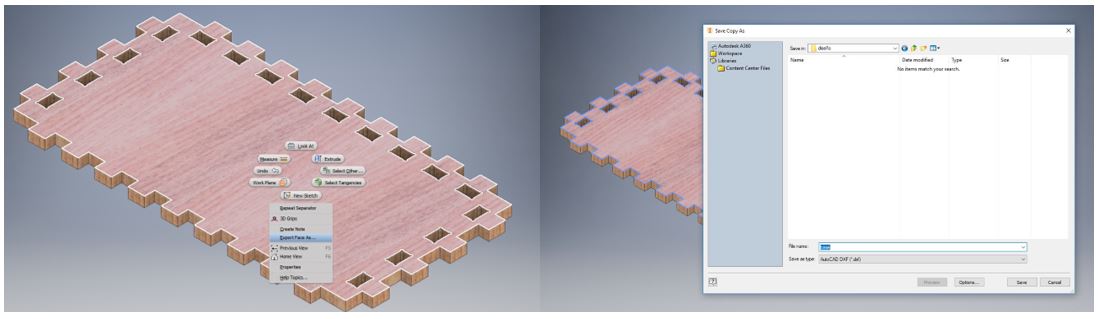
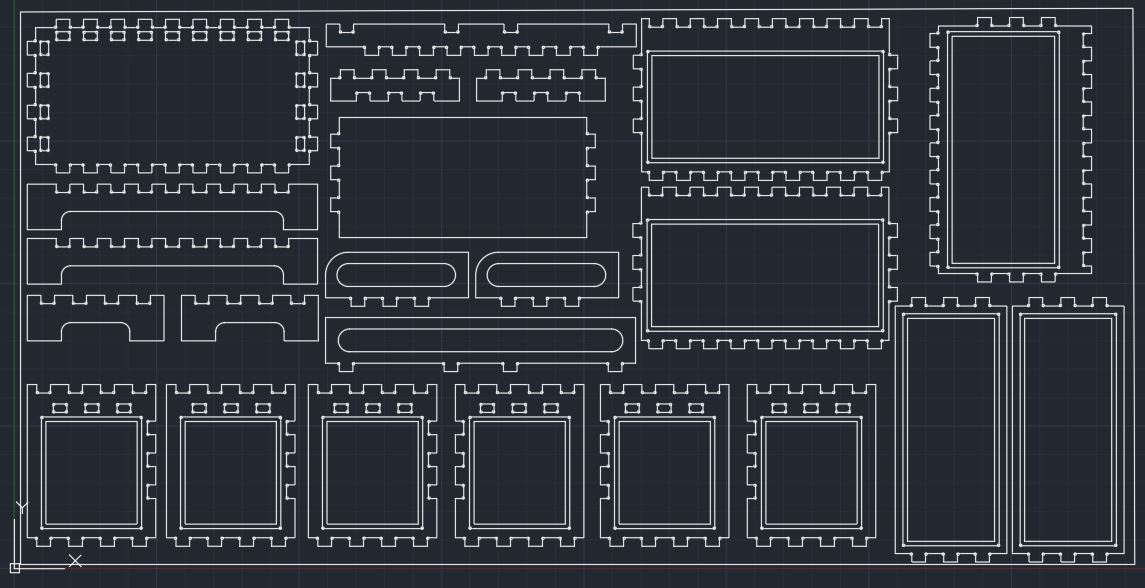
Do not forget to use the overkill command of AutoCAD to eliminate unnecessary repeated strokes.
Preparing the machine
The material used is a 2.5m x 1.3m plywood plate.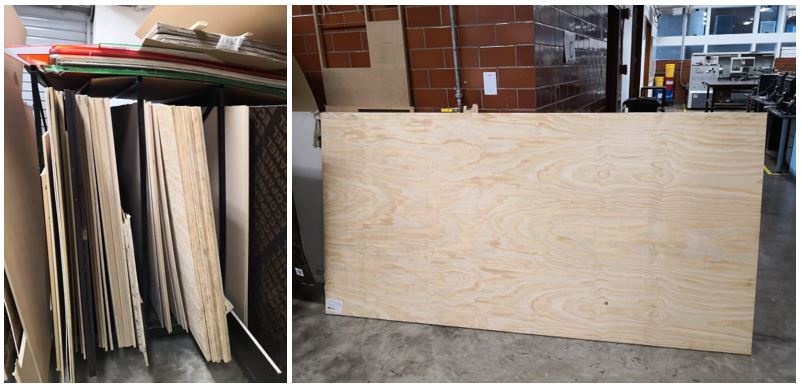
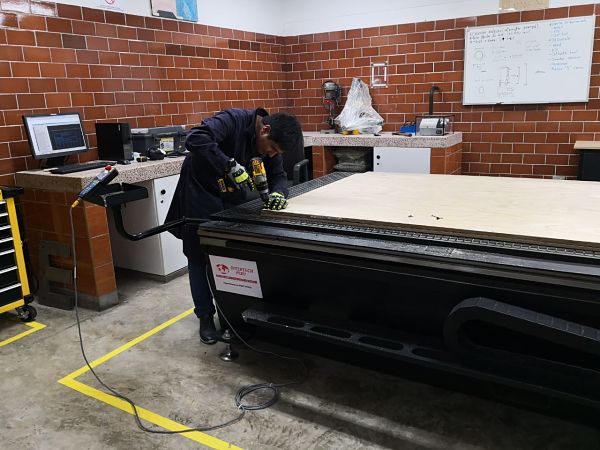
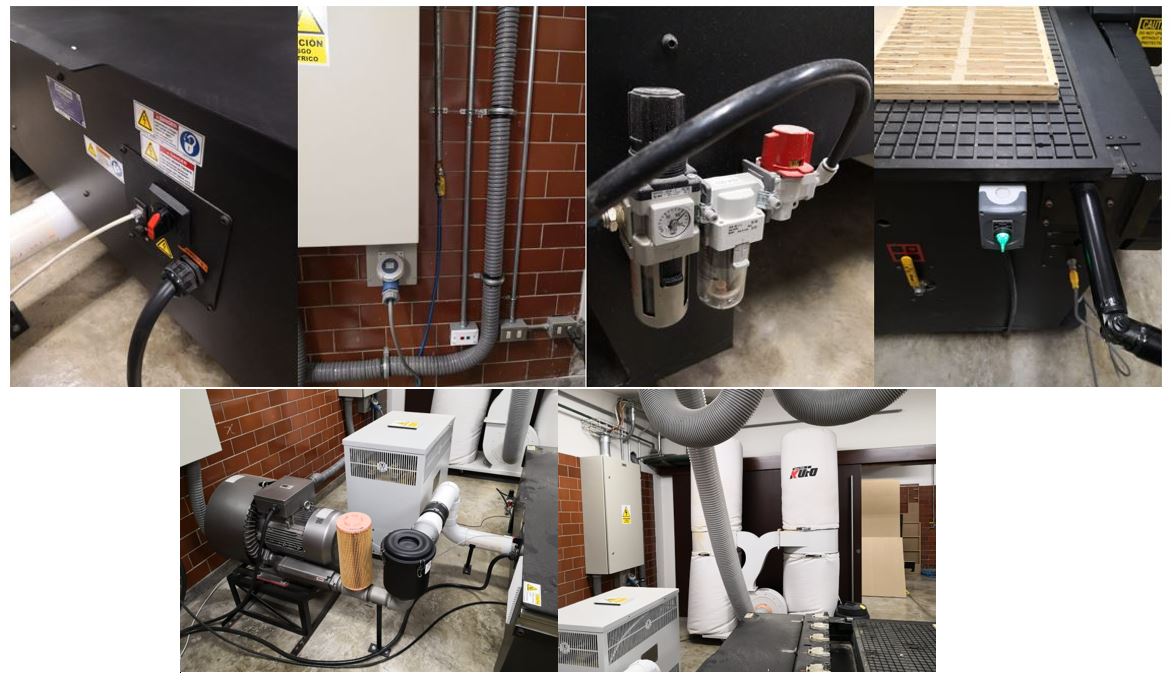
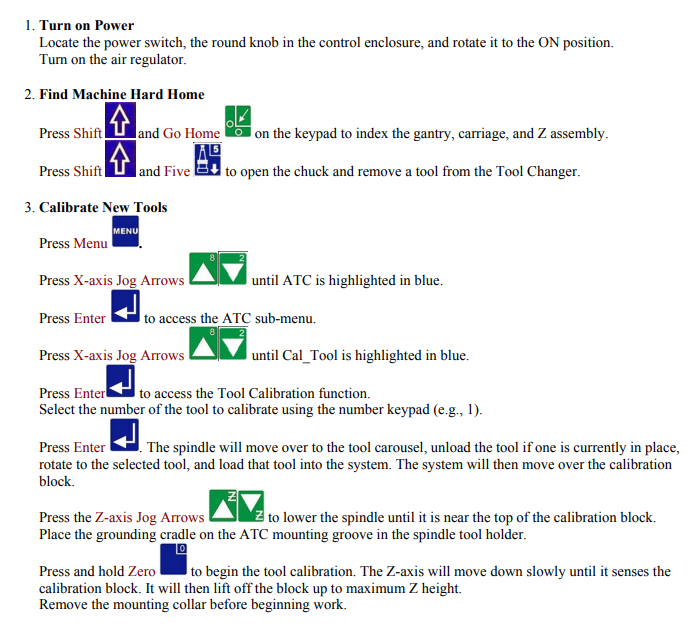
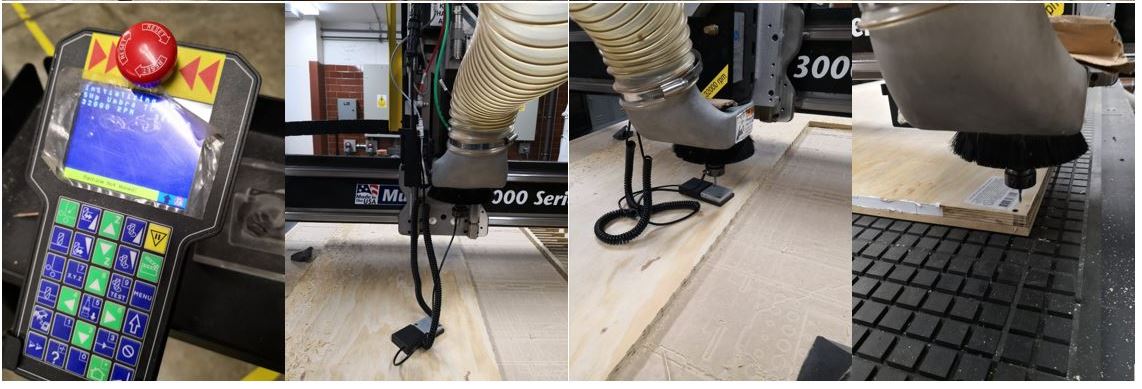
Manufacturing
The machine has several tools that are exchanged automatically using the M6 command of the G codes. In our case we will use the 3/16 " endmill.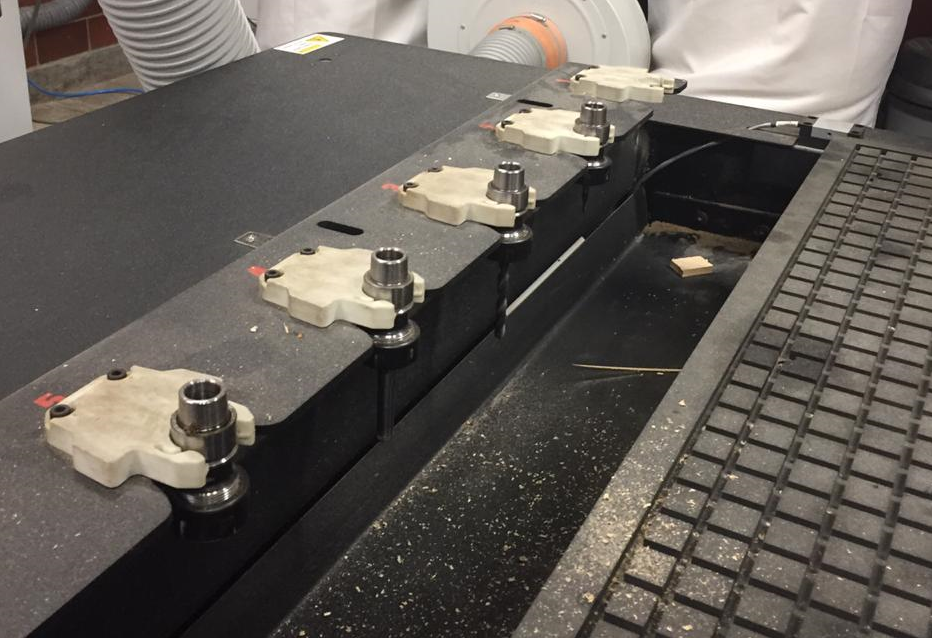
Island filling
This work makes the 5 mm wear that I do in my design. It is done as a first job because it will not make deep cuts and you cannot move the plywood, the parameters that are used are the following.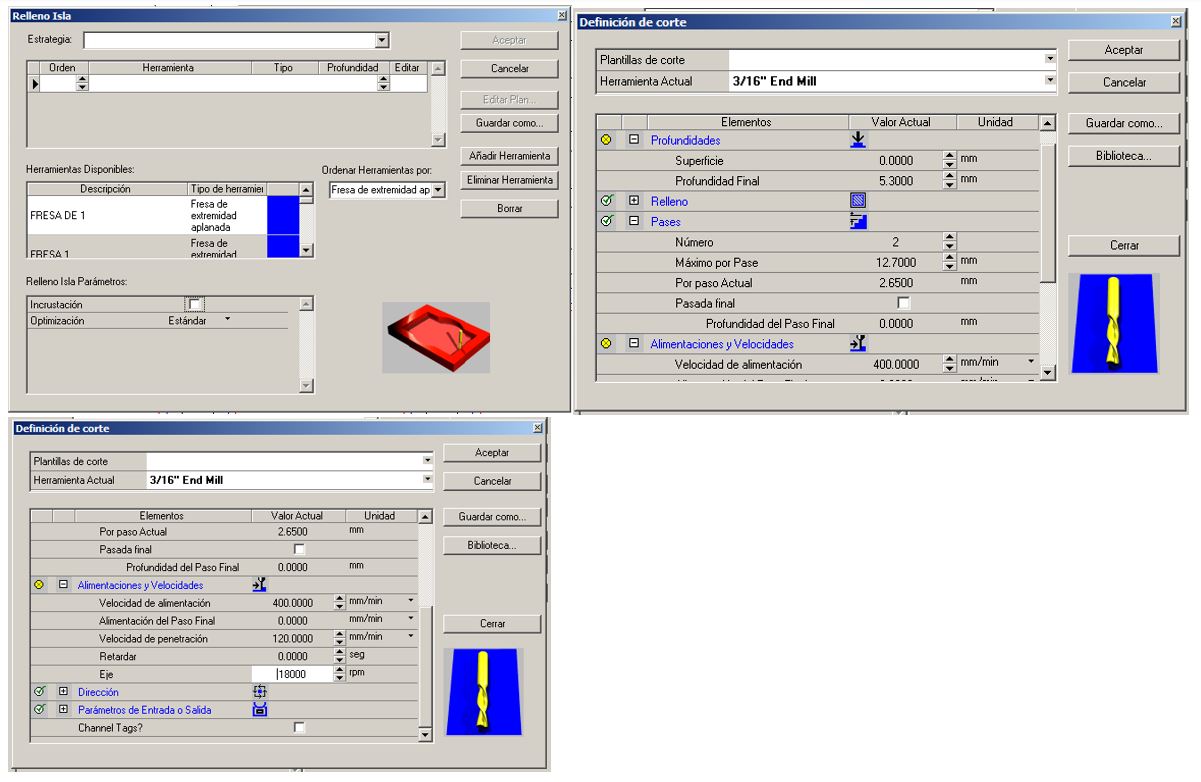
- Depth: 5.3mm
- Number of passes: 3
- Speed feed: 400 min/min
- Spindle Speed: 18000 RPM
Internal
The next work that is done is the interior cut. Once worn some areas of the design, the internal cut is made ensuring that the plywood will not move. The parameters that are used to make the cuts are the following.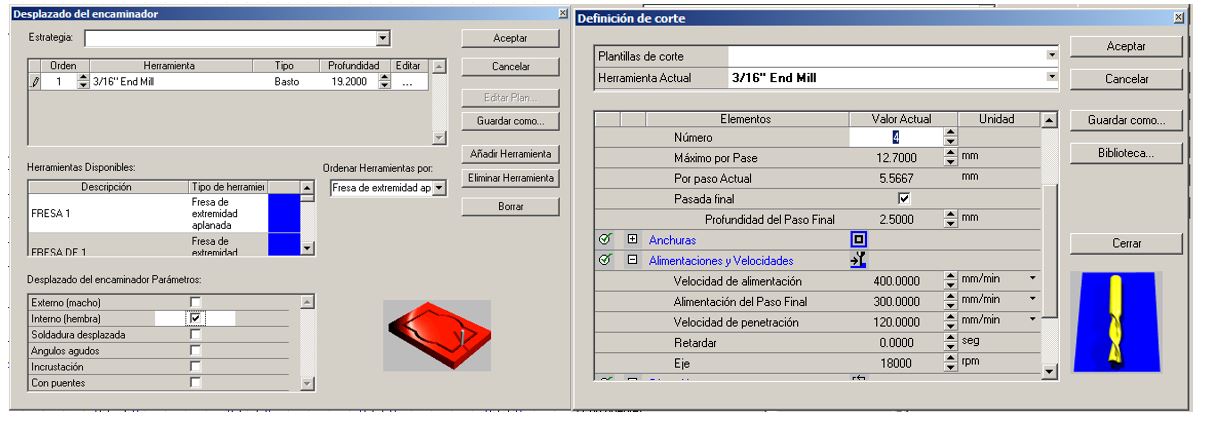
- Depth: 19.2mm
- Number of passes: 4
- Speed feed: 400 min/min
- Spindle Speed: 18000 RPM
External
The last work is the external cut, we must ensure the small pieces, so they do not move during the cut, the parameters used are the following.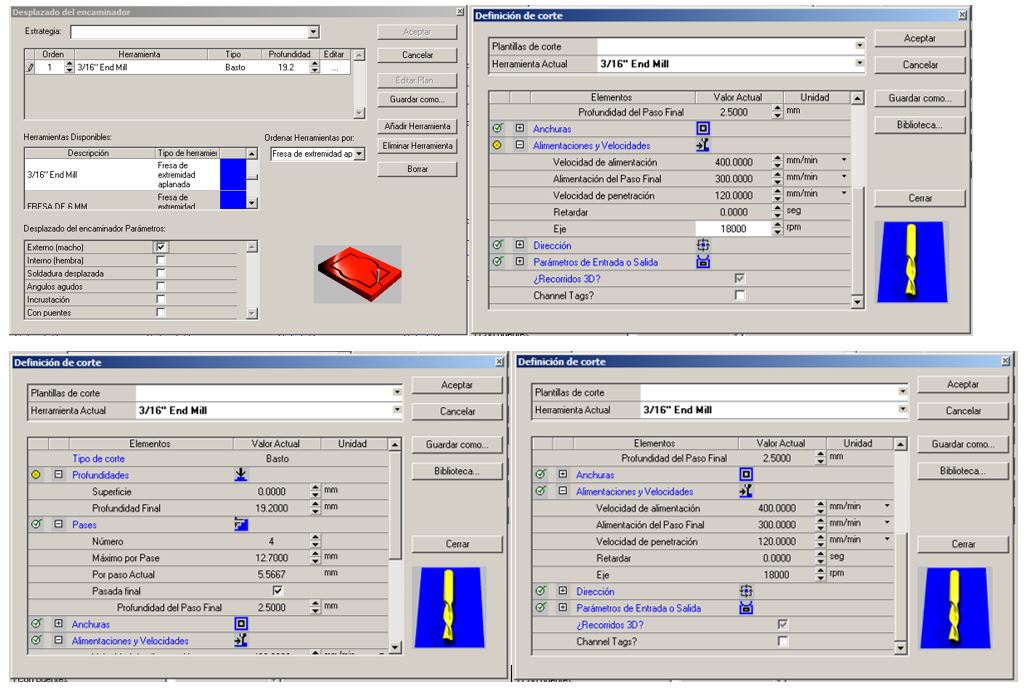
- Depth: 19.2mm
- Number of passes: 4
- Speed feed: 400 min/min
- Spindle Speed: 18000 RPM
Assembly
The result of the cut is shown in the following picture.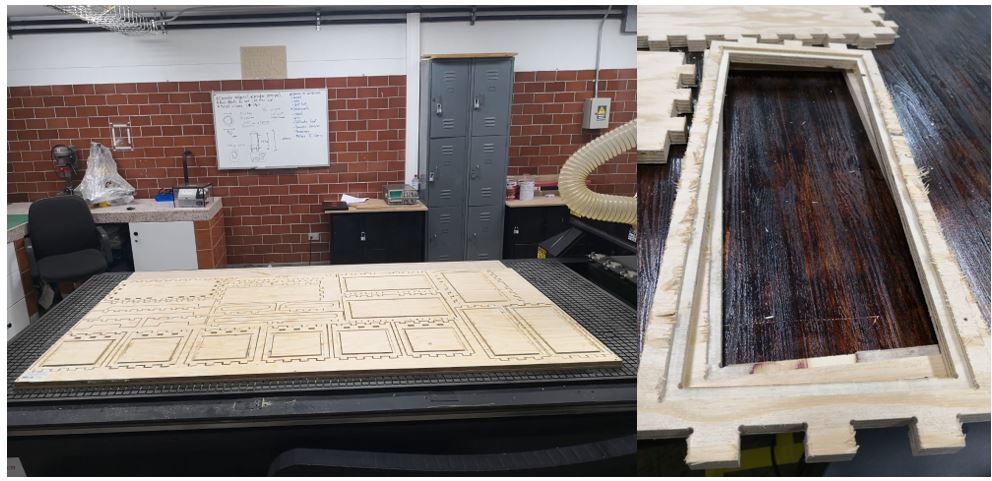
Once having all the pieces sanded and prepared, it is time to assemble the object.
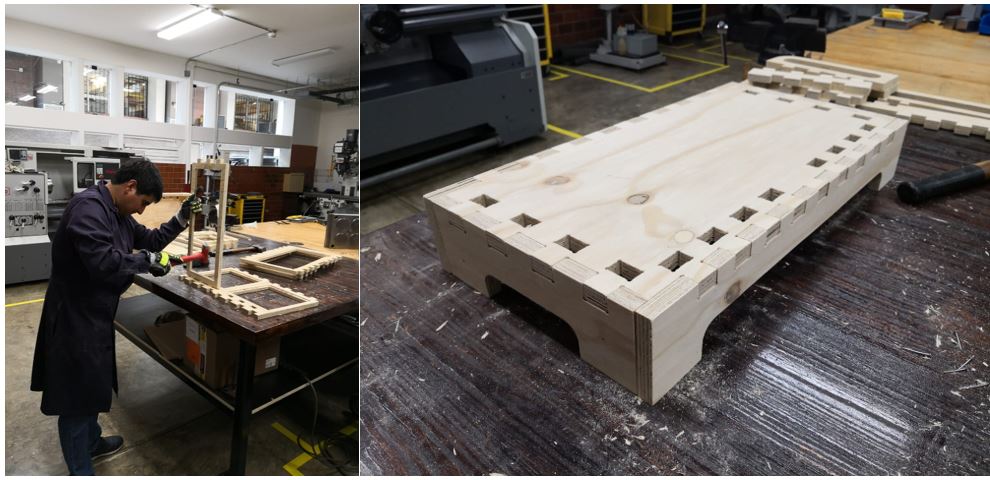
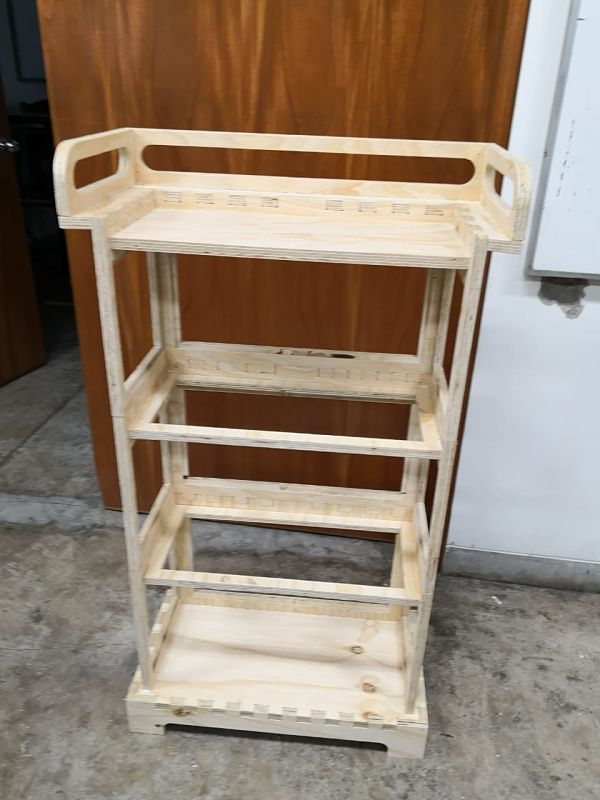
Group
As a group work, several types of tests are performed with the multicam, as a personal contribution I made the following designs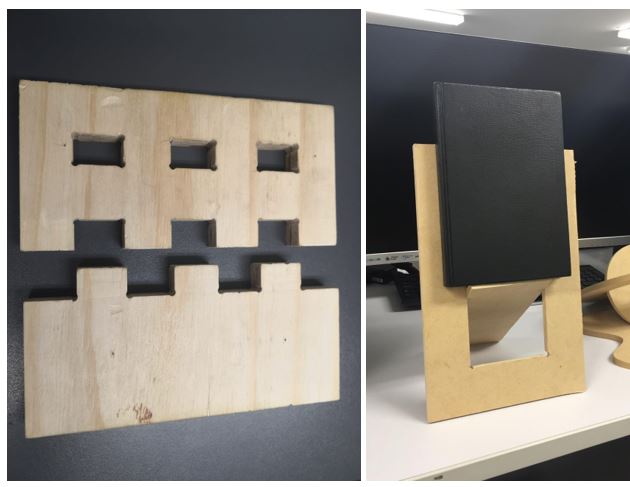
Problems
One of the main problems of the assembly are the tolerances and the correct design. In my case I had some small flaws in the design and the pieces did not fit perfectly.
For that reason I was forced to use some nails and glues to solve the problem.
Another problem is the excessive sanding of the wood edges on the edges of the furniture, it is recommended that it be sand-cut to the minimum to avoid that the pieces are very loose.
Download files
You can download this files Here (Inventor 2018):Base
Base
Front base (x2)
Lateral base (x2)
Central.
Back central part (x1)
Base central part (x1)
Left lateral central part (x1)
Right lateral central part (x1)
Final.
Final base part (x1)
Coupling back part (x1)
Coupling lateral part (x2)
Lateral final part (x2)
Back final part (x1)
Autocad (DXF)
Export file