Machine Design.
Personal Contribution
For this week, is time to actuate and automate the machine. My personal contribution was the integration between the software and the CNC board.
Board
The schematic that was made in week 15 was modified slightly to be able to carry out a routing without problems, for this some resistors 0 were added and to be able to obtain the final board.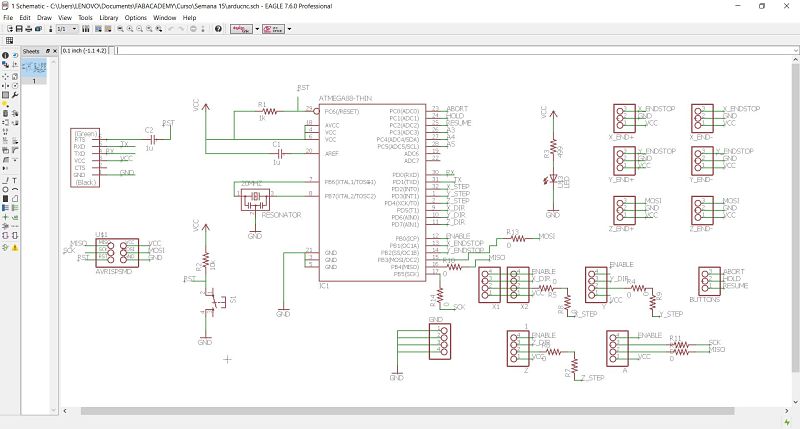
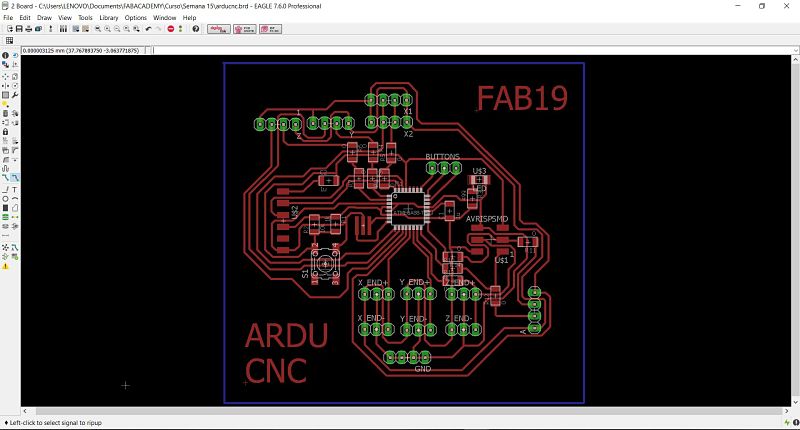
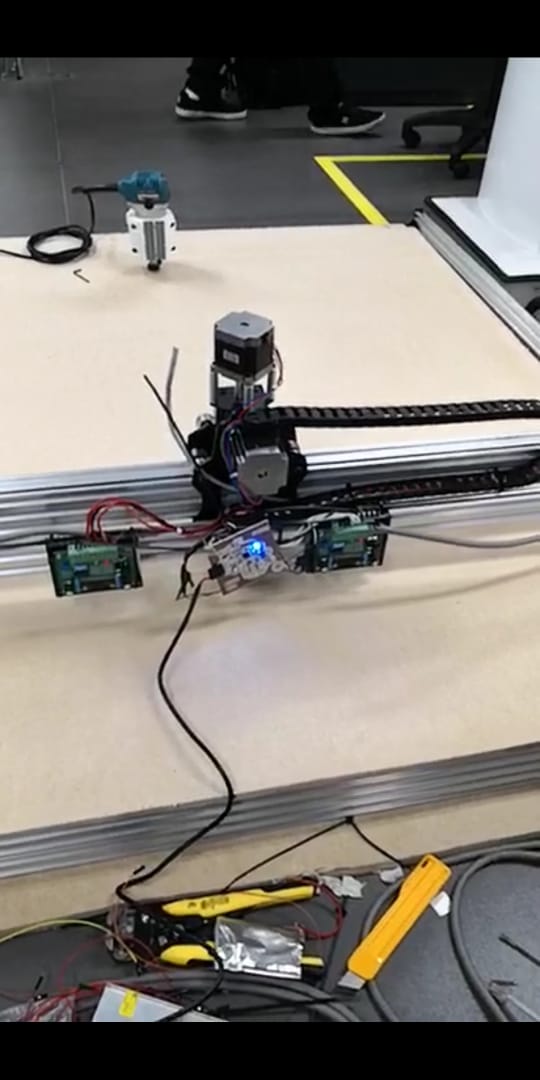
GRBL Software
Grbl is a free, open source, high performance software for controlling the motion of machines that move, that make things, or that make things move, and will run on a straight Arduino. If the maker movement was an industry, Grbl would be the industry standard. (Source: https://github.com/gnea/grbl/wiki).After reading several tutorials to upload the GRBL firmwareto the Arduino, we proceed to load it to our board, as shown in the picture.
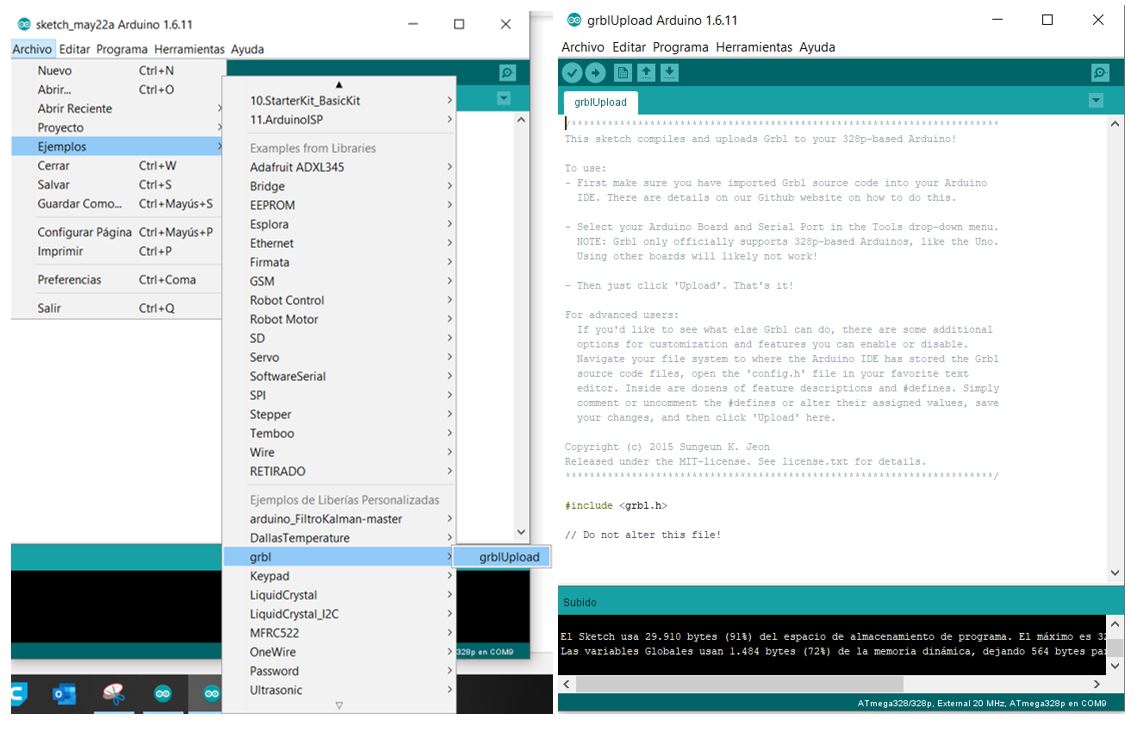
With the specifications of our components: stepper motors, belt and screw, we have the following configurations.
Belt
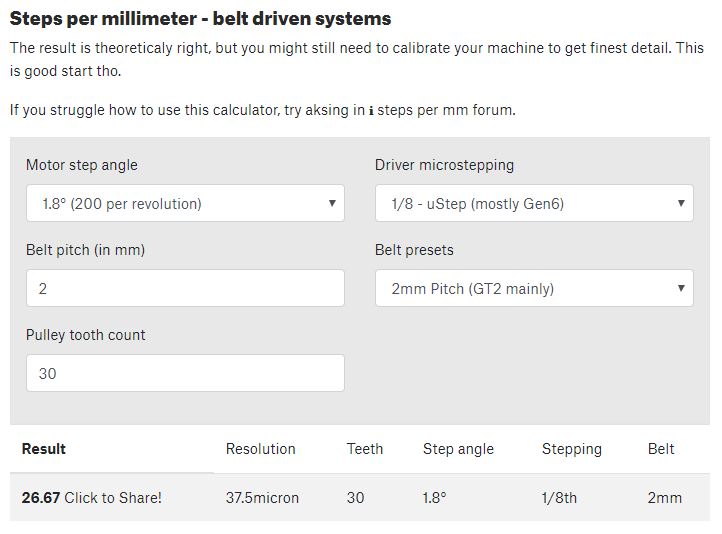
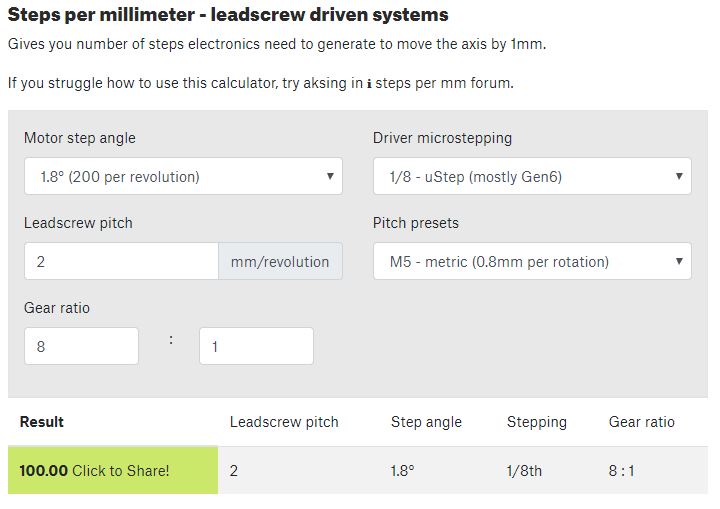
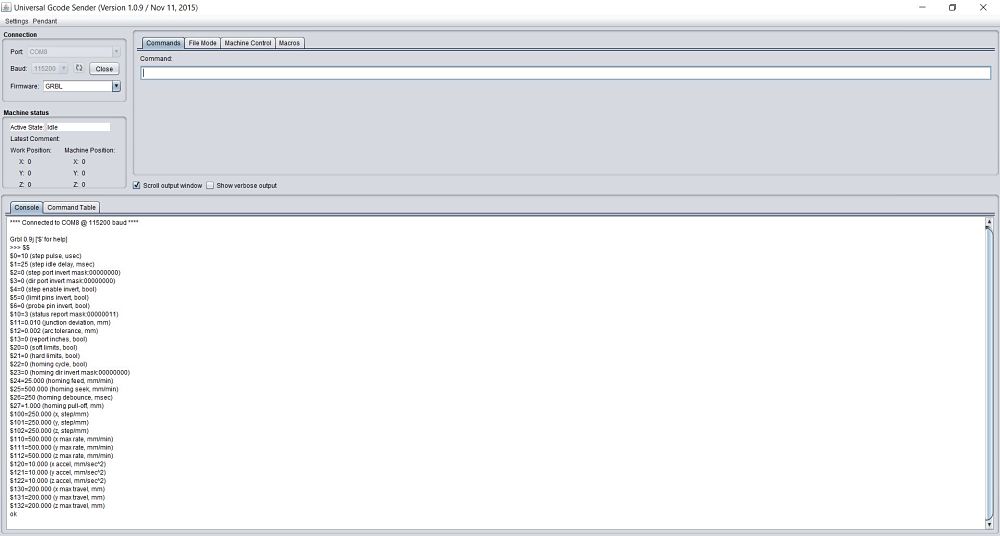
$ 100 = 26.67
, $ 101 = 26.67
and $ 102 = 100
Write the command $$ and we will see the modified parameters. These parameters can also be modified from the Arduino serial monitor, but with this software we can also move the axes and perform a job.
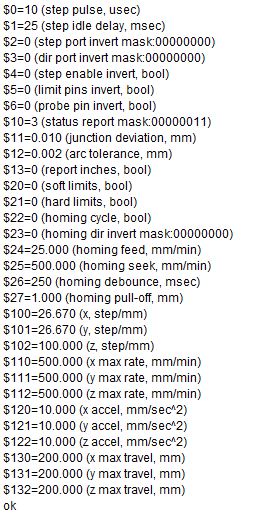
bCNC Software
Our instructor recommended the use of bCNC software, since it is totally free software and works in Python. We can download said software from this link.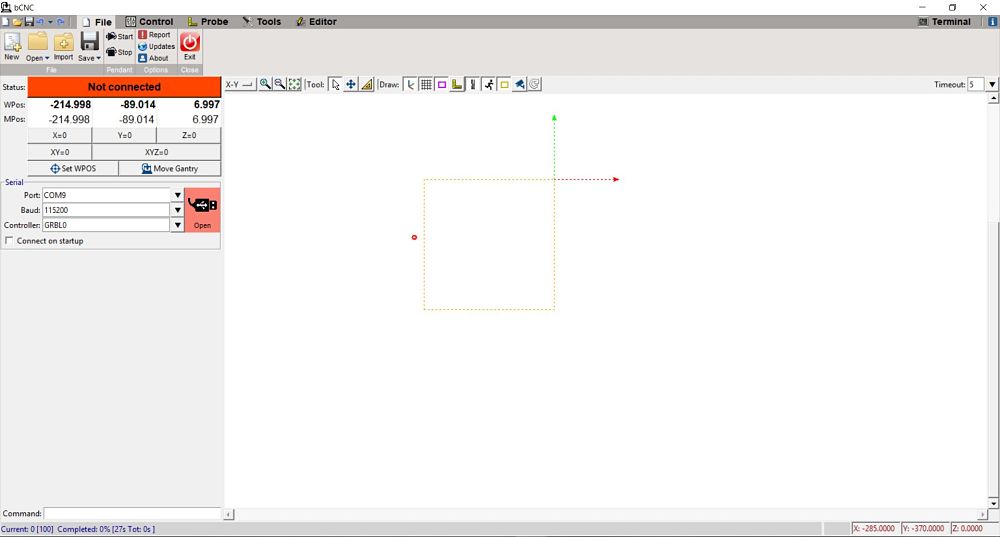
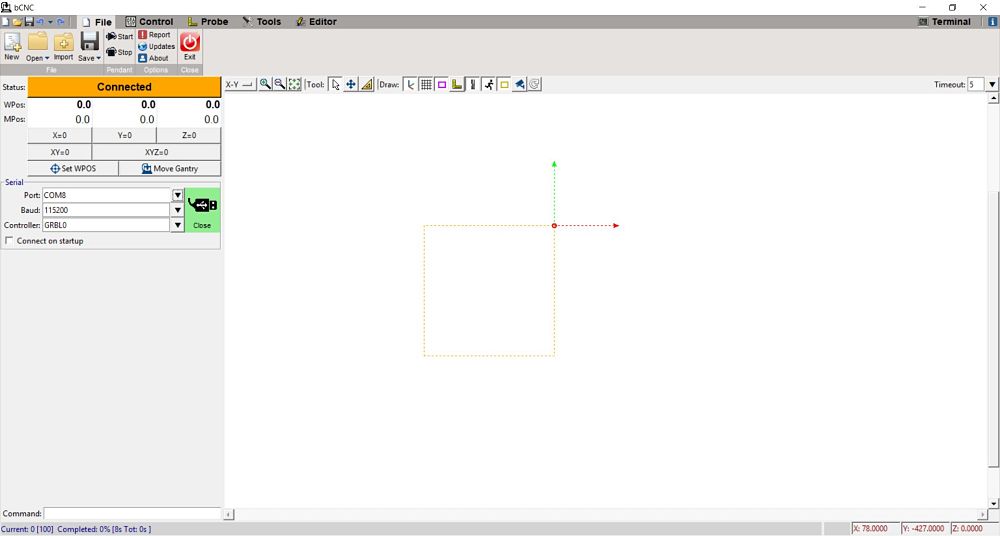

Group
To see all the documentation of the group work, you can visit the CIT page.
Download
You can download this files Here:
Schematic.
Board.
Traces.
Out traces.