final project -- about me -- weekly assignments -- fab academy
Decisions...
0 - How To Go On From Here
I really like making stuff, and making it work. I do have a problem, though, a massive one. To make stuff, you need time, and time is something I don't really have. Even less now than a few weeks ago, due to some rather massive changes at work. I want to go on, more than ever, but there will be compromises. I will have to tone down some ideas, and in some cases, buy stuff instead of making it. Which I don't exactly like, but I don't like giving up either.
1 - How To Grab Components
This is, by far, the hardest part of any placer. I was toying with the idea of a grabber, based on motorized tweezers. While it's a cool concept, I have given it up - For now, at least. It should be well possible to do, and it should be a cool way to invest time instead of money, as it would mean a lot of experimenting with cheap hardware. I don't have the time to do all that experimenting, though. Simple as that.
So, I'm back to the evil vacuum. Vacuum stuff is hard to make, requires quite a lot of tools and expensive material. But it works, and grabbing small objects by vacuum is an industry standard in such a brutal way that you can get ready made components for "little money". Including all those hard to do things like valves. So, I found a "vacuum generator" made by Festo that includes a shut-off valve and generates a small pulse of compressed air when shut off to get rid of that capacitor still sticking to the grabber. It's an off-the-shelf unit and I see no reason why it shouldn't just work. The version I want is roughly 100€, which hurts, but works out. It's a compromise.
I still need a grabber, though, and I want to build that one first before I buy anything expensive. I see two problems to solve here... First, the grabber itself. Commercial placers mostly seem to use "standard medical", non-sharp needles, or rubber "cups" for larger components. That seems reasonable, as the stuff is readily available and cheap. Also, there seems to be a standard for the mount, ISO 594 or EN 20594-1:1993 (there is a German version, too, which we should have available at the university... Or I can just saw off the cone from a cheap disposable syringe. That part is easy to solve, as we do have a good lathe. And syringes to cut apart.
Second, the grabber must be able to rotate more or less freely. While it could work to have an angle limit, it would require planning on how to pick up polarized parts to be able to place them correctly. And I would hate to have to do that, so that thing has to rotate freely. Which brings up the problem of a rotating vacuum connection that is reasonably airtight, but still moves easily enough not to disturb any alignment - I don't want to pull the "my motor is stronger than that joint"-hammer here as the weight would be unfunny. I do have an idea for that, but I haven't tried it yet. The material is on the way though.
2 - How To Move Around
Moving should be rather straight forward (and back, of course...). I plan to use geared DC motors (if I can't do a servo regulation on time, it will work without that as I'm only moving manually in the first version) and strings to move around.
A lot of stuff for that part is already here and waiting to be used. Documentation is not even remotely done yet, though...
3 - How To Control Stuff
I'm actually already working on that part. Documentation is still lacking, though...
Control will be networked. On a bus system. With rather universal boards I have wanted to make for a long time now, and a (somewhat more powerful) microcontroller doing the realtime stuff.
Teaser:
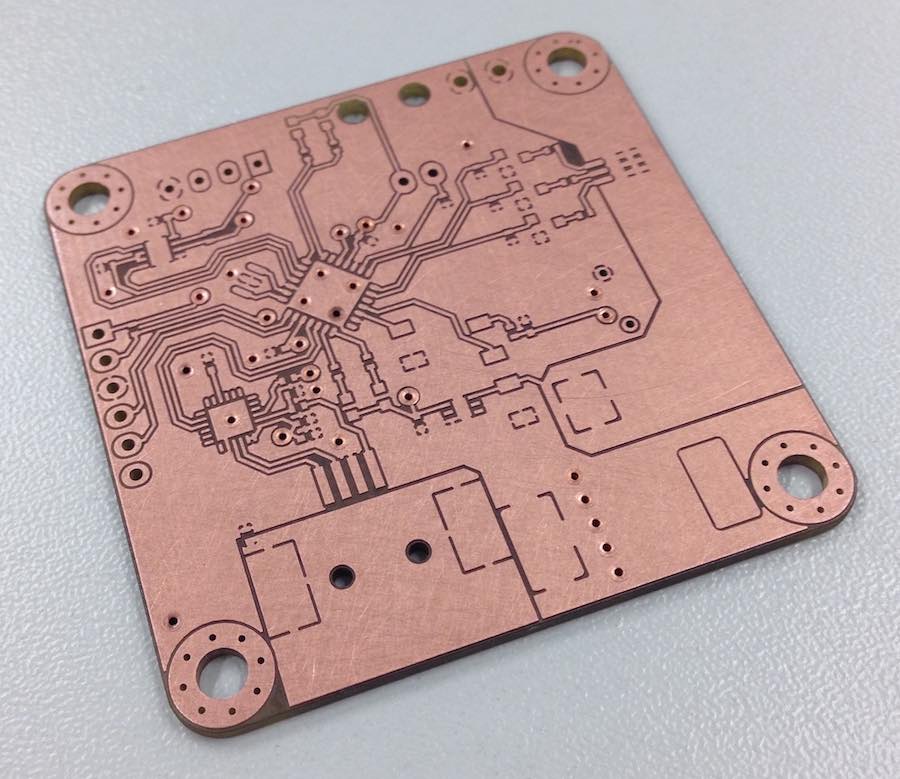
4 - How To Power Stuff
Due to the hardware I have or plan to get for the project, powering stuff will be a task:
- The Raspberry Pi I want to use for displaying the camera image and maybe (at a later date) to use that image for automatic placement needs 5V, and a considerable amount of power.
- The DC Motors as well as the Robotis Servos I'm still thinking about for some tasks need 12V.
- Most of the Electronics run at 3.3V, but need next to no power.
- The Vacuum control valve operates at 24V and needs an unknown amount of power (I have found a vague mention of 7W for a short time, less after that). It isn't available for other voltages.
What I plan on is, therefore:
- Powering the machine with a 12V power supply, directly patched to the Motor-/Stuff-Bus
- Powering Electronics with 3.3V linear regulators on the individual boards
- Powering the Raspberry Pi with a 5V switching regulator from the 12V rail
- Powering the Vacuum Valve with a step up regulator from the 12V rail, too... we'll see how well that works out
final project -- about me -- weekly assignments -- fab academy