Molding and Casting
This week i had personal reason to not be in the Fablab so i learned the steps following Coral's (classmate) process. For this assigment we designing a 3D object, milling a mould and casting it.
My idea for design was to do a coasters inspired in the side walk design.
With Rhino, i design the coaster and insered it in a box which represent the block of wax that will be the conte for the silicone molde.
After it exported it as a stl file.
Whith the design read i used the software Modela Player 4 to creat the creating toolpaths for
the milling machine. I did 3 process, roufing to make the surface flat, after the roughing to make the shape and the last one the finishing to make it more perfect.
After i choose the tools, for the roufing and roughing i use the 3,175 and for the finishing the and for the finishing the 0,8.
I also had to choose the type of path, the scan lines for the roufing and the countour lines for the other ones.
For the cutting parameters that i used was from the software alredy but i could have modifed a
bit to improve the work time.
After having the files ready i when to the machine, i fixed the wax block on the sacrifice layer. Set the Z in the midle of the wasx because it was the lowest point.
For the fisrt try i realize that i had a scale issue , and the second try the design was too big for the wax. After fix all i run a surfacing
, to make all the surface flat. After the roufing to make the firt dig in the wax and the finishing for better quality of the molde.
The next step was to make the (silicone) mix , firt i measure with water how much i will need of silicon then i mix 95% of silicon and 5% of catalyst. With the mix well mixed i used a vacun machine to take out the bubbles. After putting it on the wax i put it back to the machine to take out the rest of the bubbles.
My first try of casting was with (marbel),its just 50% of it and 50% of water but because my molde is really delicate it broke.
For the second try i did with ... and the type of reaction make a deformation on the shape.
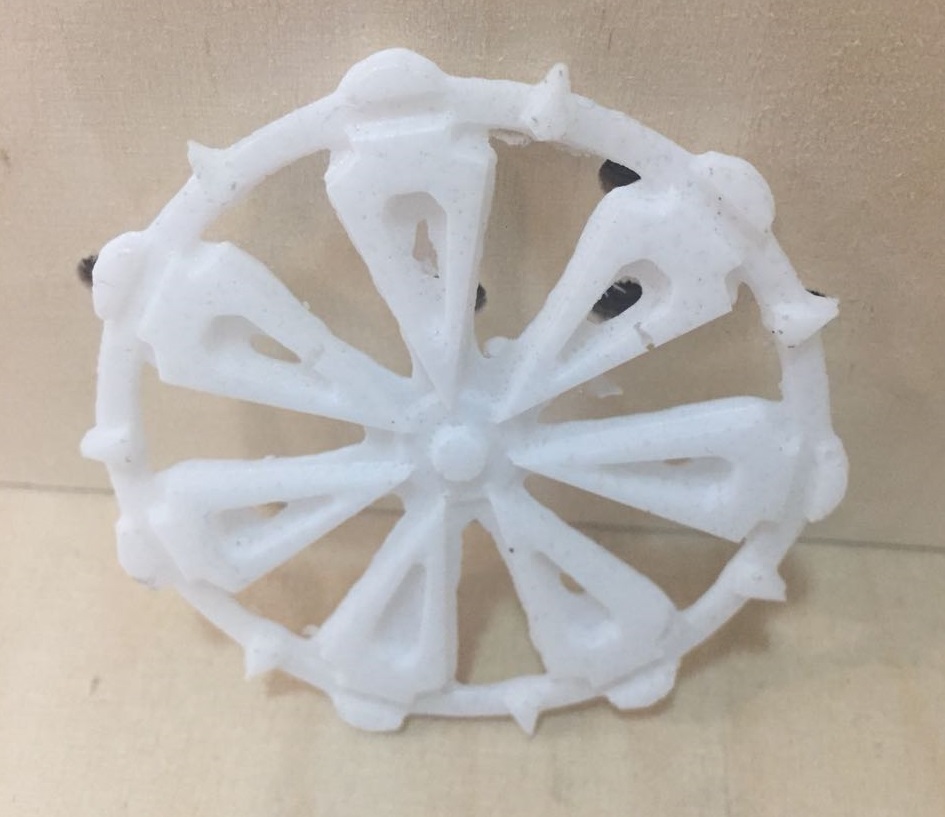
For the third try i did with the same but i tried to put weight on top to no deformate but it create a
tiny pellicle of material . I tried to remove the it but it broke in the process.
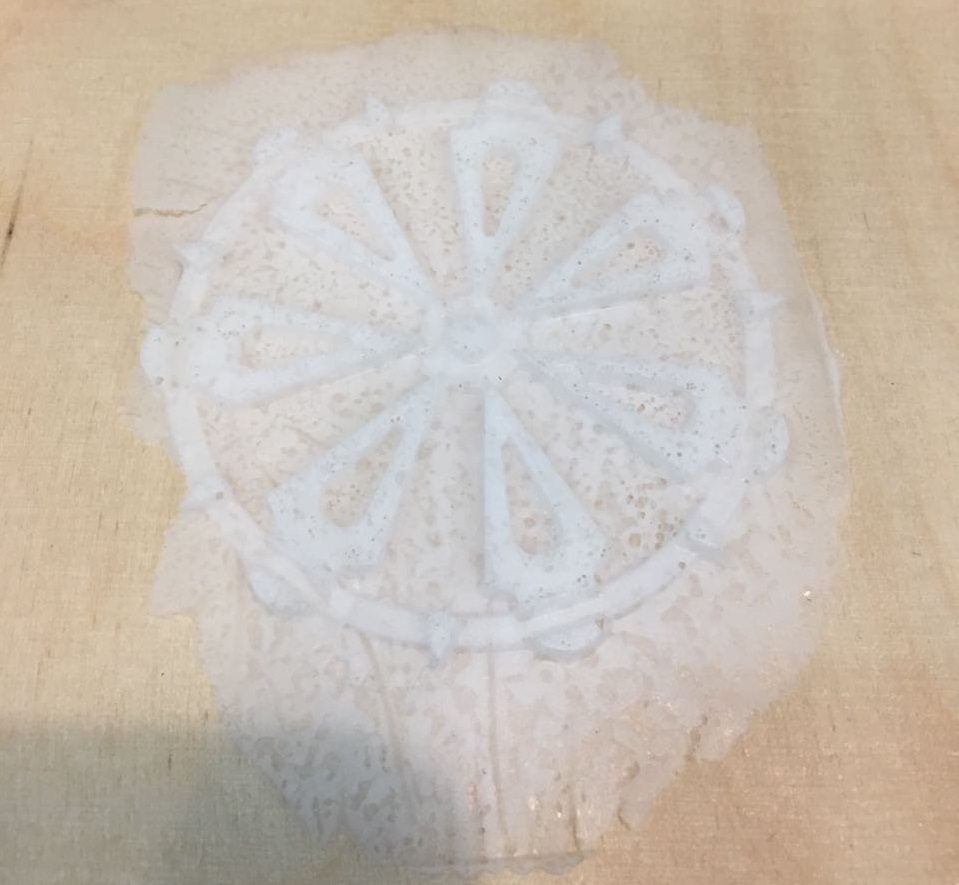
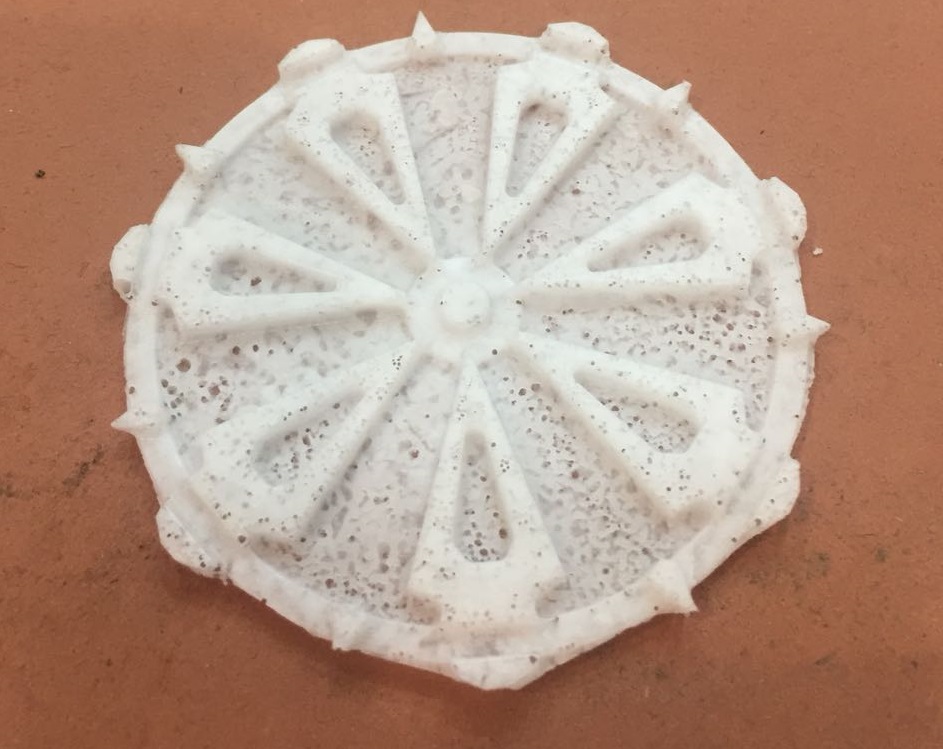
For the last try i did it with silicone, i had to spray so it would not glue together. For a perfect casting i would need more resistant material with no expasive reaction and be really precise when putting the material in the molde.
Here is the file.