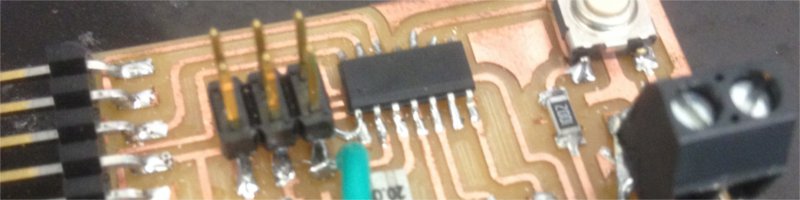
MACHINE MAKING
This week was machine making, a group project which allowed us all to focus on individual pieces of the machine. While I focused on the design of the gondola,
You can find a more complete representation of the machine making process here.
We decided right at the beginning to creating a drawbot, so the first thing I did was to familiarise myself with previous drawbots that already exist.
Two of the machines I first came across were Hektor and Viktor which used two and 4 motorised axis respectively. I then found the Polygraph which seems like the best version of something we wanted to achieve.
The next thing we did as a group was to decide actually needed to be in each part of the machine. I was a part of the gondola team, and we decided that we would need these components:
- The actual Gondola
- An arm that could turn the pen on/off
- components that could hold the ball chain and pivot depending on the position of the gondola
- some sort of weight that could act with the counterweights to make the whole thing move properly
We also decided on a basic design based on Hektor. From here the rest of the design was just adjusting the size and shape to make all of the other parts fit as people developed them.
Fab acadmey collegue Zenna worked on the initial gondola files in illustrator, which we then quickly cut out on the laser cutter in cardboard. This seemed like the qucikest and mechanically sound way to create the gondola, especially as it needed to be flat. I then adjusted the illustrator foles to fir Daniels servo arm and created a second iteration in carbaord. Once everything was approved by the team, I made the final gondola in 6mm acrylic. The idea with the spacing was that the center diamond was big enough to hold the pen in the center when the arm was in its bottom position, but had enough tolerence to not get in the way if we decided to add other pens. This is what ended up defining the total size of the gondola. We used a diamond shape so that all of the cords for the servo would not get in the way of the other cords.
The only other peice of design involved was the holes for Anna and Geoffs Ball chain pivot. Talking to Daniel, he informed me of the specific way one would usually hold ball bearings in a rig, which was to use a lip s that each part of the bearing was touching only either the pivot or gondola. However to create a lip like this on the laser cutter would be a real nuisance. In the end I just played with the tolerences of the acrylic cutting settings so that the pivot press fit tightly into the gondola.
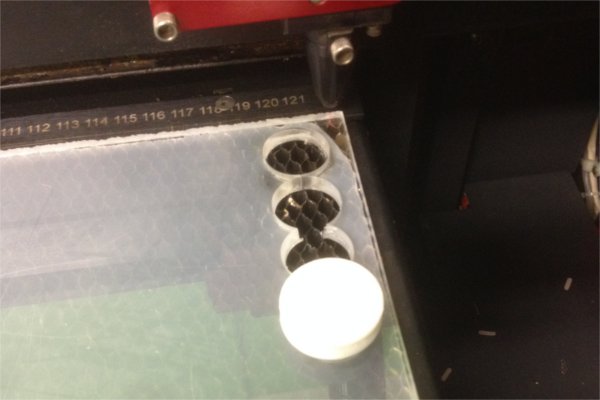
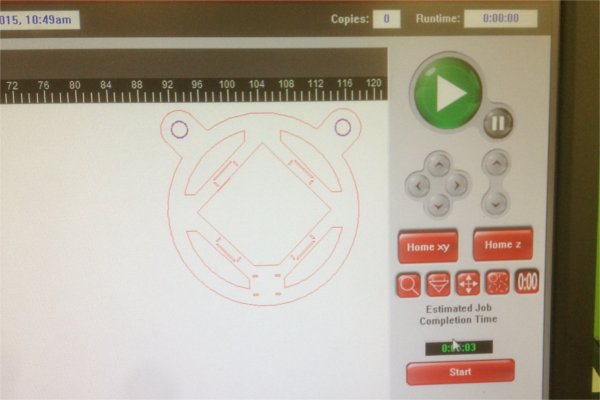
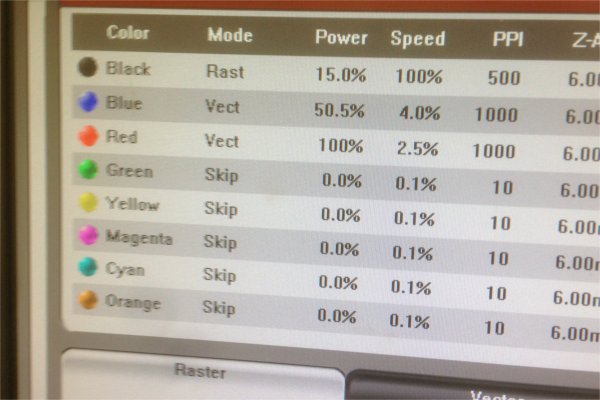
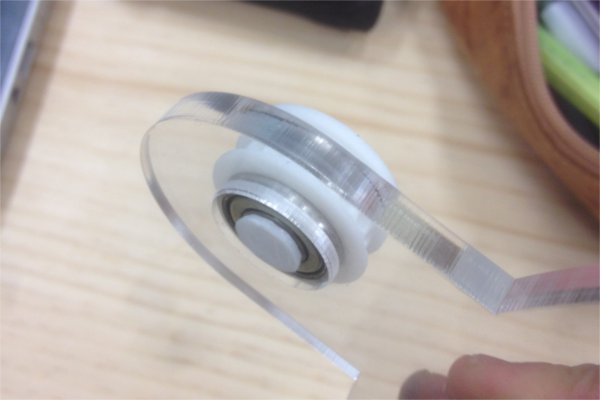
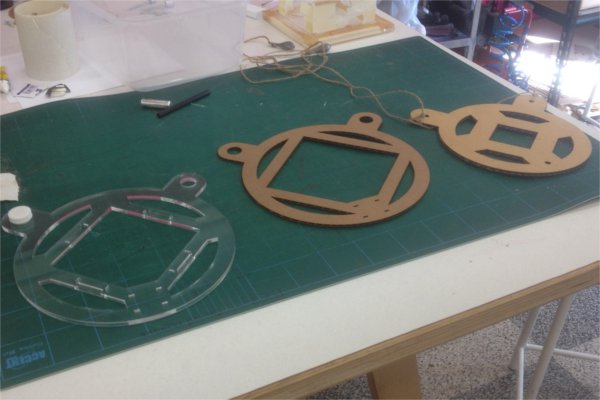
Hanging around with the rest of the group, it became clear that after the initial evaluation of the scribbly bear it was clear it was going to need some more weight! I picked up a peice of solid iron pipe and cut it until it was the right weight for the machine. After that my job was to simply help out with the assembly with the rest of the team, which mainly involved hanging around and making jokes in the hallway.
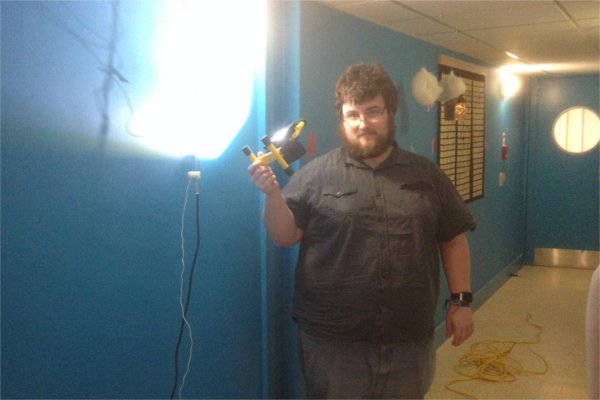
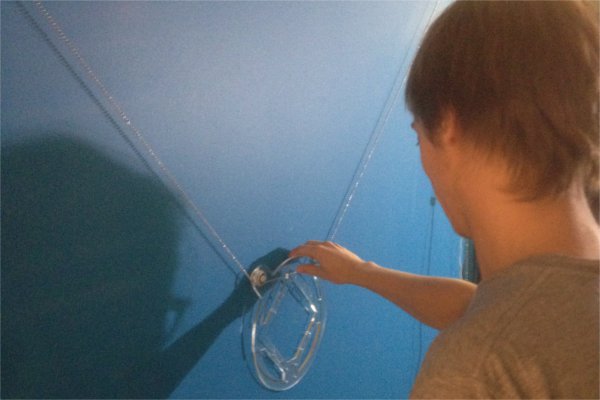
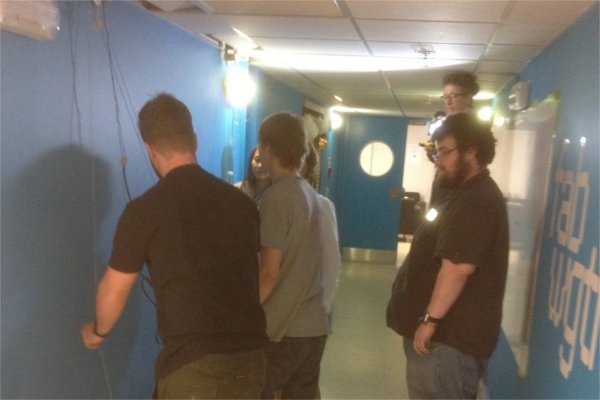