Materials & Tools
For Mold
For Casting
Mold Design
In this assignment I made a split mold, to create mallets for the air hockey table (for my Final Project). It's a very simple piece only need a revolve operation. Of course the unmolding angles are considered in the CAD draw.
![]() ![]() | ![]() (a) Draw dimentions (b) Section view (c) Render |
Then create the mold cavity and the mold core CAD draw. The mold core have over flow holes Finally save it in .stl format.[.STL Files]
Mold Manufacture
Step 01.-If you have a wood block you can jump this step. To create a wood block, cut several pieces of MDF board, and then paste it together and press it with the vises. In this case I used four 20mm layers to create a block of 80mm of height. | |
Step 02.-Screw the block of cavity mold to a piece of board. Take care and screw where the mill wouldn't pass inside de mold cavity. Then screw the piece of board on the Shopbot bed. |
Step 03.-Start the milling process. Personally I used 3 types of mills (¼" and ½" Ball point and ¼" Flat Point end mill) and 2 softwares to create the 3D paths(PartWorks and PartWorks-3D) | (Rough Cut-PW3D) |
(Fine Cut-PW3D) |
(Rough Cut-PW3D) |
(Fine Cut-PW3D) |
(Profile Cut-PW) |
Step 04.-To fix the other part of the mold screw the MDF more than normal (introduce the head of the screw inside the MDF). For this part I use ¼" Flat Point end mill with long shaft and PartWorks to create a pocket around the cilinder to create a gross profile for the 3D milling process. |
Step 05.-Star the 3D milling of the center protude, y use for these process the Ball point ½" end mill. |
The Result is like the photos below:
Casting
First spread the vaseline in all the mold surface, If you use floor wax you need to spread, at least 6 layers of wax.
For Casting, the process is too simple, only mix all the components in the correct proportion (Activator 1.5% and Catalyst 0.5%). The Monostyrene is for dilute an get the correct viscosity to reach all the parts of the mold.
Final pour the resin in the mold and close the mold until you see the resine exits the overflow holes.
If all the process was correct you can unmold in a couple of hours, depende of the temperature of the ambience (coolest take more time).

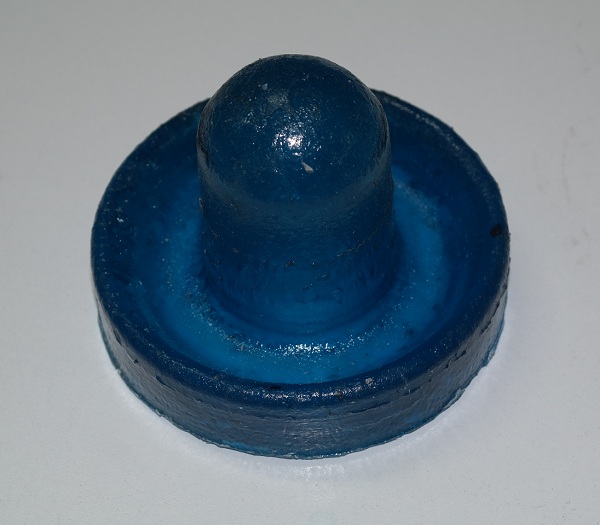