Assignments
Group Assignment
- Do your lab's safety training
- Characterize your lasercutter's focus, power, speed, rate, kerf, joint clearance and types.
Individual Assignment
- Cut something on the vinylcutter
- Design, lasercut, and document a parametric construction kit.
GROUP ASSIGNMENT
More specific detailed from the worked done with Ernesto Castro in Fab Lab Universidad de Lima here
Fab Lab Ulima s a f e t y t r a i n i n g
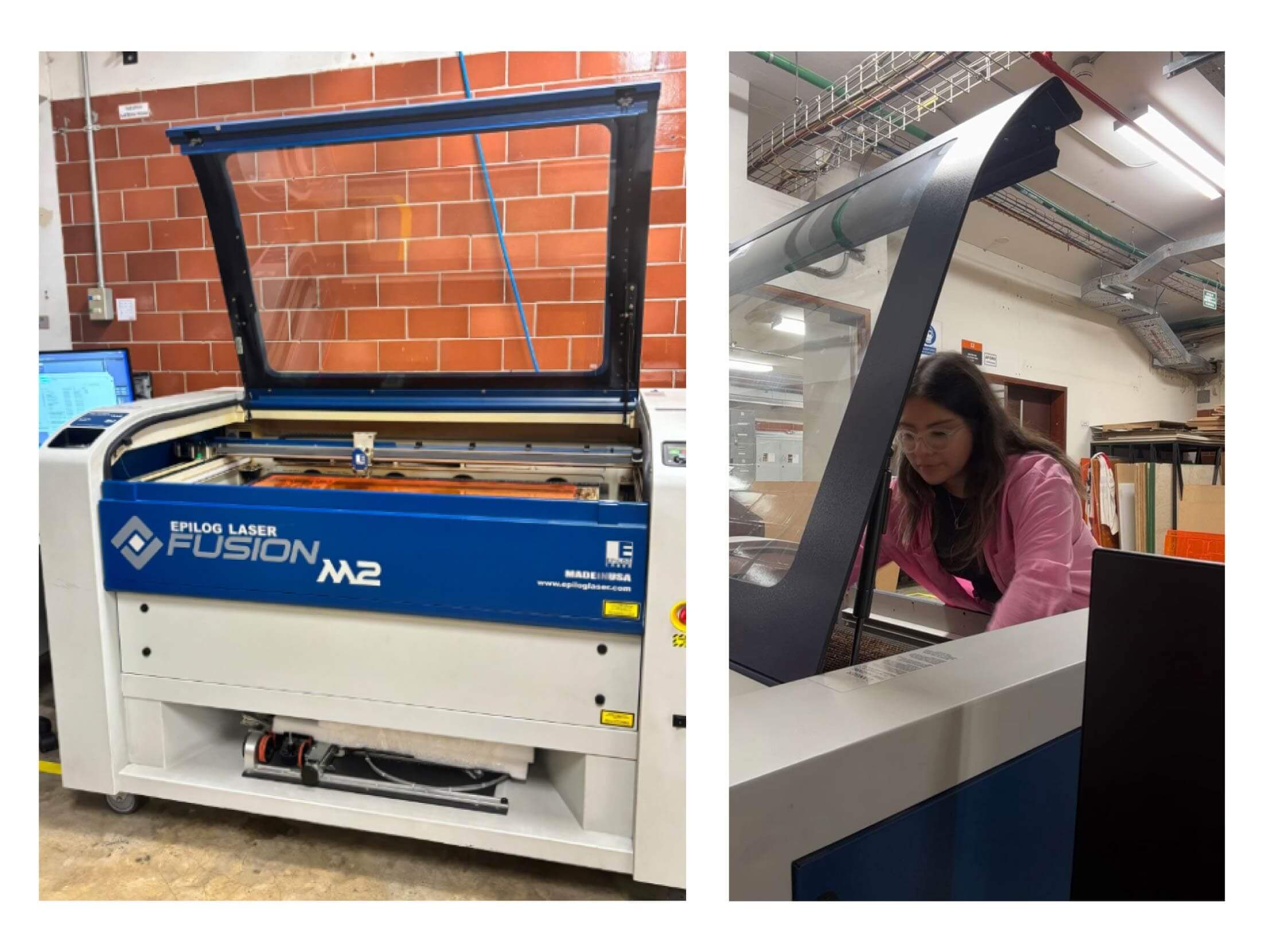
Setting the EPILOG LASER FUSION MS 30W.
The laser cutter that we have in the lab is the Epilog Laser Fusion M2 of 30 Watts for an area of 1000mmx70mm maximum. I have used before this machine in 2019 for the group studies of architecture students interested in digital fabrication called CEFADI. However I did an intro again with more detailed in how to used this machine.
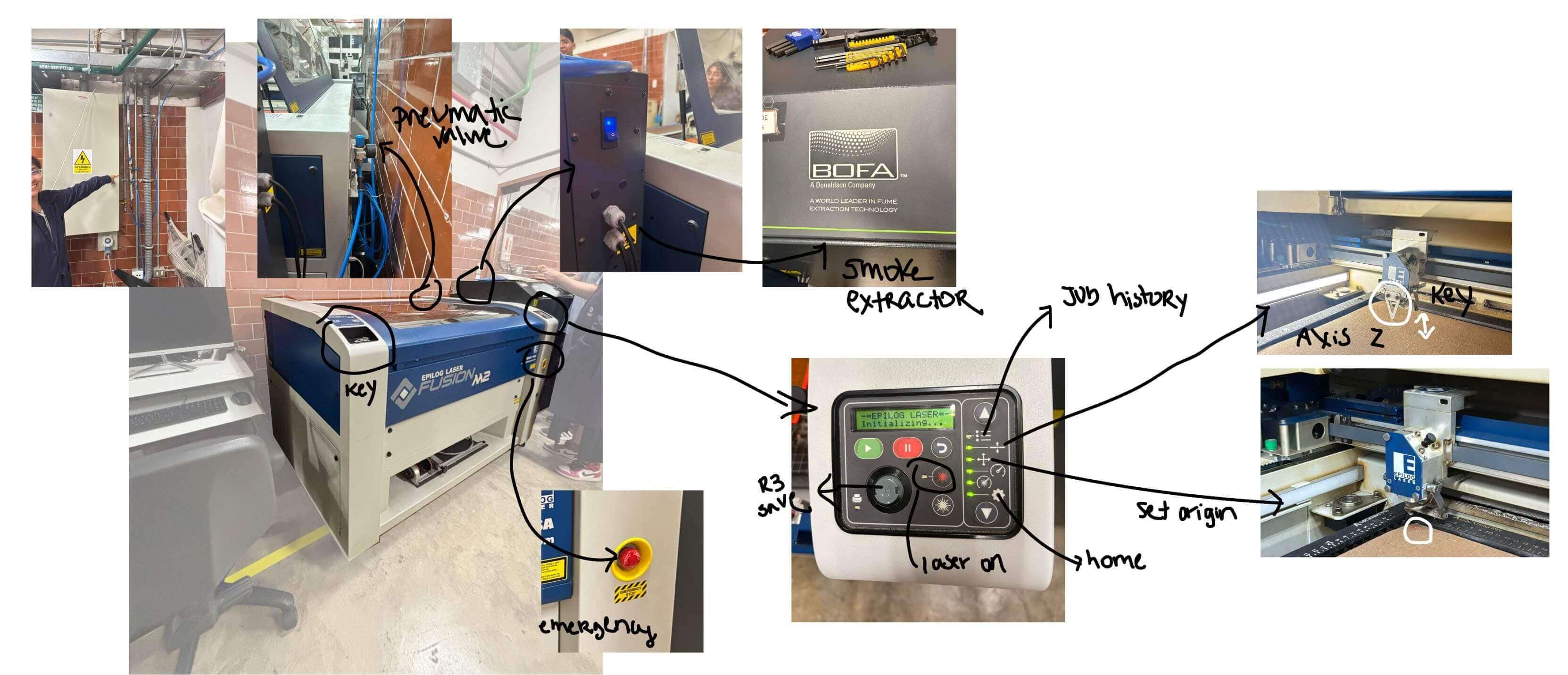
SETTINGS BEFORE CUTTING
So, to start using the laser cut First we have to set up everything in the machine an then on our document.
l a s e r c u t t e r material settings
We did some tries in many materials to test the cut and engraving settings. Some of the materials I tried were acrylic and white cardboard.
Once I understood the best settings for each material I did some final summary in this circles that also checked the tolerance of the material depending on its thickness. For example the white cardboard of 2mm fit with a space of 1.65mm. And the acrylics worked with a space of almost 2.50mm instead of 3mm.
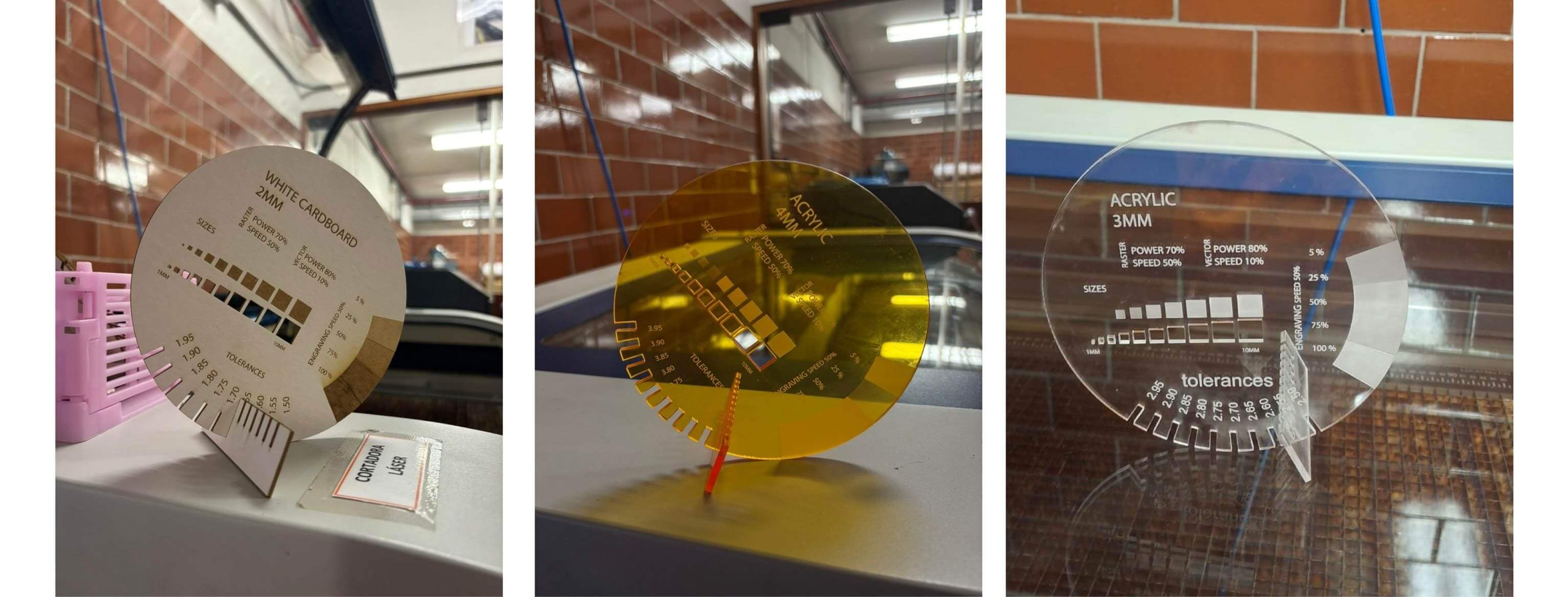
Final settings for white cardboard and acrylic
I also tried everything from flexible material and tolerance for joints in the white cardboard material for my parametric kit construction since I had lots of this material still util residue from my thesis model. So I wanted to try with this material I have been saving.
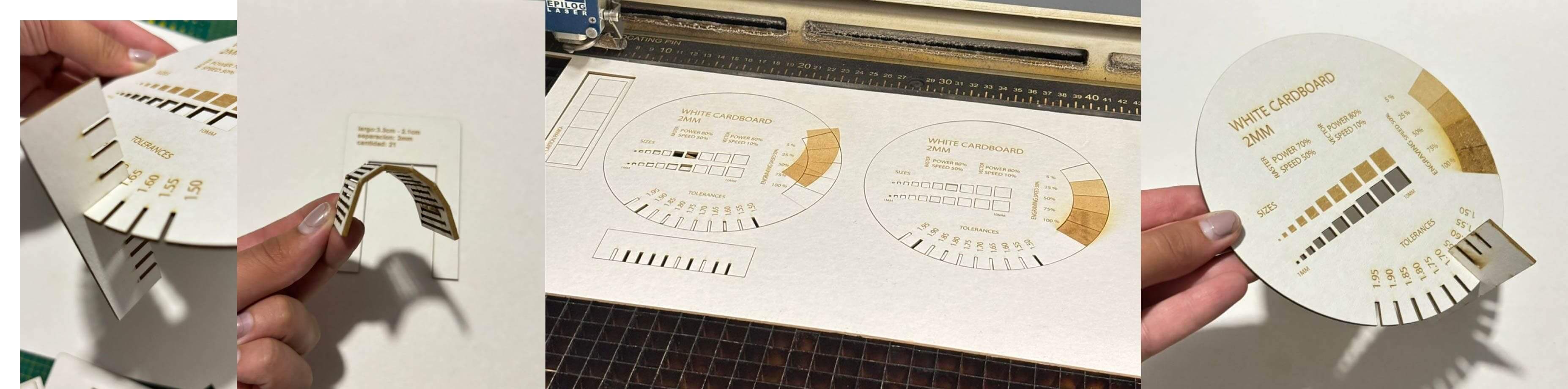
It was very important to check the spacework in the Illustrator archive (that is the software this laser cutter works in dxf documents) because when I first move the placement on Illustrator and it moved.
This happened because I did not checked if on the preference settings before printing the piece size (the space to cut) was smaller then the actual size of the space of 1000x700mm this machine has. Once I change this to the entire space values the preview updated and I could see all and not move anything manually on illustrator, because it changes everything on the settings!.
INDIVIDUAL ASSIGNMENT
v i n y l c u t t e r
The vynil cutter in the lab is the Silouette CAMEO
I had used this machine in the CEFADI team in 2019 when I was in second year of undergraduate, where we made some masks in thin cardboard to see how we can make it fold exaclty where we wanted.
2019 tests in vynil cutter with thin cardboard
p r o c e s s
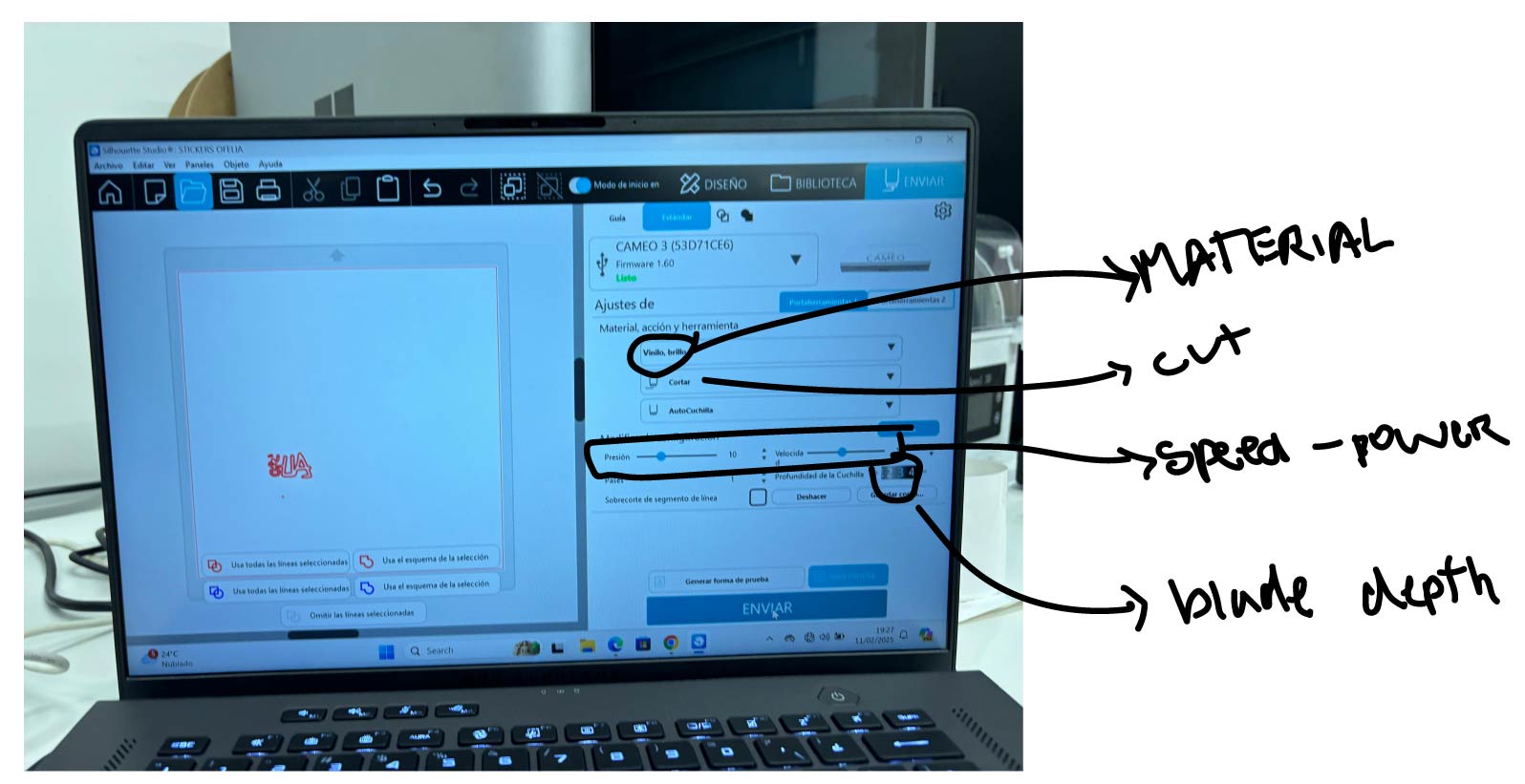
settings
First, I had to install the Silouette app and selected the
Material: in this case glossy vynil
To cut and the blase depth in this case 3.
The power and speed as the laser cutter. Here I didnt change the default settings since it is vynil.
Finally stick the material in the base and charge the material. Then send the work and wait.
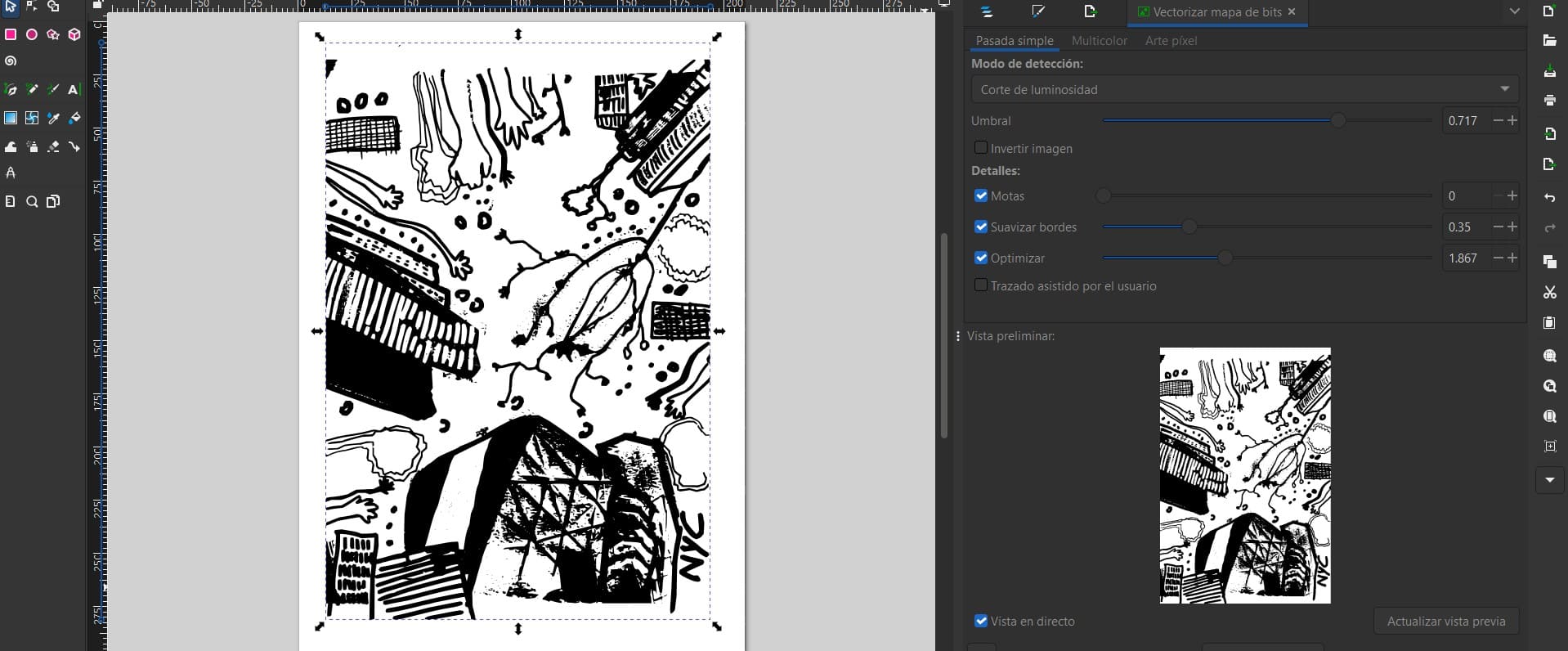
Vectors from my drawing
Transfer sticking process
I wanted to cut the stokes of the digital drawing from my cyanotypes. So, I quickly got them on Inkscape. Here I got to adjust some figures by editing the umbral of the strokes to be more detailed or thinner. I select the less thinner so I can get more stroke area.
I had to select just one part of the entire stoke because the base of our vynil cutter was damaged and we had to improvise with thick acetate we had to manueally cut and It looked like it wasn't thick enough as the original base because once it was charged it moved if the drawing was to small since the the nozzle had to move a lot and very fast. Still I tried and finally I got that small sticker in my phone case.
I only managed to cut some strokes and my name. However the big ones went wrong since I send another work smaller but didn't change the placement and cut over the one that went right. But I still got cool strokes from my drawing and my name in my laptop.
p a r a m e t r i c C o n s t r u c t i o n K I T
I M A G I N A R Y T R E E
A parametric construction kit for an unlimited and imaginary tree.
t h e p r o c e s s
From my cyanotypes drawings I got to the idea of making my imaginary city. First I wanted to make a construction kit by buildings, drawing different facades an joining them but the idea got me stuck in boxes. So looking at my drawings of cities, nature is also very important in a city. And I like to draw very organic an unusual kind of shapes we are used to see for nature. That is how I got to this parametric tree kit.
idea sketches from my cyanotypes vectors
settings
To understand how the pieces would assembly following the thickness of the material I had to make a draft manually to identify all the holes will depend on the thickness. I did the parametric joints in Free cad with spreadsheets and just one reference on the thickness. So if I changed the material everything changes but not only the thickness of the holes but also the scale of all.
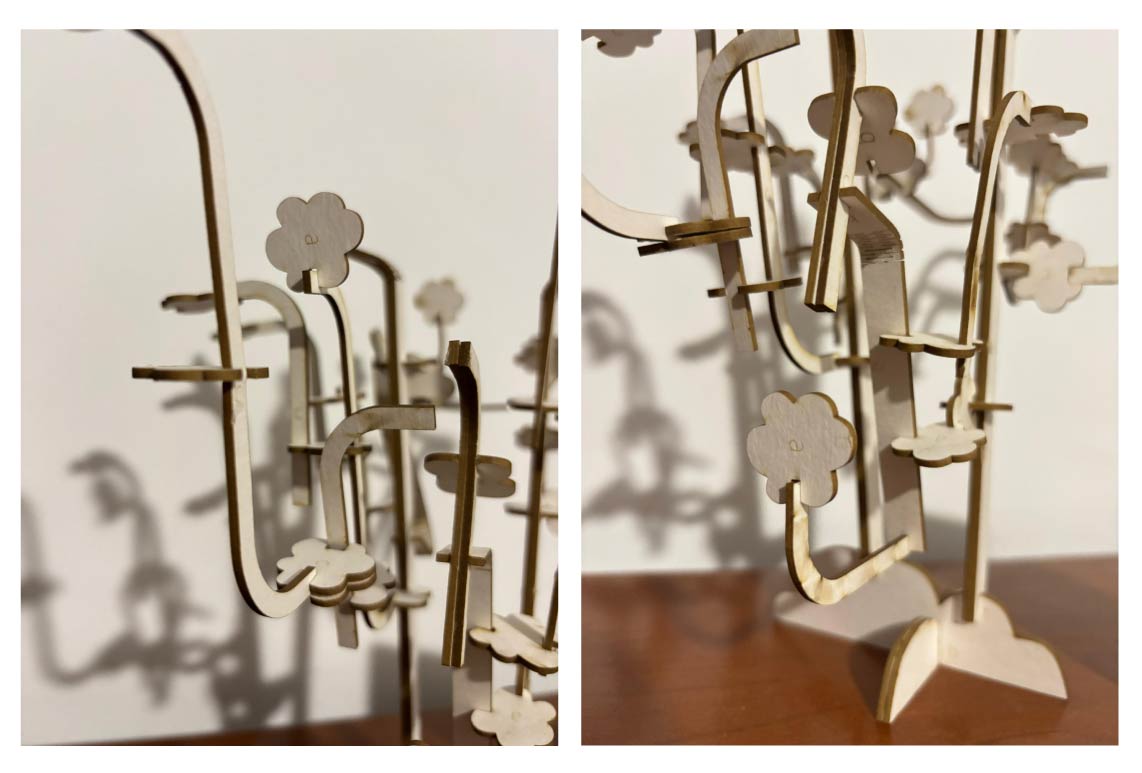
Joints
p i e c e s and a s s e m b l y
For the tree I will nedd a base, a trunk, branches and flowers. Being the flowers some extra joints to have branches in more than 2 axes. And some branches will be flat and others curves with a flexible pattern.
idea sketches to understand the pieces
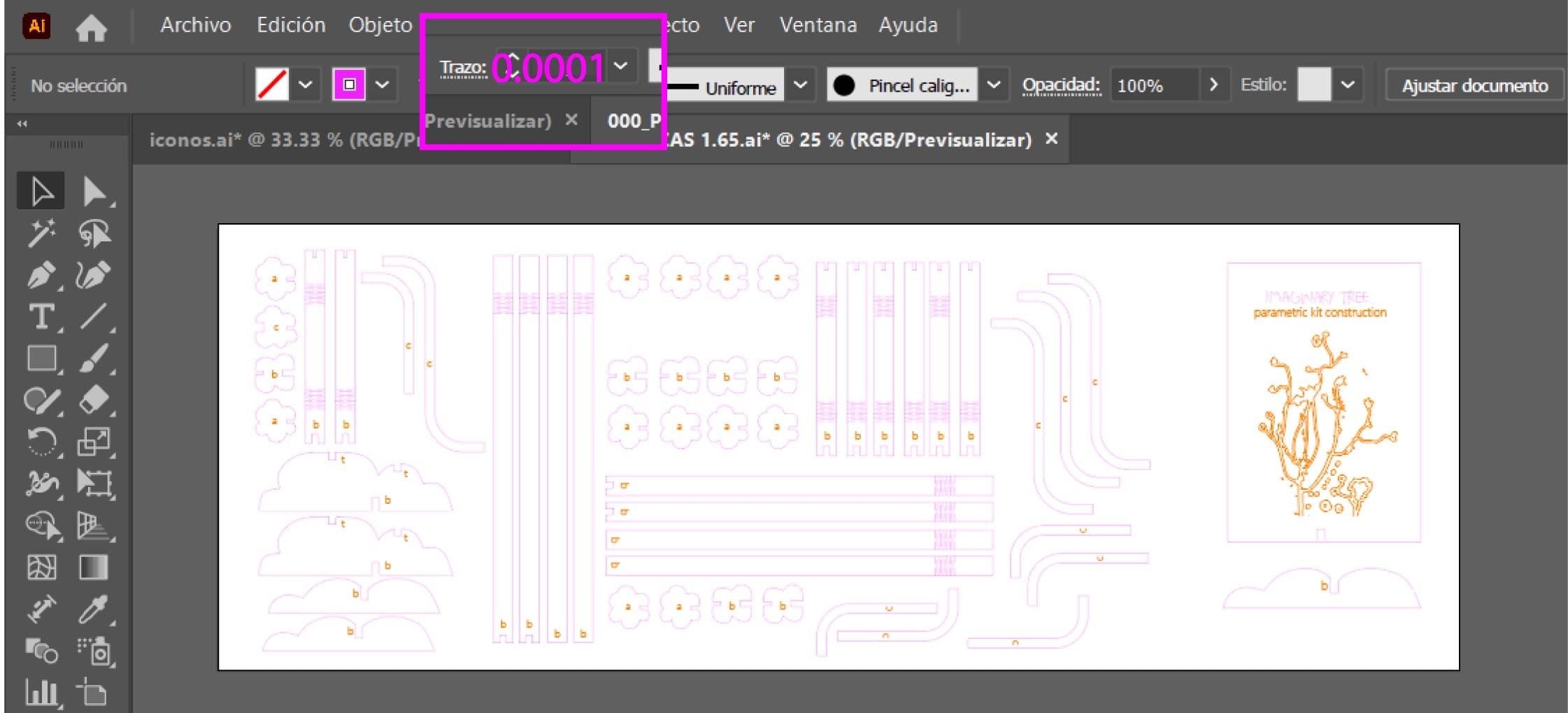
settings
When I got the tolerance og 1.65mm for this white thick cardboard of 2mm I changed the value on freecad and export the pieces in .DXF format. It is very important to remember for the lines to cut separate on another layer from the engraving and to assign 0.001 of stroke to the machine identifies to cut.
construction process
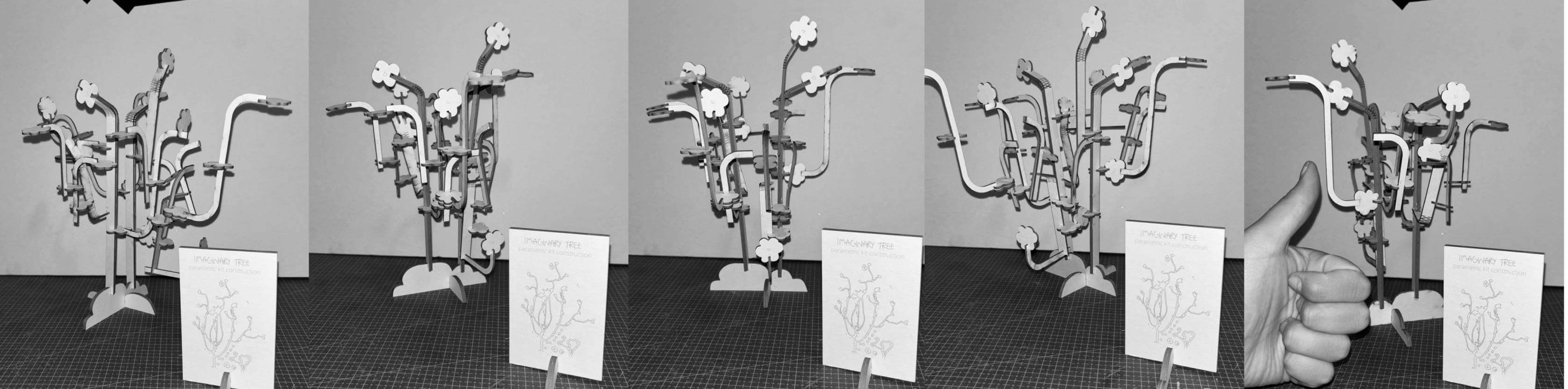
Final Iterations from changing joints and pieces
INDIVIDUAL ASSIGNMENT
v i n y l c u t t e r
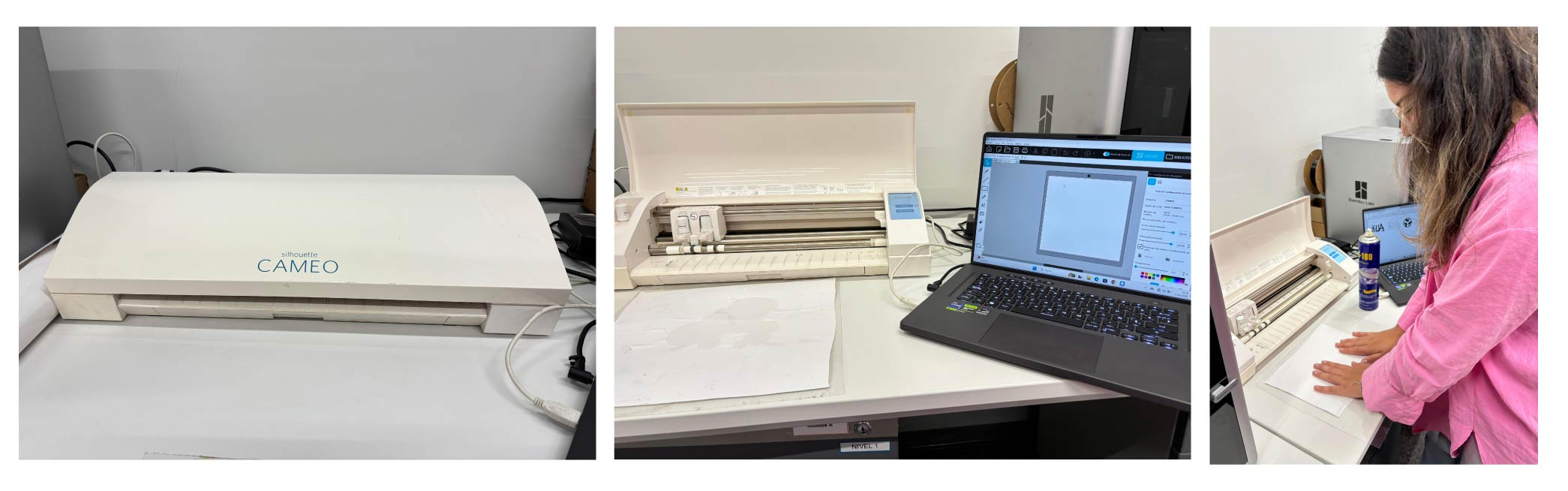
The vynil cutter in the lab is the Silouette CAMEO
I had used this machine in the CEFADI team in 2019 when I was in second year of undergraduate, where we made some masks in thin cardboard to see how we can make it fold exaclty where we wanted.
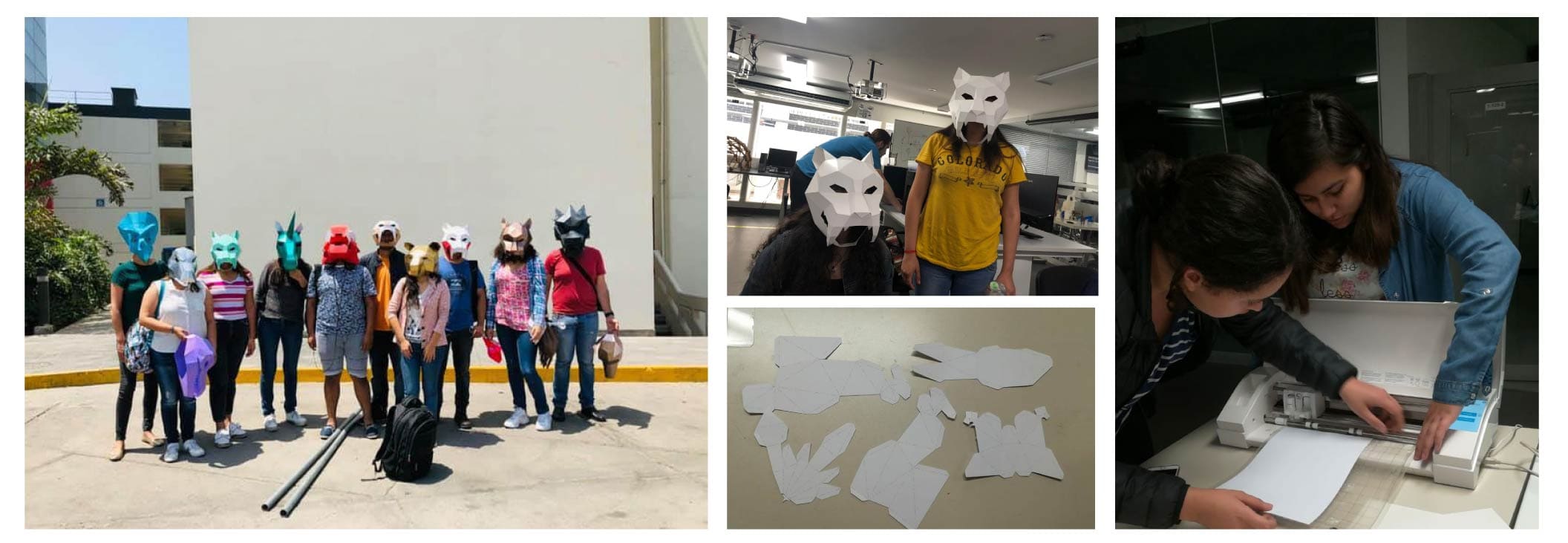
2019 tests in vynil cutter with thin cardboard
p r o c e s s
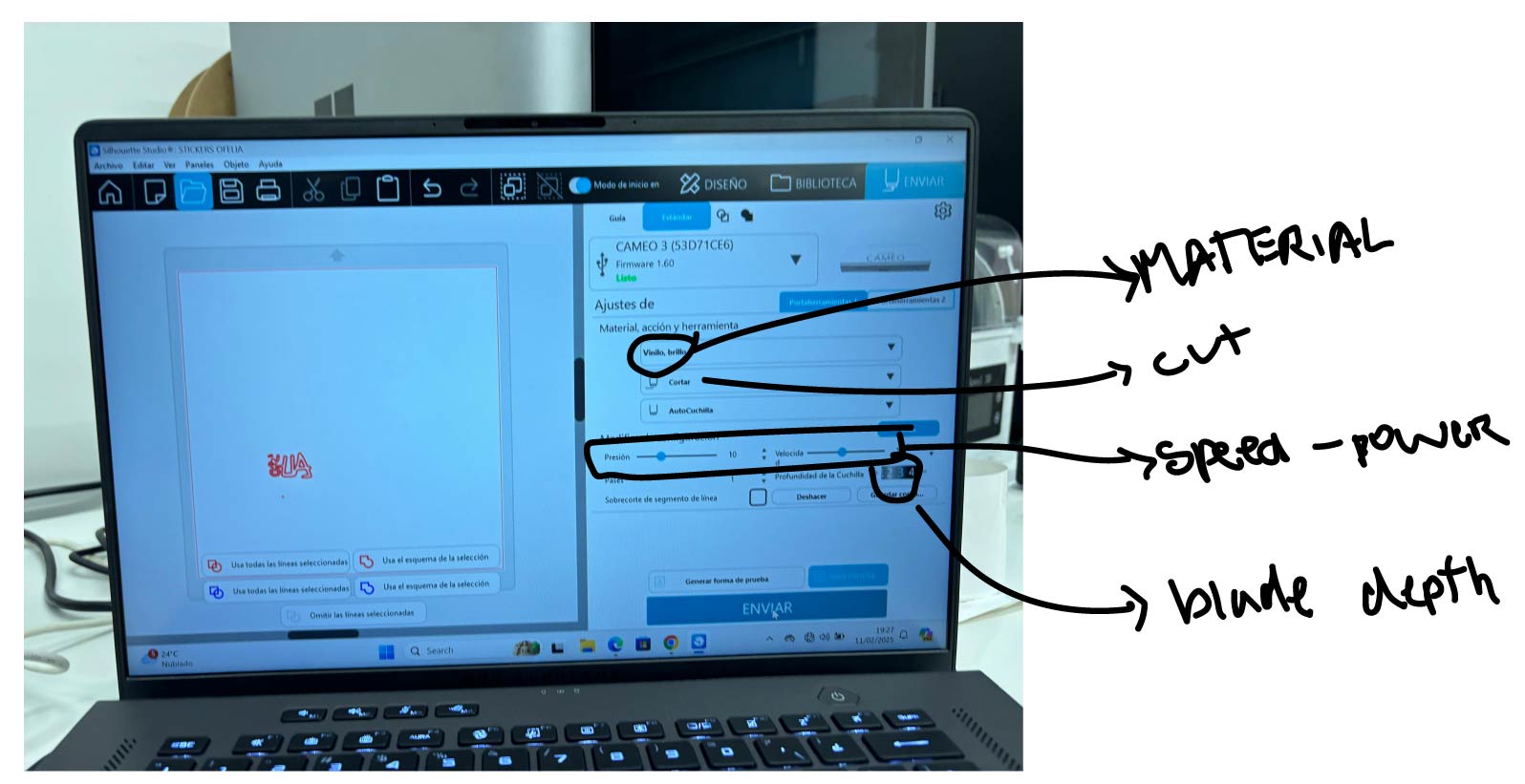
settings
First, I had to install the Silouette app and selected the
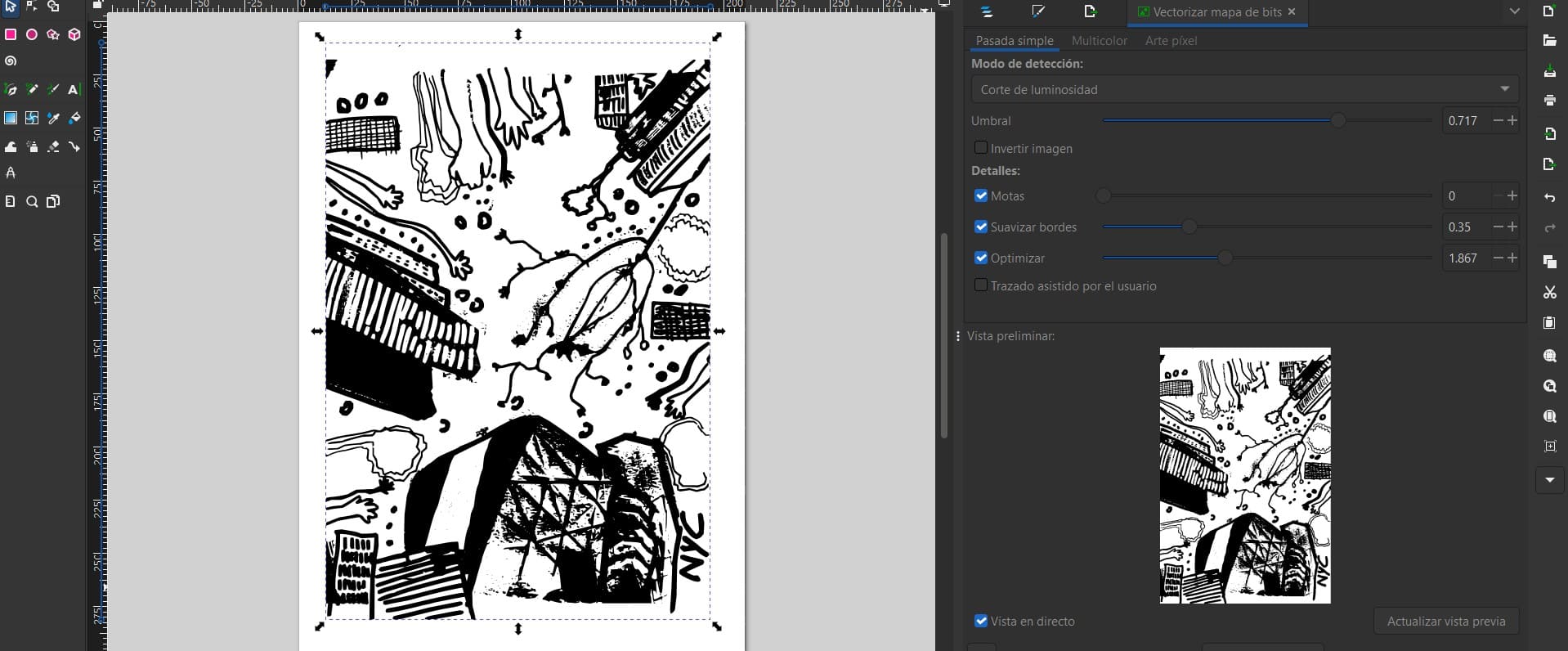
Vectors from my drawing
Transfer sticking process
I wanted to cut the stokes of the digital drawing from my cyanotypes. So, I quickly got them on Inkscape. Here I got to adjust some figures by editing the umbral of the strokes to be more detailed or thinner. I select the less thinner so I can get more stroke area.
I had to select just one part of the entire stoke because the base of our vynil cutter was damaged and we had to improvise with thick acetate we had to manueally cut and It looked like it wasn't thick enough as the original base because once it was charged it moved if the drawing was to small since the the nozzle had to move a lot and very fast. Still I tried and finally I got that small sticker in my phone case.
I only managed to cut some strokes and my name. However the big ones went wrong since I send another work smaller but didn't change the placement and cut over the one that went right. But I still got cool strokes from my drawing and my name in my laptop.
p a r a m e t r i c C o n s t r u c t i o n K I T
I M A G I N A R Y T R E E
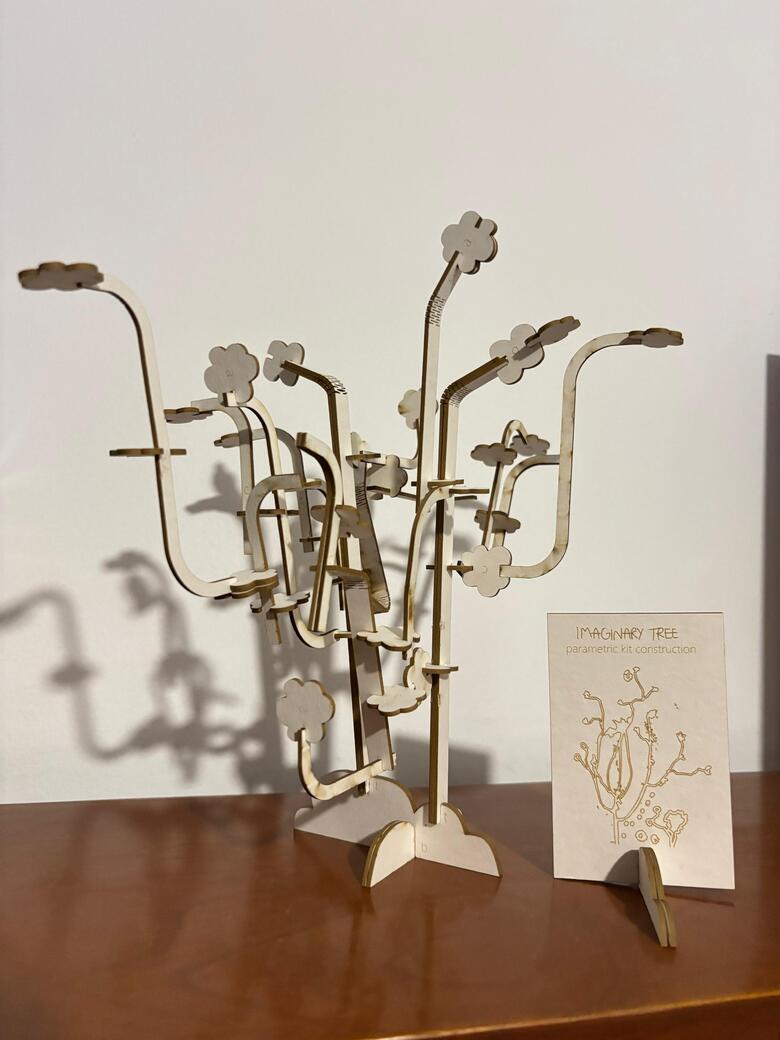
A parametric construction kit for an unlimited and imaginary tree.
t h e p r o c e s s
From my cyanotypes drawings I got to the idea of making my imaginary city. First I wanted to make a construction kit by buildings, drawing different facades an joining them but the idea got me stuck in boxes. So looking at my drawings of cities, nature is also very important in a city. And I like to draw very organic an unusual kind of shapes we are used to see for nature. That is how I got to this parametric tree kit.
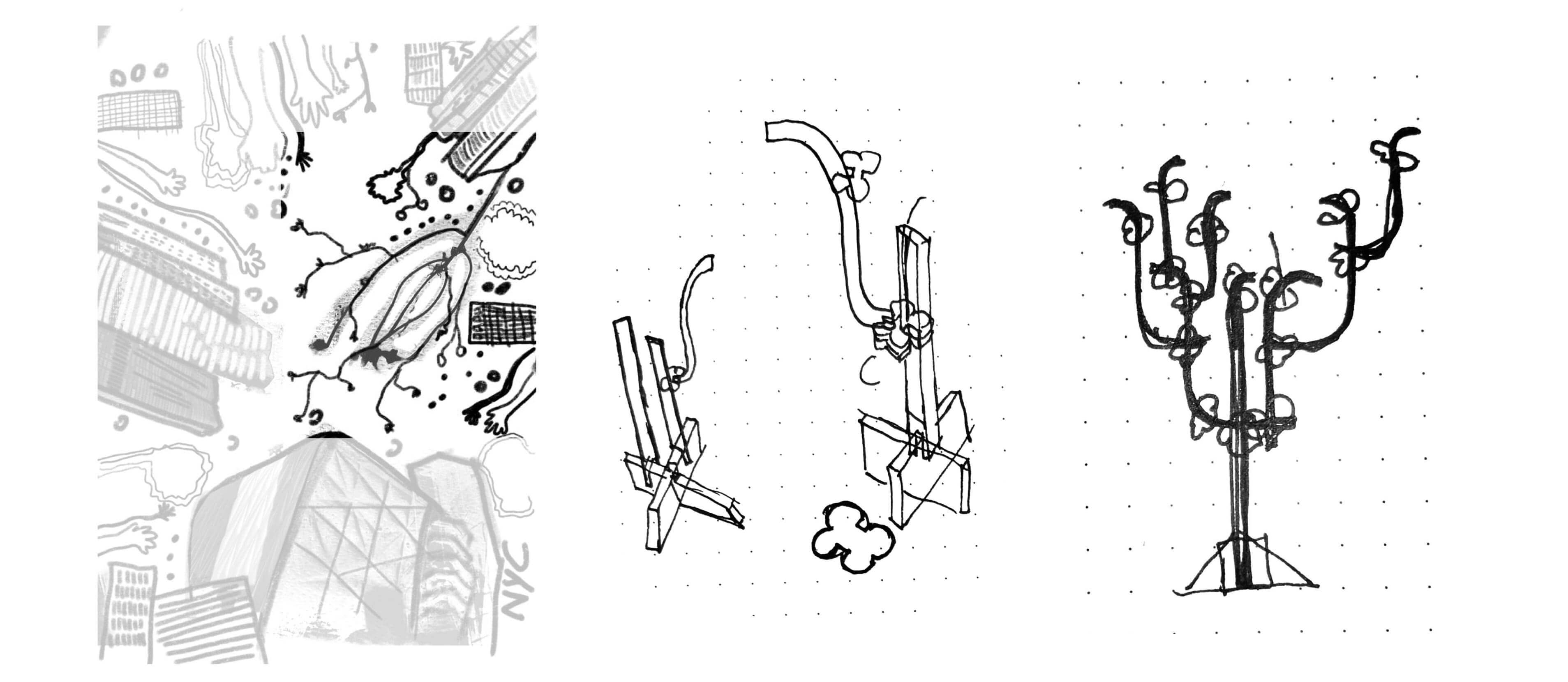
idea sketches from my cyanotypes vectors
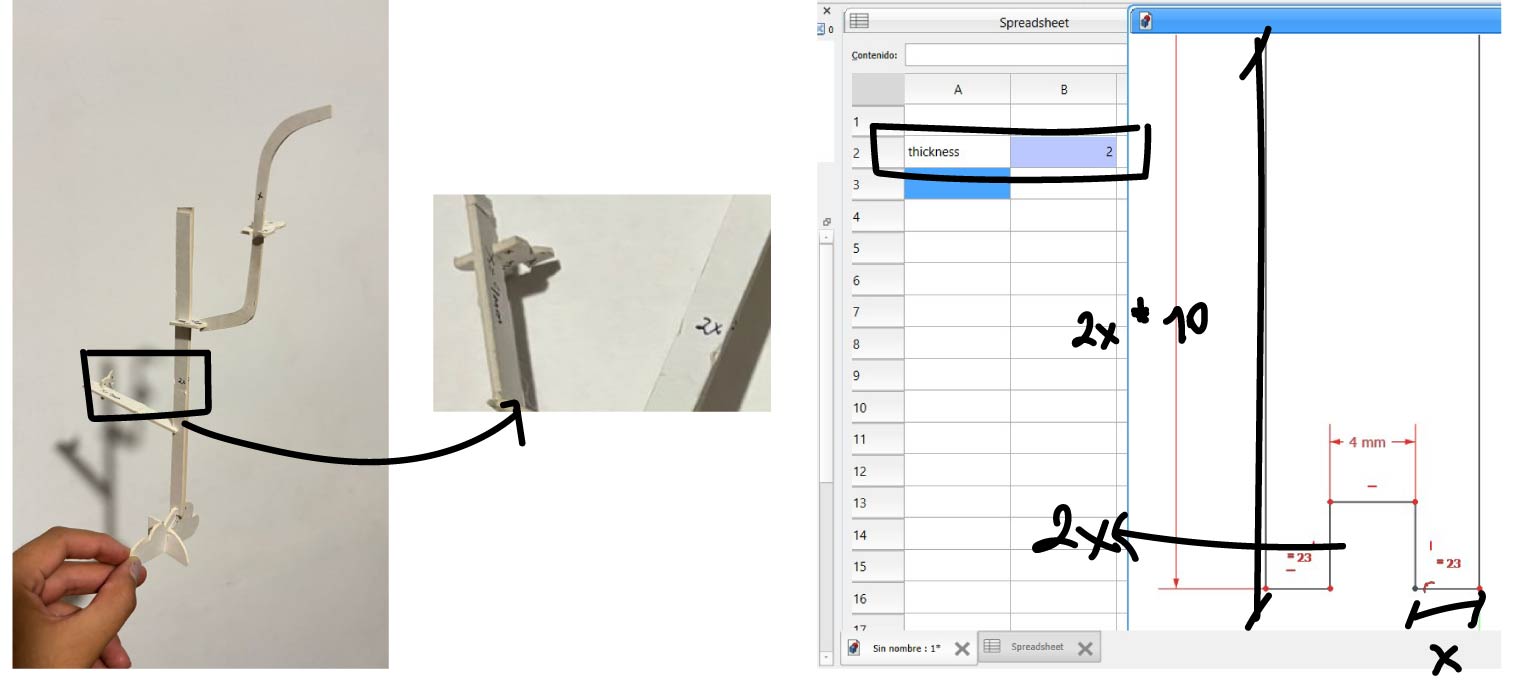
settings
To understand how the pieces would assembly following the thickness of the material I had to make a draft manually to identify all the holes will depend on the thickness. I did the parametric joints in Free cad with spreadsheets and just one reference on the thickness. So if I changed the material everything changes but not only the thickness of the holes but also the scale of all.
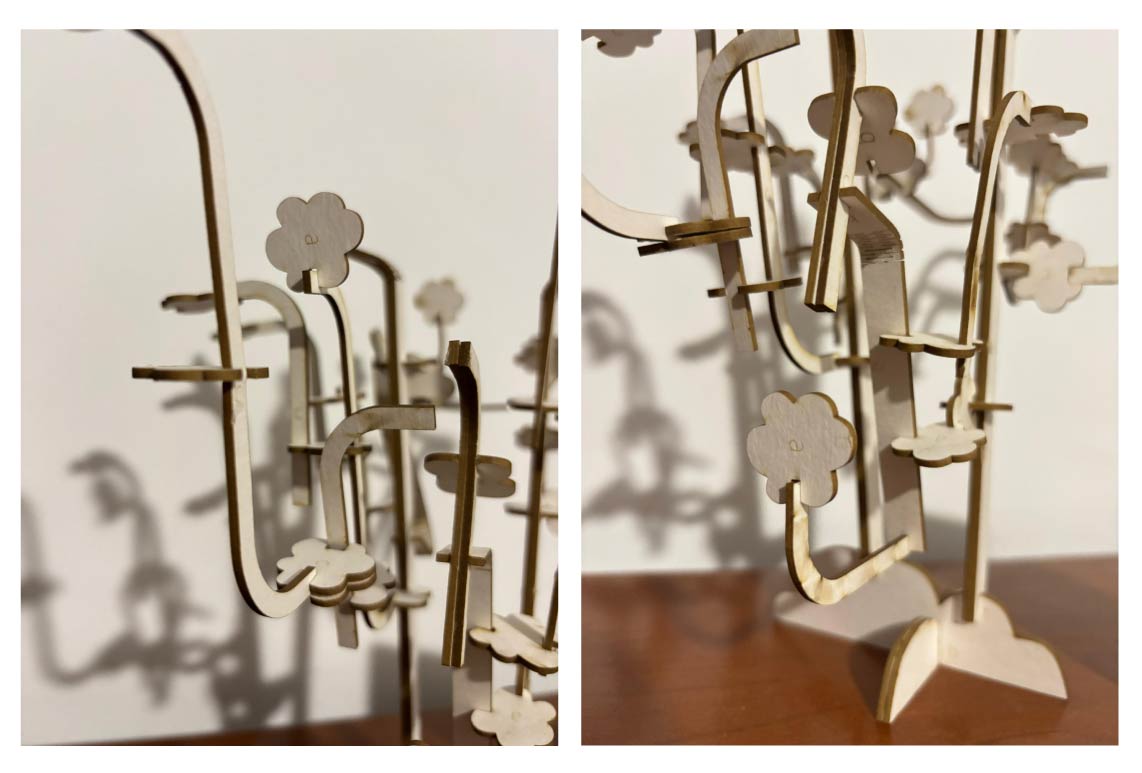
Joints
p i e c e s and a s s e m b l y
For the tree I will nedd a base, a trunk, branches and flowers. Being the flowers some extra joints to have branches in more than 2 axes. And some branches will be flat and others curves with a flexible pattern.
idea sketches to understand the pieces
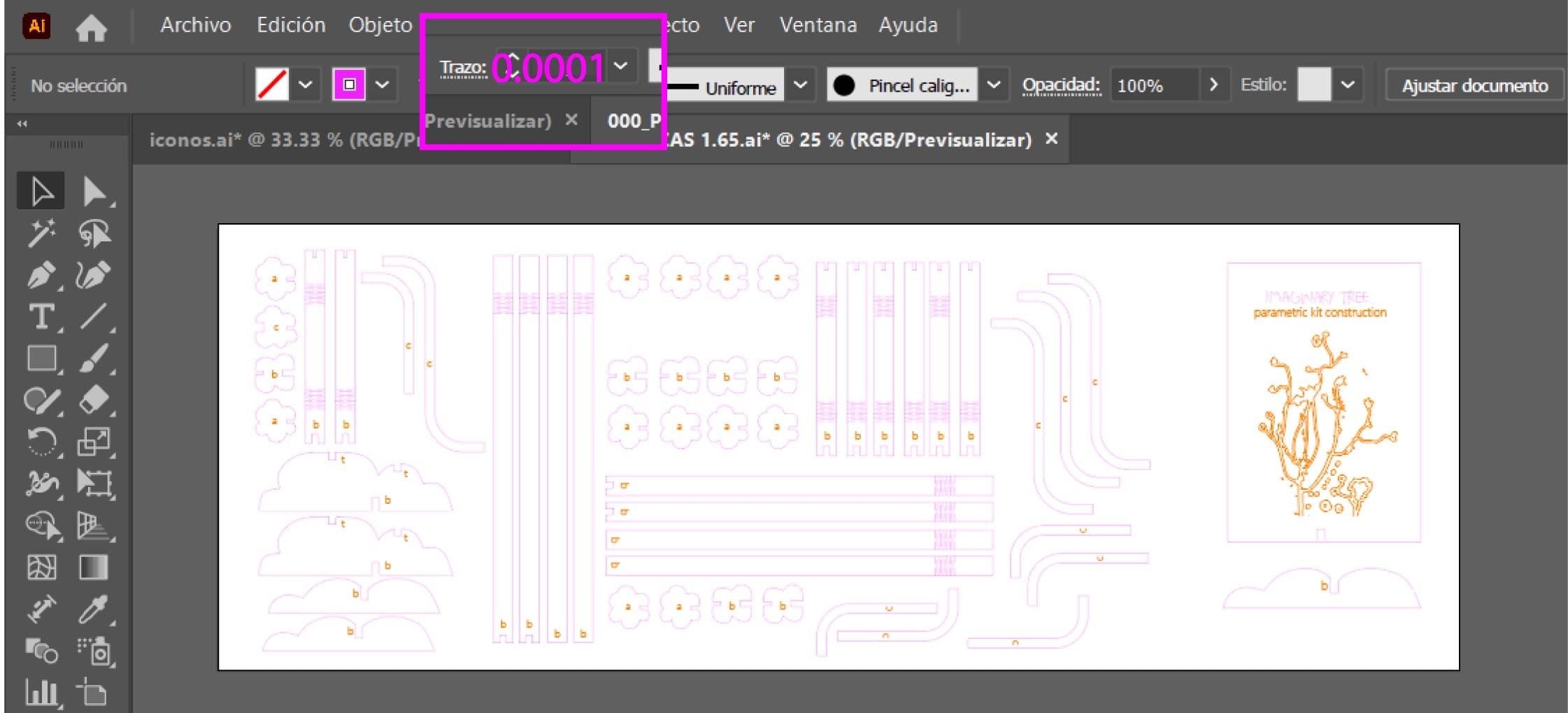
settings
When I got the tolerance og 1.65mm for this white thick cardboard of 2mm I changed the value on freecad and export the pieces in .DXF format. It is very important to remember for the lines to cut separate on another layer from the engraving and to assign 0.001 of stroke to the machine identifies to cut.
construction process
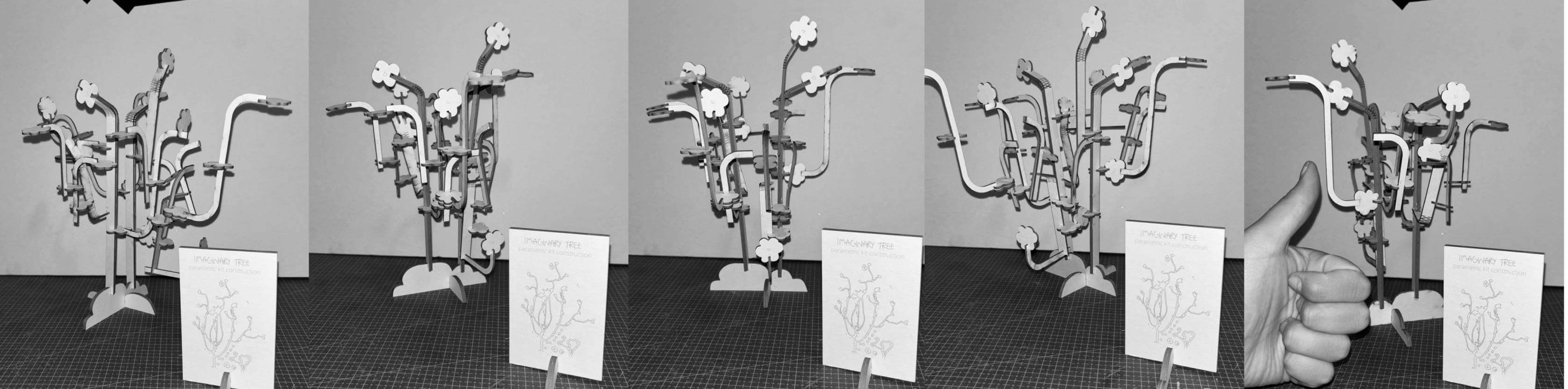