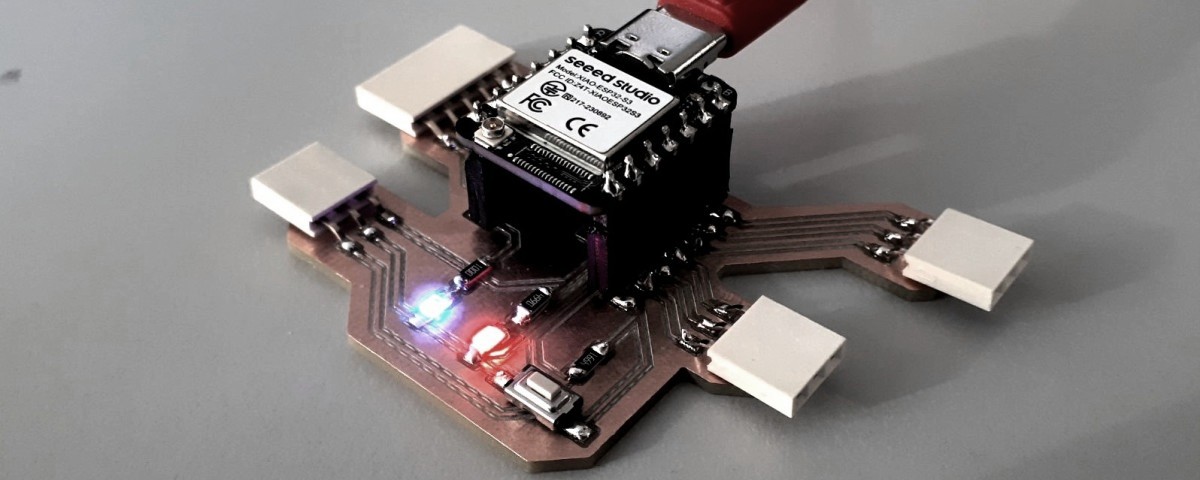
Week 8: Electronics Production
Table of Contents
This week, we learned how to fabricate a PCB based on the design from week 8 using a milling machine. We did so by milling copper-foiled PCB stocks.
This Week’s Tasks
- Group assignment:
- Characterize the design rules for your in-house PCB production process: document feeds, speeds, plunge rate, depth of cut (traces and outline) and tooling.
- Document the workflow for sending a PCB to a board house
- Document your work to the group work page and reflect on your individual page what you learned
- Individual assignment:
- Make and test a microcontroller development board that you designed
In-House PCB Fabrication (Isolation Milling)
For these my notes on the in-house-fabrication process, which was part of the group assignment, the pictures were taken and assembled by me and the text was adapted with changes from Benedikt’s website. The page of the group assignment at the lab’s page can be found here.
For PCB fabrication there are different possibilities. The one that is used in Fab Labs is milling traces out of a sheet of hard paper with a layer of copper. This material is also called FR-1 (fire retardant). There are several more types of fire retardant materials (FR-2, FR-3, …) as well, but FR-1 is used, since it is easiest to mill them.
Milling PCBs to other materials might lead to end mills wearing down more quickly. Apart from that, the dust from other materials (e.g. FR-4) might be poisonous. This article describes how to combine using a milling machine and a laser.

A flat machine bed is crucial for achieving accurate results. To ensure this, Ferdi milled the entire bed flat. To reduce machining time, we used a 6 mm flat end mill with the 6 mm collet for the Carvera. To change the collet, we used the official tool provided by Makera. If an end mill is too large for the tool changer, it can be manually changed using the following commands:
1M490.1 # Tightens the spindle collet to secure a new tool
2M490.2 # Loosens the spindle collet and releases the current milling bit

To test the capabilities of our Carvera, we used Neil’s test. For milling, we used a 0.2 mm V-bit for the traces and a 0.8 mm end mill for the outlines.

Other sources for milling bits are:
- https://www.gis-tec.com/deutsch/d_fraeser_fpcb_mc.htm
- https://www.gis-tec.com/deutsch/d_fraeser_fpcb_uc.htm
For the tool path generation we were using mods (see the documentation of my own board for details). It provided two pre-configured programs for the machine, we used the default cutting parameters. The only adjustments we made were to the tool diameters, offset number, cut depth, and max cut depth to accommodate the use of FR-4 with HSS end mills:
Parameter | Value |
---|---|
Tool 1 | 4 |
Tool 1 diameter (mm) | 0,2 |
Cut depth 1 (mm) | 0,12 |
Max depth 1 (mm) | 0,12 |
Offset number 1 | 4 |
Offset step-over 1 | 0,5 |
Tool 2 | 3 |
Tool 2 diameter (mm) | 0,8 |
Cut depth 2 (mm) | 0,3 |
Max depth 2 (mm) | 1,5 |
Offset number 2 | 1 |
Offset step-over 2 | 0,5 |
Cut speed | 8 mm/min |
Plunge speed | 4 mm/min |
Spindle | 16.000 rpm |
To achieve optimal results and minimize the risk of breaking mill bits, we ensured that our PCB stock material was perfectly flat. Normally, this is done using a straight edge, but since we didn’t have one readily available, we used a caliper gauge. Holding it against the back of the material while looking towards a light source allowed us to check for gaps. If gaps were present, we carefully bent the stock material until it was as flat as possible.

Fixturing Using Tape
To secure the stock material on the machine bed, we used thin, non-reinforced double-sided tape. In general, the cheapest double-sided tape works best—reinforced tapes should be avoided as they can create uneven surfaces. For proper adhesion while still allowing easy removal, we applied three strips of tape across the entire width.



Fixturing Using a Vacuum Pump
Later during the course, Benedikt and Ferdi built a vacuum-table component for the Carvera. Small PCBs can be fixtured by putting them above the pocket in the lower left corner. If the stock is not big enough to cover all holes, they have to be covered otherwise, such as with tape or other pieces of PCB stock.


Milling
There are three ways to correctly set the Z = 0 position:
- Using the machine’s wireless probe.
- Using a multimeter in continuity test mode (or a dedicated continuity tester) by placing probes between the copper layer and the V-bit, then slowly lowering the Z-axis in small steps.
- Listening for the V-bit (or the fat end mill) scratching the copper layer—this should also be done slowly and in small steps. Note, that it is important to turn on the spindle to do that. This can be done using the G-code:
M3 S5000
. TheS
parameter specifies the speed of the spindle. To turn off the spindle, useM5
.
We then milled the PCB.

Afterwards, the PCB needed to be cleaned. This was done in two steps:
- Scratching with a razor blade or the blade of a utility knife over the surface. Thereby the angle of the blade w.r.t. the traces when looked from above was 45 degrees. The angle of the blade w.r.t. the surface of the board surface when looked from the side was sharp. The blade was pulled, not pushed. This was done once in one direction and then from the opposite direction after turning the PCB.
- Cleaning residuals with steel wool.
The final result looked as follows.

- the smallest distance between traces was 0.007inch (0.1778mm)
- the thinnest trace was 0.01inch (0.254mm) Although these are the minimum requirements, it should be considered to have settings that go a bit higher in the numbers since these are the minimum requirements just before the PCB not being functional anymore.
In the regional review, Henk gave some additional hints:
- KiCad did not recognize design rules properly for 45-degree-angled traces. Therefore, the distance between 45-degree traces should be visibly higher than the distance between horizontal or vertical ones.
- He suggested to have more conservative settings for the minimum distance between traces. This would give more flexibility.
- If one wants to mill 2-sided PCBs, it was advised to use vias. The ones Henk used were of diameter 0.6mm and 0.8mm. They were to be riveted and then soldered to the board.
The minimum size of drill holes is dependent on the drilling tool we have. We do not use a drill, but a flat end mill. When generating the tool path, I noticed that there was no path generated for the holes. That could be fixed by making the holes slightly bigger than the end mill. Therefore, 0.9mm can be adopted as a minimum hole diameter.
How to Board House
When ordering boards from a board house, you need to choose a board house first. One of the possible ones is JLCPCB.


.gerber
files from KiCad and zip them.
.zip
file to the website.


Fabricating an own PCB
Applying the Design Rules
Going back to the board, I designed in one of the previous weeks, the design rules were not known by then. Therefore it was possible that there are design rule violations in the design. The task now was to fix those violations. Given the rules for designing a PCB, they were to be told to KiCad, so the DRC can check if they are fulfilled.






Note that when drawing tracks, they are drawn with the minimum track width. The minimum track width can hence be changed if one does not want to adjust the track width manually after drawing.
Generating the Tool path
To generate a tool path, 2D images with colors black and white resembling the traces, edges, and holes of the PCB are to be loaded into mods. Those images need to be generated. Alternatively, one can export PDF files with the black-white images directly from KiCad. I might use this workflow in the following weeks, but in this week I went with the first approach. Alternatively, FlatCAM can be used to generate tool paths from .gerber
files. The tool pcb2gcode was suggested as well.
To generate the images, I first exported the relevant layers for fabrication as .gerber
files. The shown menu can be reached via ‘File’ > ‘Fabrication Outputs’ > ‘Gerbers’. The relevant layers were all copper layers ‘Cu’, and ‘Edge.Cuts’. Clicking ‘Plot’ created the corresponding .gerber
files in the given output directory. My design also included drill holes, so I also needed to generate the drill files (clicking on the button on the lower right).







1#!/usr/bin/env python
2
3# usage:
4# `clean_pcb_png.py name_of_image.png`
5
6from PIL import Image
7import numpy as np
8import typer
9from pathlib import Path
10
11def main(img_path: Path, threshold: int = 128):
12 suffix = img_path.suffix
13 stem = img_path.stem
14 directory = img_path.parent
15
16 # Open the image and convert to grayscale
17 image = Image.open(img_path).convert("L")
18 dpi = image.info.get("dpi")
19
20 # Apply threshold
21 binary_image = image.point(lambda p: 255 if p > threshold else 0)
22
23 # Save the binary image
24 save_kwargs = {"format": "PNG"}
25 if dpi:
26 save_kwargs["dpi"] = dpi
27 output_path = Path(directory) / f"{stem}_binarized{suffix}"
28 binary_image.save(output_path, **save_kwargs)
29
30if __name__ == "__main__":
31 typer.run(main)
In the following, it is shown how to generate the tool path for a PCB.


- Tool 1 (engraving)
- diameter: 0.2 (depends on the bit used)
- cut depth: 0.12 (default)
- max depth: 0.12 (default)
- offset number: 8
- offset step-over: 0.5
- Tool 2 (cutting)
- diameter: 0.8 or 1 (depends on the bit used)
- cut depth: 0.6
- max depth: thickness of the stock (minus 0.3mm if a vacuum table was used)
- offset number: 1
- offset step-over: 0.5
The generated tool path. Note that there are some parts of the path that are actually not desired at the locations of the tabs. This could be fixed by deactivating tabs or making the tabs longer. Furthermore it can be seen that some traces are not milled properly. I did not notice this at that point, but for future, it is very important to check that for milling.
For generating the tool path for drilling the holes, there are two options. The first one is to use the generic mods program for generating G-code for milling 2D PCBs.


Milling
I then milled the PCB. The first step was again to set the working coordinate system of the Carvera to zero at the corresponding point.







Soldering
It is possible that the human body charges up itself. Then, when touching something, the charge could be transferred to the touched object. This could become a problem when soldering. The body could discharge to the electronic components one touches when soldering. This effect is called electrostatic discharge (ESD). In the worst case this could destroy components and lead to a malfunctioning circuit. Therefore, one has to ground oneself. One can do this by either touching the GND of a power socket or by wearing a grounding wristband. This wristband is connected to an ESD-safe soldering mat, which itself is connected to the GND of a power socket. Additionally, if one uses tools to touch the components to be soldered, only those tools are to be used that are ESD-safe.
This is what you do if you do it by the book. However, following the experience of my instructor and that of my peers and me, it happens rarely that ESD occurs and a component breaks as a consequence of that. The parts we are soldering are considerably cheap, so it would be annoying at most, but not too tragic if one breaks. However, if one solders very expensive components, it is definitely advised to take care of ESD protection.
I then soldered everything together. I started with soldering pins onto the ESP32 to be able to in combination with the pin sockets remove it from the PCB if needed.





I then started soldering the PCB itself.






When soldering it is to be made absolutely sure to cover the whole solder iron tip in soldering tin during and also after soldering. Otherwise the tip would oxidize and would not be able to take any more tin. One could then not solder with that iron anymore without proper cleaning.
I then added the following code to the ESP32 using the Arduino IDE. The code lets the blue LED blink and when the switch is activated, the blinking rhythm is changed.
1const int led = D6;
2const int btn = D7;
3
4// the setup function runs once when you press reset or power the board
5void setup() {
6 // initialize digital pin LED_BUILTIN as an output.
7 pinMode(led, OUTPUT);
8 pinMode(btn, INPUT);
9}
10
11// the loop function runs over and over again forever
12void loop() {
13 digitalWrite(led, HIGH); // turn the LED on (HIGH is the voltage level)
14 if(digitalRead(btn) == HIGH){
15 delay(50); // wait for a second
16 } else {
17 delay(200);
18 } // wait for a second
19 digitalWrite(led, LOW); // turn the LED off by making the voltage LOW
20 delay(100);
21}

Reflections
What I Learned
- The process of milling PCBs and SMD soldering.
What Went Wrong
- I spent a lot of time debugging the tool path generation due to erroneous
.png
images and wrong tool settings.
What Went Well
- The assignment was finished on Sunday.
What I Would Do Differently
- Given the knowledge I have now, I would just be faster with the tool path generation. Otherwise, the process was straight forward.
Digitial Files
- Adjusted KiCad files
- Gerber Files
- Tool paths
Use of Language Models
I did not use any language models for this assignment.