System Integration
Tasks for this week
- Individual Assignment: Design and document the system integration for the final project
Design and Documentation for System Integration of Butterfly-The Infinity Plotter
The Butterfly-The Infinity Plotter is a compact and efficient XY plotter designed using three omni-wheels, stepper motors, an ESP32 microcontroller, and a Bluetooth module. This document outlines the integration of the system, detailing the components, features, design parameters, and the bill of materials (BOM). The design aims to provide a precise, versatile, and cost-effective plotting solution for various applications.
System Integration
- Hardware Integration:
- Chassis and Motors:
The plotter is built on a circular chassis made from Acrylic Sheet. Three NEMA 17 stepper motors are mounted using custom brackets. Each motor drives an omni-wheel, allowing for precise movement in any direction.
- Microcontroller and Driver Boards:
An ESP 32 is used to control the plotter, interfacing with three Big Easy Driver boards (one for each stepper motor). The driver boards manage the current supplied to the motors, ensuring smooth and precise motion.
- Power Supply:
The system is powered by a 12V power supply. Voltage regulation is handled by the driver boards and the Arduino’s onboard regulator to ensure the components receive the appropriate voltage and current.
- Chassis and Motors:
- Software Integration:
- G-Code Interpreter:
The plotter features an onboard interpreter that recognizes G-code commands generated by software like Inkscape. This allows for easy conversion of designs into plotting instructions.
- Bluetooth Communication:
An HC-06 Bluetooth module allows the plotter to receive commands wirelessly from a PC or a mobile device. This provides flexibility in controlling the plotter remotely.
- Control Software:
This software is used to send G-code files to the plotter, enabling it to execute complex drawing tasks.
- G-Code Interpreter:
- Mechanical Design:
- Omni-Wheels and Motion:
The three omni-wheels are crucial for the plotter’s movement, providing traction only in the direction of rotation. This unique design allows for smooth and precise movement in any direction on the plotting surface.
- Pen Mechanism:
An SG90 servo motor is used to control the pen mechanism, lifting and lowering the pen as needed to draw on the surface.
- Omni-Wheels and Motion:
Features of the Machine
- Compact Design:
The plotter has a small footprint, making it suitable for use in limited spaces.
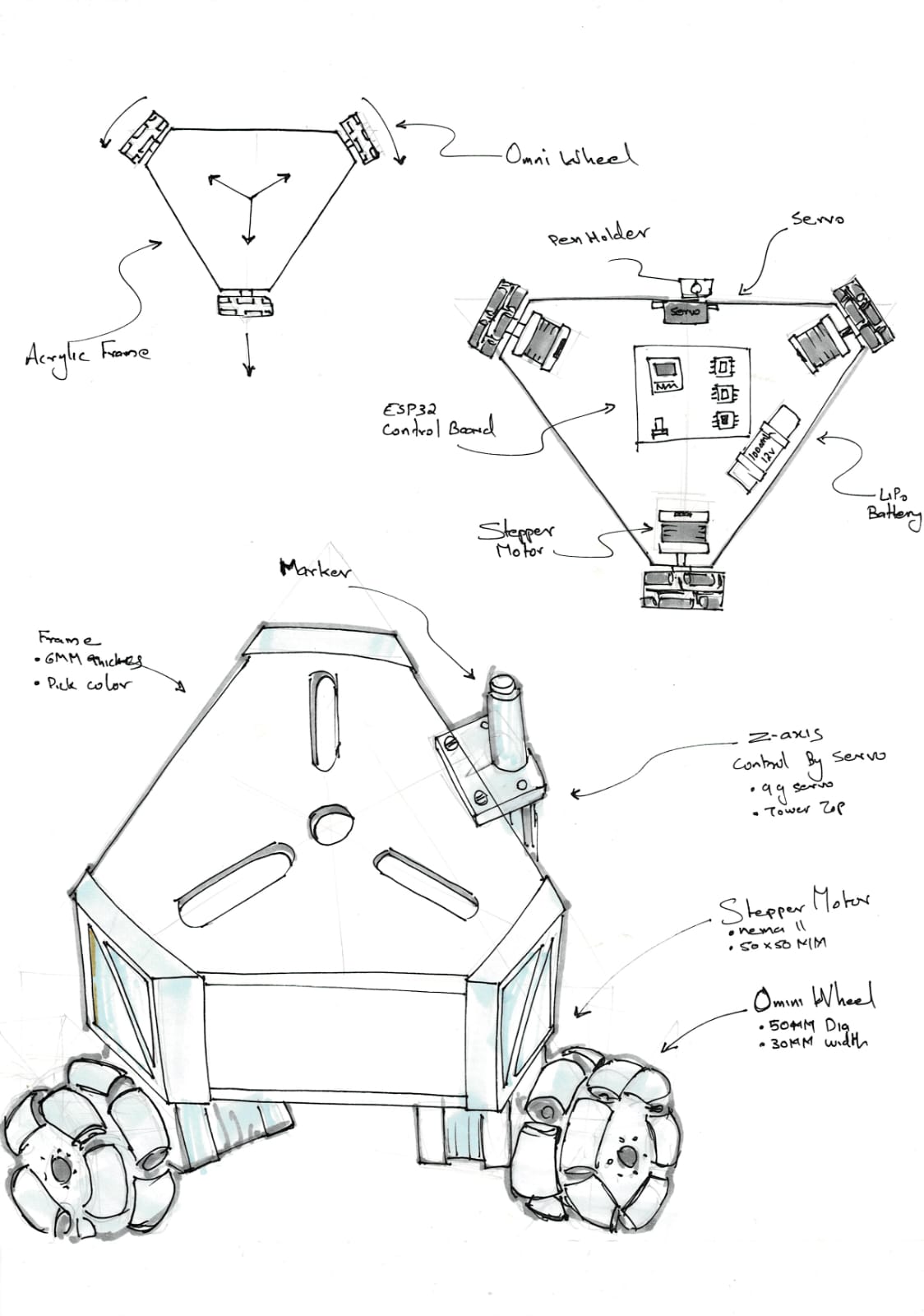
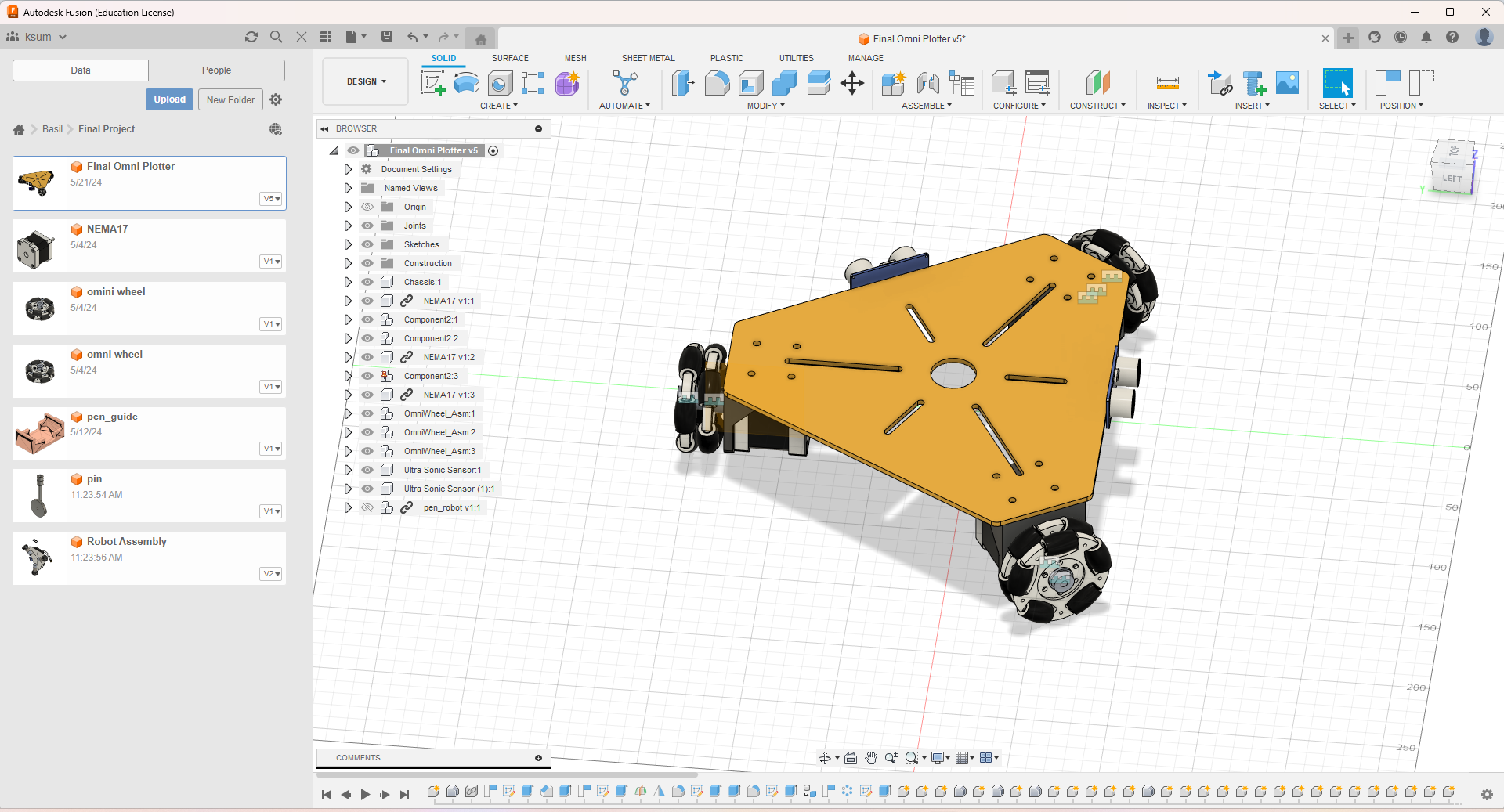
- Large Drawing Area:
Despite its compact size, the plotter can handle large drawings due to its Bluetooth design, which eliminates the need for physical connections that restrict movement.
- High Resolution:
The plotter achieves a horizontal resolution of 8.78 steps per mm, ensuring precise and detailed drawings.
- Bluetooth Operation:
The wireless design allows for remote control and operation, increasing convenience and flexibility.
- Simple Construction:
The design minimizes metalwork and only requires basic tools for assembly, making it accessible for hobbyists and DIY enthusiasts.
Design Parameters
- Plotting Area: The effective plotting area is determined by the movement range of the omni-wheels and the length of the pen mechanism. The design should accommodate various paper sizes typically used for plotting.
- Stepper Motor Specifications: The NEMA 17 stepper motors are chosen for their balance of torque and precision. The current and voltage settings are adjusted using the Big Easy Driver boards to match the motor specifications.
- Servo Motor Range: The SG90 servo motor's range of motion is calibrated to ensure the pen can be lifted and lowered accurately without causing smudges or missed lines.
- Power Supply Requirements: The 12V power supply should provide sufficient current to power all three stepper motors and the servo motor simultaneously, with consideration for peak power demands during operation.
- Bluetooth Range: The HC-06 Bluetooth module should have a range that covers the typical working area where the plotter will be used, ensuring reliable communication without dropouts.
Bill of Materials (BOM)
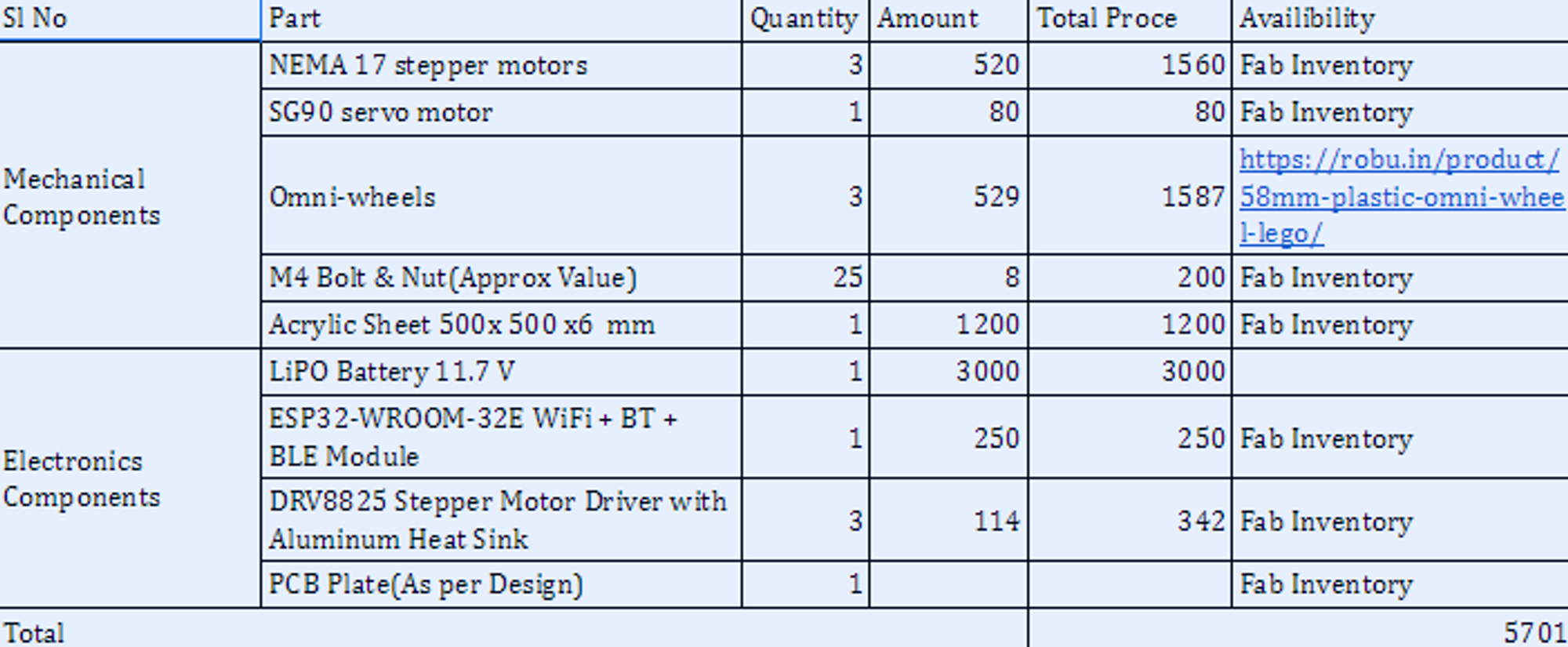

Schedule
Date | Activity | Status | Remarks |
18 May 2024 | Main Body Design | Completed | Scheduled to Zund |
20 May 2024 | Motor Bracket Design | Completed | Scheduled to 3D printing |
21 May 2024 | Wheel Coupling | Completed | Done By Milling |
22 May 2024 | Assembly of Wheels | Completed | |
23 May 2024 | Assembly of main Body | Completed | |
24 May 2024 | Testing with CNC shield | Pending | |
27 May 2024 | Electronics Design Micro Controller Board | Pending | |
27 May 2024 | Electronics Design Main Board | Pending | |
28 May 2024 | Pen Holder Design | Pending | 3D Printing |
29 May 2024 | Electronics Production | Pending | |
30 May 2024 | Soldering | Pending | |
31 May 2024 | Soldering | Pending | |
1 June 2024 | Software checking, Interfacing | Pending | |
2 June 2024 | Testing using board | Pending | |
3-5 June | Total System Integration | Pending | |
5-7 June | Documentation | Pending | |
10 June 2024 | Final Presentation | Pending |
I have completed the base design in my wildcard week
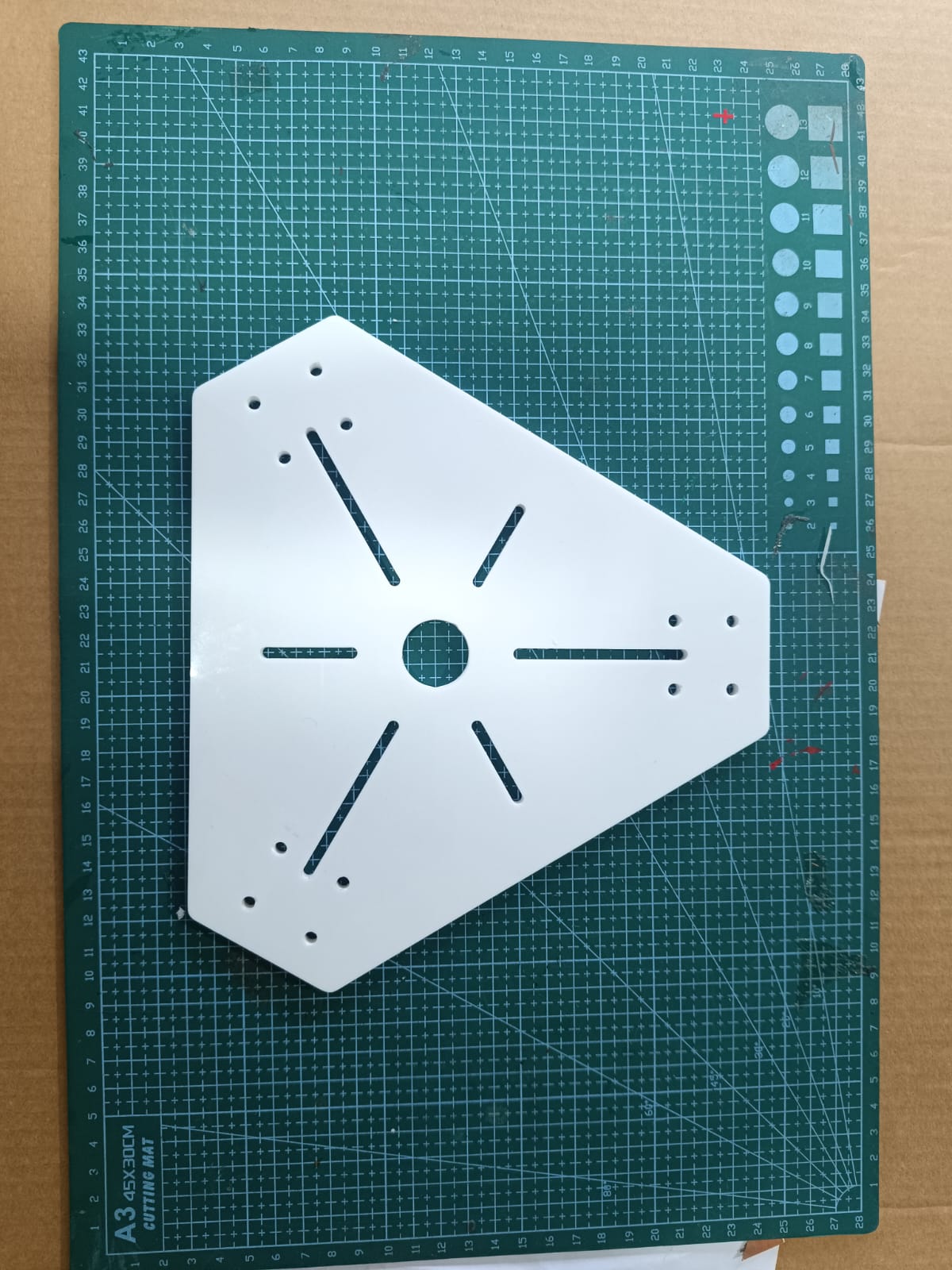
I ahve 3D Printed the motor mount & wheel base for the plotter
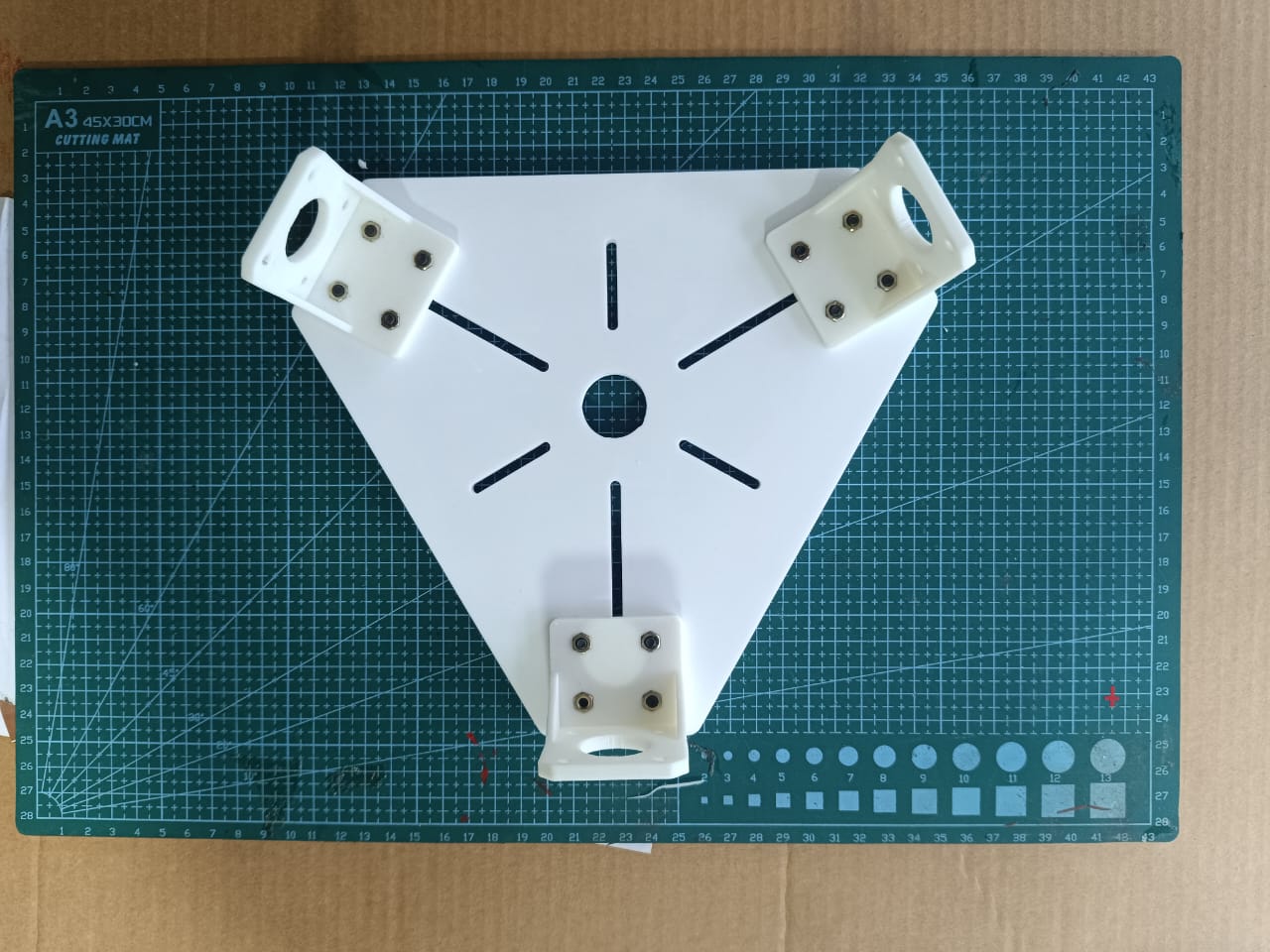
Connected motor to thrame in this week
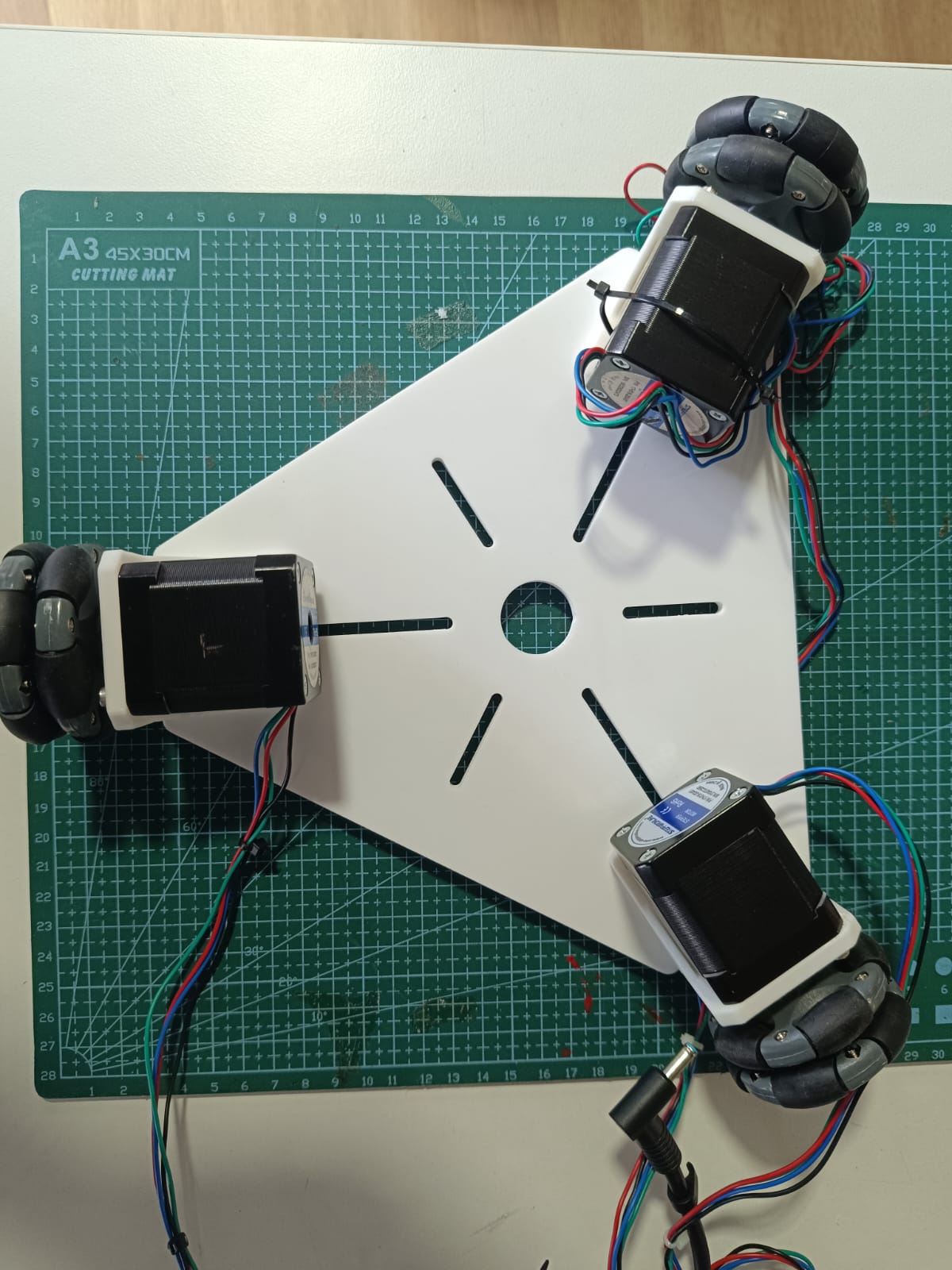