Week 17: Applications & Implications
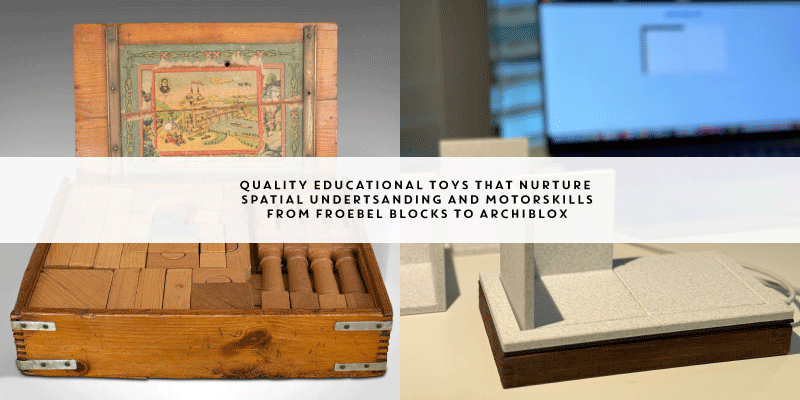
For the proof of concept prototype of Archiblox to be built as the final project for FabAcademy, I will focus on building the physical components, electonic systems, and basic user interface that virtually represents a 2D floorplan of the physical blocks.
Schedule
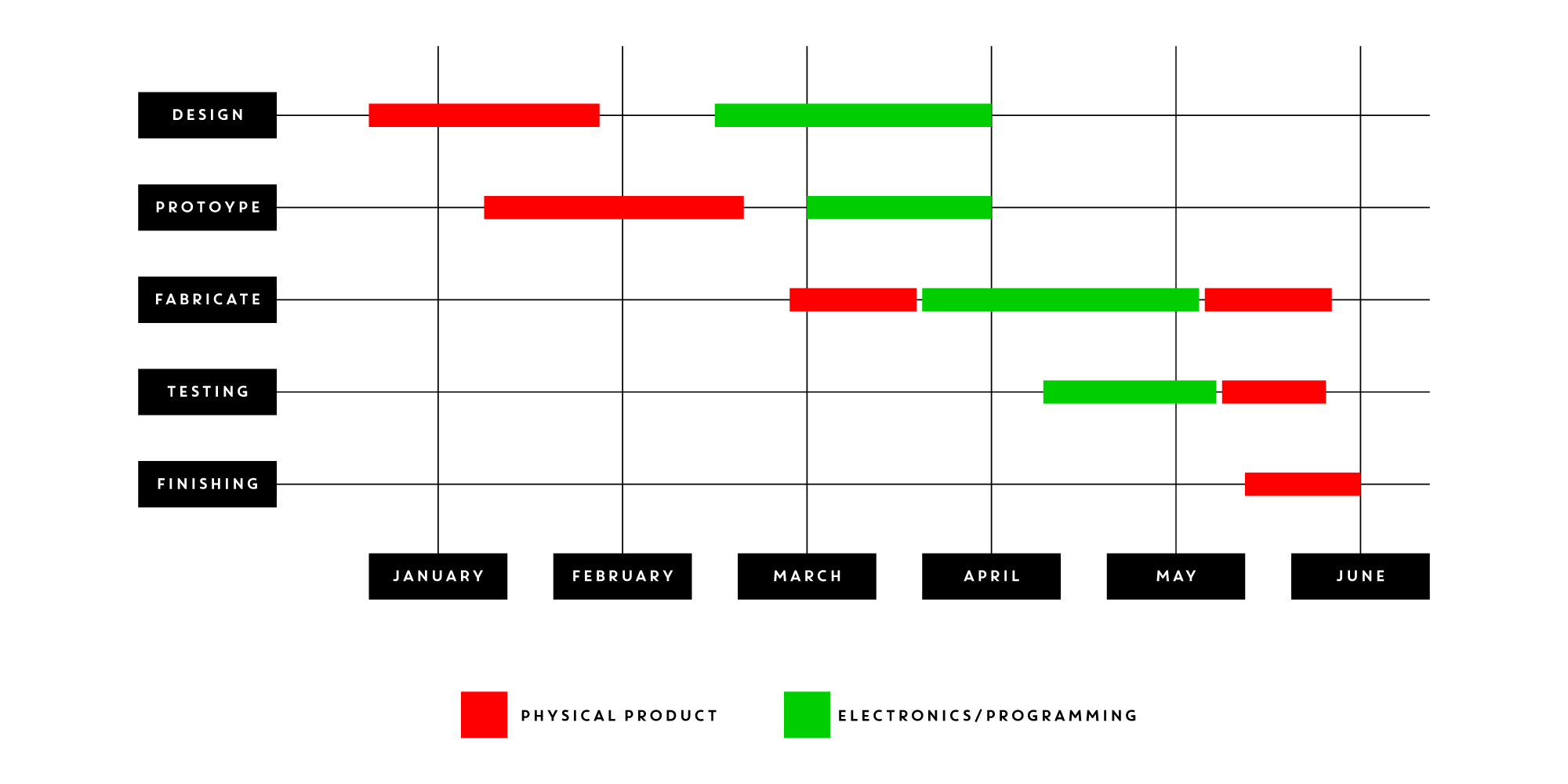
Bill of Materials
What will it do?
Archiblox discreetly senses a physical 3-dimensional tile placed on a build board and wirelessly transmits the 2-dimensional floorplan of the tile on a web app.
Who's done what beforehand?
The concept builds on the educational values of Froebel Blocks for free play, but combines it with technology to nurture advanced spatial thinking. There are other technology toys on the market that use QR codes for an AR view of a digital 3D object on a physical object through a smartphone or virtual reality/augmented reality glasses. This concept marries the best of both worlds allowing for tactile physical creativity and unlocking 2d digital play - both synced live.
What will you design?
I will design the Custom PCB boards, the Build Board, the 3-Dimensional tile variations, and the basic web interface the sensors transmit to.
What materials and components will be used?
The build board will be made up of solid wood, to harken back to the crafted toy experience, and the tiles will be made of PLA with a marble composite aesthetic.
Where will they come from?
Pine is prevalent in South Florida as many lumber yards source these locally. The Bambulabs PLA, electronic components, and magnets will be imported.
How much will they cost?
My final 2-tile mini board prototype will have a total material cost of $45.75 (refer to the bill of materials linked below) but this will not account for the sunk costs of tooling, additional quantities of components sold in bulk packs, and other overhead costs.
What parts and systems will be made?
The custom pcbs will be made on a Bantam Tools precision CNC, the build board will be made on a Shop Sabre CNC router, and the individual tiles will be made on a Bambulabs 3D Printer.
What processes will be used?
The board code will be programmed using CircuitPython on Thonny, The PCBs will be designed on KiCad and milled using the Bantam Tools CAM software. The build board will be designed in Rhinocerous3D and sliced in Bambulabs slicer, and the top of the board will be laser etched using a Full Spectrum Laser running RetinaEngrave V3. Soldering will be done using paste and a handheld heat gun for reflow. Magnets will be press-fit into the tiles and secured with adhesive.
What questions need to be answered?
This prototype will test the possibility of a new hybrid physical and digital play system. Will it be intuitive enough for a child to interact with it with little to no instruction? It will also validate the concept of using hall sensors and magnets to trigger the synchronized play environment.
How will it be evaluated?
The prototype will be evaluated by its ability to deliver the hybrid 3d and 2d live creative play experience.
What are the implications?
Archiblox would be a versatile modular system for the following markets: Educational play as a building toy, Creative play for older gaming enthusiasts including role-playing games or other map-based play, and for the Architectural Design industry to quickly mock up a layout with a client in real-time. The next version could have different customized themed-tile types to fit each market, and the web app can also have various modes to support these various use-cases.
Copyright 2024 Thomas Pupo - Creative Commons Attribution Non Commercial
Source code hosted at fabcloud/fabacademy/2024/thomas-pupo