Week 4: Electronic Production
The assignment:
2. Individual Assignement:
PCB – printed curcuit boards
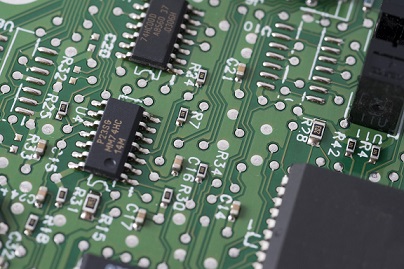
PCB boards are used in all electronic devices that we use today. So it is important to understand how these curcuit boards are designed and integrated into devices. Both from a environmental point of view (which materials are used, how is the production process etc,) and because it makes it possible for us to customize the PCBs to specific needs of our projects. The reason why it makes sense to print your own PCBs is also because it is a way to control all the wirings and reduce chances of errors like short curcuits. Its an alternative to using breadboards, jumpers etc.
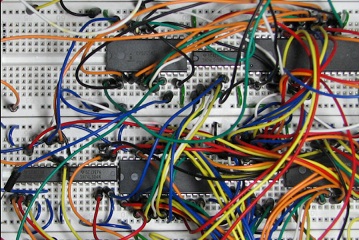
There are different types of boards. E.g handdrawn, vinylcut, flex-material etc. We will be using rigid, single sided FR1 material – because it is low cost, it has good electrical and mechanical properties and mechanical drilling can be done on it.
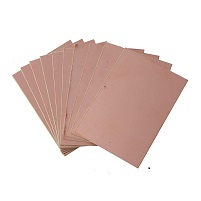
How to do it
There are different techniques. Edging (difficult to control the process and there is a lot of waste), vinylcut, fiberlaser or milling. We will be milling and the whole process consists of cutting the board>selecting the components>soldering>doing the blink test.
1. Cut the board:
Milling requires a machine, - in the lab we have a Roland SRM-20 CNC + endmills.The endmills we will be using 1/64” for the traces and 1/32” for the holes and the outline. Steps:
Position the origin of XY first and save. Then carefully set the Z-origin. Do the last mm by hand (the drop) and save. The files I used were the 3 quentorres files that were prepared in mods. On the images below you can see my process:

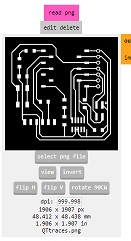
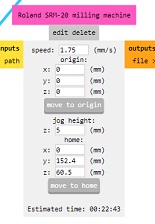
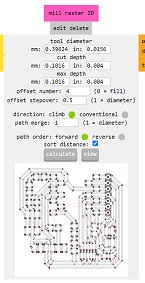
This openened a window where I could see the toolpath
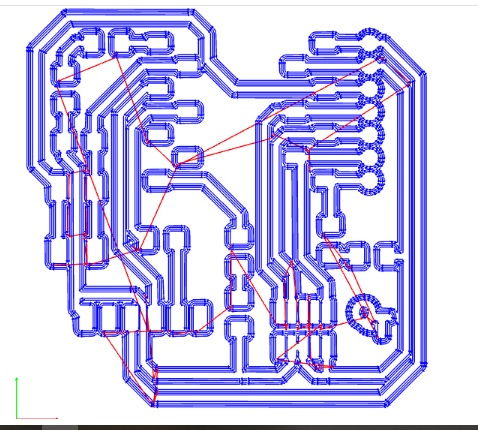