Week 3: Computer Controlled Cutting
The assignment:
1. Group Assignment:Click here
2. Individual assignment:
a. Cut something on the vinylcutter
b. Design, lasercut, and document a parametric construction kit
What is Computer Controlled Cutting? Computer controlled cutting is the usage of computer software to design objects defined by parameters to send to cutting machines, such as laser cutting machines and vinyl cutting machines.
A. Vinylcutter Roland GX-24:For the vinylcutter I wanted to do 2 things.
1. Learn the settings of the vinylcutter and making adjustments to get the machine to work right and make a test cut on a vinyl material.
2. Making a design/cut for my bag and transfer it with the heatpress.
My workflow:
1. I wanted to use Inkscape on my personal computer to work with the GX-24. So I started by downloading and installing the driver, to see if I could connect to the cutter. That worked fine.
2. As I wanted to focus on the technical part I found an image online (Wikipedia/ freelicense) and vectorized it in Inkscape.
.
Ready to cut.
3. Choose the right vinyl for your purpose. There are a lot of different types of vinyl on the market e.g. indoor- or outdoor-use, for stickers, car decorations, conductive foil, textile printing and more. I chose from the box in the lab (and hoped for the best 😊, because there where no declarations at hand)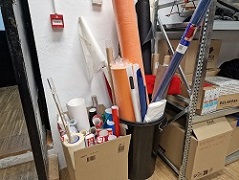
– I checked out a Danish supplier to learn more about materials: https://www.skilteproduktion.dk/materialer/standardfolie_9681.html
4. Insert the vinyl from the back. Place the roller bearings underneath the white markings and press down the lever.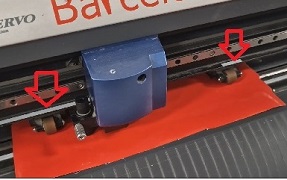
. Press enter and the knife will slide into the starting position. Note that the GX-24 measures width on a role and width and hight on a piece.
5. Make a test cut. Before pressing the test botton check the “force”. It was set to 110 grams of force which seemed a bit much (for standard vilny Roland recommends somerwhere between 60 – 100 gr/f.) So I adjusted that. There also is manual slider for minor adjustments. You might also want to check the knife for material leftovers and the distance out of the holder.
When that is done you are ready to test cut. The cut should only be in the vinyl, not in the paper and easily removeable from the rest of the vinyl.
6. Make a cut. Send the file to the Roland GX-24 and it starts cutting. When it is done cut out the piece you are going to work with and remove excess material.
7. Use application tape for this step. It takes of the vinyl from the paper.
8. Place the vinyl where you want to put it and take off the tape without leaving airbubbles under the vinyl.
For this weeks assignement I also chose to design and produce something with the heatpress and print on textiles.
I made a design with my name and an upcycling logo. File: Textil print.Just remember to mirror the image/ text before saving.
Getting the heatpress ready I warmed it up to 165 degrees and set the timer to 20 seconds. I did 2 presses.
Warming up to 165 degrees
20 seconds for each press
Let it cool betweeen each press
Done
B. Parametric design in Fusion 360.
Parametric design lets the model adapt to changes in the parameters and create new sizes or configurations. Creating a press-fit piece with parametric design in Fusion 360 involves using sketches, parameters, and constraints.
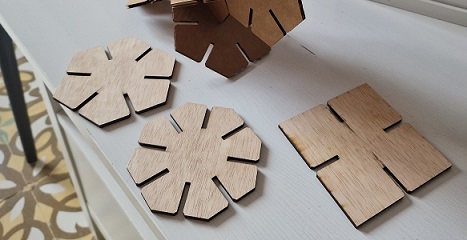
1. Sketch the model, apply dimensions and constraints
I started with an analog sketch
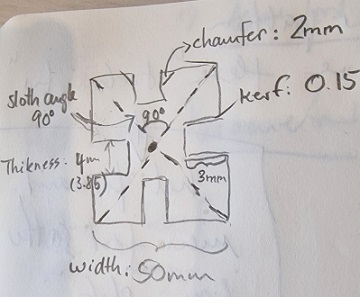
In Fusion I entered the sketch mode and started creating the sketch. 1. sketch the triangle 2. insert a rectangle for the slot. 3. Constrain the midpoint of the line to the rectangle. 4. Trim
2. Add features
Add chamfers and extrude to get an impression of height.
3. Create parametric features and link them
As you can see on the analog sketch above I had already calculated the dimensions. Instead of manually creating every part of the model, parametric design allows you to define logical rules and parameters.
The following can be used as steps to follow if you want to go from analog sketch to a parametric design:
- First go to change parameters in the “modify” menu
- Then you open a dialog box by clicking on the +symbol and add the parameters.
- In this example I start with the thickness of the material which is 4mm and press OK
Then I do the same again by clicking on the +symbol and add the next parameter. This time the kerf = 0.15 mm
And continue doing this for all the parameters untill I had all the parameters.
Parameters for pressfit and parameters in the sketch
File:Fusion pressfit.
Later I wanted to change the number of sides eg. from 4 to 6 and 8 without changing anything else. I could easily do this just by altering the number of sides in the “change parameters” menu as you can see in the originale *dxf file below
4. Export
I made a pattern so I could save 4 sided, 6-sided and 8-sided versions. Then I exported them as *dxf to continue with the process at the lasercutter and test cut.
:File:*dxf.
Reflections:
As Fusion still is new to me I struggled a bit hanging on the classinstruction. Afterwards I had some help from Tony who shared his file with me so I could see how he had done things. I then looked into it in my own pace and figured out how to do my parametric design. I had to concentrate on that instead of paying attention to Grasshopper class.
Lasercutting
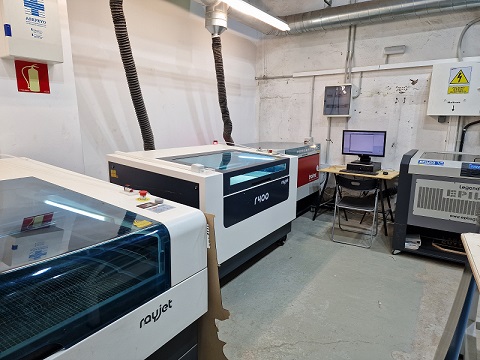
At the lasercutter I first made sure that the lasercutter was ready for use. I used the Rayjet r400.
That means setting the focus, leveling the material, opening the air-flow, turning on the extraction.
From the stationary PC I accessed the https://cloud.iaac.net:5001/ found my file (first the testfile and then the actual projectfile) and opened it in Rhino (the man in the middle 😊). As I was going to cut I made sure that the layer was red.
In the Rayjet manager I connected to the lasercutter and made material settings for Cardboard using the board from the lab. (Cut = Speed:2, Power: 20)
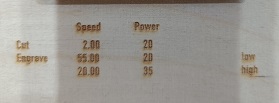
I learned that the settings are only guidelines to help you find the right settings. And then I pressed start to cut a test square. I didn´t cut through so I increased the power, - first to 25 (still not OK) and then 30 that cut through fine.
Then I cut the pressfit. The kerf settings weren´t right so I had to adjust. For the kerf test we had made a comb design. The separation between teeth decreases in steps of 0.05mm. My settings for the kerf were 0.15mm. Now I went for 0.20 mm. After testing again the fit was better and I could start cutting the project. To test materials I both cut in plywood and cardboard.