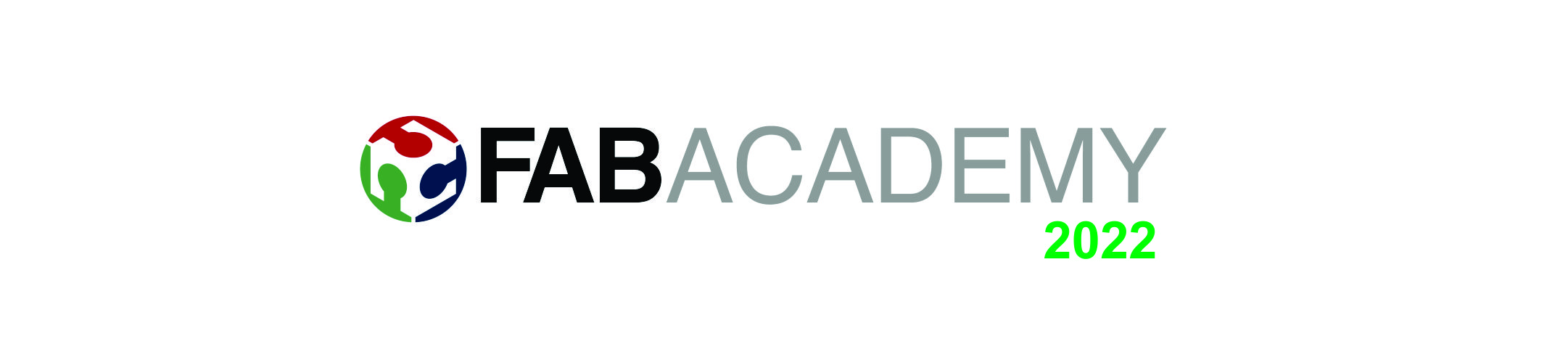
WEEK 9:
MOLDING AND CASTING
The task is to mold and cast, and design a mold.
Group Assignment:
• Review safety data sheets for each of your casting and molding materials, then make and compare test patterns with each.
Individual Assignment:
• Design a mold around the material and tools you will use, mill it (rough cut + (at least) three-axis finish cut), and use it to cast parts.
The materials to use
MoldMax
PRODUCT DESCRIPTION Mold Max® silicones are tin-based hardening silicone compounds that possess exceptional pot life and handling properties. Mold Max® silicones feature Smooth-On's exclusive “Libra®” catalyst, which allows for a long shelf life. Mold Max® silicones can be pigmented with Silc Pig® silicone colorants. The pot life of silicones for pouring is 45 minutes and they harden overnight at room temperature. Mold Max® silicones reproduce the smallest details and are suitable for various industrial and artistic applications, such as the making of molds to reproduce prototypes, furniture, sculptural and architectural elements. Mold Max® 10, 20, 25 and 30 silicones can be thickened with THI-VEX® additive for brush applications. (Note: THI-VEX® is NOT compatible with Mold Max® 40 or 60). Mold Max® 60 offers the highest heat resistance for casting metal (see separate technical bulletin). Mold Max® silicones are suitable for casting a variety of materials including wax, plaster, low-melting metals/alloys, and urethane, epoxy, or polyester resins (without mold release). Important: Weigh the components of Parts A and B using a gram scale to achieve a good result with Mold Max® silicones. Vacuum degas the mixed material with a pump and vacuum chamber to remove trapped air
TECHNICAL SUMMARY
PROCESSING RECOMMENDATIONS
PREPARATION...Safety – Use in a well-ventilated area (room size). Wear safety glasses, long sleeves, and rubber gloves to minimize the risk of contamination. Use only vinyl gloves. Latex gloves prevent the rubber from hardening. Store and use material at room temperature (73°F/23°C). Storing it at higher temperatures will also shorten the shelf life of unused material. These products have a limited shelf life and should be used as soon as possible. Sealant / Release Agent Application - Sulfur-based clays can inhibit Mold Max® rubber and produce a tacky design surface or prevent the mold from hardening altogether. If you are concerned about compatibility between the rubber and the surface, a small scale test is recommended. Apply a small amount of rubber to a non-central area of the design. Rubber inhibition occurs when it appears gummy or unhardened after the recommended hardening time. A good way to prevent this is to spray an "insulating" coat of clear acrylic lacquer directly onto the design. Let dry completely. Although not usually necessary, a release agent will facilitate release on most surfaces. Ease Release® 200 is a proven release agent for making silicone rubber molds and for releasing new silicone from hardened silicone. You can order Mann Ease Release® products from Smooth-On or your Smooth-On distributor. Since no two applications are the same, if in doubt it is recommended to perform a small test application to determine if the performance of this material is appropriate.
Start the individual task for the week by designing the part in 3D in solidworks.
After designing the part in 3D, design the mold of the part, using solidworks.
Finished mold, ready for machining on the milling machine.