Computer Controlled Cutting
What is Computer Controlled Cutting
Computer controlled cutting is a form of CNC specific to 2D machining including laser, plasma, water, vinyl, and other
forms of cutting. It uses a CAD software just like other forms of machining, but a vector CAD package is required. Most
parametric CAD softwares such as Fusion 360, Solid Works and FreeCAD all have 2D vector capabilities, however there
are some easier to use, though arguable less useful softwares, such as Affinity Designer, Inkscape and Illustrator. This
design can then be exported as the appropriate vector file such as SVG or DXF then imported into a CAM software which
will ocnvert it into machine code to be loaded into the machine.
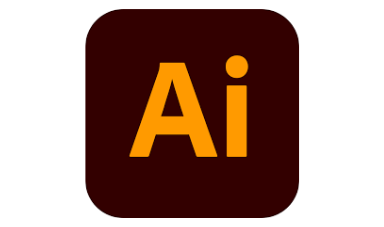
Illustrator
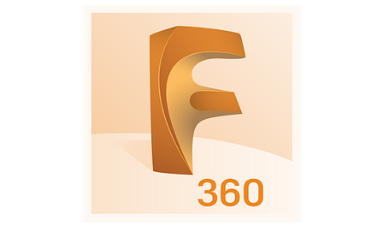
Fusion 360
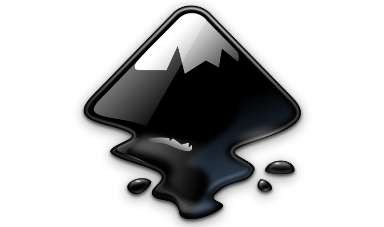
Inkscape
Vinyl Cutting
This week we used the vinyl cutter to cut out our team's logo. First off we designed our logo in a CAD software. Our group chose to use Affinity Designer,
a software nearly identical to Illustrator except its only a single purchase else then a pricy recurring subscription. We designed our logo by getting an
Alpha symbol, and placing a circle around it. It's a simple design, however a clear one, and one that will be simple to cut. Once our design was finished
we exported it as a PNG image, and imported it into our vinyl cutters CAM software. The CAM software, SureCuts Pro, take in the PNG image and traces it
in order to get vector information. We can then do simple CAD work in the CAM software, moving the cut, rotating it, duplicating it, and so forth. We
then loaded the vinyl into the vinyl cutter machine and set the approriate speed and force settings for the vinyl we were using. Afer loading the
vinyl we started the cut. Once the cut was finished we cut off the vinyl from the roll with an X-Acto knife. We then remved the excess vinyl from the cut off
piece in a process called weeving. We then transfered the vinyl to the vinyl paper slowly. All that was then left was to transfer the vinyl on the paper to the
item of interest in this case a mug I own.
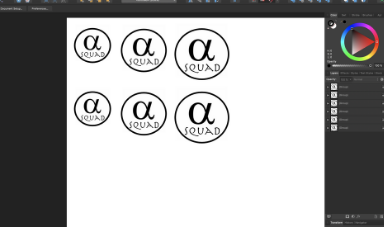
Designing Logo in Designer
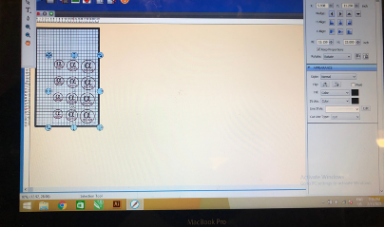
Using CAM Software Sure Cuts Pro
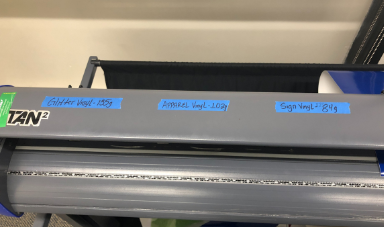
Setting Vinyl Cutter Settings
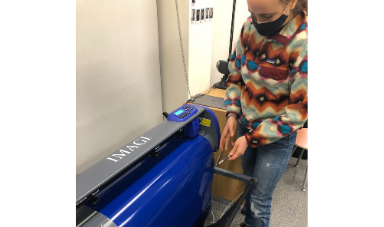
Cutting Vinyl off of Roll
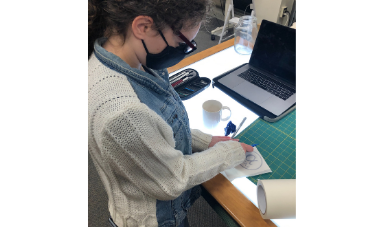
Moving Vinyl to Transfer Paper
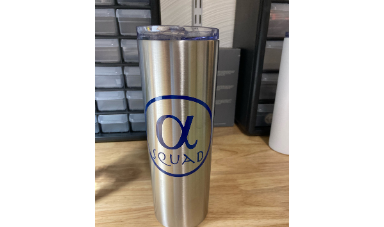
Final Vinyl Application
Characterizing our Laser Cutter
The main feature of our laser cutter my group was interested in analyzing was the kerf. The kerf is the amount of material that is removed during a cut.
For this experiment we were trying to show that the speed and power has no effect on the kerf. We designed a very simple rectangle in Inksape with a known size
and imported it to our machine's CAM software. We repeated the same rectangle cut multiple times with various powers and speeds. We noted all the values, and measured
our cut out each time using a callipers. From there I brought the data into R and wrote a very simple script to run a multivariable linear regress on the data
modeling kerf from speed and power and print a summary of the results as well as the average kerf. We found the average kerf of our laser cutter to be 0.18875, and from the
linear model the coeffecient for the speed and power have a p-value greater than 0.05, so at an alpha of 0.05 we reject the alternative in favor of the null, meaning that
the coefeccients are not significantly different then 0, so are not contributors to determing the kerf. If I had more time I would have liked to shown that what effects the kerf
is the focus of the laser, though we did a quick demonstration to show this by defocusing the laser to move the bed far away from the source resulting in a cut with a very large kerf,
as well as a small fire.
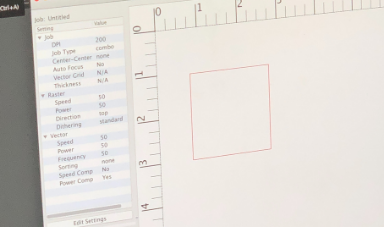
Epilog CAM Software
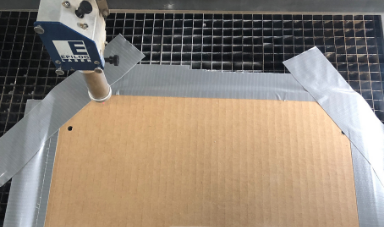
Work Holding
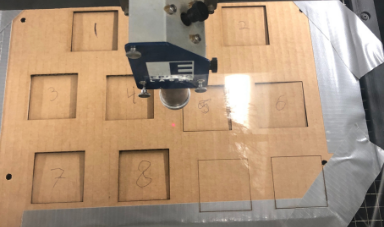
Experimental Cuts
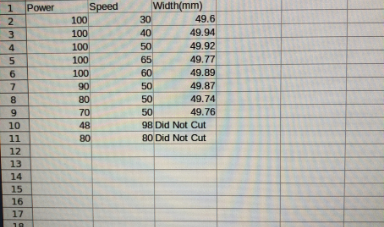
Raw Data
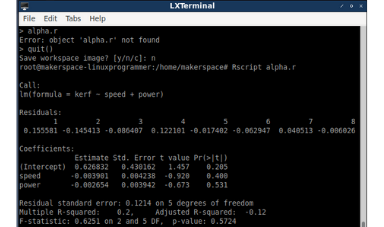
Linear Model
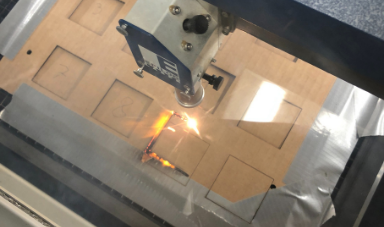
Defocusing the Laser
Press Fit Kit
The final project to make is a press fit kit, which is essentially a bunch of cutout pieces that can be assembled in various different ways. To make
this I used Fusion 360, a parametric CAD software. I decided to design my pieces with living hinges, and so started off by designing those. I found it best
to use parameters to set information on just the first two lines, then use the rectangual pattern tool to copy the two lines multiple times to make the
living hinge, and adjust the paramers as I see fit. Once the living hinge was designed I then added 3 slots on each side of the living hinge each of their width's
being the thickniess of the carboard. All that was then left to do was cut out multiple of the pieces, and have fun building different designs in various different ways.
Overall the design worked well there were no adjustments needed. I did make however the parts of the press fit fitting together a slight bit smaller than the actual size of
the cardboard in order to account for kerf by just a few millimeters. The settings I ended up using fro the vector cut on the laser cutter were 50 speed, 80 power, and 100 frequency.
Overall I was lucky and there was no need to cut multiple times since I had a good solid fitting on the first try, but if needed I can readjust the parametric settings to change the box
to make it easy to print again.
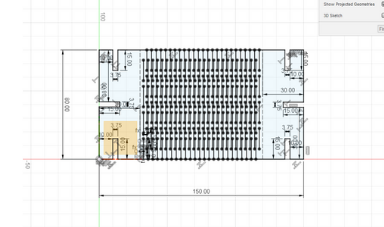
Fusion Design
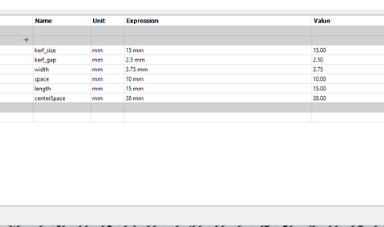
Fusion Parameters
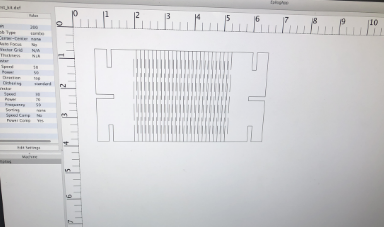
Epilog CAM Software

Cutting out Part
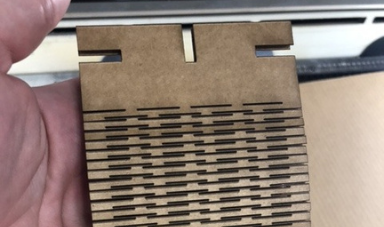
Singular Cutout Test
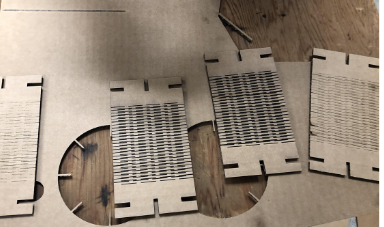
Multiple Cutouts
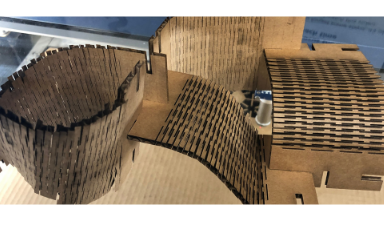
Assembly 1
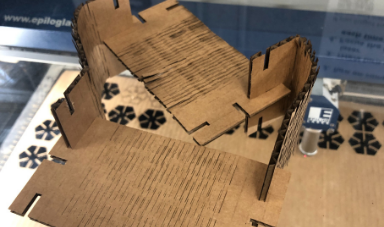
Assembly 2
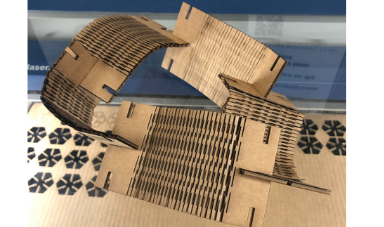
Assembly 3
Click Here to Download all the files from these projects!